Ramya M., John Paul Vas, Antony Varghese, Akhil Thomas Varghese, George Varghese, Kuruvilla Thomas Kuttothara
Mechanical Engineering Department, St. Joseph Engineering College, Mangaluru, India (VTU)
Correspondence to: Ramya M., Mechanical Engineering Department, St. Joseph Engineering College, Mangaluru, India (VTU).
Email: |  |
Copyright © 2017 Scientific & Academic Publishing. All Rights Reserved.
This work is licensed under the Creative Commons Attribution International License (CC BY).
http://creativecommons.org/licenses/by/4.0/

Abstract
Waste plastics are indispensable materials in the modern world and application in the industrial field is continually increasing. Conversion of waste plastic to fuel is one of the recent trends in minimizing not only the waste disposal but also could be used as an alternate fuel for internal combustion engines. The objectives of this work includes analyzing the properties of waste plastic fuel oil obtained by thermo-catalytic cracking of waste plastics to produce high grade liquid fuel for CI engine and compare its properties with diesel in order to understand which blend should be used in the engine. This work also includes analysis of various engine performance parameters using the obtained blended fuel at different loading conditions. The test on the obtained fuel oil is conducted at compression ratios 16 and 17. It is also conducted on diesel at compression ratio of 17 and the results were compared. It can be concluded from the results that waste plastic fuel with diesel fueled up to 5% by volume could replace the diesel fuel by operating the existing diesel engine without any modifications. There is a comparable increase in brake thermal efficiency, reduction in specific fuel consumption and a significant decrease in volumetric efficiency. The B5 blend also shows an increase in emissions of gases such as hydrocarbons, oxides of nitrogen and carbon monoxide. In addition to this smoke emitted by B5 blend is less than diesel. Furthermore the work can be improved by using better grade of catalyst for thermo-catalytic cracking, different classes of plastics and varying injection pressure and injection timing.
Keywords:
Waste plastic fuel, Thermo-catalytic cracking, Performance analysis
Cite this paper: Ramya M., John Paul Vas, Antony Varghese, Akhil Thomas Varghese, George Varghese, Kuruvilla Thomas Kuttothara, Analysis of Performance Characteristics of Waste Plastic Fuel Oil blend in a VCR CI Engine, Energy and Power, Vol. 7 No. 5, 2017, pp. 123-129. doi: 10.5923/j.ep.20170705.01.
1. Introduction
Plastics are synthetic organic materials produced by polymerization, they are typically of high molecular mass, and may contain other substances besides polymers to improve performance and/or reduce costs. These polymers can be moulded or extruded into desired shapes. In India 56 lakh tonnes of plastics are generated each year and only 60% of it is recycled. Safe method of disposing the waste plastic has not yet been effectively implemented and improper disposal of waste plastic is hazardous to the environment.There are two main types of plastics: thermoplastics and thermosetting polymers. Thermoplastics can repeatedly soften and melt if enough heat is applied and hardened on cooling, so that they can be made into new plastics products. Examples are polyethylene, polystyrene and polyvinyl chloride, among others. Thermosets or thermosetting can melt and take shape only once. They are not suitable for repeated heat treatments; therefore, after they have solidified, they stay solid.Plastics are also classified into two types, they are High-density polyethylene and Low-density polyethylene. Though work has been done to make futuristic biodegradable plastics, there have not been many conclusive steps towards cleaning up the existing problem. The process of converting waste plastic into value added fuels is explained as one of the viable solution for recycling of plastics. Thus two universal problems such as recycling of waste plastic and requirement of an alternative fuel are being tackled simultaneously. In this study, plastic wastes (low density polyethylene)were used for the thermocatalytic cracking to get fuel oil that has the same physical properties as the fuels like petrol, diesel etc.Pyrolysis is the process of heating in the absence of oxygen at high temperature of about 300°C for which a reactor was fabricated to provide the required temperature for the reaction. The waste plastics are subjected to depolymerisation, pyrolysis, thermal cracking and distillation to obtain different value added fuels such as petrol, kerosene, and diesel, lube oil etc. The hazards of plastic waste are well known to us. The conversion to oil from plastic has dual benefits. Firstly the oil produced can be used as a fuel for domestic purposes and also in vehicles and industries when further refined. Secondly the various types of pollution caused due to waste plastics can be minimized. This study includes waste plastic oil obtained by using catalyst and without using catalyst. The plastic used in this study is polypropene. The conversion of polypropene to fuel is by thermocatalytic cracking and the catalyst being zeolite. This produced more yield compared to one without catalyst. The properties of fuel were found out and compared with diesel. The engine performance test was conducted using diesel and waste plastic oil blend B5. It is found that blend of diesel and waste plastic oil gives nearer performance values to diesel fuel in the engine without any alterations.
