K. V. Bezruchko, A. O. Davidov, J. G. Katorgina, S. V. Sinchenko, S. V. Shirinsky
Laboratory of autonomous power engineering, National aerospace university, Kharkov, 61070, Ukraine
Correspondence to: A. O. Davidov, Laboratory of autonomous power engineering, National aerospace university, Kharkov, 61070, Ukraine.
Email: |  |
Copyright © 2012 Scientific & Academic Publishing. All Rights Reserved.
Abstract
Causes of degradation of electrochemical batteries, constituent in the power-supply system of objects of space-rocket technology, in the article are studied. Methods of determining the battery life time reduced. With no possibility of an experiment or a lack of time, the method of battery life time prediction is proposed for use. This method is based on the mathematical model, which is based on experimental data obtained in the battery life tests. The equations included in this mathematical model are presented. Recommendations for the use of method of prediction are presented
Keywords:
Electrochemical Battery, Degradation, Life Time, Method, Prediction
Cite this paper: K. V. Bezruchko, A. O. Davidov, J. G. Katorgina, S. V. Sinchenko, S. V. Shirinsky, Method of Prediction the Performance of Electrochemical Batteries, Long Working in Power Plant of Space-rocket Objects, Electrical and Electronic Engineering, Vol. 3 No. 3, 2013, pp. 81-85. doi: 10.5923/j.eee.20130303.01.
1. Introduction
Power supply system, which provides functioning of almost all the devices of the spacecraft, is a key component of most of the objects in space-rocket technology.Modern power supply systems are based on the scheme of direct transmission of energy from generator to the load, but their composition and design can vary depending on the purpose and specificity of a spacecraft. Functionally power supply system consists of generation subsystem, purpose subsystem and service equipment. The most part of the modern spacecraft has its service life time from 1 to 5 years, but in some cases life time can come up to 10-15 years. Usually, such life time can be achieved by increasing the capacity of the batteries and increasing the cost of the power supply system of a spacecraft.For the direct determination of the life time of electrochemical batteries financial and time costs are to be invested considerable. Thus, nowadays, an accurate determination of the battery parameters at any time of their operation and prediction of their performance for the long term is not the solution.
2. Causes of Batteries Degradation
