Yehia A. Eltaweel1, Ehssan M. Nassef2, Riham A. Hazza2
1Chemical Department, Faculty of Engineering, Alexandria University, Egypt
2Petrochemical Eng. Department, Faculty of Engineering, Pharos University, Egypt
Correspondence to: Ehssan M. Nassef, Petrochemical Eng. Department, Faculty of Engineering, Pharos University, Egypt.
Email: |  |
Copyright © 2014 Scientific & Academic Publishing. All Rights Reserved.
Abstract
Rates of copper ions removal from waste solution by cementation, using an iron rod that was covered with the screen, and the cementation kinetics of copper deposition from sulfate solutions onto iron were studied under different conditions of initial copper ions concentration, initial pH of the solution and solution velocity. It was found that the rate of copper ion removal by cementation onto iron rod increases with increasing solution velocity. However, the rate of copper ion removal decreases with increasing initial copper ion concentration. The cementation removal rate increases slightly with pH reaching a maximum value at pH 2.0 then decreases with further increase in pH. The following dimensionless mass transfer equation was found to correlate with the mass transfer coefficient to these variables: Sh = 0.18 SC0.33 Re0.844.
Keywords:
Wastewater, Cementation, Copper removal, Mass transfer
Cite this paper: Yehia A. Eltaweel, Ehssan M. Nassef, Riham A. Hazza, Recovery of Copper from Wastewater by Cementation Technique, World Environment, Vol. 4 No. 5, 2014, pp. 199-205. doi: 10.5923/j.env.20140405.01.
1. Introduction
Heavy metals are elements having atomic weights between 63.5 and 200.6, and a specific gravity greater than 5.0 [1]. With the rapid development of industries such as metal plating facilities, mining operations, fertilizer industries, tanneries, batteries, paper industries and pesticides, etc., heavy metals wastewaters are directly or indirectly discharged into the environment increasingly, especially in developing countries. Unlike organic contaminants, heavy metals are not biodegradable and tend to accumulate in living organisms and many heavy metal ions are known to be toxic or carcinogenic. Toxic heavy metals of particular concern in the treatment of industrial wastewaters include copper, zinc, nickel, mercury, cadmium, lead and chromium. Copper does essential work in animal metabolism. But the excessive ingestion of copper brings about serious toxicological concerns, such as vomiting, cramps, convulsions, or even death, Zinc is a trace element that is essential for human health. It is important for the physiological functions of living tissue and regulates many biochemical processes. However, too much zinc can cause eminent health problems, such as stomach cramps, skin irritations, vomiting, nausea and anemia, .Nickel. Exceeding its critical level might bring about serious lung and kidney problems aside from gastrointestinal distress, pulmonary fibrosis and skin dermatitis [2]. And it is known that nickel is a human carcinogen. Mercury is a neurotoxin that can cause damage to the central nervous system. High concentrations of mercury cause impairment of pulmonary and kidney function, chest pain and dyspnoea [3]. The classic example of mercury poisoning is Minamata Bay. Cadmium has been classified by U.S. Environmental Protection Agency as a probable human carcinogen. Cadmium exposes the human health to severe risks. Chronic exposure of cadmium results in kidney dysfunction and high levels of exposure will result in death. Lead can cause central nervous system damage. Lead can also damage the kidney, liver and reproductive system, basic cellular processes and brain functions. The toxic symptoms are anemia, insomnia, headache, and dizziness, and irritability, weakness of muscles, hallucination and renal damages, Chromium exists in the aquatic environment mainly in two states: Cr (III) and Cr (VI). In general, Cr (VI) is more toxic than Cr (III). Cr (VI) affects human