Daniel Necula , Nicolae Vasile, Mihail-Florin St
Automatics, Informatics and Electrical Engineering Department, Valahia University of Targoviste, Electrical Engineering Faculty
Correspondence to: Daniel Necula , Automatics, Informatics and Electrical Engineering Department, Valahia University of Targoviste, Electrical Engineering Faculty.
Email: |  |
Copyright © 2012 Scientific & Academic Publishing. All Rights Reserved.
Abstract
This article is part of a larger work titled „The electrical machines impact on the environment and solutions to reduce it” and it is in fact a case study. Far from being an exhaustive paper, it aims to identify some factors of the impact of electrical machines on the environment throughout the period of their existence, and on the other hand, to propose solutions to reduce such impact, in the context of the sustainable development concept. Generally, asynchronous motors (both three-phase and single-phase) have two demountable bearing shields. There is also a specially designed motor that has a single removable bearing shield, the other being made integral with the stator housing. Such a construction has a few advantages: it allows for better sealing, increasing resistance to heavy operating conditions such as humidity, dust, explosive gas, vibration etc. As a disadvantage, in case of coil defection at this motor type, as the coil is not available at both ends of the stator as in normal motors, extraction of the defective coils in order to replace them impose major constructive difficulties. Therefore, the problem is to find a method to extract the ferromagnetic stator core with its windings and insert it back in its place after rewinding and coating. This paper presents two novel constructive solutions: the first solution represents a device for the extraction of the ferromagnetic core from the housing with the purpose of rewinding, and the second is a device for pressing the ferromagnetic core back in its housing once it’s repaired. The two devices have been designed in order to allow the repair of small power electrical motors that have a single removable bearing shield (the other one being made integral with the stator housing). Both are manually operated and are a specific element of the central screw driven by a handle. The stator ferromagnetic core extraction device is inserted in place of the rotor of the motor to be repaired, stator core sitting on the bottom and extracting it from the housing. The device for pressing the ferromagnetic core in the housing exerts a force on the stator core at the top, while the housing is fixed. Both devices are subject to OSIM patents.
Keywords:
Maintenance, Integrated Devices, Demountable, Motors
Cite this paper:
Daniel Necula , Nicolae Vasile, Mihail-Florin St , "Maintenance - a Solution to Reduce the Environmental Impact of Electrical Machines", Electrical and Electronic Engineering, Vol. 1 No. 2, 2011, pp. 55-59. doi: 10.5923/j.eee.20110102.09.
1. Introduction
The electrical machine is an electromechanical reversible energy converter, which in motor regime converts electrical energy absorbed at terminals into mechanical energy available to the rotor shaft and in generator regime it converts mechanical energy into electrical energy. Rarely, electrical machines can work in the brake regime in which both electricity and mechanical energy is transformed into heat.Whatever the operation regime, the conversion process is always accompanied by irreversible transformation of the energy into heat.Like many other industries, electrical machine building industry is a polluting one. It can be considered without any doubt that environmental pollution begins in the phase of exploitation of minerals from which metals are extracted from which components are manufactured (Al, Cu, Fe, etc.).Pollution continues throughout the life of the machine, through: development of heat, generation of external magnetic fields, noise, vibration, emissions of volatile substances in electrical materials, loss of lubricants in service. When the unity power of electric machines is larger, the values of these parameters are higher.At the disposal of the electrical machines, the environmental impact consists in gas emanations, smoke, dust and other substances resulting from dismantling, in order to return the materials to the economic cycle.As previously shown, electric machines transform a primary energy form into another form of usable energy; this transformation also generates a quantity of energy that’s either unusable directly or very difficult to recover – the heat. Schematically, this transformation at the electrical machine level can be represented as follows:From