Sopingi1, 2, Agus Suman3, Soemarno4, Bagyo Yanuwiadi5
1Doctoral Program of Environmental Science and Technology, University of Brawijaya, Malang, Indonesia
2Government of Nganjuk District, East Java, Indonesia
3Department of Economics and Development Studies, Faculty of Economic and Business, University of Brawijaya, Malang, Indonesia
4Department of Soil Science, University of Brawijaya, Malang, Indonesia
5Department of Biology, Faculty of Mathematic and Natural Sciences, University of Brawijaya, Malang, Indonesia
Correspondence to: Soemarno, Department of Soil Science, University of Brawijaya, Malang, Indonesia.
Email: |  |
Copyright © 2015 Scientific & Academic Publishing. All Rights Reserved.
Abstract
This research was conducted on the industry of tile and brick in Kaloran and Betet village, Ngronggot Sub-district, Nganjuk District. The objective of the research is to determine the efficiency of tile and brick production process. The research used a survey method by questionnaires and interviews to obtain information from the employer of tile and brick industry. The data were analyzed with quantitative approach. The samples were taken from 90 businessmen from Kaloran and 70 businessmen from Betet village. Evaluation techniques used in this research assess the efficiency of the raw materials selection, production processes, and waste. The indicators used are raw materials, labor technology, and transportation. The entrepreneurs of tile and brick business can benefit Rp.75,418 per 1000 bricks and Rp. 106,700 per 1000 tiles. Tile and brick industry showed that the efficiency cost was 86%, while the technical efficiency indicates the efficiency of 75-100%, and the economic efficiency of 1.2-2.99%.
Keywords:
Raw material, Production process, Waste, Tile and brick
Cite this paper: Sopingi, Agus Suman, Soemarno, Bagyo Yanuwiadi, Efficiency Analysis in Small Industry of Tiles and Bricks Production (Case Study in Nganjuk District), World Environment, Vol. 5 No. 1, 2015, pp. 39-45. doi: 10.5923/j.env.20150501.05.
1. Introduction
Challenges of the industry for today and the days to come are the environmental challenge. The first challenge is a local damage, and now has expanded into a global threat. In time, people will be encouraged to commit on the efficiency of energy and natural resources; not only in large-scale industry, but also for small industries [1]. Given the efficiency of the existed company, at least the waste which generated from production process was decreased before come into the downstream. The resources were utilized to its maximum extent in such a way to achieve the optimal output [2]. The application of green industry implement the environmental concepts start from supply of raw materials, production process, until the used products and packaging [3].Small industry in Indonesia generally operates inefficient production, specifically in the utilization of raw materials, because the use of production factors is not optimal [4]. Efficiency is necessary for industrial entrepreneurs to get a combination on the use of certain production factors to produce a maximum output [5]. Efficiency means using minimal resources to get maximal results [2]. Efficiency is a measure of the input, comparing the planned production to the actual (practice) one. If the actual input is more efficient, the level of efficiency will be higher, and conversely. Core of efficiency aspects is saving [6]. Efficiency is the ability to achieve an expected output at the minimal expense of input. An activity has been carried out efficiently if the implementation has reached the target output from the lowest input, so the efficiency can be defined as the absence of waste [7]. Definition of efficiency can be divided into three types, i.e. technical efficiency, price efficiency and economic efficiency [8].In an industry, inputs are economic goods which its availability is very limited. The conversion process should be carried out efficiently thus each unit is used to provide the desired amount of maximum goods [9]. For many industries, especially energy-intensive industry, reducing consumption is a big problem in their efforts. In such structural cost, energy needs large and varied costs. By implementing environmental efficiency, thus energy efficiency can be realized in a various ways [10]. A company said to be efficient if the company use less input (costs) to produce the same amount; or use the same input to get a large amount of outputs; and use a smaller input to produce a larger number of outputs [11].Previous studies [5] analyzed the efficiency and factors that influence small industry production in Kendal District (Study on small industry of Tile Press in Meteseh Village, Boja SubDistrict, Boja). The research assessed the factors of production which had major effect in the production of tiles in Meteseh Village. Clay, labor and fuel variable had a positive and significant effect on the tile industry.Wajdi [12] also analyzed the efficiency of small-scale industries based on the Stochastic Frontier analysis. The research analyze the achievement of technical efficiency on small businesses. The research showed that technical efficiency effort of the sample belongs to quite good category. The aspects of capital and workers role have little effect on increasing company production in the studied sample. Based on the technical efficiency of Stochastic Frontier, each sub-sector of handicrafts has the highest efficiency.Kaloran and Betet village in Ngronggot Sub-district is an industrial Sub-district of tile and brick in Nganjuk District which has existed for a long time. Clay as raw materials for tile and brick, the production process uses wood fuel, and the combustion residue is directly related to nature and environment. Small Industry has a major role in employment, especially those from rural areas [5] and the demands of industrial efficiency. Thus this study was conducted to assess the efficiency of the brick and tile industry in Nganjuk. This study was expected to be benchmark for other industries to determine the extent of the efficiency of an industry.