2. An Overview on Conversion of Waste Plastic to Fuel
Plastics have become an indispensable part in today’s world. Plastics are produced from petroleum derivate and are composed primarily of hydrocarbons but also contain additives such as antioxidants, colorants and other stabilizers. Plastics are non-biodegradable polymers mostly containing carbon, hydrogen, and few other elements like nitrogen. Due to its non-biodegradable nature, the plastic waste contributes significantly to the problem of waste management. Due to its non-biodegradable nature, the plastic waste contributes significantly to the problem of waste management. According to a nationwide survey which was conducted in the year 2000, approximately 6000 tons of plastic waste are generated every day in India, and only 60% of it was recycled, the balance of 40% could not be disposed of. Today about 129 million tons of plastics are produced annually.
2.1. Waste Plastic Oil in Diesel Engines
Diesel engines are most preferred power plants due to their excellent derive ability and higher thermal efficiency. Most of the research work has been done by mixing oil developed from waste plastic disposal with heavy oil for marine application. The results showed that waste plastic disposal oil when mixed with heavy oils reduces the viscosity significantly and improves the engine performance.
2.2. Pyrolysis
Pyrolysis is a thermo-chemical decomposition of organic material at elevated temperatures in the absence of oxygen (or any halogen). It involves the simultaneous change of chemical composition and physical phase, and is irreversible. Pyrolysis is a type of thermolysis, and is most commonly observed in organic materials exposed to high temperatures. It is one of the processes involved in charring wood, starting at 200–300°C (390–570 °F). In general, pyrolysis of organic substances produces gas and liquid products and leaves a solid residue richer in carbon content, char. The pyrolysis reaction consists of three progressive steps: initiation, propagation, and termination. Initiation reaction cracks the large polymer molecules into free radicals. The free radicals and the molecular species can be further cracked into smaller radicals and molecules during the propagation reactions. The radicals will combine together into stable molecules, which are termination reactions. There are three types of cracking of the polymers: random cracking, chain strip cracking, and end chain cracking.The plastic waste were converted to fuel by thermo-catalytic cracking, the apparatus used for obtaining the fuel is shown in figure 1.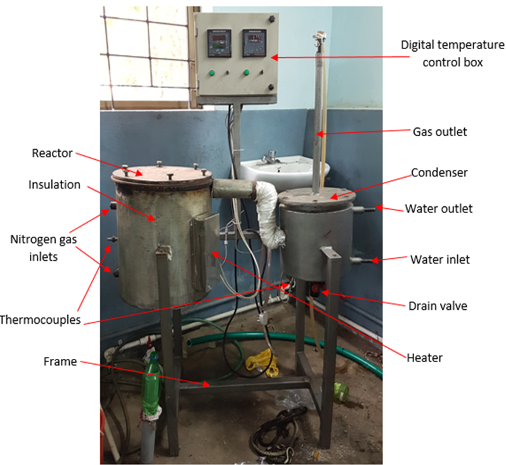 | Figure 1. Thermocatalytic cracking apparatus |
The pyrolysis reactor is designed for pyrolysis of waste plastic (PP). The reactor is a cylindrical, batch type, fixed bed reactor. The top side of reactor can be open for feeding the raw material and solid residue (char) can be removed at the end of the experiment. The temperature inside the reactor is measured by using a thermocouple. During the reaction, the top side is kept closed by two flanges tightly.In addition to it, two air tight oil gaskets are placed in order to minimize the escape of gas from the reactor. This prevents ingression of atmospheric air into the reactor. The reactor is provided with ceramic blanket insulation and a MS Perforated sheet with plaster for the insulation cover on the outer side to prevent the heat loss to the surrounding. An exit pipe at the side carries away the evolved gases during pyrolysis. Two inlets are provided for nitrogen at the side of the reactor. Zeolites are crystalline micro-porous aluminosilicates. The high-silica zeolites, with a Si/Al ratio greater than five such as ZSM-5, are widely used in petrochemical industries. The high silica content in the catalyst makes the framework to stand high temperatures that this type catalyst is suitable for high temperature pyrolysis and regeneration cycle.
