G. Gajaraj, Parth Lal, M. Raguraman
Department of Mechanical Engineering, Indian Institute of Information Technology, Design and Manufacturing, Kancheepuram, Chennai, India
Correspondence to: M. Raguraman, Department of Mechanical Engineering, Indian Institute of Information Technology, Design and Manufacturing, Kancheepuram, Chennai, India.
Email: |  |
Copyright © 2020 The Author(s). Published by Scientific & Academic Publishing.
This work is licensed under the Creative Commons Attribution International License (CC BY).
http://creativecommons.org/licenses/by/4.0/

Abstract
The present study is focused on investigating a potential alternative composite resin for the manufacture of a composite sandwich system with improved mechanical and fire retardant properties for structural applications. Epoxy based resins are commonly used in the automotive, aerospace, defence and space technologies. Epoxy resins are meeting the strength requirements; however, it requires filler additives for improving the flammability behavior. Benzoxazine resin possesses better flammability characteristics than other phenolic resins due to the nature of the formation of a comparable network after polymerization and excellent mechanical properties. This study was mainly focused on comparing the mechanical and flammability characteristics of benzoxazine and epoxy resin based carbon fibre composite sandwich structure that can be suitable for structural applications. For this characterization study, sandwich panels consisting of face sheets (made with bi-directional 2x2 twill of 200 GSM carbon fibers with Anabond® Anazine 1951 hot cured hybrid benzoxazine monomer resin and epoxy grade Lapox B11, based on Bisphenol-A with a low viscosity triethylenetetraamine based hardener) and aluminium honeycomb core bonded with a hot cure epoxy film adhesive have been developed. Mechanical properties such as tensile, flexural, edgewise compression and flatwise compression tests were conducted for both benzoxazine and epoxy resin based CFRP composite sandwich structures. In addition to mechanical testing, flammability characteristics of both benzoxazine and epoxy based composite laminates were conducted for UL94 vertical burning classification test. It is observed from the test results that both mechanical and flammability properties were found to be superior in the case of benzoxazine resin based composite system. Thus, it can be concluded that hybrid benzoxazine resin shall be considered as an alternative resin system for structural applications such as aerospace, automotive and defence systems. The details related to the materials, methods, and test outcomes are discussed in this paper.
Keywords:
Carbonfibre composites, Benzoxazine resin, Epoxy resin, Honeycomb, Sandwich
Cite this paper: G. Gajaraj, Parth Lal, M. Raguraman, Comparison of Mechanical and Flammability Properties of Benzoxazine and Epoxy Resin Based Carbon Fibre Composite Sandwich Structures, International Journal of Composite Materials, Vol. 10 No. 1, 2020, pp. 18-27. doi: 10.5923/j.cmaterials.20201001.03.
1. Introduction
Recent research advancements in lightweight materials have increasingly focused on composite sandwich structures for reducing carbon footprints of the transportation systems including automotive, marine, military, and aerospace and space applications due to its exceptional stiffness to weight ratio, high bending strength to weight ratio, high strength to weight ratio, excellent thermal insulation, resistance to fatigue, impact and blast loads [1,2].Composite sandwich structure consists of two thin face sheets and a core as shown in Figure 1. Face sheets will carry the tensile and compressive stresses in the sandwich which are bonded to the core using adhesives; face sheets are made using aluminium, steel and composites. Composite face sheets are made using glass fibre and carbon fibre with thermoset resins such as epoxy, unsaturated polyester, and vinyl ester. The core of a sandwich structure is responsible for its stiffness, shear resistance and stabilizes the face sheet from buckling and wrinkling; the core is made in the form of foams, honeycomb and corrugated lattice structure in the automotive and aerospace structures. The adhesive used between the core and the face sheet is of critical importance and serves as a medium of load transfer. A strong bond must be capable of resisting the tensile and shear force developed between the face sheet and the core [2]. | Figure 1. Schematic diagram of a sandwich panel |
It is observed from the open literature that many researchers have attempted to investigate various combinations of face sheets and core materials for achieving the required properties suitable for their relevant applications. Wang et al. [3] studied the effect of core thickness and density on the material properties of carbon-epoxy and aluminium honeycomb based composite sandwich structures. It was observed that the material strength could be improved by increasing the thickness and density of the core; an optimum result was achieved for a core density of 101 kg/m3 and a core thickness of 20 mm. Stefan et al. [4] validated the suitability of CFRP materials for application as face sheets of sandwich composites. The mechanical strength of the CFRP face sheet including tensile, flexural and compression was measured and found that the failure occurred by fiber breakage without the occurrence of any dangerous phenomenon such as delamination or fiber/matrix detachment at the interface. Zhang et al. [5] investigated the mechanical response of CFRP tetrahedral lattice truss core sandwich structure fabricated by thermal expansion rubber mould using carbon fibre prepregs by understanding the flatwise compression and the shear behavior. It is seen that the failure of CFRP tetrahedral core panels under shear loading was dominated by the peeling of truss members from the face-sheets rather than the failure of composite truss members. Sezgin et al. [6] investigated the mechanical behaviour of a composite structure fabricated with E-glass fiber/Epoxy facesheet and polypropylene based honeycomb core. It is concluded that the core influences the flatwise compression properties of a sandwich panel. Additionally, the edgewise compression showed that the panel failed under buckling collapse mode which is not the most efficient mode for crash energy absorption. Kandareet al. [7] investigated the fire retardation efficacy of ammonium phosphate carrying glass fibre veil on a sandwich of flax/epoxy laminate and their balsa core. A comparison was made between sandwich structures with and without fire protection and found that the heat release rates at