M. A Mohammed Arshad Ibrahim 1, M. Nidhin 1, R. Sudhakar 1, M. Jothilakshmi 2, R. Srinivasa Raghavan 2
1Student of Civil Engineering, B.S.Abdur Rahman University, 48, Chennai
2Department of Civil Engineering, B.S.Abdur Rahman University, 48, Chennai
Correspondence to: M. A Mohammed Arshad Ibrahim , Student of Civil Engineering, B.S.Abdur Rahman University, 48, Chennai.
Email: |  |
Copyright © 2012 Scientific & Academic Publishing. All Rights Reserved.
Abstract
In this study, the coarse aggregate are completely replaced by fly as aggregate in fly ash concrete. A mix design was done for M20 grade of concrete by IS method. Ordinary Portland cement of 43grade was selected and fly ash aggregate were prepared by mixing fly ash with cement and water. The properties of fly ash coarse aggregate were studied. The cement and fly ash proportions 70:30, 60:40 were tried with a suitable water cement ratio of 0.3 to get the fly ash aggregate. The concrete cubes, cylinder were cast with fly ash aggregate obtained from the above two cement fly ash proportion. Then the compressive strength was tested. This paper briefly presents the compressive strength development of fly ash aggregate concrete at different days of curing.
Keywords:
Pelletisation, Water Cement Ratio, Fly Ash Aggregates, Light Weight, Economical, Compressive Strength, Cube, Cylinder
Cite this paper:
M. A Mohammed Arshad Ibrahim , M. Nidhin , R. Sudhakar , M. Jothilakshmi , R. Srinivasa Raghavan , "Experimental Study on Concrete with Fly Ash Pellets Replacing by Coarse Aggregate", International Journal of Construction Engineering and Management , Vol. 1 No. 3, 2012, pp. 20-26. doi: 10.5923/j.ijcem.20120103.02.
1. Introduction
In conventional concrete, density of concrete where is in the order of 2200 to 2600 kg/m3 makes it an uneconomical structural material compared to low density fly ash aggregate concrete. In order to produce concrete of desired density to suit the required application, the self-weight of structural and non-structural members are to be reduced. Hence economy is achieved in the design of supporting structural elements which lead to the development of light weight concrete. Lightweight concrete is defined as a concrete that has been made lighter than the conventional concrete by changing material composition or production method and made by replacing the usual coarse aggregate by lightweight aggregates. Though lightweight concrete cannot always substitute normal concrete for its strength potential, it has its own advantages like reduced dead load, and thus economic structures with enhanced seismic resistance, high sound absorption and good fire resistance can be erected. Because of the above reasons the study on fly ash pellets concrete is taken in this research work.
2. Formation of Fly Ash Pellets
The constituents like cement, fly ash and water are used to produce the fly ash aggregates. Water facilitates the binding material to react and paves the way for the function of the aggregate with good bond property.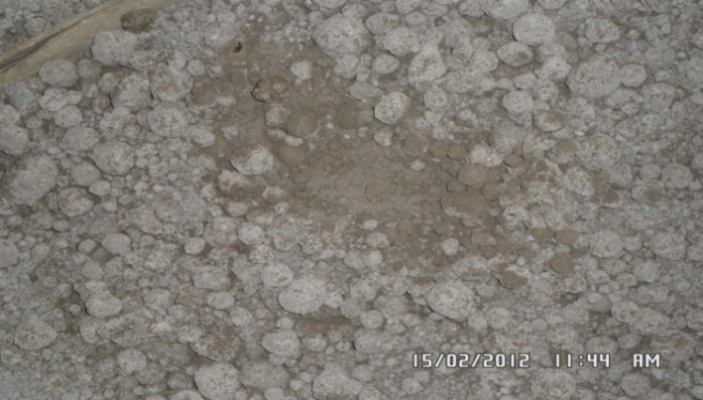 | Figure 1. Fly Ash Pellets |
3. Preparation of Fly Ash Pellets
The fly ash coarse aggregate is prepared by mixing the cement and fly ash in 70:30 and 60:40 ratios. The manufacturing process goes as follows,♣ First the required quantity of fly ash is taken in the mixer machine and then the exact ratio of the cement quantity is put in the mixer for 60:40ratio.♣ Now for mixing take the water cement ratio as 0.3.♣ The water must be added slowly care must be taken to avoid excess addition of water.♣ As the mixer rotates the cement and fly ash combine and form a spherical shaped aggregate by process of pelletisation.♣ After some time the mixer is lowered and formed fly ash aggregate is collected.♣ The same procedure is followed for the other ratios also.