3. Experimental Setup and Observations
The waste plastic fuel oil obtained was tested using various instruments and procedures to determine its properties, like, Cleveland (open cup) apparatus was used to evaluate the fire point, Redwood viscometer with a built in heater was used to find the viscosity, Bomb calorimeter is used to measure the calorific value and the following observations and comparisons with diesel were obtained as listed in table 1.Table 1. Combustion properties of Diesel, Plastic fuel, B5, B10 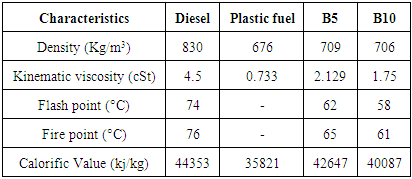 |
| |
|
3.1. Performance Characteristics Using a Diesel Engine Test Rig
The schematic diagram of the complete experimental setup of the Diesel engine is shown in figure 2. The engine test is conducted on a computerized single cylinder, 4-stroke, naturally aspirated, open chamber (direct injection) and water cooled diesel engine test rig. It is directly coupled to an eddy current dynamometer.The setup has standalone type independent panel box consisting of air box, fuel tank, manometer, fuel measuring unit, transmitters for air flow and fuel flow measurements, process indicator and engine indicator. For measurements of water flow rate for engine cooling and exhaust gas calorimeter, rotameters are used. 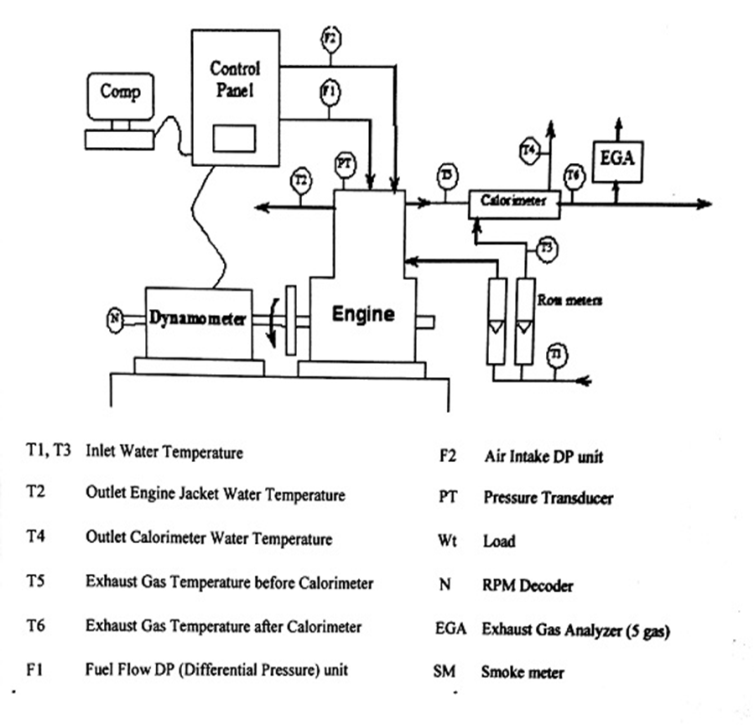 | Figure 2. Schematic of a Diesel Engine test rig |
3.2. Emission Characteristics using a Diesel Engine Test Rig
The emission characteristics are measured at no load, 3kg, 6kg, 9kg and 12kg load. The various blends are used to run the engine and its emission parameters are compared with each other as well as diesel and biodiesel. The diesel engine test rig is as shown in figure 3.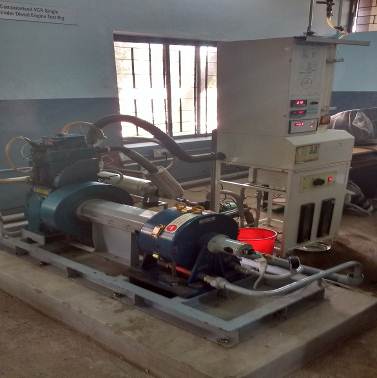 | Figure 3. Diesel engine test rig |
