Seyed Zeinolabedin Moussavi 1, Maryam Alasvandi 2, Shahram Javadi 2, Ehsan Morad 3
1Electrical & Computer Engineering Faculty, Shahid Rajaee Teacher Training University, Lavizan, Tehran, Iran
2Department of Electrical Engineering, Islamic Azad University, Central Tehran Branch, Poonak, Tehran, Iran
3Department of Electrical Engineering, Islamic Azad University, SHADEGAN Branch, PO box 6431863758, SHADEGAN, Iran
Correspondence to: Maryam Alasvandi , Department of Electrical Engineering, Islamic Azad University, Central Tehran Branch, Poonak, Tehran, Iran.
Email: |  |
Copyright © 2014 Scientific & Academic Publishing. All Rights Reserved.
Abstract
There are pivotal reasons for PMDC application in industry. Various control structures can be implemented to achieve speed optimization. The paper take into account control structure based on combination of MRAC (Model Reference Adaptive Control) and ANFIS (Adaptive Neuro-Fuzzy Inference System) for PMDC (Permanent Magnet Direct Current) motor to use advantages of both structures simultaneously. The error signal reduction in MRAC system is modified by means of ANFIS controller. The reason behind is due to smaller rule base for covering any possible situation occurring in real motor applications. Comparison of the above named combination of structures with the previous ones by means of simulation in MATLAB, Simulink proved notable improvement behavioural characteristics of PMDC motor.
Keywords:
ANFIS, MRAC, PMDC motor, Speed control
Cite this paper: Seyed Zeinolabedin Moussavi , Maryam Alasvandi , Shahram Javadi , Ehsan Morad , PMDC Motor Speed Control Optimization by Implementing ANFIS and MRAC, International Journal of Control Science and Engineering, Vol. 4 No. 1, 2014, pp. 1-8. doi: 10.5923/j.control.20140401.01.
1. Introduction
In recent years, permanent magnet DC motors are used in variety of application including heater, wiper and air conditioner of car and personal computer. These motors need no excitation current; hence no energy consumption due to field fluxes producing. In addition, PMDC motors have no requirement for field winding therefore size of PMDC motors are smaller than conventional DC motors and cost of PMDC motors are relatively lower[1]. However there exist different methods for motor Control, but these methods generally are classified into:1. PID controller [2, 3].2. Modern controller [3].3. Intelligent controller [3, 1].Model Reference Adaptive Control (MRAC) is considered beneath of modern controller; belongs to adaptive control category. In the sense of control theory and engineering, an adaptive controller is an "intelligent" controller that can modify its behaviour in response to the variations in the dynamics of the process and the character of the disturbances. An adaptive system is any physical system that has been designed with an adaptive viewpoint. The Model Reference Adaptive Control System is an adaptive servo system in which the desired performance is expressed in terms of the reference model, which gives the desired response to the reference signal [4].On the other hand Adaptive Neuro-Fuzzy Inference System (ANFIS) related to intelligent control, the strategy which combines advantages of neural network and fuzzy control.In recent years, many researches are done for designing. ANFIS based controller such as design ANFIS for speed control of induction motor, the speed controller uses error and change in error for determining controlling signal and by means of 49 if-than rule improve the dynamic performance and stabilization [5]. In other research, ANFIS based controller for stepping motor drive is designed. In mentioned controller, the best parameters for the fuzzy controller are determined by using the ANFIS methodology. Designer by means of simulation and experimental results shows that ANFIS based controller is better in tracking and adaptability than the PID and Mamdani based fuzzy controllers [6]. In other paper, researchers show that genetic-ANFIS controller has better performance than classic PID controller for induction motor [7].According to the specific application of permanent magnet DC motor and high application of ANFIS based control methods in industry; designing control method based on ANFIS for PMDC motor is remarkable subject.In this paper, we proposed control structure based on MRAC and ANFIS for PMDC motor. The control structure is compared with other methods such as adaptive – fuzzy control. After carefully simulation and making comparison; we could conclude advantages of the structure and more reasonable behaviour. The paper is organized as follow: Section 2 discusses model of permanent magnet DC motor. The adaptive controller is explained in section 3. Section 4 presents ANFIS control. The proposed strategy is explained in section 5. The simulation results and investigation are given finally in section 6.
