John Paul Vas, Ramya M., Ashlin Leroy Dsilva, Earl Serrao, Farish Demash, Joshua Damien Dsa
Mechanical Engineering Department, St. Joseph Engineering College, Mangaluru, India (VTU)
Correspondence to: John Paul Vas, Mechanical Engineering Department, St. Joseph Engineering College, Mangaluru, India (VTU).
Email: |  |
Copyright © 2017 Scientific & Academic Publishing. All Rights Reserved.
This work is licensed under the Creative Commons Attribution International License (CC BY).
http://creativecommons.org/licenses/by/4.0/

Abstract
One of the major concerns for extensive use of the plastics is the disposal of the waste plastic. Statistics show that approximately 10% of the plastic is recycled, 25% is incinerated and the remaining 65% is dumped in landfills. Plastics may take up to billions of years to degrade naturally. The continuous disposal of plastic in the landfill would definitely cause serious environmental problem. Therefore, we need to look into alternate methods to solve the problems associated with disposal of plastic waste. Thermal cracking or pyrolysis is one of the recycling options for plastic waste which involves heating of organic material at elevated temperature in absence of oxygen. It is one of the best methods to reduce load of plastic waste on available landfills. It converts plastic waste into different petroleum fractions which can be used directly in many industries as an alternative fuel for running boilers, generators, and turbines and also for domestic purposes. By using suitable catalyst, process yield can be enhanced and reaction time can be minimized which ultimately achieves efficiency in the process. In this project work we have attempted to investigate the conversion of waste plastic into liquid fuel by using pyrolysis process. A pyrolysis unit is to be designed, fabricated and evaluated for various kinds of plastic wastes, properties of liquid fuels obtained are determined. In order to enhance the yield and quality of fuel a catalyst –Zeolite is used. To remove any oxygen content and create an inert atmosphere nitrogen gas is used. To accommodate these changes some alterations in the design of the reactor are made. The liquid fuel obtained will be tested and compared with the fuel obtained without using catalyst as well as with standard fuel such as diesel. These changes incorporated are expected to increase the yield and quality of the fuel obtained.
Keywords:
Plastic, Thermal cracking, Zeolite catalyst, Catalytic cracking, Fuel
Cite this paper: John Paul Vas, Ramya M., Ashlin Leroy Dsilva, Earl Serrao, Farish Demash, Joshua Damien Dsa, Production of High Grade Liquid Fuel for CI Engine by Thermo-Catalytic Cracking of Waste Plastic, Energy and Power, Vol. 7 No. 3, 2017, pp. 81-87. doi: 10.5923/j.ep.20170703.05.
1. Introduction
Plastic is a high molecular weight material that was invented by Alexander Parkes in 1862 [1]. Plastics are also called polymers. The term polymer means a molecule made up by repetition of simple unit. Plastic is one of the most commonly used materials in daily life which can be classified in many ways such as, based on its chemical structure, synthesis process, density, and other properties. In order to assist recycling of the waste plastic, Society of Plastic Industry (SPI) defined a resin identification code system that divides plastics into the following seven groups based on the chemical structure and applications: PET (Polyethylene Terephthalate), HDPE (High Density Polyethylene), PVC (Polyvinyl Chloride), LDPE (Low Density Polyethylene), PP (Polypropylene), PS (Polystyrene) and others. Most of the plastic waste generated is disposed of in landfills. In order to reduce plastic disposal in landfills, recycling is considered as another alternative to manage plastic waste. Recycling plastic has proven difficult and it can be costly because of the constraints in water contamination and inadequate separation prior to recycling that is labour intensive. Separation is needed since plastics are made up of different resin compounds, transparency and colour. Normally, pigmented or dyed plastics have lower market value. Clearly transparent plastics are often desirable by the manufacturers since they can be dyed to transform into new products, thus have greater flexibility. With the stringent requirement to get high value product, recycling plastic becomes quite challenging nowadays. Although plastic recycling is able to reduce some amount of plastic waste, a more reliable and sustainable method has to be established. Since high demand of plastics have been received each year, the reduction of fossil fuels such as coal, gas and especially petroleum that made up plastic has gained great interest by many researchers to discover and develop potential energy resources due to the rise in energy demand. Some of the new energy resources that have been explored include solar energy, wind power, geothermal and hydropower technology. Recently, the energy conversion from waste has been an intelligent way to fully utilize the waste to meet the increased energy demand. The conversion of plastics to valuable energy is possible as they are derived from petrochemical source, essentially having high calorific value. This is done by a process known as pyrolysis or thermal cracking.Thermal cracking or pyrolysis is the process of thermally degrading long chain polymer molecules into smaller, less complex molecules