At every trial the time for 10cc fuel consumption, speed, the various temperatures and the emission parameters are checked after the engine attained stability at varied loads.During the test, emission parameters that are checked for are carbon monoxide, NOX, HC, carbon dioxide, oxygen and smoke. An Exhaust gas analyser is being used for this purpose. The Exhaust gas analyser is as shown in figure 4.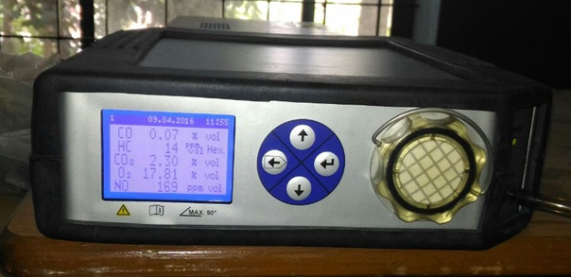 | Figure 4. Exhaust gas analyser |
Exhaust gas analyser is an instrument used to measure the exhaust gases (in parts per million, percent, grams per kilometre, or grams per mile) to determine both combustion efficiency and the amount of pollutants in the exhaust. The smoke detector indicates the amount of smoke released by an engine and is denoted in smoke units. More polluting and darker the colour of the smoke, the more harmful it is. The smoke indicator is as shown in figure 5.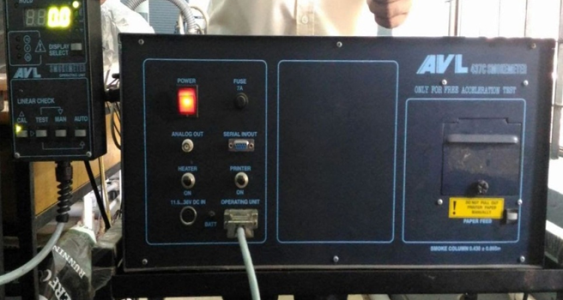 | Figure 5. Smoke indicator |
3.3. Engine Specification
The diesel engine test rig had the following specifications as listed in table 2. Four-stroke cycle, Single cylinder, totally enclosed, Constant Speed and Water Cooled.Table 2. Combustion properties of Diesel, Plastic fuel, B5, B10 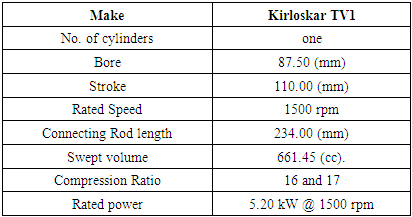 |
| |
|
4. Results and Discussions
Various performance parameters were used to evaluate and analyse the efficiency of the waste plastic fuel. The results obtained are compared with diesel at compression ratio of 17 and a blend of waste plastic fuel with diesel i.e., B5 blend at a compression ratio of 16 and 17.
4.1. Results of Performance Characteristics
The following are engine details and properties of B5 blend.Table 3. Performance Parameters 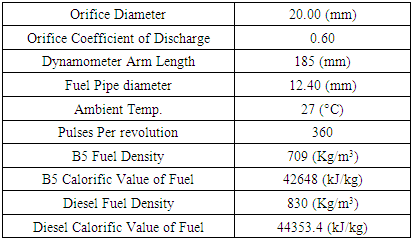 |