2. Model of PMDC Motor
The case study of this paper is PMDC motor. We need dynamic model of PMDC motor for simulation therefore we use electrical circuit and mechanical equations of motion. These equations describe behaviour of PMDC motor [8]: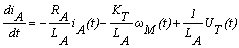 | (1) |
 | (2) |
 | (3) |
Where θM is angular position, ωM is rotor speed, iA is motor current, BM is viscous friction constant, JM is inertia of rotor, TL is load torque, RA is armature resistance, LA is armature inductance, KT is back electromotive force (emf) constant or torque constant and UT is applied voltage to motor. In PMDC motor, the electromagnetic torque (TE) and the backemf (ub) are proportional to motor current and speed motor, respectively. The back electromotive force (KT) determined by the strength of magnet, reluctance of iron and number of turns of armature winding. The stator magnetic flux remains essentially constant at all levels of armature current, therefore the torque-speed curve of the PMDC motor is linear [8].In accordance to state equations of PMDC motor, we sketch the block diagram. The block diagram of PMDC motor is shown in Figure 1.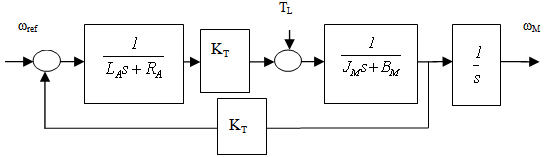 | Figure 1. Block diagram of PMDC motor [8] |
3. Adaptive Controller
Model Reference Adaptive Control (MRAC) is the control method for uncertain and undesirable system. This control method uses stable and optimum reference model for increasing performance of controller. By using this method, plant will have desired response [1].This control strategy is used two loops for obtaining optimum output, namely regulator loop and adaptation loop. Regulator loop is included plant and controller. Adaptation loop adjusts parameters of regulator and consequently reduction in the error between reference model and plant outputs is resulted. Figure 2 shows block diagram of MRAC. 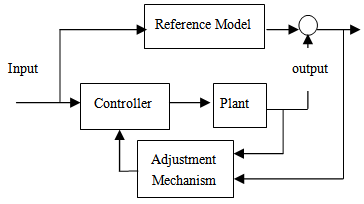 | Figure 2. Block diagram of MRAC |
Reference model as part of MRAC is described desired model. In fact, plant is forced to behave close to the reference model therefore this is significant part of adaptive controller. Controller is usually adjusted by a number of parameters. The control law is linear in terms of the adjustable parameters (linear parameterization). Adaptive controller design normally requires linear parameterization in order to obtain adaptation mechanism with guaranteed stability and tracking convergence. The values of these control parameters are mainly dependent on adaptation gain which in turn changes the control algorithm of adaptation mechanism [9].Adaptation Mechanism: It is used to adjust the parameters in the control law [9]. Different methods such as MIT rule, Lyapunov theory and etc are used to product Adaptation Mechanism. The proposed controller is used MIT rule for developing adaptive mechanism.The MIT rule was developed in Massachusetts Institute of Technology and is used to apply the MRAC approach to any practical system. In this rule the cost function or loss function is defined as [9]: | (4) |
Where e is the output error and is the difference of the output of the reference model and the actual model, while θ is the adjustable parameter known as the control parameter. In this rule the parameter θ is adjusted in such a way so that the loss function is minimized. Therefore, it is reasonable to change the parameter in the direction of the negative gradient of F that is [9]: | (5) |
 | (6) |
The partial derivative term ∂e/ ∂θ, is called the sensitivity derivative of the system. This shows how the error is dependent on the adjustable parameter, θ. There are many alternatives to choose the loss function F. For example, it can also be taken as mode of error. Similarly dθ/dt can also have different relations for different applications.Sign-sign algorithm: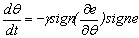 | (7) |
Or it may be chosen as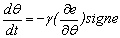 | (8) |
Where sign
In some industrial applications it is found that the choice of adaptation gain is critical and its value depends on the signal levels. So MIT rule has to be modified as follows [9]: | (9) |
Where
Also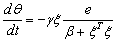 | (10) |
Where β>0 is introduced to avoid zero division when
small. Using the MIT rule defined by (4), (5) and (6) for developing the control law [9].
