Rahul Kumar, Abhishek M. K., Aaron Fuller, George Bosco M., Joyson Vinod Rego
Department of Mechanical Engineering, St. Joseph Engineering College, Mangalore, India
Correspondence to: Rahul Kumar, Department of Mechanical Engineering, St. Joseph Engineering College, Mangalore, India.
Email: |  |
Copyright © 2017 Scientific & Academic Publishing. All Rights Reserved.
This work is licensed under the Creative Commons Attribution International License (CC BY).
http://creativecommons.org/licenses/by/4.0/

Abstract
This project is an effort made to substitute conventional Organic petrochemical core Binders with Inorganic binders in accord with Pollution Prevention Act & Clean Air Act which regulated that out of 189 hazardous air pollutants (HAPs), foundry air emissions shared more than 40. Sodium silicate binders processed through a cold-box or self-setting had lower tensile strength than conventional organic binders. To enhance the properties, various additives have been added which includes both the organic and inorganic materials at different levels of concentrations but the effort did not derived satisfactory results & optimal solution to the Industry. The main aim of the project is to synthesize a composite binder with similar structural properties as organic binders in terms of the core structural integrity, shakeout properties and casting quality by using only inorganic constituents. Through extensive research on binders used in the foundry industry the use of collagen, sodium silicate, sodium polyphosphate and silica sand for the production of foundry cores has been investigated on varying composition. The three components were processed together in order to analyse the chemical stability of the composite binder. Preference were given to the air-assisted warm core box process which successfully replaced widely used cold box process and organic binders in the mass production of aluminium castings for automotive engines. The validity of the synthesized composite binder was determined through a series of test includes tensile strength, compression strength, scratch hardness, permeability and soundness of casting. The core synthesized has a tensile strength of 14 kg/cm2, compression strength of 22 kg/cm2, scratch hardness number of 85 and also sublime surface finish for the casting, thus satisfying the expectations of the industry. Results herein showed that combination of this binder could eliminate the uses of organic binder as they possess the required mechanical properties and excellent surface finish for the cast.
Keywords:
Binders, Cores, Silica Sand, Casting, Core Testing
Cite this paper: Rahul Kumar, Abhishek M. K., Aaron Fuller, George Bosco M., Joyson Vinod Rego, Study on Mechanical Properties of Bio Based and Inorganic Binders for the Preparation of Core in Metal Casting, Energy and Power, Vol. 7 No. 5, 2017, pp. 136-141. doi: 10.5923/j.ep.20170705.03.
1. Introduction
Binders are the adhesive kind of materials used for binding the sand for preparing the mould. Hydrated Sodium Silicate is the commonly used binders in industries. The foundry industry has been using it for over 50 years in the production of moulding and core sands. Sand casting is the most widely used metal casting process in manufacturing. Almost all casting metals can be sand cast. Some examples of items manufactured in modern industry by sand casting processes are engine blocks, machine tool bases, cylinder heads, pump housings, and valves. Sand casting is one of the earliest metal shaping methods known to human being. It generally means pouring molten metal into a refractory mould with a cavity of the shape to be made and allowing it to solidify. When solidify, the desired metal object is taken out from the refractory mould either by breaking the mould or taking the mould apart. The solidified object is called casting. This process is also called founding. The used sand mixture is then disposed off to landfills, which leads to environmental pollution. It is well known that the waste disposed from foundries that could potentially affect the environment, in most cases consists of used moulding and core sand as well as binders. Its share in the total amount of waste generated by the non-ferrous metal casting industry represents more than 85%. The economic use of waste is the most effective method of elimination of resulting hazards [1]. Foundries are regulated by a host of environmental regulations, including the Clean Air Act, the Clean Water Act, the Pollution Prevention Act, the Emergency Planning and Community Right-to-Know-Act, and the Resource Conservation and Recovery Act. There are multiple sources of air emission pollution within foundries. Of the 189 hazardous air pollutants (HAPs) regulated by the Clean Air Act, over 40 of them have been observed in foundry air emissions. More than 90% of these foundry HAPs are organic based, and approximately 80% of them are benzene, toluene or xylene compounds. In foundries, the primary volatile organic compound (VOC) and HAP release points occur during metal pouring, cooling, and shakeout. Glowacki et al and Goudzwaard et al found that between 30 and 70% of these VOC emissions can be attributed