Italo Martins Gomes1, Rodrigo Nogueira de Codes2, Alex Sandro de Araújo Silva2
1Petróleo Brasileiro S.A, Alto do Rodrigues-RN, Brazil
2Department of Environmental Sciences and Technology of the UFERSA, Mossoró-RN, Brazil
Correspondence to: Italo Martins Gomes, Petróleo Brasileiro S.A, Alto do Rodrigues-RN, Brazil.
Email: |  |
Copyright © 2020 The Author(s). Published by Scientific & Academic Publishing.
This work is licensed under the Creative Commons Attribution International License (CC BY).
http://creativecommons.org/licenses/by/4.0/

Abstract
The Oil & Gas industry has to constantly face equipment corrosion challenges due to the chemical characteristic of the oil, gas and contaminants in the reservoirs. In 2010, a three-layered composite was developed for the production pipelines of terrestrial oil wells as an alternative to Grade B API 5L steel, which was commonly used and more susceptible to corrosion. In this work, samples of pipelines made of this composite were collected in oil wells of areas with different operating pressures that have been working with this material for some years. The samples were analyzed through the water absorption test and compared with a new control sample in order to understand and evaluate the influence of pressure on the water absorption property during the period of operation of this new material, since water can harm the properties of composite materials. The results pointed to an increase in the water absorption of the samples with higher operating pressure compared to the control sample, probably due to an increase in the micro-voids and interface spacing between the layers caused by the conditions in service.
Keywords:
Water absorption, Composite, Oil, Piping, Glass fiber, Epoxy
Cite this paper: Italo Martins Gomes, Rodrigo Nogueira de Codes, Alex Sandro de Araújo Silva, Influence of Operating Pressure on Water Absorption of a Polymeric Composite Applied in Oil Pipelines, International Journal of Composite Materials, Vol. 10 No. 2, 2020, pp. 37-39. doi: 10.5923/j.cmaterials.20201002.02.
1. Introduction
The oil exploration industry is hindered significantly by corrosive processes due to the complex characteristics and composition of the fluids in oil reservoirs. Mature terrestrial fields (with long production periods) have the characteristic of possessing significant amounts of water and other corrosive agents along with the oil, such as O2, CO2, H2S and sulfate-reducing bacteria, which tend to attack the steel piping from the inside, in addition to the soil and atmosphere, which also tend to cause external corrosion in equipment like production pipelines.Composite materials have been a consolidated alternative for some years to be used in corrosive environments, replacing metal alloys as they join the properties of more than one material. [1] Their structural characteristics promote attractive property combinations, such as low density, high specific resistance, high modulus of elasticity, and high chemical resistance, which enable the manufacture of parts with complex geometries and high resistance to corrosion and degradation in various industrial environments. [2]Glass fiber reinforced polymer matrix composites (GFRP) are the most common composite materials in this category. The main advantages of these composites are their low cost, good tensile strength, good chemical resistance and excellent insulating properties. The disadvantages are their relatively low modulus of elasticity, high density (of the commercial fibers), sensitivity to abrasion during handling (which often reduces tensile strength), relatively low fatigue strength and high hardness (which causes excessive wear in molds and cutting tools). [3]In general, several factors are of influence on the mechanical behavior of composites. These factors include the manufacturing process used, the manner in which the loads are applied, the developed damage mechanism, the presence of adverse humidity and temperature conditions, the respective volume fractions, the properties of the interface, the presence of voids, in addition to the properties of the constituent elements. [4]The properties of GFRP composites can be affected when they absorb water above certain thresholds, which may undermine their applicability in operational situations. [4] Defects such as interaction deficiencies between layers, changes in the matrix or fiber, and micro-voids may influence the water absorption of the composite. Water absorption tests are therefore important to establish limits and detect changes of the materials in contact with water. [5]The objective of this work is to use water absorption tests to evaluate oil pipeline samples made of a newly-developed three-layered polymeric composite, operating in mature oil fields (with high water content in the reservoirs), in addition to the influence of operating pressure on the behavior of this material. This study can help prevent future failures of this new material due to harmful changes in its properties caused by water absorption and avoid problems with operational, personal and environmental accidents.