| |
|
The fuel properties indicate that the blend of B5 is best suitable to be run in the engine with no engine modifications.
4.1.1. Effect of Specific Fuel Consumption of the Engine at Different Brake Power
The figure 6 indicates that the SFC decreases with increase BP. It is seen from the graph that at brake power of 3.27 kW the Specific Fuel Consumption of B5 at CR16 and CR17 and Diesel at CR17 to be .27 kg/kWh, 0.28 kg/kWh and 0.3 kg/kWh. SFC is inversely proportional to the efficiency of the engine. Lower value of SFC leads to higher efficiency of the engine. 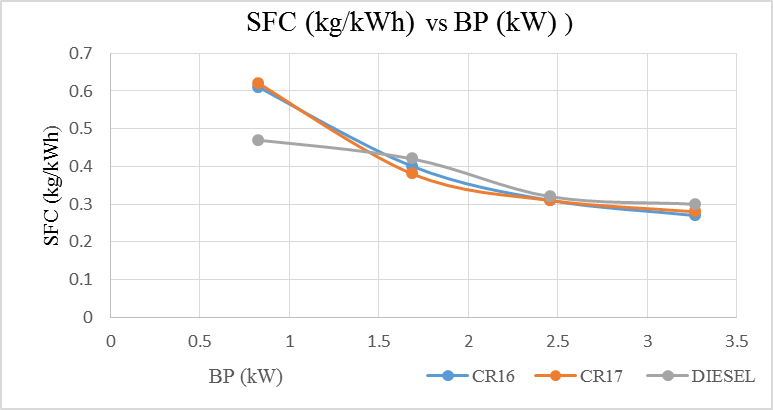 | Figure 6. Variation of SFC with the brake power |
4.1.2. Effect of Brake Thermal Efficiency of the Engine at Different Brake Power
The figure 7 indicates that BTE of diesel is 28.38% at BP of 3.27 kW and 30.89%, 29.68% for B5 fuel at CR16 and CR17 respectively. It is seen that there is a 1% increase in BTE of B5 fuel at CR17 and diesel at CR17. The increase in BTE is due to the reduction in viscosity and fuel atomization. Fuel atomization leads to improved fuel air mixing.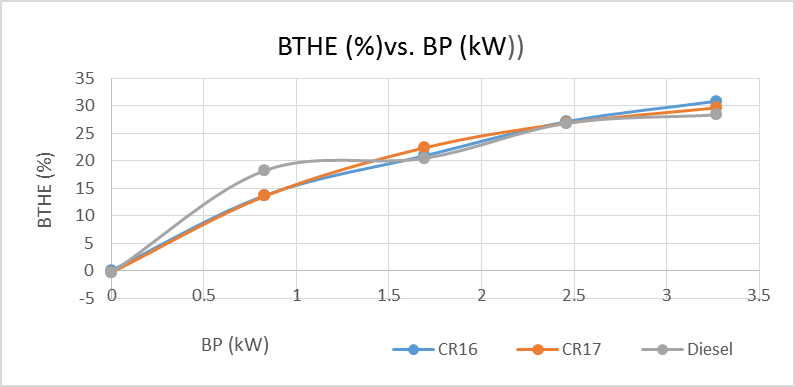 | Figure 7. Variation of Brake Thermal Efficiency with the brake power |
4.1.3. Effect of Volumetric Efficiency of the Engine at Different Brake Power
Variation of volumetric efficiency with brake power is shown in figure 8. The volumetric efficiency decreases with increase in brake power. The volumetric efficiency of diesel varies from 80.06% to 77.2% for different brake Power. The declining nature of B5 fuel at CR16 and CR17 is due to the less amount of air flow which affects the volumetric efficiency.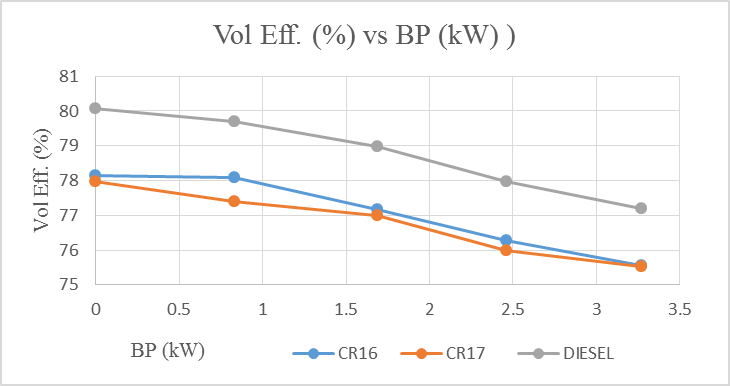 | Figure 8. Variation of Volumetric Efficiency with Brake Power |
