Ravikumar R.1, G. Sujaykumar2, Divakar Shetty A. S.3, Basavaraj Kambale2, Aravinda Pattar2
1Department of Mechanical Engineering, Faculty of Engineering, Christ University, Bengaluru, India
2Department of Mechanical Engineering, Yenepoya Institute of Technology, Moodbidri, India
3Department of Mechanical Engineering, Amrita School of Engineering, Bengaluru, India
Correspondence to: Ravikumar R., Department of Mechanical Engineering, Faculty of Engineering, Christ University, Bengaluru, India.
Email: |  |
Copyright © 2017 Scientific & Academic Publishing. All Rights Reserved.
This work is licensed under the Creative Commons Attribution International License (CC BY).
http://creativecommons.org/licenses/by/4.0/

Abstract
The huge quantity of waste tires presently produced in the world will certainly increase in the future as the associated automotive industries grow. The impact of waste rubber on the environment can be minimized by recycling with material or energy recovery. Pyrolysis offers an environmentally attractive method to decompose a wide range of wastes, including waste tires and produce fuel. The objective of this paper is to produce liquid fuel from waste tire, test its physical properties and evaluate diesel engine performance with various blends of biodiesel-diesel at different loading. Studies have been made for 2.5 kg, 5kg and 7.5 kg load conditions and with and without using blower for combustion are made. Brake power, specific fuel consumption varies with varying load conditions for different blends. The brake thermal efficiency and specific fuel consumption of the diesel engine has improved for Tire Oil 15% blend.
Keywords:
Waste tires, Disposal, Tire oil, Diesel
Cite this paper: Ravikumar R., G. Sujaykumar, Divakar Shetty A. S., Basavaraj Kambale, Aravinda Pattar, Investigation of Effect of Tire Oil Blended Diesel on Engine Performance, Energy and Power, Vol. 7 No. 3, 2017, pp. 61-64. doi: 10.5923/j.ep.20170703.01.
1. Introduction
The disposal of scrap tires becomes a serious environmental problem. The accumulation of discarded waste tires leads to environmental pollution. A large fraction of the scrap tires is simply dumped in sites where they represent hazards such as diseases and accidental fires [1]. Rubbers are not biologically degradable, and this fact creates problems with their disposal. The impact of waste rubber on the environment can be minimized by recycling with material or energy recovery. However, during processing and moulding rubber materials are cross linked, and therefore they cannot be simply again softened and re moulded by heating [2]. Pyrolysis offers an environmentally attractive method to decompose a wide range of wastes, including waste tires. In the pyrolysis process, the organic volatile matter of tires (around 60 wt. %) is decomposed to low molecular weight products, liquids or gases, which can be used as fuels or chemicals source. The non-volatile carbon black and the inorganic components (around 40 wt. %) remain as solid residues and can be recycled in other applications [3]. Combustion of tires has been used also for generation of electrical energy. However, for minimizing emissions the conditions of the combustion process must be optimized [4]. pyrolysis oil as finished product is in great is in great demand in the market which is consumed & used by number of industries as a burning fuel. Pyrolysis oil cost is cheaper than furnace oil & light diesel oil as per Indian oil market hence, can be used as a substitute according to the various applications [5]. During fabrication of the pyrolysis unit a solid plate of cast iron is welded to the bottom end of the hollow cylinder barrel and the top end of the cylinder is welded with a hollow plate of same material and dimension now another solid plate having similar characteristics is placed on top of the cylinder. The top most plate is held in position by nut and bolt arrangement. A double layered gasket along with fine layer of grebes is placed in between the solid plate and the hollow plate and then the nut and bolt are tightened. Now a small hole is drilled in the cylinder at the upper half and to this hole a long copper tube is gas welded such that the copper tube is tilted downwards. Now the entire copper tube is covered with a galvanized iron pipe which acts as a cooling chamber.