equivalent thermal exposure times were significantly lower for the fire retarded sandwich.Palomba [8] had compared and contrasted single layer and double layer aluminium cores of different grades with aluminium alloy skin to achieve superior properties. It is concluded from this research [8] that a multilayer honeycomb structure with a bigger cell size of 6mm in the bottom and smaller cell size 3mm on the top resulted in uniform compression, that is no localized deformation and reduced displacement on the surface of impact when subjected to low impact velocity tests.The effects of inter-ply stacking sequences on the ballistic and structural performance of ultra-high molecular weight polyethylene fiber/Carbon fiber hybrid composite hard ballistic panels were studied in [9]. High velocity and V50 ballistic impact assessment were conducted for the various configurations of inter-ply sequence. The presence of a stiffer carbon fiber composite layer on the UHMWPE Dyneema® hard ballistic panel on the outside had improved the bending rigidity of the panel. Through a front facing carbon hybrid configuration, a significant reduction and a dramatic improvement in flexural strength were obtained. Hence, during designing of panels involving Dyneema® in ballistic impact and structurally demanding environments, few layers of carbon composite in the outer layers of a hard-ballistic panel can be selected.The impact response of glass fiber reinforced aluminium honeycomb sandwiches was studied by Crupi [10] by bending and low velocity impact tests. The experimental tests have demonstrated that the amount of energy absorption of the honeycomb sandwiches is highly improved reinforcing them utilizing GFRP outer skins, which can be designed according to the application of the sandwich. Wadley [11,12] explored the effect of core topology of projectile penetration in hybrid aluminum/alumina sandwich structures. By comparison to previous findings on the ballistic performance of structures with slip-fit triangular inserts, the combination of the change in the insert shape and the difference in fabrication procedure (slip-fitting vs. shrink fitting) resulted in an increase in ballistic limit from 1050 to 1400 m/s. Furthermore, above the ballistic limits, at an impact velocity of 1600 m/s, the preceding changes lead to a reduction in the ejectavelocity, from about 590 to 125m/s. The change from slip-fitting to shrink fitting alone, demonstrated for chosen topology type, appears to give some improvement, as manifested in a reduction of ejecta velocity from 590 to 420 m/s. Additional benefits are derived from the insert shape changes: the ejecta velocity decreasing with an increasing base width of the inserts, from 420 to 125 m/s. The latter benefits appear to be most pronounced when the base width of the inserts is at least three times the diameter of the projectile.Wines [13] addressed that low velocity, drop weight behavior of small (100 mm by 100 mm) sandwich panels with CFRP skins. The main point of interest is the core material, and the focus of the paper is in the use of body centered cubic (BCC) micro lattice cores made from Ti6Al4V titanium alloy and 316L stainless steel manufactured using selective laser melting. The mechanical behavior of the micro lattice core is compared to that of conventional aluminium honeycomb. The paper discusses the manufacture and characterization of the core materials, the measurement of core properties from strut tensile tests, block compression tests and the drop weight impact performance of the panels. Impact performance is expressed in terms of panel penetration. It is observed that Ti6Al4V BCC micro lattice structures can compete with aluminium honeycomb from the point of view of Foreign Object Impact (FOI) performance in aerospace sandwich panels. Jamil [14] has numerically simulated and experimentally tested and validated the blast response of polyether grade thermoplastic polyurethane sandwich core with aluminium alloy 2024-T3 skins which were used as facings to enhance the blast resistance of sandwich structures with thermoplastic polyurethane cores and varying thicknesses. It is concluded that an increase in the blast resistance relative to the plain 5mm thermoplastic polyurethane of 14.0, 23.8 and 71.2% was observed with the addition of AA 2024-T3 skins and increases in the core thicknesses of 5, 10 and 20 mm, respectively.Amongst all, composite sandwich panels showed promising capabilities predominantly on the weight, strength and stiffness behavior of the materials specifically for impact, blast and fatigue responses [1-15]. However, several issues are to be addressed including flame retardancy, cost of materials, manufacture and, delamination characteristics under extreme loading conditions. It is also observed that the addition of flame retardant additives results in deterioration of mechanical strength. Therefore, the selection of material for individual constituents such as fibres, resin and bond adhesives must be made with careful consideration to achieve the desired properties including tensile and flexural strength, fire retardancy, impact response and corrosion.Therefore, this study essentially focuses on comparing the mechanical and flammability characteristics of hybrid benzoxazine and epoxy resin based carbon fibre composite systems to verify its suitability for structural applications. Face sheets were fabricated using bi-directional 2x2 (200 GSM) carbon fibre twill with Anabond® Anazine 1951 hot cured hybrid benzoxazine monomer resin and also with epoxy grade Lapox B11, based on Bisphenol-A with a low viscosity triethylenetetraamine based hardener. Aluminium honeycomb core with a density of 82kg/mᶾ, foil thickness of 70µm and a cell diameter of 6 mm were selected. Anabond® EFA 960 film adhesive was placed between the developed face sheets and honeycomb to form the composite sandwich structure. Three samples for each test was prepared and tested according to their respective ASTM standards. The test results are summarized and compared between composite sandwich systems based on benzoxazine and epoxy resins. The test results indicated that mechanical and flammability properties are greater in the case of benzoxazine resin based composite sandwich system. It can be concluded that hybrid benzoxazine resin shall be considered as a prospective alternative resin system for high-end structural applications such as aerospace, automotive and defence systems.
2. Materials
Composite sandwich structures comprise of fibre, resin, core structure and bond adhesives. The details of all the constituents of composite sandwich system are discussed in this section.
