Luiz Fernando Valadão Flôres, Marco Antônio Rosa do Nascimento, Lucilene de Oliveira Rodrigues, Fagner Luis Goulart Dias
Federal University of Itajubá -.UNIFEI, Itajubá, MG, Brazil
Correspondence to: Marco Antônio Rosa do Nascimento, Federal University of Itajubá -.UNIFEI, Itajubá, MG, Brazil.
Email: |  |
Copyright © 2017 Scientific & Academic Publishing. All Rights Reserved.
This work is licensed under the Creative Commons Attribution International License (CC BY).
http://creativecommons.org/licenses/by/4.0/

Abstract
The growing need of use of more efficient and less costly thermal power plants, given its proposal for electricity generation in Brazil which increased significantly in recent decades ultimately encourages the development of technologies to monitor its operation. Thus improvements in thermal performance of steam turbines will help gaining competitive advantage in the market by reducing operating costs and increasing the amount of the plants available on producing power more efficiently. This work aims to present the results of the methodology modification and the computer tool development based on the Spencer et al. [7] method to determine the drop of thermal performance of steam turbines operating in a combined cycle with cogeneration. Several adjustments were carried out to the methodology originally chosen as a reference, as it does not count for the use of cogeneration, i.e. without extractions at intermediate stages of the steam turbine. Thus, the method was modified to contemplate the steam extraction, and it was obtained satisfactory results when compered with existed Cogeneration Power Plant Heat flow. It can be noted by checking the results that the largest deviation of the efficient values obtained occurred in the low-pressure section with 2.14% as the biggest one mainly because of the large number of parameters that vary simultaneously and the strong influence of the extraction on this section which does not occur in the high and medium pressure turbines. However, the deviations were rather low once the methodology has a general application addressing machines with very different characteristics. In addition to this study, the adjustments were made to replicate the characteristics of the Heat flow Diagrams in some cases it was difficult to find any trend for all load.
Keywords:
Dropof performance, Thermodynamic analysis, Efficiency, Energy
Cite this paper: Luiz Fernando Valadão Flôres, Marco Antônio Rosa do Nascimento, Lucilene de Oliveira Rodrigues, Fagner Luis Goulart Dias, Theoretical Modification of a Methodology for Determining Steam Turbines Thermal Performance Lossin a Combined Cycle with Cogeneration, Energy and Power, Vol. 7 No. 1, 2017, pp. 1-9. doi: 10.5923/j.ep.20170701.01.
1. Introduction
Given the current situation of the planet, where the resource of water was considered inexhaustible, has become scarcer and the competitiveness of electricity generation market has increased gradually in recent decades in Brazil. Thus electricity generation coming from Thermal Power Plants in the country has increased over the past two decades, besides the water resources shortage, most of those resources destined for the hydroelectric generation have already been explored. The electricity generation costs in Thermal Power Plants is higher than the corresponding costs in Hydroelectric Power Plants. The reduction of these costs, as well as an efficient operation management in Thermal Power plants will be worthwhile.The use of thermal systems working in Combined Cycle has been applied and widely used, as well as the use of Cogeneration Systems in industrial plants. Therefore, the increasing need to reduce the cost of the power output by Thermal Power Plants have encouraged the development of technologies to monitor and to diagnose its operation of the equipments and the facilities, stimulating the enhancement of techniques for that. Thus, the techniques for monitoring steam turbine faults will improve its thermal performance as well as the quality of maintenance, reducing the turbine downtime, its operating costs and increasing plant availability in power generation with an appropriate efficiency. Through an extensive review of the literature there was a search for concepts that were used during the work, through various existing publications, for an assessment of the state of the art on the subject under study, therefore obtaining information that supported the choice of the methodology calculation for this work, justifying its development. It was observed that two issues are critical for the analysis of performance drop in steam turbines. The first relates to turbine efficiency, presenting an overview of the factors of load losses seeking as most as possible to quantify them. The second deals with the most frequent failure mechanisms in steam turbines such as: leaks, fouling, erosion, unbalance and mechanical failure of the blades (internal damage), as well as methodologies and /or programs for its evaluation.Latcovich, J. et al. [1] shows in his report a study by the North American Electric Reliability Council (NERC) in which the main failure mechanisms and their causes in thermal power plants burning fossil fuels are shown including a classification on the frequency of occurrence and severity.According to Morais, C. [2], there are studies on the analysis of performance in steam turbines that aims on reducing costs and achieving a better steam cycle performance in a thermal plant, like Kubiak et al. [3] which proposed a simple algorithm to determine the thermal performance of steam turbines considering the deterioration of the turbine flow section. Morais, C. [2] also points out the work of Schofield [4] where the major causes of deterioration of thermal performance in steam turbines are defined and quantified. It also determines the deterioration rate as a consequence of the turbine design features, the quality of the steam, the operating procedure