to the breakdown of petrochemical core binders such as conventional phenolic urethanes during the aforementioned processes. This range stems from the array of many different core binders that each present their tell-tale array of volatile organic compounds (VOCs). Also, the magnitude of VOC emissions release corresponds to the extent that a foundry uses cores for the particular metal casting that is being poured. The Pollution Prevention Act states that the most optimal way of reducing manufacturing waste is to eliminate the source of the pollution. There is a great opportunity to reduce VOC air emissions in foundries at the source by replacing conventional petrochemical core binders with less-polluting binders [2]. This made the evolution of more and more inorganic binders. Inorganic binder, which is soluble in sodium silicate, belongs to a group of ecological binders, is a non-toxic and cheap compared to organic with disadvantages of poor knocking out property, low plasticity, poor reclaimability made industries to stick again to organic or mixture of these in foundries. Some additives and modifiers, such as phosphates improve the sand collapsibility after hardening [3]. This is the reason why numerous scientific and research centres as well as manufacturers of binders carryout intense research on the development of new, or modification of so far existing, inorganic binders [4]. The growing complexity of core shape, high strength and core removal requires new materials for the core base, binders and coatings. In a quest for the perfect solution, the inorganic binders are receiving recently a renewed interest. Thus binders such as Collagen, α-starch, cordis binder, and AWB binder are where research is been concentrated on. There are many companies focused on developing inorganic core binders for the automotive industry, including Minelco GmbH (LKAB Minerals), ASK Chemicals, HA International, BMW, Foseco, and Honsel. In addition to individual effort, there are also joint ventures involving clusters of companies [5]. The polyphosphate glass in the combination glass binder system improved flowability of sand mixtures, tensile and shakeout properties of sand cores. Excellent collapsibility of the cores made with the combination binder was also documented at casting temperatures from 200°C to 1425°C (390℉ to 2600℉). Foundry tests showed that mechanical shakeout for urethane binder was 5-10 times longer, compared to the combination binder, when pouring aluminium. GIFA, in 2003, was considered as a turning point, when the leading manufacturers of foundry binders presented information about their progress on the development of new inorganic binder systems, including two-component binders based on water glass. Several years later, two of these two-component systems were successfully implemented in the large-scale production of aluminium engine blocks and heads. The new two-component binders had created really new possibilities and prospects for the widespread introduction of inorganic binders [6]. New raw materials are being identified, new processes and chemistries are being developed, and creative products with novel attributes are being introduced in the market places. Also, separation technology and process engineering as well as increased sophistication in the design and development of instrumentation are all contributing towards the expansion of our knowledge and capacity to create products. Thus, there is no doubt that bio based polymers are destined to have a promising future as adhesives, gums, binders, and emulsions. Many challenges and concerns posed by renewable polymers have been and are being addressed by researchers worldwide [7].
2. Aim of the Research
With constantly growing requirements for environmental protection are increasingly important these technologies, while ensuring required technological parameters, provide the least possible harmfulness for environment, therefore the aim of executed project is to substitute a novel or commercial used organic binders in industries with non-pollutant inorganic binder for the preparation of core in metal casting.The objective is to prepare a core, using composite binder involving collagen, sodium silicate and sodium polyphosphate using warm box method and to conduct various tests to find out the tensile, compression, scratch hardness, refractoriness, surface finish and knocking out properties of the core. The objectives of the research herein have been to yet further evaluate and advance the development of this two component system which involves collagen, sodium silicate and sodium polyphosphate core binder and to substitute these novel binders for petro-chemical binders, so as to improve the properties of the cores used in the industry.
3. Materials and Methods Used in the Research
3.1. Materials
In this study in order to prepare a core of good properties some materials are been used, main or major quantity of material used make a core is sand, therefore in this study silica sand of GFN No. 49 is used. The second major proportion is binders; here sodium silicate Na2SiO3 as the base binder, Collagen and sodium polyphosphate Na5P3O10 as substitute binder is used.