through heat and pressure. The process requires intense heat with shorter duration and in absence of oxygen. It prevents the formation of COx, NOx and SOx due to absence of oxygen [2]. The three major products that are produced during pyrolysis are oil, gas and char which are valuable for industries especially refineries. Thermal cracking was chosen by many researchers since the process was able to produce high amount of liquid oil up to 80 wt% at a moderate temperature of around 500°C [2]. In addition, thermal cracking is also very flexible since the process parameters can be manipulated to optimize the product yield based on preferences. The liquid oil produced can be used in multiple applications such as furnaces, boilers, turbines and diesel engines without the need of upgrading or treatment. Unlike recycling, thermal cracking does not cause water contamination and is considered as a green technology because the pyrolysis by-product which is gaseous has substantial calorific value that it can be reused to compensate for the overall energy requirement of the pyrolysis plant. The process handling is also much easier and flexible compared to the common recycling method since it does not need an intense sorting process, thus less labour intensive.Pyrolysis of waste plastics in the presence of a catalyst lowers the pyrolysis temperature and reaction time, increases the conversion rate of waste plastics into fuel, increases the yield of fuel and satisfies the diesel and petrol quality of fuel by increasing the octane value of petrol and decreasing the pour point of diesel. The catalysts used for this purpose are solid acids such as silica, alumina, zeolite β, zeolite Y, mordenite, HZSM-5, MCM-41 etc [2]. Acidic catalysts (HZSM-5, zeolite Y, mordenite and so on) have greater efficiency compared to less acidic catalysts such as amorphous alumina silicate. The pore size and structure of catalysts determine their performance in the cracking reaction as well as products obtained.
2. Process Parameters
2.1. Chemical Composition of Feedstock
Plastics can be classified according to structural shape of polymer molecules as linear, branched, or cross-linked. A cross-linked polymer can be described as an interconnected branched polymer with all polymer chains linked to form a large molecule. Thus, the cross-linked polymer constitutes a large molecule. Theoretically, the molecular weight of a cross linked polymer can be infinite. In reality, the molecular weight of a cross linked polymer will be limited due to breaking down of the molecular inter-connections during the processing or the weight of the polymer sample. The cross-linked polymer cannot be dissolved in solvents or be melted by heat because of their network structure. For example, PEX, a common abbreviate of cross-linked polyethylene, is widely used in oil and water piping. In pyrolysis process, cross linked polymer will crack rather than melt or evaporate. This is different from the reactions of linear or branched polymers in pyrolysis process.
2.2. Temperature
The temperature has the greatest impact on reaction rate that may influence product composition of liquid, gaseous and char for all plastics. The operating temperature required relies strongly on the product preference. If gaseous or char product was preferred, higher temperature more than 500°C was suggested [3]. If liquid was preferred instead, lower temperature in the range of 300–500°C was recommended.
2.3. Type of Reactor
From the literature study, it was concluded that the batch or semi-batch reactors are the best reactors to be used in thermal pyrolysis to obtain high liquid yield since the parameters can be easily controlled. However, batch operation was not suitable for large scale production since it required high operating cost for feedstock recharging and thus, it was more appropriate for laboratory experiment. Fluidized bed reactor is concluded to be the best reactor to perform catalytic plastic pyrolysis since the catalyst can be reused many times without the need of discharging, considering catalyst is a very expensive substance in the industry. Besides, it is more flexible than the batch reactor since frequent feedstock charging can be avoided for continuous process and the process does not need to resume often [3]. Hence, fluidized bed reactor would be the most suitable reactor for large scale operation in terms of economic point of view.
2.4. Pressure
Operating pressure has significantly effect on both the pyrolysis process and the products. The boiling points of the pyrolysis products are increased under higher pressure, therefore, under pressurised environment heavy hydrocarbons are further pyrolyzed instead of vaporized at given operation temperature [1]. In effect, under pressurized pyrolysis, more energy is required for further hydrocarbon cracking. The average molecular weight of gas product also decreases with the increase of pressure. The influence of pressure on the concentration of double bond, C=C, of the liquid product was not significant. In summary, pressure has major effects on the pyrolysis reaction and the distribution of PE pyrolysis products, but has minor effect on the double bond components. Moreover, in terms of economic viewpoint, additional units such as compressor and pressure transmitter need to be added into the overall system which increases the operating cost if the factor of pressure is considered.