of the plant and the easiness to recover efficiency, or the efficiency of the turbine, after regular maintenance. Tirone, et al. [5] conducted a collection of deterioration of steam turbines cases for seven years and on this paper they describe what are the diagnoses and methodologies based on thermodynamic analysis of the performance parameters of the steam turbines. It was come to a conclusion of the significance of using a monitoring system and developing a maintenance program based on the diagnosis reached after the analysis of the thermodynamic parameters of a steam turbine. According to Li et al [6] four main common problems can be expected regarding damage in steam turbines:• Excessive steam leaks (damage by wear and friction in sealing system);• Erosion of solid particles;• Internal damage;• Fouling.Each of these potential problems has features that will allow diagnosis based on the results of performance tests monitoring. Li et al. [6] shows on its work a part of typical loss found in an inspection for each of the mentioned causes which are highly variable where a maximum deviation of 12% is observed due to wear on the sealing system. This work aims to present the results of the methodology modification and the computer tool development based on the Spencer et al [7] method to determine the drop of thermal performance of steam turbines operating in a combined cycle with cogeneration through the evaluation of the machines thermodynamic status degradation. Several adjustments were carried out to the methodology originally chosen as a reference as it did not count for the use of cogeneration i.e., without extractions at intermediate stages of the steam turbine. Thus, the method was modified to contemplate the steam extraction, and results ware compered with existed Cogeneration Power Plant Heat flow.As this technology is not yet available for this type of cycle, it contributed with procedures and a methodology that will allows the reduction of operating costs and the increase of availability and reliability of the system of thermal power plants operating in a combined cycle with cogeneration thus enabling:• Computer procedures to analyze the steam turbine performance drop;• Process improvement; • Improving the service quality; • Expansion of equipment lifespan.
2. Spencer, Cotton and Cannon Methodology
The turbines can be modeled with different levels of complexity. According to Ungría, A. et.al. [8] the most accurate methods are those applied stage by stage considering correlations and a multitude of parameters such as geometric data of machine components which in most cases are not so simple to obtain. However, General Electric® developed a set of techniques for steam turbine modeling (Bayli et al [9]; Bayli et al [10]; Spencer et al [7]) simpler than other existing methods.Given this set of modeling techniques developed by General Electric® various computer-modeling programs use these techniques. Ungría, A. et al. [8] developed a real exergetic simulator for the operating conditions of a steam thermal power plant. The authors applied the methodology described by Spencer et al. [7] adding it to the exergetic analysis. The simulator was mainly developed to predict the thermal power plants behavior on partly loaded conditions. According to the authors there are several methods typically used to model steam turbines with different levels of complexity. However, methods and procedures published by General Electric® allow parameter picturing such as efficiency at partial load or base load with and without reheat. According to Ungría, A. et al. [8], this methodology has been used in several independent commercial programs such as SYNTHA, PEPSE, PRESTO, STEP and SICIVEX among others, during the development of steam cycles simulators. According to Ungría, A. et al. [8] machine behavior should be exactly reproduced i.e., not only the main flows should be considered but also secondary flows, steam leaks, steam sealing and auxiliary tanks adjustments. According to Table 1 adapted from Ungría, A. et al. [8] there is a comparison of the results obtained by General Electric® method and the acceptance tests performed.Table 1. Comparison of efficiencies with GE method and the Heat Rate achieved on commissioning tests (Adapted from Ungría, A. et al. [8]) 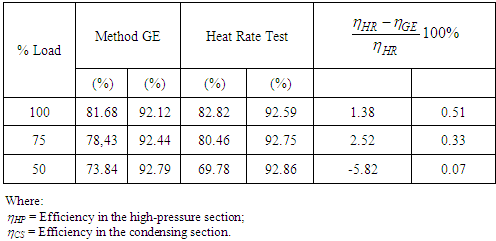 |
| |
|
According to the method applied by General Electric® the high-pressure section efficiencies have a correction factor for partial load whereas the condenser efficiency does not. As stated by the authors, the method originally developed by General Electric® presents very close results of actual operating condition from a reduced number of parameters which enables and facilitates application. Another important factor corresponds to the flexibility of this methodology, which can be applied in various configurations. Thus, in view of the wide acceptance and use of the methodology described by Spencer et al. [7] this will be used throughout this work where the calculation of the parameters will be displayed normally used for monitoring steam turbine performance such as, mass and energy balance; efficiency in the turbine sections; net power, lines of expansion, etc.
3. Case Study
A case study was carried out in a Thermal Power Plant (TPP) operating in combined cycle with cogeneration that powers an oil refinery. However, as a Commissioning Test had not been done in the TPP under study, it should be noted that a project reference state was adopted using the data from the Heat flow Diagram provided by the steam turbine manufacturer. The Heat flow Diagram is a document supplied by steam turbine manufacturers, which presents the features of a machine through the thermodynamic properties of steam at various measuring points. They are designed from simulation programs or developed by the manufacturer and must be measured by practical tests which generates results for different power inputs.
