Taiser Attia
Design and Production Engineering Department, Faculty of Engineering, Ain Shams University, Cairo, Egypt
Correspondence to: Taiser Attia, Design and Production Engineering Department, Faculty of Engineering, Ain Shams University, Cairo, Egypt.
Email: |  |
Copyright © 2019 The Author(s). Published by Scientific & Academic Publishing.
This work is licensed under the Creative Commons Attribution International License (CC BY).
http://creativecommons.org/licenses/by/4.0/

Abstract
Plastic disposal affects wildlife, food chain, groundwater, and air quality. Nowadays, people are more aware about the harmful effects of plastic waste. One of the most promising solutions is bioplastics. Bioplastics seem an attractive Eco-friendly alternative since they can easily degrade under certain conditions. Linear low-density polyethylene is loaded with 10, 20 and 30 weight % of fibers. Fibers are alkalinized, neutralized and then dried. The added amount of maleic anhydride grafted polypropylene coupling agent has a constant ratio of 6.7% in terms of the natural fibers. 3 wt.% of ferric stearate as prominent oxo-biodegradation agent is added as well. Up to 24 wt% ammonium polyphosphate is added as fire retardant constituent. Twenty-eight experiments are planned statistically. Mixing is carried out mechanically in a kneader at 180°C. Tests of ISO 527, 179, UL94 and ASTM D-578-90 are carried on the samples to investigate the mechanical properties, impact strength, flame retardance and water absorption behavior of the compounds after being shredded and molded into standard samples. The results show that the jute has better behavior on the mechanical properties as well as reduced water absorption with respect to the other fibers. Presence of flame retardance was superior for the corn silk composites but on the other hand they have high water absorption values. Jute composites show the least temperature to lose 5% weight, flame retardant addition cause slight increase in thermal stability, while long sugar cane fibers show the best thermal stability.
Keywords:
Natural fiber, Polyethylene fiber composites, Flame retardance, Thermoplastic composites
Cite this paper: Taiser Attia, Natural Fiber Thermoplastic Composites with Biodegradant and Fire Retardant Additives, International Journal of Composite Materials, Vol. 9 No. 1, 2019, pp. 24-31. doi: 10.5923/j.cmaterials.20190901.04.
1. Introduction
Nowadays, more than 35 million tons of wastes deriving from different plastic products are produced each year in the world and only 7% of them are recycled, the remaining waste being deposited in the landfills or dispersed in the oceans [1]. The global market for biodegradable bioplastics, produced based on renewable resources, has grown from a small base of 262,000 tons in 2007 to 505,000 tons in 2009 and is set to reach 885,000 tons by 2011. The forecast of the world market for biodegradable plastics would grow by more than 20% per year [2].On the other hand, natural fiber thermoplastic composites (NFTCs) are characterized by attractive features such as high availability, carbon neutrality, and relatively good specific strength and stiffness. In addition, they are compatible with normal polymer compounding machines [3-4]. However, most of the research about NFTCs work with non-biodegradable polyolefins [3] or biodegradable thermoplastics with less commercial impact as PLA [5]. Production of biodegradable NFTCs with other additional properties such as flame retardance would give a new spectrum for applications in construction profiles or bulky electric industries. The candidate fibers in this work are three types of locally produced fibers in Egypt. Jute, bast fiber, is selected as benchmark fiber with respect to the other two fibers, because they are numerously reported in literature [1-3]. Bagasse fibers out of sugarcanes are bi-products of the sugar industry which are mainly burned as fuel in sugar mill boilers [6]. They are characterized with their low cost, low density and acceptable mechanical properties so that they are candidate for reinforcing other thermoplastics. Corn silk fibers are also abundant found in the Egyptian local market. They are extracted from the corn petals by means of retting and hand stripping process [7].
2. Experimental Work
The experimental work was divided into four stages. The first stage involved the preparation of all fiber species with the required aspect ratios, preparation of maleic anhydride polyethylene and the rest of materials including ferric stearate, ammonium polyphosphate, and high-density polyethylene. The second stage was mixing all previous components to make sure that the ingredients of each experiment within the plan have appropriate homogeneity. The third stage was using the injection machine to get the required sample shape for each test. The last stage was testing the mechanical physical and chemical properties of each sample using tension, impact, water absorption and thermal gravimetric analysis TGA tests. First stage of preparing the NFTC samples is as following:
2.1. Natural Fibers
Jute are used as chopped lengths of (20mm-10mm-5mm). Bagasse fibres are used with working average lengths of (long 14mm-meduim 8 mm-short 0.4mm). Corn silk fibres of working average lengths are (long 9 mm-meduim 5mm-short 2 mm).
2.2. Polyethylene and Additives
Linear low density polyethylene is was supplied by ExxonMobil company, Qatar. Fire retardant ammonium polyphosphates AP (16%-18%-20%-22%-24%) [6] are added. Maleic anhydride compatibilizer MAPP was prepared by mixing PP with MA in a weight ratio of 98:2, and then 1% of peroxide was added, the mixture is blended using mechanical mixture [6]. 3 wt% Ferric stearate was added as pro-oxidant to the polyethylene.