4. Preparation of Fly Ash Pellets Concrete
4.1. Mix Design
The preparation of fly ash concrete is made as the conventional concrete. But the changes in the mix design must be done to corresponding to the changes in the densities of the aggregates. Here are the list of materials used along with their quantity and the final mix design.(i) Cement = 50 kg(ii) Sand = 71.25 Kg(iii) C. A = 86.4 Kg(iv) Water =25 Kg(v) Extra quantity of water added for the absorption of Coarse aggregate for 1% = 1.295 Litres0.5: 1 : 1.425:1.728 is the required mix proportion for M20 mix
5. Characteristic Compressive Strength PF Fly Ash Pellets Concrete
5.1. FOR CUBES
Table 1. Compressive strength of cube specimen |
| | Grade of concrete | Concrete with 60:40 Fly Ash pellets | Concrete with 70:30 Fly Ash pellets | 7 days curing | M20 | 29.704 MPa | 24.852 MPa | 28 dayscuring | M20 | 36.62 MPa | 34.12 MPa |
|
|
5.2. For Cylinder
Table 2. Split strength of cylinder specimen |
| | Grade of concrete | Concrete with 60:40 Fly Ash pellets | Concrete with 70:30 Fly Ash pellets | 7 days curing | M20 | 15.36 MPa | 15.18 MPa | 28 dayscuring | M20 | 24.14MPa | 23.03 MPa |
|
|
6. Comparisons of Strength and Cost
6.1. Comparison of Physical Properties of Conventional Aggregate with Fly ash Aggregate
♣ The above table shows that even though the impact value of both the ratio of fly ash aggregate is high they can be used in the building concrete but they can’t be use be used as a road materials.♣ The above table also shows that the abrasion value of the fly ash aggregate is less when compared to conventional aggregate so they are good in abrasion.♣ The 60:40 ratio aggregates attrition value is high, but 70:30 aggregate is good in attrition.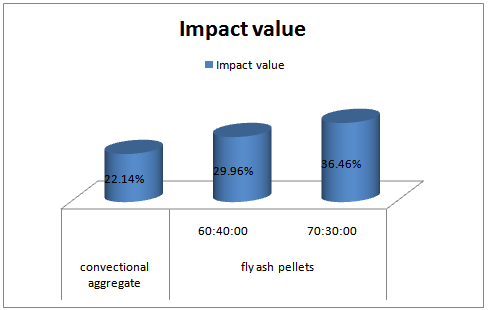 | Figure 2. Impact Value Graph |
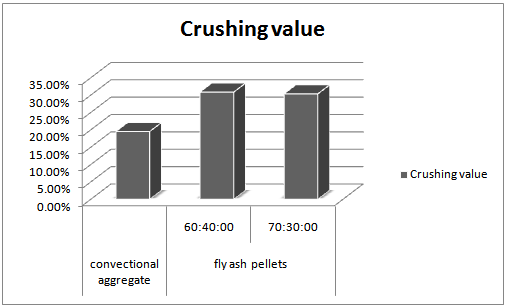 | Figure 3. Crushing Value Graph |
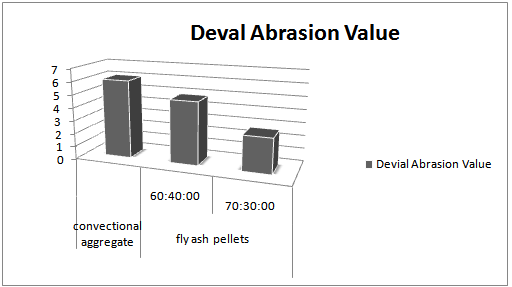 | Figure 4. Deval Abrasion Graph |
Table 3. Properties Of Fly ASH Pellets And Conventional aggregate |
| S.NO | PROPERTIES | CONVENTIONAL COARSE AGGREGATE | FLY ASH COARSE PELLETS | 60:40 | 70:30 | 1. | Shape | Angular | Spherical | Spherical | 2. | Specific gravity | 2.75 | 1.456 | 1.45 | 3. | Impact value | 22.14% | 29.96% | 36.46% | 4. | Crushing value | 19.5% | 30.85% | 30.34% | 5. | Size (mm) | 4.75 to 20 | 4.75 to 20 | 4.75 to 20 | 6. | Abrasion Value | 6.03 | 4.85 | 2.7 | 7. | Attrition value | 1 | 5.7 | 4.6 |
