K. K. Leung1, K. M. Chau2
1Asset Management Department, CLP Power Hong Kong Limited, Hong Kong, China
2Engineering Projects Department, CLP Power Hong Kong Limited,Hong Kong, China
Correspondence to: K. K. Leung, Asset Management Department, CLP Power Hong Kong Limited, Hong Kong, China.
Email: |  |
Copyright © 2012 Scientific & Academic Publishing. All Rights Reserved.
Abstract
Driven by ever-changing business environment, technological innovations and changes of supply / demand markets are very common nowadays. These may create either risks or opportunities to power business operators. CLP Power Hong Kong Limited (CLPP), a power utility in Hong Kong, has therefore developed a systematic approach to ensure high reliability of the High Voltage (HV) cable system while driving the cost down. This paper shares CLPP’s approach in three key parts, namely prudent design procedures, strategic sourcing of suppliers and installation management. Riding on the technology advancement of cable industry, HV slimCross-linked Polyethylene(XLPE) cable system is well proven learnt from the sound experience in Extra High Voltage (EHV) cable industry. The reduced cable size is beneficial for cable transportation, ergonomics and environmental protection. The Company’s 2-level Strategic Sourcing Model helps source price competitive yet quality suppliers. With in-depth investigation in suppliers’ long-term sustainability, the suppliers selected through this model created significant saving to the Company without sacrificing system reliability. Together with the optimised installation and commissioning practices, the approach has delivered significant contributions to CLPP, such as maintaining high reliability, saving cost, securing cable material supply, and achieving high safety, health, environment and quality (SHEQ) performance.
Keywords:
Sourcing, Oil-filled Cable, Cross-linked Polyethylene (XLPE), Medium Density Polyethylene (MDPE), Slim Cable, Insulation, Pre-fabricated Joint, Total Life Cycle Cost (TLCC)
Cite this paper:
K. K. Leung, K. M. Chau, "From Slim Design, to Strategic Sourcing of Supplier, to Optimised Installation and Commissioning of HV Cable System in CLP Power HK Limited", Electrical and Electronic Engineering, Vol. 2 No. 6, 2012, pp. 355-361. doi: 10.5923/j.eee.20120206.03.
1. Introduction
High voltage (HV) cable system serves the backbone of power network in CLPP. Any failure in HV cable system may cause disastrous power interruption. While HV cables have been massively employed in the Company’s transmission grid, effective means to ensure optimized project cost, technically sound design, good product quality and well controlled installation management are of utmost importance. Therefore, when developing new components in HV cable system, the procurement team and project team put every possible effort to achieve the objectives through prudent design procedures, strategic sourcing of suppliers and installation management.The development of new HV cable products, sourcing cost-competitive suppliers together with the optimized installation and pre-commissioning procedures have delivered significant tangible and intangible benefits. This paper illustrates the impressive development process through a recently implemented cable project – adopting HV XLPE cable with thinner insulation.
2. Project Background
In CLPP, oil-filled cable was the earliest cable type used in the 132kV cable system. After 1990’s, Cross-linked Polyethylene (XLPE) insulated cable has become the main cable type for new circuits due to the proven technology, environmental friendliness, simpler design and easier installation and maintenance for cables and accessories as compared with oil-filled cable system. At that time, the status quo of XLPE cable technology allowed insulation thickness of around 20mm for 132kV XLPE cable. Technology producing cable made of thinner XLPE insulation was not mature[1].With significant improvement in XLPE cable insulation technology, in terms of design, materials, manufacturing control and the quality assurance, a new generation of 132kV XLPE cable with thinner XLPE insulation has emerged and become mature[2]. Therefore, an assessment of the insulation thickness to be adopted for 132kV transmission cable was conducted, aiming at comparing the pros and cons of cables with 20mm insulation and those with thinner insulation of 17mm (hereafter slim cable), and recommending the most beneficial choice of insulation thickness for 132kV XLPE cable in CLPP.
3. Business Drivers
In the Company, it is the business objective to optimise Total Life Cycle Cost (TLCC) by adopting the 132kV slim XLPE cable design without sacrificing supply reliability, equipment quality and compatibility with conventional cable of thicker (20mm) insulation[3]. Moreover, the introduction of slim cable should not block the entry of cost-competitive suppliers, which are the key driver to lower the purchase price in open bid environment.To meet the above objectives, a comprehensive approach covering design, supplier sourcing and installation management is developed accordingly.
