K. Kalovrektis1, Ch. Lykas2, I. Fountas1, A. Gkotsinas1, I. Lekakis3
1University of Piraeus, Informatics Department, Piraeus, Greece
2University of Thessaly / Agricultural Sciences, Volos, Greece
3University Technological Educational Institute (T.E.I.) of Piraeus /Mechanical Engineering, Athens, Greece
Correspondence to: K. Kalovrektis, University of Piraeus, Informatics Department, Piraeus, Greece.
Email: |  |
Copyright © 2012 Scientific & Academic Publishing. All Rights Reserved.
Abstract
A network of hardwired conventional sensors have been used traditionally for sensing, monitoring and control of the climate in greenhouses and fertigation of the crop. However, in recent years due to the introduction of new cultivation methods, e.g. hydroponics, the number of required sensors in greenhouse installations has increased drastically and their associated monitoring and control has become complex. In addition, the extensive wiring of the sensor network has increased the requirements for system maintenance and measurement errors. The development and application of wireless embedded sensors for monitoring and control of hydroponic systems can result in reduction of measurement errors, easy expansion of the sensor network system, reduction in the cost of system installation and its maintenance and safe data transfer. In addition, the use of embedded computer systems and appropriate software can provide flexibility and reliability in measuring and controlling the parameters of hydroponic systems at reduced cost.
Keywords:
Control, Sensor, ZigBee, Network, Embedded, Hydroponic, Irrigation, Drainage
Cite this paper: K. Kalovrektis, Ch. Lykas, I. Fountas, A. Gkotsinas, I. Lekakis, Development and Application Embedded Systems and Wireless Network of Sensors to Control of Hydroponic Greenhouses, International Journal of Agriculture and Forestry, Vol. 3 No. 5, 2013, pp. 198-202. doi: 10.5923/j.ijaf.20130305.02.
1. Introduction
The hydroponic systems, that have found a rapid development and widespread use in recent years, employ for their control a large number of sensors which are monitored continuously. This has created some new problems not previously encountered in greenhouse installations related to the required extensive hardwiring of the network of sensors, such as work restrictions inside the greenhouse, loss of precision during data transfers, difficulties in assembling, modifying and disassembling the network every time is required a change or extension of crop during the cultivation period. During these changes the system is not controlled, which may result in crop failure. The control of hydroponic systems recently is based on expert systems and artificial intelligence methodologies coupled with biophysical models that have been developed as a result of extensive research on plant physiology. The input parameters to these models are the indoor climate conditions of the greenhouse and the conditions in the culture substrate, used in the form of a continuously updated data base. The results of these models are used for controlling the indoor conditions in the greenhouse and the fertigation system. Thus, for the expert systems to operate properly becomes necessary uninterrupted monitoring of the sensors output[1]. The errors encountered in the measurements or data transfer limit the effectiveness of the expert system[2] and may lead to failure of the indoor climate and fertigation management system.To secure error free data artificial intelligence methods and neural networks (NNs) are used for the identification and evaluation of the transferred information from the sensors. This way, optimization in detecting the errors and in controlling the hydroponic system is possible by simply recording the signal outputs of sensors and actuators[3]. The objective of this work is to present a wireless accurate method of data transmission for monitoring and controlling a hydroponic system. This approach leaves the greenhouse area free from hardwires and makes the works in it much easier and cost effective. The communication between sensors, actuators and controllers, is realized in real time via wireless transmission, with the use of IEEE 802.15.4 standard which can secure data transfers by using a 11-chip (PN) Barker code.