3.2. Methodology
3.2.1. Optimization of Considered Components of Composite Binder
In the first set of tests performed, collagen proportion is varied and unvarying other two binder compositions. In second set sodium silicate is varied and rest two are kept constant. In third set of test sodium polyphosphate is varied and unvarying other two resulting in increasing strength properties.
3.2.2. Sample Preparation for Tensile and Scratch Hardness Test
Silica sand of GFN 49 is preheated at 45°C in rapid dryer, then the dried sand is mixed with different proportions of binders in a bowl using kitchen aid mixer with speed setting ‘4’. The prepared mixture is filled into dog bone shaped core box. Using sand rammer the mixture is rammed 4 times in order to set the mixture into the mould. The sample along with the core box is kept inside the core oven at about 110°C for 1 hour. Now the sample is taken out and released from core box and is cured for another 20min in open air. The prepared sample is tested in Universal Strength Machine with the help of tensile attachments and values were noted down. For performing scratch hardness test, with the help of scratch hardness specimen, is moved on to the cured specimen surface and values were noted down.
3.2.3. Sample Preparation for Compression and Permeability Test
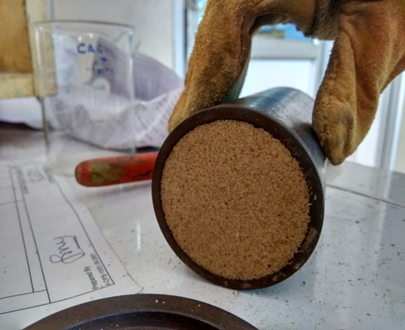 | Figure 1. Cylindrical Specimen in Compression Pattern |
Silica sand of GFN 49 is preheated at 45°C in rapid dryer, then the dried sand is mixed with different proportions of binders in a bowl using kitchen aid mixer with speed setting ‘4’. The prepared mixture is filled into compression core box. Using sand rammer the mixture is rammed 4 times in order to set the mixture into the mould. The sample along with the core box is kept inside the core oven at about 110°C for 1&1/2 hours. Now the sample is taken out and released from core box and is cured for another 20min in open air. The prepared sample is tested in Universal Strength Machine with the help of compression attachments and values were noted down. For performing the permeability test the cured sample is placed in the permeability attachment and is mounted on Digital Permeability Tester and the drum is lifted to its 0th reading and the machine is switched on by pressing the start button, corresponding results were noted down.
3.2.4. Tests for Refractoriness and Surface Finish of the Casting Obtained
The final test is performed by carrying out casting using the core produced using the composite binder in order to find out the refractoriness of the core as well as the surface finish of the casting produced. Using a wooden pattern the mould is made, respective gating and riser systems is been added to the mould. A print is placed on the mould in order to create a cavity for placing the core. After the mould is dried, core prepared is placed into the cavity along with the clamping system and closed with other half of the mould. Dimension of the wooden pattern is 90mm diameter and 70mm height. Dimension of core is 50mm diameter and 50mm height, a small portion of the wooden pattern is left inside the cavity of the mould in order to hold the core which is of 20mm. The molten metal (stainless steel) is poured into the mould at a temperature of 1560°C. After solidification of the metal the cast is separated from the mould by mechanical action. The gating and risers are machined off and the outer part is smoothened using the grinder. Finally the surface finish of the casting is analysed using the comparator.
4. Experimentation
All the tests were performed under the supervision of production engineer in GWASF Quality Castings Pvt. Ltd. Universal Strength Machine (Digital) VUD model, equipped with tensile attachments was used to perform tensile test over a (dog bone shaped) specimen of size 2.75inch×1inch×1inch according to AFS standard, by mixing percentage composition of binders for 100g of sand. USM with compression attachments was used to perform compression test over a cylindrical specimen of size 50mm×50mm according to AFS standard, by mixing percentage composition of binders for 150g of sand. Scratch Hardness Equipment was used to perform Scratch Hardness on (dog bone shaped) specimen of size 2.75inch×1inch×1inch according to AFS standard. Digital Permeability Tester equipped with permeability attachments was used to conduct permeability test over a compression sample of size 50mm×50mm according to AFS standard, by placing the compression specimen inside the permeability attachments and mounting it on the tester. Refractoriness and the surface finish of our composite core binder were analysed by casting a product of stainless steel at a temp of 1560°C and by using a surface finish comparator.
