M. Marouf Wani
Mechanical Engineering Department, National Institute of Technology, J&K, Srinagar, India
Correspondence to: M. Marouf Wani, Mechanical Engineering Department, National Institute of Technology, J&K, Srinagar, India.
Email: |  |
Copyright © 2021 The Author(s). Published by Scientific & Academic Publishing.
This work is licensed under the Creative Commons Attribution International License (CC BY).
http://creativecommons.org/licenses/by/4.0/

Abstract
This paper presents the possible design of a zero carbon emission hydrogen engine based on its octane demand. The result investigations were done on a turbocharged four stroke four cylinder spark ignition engine using hydrogen as its fuel supplied with the help of a carburetor. The professional, thermodynamic, internal combustion engines simulation software AVL BOOST was used during analysis and synthesis of the engine design. The Software uses the basic conservation equations of mass, energy and momentum along with the numerical finite volume method. The laws of thermodynamics and gas dynamics were used to compute the values of various thermodynamic and gas dynamic variables in all engine components. The software has provision for designing the model using basic elements. It allows selection and use of suitable combustion model, heat transfer model, model for the frictional power, etc. The modeled engine was run in the hydrogen mode by varying its engine speed, air-fuel ratio, compression ratio and start of combustion one by one. It was observed that the octane demand of the hydrogen engine varies for each of these design and operating variables under consideration. It was observed that higher engine speeds and lower compression ratio suit the design of this type of engine. Further the richer mixture, otherwise suitable for maximizing power, and an optimum spark timing range suits the selection of hydrogen as a fuel for internal combustion engine.
Keywords:
Octane Demand, Engine Design, Internal Combustion, Four Stroke Cycle, Spark Ignition, Hydrogen, Zero Carbon Emission
Cite this paper: M. Marouf Wani, Thermodynamic Investigations on the Design of a Spark Ignition Hydrogen Operated Engine, Energy and Power, Vol. 11 No. 1, 2021, pp. 20-25. doi: 10.5923/j.ep.20211101.02.
1. Introduction
Hydrogen is also under considered as an alternative source of energy to gasoline in passenger car applications operating with spark ignition. The use of hydrogen fuel in the internal combustion engines results in the drop of CO and HC emissions to zero level. The high heating value and high RON for hydrogen contributes towards its suitability as a source of energy for internal combustion engines. However its use as a gaseous fuel results in a drop in the volumetric efficiency of the engine. For Hydrogen Fuel the stoichiometric equation isH2 + ½(O2 + 3.773N2) = H2O + 1.887N2and the stoichiometric (A/F) ratio is 34.3.For stoichiometric hydrogen-oxygen mixture no reaction occurs below 400C unless the mixture is ignited by an external source such as a spark; above 600C explosion occurs spontaneously at all pressures. [1]There is some possibility of some minimum HC emissions resulting because of the circulation of the lubricating oil to the combustion chamber walls. The octane number of the hydrogen will decide the selection and computation of the design and operating parameters of the hydrogen engine. [2,3]Shuofeng Wang et. al., conducted experimental investigations on combustion of a hydrogen-blended gasoline engine at high loads and lean conditions. The results showed that the addition of hydrogen was able to reduce the cyclic variation in indicated mean effective pressure. Moreover, the fuel heat release rate and peak cylinder pressure were accelerated after the hydrogen addition. Both HC and CO emissions were reduced significantly after the hydrogen blending. NOx emissions were slightly increased after the hydrogen addition due to the high flame temperature of hydrogen. [4]Choongsik Bae, Jaeheun Kim compared the possible use of various alternative fuels for both the spark ignition engines and compression ignition engines. He found that till 2040, internal combustion engines only will be the main prime movers for about 90% of the transportation sector. It was found that the demand for transportation fuels will grow continuously at the rate of 1.2% to 1.4% annually. Hydrogen is widely used as the fuel for combustion in industries and aerospace field due to its high energy density, high flame speed, and wide flammability limits. There is also a scope for its use in the transportation sector. Hydrogen can be used from conventional to advanced combustion concepts. Hydrogen can be produced from fossil resources, such as natural gas and coal, as well as renewable resources, such as biomass. Hydrogen can also be produced through electrolysis of water with solar generated electricity in terms of CO2 emission reduction. However this type of production scale is very small currently. Today, more than 90% of the hydrogen produced is derived from fossil fuels, including natural gas, oil and coal, via a steam reforming process. The high octane number of hydrogen provides the opportunity to increase the compression ratio to increase the engine