Philip Ray Pearson 1, Rachel V. Beecham 2, James Saul 3
1916 Milwaukee Avenue,Lubbock, TX 79416
2Mississippi Valley State University, Department of Natural Science, Itta Bena, Mississippi, 38941, United States
3Harry Saul Minnow Farm, Inc. De Valls Bluff, Arkansas, 72041, United States
Correspondence to: Rachel V. Beecham , Mississippi Valley State University, Department of Natural Science, Itta Bena, Mississippi, 38941, United States.
Email: |  |
Copyright © 2012 Scientific & Academic Publishing. All Rights Reserved.
Abstract
In 2008, we conducted one swimming performance and metabolism study and one transportation study on the golden shiner, Notemigonus crysoleucas. During field work for these experiments, we consulted baitfish farmers, observed harvests, and participated as workers in actual in-vat grading events. We concluded that the physically demanding in-vat grading process could be improved by mechanization, so we developed a prototype system based on existing grading panels. We constructed a gantry system to raise, lower, and pull grading panels through the length of a rectangular holding vat. Electrical power for the prototype was provided by a 12-volt marine battery. We conducted three successful fish grading events. The grading panel remained in contact with the vat floor and vat walls at all times. No fish evaded the panel by swimming under or around the panel, and all unwanted animals such as crawfish and tadpoles were captured. After one of the tests, the farm manager reviewed the graded fish, approved the grade, and immediately loaded the fish for shipment to a customer. A limited benefit-cost analysis indicated that the benefit of mechanization during the first year of operation was approximately US$8,600. The golden shiner Notemigonus crysoleucas is cultured for use as live bait by anglers. Golden shiners are harvested from ponds containing a mixed-size population, and are placed in rectangular holding vats, where they are sorted into specified weight categories. Workers on Arkansas baitfish farms typically sort golden shiners by physically pulling rectangular panels comprised of a set of uniformly spaced vertical rods through a vat holding as much as 400 pounds of fish. We developed and tested a device that replaces physical effort with machine power to accomplish the grading process.
Keywords:
Golden Shiner, Grading, Baitfish, Harvesting
Cite this paper:
Philip Ray Pearson , Rachel V. Beecham , James Saul , "A Mechanized Panel Grading System for the Golden Shiner: Proof of Concept", International Journal of Agriculture and Forestry, Vol. 2 No. 6, 2012, pp. 311-314. doi: 10.5923/j.ijaf.20120206.08.
1. Introduction
An aluminium frame fitted with uniformly spaced rods or bars (Figure 1) is typical of bar graders used to sort a mixed population of the golden shiner Notemigonus crysoleucas into more homogeneous groupings. Since there is no industry standard for holding vat dimensions, grading panels are custom fitted to a given set of holding vats (1). The 71 x 30 in panel shown in Figure 1 is designed to fit a rectangular concrete holding vat having inside width of 72 in. The flexible material attached to each end of the grader fills the space between the ends of the panel and the vat wall. Workers use the attached ropes to pull the panel through the length of a vat that may hold up to 400 lb of golden shiners. The number 16 on the panel indicates that the space between each bar is 16/64th in. This grading panel will separate fish having mean weight ≥ 6 lb per 1,000 fish from a mixed-size population. (1, 2).