4. Design
4.1. Technical Soundness
In cable design, cable insulation thickness is generally determined by thickness for AC voltage (tAC) or thickness for impulse voltage (tImp). The minimum insulation thickness calculated by this concept is less than 17mm for 132kV XLPE cable[8]. However, the calculation is based on the average electrical stress. In practical situation, maximum stress shall be strictly met for allowable defect level and quality control in factory and on-site[9]. For cable system installed by direct burial method like the situation in CLPP, adoption of slim cable type in the earlier stage is not appropriate due to the huge subsequent impact and effort for fault repair in case of type fault or quality defect by possibly immature technology.
Um: Maximum line voltageEL,AC: Minimum AC breakdown stressBIL: Lightning impulse withstand voltageEL,Imp: Minimum impulse breakdown stressK1 through K6:Compensation factors due to aging, temperature and safety marginDepending upon cable conductor size, the electrical stresses of 132kV slim cable range from 5.5kV/mm to 7.8kV/mm at conductor screen and 2.8kV/mm to 3.7kV/mm at insulation screen. In contrast, the electrical stresses of 400kV 2500sqmm XLPE cable at conductor screen and insulation screen are about 10.2kV/mm and 5.3kV/mm respectively, which have been well adopted in the EHV cable industry.In fact, new generation of HV slim XLPE cable system is developed with similar technology and design stresses to those found in EHV XLPE cable system (Figure 1). The technology soundness is well proven. 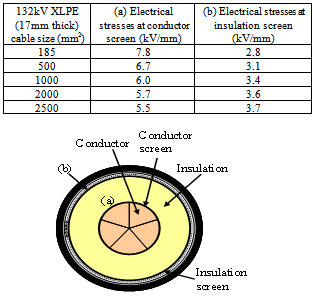 | Figure 1. Electrical stresses at different parts of 132kV XLPE cables |
4.2. Safety, Health and Environmental Considerations
Due to smaller cable size and lighter weight, the use of 132kV slim cable system can ease the transportation and installation of cable, resulting in better ergonomics. From environmental point of view, the adoption of slim cable in 132kV cable system can significantly save the consumption of raw materials for insulation and over-jacket due to smaller cable size. It is estimated that about 22% of XLPE and 8% Medium Density Polyethylene (MDPE) can be saved for production of 1000sqmm cable, and about 18% of XLPE and 5% MDPE can be saved for 2000sqmm cable.Furthermore, there is potential benefit in maximizing the transportation length of the cable to allow reduced numbers of cable drums and joints.
4.3. TLCC
Prudent cost management is a policy in CLPP. Therefore, one objective is introducing cost-effective solution to high voltage cable system with high quality and low risk exposure to equipment failure. Life cycle costs are summations of cost estimates from acquisition to disposal for both equipment and projects as determined by an analytical study and estimate of total costs experienced during their life. The assessment team has therefore to consider TLCC from the multi-dimensional perspectives including design, development, production, installation, operation, maintenance, support, and final disposition of a major system over its anticipated useful life span. The objective of TLCC analysis is to choose the most cost-effective approach from a series of alternatives so that the least long-term cost of ownership is achieved.