2.5. Residence Time
Residence time can be defined as average amount of time that the particle spends in the reactor and it may influence product distribution [2]. Longer residence time increases the conversion of primary product, thus more thermal stable product is yielded such as light molecular weight hydrocarbons and non-condensable gas. Nevertheless, there is a temperature limitation in the process that may influence the product distribution where until that instant, the residence time has not much effect on the product distribution. A study on the effect of residence time and temperature on product distribution of HDPE thermal cracking in fluidized bed reactor was conducted. It was found that higher liquid yield obtained at longer residence time (2.57 s) when the temperature was not more than 685°C. However, the residence time had less influence on the liquid and gaseous yield at higher temperature above 685°C.
2.6. Use of Zeolite Catalyst
Zeolites are crystalline micro-porous aluminosilicates. Therefore, Si/Al ratio is the most important parameter for zeolites which is applied to classify the zeolites. The high-silica zeolites, with a Si/Al ratio greater than five such as ZSM-5, are widely used in petrochemical industries [4]. The high silica content in the catalyst makes the framework to stand high temperatures that this type catalyst is suitable for high temperature pyrolysis and regeneration cycle. A high dispersion of acidic protons assures that each proton performs maximum acidity. Consequently, acidity is also an indicator to reflect the property of zeolites. A test was conducted on the three types of nanocrystalline zeolite with different Si/Al ratios and specific surface area. High Si/Al ratio implies a high total acidity of zeolites. These zeolites are preferred for polyolefin cracking. Lower Si/Al ratio implies lower acidity and smaller crystal size of zeolite provide higher efficiency in terms of conversion. The use of catalyst is dependent on the difficulty of changing catalyst, the cost of catalyst, and the efficiency of the catalyst. It was proved that the ratio of SiO2/Al2O3 of the HZSM-5 zeolite highly affected the product fraction yield in HDPE pyrolysis. Low ratio of SiO2/Al2O3 indicated the high acidity of the zeolite. The highest acidic catalyst (SiO2/Al2O3 = 30) was more active in cracking waxes, thus producing higher light olefins and lower heavy fraction of C12–C20 compared than the lowest acidic catalyst (SiO2/Al2O3 = 280). The reduction of SiO2/Al2O3 ratio from 280 to 30 improved the yield of light olefins from 35.5 to 58.0 wt % and decreased the yield of C12–C20 from 28.0 to 5.3 wt%. Besides, the reduction of SiO2/Al2O3 ratio in zeolite also raises the yield of light alkanes and aromatics [4]. The highest acidity catalyst with the lowest ratio of SiO2/Al2O3 led to a higher octane number with high content of aromatics and benzene, but lower concentration of olefins.
2.7. Type and Rate of Fluidizing Gas
Fluidizing gas is an inert gas (also known as carrier gas) which only engaged in transportation of vaporized products without taking part in the pyrolysis. There are many type of fluidizing gas that can be used for the plastic pyrolysis such as nitrogen, helium, argon, ethylene, propylene and hydrogen [5]. Each type of fluidizing gas has different reactivity based on its molecular weight. Nevertheless, of all those gases, nitrogen was commonly used by most researchers as fluidizing gas in plastic pyrolysis since it was easier and safer to handle than the high reactivity gas like hydrogen and propylene due to their flammability hazard. Besides, even though helium was able to produce high liquid yield after hydrogen, it was rarely used since the availability was limited and more expensive than nitrogen. Besides the type of fluidizing gas, the fluidizing flow rate also may influence the final product distribution. It was found that the rate of degradation dropped instantly at the lowest fluidizing flow rate of 300 ml/min [5]. The contact time for primary product is high at lower flow rate, causing the formation of coke precursor (BTX) to increase with the secondary product obtained even though the overall degradation rate is slower. This was indicated by the high residue left when lower fluidizing flow rate was applied. The gasoline and hydrocarbon gases fraction were also maximized at the highest fluidizing flow rate of 900 ml/min. Hence, the type and rate of fluidizing gas are also very important in plastic pyrolysis.