2.1. Fibre
Bi-directional 2x2 twill carbon fiber (200 GSM) has been selected for this study. 2x2 twill weave has a very good bi-directional property that means it has same mechanical property in both x and y direction; also the orientation between layers will not affect the property of the laminate whereas, in case of unidirectional fiber, layup and the direction of fiber orientations plays a critical role in the mechanical property which may further complicate the deciding criteria. 2x2 twill is one of the widely used weave patterns in many aerospace and defence industries. This bi-directional 2x2 carbon fiber twill supplied by M/s. BhorForce®TC200, was employed to lay-up composite laminates as reinforcing agents with tensile strength and tensile modulus of 4000MPa and 240GPa respectively. Its density, filament diameter and elongation were observed as 1.8g/cm³, 7µm, and 1.7% respectively.
2.2. Benzoxazine Resin
A commercial grade of hybrid benzoxazine, Anabond® Anazine 1951-hot cured hybrid benzoxazine monomer resin based on Bisphenol-F and Phenol was employed in this study. Table 1 shows the properties of the uncured resin. This thermoset resin can polymerize on heating to 200°C to give good thermal resistance and high mechanical strength properties. This resin has good processability with nil volatiles and near-zero volume change during cure; it has also got fire, smoke and toxicity property and has no water absorption. The flammability characteristics of benzoxazine are very similar to the phenolic resins due to the formation of a comparable network created after polymerization [R].Table 1. Properties of Anabond® Anazine 1951 resin 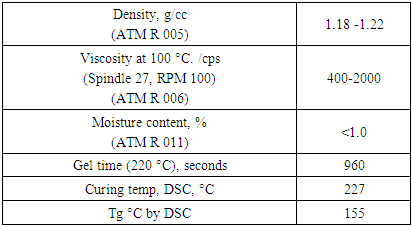 |
| |
|
2.3. Epoxy Resin
A commercial grade of liquid epoxy of medium viscosity, Lapox B11, based on Bisphenol-A with a low viscosity triethylenetetraamine based hardener (TETA, curing agent) was employed for this investigation. Table 2 shows the properties of the uncured epoxy resin. This thermoset resin with the appropriate curing agent can provide an excellent combination of mechanical, thermal, chemical and other physical properties.Table 2. Properties of Lapox B11 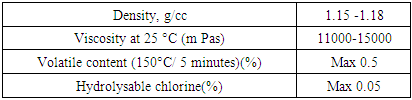 |
| |
|
2.4. Honeycomb
The function of a core is to support the thin skins so that the structure does not buckle (deform) inwardly or outwardly and to keep the sandwich components in relative position to each other. To accomplish this, the core must have several important characteristics. It has to be stiff enough to keep the distance between the faces constant. It must also be rigid in shear such that the faces do not slide over each other. The shear rigidity forces the faces to cooperate with each other. If the core is weak in shear, the faces will not cooperate and the sandwich will lose its stiffness. It is the sandwich structure as a whole that gives positive effects. However, it should be mentioned that the core has to fulfill the most complex demands. Strength in different directions and low density are not the only properties that the core has to have. Often, there are special demands for buckling, insulation, absorption of moisture, and ageing resistance, etc. The core can be made of a variety of materials, such as wood, aluminum, and a variety of foams. A honeycomb structure as the name suggests resembles a honeycomb with hexagonal cells and each honeycomb core is characterized by its cell size, foil thickness and density. Aluminium honeycomb was selected as the core material for our investigation with a density of 82kg/m3, foil thickness of 70µm and a cell diameter of 6 mm.
2.5. Adhesive
It is important to note that to keep the faces and the core co-operating with each other, the adhesive between the faces and the core must be able to transfer the shear forces between them. The adhesive must be able to carry shear and tensile stresses. It is hard to specify the demands on the joints. A simple rule is that the bond adhesive should be able to take up the same shear stress as the core. Anabond® EFA 960 film adhesive has been used to bond the carbon fiber laminates with aluminium honeycomb core structure.