5. Results and Discussions
5.1. Mechanical Properties
5.1.1. Tensile Strength
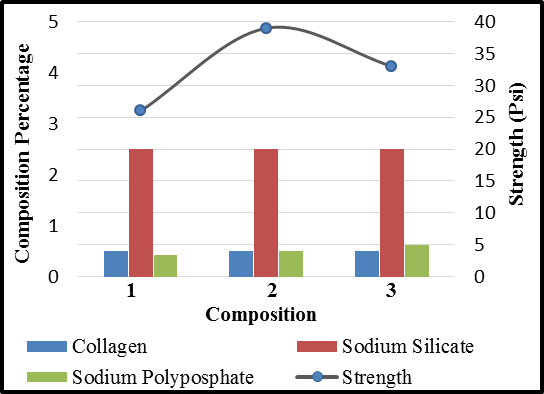 | Figure 2. Composition v/s Tensile Strength |
Tensile specimen with 0.5% collagen, 2.5% sodium silicate and increasing amounts of sodium polyphosphate from 0.425% to 0.625% is been analysed. From the above graph it is noticed that the tensile strength of the specimen increases with increase in composition of sodium polyphosphate till 0.5% beyond which the tensile strength begins to decrease.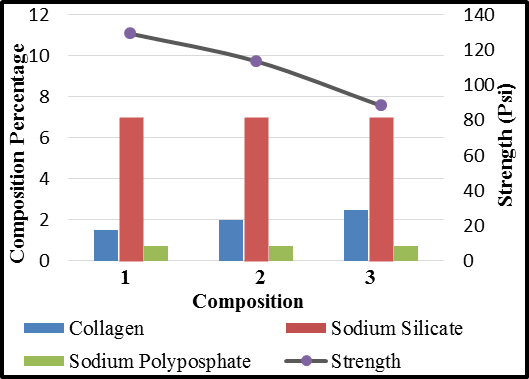 | Figure 3. Composition v/s Tensile Strength |
Tensile strength of samples with 7% sodium silicate, 0.75% sodium polyphosphate and increasing in amounts of collagen is analysed. From the graph it is noticed that there is a decrease in tensile strength when collagen is varied from 1.5% to 2.5%.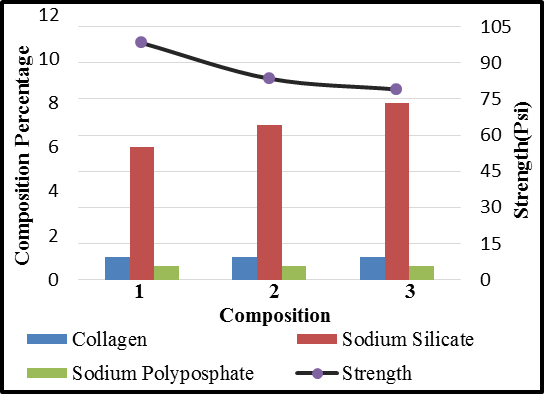 | Figure 4. Composition v/s Tensile Strength |
In the above testing the specimen composed of 1% collagen, 0.75% sodium polyphosphate, and varying composition of sodium silicate from 6% - 8%, it is observed that tensile strength decreases when sodium silicate composition is been increased to more than 6%. From the above analysis the effects in varying the composition of each component is understood. Based on these results, four different composite binders are been considered as they have a tensile strength ranging from 10-14 kg/cm2. The various compositions which exhibit good tensile strength are shown in table 1.Table 1. Testing Specimen Compositions 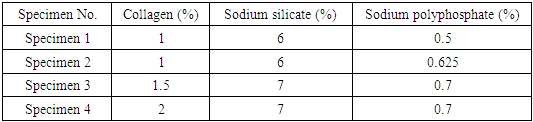 |
| |
|
5.1.2. Compression Strength
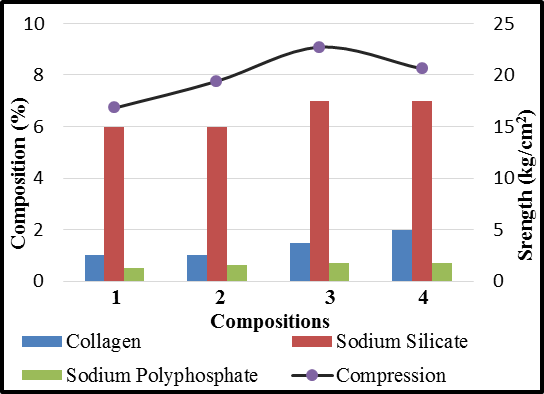 | Figure 5. Composition v/s Compression Strength |
Analysis is been done for the four specimens which have excellent tensile strength properties. Here in the graph one can observe that maximum compression strength of 22 kg/cm2 is obtained for sample no. 3, where collagen is kept for 1.5%, sodium silicate for 7% and sodium polyphosphate for 0.7%. This property decreases when collagen is increased from 1.5% to 2% while keeping the other two constant.