2. Control System Analysis
The management of hydroponic systems is based on greenhouse climate control and culture fertigation, as is shown in Fig. 1. For the effective management and control of hydroponic systems continuous monitoring and recording of the following parameters is required: § the climatic parameters indoors and outdoors of the greenhouse, § the humidity and temperature levels in the substrate of the culture,§ the amount of irrigated and drained water from the crop (using Load Cells) and § the pH and Electrical Conductivity (EC) of the nutrient solution.Several of these measurements like temperature, pressure and EC are based on the resistance changes of the sensor and consequently they are strongly influenced by the resistance of the materials used for its interconnection. Especially for the EC measurements, the sensor must not be connected to a data logger or other device with a cable longer than 3m. This restricts the long distance transfer of its signal output.Based on the above, when there are changes in the climate inside the greenhouses (especially of humidity and temperature levels) or the length of connection cable becomes longer or the cables transferring the signals are damaged may result in considerable measurement errors. These errors become even larger for sensors with increased sensitivity. In addition, very often in the vicinity of greenhouses are installed distributors of high voltage current which create strong magnetic fields and result in significant attenuation and distortion of signals[4]. An important element in the implementation of a hydroponic system is the control strategy for initiating and terminating the irrigation of the crop. The initiation of the irrigation is based either on the level of pH and/or EC in the culture substrate or on a predefined required water dose. The criterion which is used to trigger initiation of irrigation changes several times during the course of a day period, depending on the dynamic conditions of the crop. Consequently in a hydroponic culture the triggering for initiating the irrigation takes place: A. When is recorded a specified percentage reduction (usually by 20%) in the water content of the culture substrate from that at its saturated state. In this case, the dose of water is that to make the culture substrate again water saturated and the frequency of irrigation changes in the course of time depending on the plants transpiration rate (Case A of Fig. 1).B. When the pH and/or the EC levels in the substrate of the culture exceed predetermined limits, irrespectively of the water content left in the substrate and therefore available to the crop. The dose of water is determined by the amount lost through plants transpiration during the last period without irrigation or until the pH and/or EC values in the substrate reach predetermined values (Case B of Fig. 1). 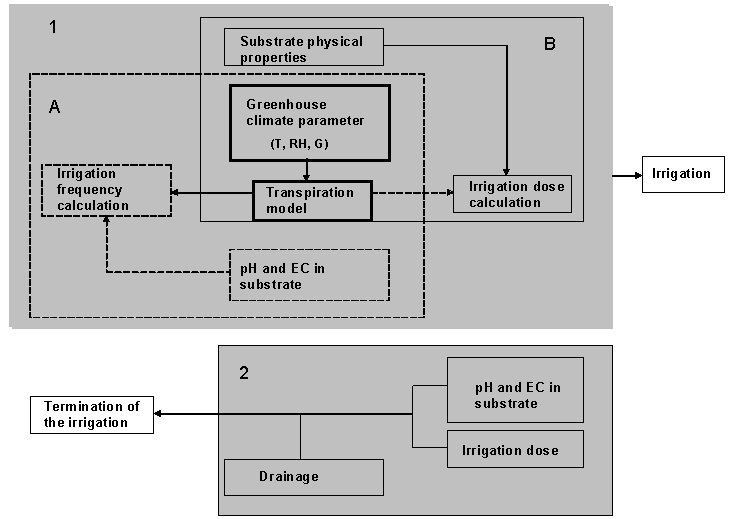 | Figure 1. Irrigation control block diagram of the hydroponic system |
The termination of the irrigation takes place when the predetermined conditions for the corresponding initiation case above were met. In all the above described cases, the correct and reliable operation of the crop facility is based on the continuous flow of accurate information.
