Md. Mahbubur Rahman, Md. Mutasim Uddin, Md. Monir Hossan, Md. Mazharul Helal, Suraiya Ireen, Dr. Jagannath Biswas
Textile Engineering Department, Green University of Bangladesh, Dhaka, Bangladesh
Correspondence to: Md. Mahbubur Rahman, Textile Engineering Department, Green University of Bangladesh, Dhaka, Bangladesh.
Email: |  |
Copyright © 2022 The Author(s). Published by Scientific & Academic Publishing.
This work is licensed under the Creative Commons Attribution International License (CC BY).
http://creativecommons.org/licenses/by/4.0/

Abstract
The effect of soda ash on fastness properties and some physical properties of reactive dyed cotton fabric were compared with the varying concentration of soda ash. Soda ash changes the pH of the fiber-reactive dye and cellulose fiber so that the dye reacts with the fiber, making a stable connection that holds the dye to the fiber. It actually activates the fiber molecules so that they can chemically attach to the dye. Three different concentration of soda ash (10g/l, 15g/l, 20g/l) were used to compare the fastness. Different fastness properties of cotton dyed fabric such as rubbing fastness, washing fastness, water fastness, saliva fastness, perspiration fastness and physical properties such as abrasion and pilling resistance were investigated. Optimum amount of alkali helps to achieve required pH of dye liquor which facilitates the reactive dye fixation onto cellulosic materials. The extent of dye fixation was also conceptualized and observed better color fastness which was invariably in all tests. In most of the cases, the colour fastness properties and physical properties were improved at soda 20g/l.
Keywords:
Reactive dye, Soda ash, Cotton knitted fabric, Fastness properties
Cite this paper: Md. Mahbubur Rahman, Md. Mutasim Uddin, Md. Monir Hossan, Md. Mazharul Helal, Suraiya Ireen, Dr. Jagannath Biswas, Effect of Varying Concentration of Soda Ash on Fastness Properties of Reactive Dyed Cotton Fabric, International Journal of Composite Materials, Vol. 12 No. 1, 2022, pp. 10-16. doi: 10.5923/j.cmaterials.20221201.02.
1. Introduction
Cotton fiber is very popular among all textile fibers for their comfort, breathability, strength and versatility. Cellulosic fiber dyeing with reactive dyes is one of the most convenient and popular methods (Rahman Bhuiyan et al., 2017). Cotton can be dyed easily using reactive dyes due to its hydroxyl group (–OH). Direct dyed cotton has poor wash fastness due to weak bond between dye and fiber molecules (Chakraborty, 2014). Reactive dyes form strong covalent chemical bond with cotton fiber.Reactive groups of the dye molecule make the covalent bond with the cellulosic fiber polymer and act as an integral part of fiber and give good wash fastness (Clark, 2011). During the application of reactive dyes to cellulose (cotton) fibers under highly alkaline condition, a hydrolysis reaction takes place, originating the non-reactive oxi-dye form and those dyes (oxi-dye) stay on fabric surface. As a result, most of the cases it is seen that fastness properties of reactive dyed cotton fabrics are not good. Therefore, fixing agent is applied on reactive dyed fabric to develop the different fastness properties (Clark, 2011). The salt is associated in nursing exhausting agent to push the color towards polysaccharide molecules and therefore the alkali (soda ash) is hydrolyzing/fixing agent for the reactive colors. Sohel et al. studied the effect of soda ash on dyeing of woven cotton fabric with reactive dyes. They found good results on colour fastness to wash, water, and rubbing. They used 100% cotton woven fabric of 140 gsm and dyed the fabric with Procion Red H-3B and Reactive Black B dyes and the concentration of soda ash were 5%, 10% and 15% respectively. Paul et. al studied on the effect of alkali on dyeing of cotton fabric with reactive dye (shade 1%) and reported that the wash and rubbing fastness is good to excellent (Debasree Paul et al., 2017). Tofazzal et. al studied the effect of soda ash on dyeing on cotton fabric with Novacron Blue reactive dyes and found 20 g/l concentration as optimum (Tofazzal Hossain et al., 2019). Chowdhury studied the effect of alkali (soda ash) on rubbing fastness of reactive dyed cotton fabric has been studied and found pH value 12.02 as optimum (Chowdhury, 2014). Agarwal and Fu et al. studied Polymer aided dyeing at neutral pH (without using alkali) but found comparatively poor fastness properties than the conventional method (B. J. Agarwal, 2010, Fu et al., 2016). Uddin et al. studied the performance of eco-alkali in dyeing of cotton fabric with Novacron Blue FN-R and Novacron Blue 3GL dyes and did not find satisfactory results in terms of dye fixation percentage and color strength (Uddin et al., 2014).Environmental impacts of using alkali are also very high. So, reducing the usage of soda ash by ensuring optimum alkali concentration is very crucial (Hassaan & Nemr, 2017). This study concerns with the effect of varying concentration of soda (other parameters were kept same) on fastness properties in dyeing of cotton fabric with reactive dyes.In this study, three different types of reactive dyes: Reactive Yellow 176 (Synozol), Reactive Yellow 86 (Novacron) and Reactive Yellow 84 (Clariant) were used. The aim of this paper is to examine the fastness properties in the variation of alkali concentrations without changing the amount of dyes, auxiliaries and dye bath conditions. Color fastness to washing, rubbing, saliva, perspiration and sea water with varying alkali load are tested in details and actual results are analysed. In addition, abrasion and pilling properties of the dyed fabrics are done for comparison.