4. Adaptive Neuro-Fuzzy Inference System
Nowadays, there are advanced developments in neuro-fuzzy synergisms for modelling and adaptive control of nonlinear systems [10]. Some of the advantages of ANFIS are fast convergence due to hybrid learning and ability to adjust the shape of input membership functions. Because of this, it offers better tracking and adaptive capabilities than any other controller [10].Using training data, ANFIS constructs a fuzzy inference system whose membership functions parameters are tuned using either a back propagation algorithm alone, or in combination with recursive least squares type algorithm. Using hybrid learning technique, the learning process speeds up compared to the gradient method alone, which exhibits the tendency to be trapped in local minima [11].For simplicity, we assume the fuzzy inference system under consideration has two inputs x and y and one output z. We suppose that the rule base contains two fuzzy if-then rules of Takagi and Sugeno's type [12]. Rule 1: If x is A1 and y is B1 then f1=p1 x+ q1 y + r1Rule 2: If x is A2 and y is B2 then f2=p2 x+ q2 y + r2Then type-3 fuzzy reasoning is illustrated in Figure 3(a) and the corresponding equivalent ANFIS architecture is shown in Figure 3(b). The node functions in the same layer are of the same function family as described below [12]: | Figure 3. (a) Type-3 fuzzy reasoning. (b) Equivalent ANFIS |
Layer 1: Every node i in this layer is a square node with a node function [12]: | (11) |
Where x is input to node i and Ai is the linguistic label associated with this node function.Layer 2: Every node in this layer is a circle node labelled ∏ which multiplies the incoming signals and the product out. For instance [12],  | (12) |
Each node output represents the firing strength of a rule [12]. Layer 3: Every node in this layer is a circle node labelled N, the ith node calculates the ratio of the ith rule's firing strength [12]: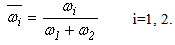 | (13) |
Layer 4: Every node i in this layer is a square node with a node function [12]: | (14) |
Layer 5: The single node in this layer is a circle node labelled
that computes the overall output as summation of all incoming signals, i.e. [12],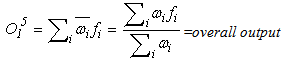 | (15) |
5. Proposed Controller
As already we discussed our strategy based on implementation both ANFIS and simultaneously MRAC on PMDC motor. In this strategy, fuzzy controller is designed by using ANFIS. The ANFIS controller is located in error path of MRAC. As important part of MRAC, second order critically damped system is under investigation as reference model. Behavioural optimization of PMDC motor using the novel strategy were taken into consideration. The schematic of proposed controller is as below: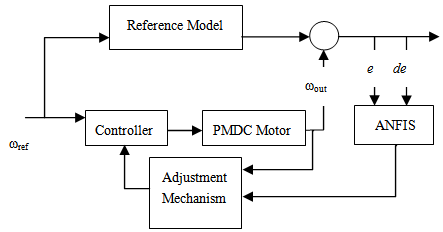 | Figure 4. Proposed control structure |