efficiency. Its wide flammability limits also enable un-throttled operation with lean combustion. The high laminar flame speed, an order of magnitude higher than hydrocarbons, is a distinct combustion characteristic of H2. The laminar flame speed is about 1.85 m/s for H2, while the speed for hydrocarbon fuels range from 0.3 to 0.5 m/s. Therefore, a PFI engine operating with H2 has a higher thermal efficiency over the conventional gasoline fueled engine, due to the availability of lean un-throttled operation, high flame speed, and potential for higher compression ratio. However, attentions should be paid on the possibility of greater heat transfer losses through the cylinder wall with H2 fueled engines. The auto-ignition temperature of H2 is 858 K, which is higher than that of gasoline fuel (around 550 K). However the minimum ignition energy of hydrogen is 0.02 mJ (while that for equivalent gasoline–air mixture is 0.24 mJ) and may cause backfire and pre-ignition, which are critical issues for H2 fueled engines. H2 combustion does not produce carbon related emissions, such as CO, CO2 and PM, due to the absence of C atoms. However, note the carbon footprint if carbon based feed stocks are used to produce H2. NOx is the only non-trivial engine out emission pollutant. There are some available approaches to reduce NOx emissions. The first approach is to adopt an ultra lean combustion with an equivalence ratio ( ϕ) lower than 0.45, in order to reduce the peak combustion temperature; however, this limits available engine torque. The low energy density on a volumetric basis also hinders the maximum torque characteristics. Another approach is to install an after treatment downstream of the engine. A lean NOx trap (LNT) would be needed when operating at a moderately lean condition with equivalence ratio below 1 at higher cost; while a lower cost TWC is required when operating at stoichiometric conditions. However, research on the prevention of abnormal combustion, such as pre-ignition, needs to be resolved, prior to operation under the stoichiometric condition. [5]Gharehghani et. al., conducted computational investigations on the effect of hydrogen enrichment on the engine operating range and combustion Characteristics by using a validated multi-dimensional CFD model coupled with detailed chemical kinetics mechanism. The results indicated that misfiring occurs in equivalence ratios of about 0.61, 0.48 and 0.42 for hydrogen fractions of 0%, 30% and 50% respectively. It was found that hydrogen fraction decreased the emissions of CO, and HC and CO2. Adding 30% hydrogen reduced CO2 emission by 10.2% while 50% hydrogen fraction led to 22.7% CO2 reduction. [6]Baris Acikgoz a et. al., conducted experimental investigations on a two cylinder, four stroke, spark-ignition engine with methane-hydrogen blends in port fuel injection mode. The results showed that at low engine speed the brake specific fuel consumption increased by increasing the percentage of hydrogen in fuel blends. However the BSFC was decreased by increasing the percentage of hydrogen at high engine speeds. The brake thermal efficiency decreased by increasing the percentage of hydrogen. The CO2, NOx and HC emissions were decreased whereas the CO emission was increased by adding more percentage of hydrogen. [7]H. An et. al., used KIVA4 coupled with CHEMKIN TO simulate the performance, combustion and emission characteristics of a hydrogen assisted diesel engine under various operating conditions. The results were validated against the experimental results with 0% of hydrogen induction. At low engine speeds the induction of hydrogen increased the indicated thermal efficiency, in-cylinder pressure and apparent heat release rate significantly. At high engine speed and high load conditions, no tangible changes on the engine performance, combustion characteristics were observed. The CO and soot emissions were reduced under most of the engine operating conditions. However the NOx emissions showed a slight increase at low engine speed of 1600 rpm. [8] B Nagalingam et.al., conducted research investigations on an AVL stationery type research engine with hydrogen as its fuel. The aim was to investigate the percentage gain in output and thermal efficiency, knock limited combustion air ratios, NO emission and combustion characteristics at different supercharging pressures. It was observed that as compared to the naturally aspirated engine, the output of the supercharged engine increases as much as 233%, the thermal efficiency increased by 29% at the combustion air ratio of 2.0 and speed of 1200rpm. The NO emissions increased in case of supercharged engine. The Knock limits were leaner with supercharged version as compared to the naturally aspirated version engine. It was further observed that in case of the supercharged engine, the spark plug gap was to be reduced and the ignition system needed to be better insulated to avoid ignition failure. [9]Kim J. et.al., Conducted experimental investigations on a direct injection spark ignition engine fuelled with hydrogen to optimize injection hole configuration and injection timing. It was observed that the qualitative trend of the hydrogen engine was similar to that of the gasoline engine in terms