the standpoint of the environmental protection process, in addition to the useful forms of energy (mechanical or electrical), the electrical machines also produce losses, as heat[4]. The lost energy can be recovered by taking the heat from the cooling circuit either directly or from the space immediately adjacent to the machine and using it in a different process than the electromechanical conversion process by which it was generated. If it’s not used, this heat can be regarded as a waste that adversely affects the environment.In accordance with the above analysis, a direction to reduce environmental effects of electric machines is the minimization of the heat loss residue. It is obvious that environmental effects depend on the type of conversion used, on the construction and machine size. Therefore, a solution to mitigate the impact of the heat over the environment is to recover the heat and reuse it. However, this can be achieved only for large machines (either motors or generators).For the new electrical machines, solutions need to be found from the project phase to: increase the power efficiency (by using new materials), insure easier dismantle, simplify the construction method.For the machines that are already in production, the impact over the environment can be reduced by increasing their life through a rational maintenance plan and by finding overhauling solutions, which is requires less resources and less energy than the dismantling and replacement of the defective parts. Such a solution is described below, for a certain kind of motors, having a single demountable bearing shield. 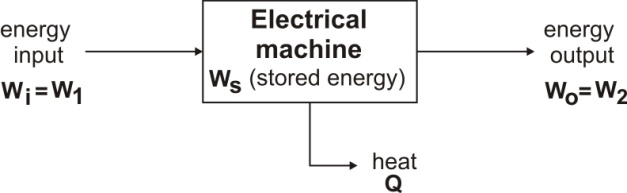 | Figure 1. Energy balance of an electrical machine |
2. The Electrical Motors Generalities
From the literature[5,6] it is known that all rotating electrical machines, except for the motors embedded in the working machines, are composed of three main subassemblies, namely:The stator;The rotor;The bearing shields.In turn, the stator is built of the following elements:Magnetic circuit (stator magnetic core);Windings and / or permanent magnets;Stator housing (with or without mounting feet);Terminal box;Other accessories. The rotor consists of the following elements:Windings and / or permanent magnets;Magnetic circuit (magnetic rotor core);Shaft (rotor shaft);Rings;Other accessories.Bearing shields are required to sustain the stator and the rotor and to seal the machine. In the actuation systems, the front bearing is also used to attach the motor to the working machine. In general, both shields are removable, but the trend of specialization of electric motors for various types of applications to optimize efficiency throughout the whole system (electrical motor – drive – working machine), led to the emergence of the single demountable bearing shield motors, the other shield being made integral with the stator housing.This type of construction brings benefits such as:Better alignment of the rotor shaft with the first stage of mechanical located on removable bearing shield and with electric brakes positioned on the non-demountable shield;Mechanical reduction between the motor and working machines deviations;Better motor sealing making it suitable for operation under heavy environmental conditions (humidity, particulate matter, explosive gas environments etc.);Greater resistance to vibration.Bearings or sliding bearings, cross brush (if applicable), and a range of accessories (protective grills, outdoor fan and fan cover, lubricating devices) are mounted on the shields.Starting from the fact that industrial activity has unfortunately a major negative effect on the environment, the proposed EU policy objectives are the preservation, protection and improvement of the quality of existing natural resources prudently and rationally in accordance with the concept of sustainable development, in order to protect human health and the environment and to improve quality of life.Equipment and electrical machines are included in an area that needs to be approached from these perspectives.Electrical machines incorporate active materials (to achieve the windings and magnetic circuit), insulating materials and various other materials necessary for the mechanical structure (for support and to protect the active parts).To make an assessment of the negative impact of electric machines on the environment, we need to take into account both the quantities of materials actually found embedded in the machine and also the technological losses of such materials during the manufacturing process, most of the losses often found as waste.Here are some calculation formula, allowing the correlation between the nominal data of the machine (power, current, voltage, torque, speed etc.), electric and magnetic machine requests (induction, current density) and size of machine or subassemblies thereof. These formulas allow the assessment of material consumption and thus the environmental impact.Evaluation of the material consumption from the composition of electrical machines is based on so-called main dimensions of the machine.They are:Induced armature diameter, denoted by D;Ideal length of the machine, denoted by li.With these two dimensions we can determine the apparently volume of the induced armature with the formula: | (1) |