4. Adjustments to the Methodology
According to the methodology developed by Spencer et al. [7] the efficiencies values of the high, medium and low pressure sections are obtained using a sequence of calculations presented in the original work, which are summarized in Table 2.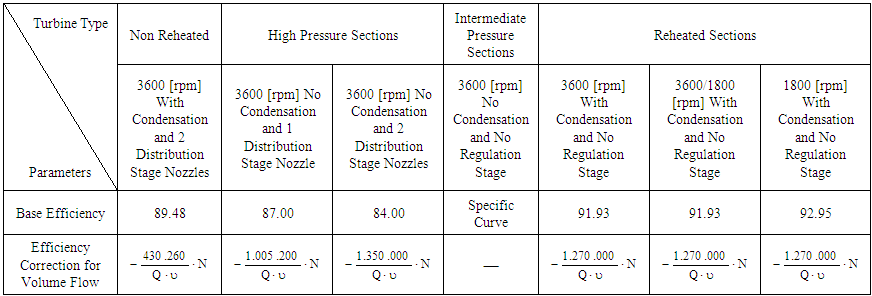 | Table 2. Efficiency Calculation Procedure (all corrections are in percentage) (Adapted from Spencer et al. [7]) |
Table 2 partially reproduces the original table used by Spencer et al [7] and to use it, the desired pressure section of the steam turbine to be studied must be selected such as high pressure section, and how many nozzles a section has.For each column in Table 2 correction curves must be applied such as: efficiency correction for the regulation stage; efficiency correction for pressure ratio; efficiency correction for the initial conditions; efficiency correction for the partial load regulatory stage; correction efficiency for partial load; efficiency correction for 1800 [rpm] replacement in the low pressure section.High pressure sectionFollowing the steps outlined in Table 2 to obtain the efficiency from the high-pressure section they were applied to the Heat flow Diagram data. The Heat flow Diagram corresponding to the electric power maximum load of 55 MW was chosen, as maximum condition, which should be corrected as the steam turbine works at partial loador varies only the steam characteristics. In summary, the final efficiency will be obtained from penalties on the maximum efficiency varying according to the operating characteristics.At first, the steps of the method have been applied keeping the same initial efficiency suggested by Spencer et al. [7], in this case 87%, a power of 55 MW as mentioned above, using the steam conditions for 55 MW. The resulting isentropic efficiency manually calculated was higher than the one found after the corrections sequence proposed by the methodology.In this case, it was found that the only steps that corrected the value of initial efficiency were employed by the method to adjust the differences between the machines used by Spencer et al. [7] and by the TPP under study, which should not be modified. Furthermore, the steps corresponding to the partial load operation were not applicable, leaving only the possibility of adjustment of the initial efficiency left. Based on what has been described, the initial efficiency suggested by Spencer et al. [7] was adjusted to the power of 55 MW in order to adapt it to the steam turbine characteristics of the TPP under study. This calculation was performed using Microsoft Excel® "Goal Seek" tool where the final value was changed in order to match the calculated efficiencies from the Heat flow Diagram and from the methodology. Then, the same initial value obtained after the adjustment has been applied in other load of the Heat flow Diagram, resulting in some differences in the final efficiency of values calculated by the methodology after correction steps, compared to the properties reported in the Heatflow Diagram. Such divergences will be presented on the course of this paper.As the steps to calculate the efficiency correct the previous value from a percentage (penalty), the needed values to adjust, Heat flow Diagram vs. Spencer, in each load, they were determined with the help of the already mentioned Excel® tool called "Goal Seek".Finally, a curve was found that represented the calculated deviations between the used methodology and the data presented in the Heat flow Diagram by the flow rate, TFR, being the power of 55 MW a unit value and its absent of corresponding adjustment.Incorporating the trend curve in the methodology firstly proposed by Spencer et al. [7] as a new step, and with the small deviations found after applying the adjustment curve, the results of Spencer and Heat flow Diagram were overlapped.Finally, the resulting value of the isentropic efficiency, corrected after applying the methodology of Spencer et al. [7], will provide the outlet steam enthalpy of the high pressure section, which can be compared with the calculated value from the operation data. Furthermore, as the flow rate changes, the new comparison enthalpy is automatically determined by the method of Spencer et al. [7], to be analyzed lately with the operation value of the steam turbine.Intermediate pressure sectionContradictory to the procedure used in the high pressure section, which is characterized by penalties in the assigned initial efficiency at the intermediate pressure section the result of the methodology proposed by Spencer directly results in efficiency.As long as in the high pressure section after the analysis of the equations used on this section, the efficiency calculated by the Spencer et al. [7] method with Heat flow Diagram was set for 55 MW by reducing the initial value of a constant use in the calculation through Microsoft Excel® "Goal Seek" which varied the initially allocated amount to achieve the same efficiency of the Heat flow Diagram. That was necessary to ensure