4.2. Results of Emission Characteristics
The following are emission results obtained with B5 blend at a compression ratio of 16 and17.
4.2.1. Effect of Emission of Hydrocarbons at Different Brake Power
The Figure 9 shows variation of HC with the brake power. At the brake power of 3.27 kW diesels give value of 28 while B5 at CR17 and B5 at CR 16 show 30 and 32 respectively. The value of B5 at CR 17 is greater than diesel at CR17 at max power comparing with the start where the diesel leads the B5 fuel at CR 17. The B5 fuel emits more HC than diesel. 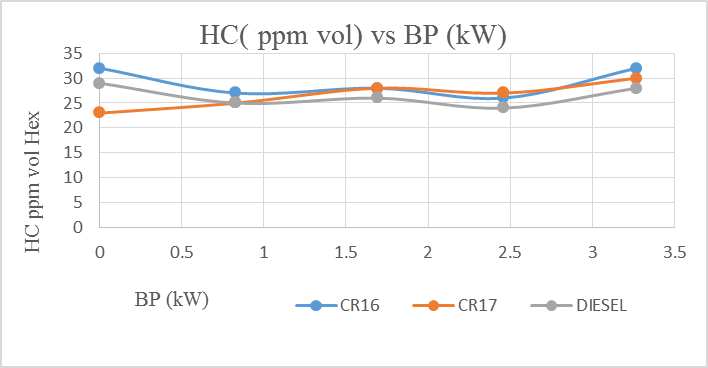 | Figure 9. Variation of HC with the brake power |
4.2.2. Effect of Emission of Oxides of Nitrogen (NOX) at Different Brake Power
The Figure 10 indicates the variation of NOX with BP. From the graph it is seen that at BP of 3.27 kW. The NOX emission is 1200 ppm vol for B5 fuel and shows the same characteristics as that of diesel.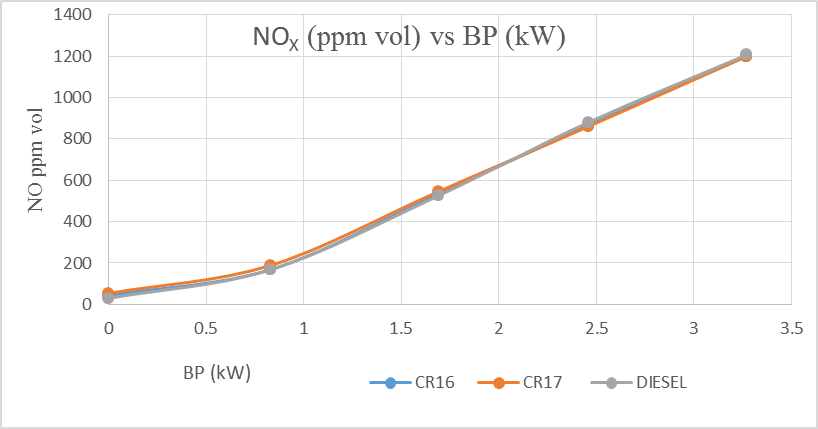 | Figure 10. Variation of oxides of nitrogen with the brake power |
4.2.3. Effect of Emission of Carbon Dioxide at Different Brake Power
The emission of CO2 to atmosphere is harmful for the environment. Figure 11 shows emission of carbon dioxide by B5 at CR 16 and 17 is more than diesel. The volume of CO2 emitted by diesel is 6.9 at the power of 3.27 KW and the emissions of B5 at CR 16 and CR 17 is 7.4 and 7.5 respectively. The three exhibit a similar nature in the graph. The reason for diesel to emit less CO2 is due to better combustion of diesel than B5.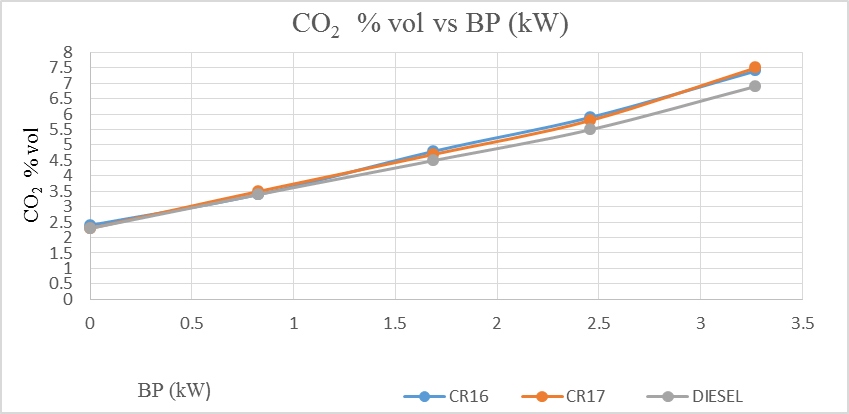 | Figure 11. Variation of oxides of nitrogen with the brake power |
4.2.4. Effect of Emission Carbon monoxide at Different Brake Power
