Daniel Necula , Nicolae Vasile , Mihail-Florin Stan
Automatics, Informatics and Electrical Engineering Department, Valahia University of Targoviste, Electrical Engineering Faculty 18-24 Unirii Blvd., 130082 Targoviste, Romania
Correspondence to: Daniel Necula , Automatics, Informatics and Electrical Engineering Department, Valahia University of Targoviste, Electrical Engineering Faculty 18-24 Unirii Blvd., 130082 Targoviste, Romania.
Email: |  |
Copyright © 2012 Scientific & Academic Publishing. All Rights Reserved.
Abstract
This article presents some defects in the electrical machines and a few methods for appropriate diagnosis. It is part of a broader study that aims to identify electrical or mechanical defects that can occur in electrical machines in operation, a description of their manifestation, prevention and ultimately solutions to remedy them. Intention is that this work becomes a guide to maintenance and repair of the electrical machines that can be used by specialized personnel.It is known that the correct selection of the appropriate machine for each application, the usage of the correct loading and ventilation, the selection of suitable protective elements and the preventive maintenance is the guarantee of extended service life of these machines. It is well known too that a number of concealed defects (both material and regarding the installation) can produce more or less damage, that’s why careful monitoring of electrical machines (especially those of high power) is very important. At least as important are the methods of diagnosis of mechanical or electrical defects, some of which can provide the specialized maintenance personnel with data about the machine itself, before the appearance of defects and without dismantling the machine.The methods used are specific to preventive maintenance such as measurements, verifications, and tests.We conclude that the defects in the electrical machines are multiple, can have internal or external causes, affect nearly all the constructive elements, have specific ways of manifestation, and that their appearance is often preceded by some signs that can warn the operating and maintenance personnel.Compliance with the correct operation scheme of the electrical machines, knowledge of the manifestation of defects, professionalism of the staff, combined with the use of appropriate protective elements may lead to increasing their life span and reduction of the consumption of material and financial resources.
Keywords:
Defect, Reversible, Diagnosis, Eccentric, Concentric
Cite this paper:
Daniel Necula , Nicolae Vasile , Mihail-Florin Stan , "Electrical Machinery Defectsand Diagnosis Methods", Electrical and Electronic Engineering, Vol. 2 No. 5, 2012, pp. 292-296. doi: 10.5923/j.eee.20120205.08.
1. Introduction
1 – stator housing; 2 – stator magnetic core; 3 – stator windings; 4 – fastening pads; 5 – rotor shaft; 6 –magnetic rotor core; 7 –ball bearing; 8 –bearing shield; 9 –terminal block; 10 –terminal box; 11 –fan; 12 –fan cover.- the stator is composed of a cylindrical iron core, which is disposed inside the stator windings; in turn, the stator core is inserted in the stator housing; in general, it plays the inductor role in the electric motors and in the generators it is induced;- the rotor consists of a ferromagnetic core with the rotor winding at the outer periphery; inside the rotor core, coaxial and integral with it, it is the rotor shaft, supported at the two ends by the bearings located in the two shields;- the bearing shields are designed to close the machine mechanically, help to centre the rotor inside the stator and maintain an uniform air gap between the stator and the rotor;- the bearings can be sliding or rolling (bearings); they are designed to allow the rotation of the rotor around its axis inside the stator and can be lubricated with grease or oil.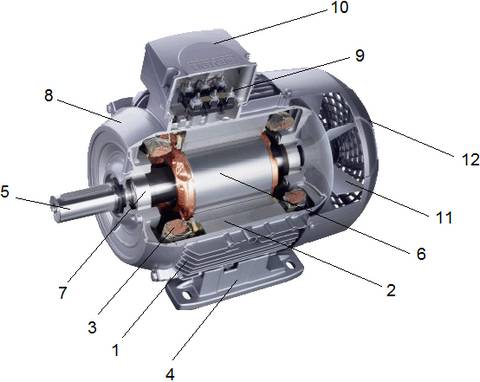 | Figure 1. |