3. Method of Manufacture
3.1. CFRP Face Sheets
Face sheets are very important components of the sandwich structure due to its capability to share the tensile and compressive stresses induced in the sandwich. The local flexural rigidity is so small that it can often be ignored. Conventional materials such as steel, stainless steel and aluminum are often used for face sheet material. In many cases, it is also suitable to choose carbon fibre or glass fibre reinforced plastics as face materials. Fibre reinforced plastics can be tailored to fulfill a range of demands including anisotropic mechanical properties, freedom of design and excellent surface finish. Composite skins such as CFRP and GFRP rely on the type of fibre, reinforcement and the lay-up scheme used.For this study, the amount of resin requirement was chosen as 60:40 fibre-resin volume ratios as advised by M/s. Anabond, India who is the supplier of the hybrid benzoxazine resin (Trade name as Anabond® Anazine 1951) and a similar ratio was chosen for epoxy resin for comparative research. Benzoxazine resin is supplied in a solid form by Anabond; it is initially diluted by adding acetone for better application and wettability onto the fibre and then the prepreg is kept in an oven at around 80ºC for evaporation of the acetone solvent that enables the composite to dry fast.The selected carbon fibre cloth (bi-directional 2x2 twill of 200 GSM) was used for making a five-layered laminate and cut for a dimensional requirement of 165 mm x 165 mm that weighed 50g as shown in Figure 2. The amount of resin required for each laminate was computed based on a 60:40 fibre-volume ratio and then it was diluted by adding enough acetone solvent to increase the viscosity for better wettability and uniform application of the resin onto the fibre as shown in Figure 3. The evaporation of the solvent in the fibre resin system was carried out by keeping the wet laminate into an oven at 80ºC for 30 mins. Constant contact pressure of about 20 kg/cm² was applied at room temperature for 5 mins using a hot press to ensure the stacked prepreg are tightly aligned and formed. Curing cycle starts with heating the laminate in an incremental manner to 160ºC as given in Table 3 whilst constant pressure of 20kg/cm2 is applied and then the laminate was kept in the oven at 200ºC for 2 hours for post-curing. The final CFRP laminate manufactured using this process is as shown in Figure 3(b).Table 3. Temperature increments in the hot pressing of laminate  |
| |
|
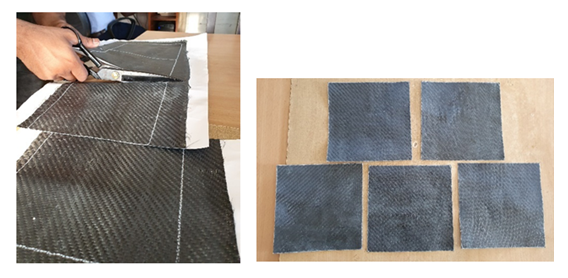 | Figure 2. Cut bi-directional 2x2 carbon twill with dimensions 165mm x 165mm |
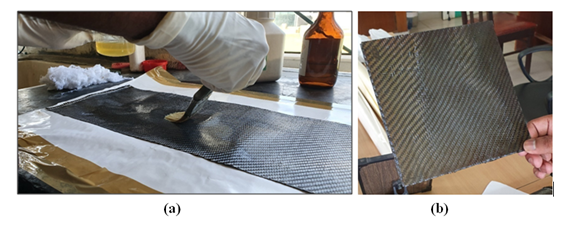 | Figure 3. (a) Application of diluted benzoxazine resin onto carbon fibre cloth and (b) final laminate |
A similar approach was followed for the preparation of epoxy based CFRP face sheets. Again, a 60:40 fibre-resin volume ratio was chosen following the benzoxazine based face sheets for comparison. The hardener was mixed with the epoxy resin homogeneously in a stoichiometric ratio of 100:13 (w/w). The mould was cleaned thoroughly and mould release wax was applied on the mould. The resin mix was then uniformly applied onto the fibre and stacked up to 5 layers. Once stacked, the mould was closed and the composite was left toinitially cure at room temperature under constant pressure of 20kg/cm2 for 1 hour and later subjected to a post curing temperature of 80°C for 5 hours.
3.2. Aluminium Honeycomb Sandwich
CFRP face sheets have to be manufactured using the process outlined in section 3.1. One of the sides of the face sheets was rubbed with sandpaper to ensure better bonding with honeycomb. A cut of the film adhesive of the same dimensional size(Anabond® EFA 960) was placed between face sheet and honeycomb for making the sandwiched structure and then a uniform load of 50kg was applied on top of the sandwich structure using a hot press with a cure schedule of 175 ± 5ºC for 1 hour ±15 mins with a heating rate of 1.2ºC/min. The manufactured sandwich structure is now ready for testing as shown in Figure 4.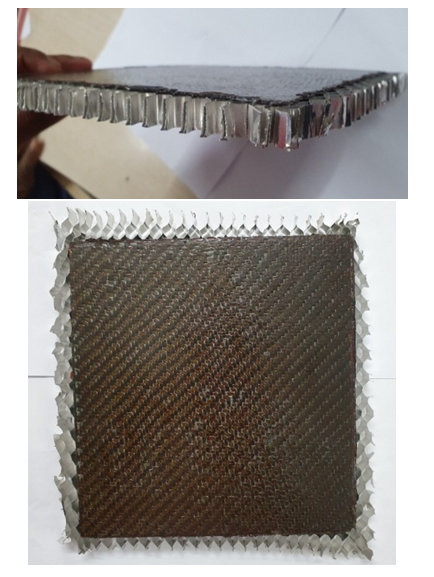 | Figure 4. Prepared sandwich panel |
4. ASTM Test Standards and Experiments
The specimens were tested by following ASTM standard D 3039 for tensile properties, ASTM D7264 for flexural properties. The specimens were water-jet cut from the panels parallel to the x-axial direction (based on the first layer). The dimensions of the tensile test specimen were 200x20 mm² and the dimensions of the flexural test specimen were 120x12 mm². Tensile and bending tests were conducted using a Universal Testing Machine (Shimadzu), with a constant crosshead speed of 1.3mm/min and 1mm/min respectively. The sandwich panel was tested by following ASTM C364 for the edgewise compression test and ASTM C365 for flatwise compression. The dimensions of edgewise compression and flatwise compression test specimens were 80mm x 80mm and conducted with a constant crosshead speed of 0.5mm/min. Three replicate samples were tested for each test. The average tensile, flexural, edgewise compression, and flatwise compression properties were determined for all the test cases. Additionally, the UL94 flammability classification test was performed and the fire retardance behaviours of the samples were measured.