the possible deviations found at partial load only occur due to a variation of the electric power generated. Finally, the modified equation was applied to the properties present in the Heat flow Diagram to remaining load besides the entry data that resulted from the application of the methodology to the high pressure section. Some deviations were found and they will be presented in this paper. A trend curve has been reproduced from the deviations found. Incorporating the trend curve in the methodology originally proposed by Spencer et al. [7] as a new step it could be observed that, after applying the adjustments, the methodology coincided with the Heat flow Diagram expected data.Low pressure sectionAs applied to the high-pressure section the method of Spencer et al. [7] employs a given baseline efficiency which is a feature of the machines used by Spencer, Cotton and Cannon, throughout the development of the methodology. As noted in the high-pressure section the isentropic efficiency also drops as the power generated by the steam turbine decreases as seen in the Heat flow Diagram. However, steam properties at the inlet and at the outlet of the low-pressure section are different for each load, in order to meet the goal, preset by the manufacturer, as mentioned before. Among the parameters, we have the pressure ratio, the enthalpy change and the moisture at the outlet that varies according to the load of the steam turbine. One of the few identified parameters that remained constant is the ratio between the enthalpy change and the enthalpy of the inlet of the low-pressure section
Based on this, the electric power of 55 MW was elected as the initial one, using the same strategy as in the high-pressure section. Next, the methodology was applied to this load, yielding a greater value than the one reported by the Heat flow Diagram.In this case, the efficiency value suggested by Spencer et al. [7] was decreased from 91.93 to 86.71 through Excel®"Goal Seek" tool in order to adapt the calculation procedure of steam turbine characteristics under study. It is worth to point out that the methodology developed by Spencer et al. [7] is set for a family of machines which originally is carried out by the General Electric® machines. Furthermore, it is ensured that possible deviations found in other load will only be related to the demanded power variation.Afterwards, the same initial baseline efficiency was applied to the other load presented in the Heat flow Diagram.In order to adjust the observed deviations, the procedure used was similar to the one used in the high-pressure section using the "Goal Seek" tool in order to get the calculated enthalpy deviations between the methodology and the Heat flow Diagram, for each power value. Thus, a new step was added to the methodology originally proposed by Spencer, Cotton and Cannon, adding to the final calculated enthalpy value the correction enthalpy properly adjusted to each power. Finally, based on the several correction enthalpies a trend curve of the flow rate in this section was created, maintaining the same correction procedure.Following the application of the trend curve the corrections were made in Visual Basic and implemented in the Excel® spreadsheet with some deviations still being found. Here, after analyzing the procedure applied in the previous sections it was found that the enthalpy conditions used initially for the power 55 MW remained constant, while the steam conditions varied along with the power.This happens due to the low-pressure section isentropic efficiency calculation procedures, which has an extraction in an intermediate stage of the section and not in the last stage as noted in other sections.In this case, the adjustment made was kept at first, as the methodology does not have correction curves to determine the penalties that the extraction characteristics variation can influence the initial efficiency value. Afterwards, the steam properties were kept constant, observing how it affected the efficiency of calculated value previously. Thus, using the "Goal Seek" Excel®tool, the final enthalpy differences could be identified and distributed through the pressure ratio, i.e. the exhaust operating steam pressure over the steam pressure at 55 MW on extraction also.Applying the proposed adjustment curve deviations were significantly reduced and considered satisfactory.
5. Definition of Control Volume
The defined control volume to be used in the previously developed methodology is shown in Figure 1.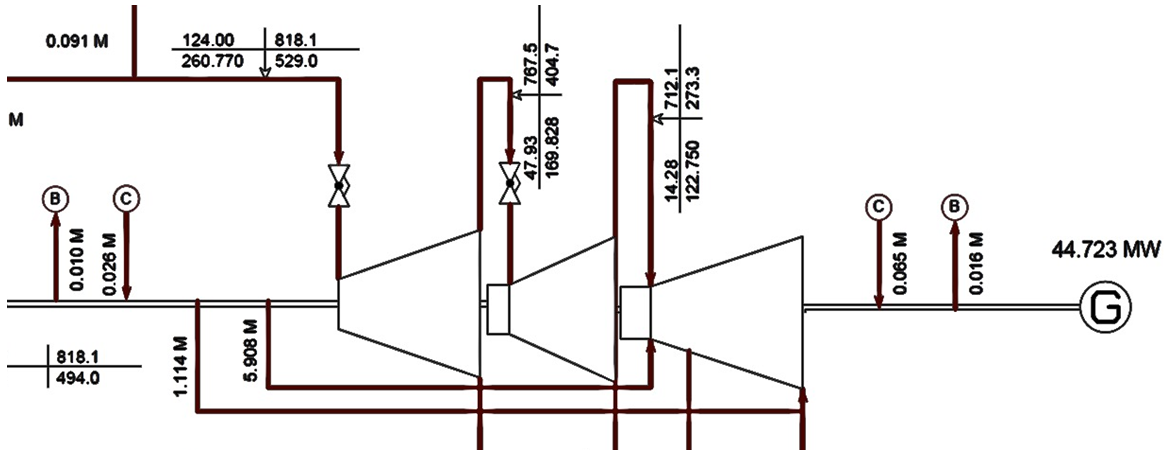 | Figure 1. Simplified steam flow diagram (Siemens power plant documents) |
Figure 1 illustrates a steam flow diagram of a turbine with three pressure levels taken from the documents of TPP under study. For the application of the methodology it is important to identify the instrumentation and the main steam flow as well as secondary flows for control and sealing. The greater the number of details in the choice of the control volume the better the thermal performance diagnosis will be.