of spark timing, air-fuel equivalence ratio and engine speed. However the magnitudes with the parameters considered were different for the two types of engines. [10]Teruo Suzuki et.al., conducted experimental investigations on a commercial spark ignition direct injection gasoline engine with gasoline, pure hydrogen and reformer gas (H2,CO,CO2 and CH4). The engine was first modified to a manifold injection system type of engine using the injection system of a CNG vehicle. This type of engine design also made it possible to run the engine both in a homogeneous charge and stratified charge mode. It was observed that the thermal efficiency of the engine in a dual fuel operation with gasoline and hydrogen combination and gasoline and reformer gas combination was much higher as compared to that with neat gasoline for low and mild load operation. Further the operating range of the hydrogen engine in terms of knock is increased by addition of gasoline in its dual fuel mode design. The NOX emissions from the engine in its dual fuel mode operation with gasoline and hydrogen combination and gasoline and reformer gas combination was almost zero under low load conditions. However the NOX emission increased sharply with increase in load. [11]Peter A. Dennis et.al conducted experimental investigations with hydrogen on a 6 cylinder, spark ignited, port fuel injected production engine. The engine was further modified for turbo-charging, multiple fuel injectors per port and charge dilution techniques. It was possible to reduce the pumping losses through ultra-lean burn and throttle less operation and charge dilution control. The lean operation of the engine resulted in a thermal efficiency of 38%. The NO emissions were reduced under lean-burn operation. [12]Pedro Orbaiz et. al., conducted energy balance type of experimental investigations on a reciprocating spark ignition engine fuelled with natural gas, hydrogen and two different synthesis gases. The investigations were conducted particularly in lean-burn mode and by varying the fuel composition. It was observed that increasing the hydrogen content increased the heat losses from the engine cylinders to a higher extent relative to that with natural gas. The thermal efficiency of the engine was consistently at its peak value under lean air-fuel ratio operation. It was possible to optimize the engine operating conditions for best possible fuel combination for minimum fuel loss which otherwise occurred both with rich mixture due to incomplete combustion associated with higher heat loss across the engine cylinder boundaries and with lean operation due to quenching of flame. [13]J.M. Gomes Antunes et. al., conducted experimental investigations on a direct injection compression ignition hydrogen engine. Test results showed that the power to weight ratio was increased as compared to conventional diesel engine. A thermal efficiency of approximately 43% was achieved with hydrogen fuel as compared to 28% in diesel mode. The nitrogen oxide emissions were reduced by 20%. [14]Maher A.R. Sadiq Al-Baghdadi et. al., conducted computational investigations on the effects of equivalence ratio, compression ratio and inlet pressure on the performance and NOx emission of a four stroke supercharged hydrogen engine. The results were verified and compared with experimental data obtained from tests on a Ricardo E6/US engine. The results showed that supercharging was more effective method to increase the output of a hydrogen engine rather than increasing its compression ratio at its knock limited equivalence ratio. Both specific fuel consumption and engine efficiency improved for the hydrogen fuel, lean equivalence ratio and high inlet pressure of charge. Also under some range of operating conditions the engine developed power equivalent to its naturally aspirated gasoline version with same level of NOx emissions without any pre-ignition problems. Further it was found that the mathematical model was valid up to 1.8 bar of inlet pressure only as further increase in inlet pressure using the supercharger resulted in engine knock. [15]Alberto Boretti conducted modeling based computational investigations on a heavy duty Diesel truck engine with hydrogen as its possible fuel. The results showed that the modelled hydrogen engine has higher efficiencies than as compared to diesel fuel over its entire range of load. [16]
2. Theoretical Basis [17]
2.1. The Cylinder, High Pressure Cycle, Basic Equation
The calculation of the high pressure cycle of an internal combustion engine is based on the first law of thermodynamics.The first law of thermodynamics for high pressure cycle states that the change of internal energy in the cylinder is equal to the sum of piston work, fuel heat input, wall heat losses and the enthalpy flow due to blow-by.In order to solve this equation, models for the combustion process and the wall heat transfer, as well as the gas properties as a function of pressure, temperature, and gas composition are required.Establishing the relation between pressure, temperature and density, for in-cylinder temperature can be solved using a Runge-Kutta method. Once the cylinder gas temperature is known, the cylinder gas pressure can be obtained from the gas equation.