2. Materials and Methods
2.1. Materials
100% Cotton knitted single jersey fabric (desized, scoured and bleached) was used in this research which was collected from the Magpie composite limited, Bangladesh. The GSM of the fabric was 160. Three types of reactive dyes like Reactive Yellow 176 (Synozol), Reactive Yellow 86 (Novacron) and Reactive Yellow 84 (Clariant) were collected from Dysin Company Limited, Bangladesh and their structure are given below. The other chemicals like glauber salt, soda ash, wetting agent, levelling agent and sequestering agent and anionic detergent which were all of laboratory reagent grade, was collected from AUXI TEX, Bangladesh.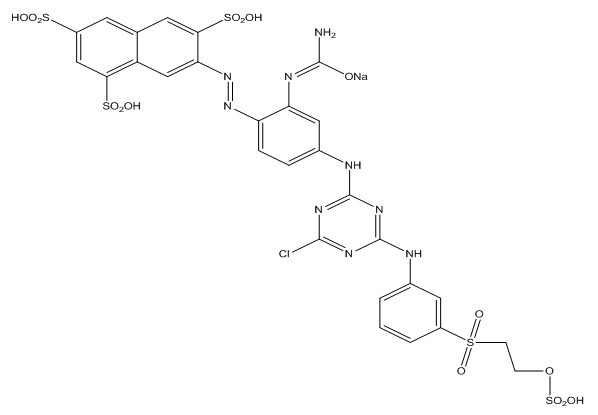 | Reactive Yellow 176 (Synozol) |
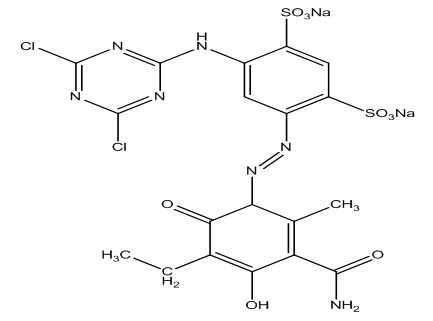 | Reactive Yellow 86 (Novacron) |
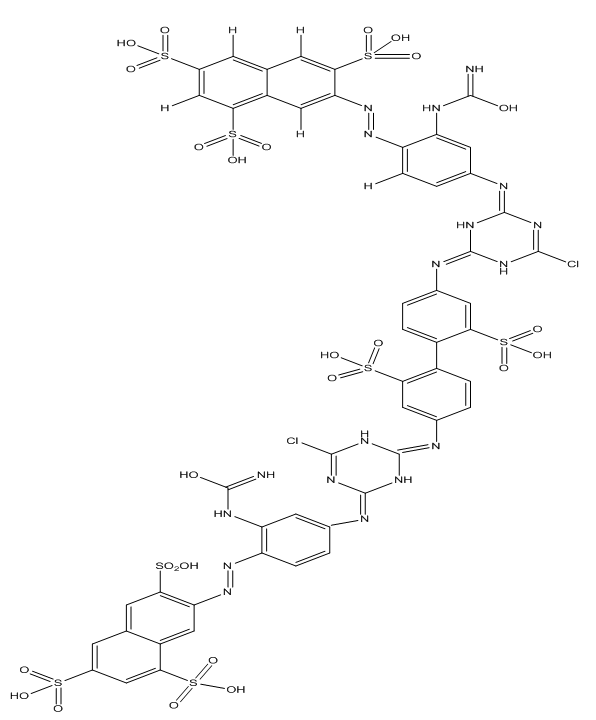 | Reactive Yellow 84 (Clariant) |
2.2. Dyeing Procedures
We have dyed single jersey 160 GSM knitted fabric in Lab Dyer 212 dyeing machine of MAG brand. The dyeing temperature was 60°C, pH of dyeing solution was 11-12 and dyeing time was 60 minutes. Material to liquor ratio was 1:15. Dyeing was done using three different types of reactive dyes (Synozol, Novacron, Clariant). We conducted three different recipes by varying the concentration of soda ash (10 g/l, 15 g/l, 20 g/l). Then we measured the color fastness of the dyed samples to understand and compared the effects of various recipes and establishing a standard concentration of soda ash to be used for the process.