Real machine is developed around this volume V, so this knowledge is important for the preliminary assessment of the consumption of materials needed for the machine. To optimize the construction, machine required material consumption should be introduced in the calculation of a parameter of correlation between the diameter D and ideal length of the machine li. This parameter is called geometry factor and is denoted by . | (2) |
where p is the number of pole pairs of the machine and is the polar step of the machine. For any type of electrical machine, size is determined by the electromagnetic power, which is converted into power in the conversion process that occurs through the air-gap of the machine. It is only a part of the power P1 received by the machine.Due to the specific mathematical model of the machine, calculation formulas differ from one machine to another (AC machine, AC machine with collector, DC machine etc.).It is clear that electric cars have a negative impact on the environment from extracting ore from the earth, continuing with the transformation of their materials (copper, aluminum, bronze, steel, iron etc.) needed for the various structural elements. Also, the running of the various components (for example stator and rotor core plates, processing arbors, casting carcasses etc.) results in a range of wastes that are either stored or returned to the circuits that have an impact on the environment. During operation, the electrical machines have a negative impact on the environment: electromagnetic fields, noise, heat and so on are created around them.Even their scrapping causes problems because of their breakup components, because sorting of materials and their reintroduction into the circuit, resulting in polluting operations.It is therefore very important to move to a new type of electric machine design, in addition to efficiency calculations also provide new design solutions (for example machines without notches, which, in case of dismantling, the materials are recovered and easily separated) to reduce environmental impact.Among the ways to reduce the impact on the environment we can include: the proper and efficient operation and maintenance of electrical machines in use.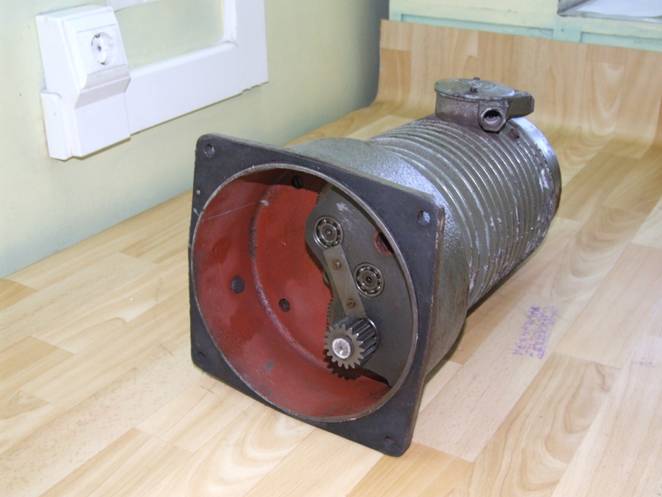 | Figure 2. View of motor with integrated construction from demountable bearing shield |
3. Motors with Integrated Gear and Single Demountable Bearing Shield
This type of motors differs from the general purpose motors in that it has a single demountable bearing shield, the other being cast common body with the aluminum housing [4]. Mounting on the working machine is done through a removable shield that is integrated with the first gear of a speed reducer. At the opposite side, on the non-demountable shield, it is mounted the electrical brake[1].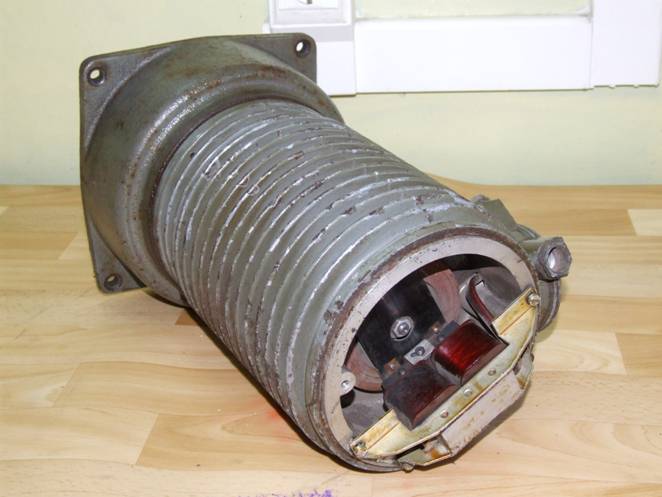 | Figure 3. View of motor with integrated construction from non- demountable bearing shield |
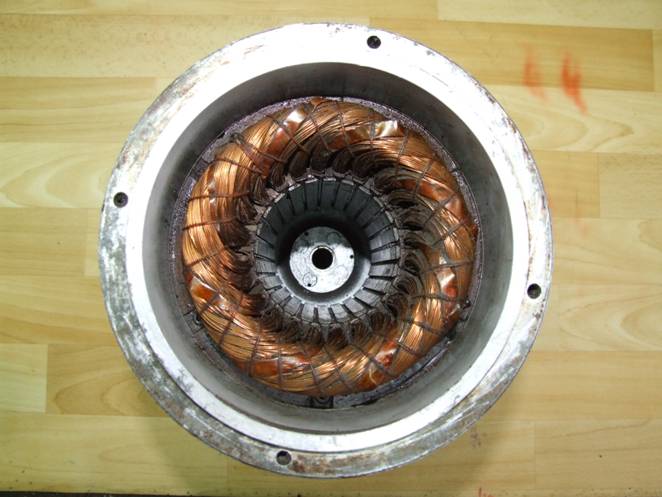 | Figure 4. Interior view of the stator of the electric motor |
As noted above, although it has certain advantages, in case of winding failure, such a design creates special technical problems. These include:The stator can’t be rewound because it doesn’t provide access at both ends for removing the defective coils and introducing new ones;Rewinding may be possible by extracting the magnetic core from the housing, but this requires specialized devices that allow both to extract the core and to insert it back;To design the actual removal device, we must keep in mind that the design of the motor provides access only through the inside of the stator, the place normally occupied by the rotor.These types of motors are often used in systems operating in the energy sector. They can be manufactured by a German manufacturer (AUMA), Italian (BIFFI), Czech (MODAKT) etc.Because their maintenance cost is lower compared to buying new ones, we’ve been interested in repairing of such motors and in this respect we have developed two innovative devices to make the repair possible.