5.1.3. Scratch Hardness
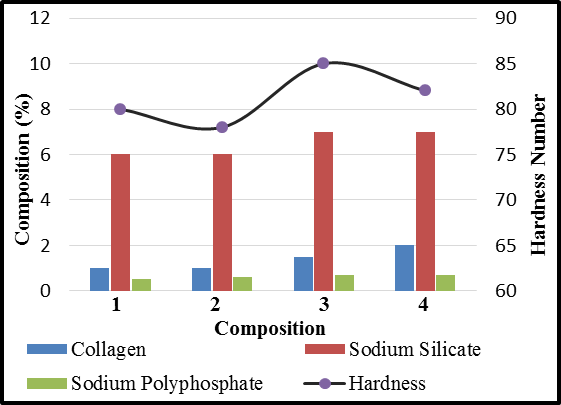 | Figure 6. Composition v/s Hardness Number |
From the above graph it is observed that for sample 3 an extremely high value of 85 scratch hardness number is been achieved. The general hardness of a core is in the range of 5-75, while the core created by the new composite binder is in the range of 78-85.
5.1.4. Permeability
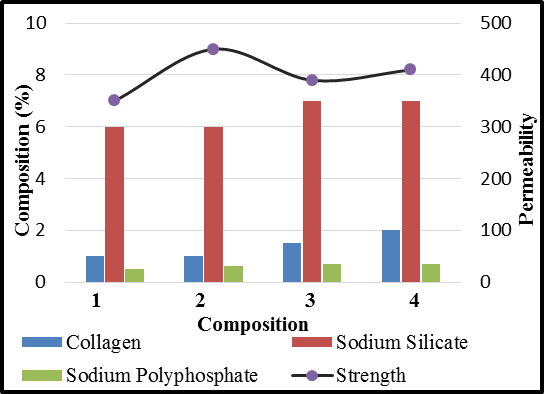 | Figure 7. Composition v/s Permeability |
The value of permeability varied from 350 to 450 as shown. It denotes that the core made from these compositions have the property to release gases generated during solidification process of molten metal.
5.1.5. Surface Finish & Refractoriness
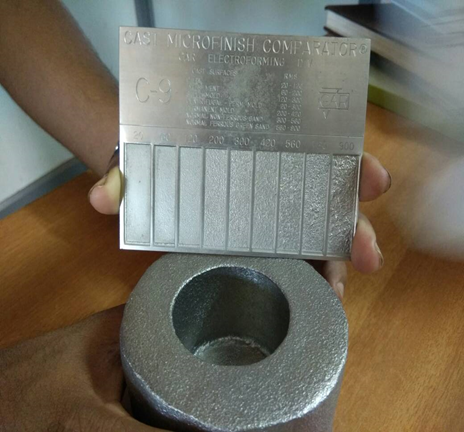 | Figure 8. Casting analysed with the help of comparator |
Using the comparator we were able to analyse the surface finish of the casting and achieved results of surface finish ranging from 300-420 RMS. The core was able to withstand extremely high temperature of 1500°C thus showing high refractoriness property.
