Patrick O. M. Ogutu1, Nicholas Oyie1, Winston Ojenge2
1Department of Electrical Engineering, Murang’a University of Technology, Murang’a, Kenya
2Department of Electrical Engineering Technical University of Kenya, Nairobi, Kenya
Correspondence to: Patrick O. M. Ogutu, Department of Electrical Engineering, Murang’a University of Technology, Murang’a, Kenya.
Email: |  |
Copyright © 2021 The Author(s). Published by Scientific & Academic Publishing.
This work is licensed under the Creative Commons Attribution International License (CC BY).
http://creativecommons.org/licenses/by/4.0/

Abstract
This paper is about performance improved chicken chicks’ Banda, which uses the environmental conditions to measure and control the cage humidity and temperature. The change in environmental condition is used to turn on the heater and the fan so as to achieve the expected temperature and humidity. The research l developed the system mathematical model depicting the chicken chicks’ Banda, designed a prototype humidity and temperature controller and use the learned behavior to implement a simulation of two systems that is the fuzzy logic and neuro fuzzy logic to analyze the behavior by using the Matlab tool box. Neural fuzzy logic is used to monitor and control the chicken chicks’ cage desired temperature and humidity which is of set target of 27°C and 60% respectively. The result should show that the process controller is able to keep track on the reference input and the resultant response of neural fuzzy control so as to better track and optimize performance in comparison with fuzzy only controllers. The hybrid optimization method which consist of least square estimator and Back propagation should be used in the process and the training done using gradient descent method. The result show that there is improved performance as depicted by a settling time of 0.8 seconds to 0.5 seconds and overshoot improvement from 30% to 0.935% as a result of neuro- fuzzy technique.
Keywords:
Controller, Logic, Fuzzy Logic, MATLAB, Neural Fuzzy Logic, Optimize
Cite this paper: Patrick O. M. Ogutu, Nicholas Oyie, Winston Ojenge, Performance Improvement of a Chicken Chicks’ Banda Using Neuro-Fuzzy Logic Controller, Electrical and Electronic Engineering, Vol. 11 No. 1, 2021, pp. 7-12. doi: 10.5923/j.eee.20211101.02.
1. Introduction
Temperature and humidity environmental control is utilized in nearly each and every field of application such as domestic set up, industries, research work and other many areas. The paper illustrate a mathematical model of a chicken chicks’ Banda temperature and humidity control using [1] neural Fuzzy logic control. Based on practical data taken in the laboratory set up, a transfer function model of the chicken chicks’ Banda temperature control system is formulated. Then a system design of a neural Fuzzy logic is fully implemented so as to improve its step input response. The research explores the capability of using hybrid in improving system performance and behavior in comparison to other known methods. The conventional PID controllers are not efficient and reliable due to the non-linearity presence in the process and to make the matters worse it results into maximum overshoot and settling time.The major focus of this research is to apply hybrid technique that is neural fuzzy to model, design and test the controller to get optimum performance at the expected output. It has been realized that, though Ziegler Nichols tunes systems very optimally, a better performance is needed for very fine response and this is obtained by using neural-Fuzzy Logic Controller [2] (FLC) methodology. In this research, the temperature and humidity control of a chicken Banda is implemented using micro controller designed and programmed unit and then neuro-fuzzy logic controller made as per the experimental data. After implementing the design, the [1] temperature of the cage can be kept between 22°C to 27°C which happen to be the desired temperature and the humidity is kept between 60 to 80%. Proper ventilation and humidity of the chicken chick’s Banda is achieved by monitoring the amount of water in the cage.