2. Research Methods
The method used in this research is descriptive method with a quantitative approach. The experiment was conducted in the Kaloran village and the Betet village Ngronggot Sub-district, Nganjuk District, East Java. The study began in July 2012 to December 2012 (6 months). The study population comprised of 90 businessmen from Kaloran Village, and 70 from Betet village.The sampling method used in this study was Simple Random Sampling, the sample from the population members taken randomly without regard to strata (levels) in members of the population [13]. The sampling technique was used the formula of Taro Yamane as follows:n = N / (N.d2 + 1)Where:
n = the number of sample
N = number of population
d2 = the specified precision (percent Leeway inaccuracy due to sampling errors which still tolerated)Based on the Determination Formula of Total Sample above, if assumed precision level was set at 10%, thus minimum sample quantity was 61 samples taken from Betet village and 89 samples from Kaloran village. However, in this study 160 samples was used, 70 samples from Betet village and 90 samples from Kaloran village. The samples consisted of: 1) tile entrepreneurs: 6 from Betet and 7 from Kaloran; 2) brick entrepreneurs: 77 from Kaloran and 59 from Betet, 3) tile and brick entrepreneurs: 5 from Betet and 6 from Kaloran.The implementation of business groups was divided as follows: 1) raw brick business group – only produced bricks and sold in raw form; 2) bricks business groups – produced the raw bricks and conducted combustion process; 3) Tiles and bricks business group – produce roof tile from raw to final product, and bought the raw bricks to be burned with the tile and sold them in finished (mature) form.Evaluation techniques used in this study to provide an assessment on the efficiency of the raw materials selection, production processes, and outcomes. Evaluation on the efficiency of each variable is as follows (Table 1).Table 1. Evaluation of Engineering Data 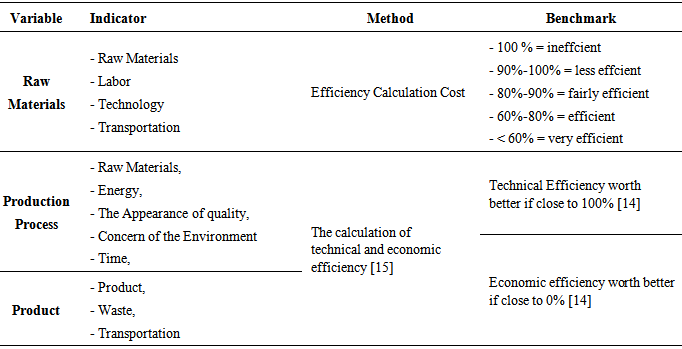 |
| |
|
For the calculation of the cost efficiency using the following guidelines [16];
The calculation of technical and economic efficiency used 12 indicators [15], i.e. Material Cycle Efficiency: MCE, Energy Cycle Efficiency (ECE), Process Overall Environmental Efficiency (POEE), Final Product Environmental Efficiency (FPEE), Energy Cycle Environmental Efficiency (ECEE), Product Absolute Quality Efficiency (PAQE), Product Constant Quality Efficiency (PCQE), Equipment Static Operation Efficiency (ESOE), Equipment Dynamic Operation Efficiency (EDOE), Product Mix Variability Efficiency (PMVE), Product Volume Efficiency (PVE), and Input Efficiency (IE). Only indicator that meets the course will be used in the calculation.