3. Wireless Interfacing to Control a Hydroponic Greenhouse
A wireless sensor network and information control system was applied in a hydroponic cultivation of cucumbers in a greenhouse facility at the experimental farm of University of Thessaly in Volos, Greece. A plan view of the facility, shown in Fig. 2, includes a room placed approximately 70m far apart from the greenhouse in which is placed the computer for data acquisition and control. The instrumentation included a temperature sensor, an electric conductivity (EC) sensor as well as an electronic balance. The computer is interfaced through the RS-232 serial port with an embedded Full Function Device (FFD) based on ZigBee technology, which acts as coordinator of the wireless network of sensors and devices. It was estimated that if there were employed Nickel wires (ρ=7.8 10-8 Ωm) for transferring the output signals of the sensors would have resulted in a 4% amplitude attenuation of the signals at the computer input due to the wire resistance alone.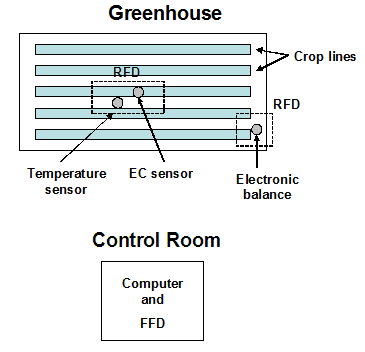 | Figure 2. Greenhouse facility with installed sensors and data acquisition control room |
For the wireless transmission of sensor signal outputs and control signals were used two embedded Reduced Function Device (RFD) units as shown in Fig. 3, which included provision to supply power to the sensors and to condition their signal outputs. One of the RFD units supports the temperature and EC sensors and the climatic controls and the other the electronic balance and the controls of the hydroponic system.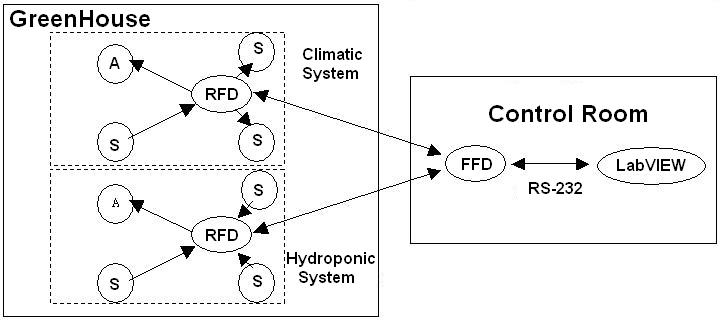 | Figure 3. Star Network Wireless Model ( Sensors (S), Actuators (A), Reduce Function Device (RFD) and Coordinator (FFD)) |
In the block diagram of Fig. 4 is shown the development integrated embedded system that supports the FFD and RFD units (only the RFD unit includes interfaces for sensor and actuators). It includes a programmable micrcontroller with stack architecture which is made up of blocks called layers: the Medium Access Control (MAC) layer, the Network Layer, the Secure layer and the Application layer which defines the application profiles in software for the sensors and the actuators to be connected.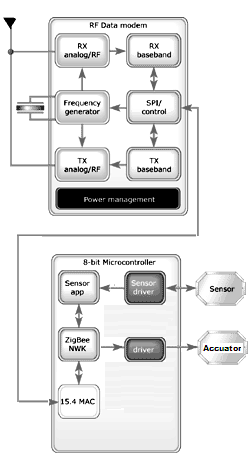 | Figure 4. Block diagram of integrated embedded system |
The software is running in the memory of a microcontroller with the support of ΙΕΕΕ 802.15.4 protocol. The ZigBee Stack defines all layers of protocol and the type of communication between them, the creation of data packets and their transmission and all other support services that are required to form a network with other devices[5],[6]. In the present study, for the handling of FFD and RFD units the PIC18LF4620 microcontroller was selected, because of it’s:§ Low power consumption § Low input voltage for operation (nanowatt Technology), § Support of synchronous and asynchronous communication gates with sensors and integrated ZigBee radio transceivers.The transmitter and receiver circuit of ZigBee signals was built on an independent board from that of the microcontroller, because this way it can support RF data modems from different manufacturers. The integrated RF modem chosen here is the CC2420, (2.4GHz) (Fig. 5), because of its special functions in handling data packets and the link quality indication. These functions reduce the operational load of the microcontroller which leads to selecting a model of smaller size and cost, that allows its use in applications with limited available space, as for some of the measurements in the present study. The communication between microcontroller and RF modem takes place through a Serial Peripheral Interface (SPI).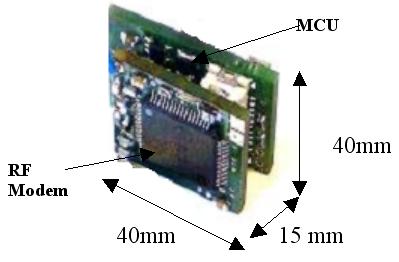 | Figure 5. RF Modem CC2420 and main board of embedded system |