2.1.1. Combustion Model
2.1.1.1. Heat Release Approach
Vibe Two ZoneThe rate of heat release and mass fraction burned is specified by the Vibe function.Here the first law of thermodynamics is applied separately to the burned and unburned mixture while assuming that the temperatures of these two mixtures is different.
2.1.1.2. Gas Exchange Process
Basic EquationThe equation for the simulation of the gas exchange process is also the first law of thermodynamics.The variation of the mass in the cylinder can be calculated from the sum of the in-flowing and out-flowing masses.
2.1.1.3. Heat Transfer
The heat transfer to the walls of the combustion chamber, i.e. the cylinder head, the piston, and the cylinder liner, is calculated from Newton’s law of cooling.In the case of the liner wall temperature, the axial temperature variation between the piston TDC and BDC position is taken into account.For the calculation of the heat transfer coefficient, the Woschni 1978 heat transfer model is used.
2.2. Pipe Flow
The one dimensional gas dynamics in a pipe are described by the continuity equation, the equation for the conservation of momentum and by the energy equation.The wall friction force can be determined from the wall friction factor. Using the Reynold’s analogy, the wall heat flow in the pipe can be calculated from the friction force and the difference between wall temperature and gas temperature.During the course of numerical integration of the conservation laws, special attention was focused on the control of the time step. In order to achieve a stable solution, the CFL criterion (stability criterion defined by Courant, Friedrichs and Lewy) has been satisfied.An ENO scheme is used for the solution of the set of non-linear differential equations discussed above. The ENO scheme is based on a finite volume approach. This means that the solution at the end of the time step is obtained from the value at the beginning of the time step and from the fluxes over the cell borders.
2.3. Knock Model
Ignition Delay And Octane Number Requirement.AVL Boost uses the following equation based model proposed by Hires etal. for the calculation of ignition delay in combustion.
where τiD = ignition delayON = Octane Number RequirementA = 17.68 msB = 3800 Ka = 3.402n = 1.7
3. Methodology
1. Started the engine design procedure with the known research octane number of hydrogen.2. Next the thermodynamic simulations were conducted to find the design and operating parameters of the same engine which could suit normal combustion with same fuel.3. As such the following parameters were optimized:Bore, stroke, compression ratio, suitable operating range of engine speed and the suitable operating range of the load on the engine. The load calculations are represented in terms of the suitable air-fuel ratio. The suitable range of the spark timing in terms of start of combustion.
4. Results and Discussions
4.1. Effect of Speed on Octane Demand of the Hydrogen Engine