2.3. Test Methods
Color fastness to washing, rubbing (wet and dry), saliva, perspiration (acidic and alkaline), sea water, abrasion resistance test and pilling resistance tests were done using ISO 105 C06 C2S, BS EN ISO 105 X12, GB/T 18886, ISO 105 E04, ISO 105 E02, ISO 105 E02, ASTM D4966-98 and TS EN ISO 12945-2 methods respectively. Each test was done five (05) times and mean values were considered.
3. Results and Discussions
3.1. Color Fastness to Washing
Color fastness to washing is an important parameter to assess the longevity of color on a textile material. Color fastness to washing is measured using grey scale for color change and color staining. A multifiber fabric is attached with the main dyed sample to assess the color staining.Table 1. Color fastness to washing test results using Synozol, Novacron and Clariant dyes with varying soda ash concentration 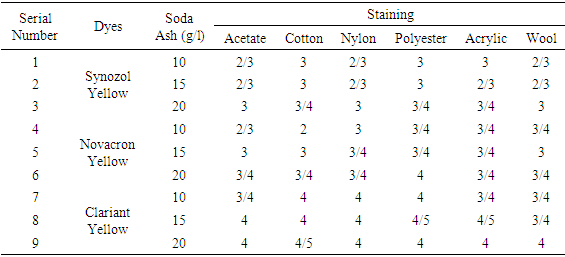 |
| |
|
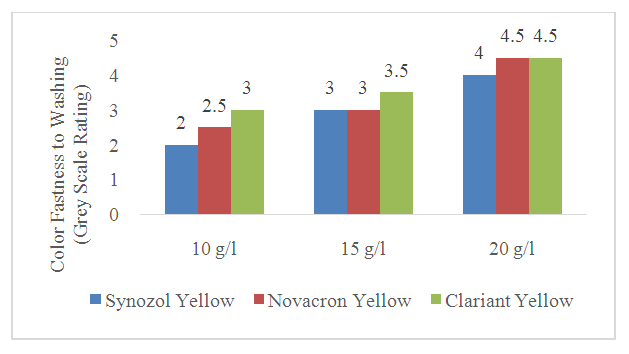 | Figure 1. Color Fastness to washing test results using Synozol, Novacron and Clariant dyes with varying soda ash concentration |
From the results, it is evident that the color concentration of soda ash is directly proportional with color fastness to washing of cotton fabric dyed with various types of reactive dyes. With the increasing amount of soda ash, the color fastness rating also increases for all the three dyes up to 20 g/l and the best color fastness to washing results are found by using Clariant Yellow dyes. It is supposed that required alkali concentration of dyebath is achieved using 20 g/l alkali which enhance dye fixation. As a result, enhanced color fastness to washing is observed for clarinet yellow.