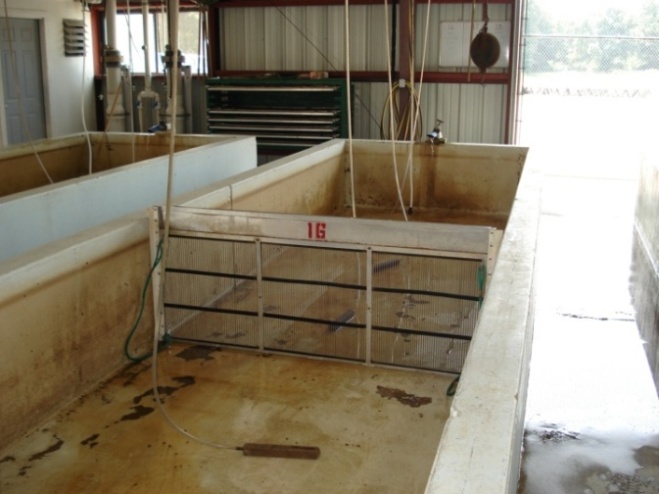 | Figure 1. A grading panel designed for use in a rectangular concrete holding vat. Uniformly spaced rods prevent golden shiners Notemigonus crysoleucas having cross-section greater than 16/64 in from swimming through. Flexible strips attached to each end prevent fish from swimming around the panel. Workers use the ropes to pull the panel through a vat containing up to 400 lb of fish |
To the casual observer, the act of ‘pulling a grader’ appears to be just that. Subtle nuances become apparent, however, when one actively participates in the grading process. When using a panel of the type shown in Figure 1, each of the two workers must exert downward force on the top of the panel, while pulling the panel through the vat. At the same time, each worker must be aware of the position of the panel with respect to the vat walls. If inadequate downward force is applied, then contact between the panel and the vat floor may be lost, and fish can evade the grading bars by swimming under the panel. If the sealer strips lose contact with the vat walls, then fish can evade the grading bars by swimming around the ends of the panel. (6,7)Because mechanization of the in-vat grading process is possible, we established criteria for a prototype. We envisioned a self-propelled, wheeled device (similar to a gantry crane) that rolled along the tops of the vat walls. The apparatus must be compatible with existing grading panels, and should eliminate the need for workers to pull panels through the vats. Review of scientific literature revealed no examples of a device of this type, so we developed a proof of concept for a mechanical grading system.
2. Methods
We conducted an informal survey of holding vat sizes during visits to a number of Arkansas baitfish farms and found no standardization of vat dimensions. Development of a 'one-size-fits-all' device was impractical, so we decided to tailor specifications for the prototype to vats on one farm. The owners of Harry Saul Minnow Farm, Inc., De Valls Bluff, Arkansas, allowed us to work in their holding and grading facility (5). Rectangular concrete vats at the Saul farm have 6.5 in wall thickness, an inside width of 6 ft and length of 38 ft. Depth of each vat varies from 28 in at the shallow end to 30 in at the deep end. We assembled a towing cart from a heavy-duty, wheeled utility cart, a 12 volt DC (VDC) sealed marine battery, and an all terrain vehicle (ATV) winch. On each test, we placed the cart against the vat wall at the outlet or deep end of a given vat, and winched the device through the length of the vat.We field tested four versions of the mechanized grader under a pass-fail evaluation criterion. A successful design would keep the sealer strips in contact with the vat walls and keep the bottom edge of that panel in constant contact with the vat floor. We conducted one test in a dry vat, two tests in vats containing water, but no fish, and three actual fish grading events,.