Occurred in the battery degradation processes lead to lower battery performance. Decrease of discharge capacity, decrease the discharge voltage, increase the charging voltage, increase the self-discharge and other signs of deterioration in the values of the basic parameters of the battery are the result of the degradation processes. Therefore, the actual battery life time depends on a number of degradation processes occurring there. (see Fig. 1)[1].Based on the analysis of nickel-cadmium batteries, it can be concluded that over time there is a gradual deterioration of their performance (especially at the end of the discharge). Degradation processes that lead to deterioration of battery performance associated with either irreversible (partially reversible) chemical reactions, or the structural changes of the active mass of the electrodes.[2, 3]. This deterioration is inevitable. However, this deterioration can diagnose, predict and determine the remaining life time. All of these innovations will significantly shorten time of the test battery. In addition, it will identify the imbalance battery in the pack in the early stages.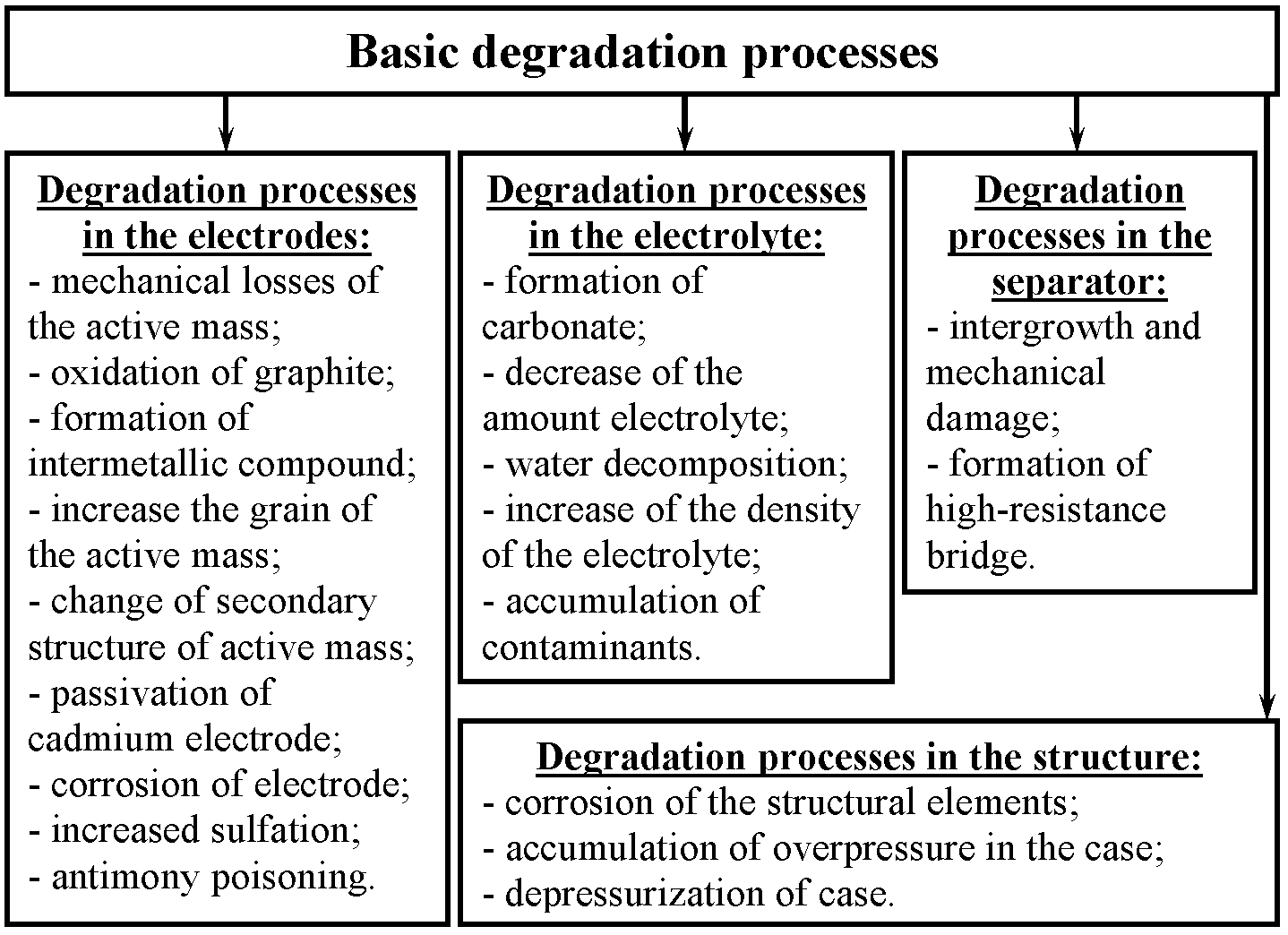 | Figure 1. Basic degradation processes that occur in batteries for their operation |
3. Methods for Determination of Life Time
Battery life time can be defined both as mathematical model and experimentally. (Fig. 2).Traditional experimental methods to determine the battery life time involve tests in real-time scale. The duration of these tests is unjustifiably high. The use of accelerated life tests will significantly shorten the determination of battery life time[4, 5]. However, the battery life time can be determined without experimental studies (e.g. in the spacecraft) or a shortage of time to use prediction.The process of prediction the characteristics of electrochemical batteries is very time consuming as it requires making the most detailed mathematical model of the battery, which takes into account the effect of all processes in the battery (current-producing and degradation).The primal problem of prediction is to identify changes in the characteristics and parameters of the temporally. At present there is a number of methods for prediction[6] (Fig. 3).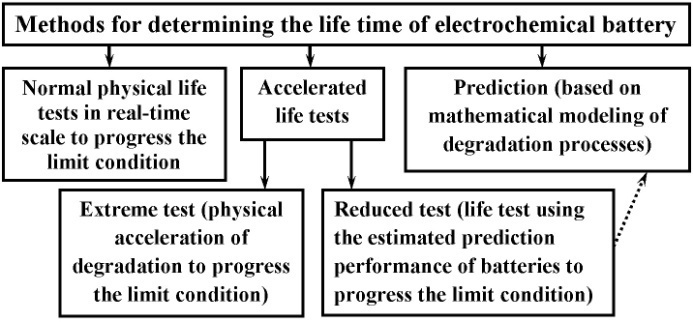 | Figure 2. Methods for determining life time of electrochemical batteries |
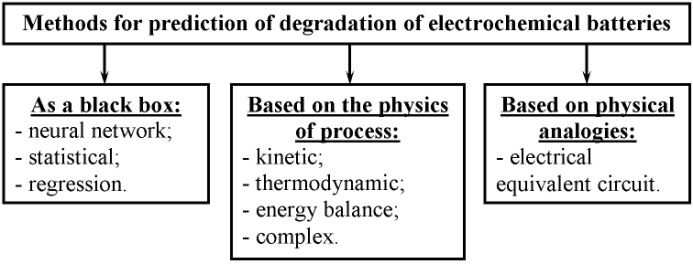 | Figure 3. Possible methods for prediction of degradation of electrochemical batteries |
4. Development of Method for Prediction of Behaviors of Batteries for a Long Period of Operation
To solve the problem of predicting the state of batteries for a long period of operation, the authors have developed a method for prediction life time based on the current values parameters of the batteries. Application of this method allows determining the most favourable operating modes of the batteries.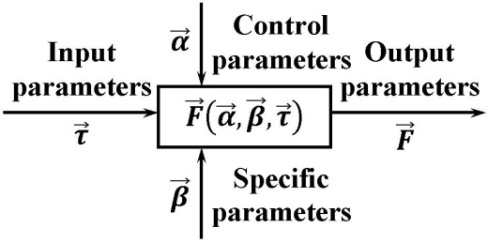 | Figure 4. Possible methods for prediction of degradation of electrochemical batteries |