3. Methodology
Thermal cracking or pyrolysis is a thermochemical decomposition of organic material at elevated temperature in the absence of oxygen. In this process, long polymer molecules are broken down into shorter chains of hydrocarbons with the help of heat and pressure. Essentially the process is mimicking the natural process by which organic materials are broken down into oil in the nature which takes millions of years. The pyrolysis process does this with intense heat in a closed system in a short amount of time. A catalyst can be used to lower the temperature and increase the yield [6].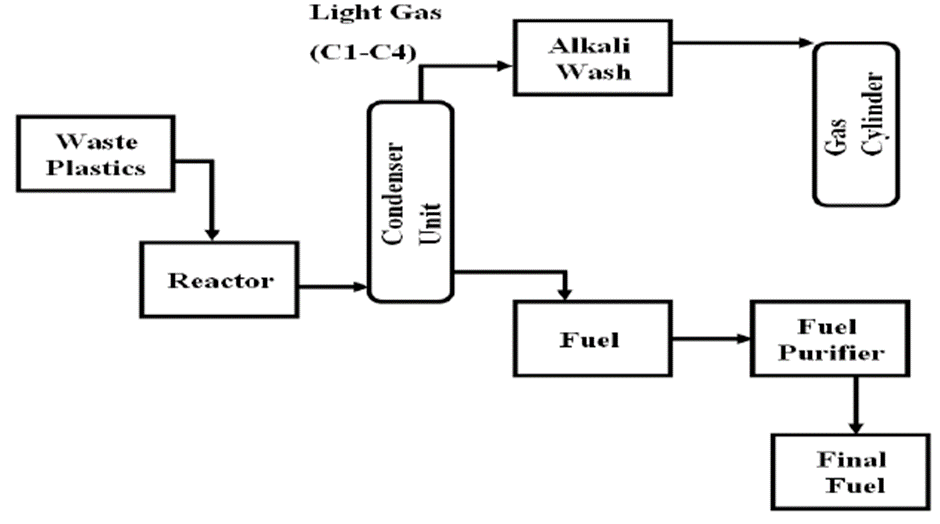 | Figure 1. Block diagram of the thermal cracking of plastic [6] |
The process includes the following steps: 1) Shredding: The plastic waste material is segregated and cleaned. Then it is shredded to speed up the reaction and to ensure that the reaction is complete. 2) Anaerobic heating: The shredded material is heated in a controlled environment in an oxygen-free reactor. The present work includes replacing the working fluid with nitrogen gas. One of the most crucial factors in this operation is maintaining the right temperature (~430°C for plastic) and the rate of heating, as they define the quality and the quantity of the final product. The work also includes introducing a catalyst which will effectively lower the required temperature thereby reducing energy consumption. 3) Condensation: The gas that comes out from the reactor must be condensed by passing it through a condensation tube or by directly bubbling it in water. 4) Distillation: This mixture of liquid fuel that is obtained can be used as furnace oil but it isn't sufficiently pure for engines. If the liquid fuel is to be used as an engine fuel, we need to extract and purify the desired products from the mixture through fractional distillation. 5) Analysis: The liquid fuel obtained from distillation is tested for various physical and chemical properties.
4. Design and Fabrication
The apparatus shown is figure 4 was constructed as follows:
4.1. Pyrolysis Reactor
The pyrolysis reactor is designed for pyrolysis of waste plastic (PP). The reactor is a cylindrical, batch type, fixed bed reactor. The top side of reactor can be open for feeding the raw material and solid residue (char) can be removed at the end of the experiment. The temperature inside the reactor is measured by using a thermocouple. During the reaction, the top side is kept closed by two flanges tightly. In addition to it, two air tight oil gaskets are placed in order to minimize the escape of gas from the reactor. This prevents ingression of atmospheric air into the reactor. The reactor is provided with a ceramic blanket insulation and a MS Perforated sheet with plaster for the insulation cover on the outer side to prevent the heat loss to the surrounding. An exit pipe at the side carries away the evolved gases during pyrolysis. Two inlets are provided for nitrogen at the side of the reactor.
4.2. Electrical Heater
An electrical heater (spiral type) is provided inside the reactor for thermal degradation of waste plastic. The thermal degradation of waste plastic is caused by electrical heating. SS terminal box for heater is placed outside the reactor and is connected to the digital temperature control box.