3. Results and Discussion
Design of the prototype was an iterative process. The Mark I was comprised of a light-weight, wheeled framework that used clamps to hold the grading panel. An in-vat test showed that the 14-in wheel base was inadequate and that the light weight frame provided insufficient mass to resist the tipping force caused by movement through the vat. The clamps did not adequately secure the grading panel, and the 3-in wheels were unsatisfactory. 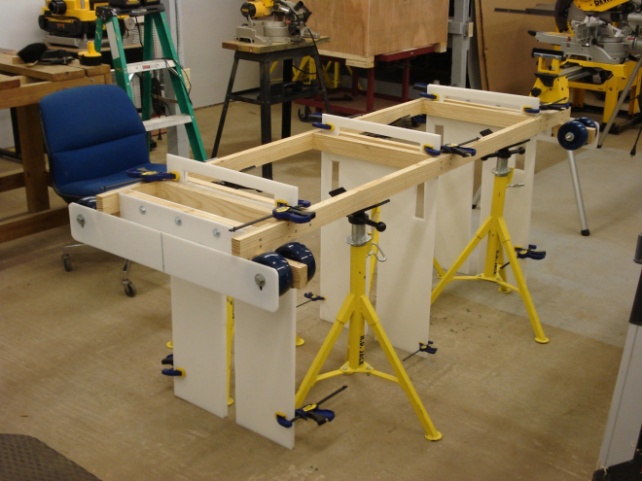 | Figure 2. The Mark II prototype tested guide strips (rectangular high density polyethylene (HDPE) pieces bolted to each end), polyurethane wheels (5-in diameter x 2-in width), and panel holding devices (large, slotted panels of HDPE) |
The Mark II (Figure 2) was constructed from wood and high density polyethylene (HDPE). We increased the wheel base to 21 in, replaced the 3-in. diameter nylon wheels with polyurethane wheels having 5-in diameter and 2-in width, and fabricated guide strips and a set of panel holders from sheets of HDPE. A limited test of the Mark II in a dry vat revealed that the panel holders were poorly designed, and that the guide strips did not keep the wheels on the tops of the vat walls.The Mark III (Figure 3) used the I-frame design of the Mark I, but included a u-shaped push bar that extended to within 2 in of the floor at the shallow end of the vat. We used 8-in extruded aluminium channel for the cross-bar and constructed push bar supports from extruded aluminium angle and aluminium plate cut in the shape of Isosceles triangles (Figure 4). We used the 21-in wheel base and 5-in diameter x 2 in wide polyurethane wheels from the Mark II, and replaced the guide strips with horizontal stabilizer wheels. 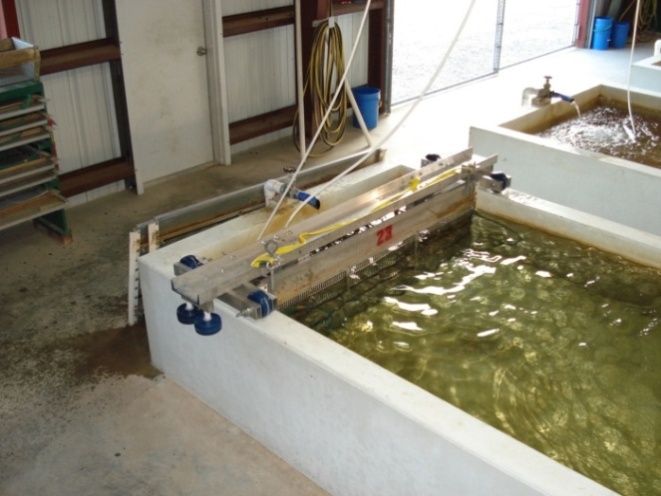 | Figure 3. The Mark III was the first version constructed from extruded aluminum components. The 5-in x 2-in polyurethane wheels tested on the Mark II proved satisfactory for use on the tops of the vat walls and as horizontal stabilizers |
 | Figure 4. Supports designed for the push bar on the Mark III. The supports were comprised of extruded aluminum angle and 0.125 in thick aluminum Isosceles triangles. These supports were also used to reinforce the draw works on the Mark IV prototype. The design shown in this figure is complex and assembly is time consuming. The authors suggest that individual builders substitute a simpler design of their choice |