2. Literature Review
The operation of machines by the use of human being as the main controller of the process has a lot of human errors resulting in inaccurate final product. The highlights and overview of literature review discussed depicts poor performance in temperature and humidity control. Different processes usually require process timers’ counters, relays and temperature controllers which in reality do not provide improved performance. The change from static state of the process to the dynamic condition causes significant variation in the process performance as discussed by different authors:-Heat exchanger temperature control was studied by [1] - [2] and the system took 45 seconds to raise to the set point and during oscillation time it took 20 seconds to attain stability. The new controllers showed success in decreasing the switching while the model predictive controller improved the temperature control i.e. smooth temperature was achieved. A simplified thermal model and optimal temperature control accurately predicted the thermal characteristics and the average mean square errors at 11.14% and 12.82% respectively. Accurate linguistic neuro fuzzy models was effectively built by [3] - [4] that competed well with other existing approaches, both conventional and intelligent control method is optimized to the advantage of the system however neural network was found to be hard to put in real application but effected fast response time. Advanced controllers were used to reduce errors and increase in energy consumption. The Artificial Neural Network-ANN model displayed best results to intermittent thermal change when compared to ON/OFF base line controller. The model reduced the time lapse to reach the desired temperature. Addition of neural network resulted into a stabilized temperature. The researchers [5] - [6] Studied Fuzzy Logic Controller FLC /Genetic Algorithm- GA and GA-Proportional Integral Controller-PID schemes were effectively used for stability control for nonlinear system. The author could not identify the controller that is more superior to the other. Simulated results demonstrated that there was improvement in learning the system performance in relation to previously employed system. The PID tuning parameters were determined using GA with fuzzy logic control, the control output reached the steady state error faster however the overshoot and settling time was not covered well hence the introduction of this paper to bridge the gap.Clearly detailed investigation by [23] on the limits of permissible discretization using deterministic artificial intelligence (DAI) was used to provide optimal learning and trajectory shaping to improve the step performance. DAI outperformed the model following approach resulting into minimal transient by almost 2-70% and the model following action resulted into 29% less error in input compared to DAI due to efficacy with discretized implementation.Pontryagin minimization of Hamilton systems was used by [24] to derive controls proved efficacy for sensors and autonomous systems however the Hamilton final value was not met however other optimally conditions were fully met and realized, The question of the six optimally necessary condition when not in agreement was not declared in the study.Sensors play a vital role in control, [25] investigated the algorithm option for combining physical (noisy) sensors and computational modes to provide additional information about system states, inputs and parameters emphasizing on deterministic options rather than the stochastic one. The proposed method achieved 69-72% improved state estimation and 29-33% while simultaneously achieving mathematically minimized cost of utilization in guidance, navigation and control criterion.
3. Modelling Design and Methodology
The process is modelled by considering the temperature of the surrounding and the internal conditions. Consider the Energy conservation principle [7] | (1) |
 | (2) |
Let the heat transfer of air be given by hairTherefore 

 | (3) |
Now let d/dT be given in terms of S domain and combining equation 1, 2 and 3 hence resulting into
becomes 
 | (4) |
Let
Then 
Transfer function =
Where by Tif = is the Time constant which can be obtained by the formulae =
The symbol KIf = is the gain of the plant which result into the formulae =
The chicken chicks’ Banda modelled system is a first order with a time constant which depends on Density of air, Heat capacity of air, Area of the wall and Overall heat transfer coefficient for the wall. The transfer function is directly proportional to the gain constant of the plant which is inversely proportional to Heat capacity of air and Area of the wall.This paper tackles the performance improvement of chicken chicks’ Banda. The materials used to achieve the research results include a bulb, humidity sensor, temperature sensor, cooling fun, display unit, and Arduino and Matlab software. The method used to achieve the desired results is stated as follows:-the circuit is connected as per the circuit diagram and the characteristics behavior of the system is observed for fuzzy and neuro fuzzy system using the Matlab Simulink. The circuit was designed using Simulink Matlab software as shown in fig 1 with the following components: -step input, error detector, derivative unit, PID controller, Mux, scope and the fuzzy logic controller. Fuzzy rules were created for humidity and temperature respectively and Mamdani type used to create the fuzzy logic design. While for ANFIS dated was loaded, FIS generated, and validated then loaded in the circuit. The circuit was then run and the two scopes observed. Hybrid artificial intelligent and optimization algorithm was successfully used for modelling and optimizing the process to improve the performance.