5. Strategic Sourcing of Supplier
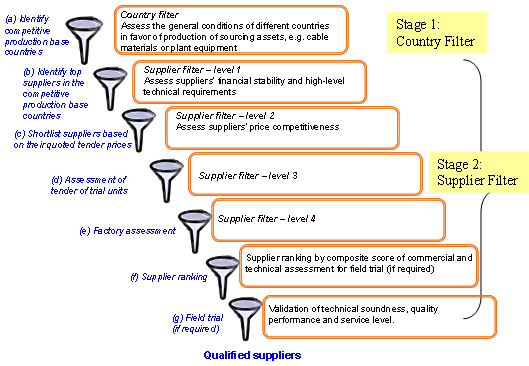 | Figure 2. Strategic Sourcing Model |
Availability of wide supply base is a key pre-requisite to the successful introduction of new product at reasonable cost. Therefore, a market survey had been carried out to assure a number of qualified suppliers were capable of manufacturing 132kV slim XLPE cable. Survey indicated that transmission cable products become mature and are manufactured in a number of emerging countries. For instance, a number of cable manufacturers there had been capable of supplying 132kV or 154kV XLPE cables with insulation thickness of 17mm or even thinner. It provides us with opportunity in cost management if we can develop and expand our supply base in the emerging regions with quality products. The saving normally results from lower production, labour, logistics, land and transportation costs. However, it also imposes challenges in maintaining existing quality level. The issues include differences in cultural and political environments, staff competency, technical capabilities, government interference and intellectual property protection, etc.To ensure that the selected cable suppliers are financially, commercially and technically sound, a Strategic Sourcing Model (Figure 2) is developed by CLPP so that the company can benchmark suppliers globally and effectively for sourcing commercially competitive and technically capable suppliers[4]. The model has two key stages below:In stage 1 of the sourcing model, countries are listed based on a TLCC basis, combined with long-term macro indicators that may well influence the long-term sustainability and profitability of the relationship. Examples of indicators are:• TLCC (e.g. labour costs, tax, duties and antidumping tariffs, other life cycle cost components, etc.)• Competence (e.g. business performance in the industry of the concerned asset type, technology readiness, production process sophistication, etc.)• Quality (e.g. ISO ownership ratio)• Logistics (logistics cost, lead time, time to export and infrastructure rating)• Miscellaneous (e.g. intellectual property protection, macro-economic stability, business sophistication, corporate responsibility, safety and pollution, foreign exchange risk, etc.)• After-sales services and quality consistence of suppliers in the countriesIn stage 2, it is proposed to short-list a few countries and then search for the optimal suppliers within each of these countries. In this stage, more micro-criteria such as industry-specific criteria and company-specific criteria can be included. Process flowchart of this model is depicted below:In this stage, CLPP begins with understanding the reference price levels and financial situations of the various suppliers passing the country filter before going into in-depth technical assessment, which normally takes much longer time than financial assessment. This is to ensure that the sourced suppliers will be at a competitive position to drive the price down in future tender. The clues to obtain valid reference price for comparison is that suppliers are informed the supplier sourcing process and the potential business volume if they are qualified. As such, a competitive price based on the potential business volume will be quoted by suppliers. Only if there is a good match of suppliers’ price level and CLP’s expectation, the engineering team will further assess the suppliers in details through in-depth desktop and factory audit.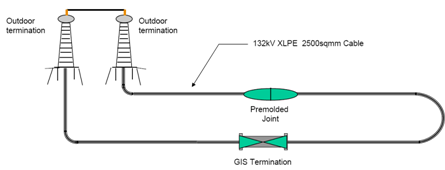 | Figure 3. Test arrangement for 132kV cable system |
5.1. In-depth Desktop Assessment
Technically sound design does not warrant good cable quality. It is equally crucial to assess the capability of individual cable manufacturers. Hence detailed investigation of supply reference of individual manufacturers is required. In this area, their historical service experience with EHV cable systems is considered a good reference to prove the technical soundness of the 132kV slim XLPE cable system. In order to ensure reliability and longevity of a cable system, the evaluation criteria for qualification shall include but not limited to the following:• Cable systems with the same constructions and accessories of the same family have been qualified for equal or higher rated voltages;• Sufficient amount of good service experience at cable systems with equal or higher stresses can be demonstrated; and• Type test has been conducted in accordance with latest version of IEC 60840[5] and relevant technical specification.