2. Methodology
2.1. Fabrication of Tire Pyrolysis Unit
For the production of liquid tire oil, fabrication of tire pyrolysis unit has to be done. This is done by using a cast iron hollow cylinder barrel, two solid plates and one hollow plate of cast iron, a galvanized iron pipe, a copper tube and few collars. During fabrication of the pyrolysis unit a solid plate of cast iron is welded to the bottom end of the hollow cylinder barrel and the top end of the cylinder is welded with a hollow plate of same material and dimension now another solid plate having similar characteristics is placed on top of the cylinder. The top most plate is held in position by nut and bolt arrangement. A double layered gasket along with fine layer of grebes is placed in between the solid plate and the hollow plate and then the nut and bolt are tightened. Now a small hole is drilled in the cylinder at the upper half and to this hole a long copper tube is gas welded such that the copper tube is tilted downwards. Now the entire copper tube is covered with a galvanized iron pipe which acts as a cooling chamber. Two collars are provided at the two ends of the G.I pipe for water inlet and outlet. A cylinder with 36 cm diameter, 50 cm length and 0.5 cm thickness is used for pyrolysis unit. A solid plate with 40 cm diameter and 0.5 cm thickness and flat hollow plate of outer diameter 40 cm, inner diameter 32 cm and 0.5 cm thickness is used. Initially in this process scrape tire are shredded into small pieces by using different cutting technique and shredded. Now this forms the primary feed stock for the pyrolysis process. Now this shredded tire is accurately weighed to the required quantity and is feed into the cast iron cylinder, next the cylinder top is closed by using a cast iron solid plate. Between the cylinder and the solid plate a doubled layered gasket coated with thin layer of grease so places so that there is no temperature or pressure loss. Now the solid plate, gasket and the cylinder is tightened against each other by using nut and bolts. Heat is then supplied from the combustion chamber with the help of wood and charcoal as burning agent also blower is used to increase the rate of heat transfer. As the temperature starts to increase the shredded tire starts to undergo chemical changes and phase changes when the temperature reaches about 60°C the rubber inside starts to melt and only gases are produced, this temperature is indicated by temperature gauge. When the temperature reach 80°C large amount of vapours are produced and this vapour is condensed with help of condenser hear we make use of water as a condensing agent. The pyrolysis unit is shown in the figure 1.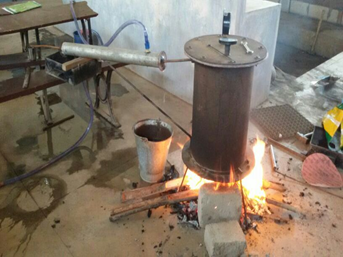 | Figure 1. Working of Pyrolysis unit |
2.2. Conversion of Waste Tires into Useful Liquid Fuel Component
The liquid fuel component is produced from thermal pyrolysis process. Thermal pyrolysis process is carried in a tire pyrolysis unit. The feedstock raw material is converted into liquid tire oil using vaporization and condensation process within the initially fabricated unit. Macro and Micro hydrocarbons are broken down to convert scrape rubber into tire oil product in thermal pyrolysis process. At the temperature of about 90°C the product (rubber oil) is obtained by condensing the vapour through the copper tube in the condenser tube. This liquid will be coming out of the copper tube in a drop wise form. With the increase in the temperature of about 280°C we obtain the continuous flow of rubber oil and this will be collected in a separate metallic container. The obtained solution of rubber oil is then used for the preparation of blends of 10%, 15% and 20% by mixing with diesel. These blends are then used for the determination of various properties such as flashpoint, fire point, density, dynamic viscosity and calorific value. Performance test is carried out in a single cylinder diesel engine for different blends. The required parameters are noted down and the results are obtained by calculation for all the blends separately. The results of each blend were compared to see which ratio of rubber oil and diesel give the best results. It was found that Rubber Oil 15% (Diesel-85% and Rubber Oil-15%) would give the best results for both Specific Fuel Consumption and Brake Thermal Efficiency.
2.3. Evaluation of Produced Liquid Fuel Properties
Produced liquid fuel properties were evaluated using various apparatus. The main product produced by pyrolysis plant is Tire oil (industrial fuel oil). This is used in many industries as a fuel. There are 2 types of oil we get from the process, one is normal Tire oil and other is heavy oil. Heavy oil is about 5% to 7% of Tire oil. The final percentage of oil is about 40% to 45% depends on Tire quality. Nowadays there is a great demand of fuel oil in the market, as every industry requires fuel for heating purpose. Flash and fire point of all blends were found out in Abel’s flash and fire point apparatus. Density and dynamic viscosity of all the blends including diesel were found in saybolt viscometer. Calorific value of all blends including diesel were found in bomb calorimeter.