4.1. Tensile Test
The tensile test was performed under ASTM D3039 standard which is suitable for polymer matrix composites. This test method has been designed to produce tensile property data for material specifications and structural design and analysis. The cut samples for testing areas shown in Figure 5. The tensile tests were conducted by applying a constant strain rate of 1.3mm/min as given in the standard. Three different samples were made and tested as listed in Table 4. Tensile strength between these three cases was compared. It is noted from this table that there has been a 49% strength increase in 5 layer configuration compared to 3 layer configurations; 18% strength increase was observed in 8 layer configuration compared to 5 layer configuration. However, a smaller thickness increase was observed for 5 layer configurationand possessed excellent tensile strength. In addition, 5 layer configurations were manufactured with epoxy resin and the tensile test was conducted as described above. The 5 layer epoxy resin based CFRP samples exhibited a tensile strength of 366.79 MPa, much lesser than the strength displayed by the benzoxazine resin based samples as indicated in Table 4. The tensile strength of epoxy based composite laminate has been validated and confirmed with observations in [16]. It can be concluded that the benzoxazine resin based samples exhibited superior tensile strength compared to epoxy- based composites. The snap-shot of the testing process and the post-mortem report of the test samples are shown in Figures 6 and 7. DGM (Delamination at Gauge Middle) and LIT (Lateral Inside Grip Top) stand for delamination at gauge middle and lateral inside grip top respectively.Table 4. Tensile test results 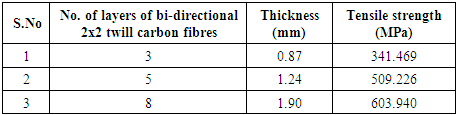 |
| |
|
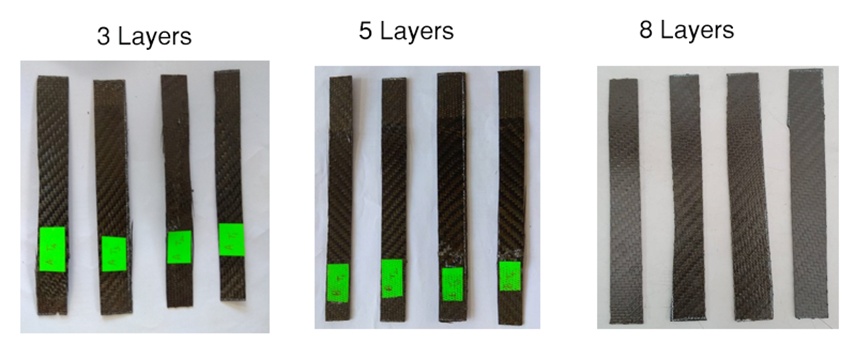 | Figure 5. ASTM D3039 tensile test specimen samples |
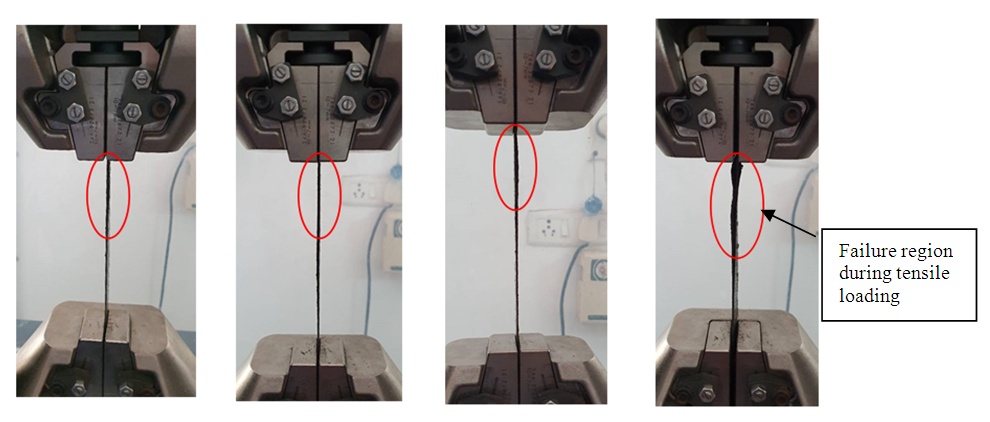 | Figure 6. Progressive failure of tensile sample |
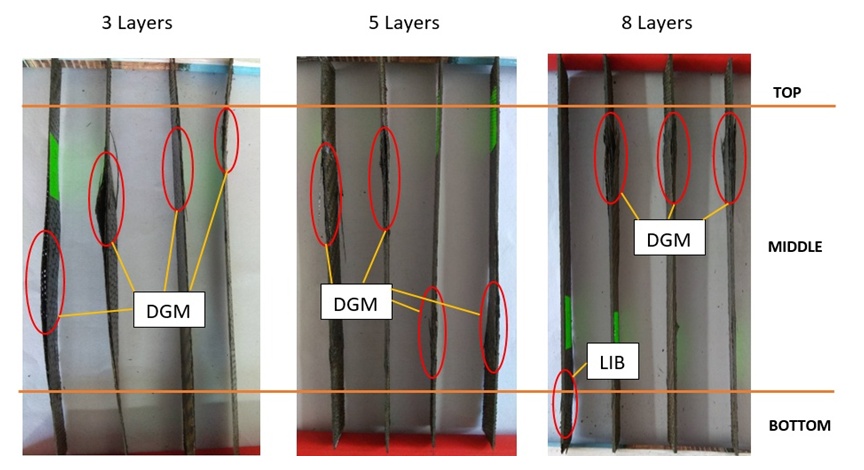 | Figure 7. Failed tensile samples |
4.2. Flexural Test
The flexural test was performed under ASTM D7264 standard which is suitable for polymer matrix composites. This test method has been designed for optimal use with the continuous-fibre-reinforced polymer matrix and differs from other flexural methods like D790 and D6276, which includes the chance in span-to-thickness of 32:1 in D7264 whereas other two methods use 16:1. The cut samples for flexural testing for testing areas shown in Figure 8. Samples were cut for three different thicknesses and tested as given in Table 5. The loading noses and supports shall have cylindrical contact surfaces of radius 3mm [0.125in], with a hardness of 60 to 62 HRC, as specified in Test Methods E18, and shall have fine ground surfaces free of indentation and burrs with all sharp edges relieved. The speed of the crosshead movement for the testing was set to 1mm/min [0.05in/min] for the specimen with standard dimensions. The span must be measured accurately to the nearest 0.1mm [0.004in] for spans less than 63mm [2.5in] and the nearest 0.3mm [0.012in] for spans greater than or equal to 63mm [2.5in].Table 5. Flexural test results 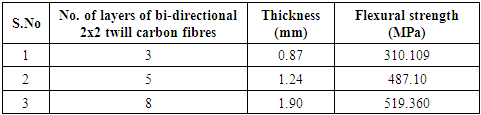 |
| |
|
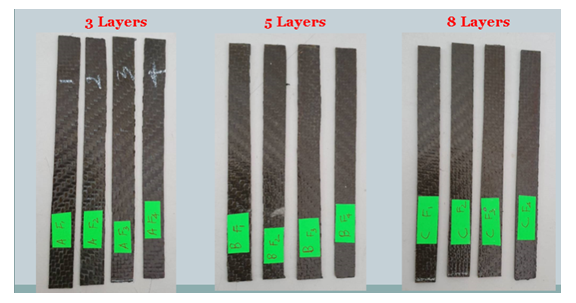 | Figure 8. Cut flexural test specimens for testing |
The results obtained from the tests are listed in Table 5. It is noted from this table that about 57% increase in flexural strength was observed from 3 layers to 5 layer configuration and a6% increase for 5 layers to 8 layer configuration. 5 layer epoxy based CFRP samples on the other hand exhibited a flexural strength of 640 MPa, similar to the results shown in [16], which is greater than benzoxazine based samples.
4.3. Edgewise Compression Test