3.2. Color Fastness to Water
Color fastness to water is another important parameter to assess textile material and how they respond with color is described in Table 2 and Figure 2 respectively. Color fastness to water is also measured using grey scale for color change and grey scale for staining. A multifiber fabric is attached with the main dyed sample to assess the color staining, as done for color fastness to washing.Table 2. Color Fastness to water test results using Synozol, Novacron and Clariant dyes with varying soda ash concentration 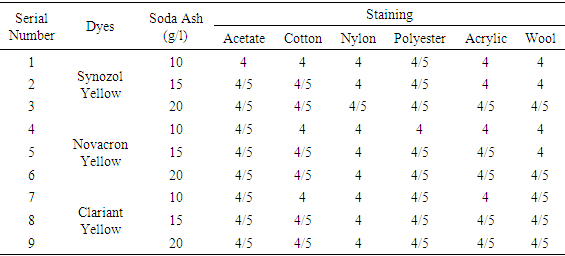 |
| |
|
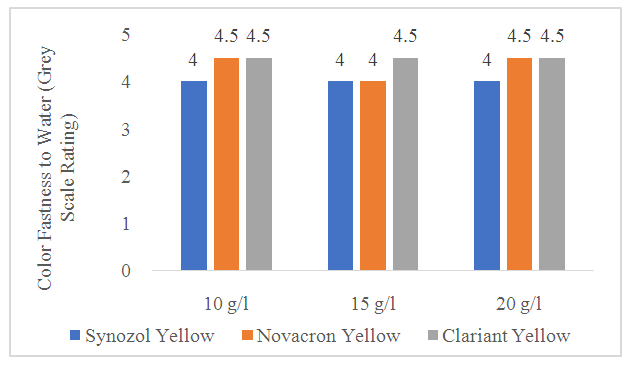 | Figure 2. Color fastness to water test results using Synozol, Novacron and Clariant dyes with varying soda ash concentration |
From the results, it is visual that the color concentration of soda ash has directly related with color fastness to water of cotton fabric dyed with various types of reactive dyes. As the amount of soda ash increased, the color fastness rating also increases for all the three dyes up to 20 g/l. We assume that, there is less chance of color bleeding against water as fixation is better and better fixation is achieved using optimum alkali. Color staining rating is also very good to excellent for various types of fiber of multifiber fabric.
3.3. Color Fastness to Perspiration
Color fastness to perspiration properties is depicted in Table 3,4 and Figure 3,4 respectively. Human perspiration can be of two types: acidic and alkaline. Color fastness to perspiration was done using two types of solution: acidic and alkaline. Color fastness to perspiration is measured using grey scale for color change and color staining. A multifiber fabric is attached with the main dyed sample to assess the color staining. Table 3. Color fastness to perspiration test results using Synozol, Novacron and Clariant dyes with varying soda ash concentration (Acidic Solution) 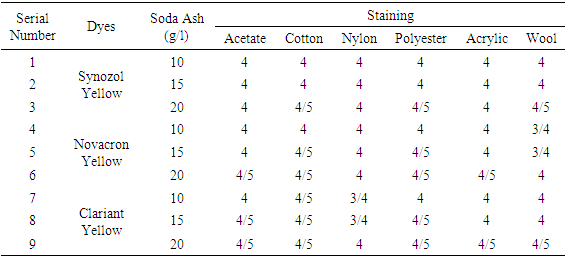 |
| |
|
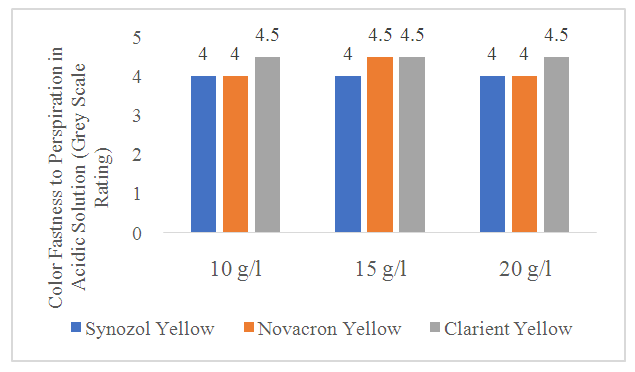 | Figure 3. Color fastness to perspiration test results using Synozol, Novacron and Clariant dyes with varying soda ash concentration in Acidic Solution |