2.4. Evaluation of Engine Performance
Engine performance is evaluated using a diesel engine setup. BP is calculated using a rope brake dynamometer. Specific fuel consumption and brake thermal efficiency are calculated for various load condition of 2.5 kg, 5 kg and 7.5 kg loads and constant speed condition of 1500 RPM. First, engine is operated only with diesel and then with the blends of different ratios of 10%, 15% and 20% of tire oil with diesel. Comparison is done with the results to evaluate the engine performance.
3. Results and Discussion
The below table 1 shows different properties of diesel, various blends and the pure rubber oil. As shown in the table diesel has high fire point compared to tire oil and the fire point decreases with increase in the blending ratio. The rubber oil has flashed and fire point at room temperature. Now the density goes on decreases from diesel to rubber oil but at the same time the dynamic viscosity and the calorific value goes on increases from diesel to rubber oil. Now since the fire point is less compared to diesel, low ignition pressure is required for the combustion of the fuel. Since the density is more and the dynamic viscosity is less of the fuel produced than the diesel low pressure ejection system can be used in the engine since the fuel flows with less friction in the ejection system compared to diesel.Table 1. Properties of Tire Oil and Blends 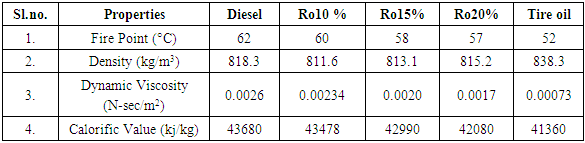 |
| |
|
Figure 2 shows increase in the brake power with increase in the load. As the readings are taken for constant RPM of 1500, Brake power is same for all the blends at respective loads.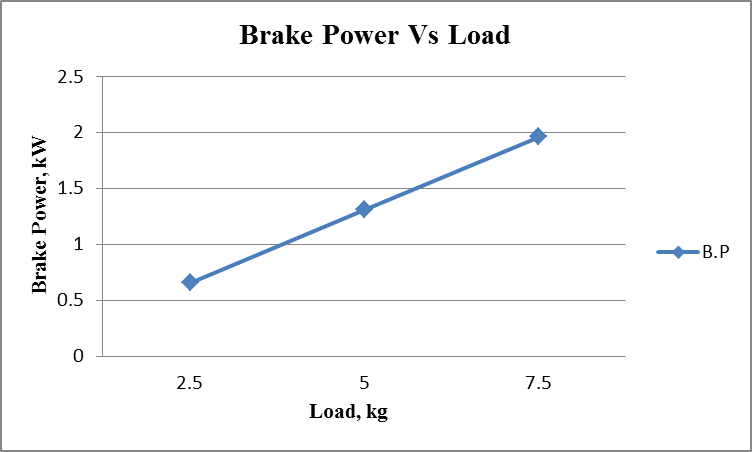 | Figure 2. Break Power v/s Load Graph |
Figure 3 and figure 4 shows that, 15% blend of tire oil with diesel gives better results with high brake thermal efficiency and low specific fuel consumption. But 20% blend of tire oil with diesel shows lower efficiency and high specific fuel consumption. Observations shows that increasing tire oil more than 15% is not suitable for engine. 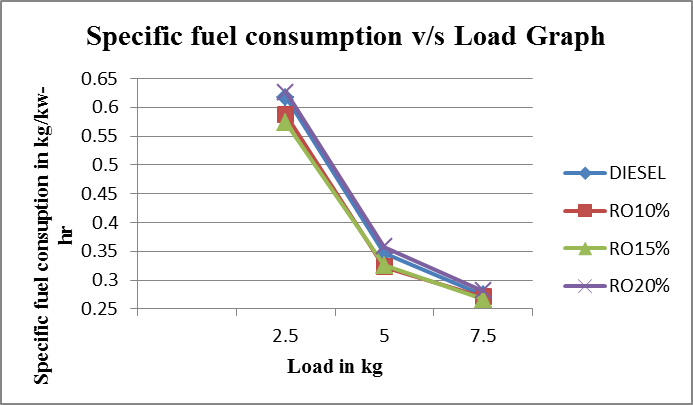 | Figure 3. Specific fuel consumption v/s Load Graph |
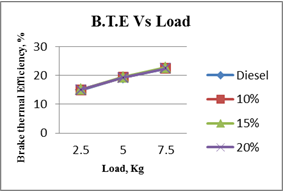 | Figure 4. Brake Thermal Efficiency v/s Load Graph |
Table 2 shows the effect of blower in tire oil production using 1kg of tire as input. Tire oil production is increased by almost 3 times than normal condition. Use of blower will decrease the black char production. That indicated maximum extraction of tire oil. But it demands extra energy supply for the blower.Table 2. Effect of Blower on Tire Oil Production  |