physiology, accumulates in the food chain and causes severe health problems ranging from simple skin irritation to lung carcinoma [4]. Faced with more and more stringent regulations, nowadays heavy metals are the environmental priority pollutants and are becoming one of the most serious environmental problems. So these toxic heavy metals should be removed from the wastewater to protect the people and the environment. Different methods are employed to recover the metal or remove the undesired impurities from the leach or industrial waste solutions, such as neutralization with acid or base solutions, chemical precipitation, crystallization, solvent extraction, flotation, ion exchange, adsorption onto different adsorbents, reverse osmosis, chelating ligands, electrodialysis and electrowinning. These methods have some drawbacks. For example, chemical precipitation requires extremely long settling time; ion exchange and adsorption process are slow and expensive, and may require frequent regeneration for adequate performance; reverse osmosis, electrodialysis, electrowinning and solvent extraction methods are very expensive, and have high operating costs. Cementation is an important chemical process used in industry to precipitate and recover valuable metals from leach or waste solutions. Cementation method has some advantage, such as recovery of metals in essentially the pure metallic form, simple control requirements, low energy consumption and in general low cost process [5]. It seems that the most reasonable and simple method for copper recovery is the method of its cementation using scrap iron to produce metallic copper sediments suitable for metallurgical processing. Due to different standard reduction potentials: | (1) |
 | (2) |
copper ion becomes readily reduced on the metal iron surface, while the related amount of iron is dissolved. In standard conditions the reaction: | (3) |
is driven by standard emf= 0.78 V. Because industrial solutions besides copper also contain Fe2+ and Fe3+ ions, when scrap iron is introduced, due to reduction potential | (4) |
The reaction | (5) |
With standard emf = 1.211 V can be expected.The deposited copper due to Fe- ions presence may undergo dissolving according to the reaction  | (6) |
With standard emf = 0.431 V.Because the waste copper solutions usually contain H2SO4 scrap iron etching | (7) |
should also be considered [6]. The objective of this study is to remove copper. The removal technique done in this work is cementation of this metal on a screen layered iron rod. The main objective of this work is to examine the different parameters which effect on the percentage removal and the residual concentration of the cemented ion. These parameters are initial concentration of the solution, the pH of the solution, and flow rate of the solution.
2. Methods
2.1. Experimental Setup
The experimental setup is in Figure 1. It consists of a Plexiglas container of 6cm diameter and 30 cm height. Glass tank of 20cm width, 20cm length, and 30cm height. Overflow container of 18cm width, 18cm length, and 9cm height. Iron rod with 30cm length and 2.44cm diameter covered with screen. A 220 volt pump. 3valves 0.5 inches. 0.5 inch pipes with 1.75cm internal diameter.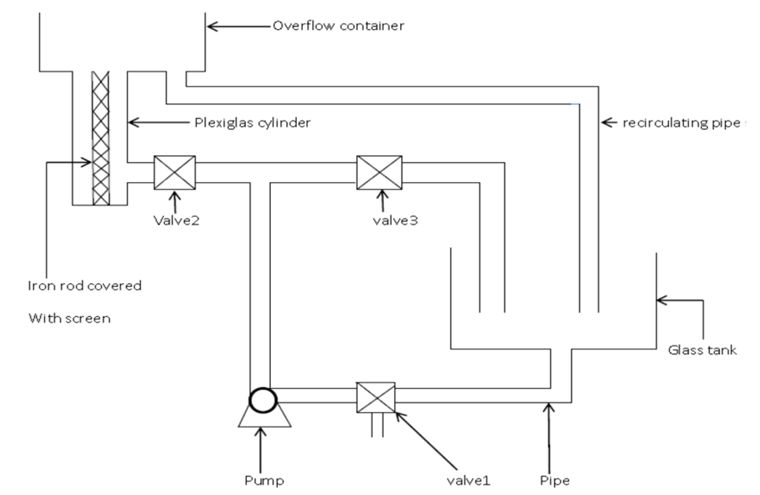 | Figure 1. Schematic diagram of the experimental setup |
2.2. Reagents and Analytical Procedures
Before each run a stock solution of copper sulfate was prepared by dissolving the copper sulfate analytical reagent in distilled water. The experimental desired concentrations were obtained by successive dilutions with distilled water. The pH of the solution was adjusted by adding 0.1N hydrochloric acid solution or 0.1N sodium hydroxide for each experiment. The A digitally calibrated pH-meter (HANNA, Model pH 211) was used to measure the pH of each solution. The analytical determination of copper sulfate solutions was carried out by idometry [7] using a standard solution of sodium thiosulfate.