5.2. Factory Audit on Manufacturing Process and Supply Chain
CLPP regards factory audit as a key to assessing manufacturers’ implementation effectiveness of production plant. The primary purpose of such audit is to assure that the manufacturer is conducting all required tests (Figure 3)[10, 11, 12] in accordance with the international standard[5] and has standardized quality assurance procedures[4][13]. For example, the production procedures must be organized in such a way that the raw materials and manufacturing environment are well controlled with stringent conditions[14]. The audits have been proven to be very beneficial for many HV cable projects as manufacturer’s performance determines cable quality to great extent.One of the important issues to address in a plant audit is routine equipment calibration and maintenance. Cable manufacturing is a highly thermo-mechanical process. Components like extruder screws and wire-drawing dies experience wear and must be carefully maintained in order to assure that they retain their ability to produce a high-quality product (Figure 4)[6]. Extrusion zone heaters, nitrogen gas temperature measuring devices as well as production test equipment must be calibrated regularly. A good means of evaluating a manufacturer’s maintenance and calibration practices is to examine their quality manual and then verify that staff at all levels including managers, engineers and shop-floor follow their procedures.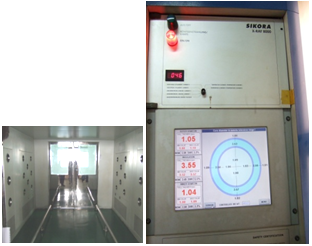 | Figure 4. Examples of quality control facilities in extrusion zone - air shower (left) and on-line X-Ray scanner (right) |
Another issue covered in the plant audit is to verify the security of supply chain. When product specification is devised, one major consideration is to adopt technologies and materials as commonly used in the supply market as possible. The more the customization is, the higher the price and supply risk are. By virtue of factory audit, CLPP can elicit true market intelligence and prepare a product specification practical to supply market while maintaining high product reliability.With sufficient findings collected from different factory audits, the audit results can be used to benchmark cable manufacturers’ plants and capability, and to aid in the selection process of high quality cable products. Furthermore, it not only gives the manufacturer notice that the purchaser is genuinely interested in purchasing a high quality cable but also it provides an ideal opportunity for the purchaser to give feedback to the cable manufacturer.
6. Installation Method and Standard
The reliability of power cable network depends mainly on the quality of materials and the quality of installation work. Stringent control of cable installation works is therefore important for cost management and assurance of high level of safety, environmental friendliness and quality. CLPP adopts direct buried standard for installation of cables. As there are increasing concerns from the public to reduce inconvenience to the traffic, ducted system is also adopted in some circumstances.In the assessment of cable technical specifications, the cable dimensions, bending radius and pulling tension are considered. 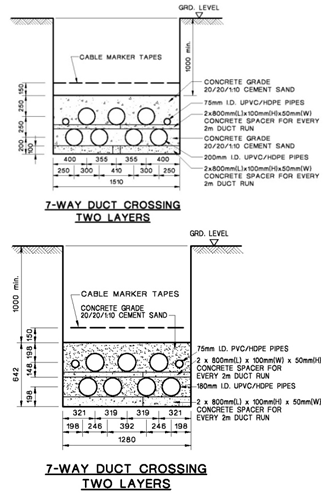 | Figure 5. Typical cross sections of the duct block |
When cables are installed in ducts, the minimum diameter of the PVC duct is usually 1.3 times of cable overall diameter (or cable overall diameter plus 30mm whichever is larger). If the cable is smaller or lighter, it is easier for site installation. Reduced insulation thickness and hence stiffness of cable also makes site installation easier.If the diameter of the PVC duct is larger, the trench width has to be increased. This will result in higher trenching cost. CLPP standardized the use of 200mm diametrical PVC pipes for installation of all cable sizes long ago. Recently, for cost optimization, we have started using cable pipes of this size only for large cables with 2000/2500sqmm conductor sizes. For smaller conductor sizes (1000sqmm or below), we have reduced the pipe diameter to 180mm and the trench width has been reduced from 1510mm to 1280mm (Figure 5). With the use of slim cable, there is further cost saving by reducing the pipe size from 180mm to 150mm and, in turn, the trench width can be reduced accordingly. Besides, more cables can be coiled in the same cable drum, leading to increased cable section length and reduced number of joints and joint bays. Though the cost saving in this aspect is not significant, it creates the benefit of easier cable laying owing to lighter weight. For example, the weights of 1000sqmm XLPE cables with 20mm and 17mm insulation thicknesses are 27.1kg/m and 24.5kg/m respectively, equivalent to about 10% reduction.