The figure 12 indicates the variation of emission of carbon monoxide with Brake Power. Diesel and B5 fuel CR17 emit the same amount of carbon monoxide i.e. 0.06% vol at a BP of 3.27 kW. It is Cleary seen from the graph that the emission of carbon monoxide reduces with increase in BP. The formation of the carbon monoxide is due the incomplete combustion of the fuel.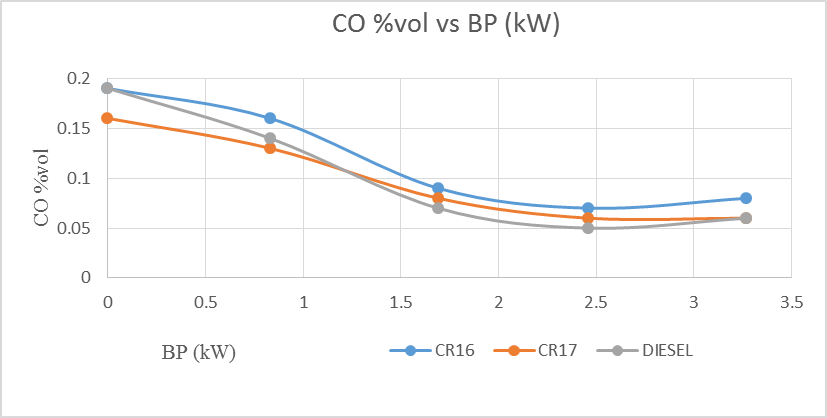 | Figure 12. Variation of CO with the brake power |
4.2.5. Effect of Emission of Oxygen at Different Brake Power
The figure 13 shows the Variation of O2 with the brake power. The nature of the graph is a declining one i.e., emission of O2 reduces as the power increases. Diesel at CR 17 emits more oxygen than B5 fuel at CR 16 and 17. The volume of oxygen emitted by diesel is 11.45 at max brake power of 3.27 while B5 at CR 16 and 17 gives out volume of 10.73 and 10.68 respectively.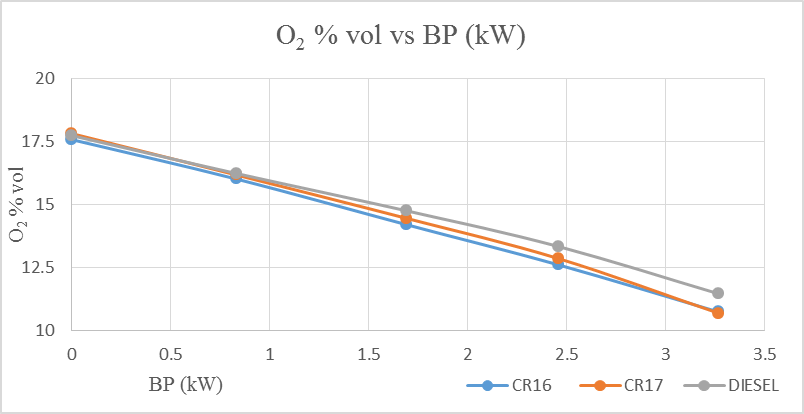 | Figure 13. Variation of Oxygen with the brake power |
4.2.6. Effect of Emission of Smoke at Different Brake Power
Emission of Smoke is harmful for human beings and also the atmosphere. Figure 14 shows emission of smoke increase as power increases for the three set of fuel B5 at CR 17 emits lesser amount of smoke than diesel at same compression ratio. The increase in emission of smoke for B5 at CR 17 is from 14.2 at the start to 53.7 at maximum power whereas for diesel it is from 20.9 at the start to 53.9 at maximum power. It shows B5 at CR 17 is better than diesel in the smoke aspect.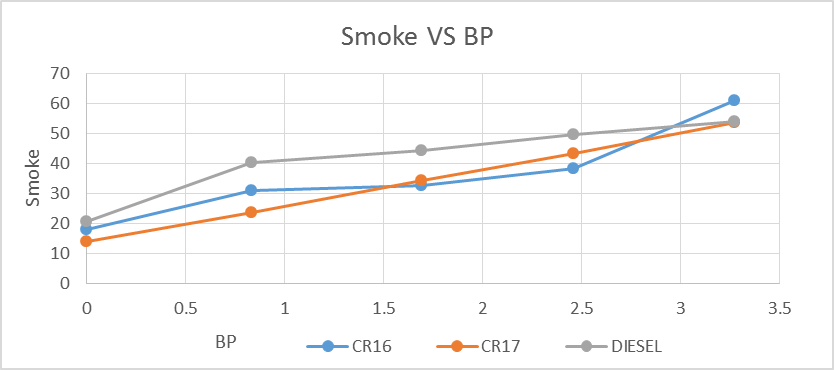 | Figure 14. Variation of smoke with the brake power |
4.3. Results of Combustion Characteristics
The following are combustion results obtained with B5 blend at a compression ratio of 16 and 17.