2.3. The Cementation Process Procedures
Copper solutions were prepared from the stock solution by successive dilution to the desired concentrations. In each run 7 liters of the freshly prepared solution were added in the glass tank and fed by a pump into the plexiglass cylinder, then it will be recycled back to glass tank. The pH of the solutions was adjusted by adding 0.1 N hydrochloric acid solution or 0.1N sodium hydroxide for each experiment. The volumetric flow rate was adjusted to a certain value before each run. During experiments, 50 ml samples were collected every 30 minutes and analyzed for the percentages removal of copper ions. The rate of cu+2 removals was determined under different parameters. Table 1. gives a summary of all studied parameters and their ranges. The physical properties of copper sulfate solution such as density and viscosity were measured experimentally using density bottle and Ostwald viscometer [8], whereas the diffusivity was calculated from literature (Table 2) [9].Table 1. Summary of all studied parameters and their ranges 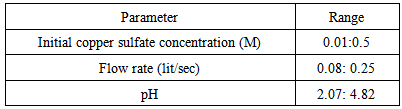 |
| |
|
Table 2. Physical properties of copper sulfate solutions measured at 25℃ 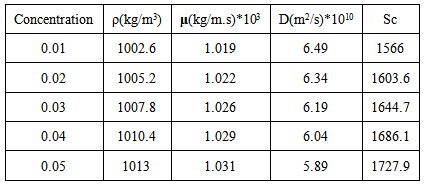 |
| |
|
3. Results and Discussion
The present study was conducted in a simple semi batch reactor where the rate of reaction is given by [10]: | (8) |
Which upon integration yields: | (9) |
 | (10) |
The mass transfer coefficient of the cementation reaction was obtained under different conditions by plotting ln Co /C vs. Time as shown in Figures (2, 4 and 6), the slope of the resulting straight line gives ( KA / V) from which the mass transfer coefficient can be calculated.
3.1. Effect of Initial Copper Ion Concentration
The effect of initial copper ion concentration on mass transfer coefficient is shown in Figure 2. In addition, the removal percentages of different copper concentrations is shown in Figure 3.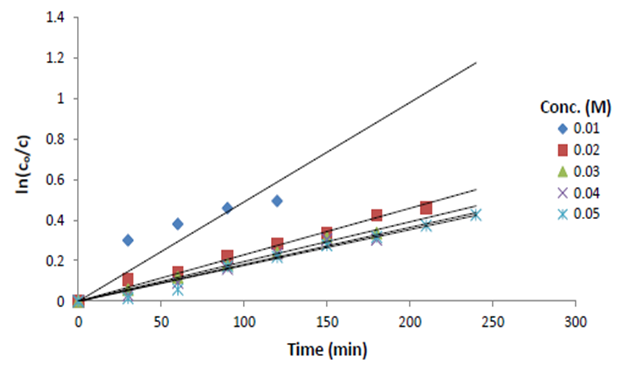 | Figure 2. Effect of initial concentration of copper sulfate |
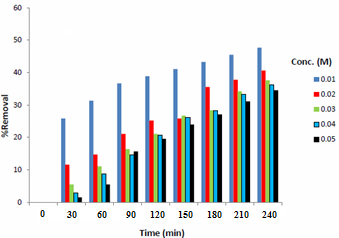 | Figure 3. Removal percentages of different copper ions concentrations |
It is clear from Figure 2 that as the initial copper ions concentration increases, the mass transfer coefficient decreases, which may be attributed to the following causes: (i) during cementation, a solid porous layer of metallic copper is formed on the surface of iron road covered with a screen which inhibits the rate of cementation by virtue of increasing the resistance to copper ions diffusion towards the iron surface, (ii) as the concentrations of copper ions in solution increase interionic attraction between ions increases with a consequent decrease in the activity of copper ions and its diffusion coefficient. This is agreement with previous studies on cementation of copper ions on zinc [11]. From the above results it is obvious that the mass transfer coefficient ”K” depends on, initial copper ions concentration, that is, physical properties of the solution.