6. Summary of the Deviations after Calculations
After making the adjustments, adding the new steps to the methodology (modified methodology) and developed the computer program, the results of the calculations are presented below for: • Isentropic efficiency;• Powers;• Expansion lines.The results are a comparison between Spencer and Cotton Modified Methodology (spreadsheet) X Heat Flow DiagramA - Isentropic efficiency for high, intermediate and low pressure sectionsFigure 2. presents the result of deviations obtained by the Excel® sheet for the Electric Power of 55 MW.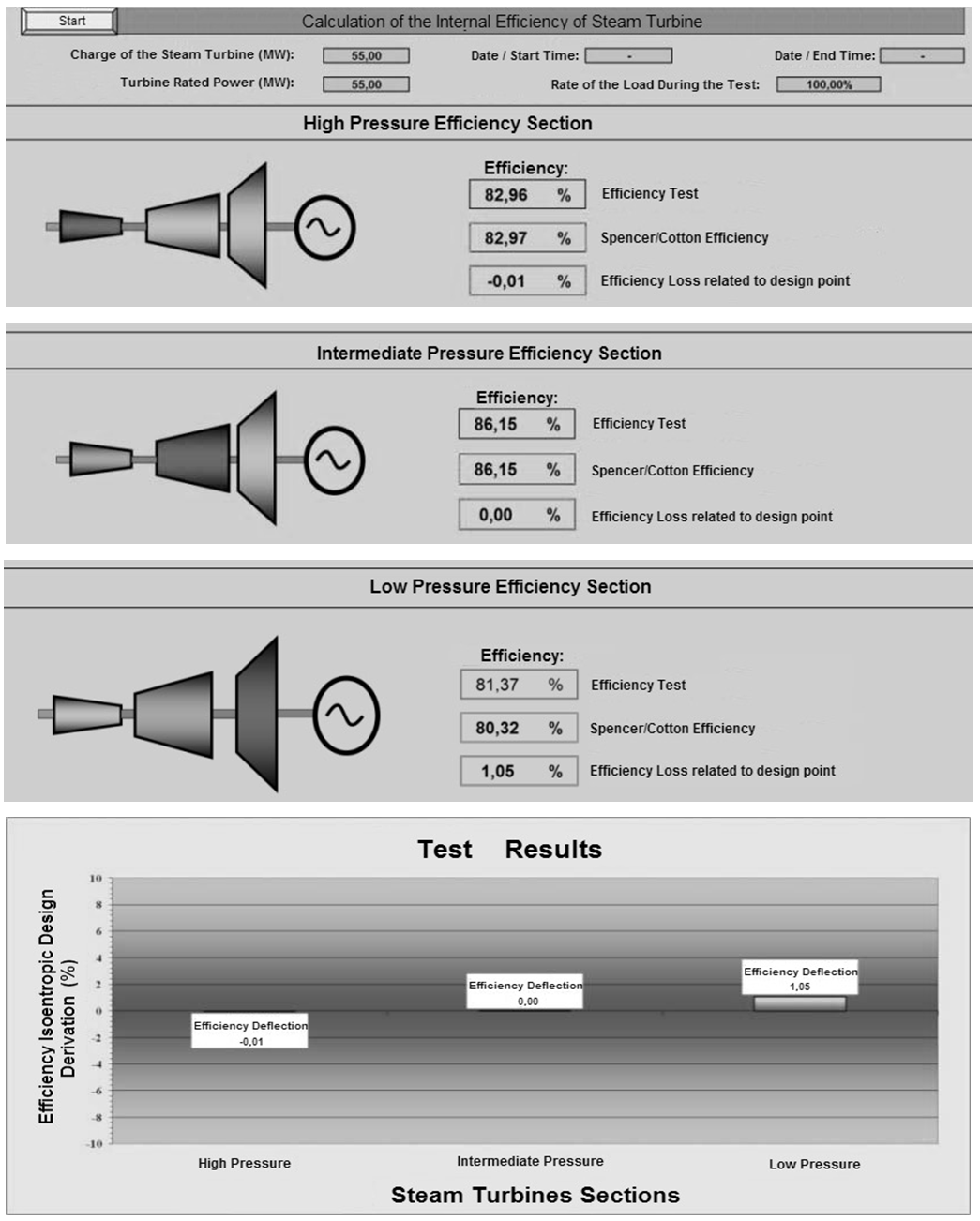 | Figure 2. Distribution of deviations of the TV sections efficiencies |
With the results obtained from the Heat flow Diagram for the remaining values of electric powers, Table 3 was set up, which shows the powers of each Heat flow Diagram and the deviations for each section of the turbines, i.e., high, intermediate and low pressure sections.Table 3. Deviations of the employed methodology results against the Heat flow Diagram results for high (HP), medium (IP) and low (LP) pressure sections 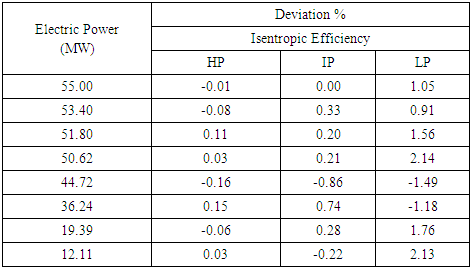 |
| |
|
Note that, in Table 3, the largest deviations occurred in the low pressure section, with 2.14% being the biggest, mainly because of the large number of parameters that vary simultaneously. Additionally, the steam conditions in the extraction strongly influences the efficiency result of the lower section, which does not occur in the remaining sections. However, deviations are low based on the fact that the methodology has a general application, where machines with very different characteristics are addressed. Moreover, in this study, the adjustments were