3. Result and Discussion
3.1. Tile and Brick Production
The main raw material for tiles and bricks is clay-sand mix. For tile, the comparison of the clay and the sand is 2:1, meanwhile bricks are 1:1. Median raw material obtained by purchase the land in the edges of Brantas River, 5 km from the production factory. The raw materials were also taken from the garden soil. Soil purchasing is Rp. 180,000 for brick materials and Rp. 200,000 for the tile materials. This cost includes rent for land, energy transport (mine site to factory), and rent of heavy equipment transportation. Within a month, average bricks production is 10,000; while average tiles production are 3,000. The survey showed that 2 of 5 respondents in Betet Village produce < 5000 bricks and 3 respondents produce 5000-10000 bricks per month. Otherwise, 3 of 6 respondents in Kaloran Village produce < 5000 tiles in a month, while 3 respondents produce approximately 5000-10000 bricks in a month.To make a tile, soil had to be milled and then pressed by a press tool according to the types of expected tile. Previously, the press tool lubricated with klentheng oil and fuelled by diesel. The pressed tile laid on tempelang; an instrument made of wood to put the wet tiles, then tempelang compiled into a plangkan. Raw tiles drying process was done under direct sunlight for 12 hours in dry season, while in rainy season it needs up to one week or more. The edges of dried tiles trimmed with a knife, then burned using furnace combustion process or pawon. Fuel used in the combustion process was various, e.g. wood waste (rencek and dongklak) and waste corn cobs (janggel), mixed or separately. The combustion process was done in 15 hours, with the average of furnaces capacity was 10,000 tiles. After burning stages, tiles had been ready to be marketed after sorted out the failed product.Brick making process is generally very similar to the tile-making process. The simple steps begin with extracting the raw materials, e.g. clay or loam. Then the clay was dug to be transported to the site of bricks production. The clay is then poured or mixed with water, stirred so that the water can seep the clay and then left for at least one night. However, usually the brick making process is much simpler. Clay and water has been mixed and stirred manually by hand (or pressed with feet) without milled with molen. The duration of agitation was less than on tile.
3.1.1. Brick Production
In bricks making process, soil that has been mixed with brick mold pressed in a flat frame. Same with the tile, brick drying performed under a direct sunlight for about 12 hours in the dry season, while in the rainy season can be up to one week. The dried bricks’ edges trimmed with a knife then combusted using furnace. The combustion fuelled by waste wood or rice husk for 12 to 24 hours, depend on the capacity of the furnace. However, for people who do not have a furnace, combustion is usually implemented with a simple way of making disposable furnace, which is immediately broken down. Each combustion process could reach 10000 to 20000 bricks. The product components and the amount of costs incurred in the brick industry are as follows. a) Supply of Raw Materials It is consisted of top soil raw materials, labour, tools, and transportation to the location. The total cost for the supply of raw materials is Rp. 180,000 for 2200 bricks. b) Production ProcessProduction process consisted of three elements:l Labour; covering for brick molding, for furnace loading and combustion. The total cost of providing labour for producing 1000 brick is Rp. 130,000. l Equipment; main equipment for the production process include brick mold, comb knives, and hoes, supported with plastic cover and water. l Fuel; in the form of rencek firewood, dongklak firewood, corn cob, and rice husk. The average fuel cost to burn 12000 bricks is Rp. 1,250,000.c) Transportation The third component in brick production is transportation; transportation of raw materials to the burning place is Rp. 30,000 per 1000 bricks, with the contract system. Carts used in site are Rp. 500,000 per unit for 5 years. d) WasteFourth component in production processing is waste; including the wages on milled failed-production brick for Rp. 30,000 per m³ and the cost to purchase bags for ashes, Rp. 3,000 per sack.If the industry only produces bricks and sells them in raw form, then the profit is Rp. 5,122.5 for 1000 brick; only 4.71% compared to the industry that produce and sells the brick in mature forms. Although there are extra cost for burning power, furnace and fuel, the profit is Rp. 108, 680. Otherwise, the industry that bought the raw bricks and sells them in the mature form profited for Rp. 75,418 with different cost on the raw brick materials and for plug unloading, burning and furnace (Table 3).
