Md. Rokonuzzaman, Md. Abdullah Al Mamun, A. K. M. Ayatullah Hosne Asif
Department of Textile Engineering, Mawlana Bhashani Science and Technology University, Tangail, Bangladesh
Correspondence to: A. K. M. Ayatullah Hosne Asif, Department of Textile Engineering, Mawlana Bhashani Science and Technology University, Tangail, Bangladesh.
Email: |  |
Copyright © 2017 Scientific & Academic Publishing. All Rights Reserved.
This work is licensed under the Creative Commons Attribution International License (CC BY).
http://creativecommons.org/licenses/by/4.0/

Abstract
In order to study the effects of heat setting conditions on the properties of 100% cotton yarn, 30/1 Ne combed ring yarn cones were heat setting in a XORELLA CONTEXXOR (yarn conditioning and steaming system). The quality parameters such as unevenness (Um% and CVm%), imperfections/km (thick places/km, thin places/km and neps/km), yarn hairiness, yarn strength (count strength product), moisture% and yarn cone weight were measured before heat setting and after heat setting (after 2 hours, 8 hours, 16 hours and 24 hours of heat setting) by using Uster evenness tester, yarn strength tester, moisture regain tester and electronics balance. Yarn quality was deteriorated after 2 hours, 8 hours, 16 hours and 24 hours of heat setting compared to before heat setting yarn. But count strength product, moisture% and yarn cone weight was found satisfactory level after 2 hours, 8 hours, 16 hours and 24 hours of heat setting compared to before heat setting yarn. As a result finished yarn should be delivered to the knitting and woven industry after 8 hours of heat setting due to better yarn quality.
Keywords:
Heat setting, Yarn cone, Cotton yarn, Unevenness, Yarn strength
Cite this paper: Md. Rokonuzzaman, Md. Abdullah Al Mamun, A. K. M. Ayatullah Hosne Asif, Effect of Heat Setting Conditions on the Quality of Yarn, Frontiers in Science, Vol. 7 No. 3, 2017, pp. 46-49. doi: 10.5923/j.fs.20170703.03.
1. Introduction
Upto 20% greater efficiency due to a reduction in the unwinding tension, fewer needle breaks, uniform moisture content and friction values, regular stitch formation, no change in size of finished articles, no extra dampening required, free from electrostatic, less fly hence less problem are the benefits achieved for knitting, upto 15% fewer yarn breaks due to greater elongation, less fly resulting in a better weaving quality, increased strength, increased take-up of size, enhanced level of efficiency in the weaving plant, softer fabrics get in weaving, conditioning and fixing of the twist at the same time in a single process for twisting, no streaks and better dye affinity get in dyeing from XORELLA yarn conditioning and steaming system [1].Moisture in the atmosphere has a great impact on the physical properties of textile fibres and yarns. The amount of moisture in textile materials depend on relative humidity and temperature. High relative humidity in different departments of spinning result in major problems. But on the other hand, a high degree of moisture improves the physical properties of yarn. Moreover it helps the yarn to attain the standard moisture regain of the fibre. Yarns with lower moisture content than the standard value cause economically loss in sale. Therefore, conditioning and heat-set is to provide an economical device for supplying the necessary moisture in a short time [2]. Kinking and snarling during the unwinding process lead to yarn breaks and loss of quality. Relaxing with steam increases efficiency in all subsequent operations, such as winding, twisting, warping, weaving and knitting. Yarn with high twist multiples, core yarn and also synthetic filaments require heat setting to stabilize the torque. With the XORELLA steaming process the yarn get even treatment throughout all layers. Perfect sterilization during process can be guaranteed only if clean saturated steam (100% controlled vaccum and temperature), free from any air, arrives at and penetrates all the material being sterilized (no mildew, no discoloration of the material) [3]. Twisting, spinning, weaving, knitting etc. manufacturing process causes tension in fiber and yarns. Yarns tend to kink and snarl in order to relax themselves and get rid of this tension. Tension, kinking and snarling are likely to lead to problems in the following manufacturing processes [4]. To relax yarns, to prevent them from snarling, to enable them to be worked efficiently in the following processes and to fix yarn-twisting are the objectives of conditioning and heat-setting (twist-setting). Recently, conditioning and heat setting operate under vacuum with saturated steam which can eliminate the downsides of the conventional systems. Yarns are conditioned or heat-set with saturated steam under vacuum with the aid of steaming in these systems [5]. A treatment with steam under vacuum in heat setting process improves efficiency and quality in weaving and knitting plants by reducing yarn tension, softening yarns, moisturizing them homogenously, eliminating electrostatic effects and reducing fly and dust [6]. Unset yarns squeeze bobbins get deformed during dyeing with a pressure from the outside section towards the inside section. The yarn bobbins get less deformed by using higher temperature of heat setting [7]. Skewness increases in weaving due to improper heat setting, a situation in which warp and weft yarns cannot be tied together with a right angle, although they are straight [8] and it increases diagonal run in knitwear [9].