based to reproduce the characteristics of the Heat flow Diagram, which in some cases, was somewhat difficult to find a trend for all loads.B - Generated Mechanical and Electric PowersSimilarly, to section A, the next step corresponds to the determination of the generated mechanical powers. Here, to calculate the mechanical power in the three sections of the steam turbine, the classic thermodynamic theory, through the vapor masses resulted from the mass balance and the steam enthalpies, both determined by methodology as calculated via the read values by instruments, were applied.Figure 3 shows the result of the deviations obtained by the Excel® sheet (Spencer Modified) for the values of the Heat flow Diagram for the Electric Power of 55 MW.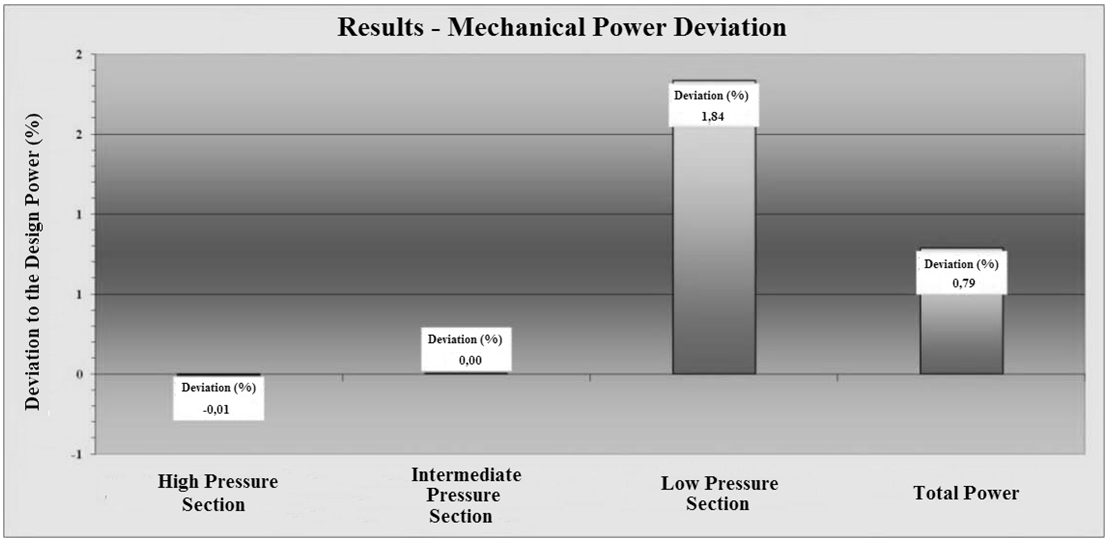 | Figure 3. Deviations distribution of the TV sections mechanical power |
After determining the mechanical power in each section, the correction curves of the generator were applied, supplied by the manufacturer in order to estimate the electric power generated. However, the displayed electric power value, then compared with the value provided as an input data, refers to the total power generated by the steam turbine, as it does not justify a per section analysis of electric power.Table 4 was made with the results obtained for other power values, which shows the potencies of each Heat flow Diagram and the mechanical power deviations for each section of the turbine, i.e. high, intermediate and low pressure sections, as well as the electric power deviations.Table 4. Deviations of the used methodology results against the Heat flow results for the Mechanical and Electric Powers 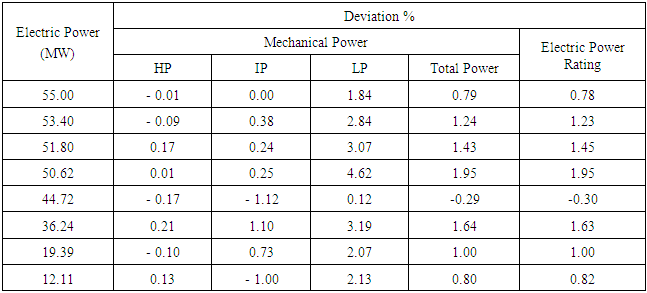 |