4.3. Condenser
A condenser is provided for condensation of volatile gases which is then known as Pyrolytic oil. The reactor is connected to the condenser by MS coupling. Hot gases passed through the inside tube of condenser are condensed with the help of circulation of cold water surrounding the tube through a water inlet located at the lower side of the condenser. The water exits through a water outlet located at the upper side of the condenser. The temperature inside the condenser is measured by using a thermocouple. A mild steel cone is attached at the bottom of the condenser. A mild steel ball valve is attached to the cone which is used to drain the liquid fuel. The uncondensed gases are passed through a pipe which is bubbled under water through a hose.
4.4. Frame and Digital Temperature Control (DTC) Box
The entire frame is made up of GI square tubes. The DTC box is mounted upon an angler frame. Both the reactor and condenser thermocouples are connected to the DTC box which indicates the temperatures within the reactor and condenser. 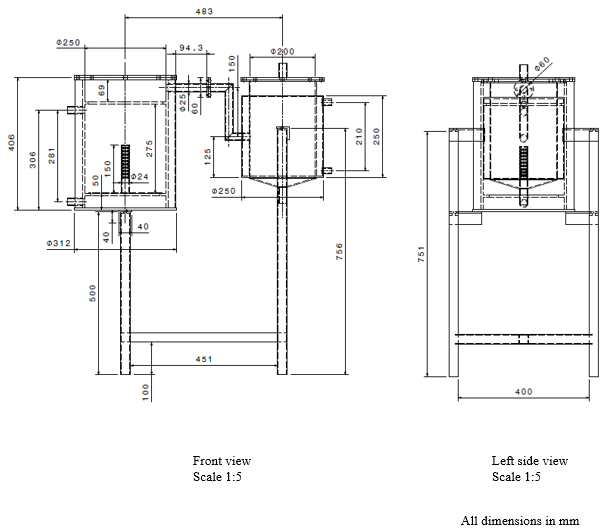 | Figure 2. Front and side views |
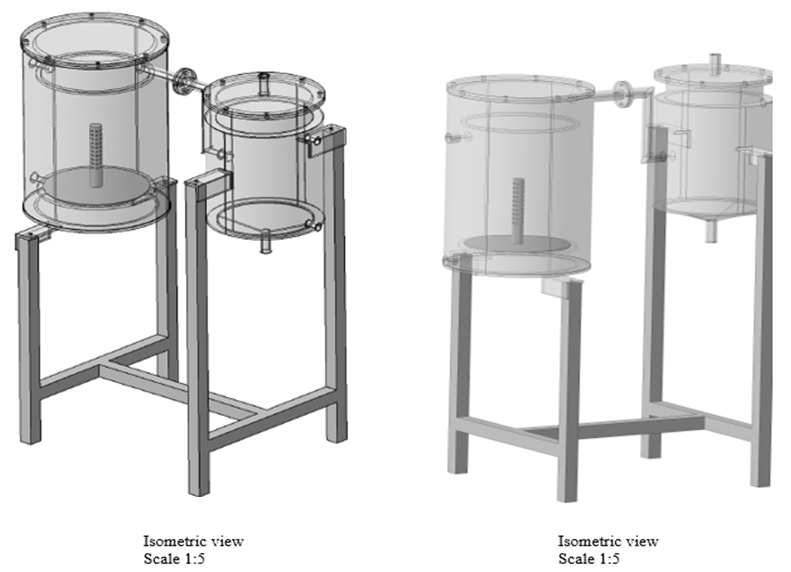 | Figure 3. Isometric views |
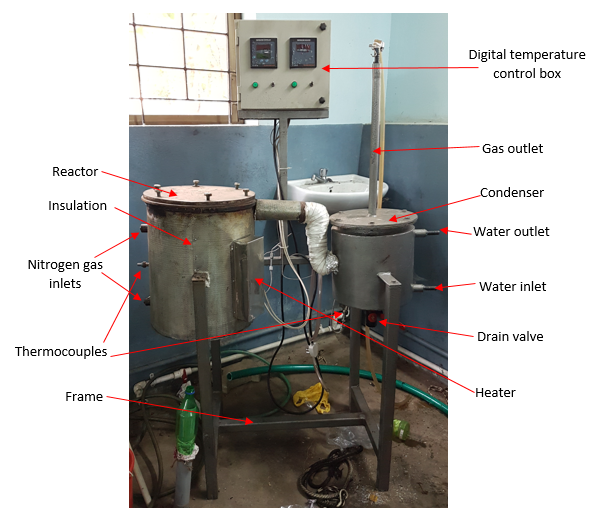 | Figure 4. Final apparatus |
5. Experimentation
The thermal cracking process is conducted by using the apparatus shown in figure 4. The reactor is completely filled with Polypropylene plastic. Water at room temperature is used as a coolant in the condenser. Three tests are conducted by varying the ratio of plastic to catalyst and by replacing the working fluid with nitrogen gas. The details of the tests are explained below: Sample 1: Feed: PP plastic + Nitrogen gas (9 litres/hr) Maximum reactor temperature attained: 634°C Maximum condenser temperature attained: 62°C Time taken: 108 mins Liquid yield obtained: 2.5 litres Sample 2: Feed: PP plastic (5 kg) + Zeolite catalyst (1 kg) + Nitrogen gas (9 litres/hr) Maximum reactor temperature attained: 467°C Maximum condenser temperature attained: 53°C Time taken: 78 mins Liquid yield obtained: 4 litres Sample 3: Feed: PP plastic (5 kg) + Zeolite catalyst (2 kg) + Nitrogen gas (9 litres/hr) Maximum reactor temperature attained: 449°C Maximum condenser temperature attained: 55°C Time taken: 67 mins Liquid yield obtained: 4.7 litres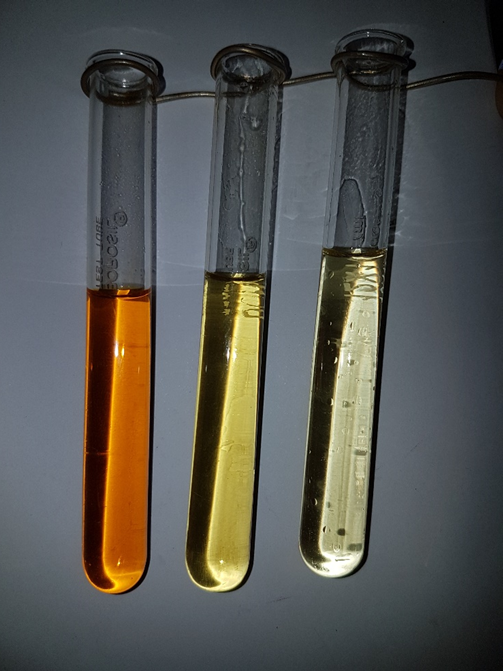 | Figure 5. Extracted samples used for testing. Sample 1 (left), Sample 2 (middle), Sample 3 (right) |
6. Results and Discussion