3.1.2. Tile Production
a) Supply of Raw Materials The cost for the supply of raw materials includes the clay soil as raw materials, labour for loading and unloading, tools, and transportation to the location. The total cost for the supply of raw materials is Rp. 200,000 for 1100 tiles. The raw material is processed into the mill; clay milling costs is Rp. 70,000 for 1100 tiles. b) Production ProcessThe production process covering: l Labour; for molding, set the furnace, and combustion. Costs incurred for 1000 tile is Rp. 420,000. l Equipment; The main equipment for the production process include: the press, the base tile, and furnace. l Operations and maintenance; covering the press tool maintenance, provision of additional materials (klentheng oil and diesel). l Fuel; in the form rencek firewood, dongklak firewood, corn cob and corn silk. Rice husk was no use as in brick combustion due to the worse results. The fuel cost to burn ±10000 tiles is Rp. 1,250,000.c) TransportationThe transportation from raw tiles to the furnace is Rp. 30,000 per 1000 tiles, with the contract system. Carts used in site are Rp. 500,000 per unit for 16 years. d) WasteFourth component in production processing is waste (similar to bricks processing); including the wages on milled failed-brick product for Rp. 30,000 per m³ and the cost to purchase bags for ashes is Rp. 3,000 per sack. Costs incurred for each 1000 tiles is Rp. 842,300 and the selling price of each 1000 tiles is Rp. 950,000. Thus, the profit for each 1000 tiles is Rp. 107,700.The waste from the failed production process of tile, brick and ash can be used and recycled. In every 12000 bricks and 10000 tiles combustions, there are approximately 10% product failures. The failed product processed with soil into fine brick (red cement). Each 1 m³ of fine brick can be obtained from 1500 or 3000 bricks or tiles. Milling costs is Rp. 30,000 per m³, and the selling price of fine brick or tile is Rp. 150,000 per m³. Every 1000 bricks gains from product failure were about Rp. 7,000, while every 1000 tiles gained from failed product is Rp. 2,000.The ashes still also have value. Each burning phase resulted ± 5 sacks of ash. The selling price of ash is Rp. 5,000 per sack. However, employers must provide a price of Rp. 3000 per sack. Income that can be derived from the sale of ash from 1000 bricks is ± Rp. 833 and the income that can be earned from the ash of 1000 tile is ± Rp. 1,000.