During the operation, all these building blocks can be the host for a defect, which, depending on its severity, can endanger the electrical machine.The causes of failure of the electrical machines can be internal or external. Internal defects can be mechanical or electrical. Regarding the category of mechanical defects, we can note:- the eccentricity of the rotor to the stator, which may have originated either in faulty workmanship or loosening bolts fixing the bearing shields in the stator housing or advanced wear of the bearing shields;- rotor shaft bending, possibly due to its excessive heating caused by friction in the bearings or friction between rotor and stator;- premature wear of the bearings or their permanent damage due to the loss of lubricant with different causes (non maintenance program, breakdown of the oil lubricating circuit, etc.);- displacement of the coils due to the electrodynamic efforts they are under and an insufficient fixing; weakening notch fixation in these coils causes vibrations and due to the friction occurring between the coil and the core short circuit faults can occur.All the defects listed above are accompanied by vibrations of the machine and noise.From the category of internal electrical faults the following can be mentioned:- disruptions of the rotor cage bars or coils;- short circuits between coil turns or between different coils or earthing caused by the destruction of insulation; it should be mentioned here that compliance with the machine load and operating temperature limit is very important for the lifetime of the machine;- stator and rotor windings interruptions, separation of the contact blades of the rotor winding machine collectors;- displacement of the rotor winding heads from the wiper blades of the collector.A frequently encountered phenomenon during the operation of the electrical machines is the decrease of the insulation resistance due to its moistening.The moistening of the insulation occurs especially during the cold season and occurs when the machine is shut down, when the machine is hot; the cold outside air generates the possibility of condensation.The phenomenon may have a higher magnitude as stops and starts are more frequent. Moistening of the insulation can also occur due to accidental ingress of water or other fluids into the machine, during the operation or during repairs. The insulation of the electrical machines is represented by the set of materials with electrical insulating properties, which separates electrically the conductive parts under voltages with different phases or polarities, or the conductive parts from the metal housing of the machine (ferromagnetic stator core or rotor, and housing).The insulation is of particular importance because the good functioning and life of the machine largely depends by its qualities. Of operating experience it may be established that about 40% of failures are due to problems of electrical machinery insulation.Due to this reason special attention is given to testing and checking the insulation, both during manufacture and throughout the lifetime of the machine. Tests taking place in the factory have a dual purpose, namely to validate the solution used (type test) and to certify the quality of execution (individual tests).During the operation of the electrical machines, the tests and checks have a prophylactic role (preventive maintenance), and a certification of quality for the maintenance works. During the operation, the insulation is subject of electrical, thermal and mechanical stress, which leads to aging.The higher the demands the aging occurs more rapidly and the lifetime of the machine decreases. Associated or not associated with aging, the frequency of electrical defects gets higher with the decrease of the insulation resistance, leading to the disposal of the machine. Insulation problems are specific to both the stator windings and the rotor.External causes of failure of the electrical machines can be in turn mechanical, electrical or related to the environment they are used in.a- Mechanical causes: overload, uneven load over time, shock from the driven element, and wrong installation of the electrical machine on the base or on the working machine;b- Causes of electrical nature: fluctuations in supply voltage within large limits, unbalanced voltages on the three phases of the power network, inadequate protection or its downtime.Causes due to the environment in which the machine works: temperature, humidity, particulate matter, etc.
2. The Electrical Faults of the Stator
As mentioned previously, the most common electrical defects of the stator of the electrical machine are the interruption of the coils (open coils) or short circuits between turns of the same phase or different phases. Interruption of a winding during machine operation produces a low torque and speed and increasing current in the other two phases. If the motor is equipped with protection against operation in two phases, it will stop functioning and will limit the fault. In this case, there is a chance for the coil to be repaired and once the insulation is rebuilt to recover the electrical motor. In the event of short circuits between turns, the effects are more severe, the defect leading to the disposal of the machine to replace the coil.