100 ml of each of the three samples is filtered and taken to the Quality Control Laboratory at MRPL, Mangalore for testing. Properties such as density, kinematic viscosity, Sulphur content and moisture content are determined. The boiling point distribution of the samples is determined using gas chromatography. ASTM D7500 is the simulated distillation method used for the determination of boiling range distribution of the sample by gas chromatography. A non-polar open tubular gas chromatographic column is used to elute the hydrocarbon components of the sample in the order increasing boiling point. The gas chromatographic instrument with Flame ionization detector, Agilent 7890B (USA) is used for this study. Fused Silica and stainless steel columns having 0.53 to 0.75 mm internal diameter with cross linked or bonded 100% dimethyl polysiloxane stationary phases with film thickness of 0.09 to 0.17 m have been used. The sample aliquot (0.5 g) is diluted with viscosity reducing solvent CS2 (10 ml) and introduced into the chromatographic system. The column oven temperature is raised at a specified linear rate to affect separation of the hydrocarbon components in order of increasing boiling point. The elution of sample components is quantitatively determined using flame ionization detector. The detector signal is recorded as area slices for consecutive retention time intervals during the analysis.The maximum reactor temperature attained by the using the sample without the catalyst (sample 1) is 634°C, whereas the maximum reactor temperatures attained by using the samples with the catalyst (samples 2 and 3) are 467°C and 449°C respectively. This shows that the addition of zeolite catalyst helps in reducing the maximum temperature required to thermally degrade plastic.The time taken to complete the thermal cracking process by using sample 1 is 108 mins, whereas the time taken to complete the process by using samples 2 and 3 are 78 mins and 67 mins respectively. This shows that the addition of zeolite catalyst helps in minimizing the time consumed to complete the thermal cracking process.Since the addition of zeolite catalyst lowers the maximum reactor temperature attained and also the total time consumed to complete the process, the cost of electricity required to heat the reactor is also reduced.From table 1 we can see that the Sulphur content and moisture content of the liquid fuel obtained by using samples 2 and 3 are significantly lower than that of the liquid fuel obtained by using sample 1. This confirms that the addition on zeolite catalyst reduces the toxicity of the liquid fuel and increases the combustion characteristics of the liquid fuel.Table 1. Sample properties 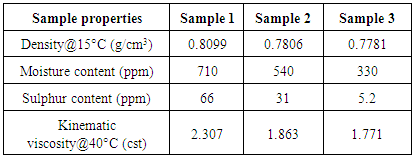 |
| |
|
From table 2 we can see that the final boiling point of the liquid fuel obtained from the samples reduces with the addition of the catalyst. The liquid fuel obtained from sample 3 requires a lower amount of heat energy to convert into the vapour state compared to the fuels obtained from samples 1 and 2.Table 2. Boiling point distribution 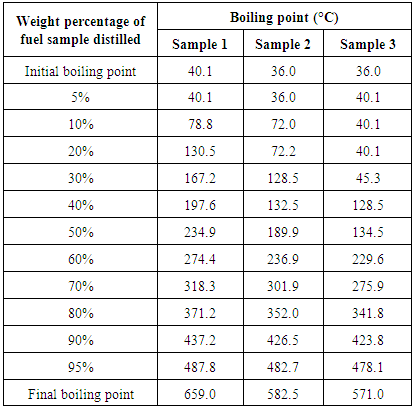 |
| |
|