Table 4. Color fastness to perspiration test results using Synozol, Novacron and Clariant dyes with varying soda ash concentration (Alkaline Solution) 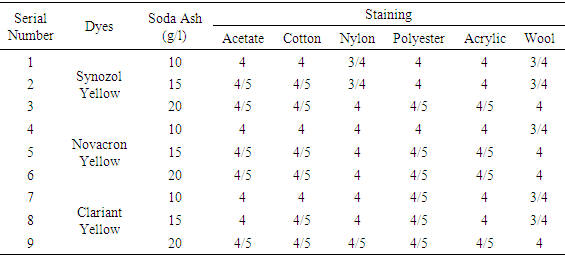 |
| |
|
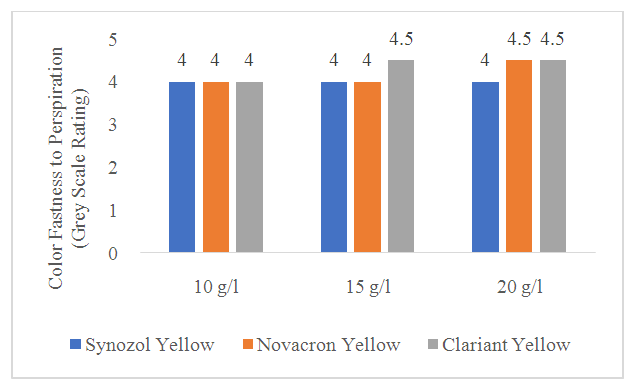 | Figure 4. Color fastness to perspiration test results using Synozol, Novacron and Clariant dyes with varying soda ash concentration in Alkaline solution |
From the results, it is clear that the color concentration of soda ash is directly related with color fastness to perspiration (both acidic and alkaline perspiration) of cotton fabric dyed with various types of reactive dyes. With the increasing amount of soda ash, the color fastness rating increases for all the three dyes up to 20 g/l. The best color fastness to washing results are found using Clariant Yellow dyes and it is inferior for Synozol yellow dyes in alkaline solution. So, alkali medium is more favourable for getting good properties than acidic condition.
3.4. Color Fastness to Rubbing
Color fastness to rubbing tests are of two types. One of which is done using dry cotton cloth and another is done using wet cotton cloth. It is a parameter to assess the longevity of color in a piece of fabric which is explained in Figure 5 and Figure 6 for dry and wet rubbing tests respectively.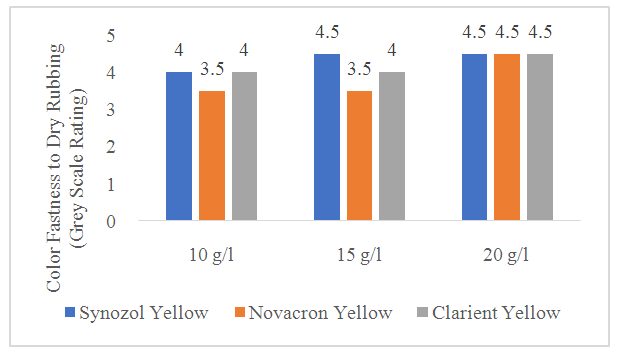 | Figure 5. Color fastness to dry rubbing test results using Synozol, Novacron and Clariant dyes with varying soda ash concentration |
From the results, it is evidential that both the color fastness to dry rubbing and color fastness to wet rubbing increase with increasing of concentration of soda ash. The best results are found using 20 g/l soda ash concentration because dye molecules create stable bond with cellulose in that optimum alkaline solution.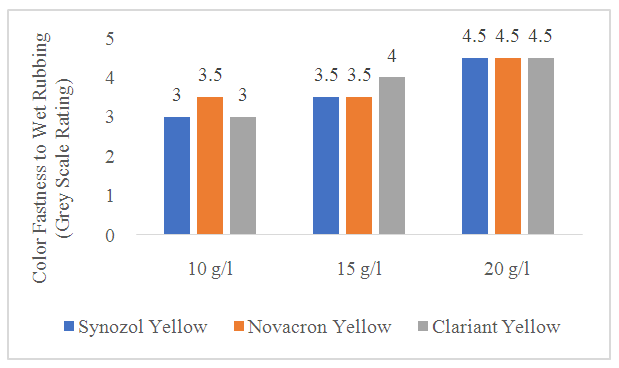 | Figure 6. Color fastness to wet rubbing test results using Synozol, Novacron and Clariant dyes with varying soda ash concentration |
3.5. Color Fastness to Saliva