The edgewise compression test is generally performed under the ASTM C364 standard for polymer matrix composites. The edgewise compressive strength of short sandwich construction specimens provides a basis for judging the load carrying capacity of the construction in terms of developed facing stress. This test method provides a standard method of obtaining sandwich edgewise compressive strengths for panel design properties, material specifications, research and development applications, and quality assurance. As per ASTM C364 standard, the test specimen shall be a core or of sandwich construction and shall be of square circular cross-section having a minimum area of cross-section as per various core types:• For continuous cores, such as balsa wood and foams, the minimum cross-sectional area shall be 625mm2 (1in2).• For open-celled cores, such as honeycomb, having cells less than 6mm (0.5in) the minimum cross-sectional area shall be 2580mm2 (4in2 ) and for cells 6mm (0.5in) or greater the minimum cross-sectional area shall be 5800mm2 (9in2).The cut specimens as shown in Figure 9 and were placed on the UTM machine bed. The load was applied to the specimen through a spherical loading block which was suspended and self-aligned for better uniform distribution of load as possible over the entire loading surface of the specimen. The load was applied at a constant rate of movement of the cross-head of 0.50mm/min (0.020 in/min) and at such a rate that the maximum load will occur between 3 and 6 min. The total thickness of the sandwich panel was measured as 14mm that exhibited 14.56MPa edgewise compression strength. Delamination and shear mode failure was observed during the edgewise compression as shown in Figure 10; this delamination was assessed to be in the acceptable range for structural applications as stated in ASTM C364 [17]. Epoxy based sandwich panel on the other hand displayed a strength of only3.43MPa. It can be concluded that benzoxazine based sandwich structures are much stronger than epoxy based sandwich panels in terms of its edgewise compression strength.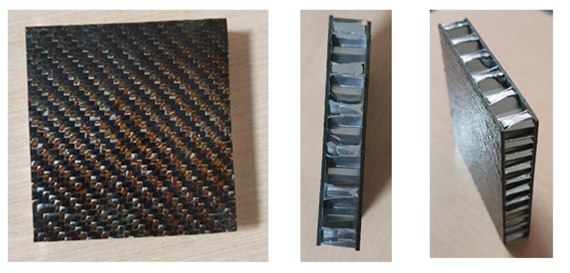 | Figure 9. Edgewise compression test samples |
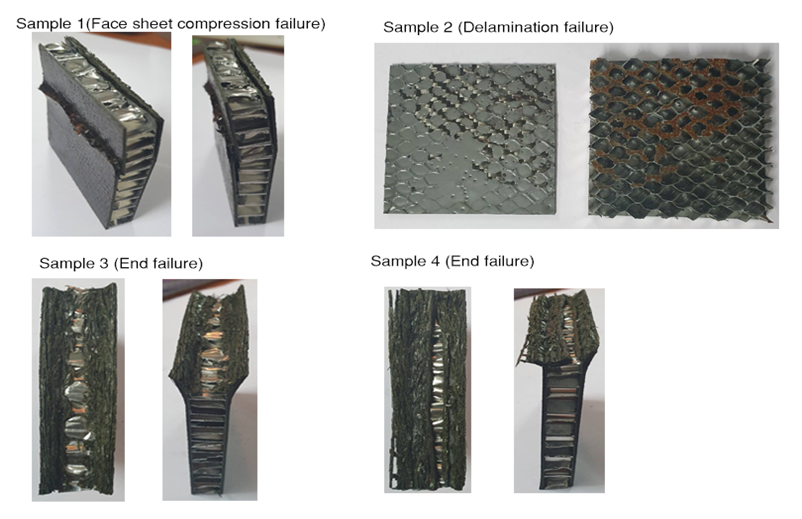 | Figure 10. Edgewise compression test failed samples |
4.4. Flatwise Compression Test
The flatwise compression test is generally performed under the ASTM C365 standard for polymer matrix composites. The flatwise compression strength is a fundamental mechanical property of sandwich cores used in the construction of sandwich panels. This test method provides a standard for obtaining sandwich flatwise compressive strengths for panel design properties, material specifications, research and development applications, and quality assurance.The cut specimen as shown in Figure 11 was placed on the UTM machine bed. The load was applied at a constant rate of movement of the cross-head of 0.50mm/min (0.020 in/min). The benzoxazine based CFRP panels exhibited a flatwise compression strength of 5.52 MPa. Core crumpling/crushing was observed during the flatwise compression as shown in Figure 12. In comparison, epoxy based sandwich panel displayed a strength of 5.42MPa which was very close and consistent with the conclusion made in [6], that is the flatwise compression property is influenced by the core of the sandwich structure. 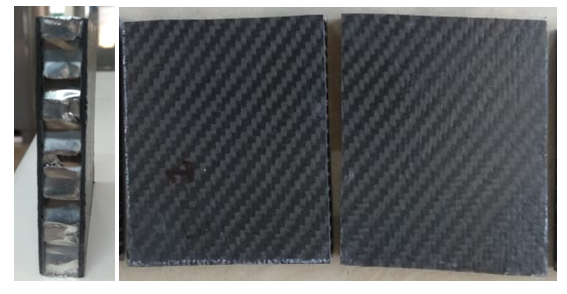 | Figure 11. Flatwise compression test samples |
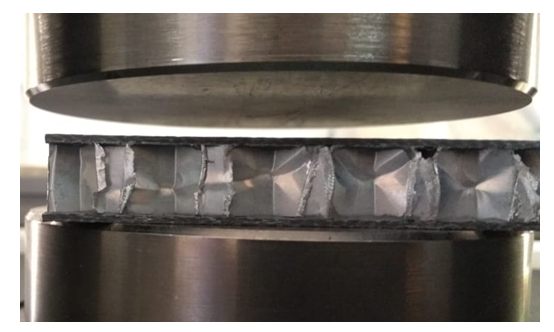 | Figure 12. Flatwise compression test ready for testing |
4.5. Flammability Test
Flammability of the composite system should be evaluated by conducting tests as per UL-94 standards. UL-94 is a standard for the safety of the flammability of plastic material in devices and appliances. This standard determines the materials tendency to either extinguish or spread the flame once the specimen is ignited. Ratings, V0, V1 and V2 indicate that the material has to be tested in a vertical position and self-extinguished within a specified time after the ignition source was removed as per details given in Table 6. The vertical ratings also indicate whether the test specimen dripped flaming particles that ignited a cotton indicator located below the sample. The after flame time, t1 indicates the time taken by the sample to self-extinguish after the first flame application. Immediately after the flame ceases, the burner is again placed for the second flame application for the specified time and the after flame time, t2 is calculated.Table 6. Flammability classification criteria 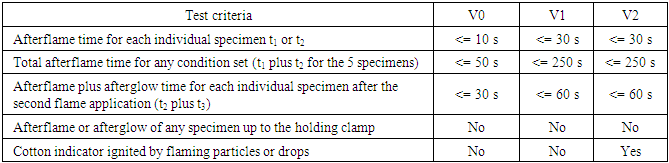 |