Method for prediction life time of the battery using the current values of the parameters, suggested by the authors, based on the application of mathematical models built on the results of battery life tests.The structure of used model is shown in Fig. 4.Depending on an operation mode, duration of operation, number of charge-discharge cycles, charge or discharge time can be input parameters of model.As control parameters of model the values characterising external effects on the battery are used. The most important such parameter is the ambient temperature. For simplification it is accepted, that the battery is in thermal equilibrium with environment.Specific parameters of model are intended for the features of the particular battery or type of batteries characteristics description.As model output parameters are used the parameters of the battery which are most important at operation such as: voltage, capacity and a battery internal resistance.The procedure for the development and application of the method for prediction life time of the battery is shown in Fig. 5.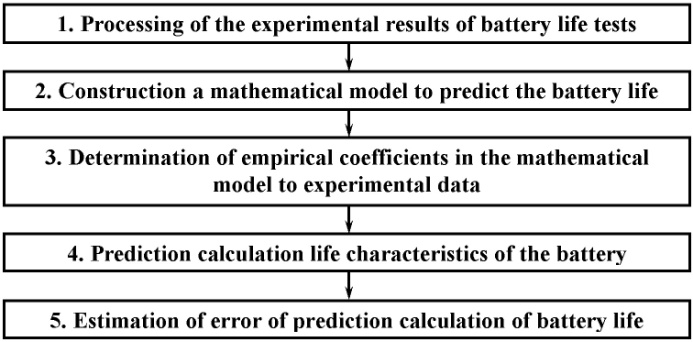 | Figure 5. Algorithm prediction calculation of life time of accumulators based on the current values parameters of the batteries |
Table 1. The equations included in the mathematical model of the electrochemical battery operating in standby mode 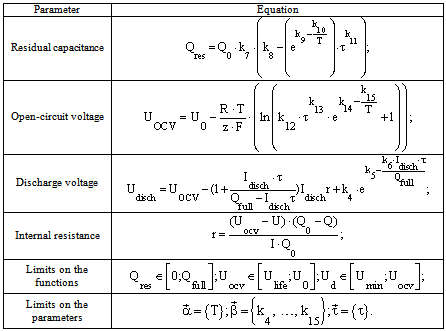 |
| |
|
Table 2. The equations included in the mathematical model of the electrochemical battery operating in buffer mode 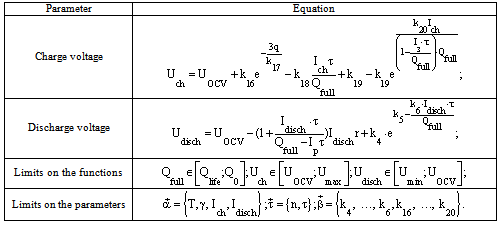 |
| |
|
Operation of some batteries is based on alternation of charge and discharge periods. Assess the effectiveness of the battery at such operation is performed by analysing the capacity characteristics of the batteries. Therefore, the battery capacity is a key parameter for prediction. The dependence of the capacity from a large number of parameters is taken into account in the development of the mathematical model.All this dependences were included to the mathematical model of electrochemical battery operating in standby mode (Table 1) and electrochemical battery operating in buffer mode (Table 2).A mathematical model developed by the authors, predicts values of the basic parameters of the battery (capacity, internal resistance, open circuit voltage, etc.) and their characteristics (charge-discharge and volt-ampere) for long periods of operation. Experimental data of current values of the basic parameters of the battery were used for the calculation of the empirical coefficients of the mathematical model by means of a method of the least squares.