On comparing sample 2 and sample 3, we can conclude that by doubling the amount of zeolite catalyst used, the sulphur content and moisture content of the liquid fuel reduces significantly, the maximum reactor temperature attained and the time taken to complete the process reduces slightly whereas the liquid yield obtained increases moderately.It can also be seen that the addition of zeolite catalyst lowers the condenser temperature only slightly.Hence, we can conclude that sample 3, with a plastic to catalyst ratio of 5:2 is the most optimized sample among the samples tested, that can be used for CI engine testing.
7. Conclusions
1. Thermal cracking or pyrolysis is one of the best methods to reduce load of plastic waste on available landfills. 2. Thermal cracking of plastic produces three products i.e., the liquid fuel, gaseous fuel and solid char and wax. 3. By using suitable catalyst, the liquid fuel yield can be enhanced and reaction time can be minimized which ultimately achieves efficiency in the process.4. The addition of catalyst also reduces the Sulphur content and the moisture content of the liquid fuel which ultimately help in improving the combustion characteristics of the fuel.5. The addition of catalyst also helps in lowering the final boiling point of the liquid fuel which helps in faster combustion of the fuel.6. Thus, we can conclude that the addition of zeolite catalyst helps in optimizing the thermal cracking process of plastic.
References
[1] | Feng Gao, “Pyrolysis of Waste Plastics into Fuels”, A thesis submitted in fulfilment of the requirements for the Degree of Doctor of Philosophy in Chemical and Process Engineering, University of Canterbury, 2010. |
[2] | Bidhya Kunwar, Bryan R. Moser, Sriraam R. Chandrasekaran, Nandakishore Rajagopala, Brajendra K. Sharma, “Catalytic and thermal depolymerization of low value post-consumer high density polyethylene plastic”, Energy, Volume 111, 15 September 2016, Pages 884–892. |
[3] | Shafferina Dayana Anuar Sharuddin, Faisal Abnisa, Wan Mohd Ashri Wan Daud, Mohamed Kheireddine Aroua, “A review on pyrolysis of plastic wastes”, Energy Conversion and Management, Volume 115, 1 May 2016, Pages 308–326. |
[4] | G. Elordi, M. Olazar, M. Artetxe, P. Castano, J. Bilbao, “Effect of the acidity of the HZSM-5 zeolite catalyst on the cracking of high density polyethylene in a conical spouted bed reactor”, Applied Catalysis A: General, Volumes 415–416, 16 February 2012, Pages 89–95. |
[5] | J. Aguado, D.P. Serrano, J.M. Escola, A. Peral, “Catalytic cracking of polyethylene over zeolite mordenite with enhanced textural properties”, Journal of Analytical and Applied Pyrolysis, Volume 85, Issues 1–2, May 2009, Pages 352–358. |
[6] | Moinuddin Sarker, Mohannad Mamunor Rashid, “First Simple and Easy Process of Thermal Degrading Municipal Waste Plastics into Fuel Resource”, IOSR Journal of Engineering (IOSRJEN) e-ISSN: 2250-3021, p-ISSN: 2278-8719, www.iosrjen.org Volume 2, Issue 9 (September 2012), PP 38-49. |