4. Results and Discussions
Results of the fuzzy and neuro fuzzy process is tabulated in the table 1 and 2 this is after designing the fuzzy inference system and loading the data in mat lab Simulink. The rule viewer describe the graphic display of the temperature, error and the crisp output at different locations, for this case when the temperature is set at 20°C and error deviation is 20 then the crisp output will be 14 which is the degree of the next cause of action. The same will vary when the position are altered as in described in Figure 1.Table 1. Parameters description 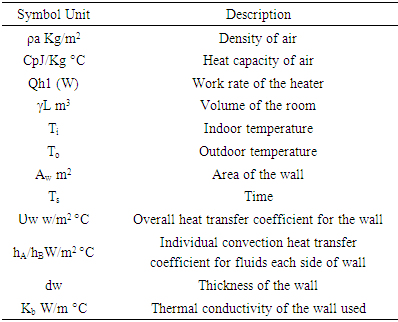 |
| |
|
Table 2. Overshoot calculation 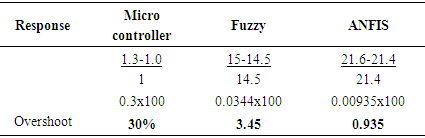 |
| |
|
Table 3. Comparison of settling time and peak over shoot 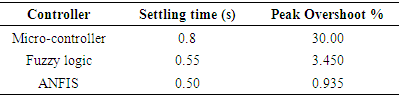 |
| |
|
 | Figure 1. Fuzzy output rule viewer |
The FLC Toolbox doesn't restrict the input number and the Surface Viewer was utilized to show the dependence on the outputs on any of the inputs it generated and plotted the output map as viewed on the surface. The surface viewer Matlab Fuzzy toolbox was limited to two inputs and one output thus becoming a 3D system, with the axis depicting the error, temperature and the resulting output as described in Figure 2.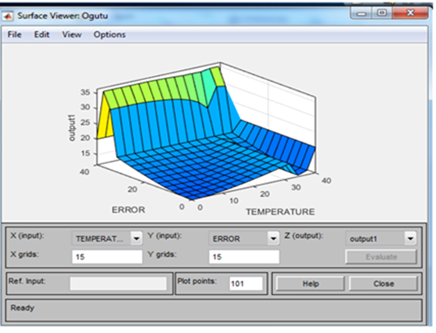 | Figure 2. Fuzzy surface viewer |
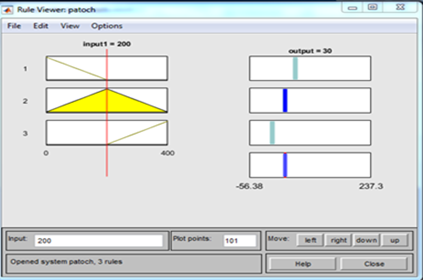 | Figure 3. Fuzzy rule viewer |
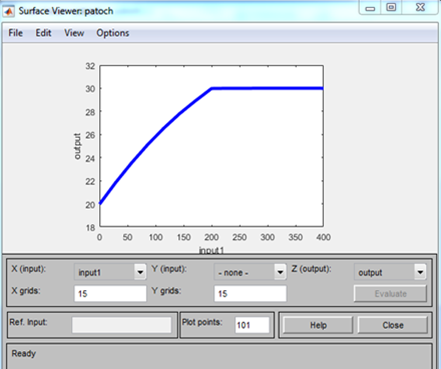 | Figure 4. Fuzzy rule viewer |
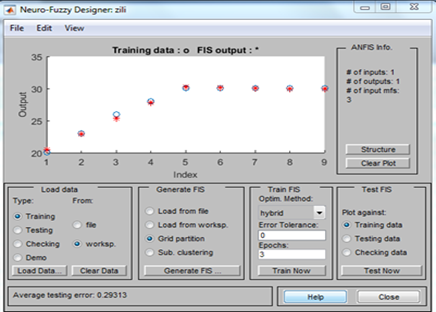 | Figure 5. Neuro -fuzzy designer |
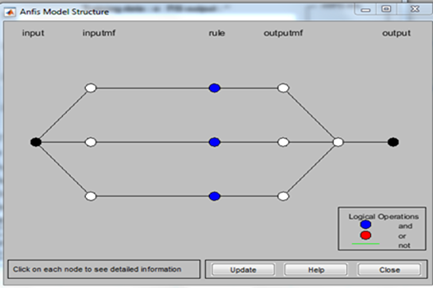 | Figure 6. ANFIS model structure |
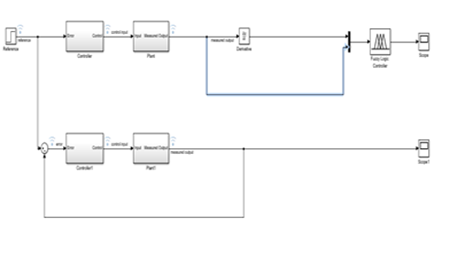 | Figure 7. General circuit diagram |
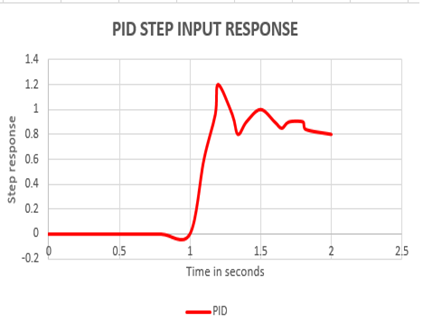 | Figure 8. PID output step response |
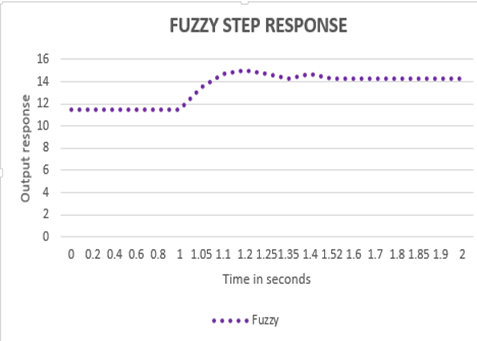 | Figure 9. Fuzzy output step response |