6. Conclusions
The composite binder consisting of Collagen, Sodium silicate and Sodium polyphosphate which was used to create a sand core was tested and results were obtained.• Tensile strength ranging from 10-14kg/cm2.• Compression strength of 16 -22kg/cm2.• Scratch hardness number of 78-85.• Permeability ranging from 350-450.The above results prove that the composite binder created can be used in Industries for the production of cores.Collagen, sodium silicate and sodium polyphosphate in the range of 1%-2%, 4%- 7% and 0.415%-0.7% with respect to 1kg of sand, respectively showed excellent mechanical properties. On increasing weight percentage of the constituents beyond the scale of optimization observed shows an adverse effect on the tensile strength of the core. During casting process along with the core created using composite binder the emission of gases were less compared to the amount of gases emitted while using traditional binders (Petrochemical Binders). The core was able to withstand extremely high temperature upto 1500°C. The core binder has shown excellent stiffness against pressure exerted by molten metal during pouring and solidification. The specimen (Stainless Steel) casted using composite core binder has excellent surface finish and minor casting defects.
ACKNOWLEDGEMENTS
The authors of the paper are grateful to Mr. Francis D’Souza, Senior Manager and Mr. Divyaprakash, Human Resource Manager, Mr. Pushparaj, Production Engineer of GWASF Quality Castings Pvt. Limited for their constant support and permitting us to conduct our project in the company premises using their resources and provided expertise that greatly assisted our project. We will remember this contribution forever. We show our greatest appreciation to our project guide Mr. Rahul Kumar, Assistant Professor. We can’t thank him enough for his tremendous support and help, with which we accomplished our project. It was an absolute honour for us to have been working under his guidance. The authors express their gratitude to all who directly or indirectly supported this technical work during execution of the project.
References
[1] | I. Izdebska-Szanda, M. Angrecki, A. Palma a Foundry Research Institute, Zakopiańska 73, 30-418 Cracow, Poland. Recycling of Waste Moulding Sands with New Binders. |
[2] | Joshua F. Allen, Fred S. Cannon, Cesar Nieto-Delgado, and Robert C. Voigt The Pennsylvania State University, University Park, PA, USA, John T. Fox Lehigh University, Bethlehem, PA, USA, Jim Lamonski Hitachi Metal Automotive Components, Lawrenceville, PA, USA, John D. Kirby ARCADIS U.S. Inc., Branchburg, NJ, USA, Full-Scale Air Emissions Monitoring And Casting Quality Demonstration of A Hybrid Hydrolysed Collagen–Alkali Silicate Core Binder, Copyright 2016 American Foundry Society DOI 10.1007/s40962-016-0021-y. |
[3] | I. Izdebska-Szanda, F. Pezarski, E. Smoluchowska. Department of Technology, Foundry Research Institute, ul. Zakopiańska 73, 30-418 Kraków, Poland, Investigating the kinetics of the binding process in moulding sands using new, environment-frien, Germany: Springer-Verlag, 1998. |
[4] | I. Izdebska-Szanda, A. Baliński, M. Angrecki Foundry Research Institute, Zakopiańska 73, 30-418 Kraków, Poland. Evaluation of Reclamability of Moulding Sands with New Inorganic Binders. |
[5] | F. Czerwinski, M. Mir & W. Kasprzak, Application of cores and binders in metal casting, International Journal of Cast Metals Research, 28:3, 129-139, DOI: 10.1179/1743133614Y.0000000140. |
[6] | Leonid Zaretskiy HA International (retired), Oak Park, IL, USA, Modified Silicate Binders New Developments and Applications, Copyright 2015 American Foundry Society DOI 10.1007/s40962-015-0005-3. |
[7] | Syed H. Imam, Cristina Bilbao-Sainz, Bor-Sen Chiou, Gregory M. Glenn & William J. Orts, Biobased adhesives, gums, emulsions, and binders: current trends and future prospects, Journal of Adhesion Science and Technology, 27:18-19, 1972-1997, DOI: 10.1080/01694243.2012.696892. |