| |
|
The specimen shall be clamped from the upper 6mm of the specimen, with the longitudinal axis vertical, so that the lower end of the specimen is 300 ± 10 mm above the horizontal layer. The methane gas supply to the burner is adjusted to produce a gas flow rate of 105ml/min with a back pressure of less than 10mm of water. The burner shall then be adjusted to produce a blue flame 20 ± 1 mm high. The flame has applied centrally to the middle point of the bottom edge of the specimen so that the top of the burner has 10 ± 1 mm below the point of the lower end of the specimen, and has maintained at that distance for 10 ± 0.5 seconds. If the specimen drips molten or flaming material during the flame application, the burner should be tilted to an angle of 45° and withdrawn just sufficiently from beneath the specimen to prevent the material from dripping into the barrel while maintaining the 10 ± 1 mm spacing. After the application of the flame to the specimen for 10 ± 0.5 seconds, the burner has to be immediately withdrawn at a rate of approximately 300mm/sec, to a distance of at least 150mm from the specimen and simultaneously the after flame time, t1 shall be measured in seconds. As soon as the after flaming of the specimen ceases, the burner has to be placed immediately again and the same procedure is to be followed to measure the after flame time, t2.All specimens were cut from a sheet material, or molded to the necessary form. After the cutting operation, care must be taken to remove all the dust particles from the surface of the specimen and the cut edges are to have a smooth finish. Standard bar specimens were cut for a dimension of 125 ± 0.5 mm wide with maximum thickness not exceeding 13mm andradius of corners is not to exceed 1.3mm. The cut samples for the flammability test are as shown in Figure 13. A total of 10 specimens were tested using the facility available at CIPET, Chennai (Govt. of India organization for testing of materials and polymers). Five samples were tested after conditioning for 48hours at 23°C and 50% RH. The experimental observations are recorded in Table 7. It is noted from this table that each individual test samples showed an after flame time way below the permissible UL94 V0 classification. The summed total afterflame time, t1 and t2 have been recorded as 9 and 14 seconds respectively which is less than UL94 V0 classification criteria and no flaming particle drips were observed. On the other hand, epoxy showed unsatisfactory results and the specimen burned up to the handle. Table 7. After flame time from the Bunsen burner test 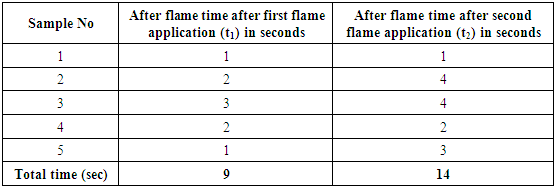 |
| |
|
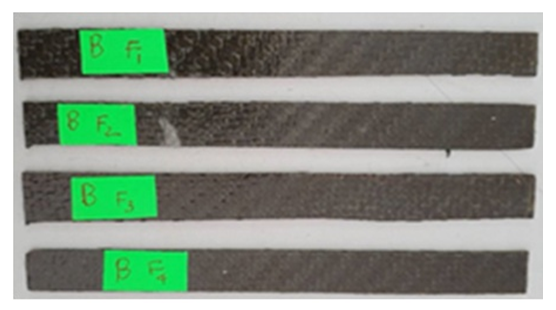 | Figure 13. Cut CFRP samples for UL94 fire retardant test |
5. Conclusions
This study presented the mechanical and flammability properties of the CFRP composite structure manufactured using hybrid benzoxazine and epoxy resins. Samples were manufactured for three different thicknesses by varying the number of layers of bi-directional 2x2 twill carbon fibres. Tensile, flexural, edgewise compression and flatwise compression tests were conducted using relevant ASTM standards for mechanical property characterization and UL-94 vertical burning standard for flammability classification for both benzoxazine and epoxy resin based composite laminates and sandwich structures. It was observed that benzoxazine based face sheets showed a 38.8% improvement in its tensile strength while its flexural