The ANFIS controller has two inputs and one output, error and its derivative are inputs where modified error is output of ANFIS controller. The ANFIS controller simulation results are displayed in Figure 5 where 2001 pairs of input-output were applied as ANFIS data. ANFIS controller is used three membership function for every input; therefore 9 rules describe all condition for controller.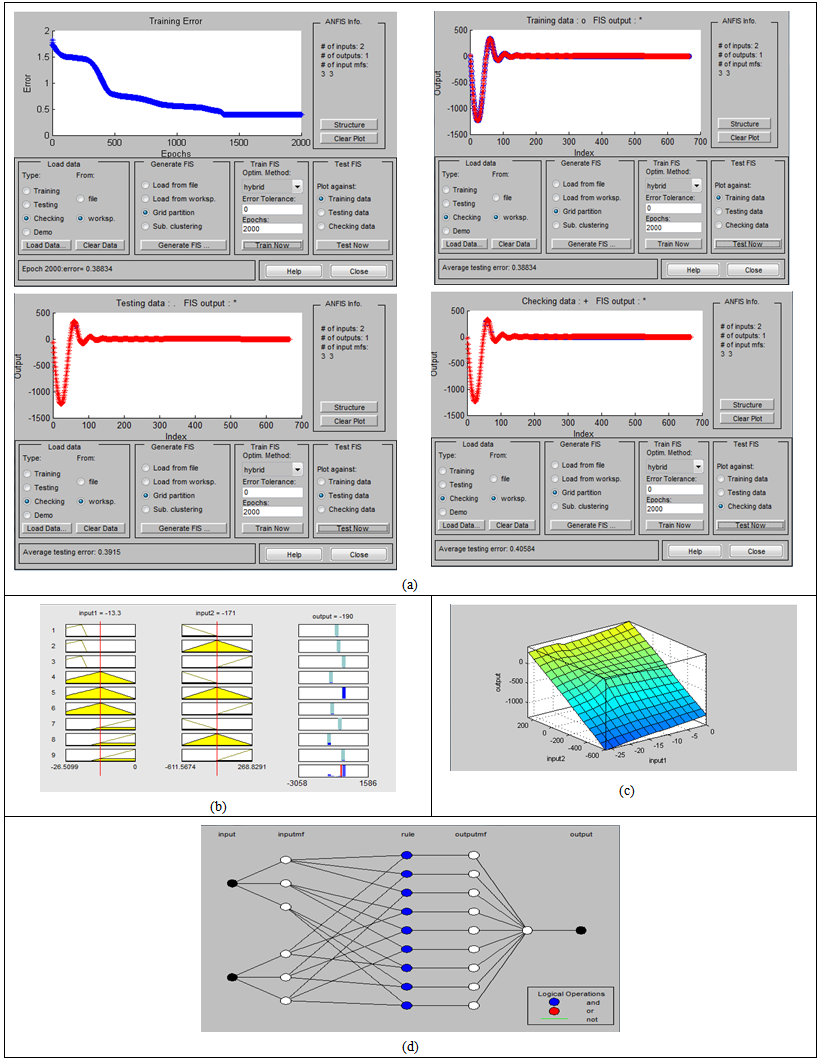 | Figure 5. (a) Results of ANFIS training and testing; (b) Rule viewer; (c) Surface viewer; (d) ANFIS Model Structure |
The Figure 5 shows rule viewer, structure and surface of ANFIS controller and more the error of training data, testing data and checking data and finally steady state errors of training data, testing data and checking data; the steady state errors can quantitatively be expressed respectively equal to: 0.38834،0.3915، 0.40584. Table 1 is obtained after training ANFIS controller. The fuzzy rules table shows that nine if-than rules describe all possible conditions.Table 1. Fuzzy Rules of ANFIS Controller  |
| |
|
Simulation results of the controller are presented in next section.
6. Simulation Results and Discussion
Parameters of permanent magnet DC motor are as follows: RA = 7.72 (ohm), LA = 0.16273 (H), KT = 1.25 (Nm), BM = 0.003 (N.m.s/r) and JM = 0.0236 (kg.m2).Figures 6(a), (b), (c) and (d) show without controller step response of PMDC motor in no load, stopping, applied load and noisy load conditions. We observe that steady state error and maximum per cent overshoot of step response are undesirable; also motor cannot recovery reference speed when applied torque; also this system hasn't reasonable behaviour in applied noisy load condition. This system can decrease speed in short time but undershoot is happened in stopping condition. We want to improve performance of PMDC motor by means of proposed controller. The proposed strategy and the model of PMDC motor are shown in Figures 4 and 1, respectively. Model of motor is embedded in Figure 4. 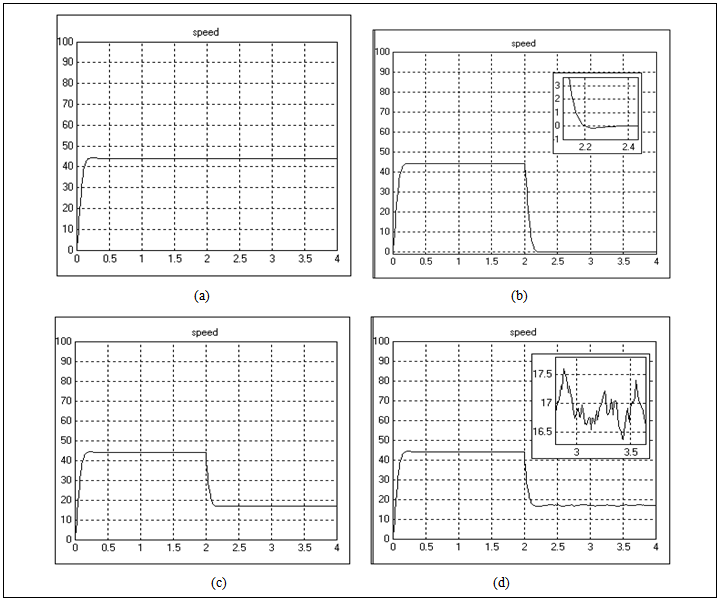 | Figure 6. Step time response of PMDC motor (a) no load;(b) zero-input response;(c) applied torque;(d) noisy load |
First we study no load condition for control methods. Figure 7 shows step response of proposed, fuzzy-adaptive and adaptive controllers.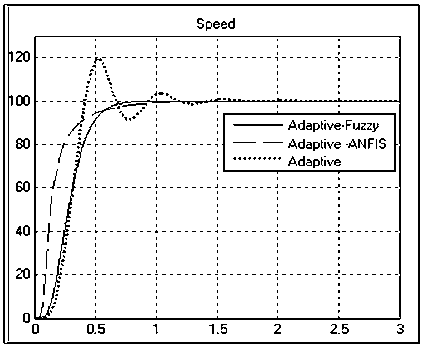 | Figure 7. Step response of proposed, adaptive – fuzzy and adaptive controllers (no load) |
Simulation shows that rise time of proposed controller is smaller than rise time of adaptive – fuzzy controller, also maximum per cent overshoot and steady state error of control methods equal to zero. The settling time of adaptive-ANFIS controller is larger than settling time of adaptive-fuzzy controller but this is reasonable value. Maximum per cent overshoot of adaptive controller is very larger than maximum per-cent overshoot of adaptive-fuzzy and adaptive-ANFIS controllers; also adaptive controller has large settling time.Figure 8 shows that the recovery time of speed and maximum per cent undershoots of adaptive-ANFIS controller are very smaller than the recovery time of speed and maximum per cent undershoot of adaptive–fuzzy and adaptive controllers. The proposed control system can immediately recover to reference speed while maximum undershoot is relatively reduced.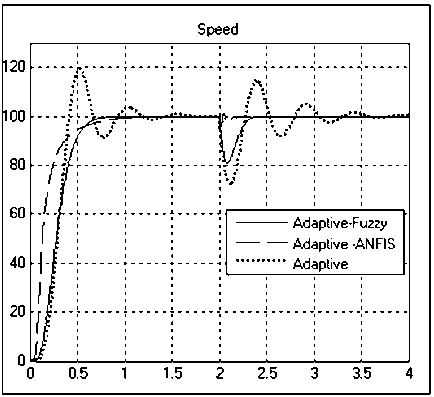 | Figure 8. Step response of proposed, adaptive – fuzzy and adaptive controllers (applied load) |