2. Materials and Method
In this study 30/1 Ne combed of 100% cotton ring yarn was used. TPI was 19.58 in 30/1 Ne. Cotton fibre fineness and staple length were 4.7 (micronaire) and 28.9 mm respectively. Yarns were wound onto packages with a Schlafhorst Autoconer 338 machine at the delivery speed of 15500 metre/min. Then 5 packages of yarn cones with assign mark were taken to quality control department for measuring actual count, Um%, CVm%, thin places (-50%)/km, thick places (+50%)/km, neps (+200%)/km, Imperfections/km, hairiness, CSP (Count Strength Product), moisture% and cone weight. After that these 5 packages of yarns with other yarn packages were subjected to heat setting under -1 bar pressure and at temperature of 60°C for 40 min. with a machine working in compliance with the direct vacuum steaming system of the XORELLA AG (Switzerland) Company. After completion heat setting, 5 packages of yarn cones with assign mark were again taken to quality control department and kept them for 2 hours, 8 hours, 16 hours, 24 hours at temperature of 27±2 °C and relative humidity of 65±2%. After that actual count, Um%, CVm%, thin places (-50%)/km, thick places (+50%)/km, neps (+200%)/km, Imperfections/km, hairiness, CSP (Count Strength Product), moisture% and yarn cone weight were measured for each mentioned time separately. Uster evenness tester was used for the measurement of Um%, CVm%, thin places (-50%)/km, thick places (+50%)/km, neps (+200%)/km, Imperfections/km, hairiness. Moisture% was measured by using moisture regain tester. Electronic balance was used for taking yarn cone weight.Yarn count: Yarn count was tested by Uster autosorter-III linked with computer system, which gives direct result. A lea of 120 yards was fed to the computer to determine English count according to its operational manual recommended by ASTM [10]. Yarn lea strength: Pendulum type lea strength tester was used to determine the lea strength in pounds. The lea of 120 yards was fed to the instrument according to the method recommended by ASTM [10].Count lea strength product: Count lea strength product was determined by multiplying the actual count value with respective breaking load of yarn lea of 120 yards according to British Standards [11].
3. Results and Discussion
3.1. Effect of heat setting on actual yarn count, Um% and CVm%
Table 1. Test result of Actual count, Um% and CVm% of before heat setting and after heat setting yarn 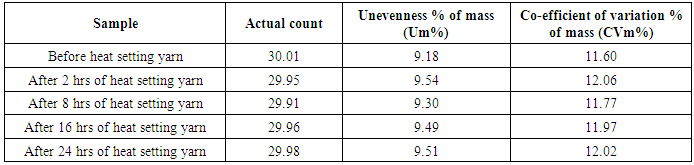 |
| |
|
From table 1, it was observed that there is no significant effect of heat setting on yarn count. Um% and CVm% increased after 2 hours, 8 hours, 16 hours and 24 hours of heat setting.
3.2. Effect of Heat Setting on Imperfections/km
Imperfections/km = [Thin places (-50%)/km + Thick places (+50%)/km + Neps (+200%)/km] (For ring yarn).Table 2. Test result of Imperfections/km of before heat setting and after heat setting yarn 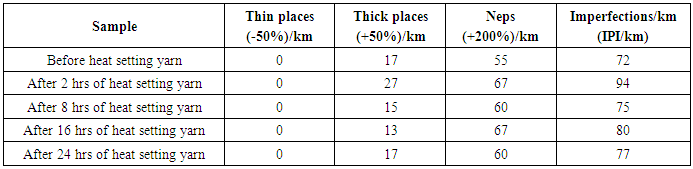 |
| |
|
Imperfections/km in yarn increased after heat setting compared to before heat setting yarn due to moisture absorption which was found in table 2. From table 2, it was also observed that after 8 hours of heat setting imperfections/km in yarn found more or less equal to before heat setting yarn.
3.3. Effect of Heat Setting on Yarn Hairiness and Yarn Strength (CSP)
Table 3. Test result of yarn hairiness and count strength product of before heat setting and after heat setting yarn 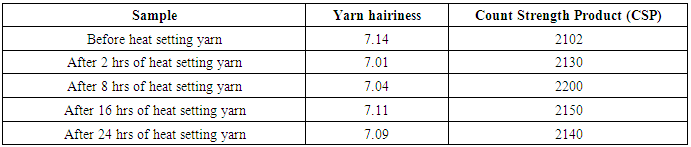 |
| |
|
From table 3, it was observed that there is no significant effect of heat setting on yarn hairiness. Yarn hairiness found more or less same for both before heat setting and after heat setting yarn. Yarn strength increased in yarn after heat setting compared to before heat setting yarn due to moisture absorption. The general effect of water molecules in the fibre is to reduce the strength of the fibre but in case of vegetable fibres such as cotton and flax, strength is increased. More CSP found after 8 hrs of heat setting yarn compared to before heat setting yarn and after 2 hrs, 16 hrs, and 24 hrs of heat setting yarn.