We tested the Mark III in a vat filled with water, and then graded a mixed population of fish. The grading panel stood upright and the flexible sealer strips remained in contact with the vat walls. The bottom edge of the panel remained in constant contact with the vat floor, and no fish swam under the panel. The farm manager approved the grade, and the fish were immediately loaded on a transport truck for delivery to a customer. In spite of its excellent performance, we rejected the Mark III because of a fatal design flaw. The fixed push bar made the device unwieldy, and in our opinion, created a potential safety hazard. The Mark IV (Figures 5 and 6) was the final version of the prototype grading system. We made extensive use of 8-in extruded aluminium, increased the wheel base to 41 in, and added a draw works and a 12VDC hoist to raise and lower a simplified push bar. The push bar supports for the Mark III were too complex, so we used 8-in channel for the Mark IV (Figure 7). Our fastener of choice was the 0.5-in x 13 thread stainless steel hex head bolt.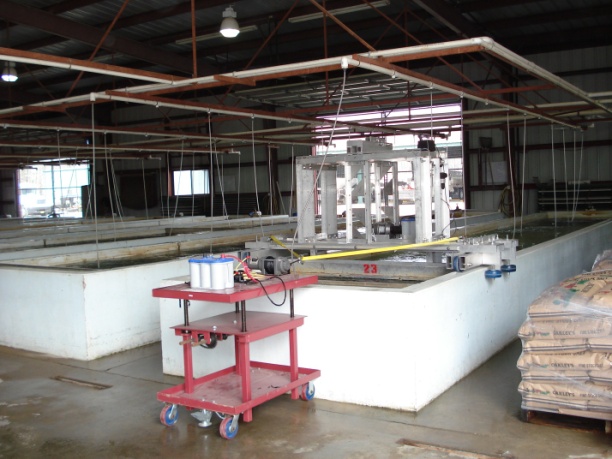 | Figure 5. The Mark IV (proof of concept) |
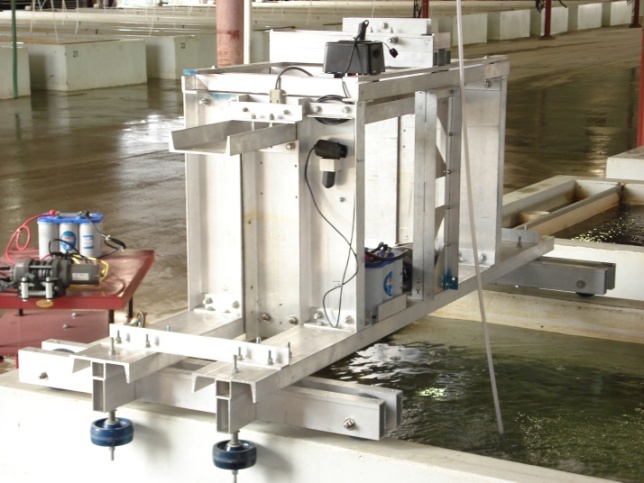 | Figure 6. Oblique view of the Mark IV showing stabilizer wheels and the limit switch (the small box at the top of the draw works). The columns reinforcing the draw works were components used in the Mark III. Please see Figure 6 |
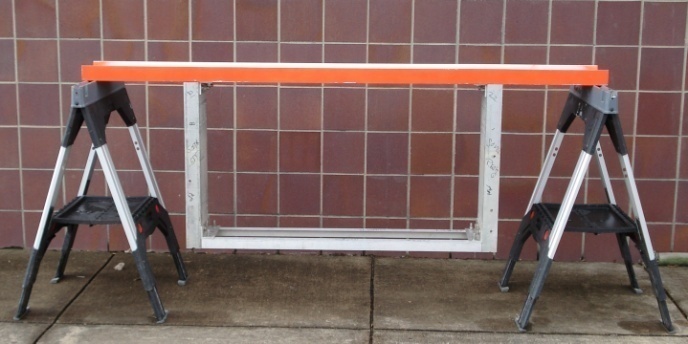 | Figure 7. The simplified u-shaped push bar designed for the Mark IV. The push bar supports and the bridge are 8-in extruded aluminum channel. The push bar and flanges are 2 x 2 x 0.25 in extruded aluminum angle |
After damaging the draw works during a test, we installed a limit switch (Figure 6) to cut power to the hoist at a specified height. We used the supports from the Mark III push bar (Figure 4) to support the Mark IV draw works (Figures 5 and 6) during the field test, but we believe that a simpler design (of the builder's choice) would be more cost effective.We tested the Mark IV by grading and crowding two vats of fish at Harry Saul Minnow Farm, Inc. The panel remained in contact with the vat floor at all times, the vat floor behind the panel was swept clean, no fish swam under or around the panels, and unwanted animals such as crawfish and tadpoles were crowded at the deep end of the vat. The Mark IV weighs approximately 425 lb, and its cost at the time of development was US$4,800 (Table 1). We performed a limited benefit-cost analysis in which we assumed that mechanization of the grading process with one Panel Pusher allowed a farmer to reduce labor needs by one farm worker. At a hypothetical baitfish farm, payroll expense for one worker was $14,600 (2,080 h/year at the federal minimum wage of US$6.55/h (3) plus Social Security taxes of 7.65% on gross wages (4)). Contrast of payroll expense to the cost of the mechanical grading system (US$5,000) and an arbitrary estimate of operating expense (US$1,000), indicated that the benefit of mechanization during the first year of operation was approximately US$8,600. Table 1. Bill of Materials for the Prototype of a Mechanical Device Designed to Push Bar Graders Through Rectangular Concrete Vats 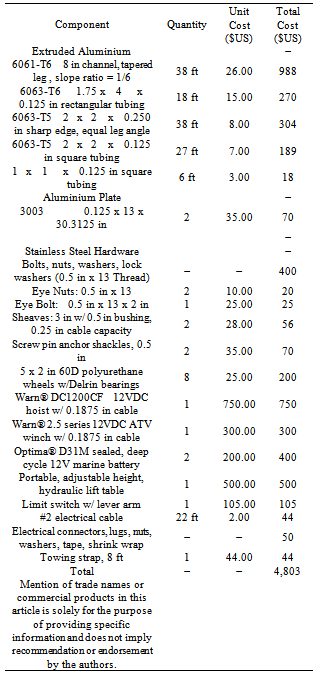 |