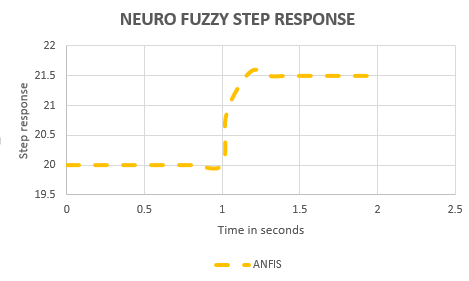 | Figure 10. Neuro fuzzy output step response |
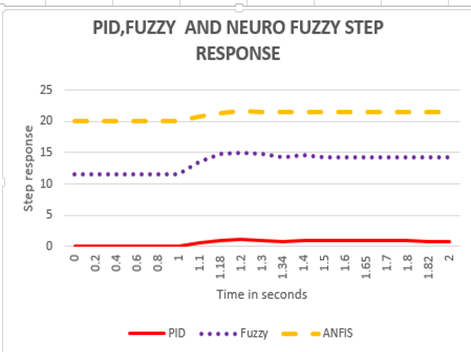 | Figure 11. PID, FLC and Neuro fuzzy output curve comparison |
The desired data was created and then saved at the workspace, anfis edit was then inserted at the command space, then the training data was loaded, then FIS was generated, then data was trained at different epochs at the grid partition, optimization was done using Hybrid method and not back propagation. The data was then tested and the following results was realized. The membership function was set to 3 while the type was trimf, the output type was set to constant, and error tolerance was set to 0 at Epoch of 3.The results from the table 2 above shows that the system has better response in terms of settling time and peak overshoot when ANFIS is used comparison to the use of PID and FLC. The process is optimized and the system is able to handle process disturbances with less effect to the set points.There is almost 21% percent performance improvement in the neuro fuzzy controller compared to a declared benchmark that is PID and Fuzzy logic controllers in terms of peak overshoot and further while. using hybrid optimization the settling time was improved from 0.8 seconds to 0.5 seconds which is remarkable improvement compared to the conventional methods.
5. Conclusions
The study was done on modeling and temperature control of a chicken chicks’ Banda using neuro-fuzzy logic for optimum performance and the results showed that ANFIS controller using hybrid optimization improved the settling time, the under shoot, the efficiency and the overshoot. This finding will go a long way in ensuring sufficient use of this technology to increase the production of healthy chicks in the Kenyan market hence achieving the government agenda of ensuring food security. The paper highly contribute to the stabilization of humidity and temperature in the poultry industry.