The Fig.1 below shows the effect of speed on the octane demand of the hydrogen engine. It is seen that the octane demand of the engine varies with respect to speed. This is because the temperature and pressure vary with respect to speed both in the burned zone and the unburned zone of the two zone combustion model. In order to avoid knock at higher temperatures in the unburned zone of the mixture, the octane demand of the engine for hydrogen fuel increases.Under low speed conditions the hydrogen in the unburned zone may get sufficient time to auto-ignite before the flame propagates to it. As such the engine design should be optimized accordingly. 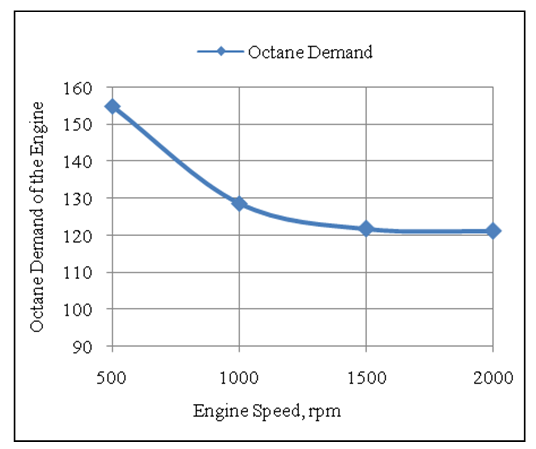 | Figure 1. Effect of Speed on Octane Demand of the Hydrogen Engine |
4.2. Effect of Air-Fuel Ratio on Octane Demand of the Hydrogen Engine
The Fig 2 below shows the effect of air-fuel ratio on the octane demand of the hydrogen engine. The octane demand of the hydrogen engine varies with respect to the air-fuel ratio of the engine. The reason is that as the mixture is made leaner, the fuel conversion efficiency increases and results in higher temperatures in the engine cylinder, demanding a higher octane number for the design of hydrogen for normal combustion.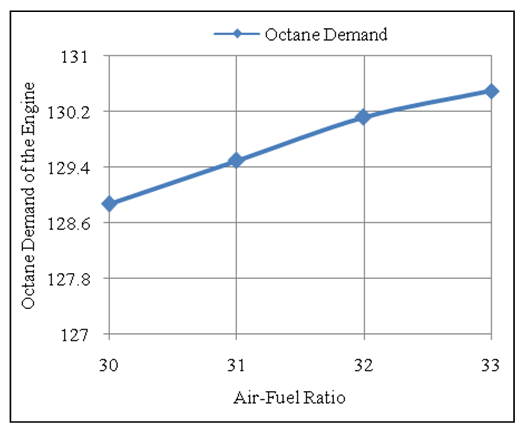 | Figure 2. Effect of Air-Fuel Ratio on the Octane Demand of the Hydrogen Engine Under Idle Speed Conditions |
4.3. Effect of Compression Ratio on the Octane Demand of the Hydrogen Engine
The Fig.3 below shows the effect of compression ratio on the octane demand of the hydrogen engine. The octane demand of the hydrogen engine varies with respect to the compression ratio of the engine. The reason is that as the compression ratio increases the temperature inside the engine cylinder also increases. The higher in-cylinder temperatures demand higher octane number in order to maintain normal combustion.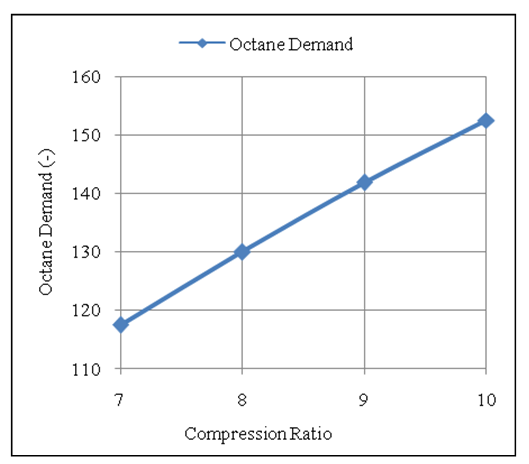 | Figure 3. Effect of Compression Ratio on the Octane Demand of the Hydrogen Engine |
4.4. Effect of Spark Timing on the Octane Demand of the Hydrogen Engine
The Fig.4 below shows the effect of start of combustion based on the spark timing on the octane demand of the hydrogen engine.It is clear that the octane demand of the hydrogen engine varies with respect to the start of combustion corresponding to change in spark timing. The reason is that there is optimum spark timing for developing peak pressure and temperature in the engine cylinder. The change in the peak temperatures as a result of change in spark timing changes the octane demand for the design of hydrogen engine.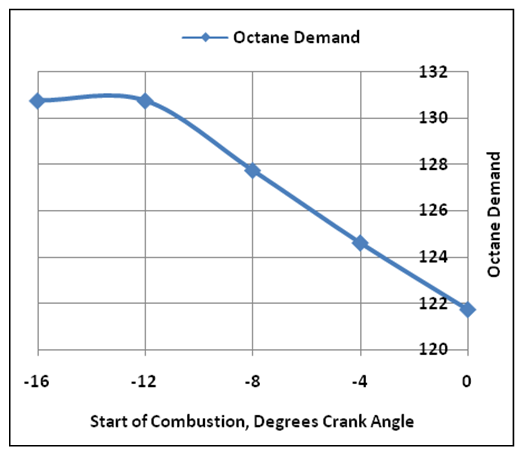 | Figure 4. Effect of Start of Combustion on the Octane Demand of the Hydrogen Engine |
5. Conclusions
1. The maximum air-fuel ratio for the hydrogen engine under idle speed conditions should be 31.75 in order to meet the octane demand of the engine for hydrogen fuel.2. The maximum compression ratio of the hydrogen engine under idle speed, and air-fuel ratio of 31.5 should be 8 to meet the octane demand of the hydrogen engine.3. The suitable range of the start of combustion for the hydrogen engine is between -10 to 0 degrees of crank angle with respect to top centre. 4. In order to ensure controlled combustion, practically hydrogen engine should be designed for lower compression ratios and lower operating temperatures. This will ensure controlled combustion because of flame propagation and not self ignition or auto-ignition.