3.2. Analysis of Efficiency
From components and production cost of tiles and bricks, the efficiency values obtained as follows:
3.2.1. Efficiency of raw materials
- Bricks Industry:
- Tiles Industry: 
3.2.2. Production Process Efficiency
a) Technical efficiencyTechnical efficiency showed in Table 2. From 12 indicators to calculate the technical efficiency and economic efficiency, not all of it could be seen in the study. Thus only the existing indicators could be calculated. For the final output variables, some components had been included in the calculation of the production process variables.Table 2. The Calculation of Technical Efficiency 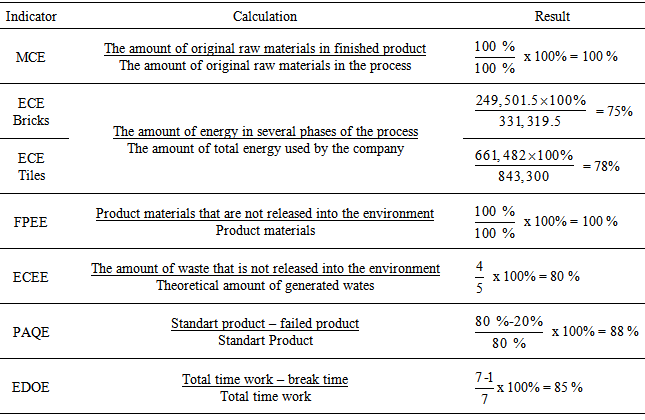 |
| |
|
b) Economic efficiencyThe ccalculation of economic efficiency (Table 3) indicates that the efficiency of the brick material cycle (Material Cycle Efficiency/MCE) was 2.99%. Whereas for the efficiency of the tiles material cycle (MCE) was 1.20%. Therefore, the tiles industry was more efficient than the brick industry. Table 3. Production Cost and Profit in Brick Industry |
| |
|
The environmental efficiency of the brick final product (Final Product Environmental Efficiency/FPEE) was 1.20%, similar to the environmental efficiency of the tiles final product (FPEE) was 1.20%. Thus the tiles and bricks production were equally efficientt. From the calculations in Table 2 and Table 3, the results of the evaluation were as follows (Table 4).Table 4. The Calculation Economic Efficiency 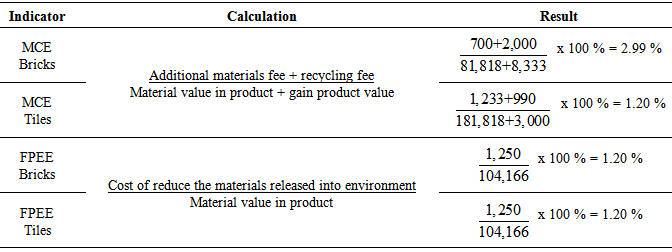 |
| |
|
From the evaluation results of the efficiency (Table 5), the efficiency of raw material is 86%, based on the applicable benchmark category of quite efficient. For variable of production process and the final product, the value of technical efficiency for the bricks energy cycle (ECE) showed 75% rate, which means quite efficient. While the technical efficiency value for environmental final product (FPEE) was 100% rate, meant very efficient. Overall technical efficiency value of the assessed variables showed relatively high rate. For economic efficiency, from the assessed variables, the averages showed a low value, which meant better.Table 5. Efficiency Evaluation Results 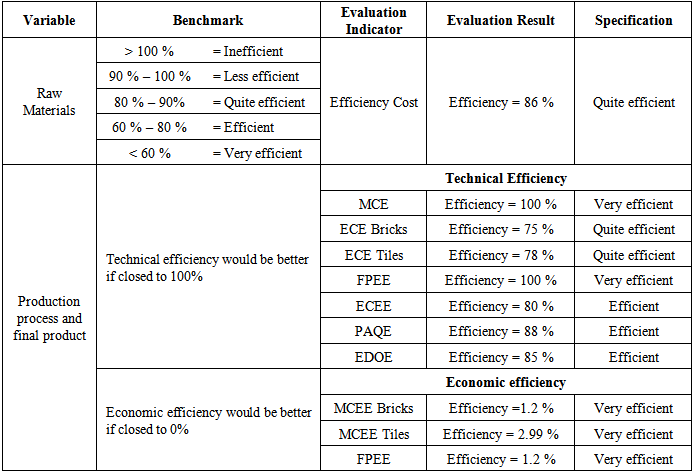 |
| |
|
4. Conclusions
The study concluded that the brick and tile industry in Nganjuk did not provide equal profits to entrepreneurs. The profit of raw bricks entrepreneur were still distance compared to bricks and tiles entrepreneurs. It was because the crude brick entrepreneurs generally produced bricks by themselves, so the labor was not taken into account.The used raw materials of tiles and bricks’ small industry in Nganjuk performed efficiently production process. From the efficiency assessment, tiles and bricks industry was quite efficient in providing the raw materials. However, it still needs to be improved. For the production process and the final product, the technical efficiency category was quite efficient to very inefficient, i.e. 75-100%. Whereas the economic efficiency was very efficient categorized because the value closed to 0%, i.e. 1,2%.Generally bricks and tiles industry could be categorized as environmental-industry, since the components used are non-destructive component and produced waste could be recycled. Revitalizing effort is needed towards the mine site ground, in order to save the environment.