Color fastness to saliva is measured using grey scale for color change and grey scale for staining. A multifiber fabric is attached with the main dyed sample to assess the color staining which is shown in figure 7.Table 5. Color Fastness to Saliva test results using Synozol, Novacron and Clariant dyes with varying soda ash concentration 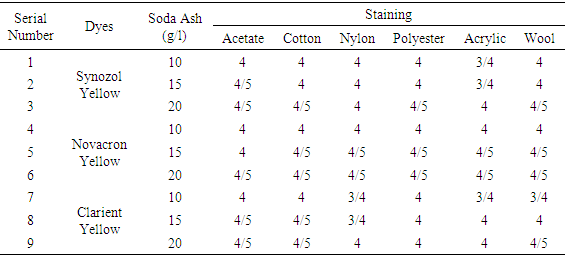 |
| |
|
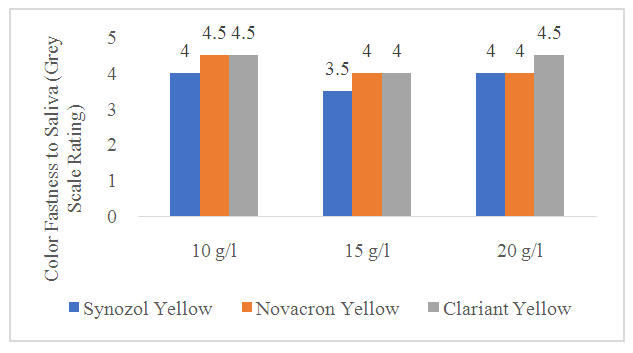 | Figure 7. Color fastness to saliva test results using Synozol, Novacron and Clariant dyes with varying soda ash concentration |
From the results, it is clear that the color concentration of soda ash is directly related with color fastness to saliva of cotton fabric dyed with various types of reactive dyes. 20 g/l alkali concentration yields better result than the other two alkaline concentrations. Comparatively better fastness is observed for Synozol Yellow and Clarient Yellow dyes than the other one.
3.6. Abrasion Test
Abrasion test is done to assess if the dyeing process has any effect on the abrasion resistance properties of the dyed fabric.This result is depicted in figure 8.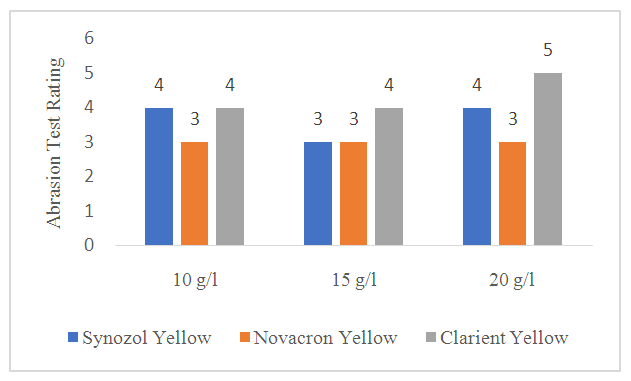 | Figure 8. Abrasion test results using Synozol, Novacron and Clariant dyes with varying soda ash concentration |
From the results, it is visual that the color concentration of soda ash has a positive influence on the abrasion resistance of reactive dyed cotton fabric. With the increment of amount of soda ash, the abrasion resistance rating generally increases and Clariant Yellow dye shows better abrasion resistance at 20 g/l soda ash concentration than the other two dyes.
3.7. Pilling Test
Pilling test is done to assess the effect of dyeing on the pilling resistance properties of the dyed fabric and the results are shown in figure 9.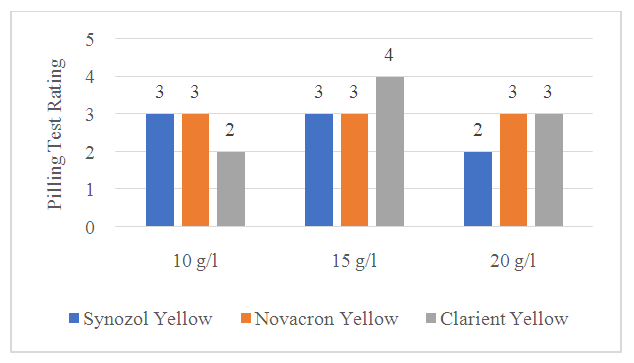 | Figure 9. Pilling test results using Synozol, Novacron and Clarient dyes with varying soda ash concentration |
From the pilling results, it is evident that the color concentration of soda ash has a positive influence on the pilling resistance of reactive dyed cotton fabric. With the incremental concentration of soda ash, the pilling resistance rating generally increases and Novacron Yellow dye shows better pilling resistance at 20 g/l soda ash.