3.2. Effect of the Solution pH
It has been established that pH is an important operating factor influencing the performance of cementation process. In this work, the examination of the pH effect on the cementation process was studied for pH ranging from (2.07–4.82). From Figure (4 and 5), it was observed that the mass transfer coefficient and the rate of cementation increases slightly with pH reaching a maximum value at pH 2.0 then decreases with further increase in pH due to the hydrolysis of the copper ion; the equilibrium pH after cementation reaches 4.0. The precipitation of copper hydroxide took place at a pH value which depends on the concentration of copper ions [12]. With increasing acidity, the rate of nucleation becomes higher, whereas the rate of nucleus growth decreases [13]. Therefore, a copper sulfate solution of pH 2.07 was selected for this study.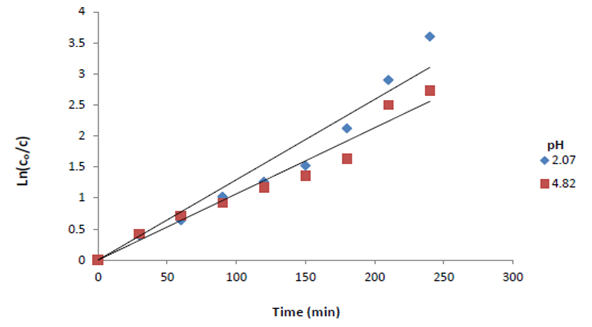 | Figure 4. Effect of pH of the copper sulfate solution |
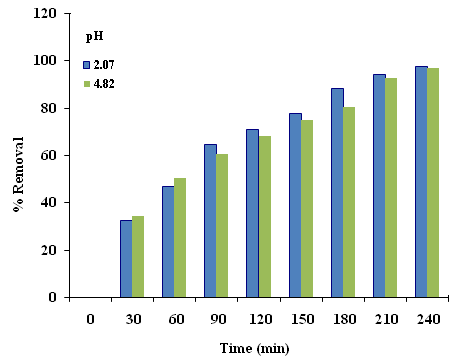 | Figure 5. Removal Percentages of different pHof the solution |
3.3. Effect of the Solution Flow Rate
Figure 6 and Figure 7 show the effect of solution velocity, which shows by increasing solution velocity the rate of mass transfer increased. Figure 6 shows that the rate of copper - ion removal by cementation onto iron rod increases with increasing solution velocity. This finding is in agreeing withthe hydrodynamic boundary layer theory according to which increasing solution velocity decreases the thickness of the hydrodynamic boundary layer built from the impingement point to the edge of the iron rod (Figure 6). Accordingly the thickness of the diffusion layer decreases with a consequent increase in the mass transfer coefficient. This finding is consistent with the results of previous studies on the effect of solution motion on the rate of cementation conducted using different means of mass transfer enhancement [14].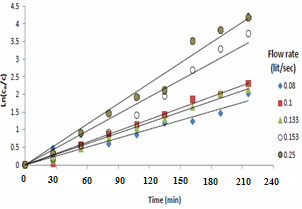 | Figure 6. Effect of flow rate of copper sulfate |
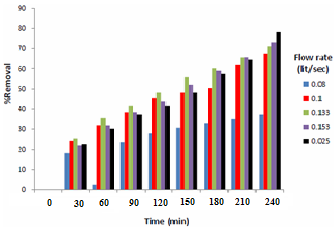 | Figure 7. Removal Percentages of Different Copper flow rate |
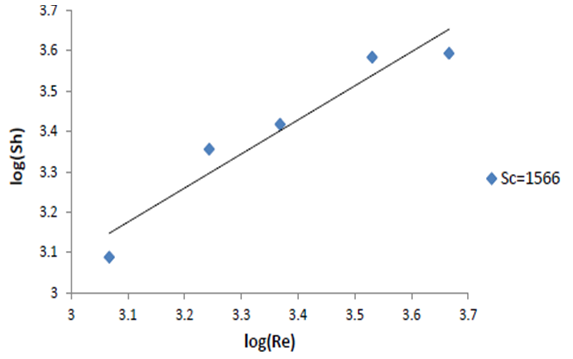 | Figure 8. log Sh vs. log Re |
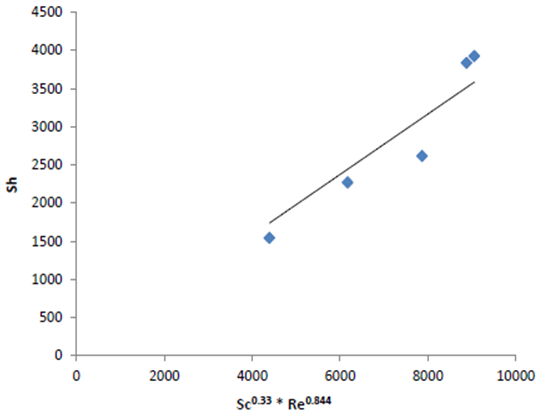 | Figure 9. Sh Vs. Sc 0.33 * Re 0.844 |
From the above results it is obvious that the mass transfer coefficient, K, depends on the velocity of solution, initial copper ions concentration, that is, physical properties of the solution and on the pH of solution. The following dimensionless mass transfer equation was found to correlate with the mass transfer coefficient to these variables (Figures 8 and 9):  | (11) |
The exponent of Sc was fixed at 0.33 following previous theoretical and experimental studies in mass transfer [15, 16]. The exponent 0.844 was obtained by plotting log Sh versus log Re (Figure 8), for the conditions: 1166<Re<5840, Sc=1566. The above equation can be used in the design and operation of high-productivity cementation reactor.