7. Pre-Commissioning Quality Assurance
To ensure post-installation quality, serving test is conducted after cables are laid. HV test is also performed before energisation of the cable circuit. These tests are to ensure integrity of the outer-sheath and the insulation. Also, there is an in-house quality assurance system to ensure the cables and accessories are installed in accordance with the relevant standard.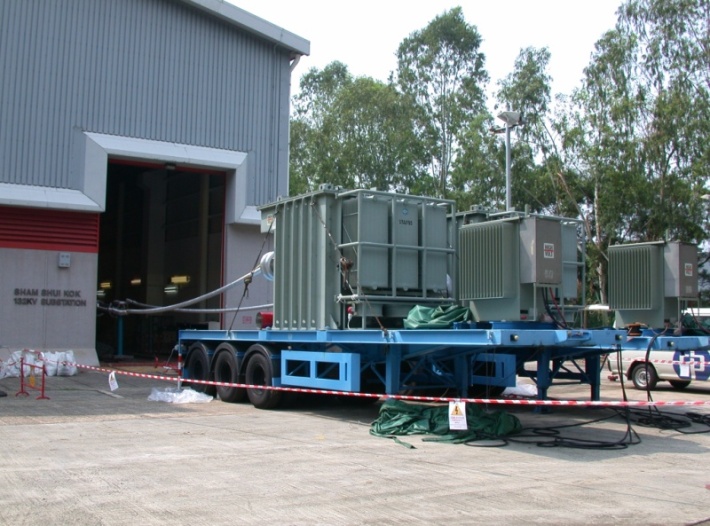 | Figure 6. HVAC testing truck employed for pre-commissioning test |
It is important to note that HVDC pressure test is well established for oil-filled cables[7] and still applicable in CLPP today. However, for XLPE cables, HVAC test is more reliable which can better detect the quality defects in the cable insulation and joints as compared with HVDC test[15]. In addition, HVDC test creates space charge accumulation in the XLPE insulation leading to much higher voltage for testing the cables subsequently. The effect is detrimental[16, 17]. In fact, the latest IEC 60840[4] also recommends HVAC for post-installation testing on cable insulation. CLPP performs the HVAC pressure test by the own project team (Figure 6).
8. Performance Review
After implementation of the new HV slim cable system, numerous benefits and implementation experience are gained.
8.1. Costs and Benefits
The actual price reduction of 132kV slim XLPE cable compared with conventional cable with thicker insulation depends on the pricing strategy of individual cable manufacturers. However, according to experience, it is found that the price of slim cable is approximately 3% cheaper than that of cable with 20mm insulation thickness, thanks to cost reduction in raw materials, manufacturing, cable drum handling, transportation and installation.In addition, there is potential saving gained from longer transportation cable drum length and less joints required for connection.On the other hand, taking into account the similar installation method, operation and maintenance effort, there is no significant difference, except easier transportation and installation, between slim and conventional cables.In short, the TLCC of 132kV slim XLPE cable is less than that of cable with 20mm insulation thickness.Most importantly, the introduction of slim cable does not narrow the supply base constituted of price-competitive suppliers. The cost saving generated by effective sourcing of price-competitive and quality suppliers is even much more significant. A double-digit percentage saving is not uncommon if it is ended up with the spend on cable produced in emerging countries.
8.2. Implementation Experience
Successful management of changes is crucial to overall project implementation. For instance, the insulation thicknesses of cables installed in each section of the circuit need to be captured in the line diagram and the commissioning test report stored in standardized information technology platform. This is to ensure proper knowledge management and facilitate future maintenance.Another issue is the interfacing problem that could arise when slim cable is connected to the old cable with 20mm insulation thickness. Previously, the design of joints was only suitable for connecting old cables. In order to tackle this problem, detailed scrutiny of existing joint design was carried out to ensure compatibility of jointing new and old cables together. Furthermore, as an error-proof measures, an application matrix of joints was prepared to show the compatible sizes of cables which can be jointed together.In the performance reviewon previous experience, factors influencing practicality for project implementation are assessed thoroughly. When cable insulation thickness is reduced, the impact on cable joint design is comparably greater as compared to that of cable. Therefore, thekey factors for consideration aremainly related to cable joint. • Electrical property of the interface between assembly parts• Elastic property such as interfacial pressure of assembly parts• Potential chemical risk of materials• The dimensions of the joints• Skill dependency / man-days required for jointing• Shelf life of cable joint materials• Special tools required for jointingApart from the above consideration, the review results alsoindicate that the root causes of failures are in common, either due to the material defect caused by installation environment controlor workmanship of jointers. The most contributing factors are:• Foreign particles or tapes appearing between stress cone and epoxy unit• Contamination or scratch on the surface of the insulation• Misalignment or improper workmanship of molding tape• Incorrect pressure of stress cone applied by the spring device (for pre-fabricated joints)• Incorrect position of stress cone installedWith the stringent assessment of the cable joint design, we seldom encounter failure of cable and joints due to design problem. To ensure well-controlled working environment, a checklist was devised for the jointers to check the materials are kept in good conditions such as temperature, humidity and cleanliness levels. In addition, we have prepared a counter checking measures for jointing works (Figure 7) to verify that those critical steps for assemblingcable joints are worked correctly, thereby warranting good workmanship.The slim cable system has been implemented in CLPP for about 4 years, and its performance is found satisfactory.