6. Future Research
To investigate the efficacy of virtual sensoring amidst unknown control actions using variations of optimization to provide state, rate and decision/control to set platform for virtual sensioring as possible future sensor replacement.
ACKNOWLEDGEMENTS
I really acknowledge the following for their contribution into the success in this paper my mum, my wife and children, the staff of the technical university of Kenya and more thanks go to my technical advisers for ensuring that the work is up to standard.
References
[1] | J. Agus, "Heat exchanger control based on artificial intelligance approach," international journal of engineering and research, vol. 11, no. 16, pp. 9063=-9082, 2016. |
[2] | Z. Zhao, "Simplified thermal model and optimal control for chilled water pipe in air conditioning system," 2019. |
[3] | A. K. Goel, "A genetic based neuro fuzzy controller for thermal processes," Computer science and technology, vol. 5, no. 1, 2005. |
[4] | F. Liu, "Comparison of ANFIS and fuzzy PID control model for performance in two axis inertia stabilized platform," 2017. |
[5] | D. Xiuxia, "Fuzzy logic control optimization using GA for multi area AGC system". |
[6] | C. C. Lee, "Intelligent control based on fuzzy logic and neural network theory," 2020. |
[7] | G. V. Dobb's, Fuzzy logic in Control, 1993. |
[8] | T. U. Denmark, Tunning of Fuzzy PID controller, 1998. |
[9] | J. Hulzerbosch, Effecting heating system for poultry houses, vol. 22, W. Poultry, Ed., 2005. |
[10] | E. D. Bolat, "Implimentation of MATLAB SIMULINK Based on Real Time Temperature control for set point changes," International Journals of circuit systems and signal processing, vol. 1, no. 1, pp. 56-61, 2007. |
[11] | M. Ahmad, "Hubrid Fuzzy logic control with input shaping for input tracking and sway suppression of Ganty Grains Crane system," American Journal of Engineering and Applied sciences, vol. 2, no. 4, pp. 241-251, 2005. |
[12] | L. B. Jaafar, "Automatic room temperature control," University of Tun Hussein, 2013. |
[13] | S. Das, "Performance comparison of optimal fractional order hybrid fuzzy PID controller for handling oscillatory fractional order process with dead time," 2016. |
[14] | H. Carlborg, "Modelling and temperaure control of an industrial furnace," University of sweden, 2016. |
[15] | C. F. Juang, "Mold temperaure control of rubber injection moulding machine by TSK type reccurent fuzzy network," Neoro computing, vol. 70, no. 3, pp. 559-567, 2006. |
[16] | D. M. Atia, "Analysis and design of green house temperaure control using adaptive neuro fuzzy inference system," Journal of electrical systems and information technology, 2017. |
[17] | J. Ahn, "Analysis of energy and control efficiencies of fuzzy logic artoficial neural network technolgies in the heating energy systems responding to changes of user demands," 2017. |
[18] | S. K. Mallick, "Study of the design and tuning methods of PID controller based on FLC and GA," National insititute of technology, 2006. |
[19] | L. A. Yusuf, "Comparison of fuzzy logic and GA PID controller for position control of inverted pendulum," 2015. |
[20] | S. N. Ikhalas, "Optimization of PID control parameters with GA plus fuzzy logic stirred tank heater temperature control," ICEECS, 2017. |
[21] | H. John "Heat transfer text book," Phlogogiston Press, 2020. |
[22] | M. Gopal, "Controllabilty," New age international, 2005. |
[23] | R. Shah and T. Sand “Comparing Methods of DC motor for UUVs, Applied sicences 11, 4972 2021. |
[24] | T. Sand “Optimization provenance of whiteplash compensation for flexible space robotics”, Depatment of Mechanical Engineering (EVN), New Yotk USA 2019. |
[25] | T. Sand “Virtual sensors of motion using Pontryagin’s treatment of Hamilton system” Journal of Marine science and Engineering Sensors 2021 21/4603 https://doi.org/10.3390/s21134603,2021. |