3. Methods of Diagnosis for the Electrical Faults of the Stator
To diagnose the electrical faults of the stator, several methods are known whose principles are based on the very specific effects of these defects: asymmetries, low torque, increasing phase currents on the working windings. Regarding the importance of electrical machines failures, experts’ opinions are divided. Some authors (A. Bellini, F. Filippetti, C. Tassoni, G. Capolino) believe that the electrical faults due to the condition of the winding and insulation are essential, while others (S. Nandi, Toliyat H., Li X.) consider that mechanical breakdowns, especially those of the bearings, are more important. From our point of view, all types of defects are important. Although some are insignificant at first, they can lead to major defects that can destroy the machine.There are various methods of diagnosis of the stator faults. One of them, developed by Filippetti, proposed transverse admittance as an indicator of failure, this resulting from the ratio of negative sequence component of stator current and the supply voltage positive component. The method is based on the hypothesis that the electrical machine with nNshort-circuit turns, therefore unbalanced, can be assimilated to a symmetrical machine to which nN turns are added, which corresponds to the shorted turns (Figure 2).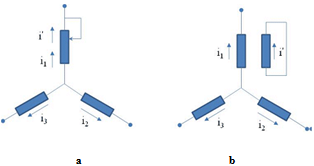 | Figure 2. a) the stator windings connected in star schema with one phase short circuit between turns; b) the equivalent circuit |
4. Mechanical Failure – Rotor
EccentricityMechanical defects can occur either due to wear over time of the various elements of the electric motor or as a result of mechanical shock transmitted at some point from the driven element. These defects are often generated by issues such as: inappropriate building solutions, improper choice of materials, form or wrong assembly of couplings, improper balance etc. In general, however, the mechanical stress the composing elements and the electrical machine as whole are subjected to does not reach the state of elastic deformation. The mechanical shocks due to uneven load, taken on the rotor shaft, are transmitted to all the building blocks of the machine, in the form of vibrations, over time leading to premature wear and at the moment to the heating of the machine. Besides the vibrations generated by taking over the shocks from driven element, there are times when the machine has its own vibration due to internal causes, such as: unbalanced rotating part (rotor), weakening of the magnetic core wedges rotor shaft rotor, pressing failure or weakness in the functioning of the stator and rotor magnetic core, advanced tread wear of the bearings.The imbalance of the rotating parts is one of the most common causes of vibration with all the adverse effects on the durability of the machine. In practice there are two types of imbalance, namely:- imbalance in a single plane (static);- imbalance in two or more planes (dynamic).One of the situations in which the imbalance of the rotor may occur (in rotor winding electrical machines) is for the rewinding. Non-uniform distribution of winding wire channels contribute to imbalance rotor magnetic core. Other sources of imbalance are uneven distribution of insulating feathers and lake, of the material used for sealing the ends of coils to the commutator segments, etc. Therefore, after rewinding the rotor, special attention is given to the balancing. Balance must be dynamic (in at least two planes), for example by x and y planes. Even after the execution of the rotor balancing operation, a certain residual imbalance remains. It is acceptable, based on experience, that the allowable imbalance is proportional to the rotor mass, thus defining the specific imbalance "e" as the ratio between the residual unbalance (kg/mm) and the rotor weight (kg). The specific imbalance "e" may be regarded as the eccentricity of the center of the mass for a static imbalance (mm). Quality grades of the balancing "G" are provided in international standards, for each grade being provided a range of permissible residual unbalance. A satisfactory quality of balancing of can be done only under a sufficiently high precision mounting of the rotor in its camps.