5. Results of the Numerical Experiment
Verification of the mathematical model was carried out on the basis of experimental resource data derived from an additional independent experiment.Figure 6 shows the capacity (a) and voltage (b)nickel-cadmium batteries НКП-90 calculated with the help of the developed mathematical model based on the current values of the battery. These batteries operate in standby mode.Figure 7 shows the minimum voltage per circle (a),charge voltage (b) and discharge voltage (c) nickel-cadmium batteries НКГ-4СК calculated with the help of the developed mathematical model based on the current values of the battery. These batteries operate in buffer mode.The calculated data were compared with experimental data obtained from life tests (shown in figures 5 and 6 crosses).The mean absolute error and the mean error of approximation were calculated to confirm the accuracy of the mathematical model. The values of the mean error of approximation for the capacity and voltage do not exceed 2% in standby mode. The values of the mean error of approximation for minimal voltage, charge voltage and discharge voltage does not exceed 4% in buffer mode. The mathematical model is adequate, because the values of mean error of approximation do not exceed the critical value of 10%.When comparing the calculated and experimental data were refined empirical coefficients of the mathematical model. The next prediction characteristic of the battery was performed using refined mathematical model.Figure 8 shows the results of predicting the capacity of the battery with a refined mathematical model.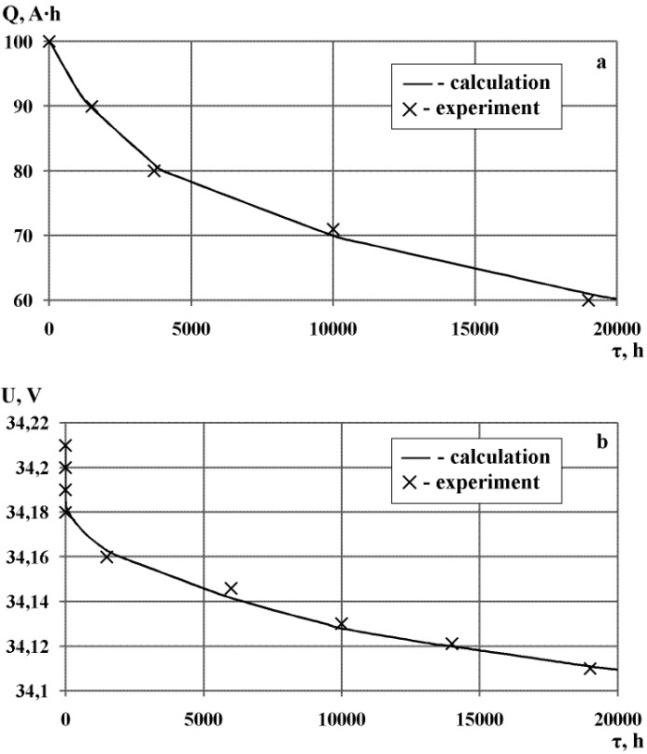 | Figure 6. The results of the calculation of capacity (a) and voltage (b) nickel-cadmium batteries НКП-90 operating in standby mode with the help of a mathematical model |
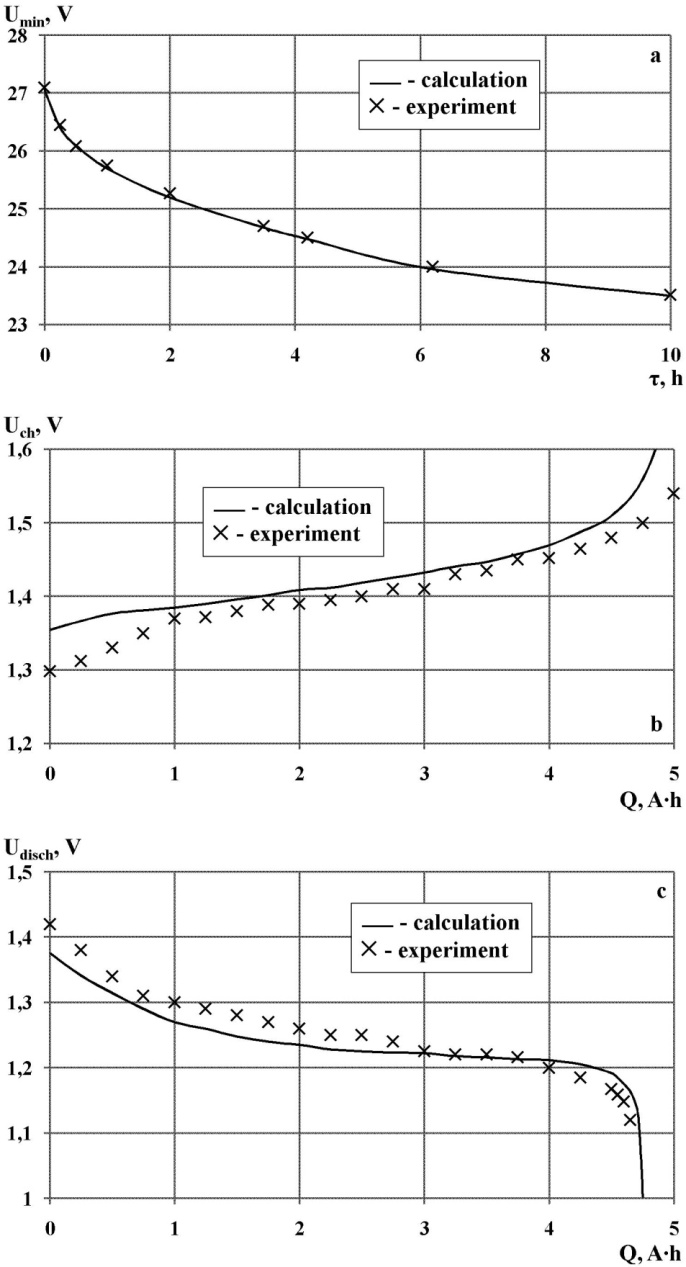 | Figure 7. The results of the calculation of minimum voltage per circle (a), charge voltage (b) and discharge voltage (c) nickel-cadmium batteries НКГ-4СК operating in buffer mode with the help of a mathematical model |