5. Recommendations
Based on the analysis in the production of tiles and bricks which includes the supply of raw materials, production processes and final processes, it can be said that the production of tiles and bricks in general has a value of efficiency. However, some aspects need to be improved. Therefore, we propose some recommendation as follows:1. Raw materials were taken from distance with a relatively high price. It is necessary to look for alternative raw materials near the site of production to suppress the prices.2. The cost of burning the bricks and tiles were too expensive, it is necessary to change the combustion pattern. In general, entrepreneurs burning capacity 10,000-12,000 either tiles or bricks. Thus it needs increasing the capacity of 20,000-25,000 tiles or bricks in into a single combustion. This certainly gives benefit to final product by pressing the cost of labor and wood materials for fuel.3. There needs to established an agreement among the entrepreneurs of tiles and bricks to raise their prices, because during this time the selling price is still relatively low when compared to other building materials. This course must be accompanied by an increase in the quality of the product.
References
[1] | Djajadiningrat, 2011, Green economy, Rekasaya Sains, Bandung. |
[2] | Sawak, H. A., 2012, Operation management as the key of green industry, Popular article, Faculty of Economy and Business, Gadjah Mada University, http://bem.feb.ugm.ac.id /index.php/publication/artikel-populer/71-manajemen-operasi-sebagai-kunci-green-industri. |
[3] | Ministry of Industry, 2012, Policy on industry development, Ministry of Industry, Workshop of Energy Efficiency Jakarta, March 27th 2012. |
[4] | Lincolin, A., 1995, Small Industries Development Potential in Indonesia, Inter-University Center of Economic studies, Gadjah Mada University, Yogyakarta. |
[5] | Kurniasari, P., 2011, Efficiency analysis and affecting factors on small production in Kendal Regency, eprints. Undip.ac.id. |
[6] | Umar, H., 2000, Marketing research on consumer behaviour, Gramedia Pustaka Utama, Jakarta. |
[7] | Nicholson, W., 2002, Theory of Intermediate Micro-economy, PT Raja Grafindo Persada, Jakarta. |
[8] | Miller, R.J., and Meiners, R. E., 2000, Intermediate Micro-economy, PT. Raja Grafindo Persada, Jakarta. |
[9] | Sinulingga, S., 2009, Planning and controlling production. Graha Ilmu, Yogyakarta. |
[10] | Budiarto, R., 2011, Energy policy towards sustainable energy system, Samudra Biru, Yogyakarta. |
[11] | Supriyono, R. A., 1999, Cost Accounting Book I: Cost Collection and determination of main cost, BPFE, Yogyakarta. |
[12] | Wajdi, F., 2012, Industry efficiency analysis based on Stochastic Frontier analysis, Jurnal Manajemen dan Bisnis, 16(1). |
[13] | Riduwan, 2008, Methods and technique to develop thesis, Alfabeta, Bandung. |
[14] | Adiyatna, H., Marimin, 2011, Audit of performance efficiency in agroindustrial production tea beverage, Jurnal Teknologi dan Industri Pangan, XII(1). |
[15] | Barbirolli, R., 1996, New indicators for measuring the manifold aspects of technical and economic efficiency of production processes and technology, J. Tech. Innov., 16. |
[16] | Munir, D., 2004, Policy and management of regional memories, Yayasan Pembaruan Administrasi Publik Indonesia, Yogyakarta. |