5. Vibration and Noise in Bearings
The bearing vibration and noise problem has worsened with the expansion of the use of small dimensions bearings (micro bearings) in the manufacture of micro motors for, and not limited to, office electronics (eg. computers), where noise of bearings may be dominant and disturbing. Movements of the bearings components (rings, cage, rolling bodies) in actual execution and operation generates vibration and noise very important for the situations outlined above.It's possible that the vibration to be weak, but propagated to other elements (in the case of electrical machines to port shields bearing and stator housing) as indirect excitation to cause important vibrations.Practice and experimental research shows that vibration and noise of bearings originate from these phenomena:-movement of rolling bodies (balls) on taxiways (the outer and inner) over localized defects (voids, cracks, peeling tool, foreign bodies from the grease used or accidentally permeated into the work environment);-movement of the rolling bodies over the rolling ways on contact surfaces that have deviations from ideal geometric shape (dimensional deviations, geometric deviations, roughness) or improper tightening;- changes in the position of the rolling bodies depending on the areas more or less affected of the rolling surface.It was also found that there is a strict dependence between the size or shape deviations game and the noise and vibration. Also should be noted that bearing construction and type of contact (surface or punctual) influence the noise and vibration (eg. the same size, roller bearings are 5-14 dB louder than the ball bearings).Radial load has a smaller influence than the axial load on the level of noise and vibration while the rotation speed especially influences this level.One of the effects of a high level of vibration of bearings may be widening holes of port shields bearings where they lean, and can lead to eccentricity of the rotor to the stator.Therefore, one of the common faults of rotating electrical machines is the occurrence of the rotor to the stator eccentricity. This defect may have its origin in an assembly error, or may be caused by loosening bolts fastening the shield bearings during operation, or deformation of the bore that are holding the bearings, which leads to changes in air gap uniformity. In all these cases, the specific element is the appearance of imbalances that disrupt the movement of rotor torque, generating noise and vibration. In severe cases, friction may occur between the rotor and the stator with dramatic consequences on the state of the machine. For these reasons, diagnosis and early detection of defects without dismantling the machine is very important.
6. Diagnosis of Rotor Eccentricity