| |
|
The largest deviation in the total mechanical power generated is 1.95% at the load of 50,62MW. The largest deviation by comparing the three turbines is 4.62% in the low pressure section for the same load. One of the reasons for that is that the methodology proposed by Spencer et al. [7] does not consider this extraction in the low pressure section. However, despite that fact, the results are good.C - Expansion LinesThe expansion lines obtained by the Excel® spreadsheet are shown below in Picture4accordingly to the electric power of 55 MW of the Heat flow Diagram. They were obtained through the characteristics of the resulting steam from the application of the methodology and through the values reported as "Input Data".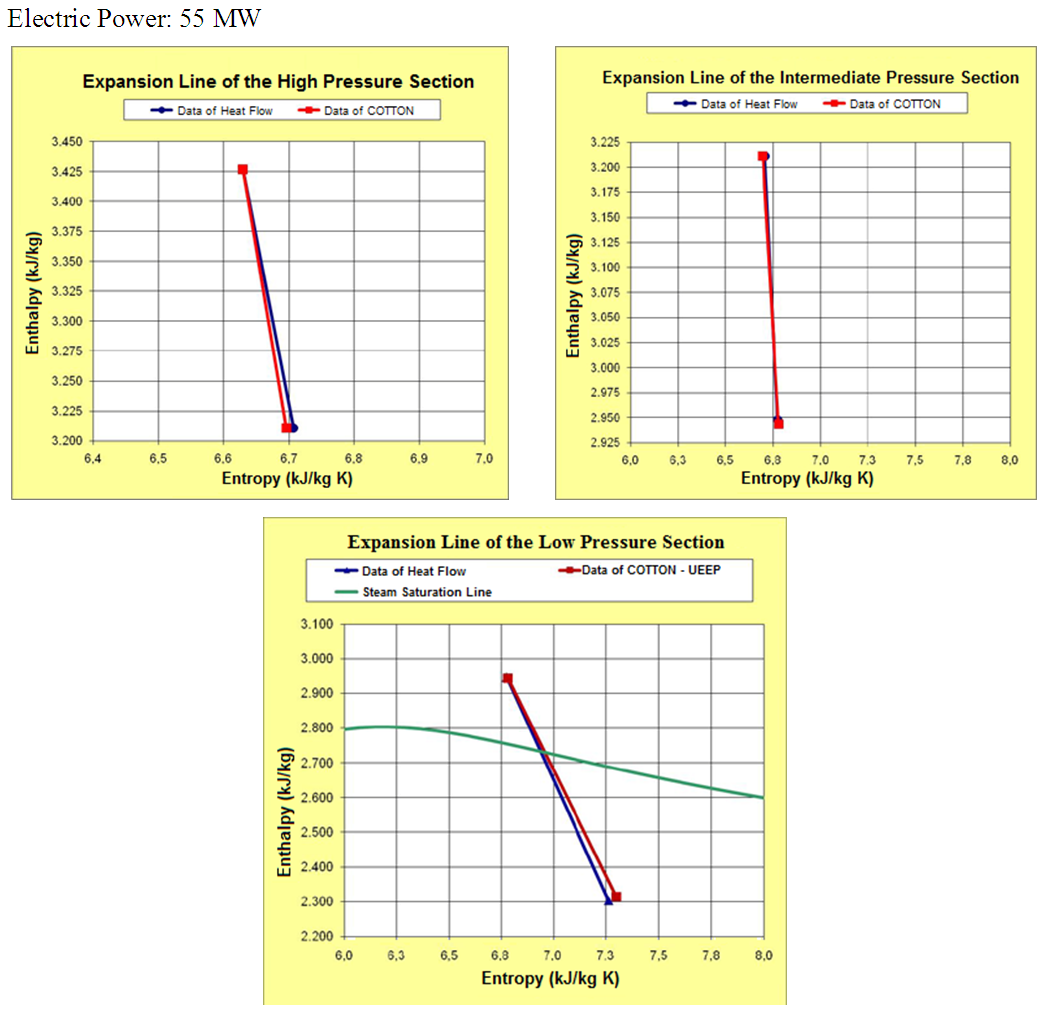 | Figure 4. Expansion Lines for TV sections - 55 MW |
The expansion lines of the remaining electric powers of the Heat flow Diagram were found, and through the results reached, it was noted that the expansion lines were almost overlapped in the high-pressure and intermediate pressure sections. This is due to the fact that the smallest deviation between the methodology and the values of Heat flow Diagram was found in these sections. But the low pressure section deviations were higher, a reflection of the analysis made throughout the efficiency calculation presented at the beginning of this work.Regarding the increase in entropy observed through the expansion lines, this does not correspond to problems during the expansion of the steam, as the exhaust entropy given by the methodology is calculated indirectly by the steam enthalpy. Thus, deviations in the exhaust enthalpy through the methodology are reflected in the generated entropy.