3.4. Effect of Heat Setting on Moisture% and Cone Weight
Table 4. Test result of moisture% and yarn cone weight of before heat setting and after heat setting yarn 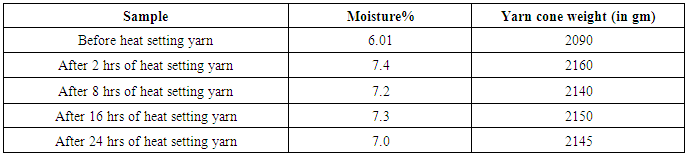 |
| |
|
From table 4, it was observed that moisture% and cone weight found more in case of heat setting yarn compared to before heat setting yarn. Yarns with lower moisture content than the standard value cause economically loss in sale. Therefore, conditioning and heat-set is to provide an economical device for supplying the necessary moisture in a short time [2].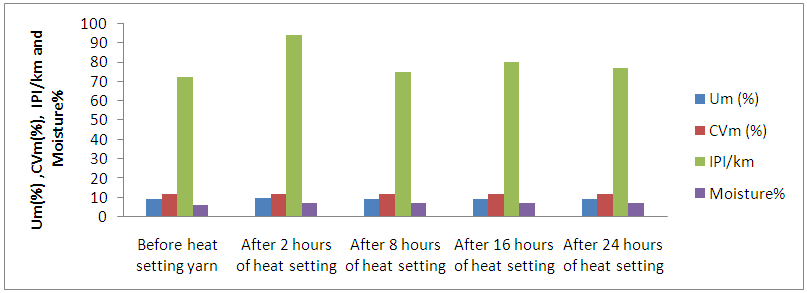 | Figure 1. Effect of heat setting on Um(%), CVm(%), IPI/km and Moisture% |
From figure 1, it was observed that Um(%), CVm(%), IPI/km and moisture% in the yarn increased due to heat setting compared to before heat setting yarn.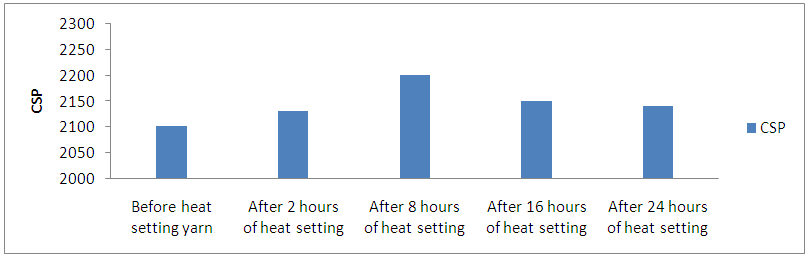 | Figure 2. Effect of heat setting on Count Strength Product (CSP) |
Count Strength Product (CSP) found more after 8 hours of heat setting yarn compared to before heat setting yarn, after 2 hours, 16 hours and 24 hours of heat setting yarn which was observed in figure 2.
4. Conclusions
In this study, count strength product, moisture% and yarn cone weight of 30/1 Ne combed yarn was found satisfactory level due to heat setting compared to before heat setting yarn. The count strength product, moisture% and cone weight of the yarns increased after 8 hours of heat setting compared to after heat setting of 2 hours, 16 hours and 24 hours. Um%, CVm% and imperfections/km of yarn was deteriorated after heat setting compared to before heat setting of yarn. As a result of these, the yarn is likely to show better performance after 8 hours of heat setting in the subsequent processes such as weaving, knitting and dyeing.
ACKNOWLEDGMENTS
The author wish to thank the authorities of Youth spinning mills Ltd., Gorai, Mirzapur, Tangail for the opportunities they have provided to conduct this study in the factory.
References
[1] | www.geocities.com/vijayakumar777/yarnconditioning.html, (2009). |
[2] | Ozdemir O., Şardağ S. (June 2004), Yarn Conditioning and New Methods, Textile & Technique, Turkey, pp. 248-260. |
[3] | www.xorella.ch |
[4] | www.welker.de/html/englisch/ heatsetting.html. (2004). |
[5] | Toggweiler P., Gleich S., Wanger F. (1995). Improved Quality With The Contexxor Conditioned Yarn, Meiland English, No. 9 pp. 154-155. |
[6] | Xorella catalogue (2003). |
[7] | Xorella Contexxor (2003), The Innovative Conditioning and Steming System, catalogue. |
[8] | Yazdi A. A., Woven Fabric Skewness and Yarn Twist. (April, 2004), Proceedings of 2nd International Istanbul Textile Congress, pp.1-7. |
[9] | Artzt P. (April, 2004). The Influence of Different Spinning Processes on The Structure and Properties of Yarns, Proceedings of 2nd International Istanbul Textile Congress, pp.1-8. |
[10] | ASTM Committee (1997). Standard Test method for Yarn number, lea strength, ASTM Designation: D 1907-97, D-1425-96. ASTM Standard on Textile Material Amr. Soc. For Test and Mater., Philadelphia, USA. |
[11] | British Standards (1985). Determination of lea strength lea count of spun yarn. Methods of Test for Textiles, B.S. Handbook II British Inst., London pp: 141-142. |