Rotor eccentricity has a static and a dynamic component, in practice both manifesting simultaneously. Diagnosis of rotor eccentricity can be done by monitoring the magnetic flux crossing the air gap.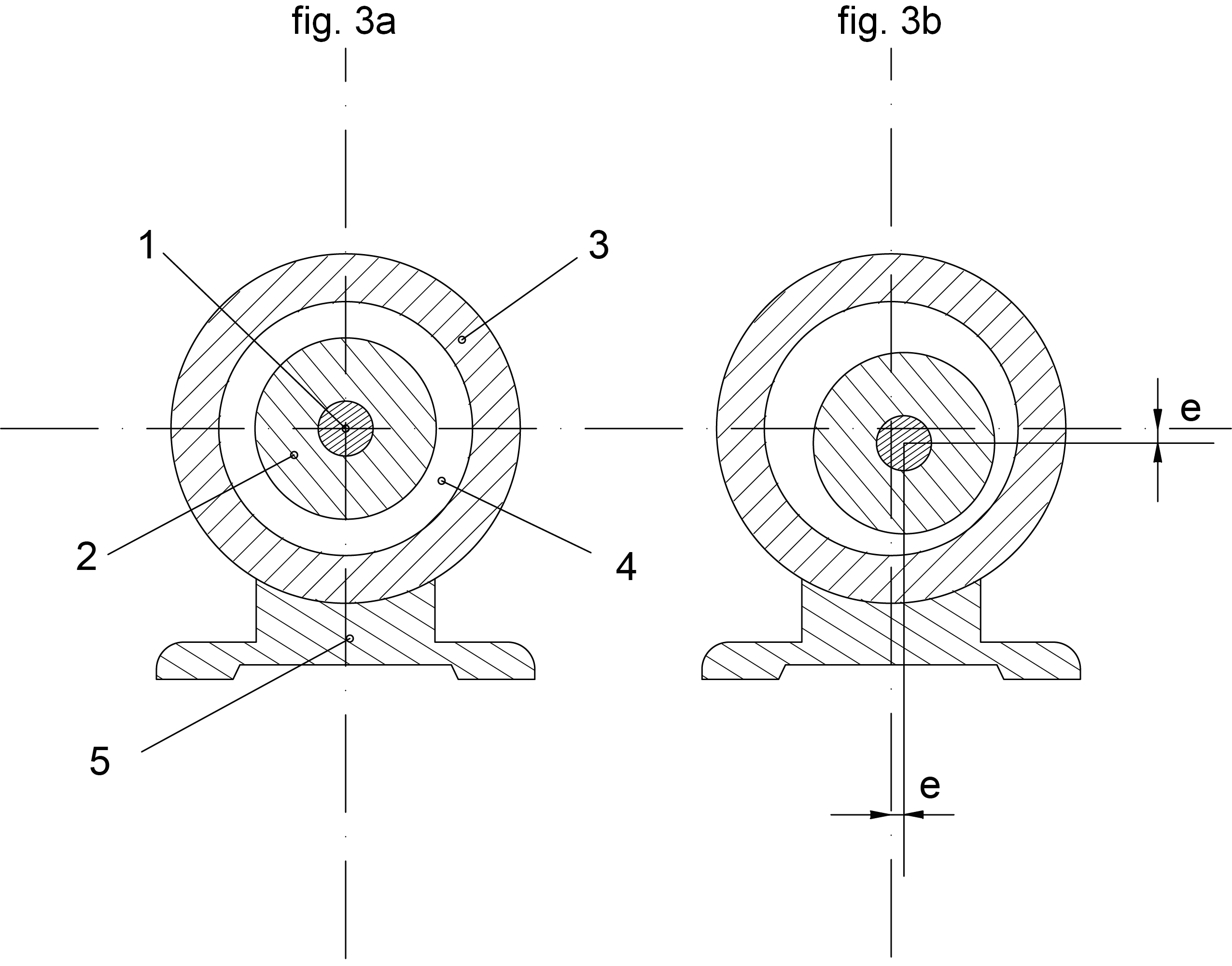 | Figure 3. a) centered rotor b) eccentric rotor 1-Rotor shafte-Rotor eccentricity 2-Rotor magnetic core 3-Stator 4-Air gap |
Spectral components sides have a frequency corresponding to the eccentricity, equalling:
where: f1 is the frequency of the power network andfris the frequency of the rotation of the rotor.Static or dynamic rotor eccentricity can be identified using the method of stator current profile analysis (MCSA).Appropriate side of eccentricity fault frequencies is:
where: k is a constant positive integer, Nr is the number of rotor bars, p is the number of pole pairs, ndis the order of eccentricity (nd= 0, for static eccentricity and nd= 1, for dynamic eccentricity), s is the motor slipping, m is the order of harmonic present in the power source of the motor (m = 1, 3, 5, ...) and f1 is the frequency of the source.In the paper Condition Monitoring and Fault Diagnosis of Electrical Motors, the authors show that the method used to detect rotor eccentricity provides satisfactory results only for a certain combination of numbers of pairs of poles and rotor slots.
7. Trends for the Future of Electrical Machines
In terms of the future of the electrical machines, concerns are directed towards increasing dynamic performance (torque response), using new encapsulation technologies, development of new types of insulating materials that allow temperatures up to 200 degrees Celsius, using amorphous metallic powders in place of siliceous sheets for the magnetic cores, making of the electric motors without notches, high frequency operation that reduces gauge. Increasing the lifetime of the machine, increasing energy efficiency to reduce energy consumption to minimize environmental impact are also pressing concerns of the specialists in the field.
8. Conclusions
The electrical machines are complex systems in which a series of phenomena as heating and vibration take place, both of mechanical and electromagnetic nature.Defects in the electrical machines can be mechanical or electrical, caused by internal or external factors, or by the environmental conditions in which they are functioning. It can be said here that between the electrical machine and the environment there is an interaction, in that on one hand the environment (moisture, dust, temperature) affects the functioning the machine and on the other hand, the heat dissipated during machine operation affects the environment.Integrated building of the electrical machines allows the embedding of different types of sensors (temperature, vibration) into their components, making possible the detection of incipient faults and allowing preventive maintenance measures.The recent years imposed edge technology in the construction of electric machines, new materials are used which allow obtaining high power densities / kg, decreasing gauge and increased reliability.