| |
|
4. Conclusions
Brake thermal efficiency and specific fuel consumption of the diesel engine has improved for Tire Oil 15% blend. Blend more than 15% is not suitable for engine. Uncondensed gas can be compressed and used as burning gas in houses and industries. Carbon black char has a vast application in the field of paint manufacturing. Steel wires have high demand in the cast manufacturing industries as a raw material for the furnaces used. All the properties satisfy the American Standard Testing Materials (ASTM). It is one of the best methods of waste tire management.
References
[1] | Juan F. Gonzalez, José M. Encinar, José L. Canito and Juan J. Rodríguez, Journal of Analytical and Applied Pyrolysis, vol. 58-59, 1 2001, pp. 667-683. |
[2] | M.F. Laresgoiti, B.M. Caballero, I. de Marco, A. Torres, M.A. Cabrero, M.J. Chomón, J. Anal. Appl. Pyrolysis vol. 71, 2004, pp. 917–934. |
[3] | C. Berrueco, E. Esperanza, F.J. Mastral, J. Ceamanos, P. Garc ´a-Bacaicoa, J. Anal. Appl. Pyrolysis vol. 73, 2005, pp. 65–73. |
[4] | L. Tang and H. Huang, Journal of Analytical and Applied Pyrolysis, vol. 72, 2004, pp. 35-40. |
[5] | Williams PT; Cunliffe AM; Brindle AJ “Enhanced pyrolysis processing of scrap tires” Journal of the Institute of Energy, vol. 74, pp.100-112. 2001. |
[6] | Cunliffe AM, Williams PT “Properties of chars and activated carbons derived from the pyrolysis of used tires”. Environmental Technology, pp.1177-1190. 1998. |
[7] | Cunliffe AM, Williams PT “Composition of oils derived from the batch pyrolysis of tyres”. Journal of Analytical and Applied Pyrolysis, pp.131-152. 1998. |
[8] | Cunliffe AM, Williams PT “Influence of process conditions on the rate of activation of chars derived from the pyrolysis of used tires”. Energy & Fuels, vol. 13, pp.166-175. 1999. |
[9] | Bottrill RP, Cunliffe AM, Williams PT “Combustion of tire pyrolysis oil”. Process Safety and Environmental Protection, vol. 76, pp.291-301. 1998. |
[10] | Williams PT; Cunliffe AM; Bottrill RP; Brindle AJ “The potential of pyrolysis for recycling used tires” in: Dhir; K R; Limbachiya; C M; Paine; A K (ed.) Recycling and Reuse of Used Tires, pp.187-202. Thomas Telford Publishing. 2001. |
[11] | Díez C, Sanchez ME, Harare P, Martinez O, Moran A. “Pyrolysis of tires: Comparison of the results from a fixed-bed laboratory reactor and a pilot plant (rotary reactor)”. Journal of Analytical and Applied Pyrolysis 2005, vol. 74(1-2), pp. 254-258. |
[12] | Cunliffe AM, Williams PT. “Composition of oils derived from the batch pyrolysis of tires”. Journal of Analytical and Applied Pyrolysis 1998; vol. 44(2), pp. |