The step response of systems when the applied noisy load is as follows:Figure 9 shows that proposed controller has better robustness in noisy load condition. The amount of variations of step response in noisy load for proposed controller is smaller than other mentioned controllers. Per cent of sum of maximum time oscillation is shown in table 3. 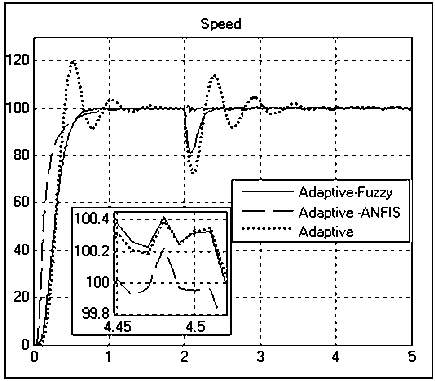 | Figure 9. Step response of control systems in noisy load condition |
Figure 10 shows zero-input response of the motor when reference speed changes to zero in t=2s. Proposed controller can decrease speed in least time. The proposed Control system reacts immediately to slow down. 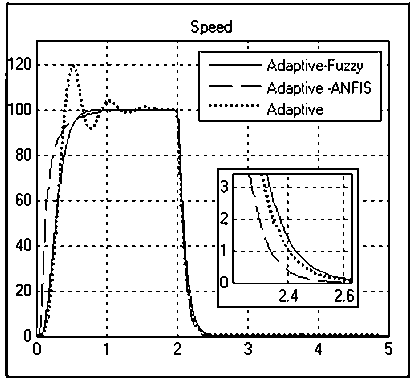 | Figure 10. Zero- input response of motor |
The rise time, settling time, steady state error and maximum per cent overshoot are shown in Table 2 (Reference speed is 100 rad/s).Table 2. Performance criteria of step response (no load) 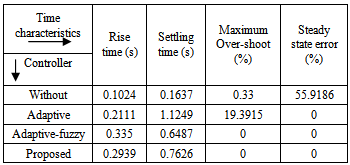 |
| |
|
Table 2 shows that without controller system has more reasonable rise time, settling time but maximum per cent overshoot and steady state error are not desirable. The table shows rise time of adaptive controller is smaller than other controllers but settling time and maximum per cent overshoot is not desirable. The proposed controller has reasonable rise time, settling time, maximum per cent overshoot and steady state error. Table 3 shows maximum per cent undershoot, recovery time, stopping time and per cent maximum variation in noise condition of step response for control systems. We observe that recovery time, maximum per cent undershoot; stopping time and maximum per cent variation of proposed controller is smaller than other controllers. According to simulation results, adaptive- ANFIS controller has more reasonable behaviour in different condition whereas other mention controller hasn't this property.Table 3. Maximum percent undershoot and variation, recovery time and stopping time of step response for control systems 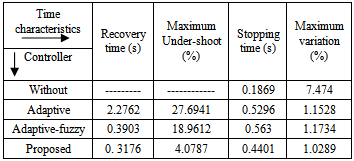 |
| |
|
7. Conclusions
The proposed combined controller proves advantages over adaptive and adaptive fuzzy controllers in time domain system behaviours. These behavioural characteristics clearly presented on the tables 2 and 3 for both situations. Improvement of the dynamic performance of the system uses even three input membership function for covering all situations thank to Sugeno inference and the defuzzification time considerably decreased. Controller implementation of more reasonable dynamic performances with only three input membership function is considerably less sophisticated.