The connection of the coordinator unit (FFD) of the wireless network with the maim computer is via a serial RS232 port. All control and measurement information are grouped into ASCII strings.The maximum number of measurements (N) depends on the memory capacity (M) of the data transmitting hardware system, the time response of measurements (Tr) and the sample period (Td) as expressed from eqn (1): | (1) |
where ‘a’ is the minimum memory capacity of data transmitting hardware system (256 Kb). This function can determine the maximum allowable number of inputs and outputs of the system. According the implementation code, each measurement parameter on FFD device, is coded between a constant string character in a 1D array such as shown in Fig. 6. | Figure 6. 1D array of data measurements with constant head |
All the measurements and the control in the present study were made in LabVIEW environment, Fig. 7.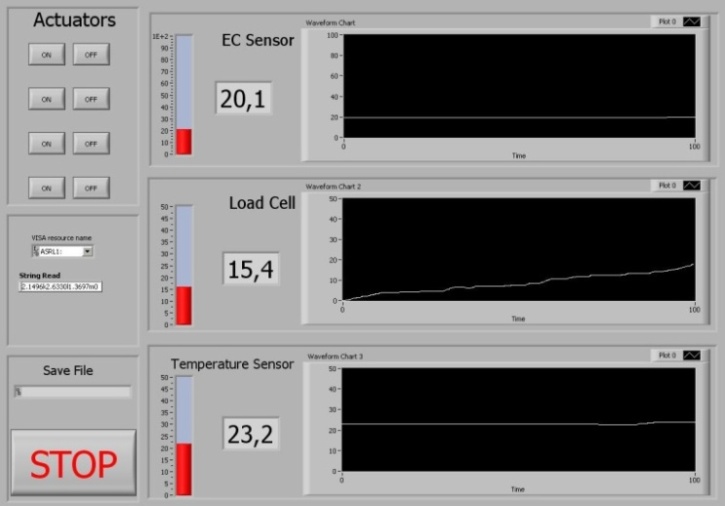 | Figure 7. LabVIEW environment of hydroponics system |
4. Results - Conclusions
The wireless sensors and information control via embedded systems and LabVIEW were employed in a hydroponic cultivation of cucumbers in a greenhouse facility at the experimental farm of University of Thessaly in Volos, Greece. The results of this study show that:A. The cost of installation of the measurement system and its interfacing, signal transmission and gathering can be reduced up to 40% when the control room is located at a distance in excess of 50m from the greenhouse.B. There was no loss of signal power and detected errors, which in the case of wired sensor networks are estimated to be approximately 4%, caused by the increased total resistance of the signal transmitting cable and the magnetic field interference.C. The measurements can be obtained using low power consumption and are clean from white noise interference that is found in wired network systems that employ intermediate signal amplifiers in transmitting the signals at large distances. D. Freeing the greenhouse from the wirings of sensor network creates a more efficient working environment and enables easy extension of the system by simply connecting additional sensors to an RDF module. E. The data transmission using 11-chip (PN) Barker code in the protocol system can be secure and reliable.Moreover the use of LabVIEW allowed quick and efficient data handling, independently from the data type, and flexibility in their processing and presentation and control of the system.
References
[1] | Nebandahl, D. 1988. Expert Systems: Introduction to the Technology and Applications, Wiley,London, 209 pp. |
[2] | Mohan, S., Arumugam, N., 1997. Expert system applications in irrigation management: an overview. Computers and Electronics in Agriculture 17:263-280 |
[3] | Ferentinos, K.P., Albright L.D., Selman B. 2003. Neural network-based detection of mechanical,sensor and biological faults in deep-trough hydroponics. Computers and Electronics in Agriculture 40: 65-85 |
[4] | Ott, H.W., Noise Reduction Techniques in Electronic Systems. New York: John Wiley & Sons, 1976. |
[5] | Kalovrektis, K., Gkotsinas, A., Glossas, N., and Assimakis, N., Communication of independent robotic grippers for safe hand-over of fragile objects, 12th International Workshop on Systems, Signals and Image Processing (IWSSIP'05), 22 – 24 September 2005 Chalkis Greece |
[6] | Zhu, Y W , Zhong, X X and Shi, J F The Design of Wireless Sensor Network System Based on ZigBee Technology for Greenhouse, International Symposium on Instrumentation Science and Technology, Journal of Physics: Conference Series 48. |