2. Experimental
2.1. Materials
In 2010, a three-layered composite (Figure 1) was developed for the production pipelines of terrestrial oil wells as an alternative to Grade B API 5L steel, which was commonly used and more susceptible to corrosion and failures that may cause environmental, operational and personal damage. This composite was produced through the filament winding process, which is characterized by high dimensional control and mechanical strength. 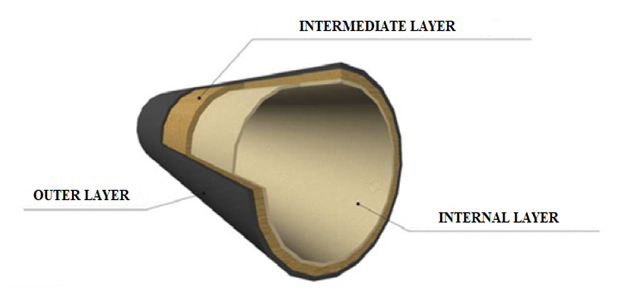 | Figure 1. Three-layered polymeric composite. [6] |
The material has an inner layer made of a glass fiber reinforced epoxy polymeric matrix, an intermediate layer of a glass fiber and silica reinforced polyester matrix and an outermost layer coated with high density polyurethane. The material was specified for 3-inch pipes, a maximum operating pressure of up to 5.17 MPa (750 psi) and a design temperature of 95°C. [6]The innermost epoxy layer with glass fiber is the most important layer of the material, since this is the layer that is in first contact with the pressure, temperature and characteristics of the fluid that flows through the pipeline and therefore needs to have the best properties. The intermediate polyester and silica layer is meant to improve the rigidity of the composite without the need to increase the thickness of the inner layer, saving on the final cost of the material. [6] The outermost layer of high-density polyurethane, on the other hand, is meant to serve as an insulating, mechanical and corrosive protection against agents present in the soil or atmosphere. [7]Tube samples made from this composite were taken from two field oil wells at different pressures that have been operating with this material for some years, and a sample was also taken from a control tube that was never used, as can be seen in Table 1, to perform comparative tests of the water absorption properties.Table 1. Samples of composite production lines 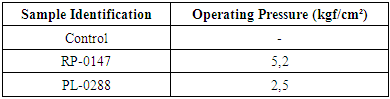 |
| |
|
2.2. Methodology
The dimensions of the removed samples are shown in Figure 2 (25.4 by 70 mm). After their removal, they were dried in an oven at 50°C for 24 hours. Afterwards, the samples were placed in tanks with pure water and weighed every 24 hours on a precision scale until reaching their saturation point.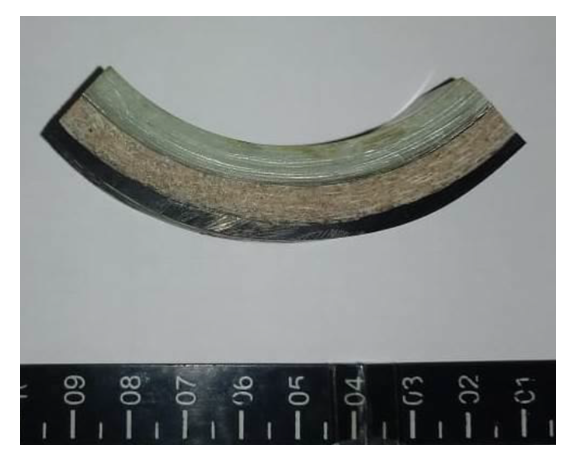 | Figure 2. Dimension of the composite sample |
The test was performed as described in the ASTM D570-98 standard. The percentage of water in the test specimen was calculated using Equation 1, where: ΔM is the water absorption percentage and Mi and Mf correspond to the sample masses before and after immersion in water. [8] | (1) |
3. Results and Discussion