ACKNOWLEDGMENTS
The Authors thank ISLAMIC AZAD University, Central Tehran Branch as this work is the result of master thesis in electrical engineering (MSc Eng.) with titled "Improvement Performance of Permanent Magnet Motor by Using Fuzzy Controller" which is on focus at the Faculty of Engineering.
References
[1] | S. Z. Moussavi, M. Alasvandi, Sh. Javadi, “Speed Control of Permanent Magnet DC Motor by using Combination of Adaptive Controller and Fuzzy Controller”, International Journal of Computer Applications, vol. 52, pp. 11-15, 2012. |
[2] | Siong, T. C., Ismail, B., Mohammed ,M.F., Tajuddin, M.F.N., Rahim, S.R.A., Zainuddin Mat Isa, Z.M., 2010, Study of Fuzzy and PI Controller for Permanent-Magnet Brushless DC Motor Drive, 2010 4th Int Power Engineering and Optimization Conf (PEOCO), Shah Alam, 517- |
[3] | Velagic, J. , Galijasevic, A., 2009, Design of Fuzzy Logic Control of Permanent Magnet DC Motor under Real Constraints and Disturbances, 2009 IEEE International Symposium on Intelligent Control, Saint Petersburg, 461-466. |
[4] | R. Prakash, R. Anita, ”Robust Model Reference Asaptive PI Control”, Journal of Theoretical and Applied Information Technology, vol. 14, pp. 51-59, 2010. |
[5] | Ashok. Kusagur, S.F. Kodad, B V. Sankar Ram, “Modeling, Design & Simulation of an Adaptive Neuro-Fuzzy Inference System (ANFIS) for Speed Control of Induction Motor”, International Journal of Computer Applications, vol. 6, pp. 29-44, 2010. |
[6] | P. Melin, O. Castillo, “Intelligent Control of a Stepping Motor Drive Using an Adaptive Neuro–Fuzzy Inference System”, International Journal Information Sciences (Elsevier), vol. 170, pp. 133-151, 2005. |
[7] | S. V. Ustun, M. Demirtas, “Modeling and Control of V/f Controlled Induction Motor Using Genetic-ANFIS Algorithm”, International Journal Energy Conversion and Management (Elsevier), vol. 50, pp. 786-791, 2009. |
[8] | Shahgholian, G., Shafaghi, P., 2010, State Space Modeling and Eigenvalue Analysis of the Permanent Magnet DC Motor Drive System, 2010 International Conference on Electronic Computer Technology (ICECT), Kuala Lumpur, 63-67. |
[9] | P. Swarnkar, S. Jain, R. K. Nema, “Effect of Adaptation Gain in Model Reference Adaptive Controlled Second Order System”, Engineering, Technology & Applied Science Research (ETASR), vol. 1, pp. 70-75. 2011. |
[10] | Jain, M., Singh, M., Chandra, A., Williamson, S.S. , 2011, Sensorless Control of Permanent Magnet Synchronous Motor using ANFIS Based MRAS, 2011 International Electric Machines& Drives Conference (IEMDC), Niagara Falls, 599-606. |
[11] | Bannae Sharifian, M.B., Shafiei, M., Sha Sadeghi, M., Golestaneh, F. , 2011, Direct Torque Control of Brushless DC Motor Drives Based on ANFIS Controller with Fuzzy Supervisory Learning, 2011 IEEE International Conference on Electrical Machines and Systems (ICEMS), Beijing, 1-6. |
[12] | J.S.R. Jang, “ANFIS: adaptive-network-based fuzzy inference system”, IEEE Transactions on Systems, Man and Cybernetics, vol. 23, pp.665-685, 1993. |