4. Case Study: Devices to Extract and Insert the Ferromagnetic Cores of Stator
To remove the stator magnetic core we developed a manually operated device, consisting of a fixed part and a movable part, that is inserted into the rotor area[1].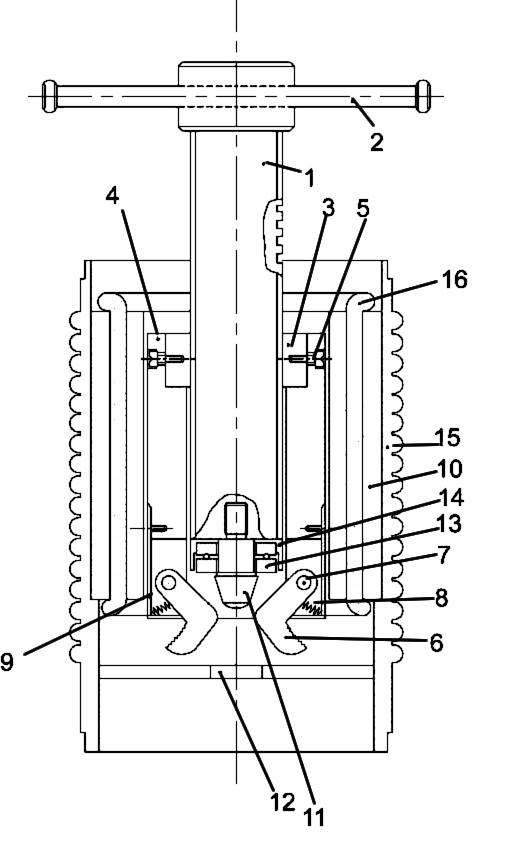 | Figure 5. Manual device from extracting stator core |
The central screw (1) is rotated using the handle (2), screwing into the bronze threaded bushing (3) jointly set on the cylindrical body (4), secured with bolts (5); due to the pressure it advances toward the bottom part, moving the fixing claws (6) which rotate around the pins (7) to reach the working position (with the active part under the stator core), compressing the springs (8) supported at the opposite end on the caps (9).Further, the conical part (11) self-centers the device into the bearing housing (12) of the non-removable shield. When the pressure bearing (13) protected by the cover (14) rests on the non-removable shield, the extraction of stator core (10) from the housing (15) begins.After the complete extraction of the core, the faulty winding core (16) is removed and the stator is rewound by classical methods and devices.After rewinding, varnishing and cleaning, the core can be inserted back into the stator housing with another device, as described below.The pressing device is comprised of a fixed part (a top and bottom flange bonded through three circular studs placed 120° apart) and a mobile part (central screw driven by a handle, a movable flange and a compression ring)[5].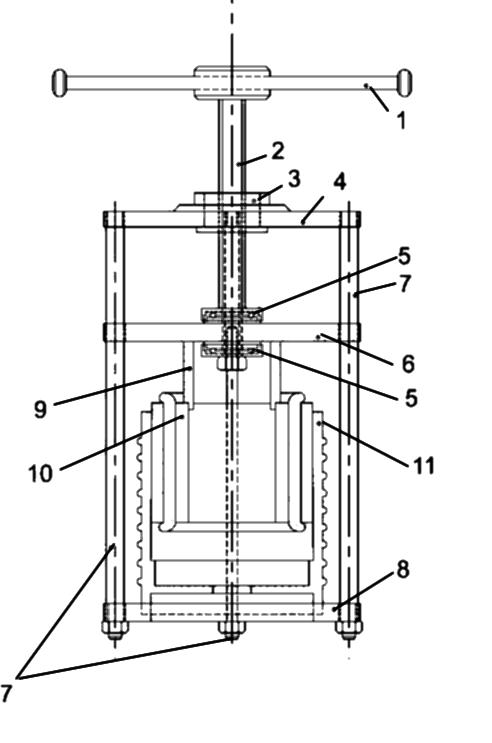 | Figure 6. Manual device from pressing stator core |
This is the process for pressing the core back into the housing:The stator housing is inserted into the device, between the inferior fixed flange and the mobile flange;The core is centered into the housing;The compression ring is placed above the core;Using the handle (1), the screw (2) is tightened into the bronze bushing (3), jointly set on the fixed upper flange (4). Through the pressure bearings (5) the screw presses on the mobile flange (6), which moves towards the bottom guided on bolts (7). Being pressed between the fixed bottom flange (8) and the ring (9), the stator magnetic core (10) is inserted into the housing (11).