Figure 3 shows the samples during the test. Figure 4 shows the water absorption results for the control sample and each well sample. All samples were saturated within 48 days of testing. As can be seen, the control sample had the lowest water absorption value (1.46%), while the sample of well RP-0147, which has higher operating pressure, had a higher water absorption than the sample of well PL-0288 (2.86% and 1.63%, respectively). Two possible situations were expected: first, that the internal pressure of the pipelines would cause compression in the polymeric matrix, reducing voids and therefore the water absorption of the samples in operation (which would not occur in the control sample). In the second alternative (which was confirmed), there would be an increase in the absorption of the samples from the wells, since the stresses of the operational conditions of the pipelines would influence the internal structure of the material and increase micro-voids and detachments at the layer interfaces, generating more space for water penetration.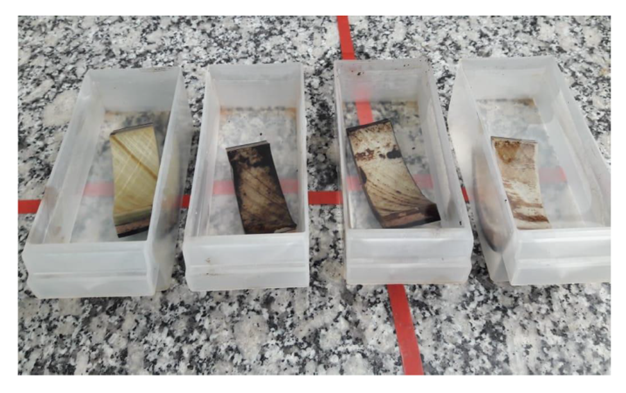 | Figure 3. Samples during the test |
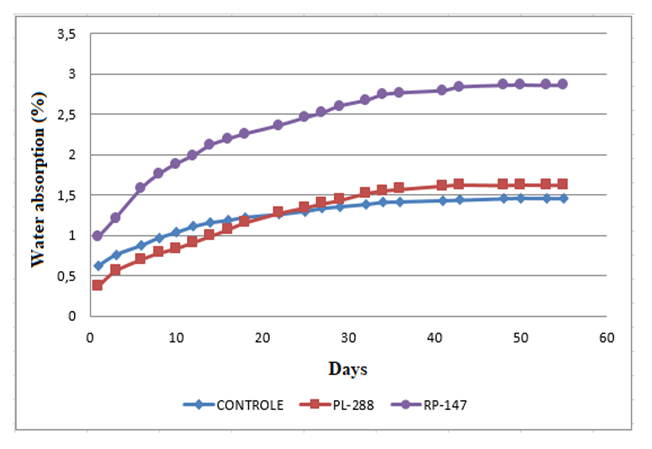 | Figure 4. Chart of the results |
4. Conclusions
It is important to study the properties of new materials in real-life situations in the field to understand their behavior and prevent failures that may cause personal, environmental and operational damage (mainly in the petroleum industry), failures which are often difficult to predict in the development stages of the material.Water absorption tests are important for the study of composite materials as these materials are sensitive to water penetration, which may cause damage to their mechanical properties and increase the risks of their application (especially in critical areas like oil & gas).The results of this study revealed that the samples in operation had more water absorption than the control sample, probably due to operational stresses, which generated (or increased) defects and voids, causing more water penetration. This fact should be treated with caution in order to establish acceptable water absorption limits for this new material that ensure its safe applicability in oil production fields.
References
[1] | MENDONÇA, P. T. R. Materiais Compostos e Estruturas-sanduíche. Barueri / SP, Ed. Manole, 2005, p. 3. |
[2] | GIBSON, A. G. The Cost Effective Use of Fibre Reinforced Composites Offshore, University of Newcastle Upon Tyne, 2002, p. 5-6. |
[3] | MALLICK, P.K. Fiber-reinforced composites: materials, manufacturing, and design. 3rd ed, 2007, p. 1-30. |
[4] | BARROS, Gustavo de Araújo. Tubulações de PRFV com adição de areia quartzosa visando sua aplicação na indústria do petróleo. Natal, 2007, p. 23-25. |
[5] | PAIVA, J. M. F.; Frollini, E. Matriz termofixa fenólica em compósitos reforçados com fibras de bagaço de cana-de-açúcar. Polímeros: Ciências e Tecnologia, 1999, p. 85-86. |
[6] | OLIVEIRA, Eugênio Onofre de. Desenvolvimento de tubulação de compósito polimérico revestida externamente com poliuretano de alta densidade, 2010, p. 39-40. |
[7] | ABE, Rodnei, Massamiti. Estudo do poliuretano de alta densidade para proteção externa de oleodutos térmicos. São Paulo, 2008, p. 91. |
[8] | ASTM D570-98. Standard Test Method for Water Absorption of plastics. ASTM INTERNATIONAL. USA, 2018, p. 2-3. |