4. Conclusions
1. In view of the present results, the use of an iron rod that is covered with a screen in conducting cementation reactions is highly recommended in practice. It is simple in design and operation. The salable product (metal powder) can be collected easily by the screen.2. The rate of copper ion removal by cementation onto iron rod increases with increasing the solution velocity. However, the rate of copper ion removal decreases with increasing initial concentration of copper ions. The cementation removal rate increases slightly with pH reaching a maximum value at pH 2.0 then decreases with further increase in pH.3. Mechanistic study of the present cementation process revealed that the process is diffusion controlled.4. A dimensionless equation representing the data was obtained. This equation can be used for the design scale up and operation of reactors used to remove copper ions from wastewater by cementation.
References
[1] | N.K. Srivastava, C.B. Majumder, 2008. Novel biofiltration methods for the treatment of heavy metals from industrial wastewater. J. Hazard. Mater. 151, 1─8. |
[2] | J.L., Huisman, Schouten, G., Schultz, C., 2006. Biologically produced sulphide for purification of process streams, effluent treatment and recovery of metals in the metal and mining industry. Hydrometallurgy 83, 106─113. |
[3] | K.A., Baltpurvins, Burns, R.C., Lawrance, G.A., Stuart, A.D., 1997. Effect of electrolyte composition on zinc hydroxide precipitation by lime. Water Res. 31, 973─980. |
[4] | N., Oyaro, Juddy, O., Murago, E.N.M., Gitonga, E., 2007. The contents of Pb, Cu, Zn and Cd in meat in Nairobi, Kenya. Int. J. Food Agric. Environ. 5, 119─121. |
[5] | Nizamettin DEMIRKİRAN, Asim KÜNKÜL, Recovering of copper with metallic aluminum, Trans. Nonferrous Met. Soc. China 21(2011) 2778−2782. |
[6] | T. Stefanowicz, M. Osifiska, S. Napieralska-Zagozda, Copper recovery by the cementation method, Hydrometallurgy 47 (1997) 69-90. |
[7] | J. Bassett, R. C. Denny, G. H. Jeffery and J. Mendham, Vogel’s Text Book of qualitative Inorganic Analysis, the English Language Book Society and Longman, New York, (2008). |
[8] | Mclntyre. P.B, Vogel H.J., Trans. Inst. Min. Met, 45(1993) 400. |
[9] | A. Dib, L. Makhloufi, Cementation treatment of copper in wastewater: mass transfer in a fixed bed of iron spheres, Chem. Eng. Proc. 43 (2004) 1265–1273. |
[10] | A.H. Elshazly, Intensification of the rate of heavy metal removal from industrial effluents by cementation on a reciprocating array of vertical parallel plates, Alexandria Engineering Journal, Vol. 44 (2005), No. 5, 789-895. |
[11] | Demirkiran, N., A. Ekmekyapar, A. Kunkul and A. Baysar, “A Kinetic Study of Copper Cementation with Zinc in Aqueous Solutions,” Inter. J. Min. Process. 82, 80-85, (2007). |
[12] | Cherry, K., 1982. Plating Waste Treatment. Ann Arbor Science, p. 46. |
[13] | Kuntyi, O.I., Znak, Z.O., Dyug, I.V., 2003. Contact deposition of copper powders onto Zinc in H2SO4–CuSO4 and H2SO4–CuSO4–Zn SO4 solutions and their morphology. Russ. J. Appl. Chem. 76 (12), 1942–1945. |
[14] | S. A. Nosier, Removal of Cadmium Ions from Industrial Wastewater by Cementation, Chem. Biochem. Eng. Q. 17 (3) 219–224 (2003). |
[15] | N.K. Amin, E.-S.Z. El-Ashtoukhy, O. Abdelwahab, Rate of cadmium ions removal from dilute solutions by cementation on zinc using a rotating fixed bed reactor, Hydrometallurgt 89 (2007) 224–232). |
[16] | V. Stankovic, S. Šerbula ,B. Janeva, Cementation Of Copper Onto Brass Particles In A Packed Bed, Journal of Mining and Metallurgy, 40B (1) (2004) 21 – 39. |