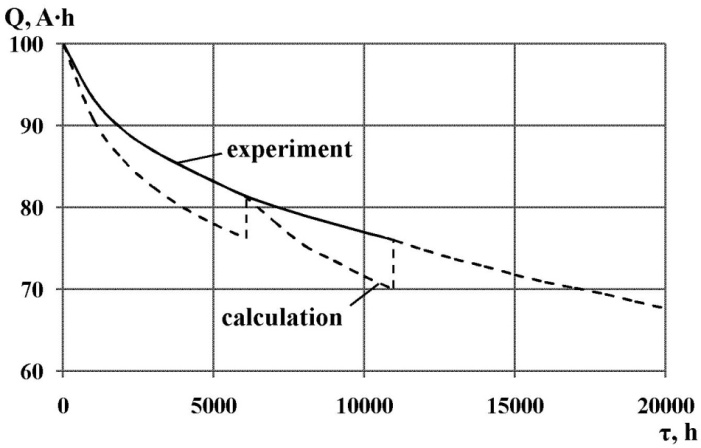 | Figure 8. Results of prediction capacity of electrochemical batteries |
6. Conclusions
The method of prediction, developed by the authors, allow to:1. diagnose the condition of the battery;2. predict the loss of battery capacity in operation;3. reduce the time of test battery;4. predict the time of failure batteries;5. predict the change in charge and discharge characteristics of the battery;6. identify and compensate imbalance batteries in the pack in the early stages;7. provide favourable mode of operation of batteries.Based on the above, the authors propose to use this method of prediction for:1. time correction of the control logic of power supply system and the organization of an optimum mode of operation;2. time compensation imbalance of capacity of battery in the pack;3. determining the need for recovery work;4. speeding up and simplifying experimental testing of power supply system;5. design of a new power supply systems and new types of electrochemical batteries.The method of prediction, developed by the authors, can be used to predict the characteristics of any of nickel-cadmium batteries are running in standby and buffer mode.
References
[1] | A.A. Kharchenko, “Analysis of the causes of degradation of nickel-cadmium batteries in the power plants of flying vehicle,” Aerospace Engineering and Technology, vol.30, pp.266-272, 2002. |
[2] | V.V. Romanov. J.M. Hashev, Electrochemical power source, 2nd ed., Moscow, USSR: Soviet radio, 1978. |
[3] | J.E. Gindelis, Electrochemical power source, Saratov, USSR: Publisher SSU, 1984. |
[4] | S.V. Shirinskij, K.V. Bezruchko, “Application of accelerated testing to assess the residual life of batteries,” Dnipropetrovsk University Bulletin, no.9/2, pp.181-185, 2007. |
[5] | S.V. Shirinskij, “Theoretical aspects of accelerated testing of alkaline batteries to self-discharge,” Aerospace Engineering and Technology, vol.28, no.2, pp.37-40, 2006. |
[6] | A.O. Davidov, T.S. Kadigrob, V.I. Laznenko, “Prediction of performance of electrochemical batteries, operating in standby mode,” Aerospace Engineering and Technology, vol.67, no.10, pp.199-202, 2009. |