7. Conclusions
Improvements in the thermal performance of steam turbines, whether operating in the Rankine cycle or combined cycle, can help the thermal plant operator obtain competitive economic advantages in the market by reducing their operating costs and increasing its energy production. The operation of a steam turbine in a combined cycle is different than a steam turbine operating in the Rankine Cycle. The main difference is the variation of the amount of steam through out the turbine, as in the Rankine Cycle the steam flow entering the 1st stage of the seam turbine is equal to or greater than the last expansion of stage outlet flow, while in the Combined Cycle the steam flow at the inlet is equal to or less than of the last stages outlet flow. Due to these main differences, the determination of the Combined Cycle steam turbine performance presents some challenges, i.e. the measurement of the boiler feed water flow. Thus, a calculation method or procedure that can be used to evaluate the performance of a steam turbine operating either in a Combined Cycle or in a Rankine cycle is worthwhile.The steam turbine performance evaluation system includes: error determination in the acquired data stream, calculation results correction for the reference conditions, layout of the real expansion lines and their graphical comparison against the reference lines for each turbine section, determination of the isentropic efficiency for each turbine section and its comparison with the reference values and graphical presentation of the results.This study was based on the methodology of Spencer et al. [7] to determine the drop of thermal performance of steam turbines operating in combined cycle with cogeneration. Several adjustments were carried out to the methodology originally chosen as a reference, as it did not count on the use of cogeneration, i.e. without extractions at intermediate stages of the steam turbine. Thus, the method was modified to contemplate the steam extraction, and it obtained satisfactory results. It can be noted by checking the results, that the largest deviation of the efficiency of the values obtained, which occurred in the low-pressure section, with 2.14% as the biggest one, mainly because of the large number of parameters that vary simultaneously, and the strong influence of the extraction on this section, which does not occur in the high and medium pressure turbines. Regarding the obtained expansion lines, before the presented results, it is observed that they were almost overlapped on the high and intermediate pressure sections. This is due to the smaller deviation found between the developed methodology and the values of the Heat flow Diagram in these sections. On the other hand, at the low pressure section, as shown in Picture 6, the deviations were higher, reflecting the previous analysis made throughout the efficiency calculation. The research carried out throughout this work has shown that there are not many advances made in the open literature, especially regarding Spencer et al. [7]’s methodology to obtain a steam turbines performance and thermal diagnosis.Given the results, it can be said that the methodology and procedures development adaptations are a potential tool to automate the performance and diagnosis studies of thermal power plants operating in a combined cycle with cogeneration.
ACKNOWLEDGEMENTS
To PETROBRAS/CENPES through the R&D with the Cooperation Agreement number 0050.0052162.09.9, for the data required for this work, besides the financial support.
References
[1] | Latcovich, J., Astrom, T., Frankhuizen, P., Fukushima, S., Hamberg, H., Keller, S., “Maintenance and overhaul of steam turbines”, Moscow, 2005. |
[2] | Morais, C.F., “Metodologia de Análise de Desempenho de Turbinas a Vapor operando em Ciclos Convencionais e Combinados”, Dissertação de Mestrado – UNIFEI, 2007. |
[3] | Kubiak, J., Angel, F. De, Carnero, A., Campos, A., Urquiza, G., Mariño, C., Villegas, M., “Advanced Method for Turbine Steam Path Deterioration & Performance Analysis”, PWR – Vol. 30 Joint Power Generation Conference, ASME 1996, Volume 2, México, 1996. |
[4] | Schofield, P., “Steam Turbine Sustained Efficiency”, GE Power Systems, GER – 3750C, New York, 1996. |
[5] | Tirone, G., Arrighi, L., Bonifacino, L., “Diagnostics Base on Thermodynamic Analysis of Performance of Steam Turbines: Case Histories”, PWR – Vol. 30 Joint Power Generation Conference, ASME 1996, Volume 2, 1996. |
[6] | Li, Kam W., Priddy, A. Paul, “Power Plant System Design”, Editora John Wiley & Sons, New York, 1985. |
[7] | Spencer, R. C., Cotton, K. C., Cannon, C. N., “A Method for Predicting the Performance of Steam Turbine Generators… 16.500 kW and Larger”, GE Power Systems, GER 2007C, New York, 1974. |
[8] | Ungría, A. J. A.; Valero Capilla, A.; Abadía, J. “Exergy simulation of real operating steam power plants”. Pergamon Press. Thermoeconomic Analysis of Improvement of Energy Systems”. Eds. C. Ruixian and M.J. Moran, pp. 485-492. Oxford, 1989. |
[9] | Baily, F. G.; Cotton, K. C.; Spencer, R. C.: “Predicting the Performance of Large Steam Turbines-Generators Operating with Saturated and Low Superheat Steam Turbines”. GER-2454A, General Electric Company, Apr 1967. |
[10] | Baily, F. G.; Booth, J. A.; Cotton, K. C.; Miller, E. H.: “Predicting the Performance of 1800-RPM Large Steam Turbines-Generators Operating with Light Water-Cooled Reactors”. GER 6020, General Electric Company, 1973. |