strength was not at par with the epoxy based face sheets. Mechanical tests on the sandwich panel as a whole, including edgewise compression and flatwise compression displayed outstanding results in favour of benzoxazine based CFRP panels. It can be concluded from the mechanical tests that benzoxazine based sandwich panels can offer better mechanical strength and energy absorption characteristics for highly demanding structural applications. Additionally and most importantly, the flammability test of the benzoxazine resin based composite system qualifies the UL-94 V0 classification, the highest level of flame retardancy as per UL-94 standard. Therefore, benzoxazine resin presents a superior alternative to the commonly used epoxy for lightweight sandwich structure, where high strength mechanical properties and UL-94 V0 flammability classification are considered essential for engineering structural applications.
References
[1] | DanZenkert, (1997), “The Handbook of Sandwich Construction”, 1st Edition, Engineering Materials Advisory Services, pp. 3-26. |
[2] | Sohel Rana and Raul Fangueiro, (2016), “Advanced Composite Materials for Aerospace Engineering: Processing, Properties and Applications”, 1st Edition, Woodhead Publications, pp. 129-137. |
[3] | Wang et al. (2017), “Strength, Stiffness, and Panel Peeling Strength of Carbon Fiber-Reinforced Composite Sandwich Structures with Aluminum Honeycomb Cores for vehicle body”, Composite Structures, vol. 184, pp. 1189-1196. |
[4] | Stefan et al. (2017), “Mechanical testing of CFRP materials for application as skins of sandwich composites”, vol. 9, pp. 97-104. |
[5] | Zhang et al. (2012), “Mechanical behaviour of CFRP sandwich structures with tetrahedral latticetruss cores”, Composites: Part B, vol. 43, pp. 471-476. |
[6] | Sergin et al. (2009), “Mechanical Behavior of Polypropylene-based Honeycomb-Core Composite Sandwich Structures”, Journal of Reinforced Plastics and Composites, vol. 29, pp. 1569-1579. |
[7] | Kandare et al. (2014), “Fire reaction properties of flax/epoxy laminates and their balsa-core sandwich composites with or without fire protection”, Composites Part B Engineering, vol. 56, pp. 602-610. |
[8] | Palomba et al. (2018), “Single and double-layer honeycomb sandwich panels under impact loading”, International Journal of Impact Engineering, vol. 121, pp.77-90. |
[9] | Zulkifli et al. (2019), “Strategic positioning of carbon fiber layers in an UHMWPE ballistic hybrid composite panel”, International Journal of Impact Engineering, vol. 129, pp. 119-127. |
[10] | Crupi et al. (2016), “Theoretical and experimental analysis for the impact response of glass fibre reinforced aluminium honeycomb sandwiches”, Journal of sandwich structures and materials, vol. 20, pp.1-28. |
[11] | Wadley et al. (2013), “Impact response of aluminum corrugated core sandwich panels”, International Journal of Impact Engineering, vol. 62, pp. 114-128. |
[12] | Wadley et al. (2013), “Effect of core topology on projectile penetration in hybrid aluminum/alumina sandwich structures”, International Journal of Impact Engineering, vol. 62, pp. 99-113. |
[13] | Mines et al. (2013), “Drop weight impact behavior of sandwich panels with metallic micro lattice cores”, International Journal of Impact Engineering, vol. 60, pp. 120-132. |
[14] | Jamil et al. (2019), “Blast response of aluminium/thermoplastic polyurethane sandwich panels - experimental work and numerical analysis”, International Journal of Impact Engineering, vol. 127, pp. 31-40. |
[15] | Hatsuo Ishida, (2011), “Handbook of Benzoxazine Resins”, 1st Edition, Elsevier, pp. 605-608. |
[16] | Rahmani et al. (2014), “Mechanical performance of epoxy/carbon fibre laminated composites”, Journal of Reinforced Plastics and Composites, vol. 33, pp. 733-740. |
[17] | ASTM C364 / C364M-16, (2016), Standard test method for edgewise compressive strength of sandwich constructions, ASTM International, West Conshohocken, PA, www.astm.org. |