|
|
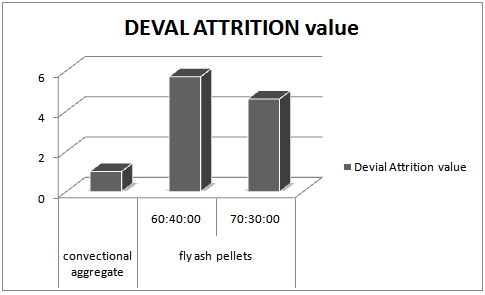 | Figure 5. Deval Attrition Graph |
6.2. Comparison of Compressive Strength of Conventional Concrete and Fly Ash Pellets
Table 4. Comparison of Compressive strength |
| S.NO | SPECIMEN | DAYS | CONVENTIONAL CONCRET | FLY ASH PELLETS CONCRET | 60:40 | 70:30 | 1. | Cube | 7 | 34.27 MPa | 27.904 MPa | 24.352 MPa | 2. | Cylinder | 7 | 11.66 MPa | 15.36 MPa | 15.18 MPa | 3. | Cube | 28 | 46.65 MPa | 36.62 MPa | 34.12 MPa | 4. | Cylinder | 28 | 21 MPa | 24.14 MPa | 23.03 MPa |
|
|
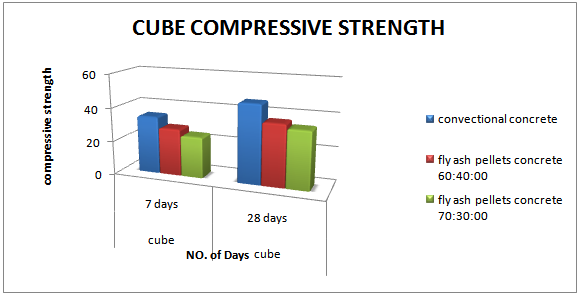 | Figure 6. Cube Compressive Strength |
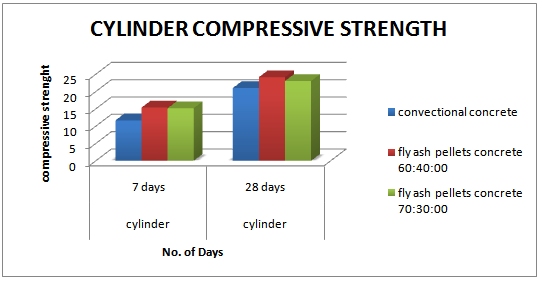 | Figure 7. Cylinder Comprezssive Strength |
6.3. Comparison of Cost of both Conventional Concrete and Fly Ash Pellets Concrete for One Cube (.15m x .15m x.15m)
Relating cost of both conventional concrete and fly ash aggregate concrete for one cube (.15m x .15m x.15m). | | CONVENTIONAL CONCRETE | FLY ASH PELLETS CONCRETE | 70:30 | 60:40 | S.NO | MATERIAL | QUANTITY | RATE | QUANTITY | RATE | QUANTITY | RATE | 1. | Cement | 2.5 Kg | Rs 17/- | 2.5 Kg | Rs 17/- | 2.5 Kg | Rs 17/- | 2. | Fine aggregate | 5 Kg | Rs 10/- | 3.56 Kg | Rs 7/- | 3.56 Kg | Rs 7/- | 3. | Coarse aggregate | 7 Kg | Rs 24/- | 4.32 Kg | Rs 13 | 4.32 Kg | Rs 17/- | 4. | | Total | Rs 51/- | Total | Rs 37/- | Total | Rs 41/- |
|
|
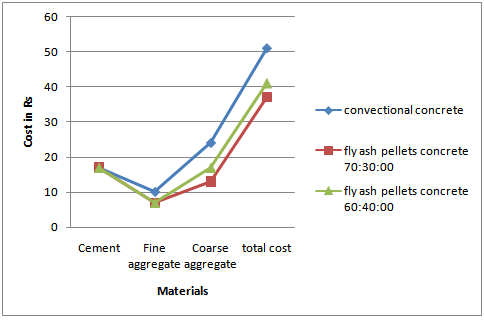 | Figure 8. Cost Analysis Graph |
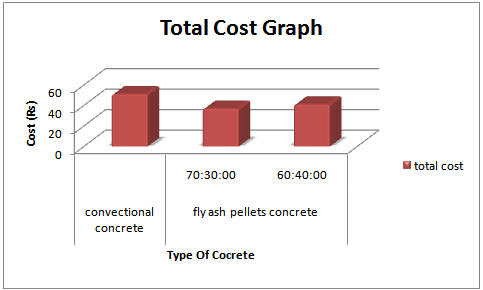 | Figure 9. Total Cost Graph |
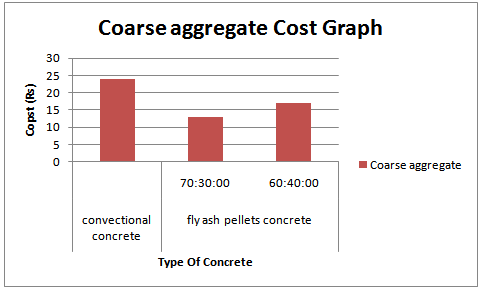 | Figure 10. Coarse aggregate Cost Graph |
♣ The above table compares the cost of conventional concrete and fly ash pellets concrete for a cube.♣ From comparison it is found the concrete from 70:30 ratio pellets shows more cost efficient i.e. nearly 27% of cost saving when compared conventional .♣ The cost efficiency is directly proportion to efficiency in manufacturing of pellets. That is if the production is 100% efficient the cost efficiency will increase to a greater extend.
7. Conclusions