4. Conclusions
In this study, optimization of amount of alkali is studied for three types of reactive yellow dyes by testing the color fastness, abrasion and pilling of dyed fabrics. 20 gm/l alkali concentration exhibited excellent results in terms of color fastness and physical properties of textile materials. Optimum amount of alkali helps to achieve required pH of dye liquor which facilitates the reactive dye fixation onto cellulosic materials. Further, better fixation yielded better color fastness invariably in every test. Reactive Yellow 84 (Clariant) shows better results than Reactive Yellow 176 Synozol and Reactive Yellow 86 (Novacron) except pilling test results. Sustainability in dyeing processes is a growing concern. Optimization of auxiliary chemical usage is important in this regard. Amount of alkali used for dyeing of cotton fabric with reactive dyes can be optimized for various color shades which will assist to minimize chemical loss. At the same time, the adversarial impacts of textile dyeing house on the environment can also be reduced through it. More works are needed to be done to optimize different dyeing processes and make dyeing industry sustainable and more environment friendly in the long run.
ACKNOWLEDGEMENTS
This work was supported in part by the Center for Research, Innovation, and Transformation of Green University of Bangladesh under grant No. 11/2019.
References
[1] | B. J. Agarwal, S. D. B. (2010). Possibilities of Polymer-Aided Dyeing of Cotton Fabric with Reactive Dyes at Neutral pH B. Journal of Applied Polymer Science, 116(5), 2658–2667. https://doi.org/10.1002/app. |
[2] | Chakraborty, J. N. (2014). Fundamentals and Practices in Coloration of Textiles (Second Edi). Woodhead Publishing India in Textiles. |
[3] | Chowdhury, T. A. (2014). Concentration of soda ash: An imperative factor for rubbing fastness of reactive dyed knit fabric. Research Journal of Social Science and Management, December 2014. https://citeseerx.ist.psu.edu/viewdoc/download?doi=10.1.1.735.2021&rep=rep1&type=pdf. |
[4] | Clark, M. (Ed.). (2011). Handbook of Textile and Industrial Dyeing Volume 1. Woodhead Publishing. |
[5] | Debasree Paul, Subrata Chandra Das, Tarikul Islam, Md. Abu Bakar Siddiquee, & Md. Abdullah Al Mamun. (2017). Effect of Alkali Concentration on Dyeing Cotton Knitted Fabrics with Reactive Dyes. Journal of Chemistry and Chemical Engineering, 11(4), 162–167. https://doi.org/10.17265/1934-7375/2017.04.004. |
[6] | Fu, S., Farrell, M. J., Hauser, P. J., Hinks, D., Jasper, W. J., & Ankeny, M. A. (2016). Real-time dyebath monitoring of reactive dyeing on cationized cotton for levelness control: part 1—influence of dye structure, temperature, and addition of soda ash. Cellulose, 23(5), 3319–3330. https://doi.org/10.1007/s10570-016-1008-9. |
[7] | Hassaan, M. A., & Nemr, A. El. (2017). Health and Environmental Impacts of Dyes: Mini Review. American Journal of Environmental Science and Engineering, 1(3), 64–67. https://doi.org/10.11648/j.ajese.20170103.11. |
[8] | Rahman Bhuiyan, M. A., Hossain, M. A., Zakaria, M., Islam, M. N., & Zulhash Uddin, M. (2017). Chitosan Coated Cotton Fiber: Physical and Antimicrobial Properties for Apparel Use. Journal of Polymers and the Environment, 25(2), 334–342. https://doi.org/10.1007/s10924-016-0815-2. |
[9] | Tofazzal Hossain, B., Kumar Saha, P., Kumar Saha, S., Abul Hasan, M., Kumar Biswas, S., Masud Rana, M., Saha, K., Md Tofazzal Hossain α, J., Kumar Saha σ, P., & Kumar Saha ρ Md Masud Rana Ѡ, S. (2019). Effect of Varying Concentration of Soda Ash on Fastness Properties of Reactive Dyed Cotton Fabric. Type: Double Blind Peer Reviewed International Research Journal Publisher: Global Journals Online, 19(4). |
[10] | Uddin, M. G., Ghosh, N. C., & Reza, S. (2014). Study on the performance of eco-alkali in dyeing of cotton fabric with reactive dyes. International Journal of Textile Science, 3(3), 51–58. https://doi.org/10.5923/j.textile.20140303.03. |