5. Conclusions
By the time the devices described above were realized, the motors with one demountable bearing shield could not be rewound. Winding failure inevitably means scrapping, cassation and dismantling with the whole chain of financial costs (replacement with a new one, charges for dismantling of faulty motor etc.) as well as negative environmental impacts.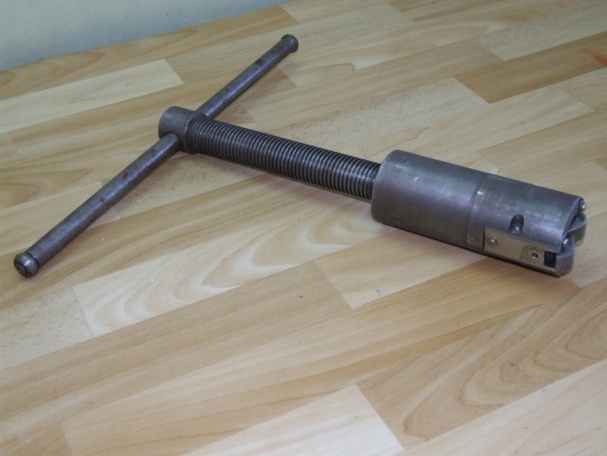 | Figure 7. he extraction device, before the insertion into the stator |
This situation lasted a very long time, because at that time there was no way to repair these motors or any references in any national or international literature. As such, constructive proposals submitted to the OSIM have resulted in two patents[2,3].The manufacture of the two devices in the mechanical workshop and their usage in the electric winding workshop at SC Termoelectrica SA – SE Doiceşti, Romania, created the possibility of the rewinding of the imported single demountable bearing shield motors and led to significant cost reduction.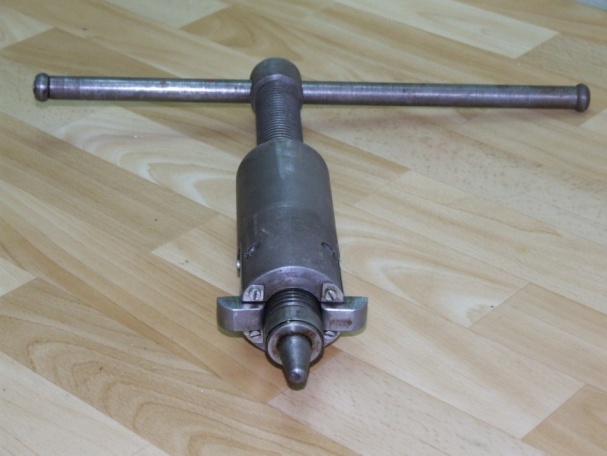 | Figure 8. Position of the device as inserted into the stator (claws expanded) |
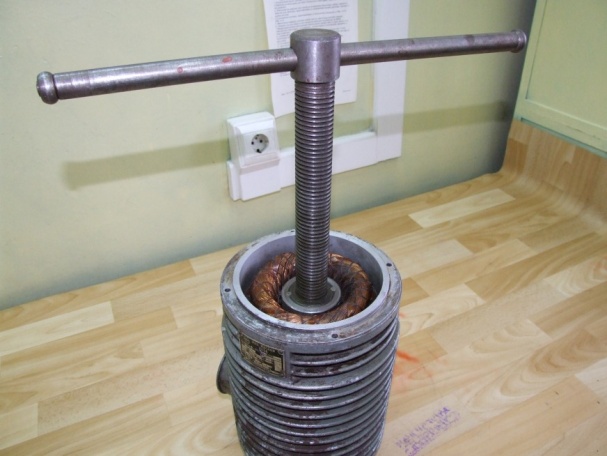 | Figure 9. The extraction device in working position |
The development of the two devices has meant an important step in reducing costs, because by using them, the most sensitive part of the motors, the winding, can be replaced whenever necessary, thus extending service life. It should be noted that such an intervention implies a smaller cost than replacing the motor, while the effect remains the same.Therefore, the authors consider that the maintenance of electric machines is both a way to reduce financial costs and also a way to reduce the impact that the very existence of such machines has on the environment.Given that many industrial units both in Romania and other countries (like Czech Republic, Poland, Germany etc.) use this type of motor, the authors consider that the proposed design solution can be generalized to all industries that use geared motors powered by a single demountable bearing shield motor.
References