References
[1] | M. D. Călin, E. Helerea, I. D. Oltean, New Consideration Regarding Frequency Influence on Soft Magnetic Materials Characteristics. The Third International Symposium on Electrical and Electronics Engineering – ISEEE-2010, Galaţi, Romania, 2010. |
[2] | Daniel Necula, NicolaeVasile, Mihail Florin Stan, New Solutions in the Maintenance of the Asynchronous Motors with Integrated Gear and Single Demountable Bearing Shield. Devices to Extract and Insert the Ferromagnetic Cores of the Stator (Case Study), PROCEEDINGS OF THE 7th INTERNATIONAL SYMPOSIUM ADVANCED TOPICS IN ELECTRICAL ENGINEERING (ATEE 2011), University POLITEHNICA of Bucharest, Faculty of Electrical Engineering, May 12-14, 2011, Bucharest, Romania, pp.481-484, ISSN: 2068-7966. |
[3] | Bellini Alberto, FilippettiFiorenzo, Tassoni Carla, Capolino Gérard-André, Advances in Diagnostic Techniques for Induction Machines. IEEE Transactions on IndustrialElectronics, Vol. 55, No. 12, December 2008, 4109- 4126. |
[4] | N. Vasile, N. Voncila, M. Rădulescu, A. Simion, M. Chefneux, L. Livadaru, Integrated Design Solutions for Electrical Machines for Rational Use of Natural and Artificial Resources, CIT-TE ICPE Publishing House, Bucharest, 2008. |
[5] | NicolaeVasile, S. Şlaiher, Electrical Servomotors, Electra Publishing House, Bucharest, 2002. |
[6] | Mihail Florin Stan, Horia Andrei, Modern Electrical Engineering. Electotechnic and Electromechanical Converters. Theory and Applications, vol. 2, Bibliotheca Publishing House, Târgovişte, România, 2010. |
[7] | M. Filip, E. Helerea, I. C. Roşca, Considerations about the Electrical Engine Vibrodiagnosis, AFASES, Brasov, 20-22 May 2009. |
[8] | M. Filip, I. C. Roşca, E. Helerea, Low Power Induction Motors Vibration Tests. Proceedings of the X-th International Symposium AVMS’2009, pp. 142-147, ISSN 1843-0902, Timişoara, May 28, 2009. |
[9] | M. Filip, E. Helerea, On the Induction Motor Vibration Testing. Proceedings of the 5-th International Conference on Interdisciplinarity in Education. ICIE’10, May 6-8 2010, Tallinn, Estonia, ISSN 1790-661X. |
[10] | S. Nandi, H. Toliyat, X. Li, Condition Monitoring and Fault Diagnosis of Electrical Motors: A Review. IEEE Transactions on Energy Conversion, Vol. 20, No. 4, December 2005, pp. 719-728. |
[11] | Mihail Florin Stan, Marcel Ionel, M. O. Ionel, Daniel Necula, AC Machines with Two Radial Air-gaps. A Variant of Asynchronous Machine with Sectioned Arbor and Two Bearings, Scientific Bulletin of the Electrical Engineering Faculty, no. 1(15) / 2011, Bibliotheca Publishing House, Târgovişte, pp. 37-42, ISSN 1843-6188. |
[12] | Marcel Ionel, Mihail Florin Stan, M. O. Ionel, Daniel Necula, Development of Generalized Mathematical Models for Variable Speed Electric Machines, Scientific Bulletin of the Electrical Engineering Faculty, no. 1(15) / 2011, Bibliotheca Publishing House, Târgovişte, pp. 19-24, ISSN 1843-6188. |