The following conclusions can be drawn from the above test and analysis of the result.♣ The physical properties of the fly ash pellets which were made artificially has attained the required strength as mentioned in the code IS 456-2000.♣ The compressive of the Class F fly ash pellets concrete has surpassed the minimum strength that a M20 concrete must have.♣ The cost analysis also proved that Class F fly ash pellets is coat effective than conventional aggregate.♣ From above comparison and result it can be said that the conventional aggregate can be successfully replaced by the Class F fly ash pellets concrete. ♣ When comparing both ratios 60:40 & 70:30 can be used successfully to replace conventional aggregate.♣ We prefer 70:30 ratio pellets Since it is more economical when compared to 60:40 ratio pellets.♣ The aggregates are vital elements in concrete. The usage of enormous quantities of aggregates results in destruction of hills causing geological and environmental imbalance. The environmental impacts of extracting river sand and crushed stone aggregates become a source of increasing concern in most parts of the Country. Pollution hazards, noise, dust, blasting vibrations, loss of forests and spoiling of natural environment are the bad impacts caused due to extraction of aggregates. Landslides of weak and steep hill slopes are induced due to unplanned exploitation of rocks♣ Fly ash is also one of the hazardous environment pollutants which cannot be disposed that it is suggested that use of aggregate made from fly ash in the future.
References
[1] | M.S.Shetty. (2005). ” Concrete Technology”, S.Chand and Co Publishing Company, pp 53 to 62 |
[2] | Gokhan Banjkal, Ata Gurhan Doren. (2000). “Utilisation of fly ash by pelletization process”, application of areas and research results, resources, conservation and recycling 30 (2000), PP 59 to 77. |
[3] | IS 10262-1982 recommended guide lines for concrete mix design |
[4] | Gao Li-Xiang, Yao Yan and Wang Ling. “Research on sintered fly ash aggregate of high strength and low absorption of water”. |
[5] | Dr.S.N.Ghosh(1995) “Mineral admixtures in cement and concrete”., Akademina books International puplisher |
[6] | Rajamani N.P, Annie peter J. , Sabitha D. and Gopalakrishanan S. (2004). ” Studies on development on bonded fly ash aggregates for use as coarse aggregate in structural grade concretes” New building materials and construction world |
[7] | Rajamani N.P and Ambily P.S. (2006). ”Selection of mortar for light weight aggregate concrete made with fly ash based aggregate”, New building materials and construction world journal June 2006(pp : 80 to 88) August 2006. |