4.3.1. Effect Of Cylinder Pressure (P-θ diagram)
From the figure15 it is noticed that the start of combustion for B5 at CR16 is at 8 deg before TDC and the peak pressure is at 58 bar at 3 deg after TDC.  | Figure 15. P-θ diagram of B5 at CR 16 |
From the figure16 it is noticed that the start of combustion for B5 at CR16 is at 6 deg before TDC and the peak pressure is at 62 bar at 5 deg after TDC.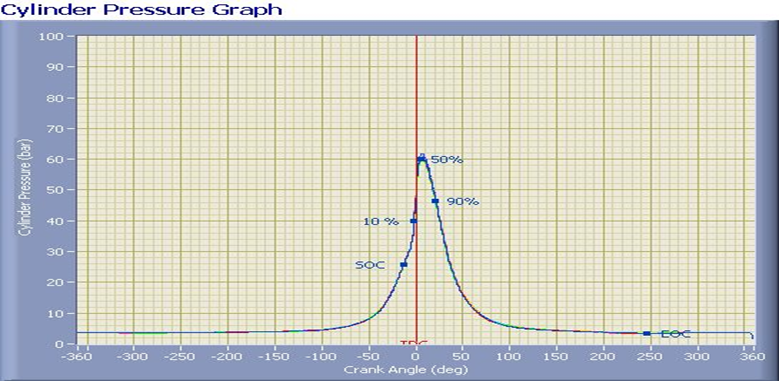 | Figure 16. P-θ diagram of B5 at CR 17 |
5. Conclusions
The various performance parameters tests to evaluate and analyse the efficiency of the waste plastic fuel was conducted. The results obtained were compared with diesel at compression ratio of 17 and a blend of waste plastic fuel with diesel i.e., B5 blend at a compression ratio of 16 and 17 This investigation leads to following conclusions:1. Thermal cracking or pyrolysis is one of the best methods to reduce load of plastic waste on available landfills.2. The addition of zeolite catalyst helps in optimizing the thermal cracking process of plastic thus producing an increase in yield of the fuel.3. The engine could be run by B5 blend at CR 16 and 17 similar to diesel4. The blend fuel shows similar characteristics with diesel.5. The smoke emitted by B5 at CR17 is less than diesel.
References
[1] | D. Damodharan, A.P. Sathiyagnanam, D. Rana, B. Rajesh Kumar, S. Saravanan “Extraction and characterization of wasteplasticoil (WPO) with the effect of n-butanol addition on the performance and emissions of a DI diesel engine fueled with WPO/dieselblends” J. Breckling, Ed., The Analysis of Directional Time Series: Applications to Wind Speed and Direction, ser. Lecture Notes in Statistics. Berlin, Germany: Springer, 1989, vol. 61. |
[2] | Viswanath K. Kaimal, P. Vijayabalan “An investigation on the effects of using DEE additive in a DI diesel engine fuelled with wasteplasticoil” M. Wegmuller, J. P. von der Weid, P. Oberson, and N. Gisin, “High resolution fiber distributed measurements with coherent OFDR,” in Proc. ECOC’00, 2000, paper 11.3.4, p. 109. |
[3] | Guohong Tian, Ioannis Kalargaris, Sai Gu “The utilisation of oils produced from plasticwaste at different pyrolysis temperatures in a DI diesel engine”. |
[4] | Ioannis Kalargaris “Experimental evaluation of a dieselengin e fuelled by pyrolysis oils produced from low-density polyethylene and ethylene–vinyl acetate plastics”M. Shell. (2002) IEEEtran homepage on CTAN. [Online]. Available: http://www.ctan.org/tex-archive/macros/latex/contrib/supported/IEEEtran/. |
[5] | Viswanath K. Kaimal, P. Vijayabalan “A detailed study of combustion characteristics of a DI diesel engine using wasteplasticoil and its blends”. |
[6] | Viswanath K. Kaimal, P. Vijayabalan “A study on synthesis of energy fuel from waste plastic and assessment of its potential as an alternative fuel for diesel engines”. |
[7] | M. Mani, G. Nagarajan, S. Sampath “Characterisation and effect of using wasteplasticoil and dieselfuelblends in compression ignition engine”. |
[8] | Senthil Kumar, G. Sankaranarayanan “Investigation on environmental factors of wasteplastics into oil and its emulsion to control the emission in DI diesel engine”. |
[9] | N. Miskolczi, A. Angyal, L. Bartha, I. Valkai, Fuels by pyrolysis of waste plastics from agricultural and packaging sectors in a pilot scale reactor Fuel Processing Technology 90 (2009) 1032–1041. |
[10] | R. Miandad, M.A. Barakat [“Effect of plasticwaste types on pyrolysis liquid oil”. |
[11] | A. Corsini, A. Marchegiani, F. Rispoli, F. Sciulli, P. Venturini “Vegetable Oils as Fuels in Diesel Engine. Engine Performance and Emissions” Owen, D. R. J., and Hinton, E., 1980, Finite elements in plasticity-theory and practice, Pineridge Press, Swansea. |