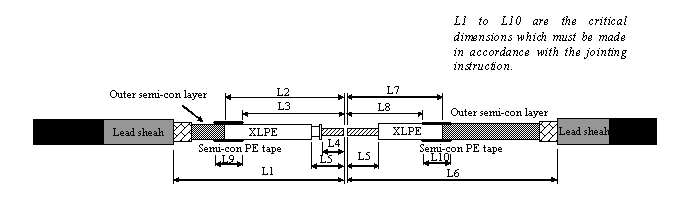 | Figure 7. Counter checking measures for jointing works |
9. Conclusions
To acquire stable and reliable supply of HV cable materials at reasonable cost, CLPP's approach in cable design, supplier sourcing and installation management are very comprehensive and stringent. However, this does not necessarily imply higher cost incurred but savings. This paper cited only typical example for illustration, yet it is not exhaustive. The approach is developed based on a number of variables according to their importance to business needs. As a key to success, it is essential to keep abreast of the supply market and technological development, and maintain close communication with suppliers and other utilities in respond to the ever-changing market. Also, the procurement professionals and engineering teams should work closely for concurrent design, supplier sourcing and project implementation so as to allow improved quality and reliability in all stages, at lower TLCC.
ACKNOWLEDGMENTS
The authors wish to thank the Management of CLPP for their support and permission to publish this paper.
References
[1] | G. F. Moore, “BICC electric cable handbook, Edition 3”, The Blackwell Science, UK, 1997. |
[2] | H. Orton and R. Hartlein, “Long-life XLPE-insulated power cables”, Canada & USA, 2007. |
[3] | K. C. Wong et al, "Quality plan for transmission plant and equipment", CLP Power Hong Kong Limited, Hong Kong, China, 2006. |
[4] | K. C. Wong et al, "Strategic sourcing protocol for major assets", CLP Power Hong Kong Limited, Hong Kong, China, 2011. |
[5] | Power cables with extruded insulation and their accessories for rated voltages above 30kV (Um – 36kV) up to 150kV (Um = 170kV), IEC 60840, 2004. |
[6] | Specification for extruded insulation power cables and their accessories rated above 46kV through 345kVac, AEIC CS9, 2006. |
[7] | Tests on oil-filled and gas-pressure cables and their accessories - Part 1: Oil-filled, paper or polypropylene paper laminate insulated, metal-sheathed cables and accessories for alternating voltages up to and including 500 kV, IEC 60141, 1999. |
[8] | D. H. Cho et al, “Development of high-stress XLPE cable system”, in cigre Conf, 2004. |
[9] | A. Toya et al, “Higher-stress designed XLPE insulated cable in Japan”, in cigre Conf, 2004. |
[10] | S. Toshio et al, “New 400kV underground XLPE insulated cable system in UAE”, in Jicable Conf, 2011. |
[11] | Smit et al, “Experience with developing and installing of a three core 150kV power cable”, in Jicable Conf, 2011. |
[12] | C. Riley et al, “HV cable qualification for IEC 62067-2006 and ICEA S-108-720-2004”, in Jicable Conf, 2011. |
[13] | C. Georg and W. Fischer, “Long time operational experience with 400kV XLPE power cable systems in Berlin”, in Jicable Conf, 2011. |
[14] | P. Hondaa and E. Dorison, “Working out extension of qualification procedures for HV and VHV cable systems”, in Jicable Conf, 2011. |
[15] | A. Weinlein et al, “On-site testing with compact AC test-system at the first 500kV XLPE cable project in South America”, in Jicable Conf, 2011. |
[16] | H. M. Man et al, “CLP transmission cable health check with HVAC frequency-tuned resonant system”, in ICEE, 2007. |
[17] | K. Y. Fung et al, “Condition Monitoring on HV equipment in CLP Power”, in CMD, 2008. |