| |
|
4. Conclusions
The field work we conducted on a working baitfish farm provided us with practical experience and valuable insights into technical aspects of golden shiner culture. We learned that “pulling a grader” is physically demanding and the task also requires mental alertness. We were convinced that the task could be mechanized, so we developed our prototype. The prototype discussed in this paper was successfully tested on three actual grading events. It was most gratifying when the farm manager reviewed our work, approved the grade, and sent our graded golden shiners to a customer. Our limited or informal benefit-cost analysis indicated a benefit of approximately US$8,600, which was caused by reducing labor need by one worker. Due to differences in holding vats, equipment, and farming philosophy among baitfish farmers, we have presented a proof of concept, not a panacea. We are certain that an interested aquaculturist can improve upon our efforts.
ACKNOWLEGEMENTS
The author thanks James, Margie, and William Saul of Harry Saul Minnow Farm, Inc. for allowing us to work on their farm, and to George Huskey, Jr. for his invaluable assistance during the construction and testing of the mechanized grading system.
References
[1] | Jensen, G.L. 1990. Sorting and grading warmwater fish. Southern Regional Aquaculture Center. SRAC publication no. 391. June. |
[2] | Dorman, L. 1991. Grader spacing and length-weight relationship for commercially reared fish. Arkansas Aquafarming 9:2. April-June. |
[3] | USDL. 2009. United States Department of Labor, Employment Standards Administration, Wage and Hour Division. Minimum Wage.http://www.dol.gov/esa.whd/minimumwage.htm. Accessed on April 02, 2009. |
[4] | SSA 2009. Social Security Administration. fact sheet: 2009 social security changes. SSA Press Office, Baltimore, Maryland, 21235. |
[5] | Saul, James. 2008. Personal interviews and consultation. January-December. |
[6] | Pearson, P.R., B.C. Small, R.V. Beecham, T.D. Sink, S.B. LaBarre, and C.D. Minchew. 2009. Effects of loading density on golden shiner survival during and after hauling. North American Journal of Aquaculture. 71(1): 24-29. |
[7] | Beecham, R.V., P.R. Pearson, S.B. LaBarre, C.D, Minchew. 2009. Swimming performance and metabolism of golden shiners. North American Journal of Aquaculture. 71(1): 59-63. |