ACKNOWLEDGEMENTS
Author is thankful to AVL Austria and its unit AVL India Ltd Gurgaon for providing BOOST engine simulation software with free license for academic research purposes. Table 1 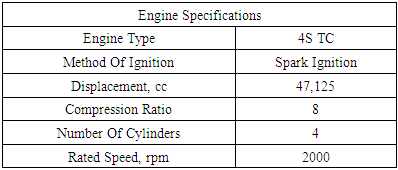 |
| |
|
Table 2. Physical And Chemical Properties Of Hydrogen [1] 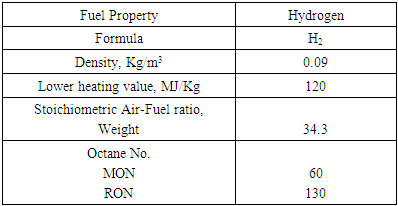 |
| |
|
References
[1] | John B Heywood, “Internal Combustion Engine Fundamentals”, McGraw Hill Book Company. |
[2] | M. Marouf Wani, “ Computational effect of speed and air-fuel ratio on the performance of a turbocharged four cylinder four stroke cycle direct injection diesel engine using hydrogen and diesel as alternative fuels” IJMIE, Volume 3, Issue 1, pages 330-344, January 2013. |
[3] | M. Marouf Wani,” Computer Simulation studies on a four stroke cycle spark ignition engine using gasoline and hydrogen as alternative fuels.” IJMIE, Volume 3, Issue 1, pages 468-483, January 2013. |
[4] | Shuofeng Wang, Changwei Ji, Bo Zhang, Xiaolong Zhou,” Analysis on combustion of a hydrogen-blended gasoline engine at high loads and lean Conditions”, The 6th International Conference on Applied Energy – ICAE2014, Energy Procedia 61, Elsevier ScienceDirect, 2014. |
[5] | Choongsik Bae, Jaeheun Kim, “Alternative fuels for internal combustion Engines”, Proceedings of the Combustion Institute, Elsevier Science Direct, 2017. |
[6] | A. Gharehghani, R. Hosseini, M. Mirsalim, Talal F. Yusaf, “A computational study of operating range extension in a natural gas SI engine with the use of hydrogen”, International Journal Of Hydrogen energy, Elsevier ScienceDirect, 2015. |
[7] | Baris Acikgoz, Cenk Celik, “An experimental study on performance and Emission characteristics of a methane-hydrogen fuelled gasoline engine”, International Journal Of Hydrogen Energy, Elsevier ScienceDirect, 2012. |
[8] | H. An, W.M. Yang, A. Maghbouli, J. Li, S.K. Chou, K.J. Chua, “A numerical study on a hydrogen assisted diesel Engine”, International Journal of Hydrogen Energy, Elsevier Science Direct, 2013. |
[9] | B. Nagalingam, Martin Dubal and Karl Schmillen K, “Performance of the Supercharged Spark Ignition Hydrogen Engine”, SAE Technical Paper 831688, 1983. |
[10] | Kim J., Kim Y., Lee J., and Lee S., “Performance Characteristics of hydrogen Fueled Engine with the Direct Injection and Spark Ignition System”, Technical SAE Paper 952498, 1995. |
[11] | Teruo Suzuki, Yoshihito Sakurai, “Effect of Hydrogen Rich Gas and Gasoline Mixed Combustion on Spark Ignition Engine”, SAE Technical Paper 2006-01-3379, 2006. |
[12] | Peter A. Dennis, Robert J., Dingli, Payman Abbasi Atibeh, Harry C, Watson, Michael J., Brear, Glen Voice, ” Performance of a Port Fuel Injected, Spark Ignition Engine Optimized for Hydrogen Fuel”, SAE Technical Paper 2012-01-0654, 2012. |
[13] | Pedro Orbaiz, Michael Brear, “Energy Balance of a Spark Ignition Engine Running on Hydrogen, Synthesis Gas and Natural Gas”, SAE Technical Paper 2014-01-1337, 2014. |
[14] | J.M. Gomes Antunes, R. Mikalsen, A.P. Roskilly,” An experimental study of a direct injection compression ignition hydrogen engine”, International Journal Of Hydrogen Energy, Elsevier Science Direct, 2009. |
[15] | Maher A.R. Sadiq Al-Baghdadi, Haroun A.K. Shahad Al-Janabi,” A prediction study of a spark ignition supercharged hydrogen engine”, Energy Conversion And Management, Elsevier ScienceDirect, 2003. |
[16] | Alberto Boretti, “Advances in hydrogen compression ignition internal combustion engines”, International Journal Of Hydrogen Energy, Elsevier ScienceDirect, 2011. |
[17] | AVL LIST Gmbh, AVL BOOST Theory, Version 2015. |