[1] | Necula, D., Vasile, N., Stan, M.F., New Solutions in the Maintenance of the Asynchronous Motors with Integrated Gear and Single Demountable Bearing Shield. Devices to Extract and Insert the Ferromagnetic Cores of the Stator (Case Study), Proceedings of the 7th international symposium Advanced Topics in Electrical Engineering (ATEE 2011), University POLITEHNICA of Bucharest, Faculty of Electrical Engineering, May 12-14, 2011, Bucharest, Romania, ISSN: 2068-7966 |
[2] | Necula, Daniel, OSIM patents No. 101 181, Romania |
[3] | Necula, Daniel, OSIM patents No. 101 190, Romania |
[4] | Vasile, N., Voncila, N., Rădulescu, M., Simion, A., Chefneux, M., Livadaru, L., Integrated Design Solutions for Electrical Machines for Rational use of Natural and Artificial Resources, CIT-TE ICPE Publishing House, Bucharest, 2008 |
[5] | Vasile, N., Șlaiher, S., Electrical Servomotors, Electra Publishing House, Bucharest, 2002 |
[6] | Stan, M.F., Andrei, H., Modern Electrical Engineering. Elecrtotechnics and Electromechanical Converters. Theory and Applications, vol. 2, Bibliotheca Publishing House, Targoviste, Romania 2010 |
[7] | Strete, Larisa Elena, Viorel, Ioan Adrian, Studies on the Linear and Rotating Variable Reluctance and Transverse Flux Electrical Machines, Tehnical University of Cluj Napoca Publishing House, Cluj Napoca, Romania 2009 |
[8] | Fuchs, Ewald F., Masoum, Mohamad A.S., Power Quality in Power Systems and Electrical Machines, Elsevier Academic Press, Amsterdam., 2008 |
[9] | Ionel, M., Stan, M.F., Ivanovici, T.D., Enescu, D., Vîrjoghe, E.O., Ionel, O.M., Strategies for Increasing Energy Efficiency in Electrical Drives, 9th WSEAS International Conference on Computational Intelligence, Man-Machine Systems and Cybernetics (CIMMACS '10), University of Los Andes, Merida Venezuela, December 14-16, 2010, pp.54-59, ISSN: 1792-6998, ISBN: 978-960-474-257-8 |
[10] | Ionel, M., Stan, M.F., Vîrjoghe, E.O., Ionel, M.O., Alghorithm for Exact Determination of Three-phase Induction Machine Parameters, 14th WSEAS International Conference on Systems (Part of the 14th WSEAS CSCC Multiconference - Latest Trend on Systems volume II), Corfu Island, Greece, July 22-24, 2010, pp. 636-643, ISSN: 1792-4235, ISBN: 978-960-474-214-1 |