2.3. Mixing
The polymer was put at the container till it is completely melted. MAPP is added in 1:10 ratio with fibres [7]. 3 wt.% of ferric stearate, as pro-oxidant, is then added in selected samples. Ammonium polyphosphate as flame retardant is then added. Finally, the fiber is added gradually and the blending continues for 7 minutes. Then the blend is dried and shreddered for further processing.Injection molding of the compounded pellets into dog-bone samples was carried out using a Fu Chun Shin Machinery FT-60 injection-molding machine. The screw diameter is 28mm. Injection rate was 60 cm3/s. Screw speed 210 rpm, for all samples. The temperature pattern was 160°C, 170°C, 180°C from input to output zones. Injection and holding pressure were 70 and 60 bar.
2.4. Samples are Made for the Tests as follows
2.4.1. Tension Tests
Tension tests were made with 5 samples according to DIN EN ISO 527-1 at 2 mm/min, 5 mm/min testing rate. Test sample is injection according to ISO 527-2. Modulus of elasticity is calculated as the slope of stress strain curve at the recommended strains (0.0005-0.0025 mm/mm) according to ISO 527-1.
2.4.2. Impact Test
Samples are tested according ISO 179-1:2010(E). Impact tests were made with 7 samples using a hammer load of 5J with Charpy and Izod impact machine XJJU-15J.Using statistical analysis JMP program. JMP is a statistical software to elimnate the number of samples test, as welll as to choose the most effectuve ranges. The program gives 28 samples to be made for the given parameters and they are as shown in Table 1. Fiber type is considered as categorial parameter while polyethylene content %, flame retardant %, fibre length are considered continuous parameters.Table 1. Design-of-experiments plan [8] 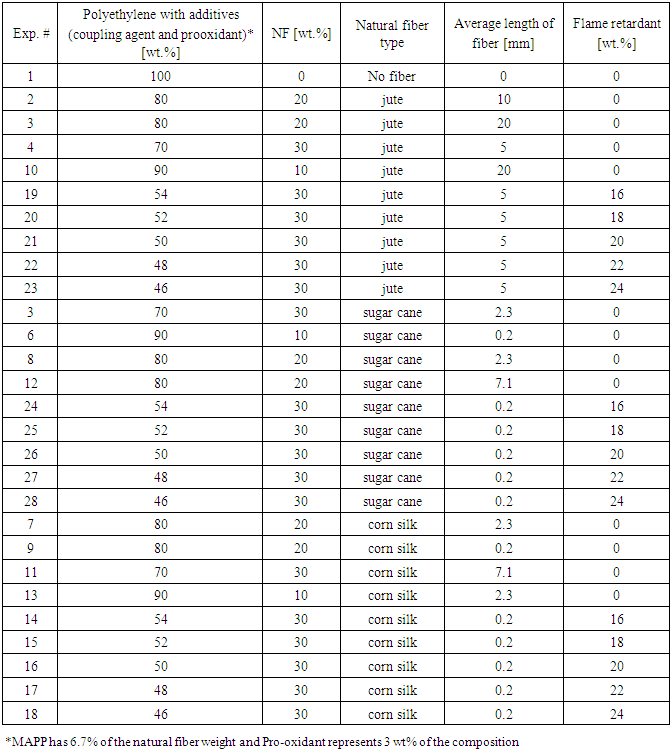 |
| |
|
2.4.3. UL94 Flame Retardance Test
The UL 94HB test describes the Horizontal Burn method. Method 94V is used for Vertical Burn, which is more stringent test than UL 94HB. The test uses a 152 x 9.88 x 3 mm3 specimen cut from the tension sample to these dimensions. For the HB test, the sample is held at one end in a horizontal position with marks at 1" from the free ends, and marks in between spaced by 1cm. A flame is applied to the free end for 30 seconds or until the flame front reaches the first mark. If combustion continues the duration is timed between the first and the last mark. If combustion stops before the last mark, the time of combustion and the damaged length between the two marks are recorded. A set of five specimens are tested. If the burning speed is slow (>75 mm/min), then UL94V test is tried. Burner flame is applied to the free end of the specimen for two 10 second intervals separated by 30 seconds after the first application. The following are recorded for each specimen. If there are drops, then it is designated as V2. If not, then it is V1. If the separation interval time is just 10 seconds and no drops occur, then the designation is V0.
2.4.4. Water Absorption Test
The sample dimensions are 76.2 x 25.4 x 3.2 mm3 according to ASTM D 570 – 98. Specimens were dried in an oven for 24 h at 50±3°C, cooled in a desiccator, and immediately weighed to the nearest 0.001g. The sample is left for a one-half-hour boiling water immersion. Water is then removed with a dry cloth and the specimens is weighed to the nearest 0.001 g immediately. The percentage increase in weight during immersion, is calculated to the nearest 0.01% as follows | (1) |
3. Results and Discussion
Table 2 illustrates the mechanical, water absorption and flame retardance properties of the samples in the plan of Table 1. The next sections discuss in detail the findings out of each test.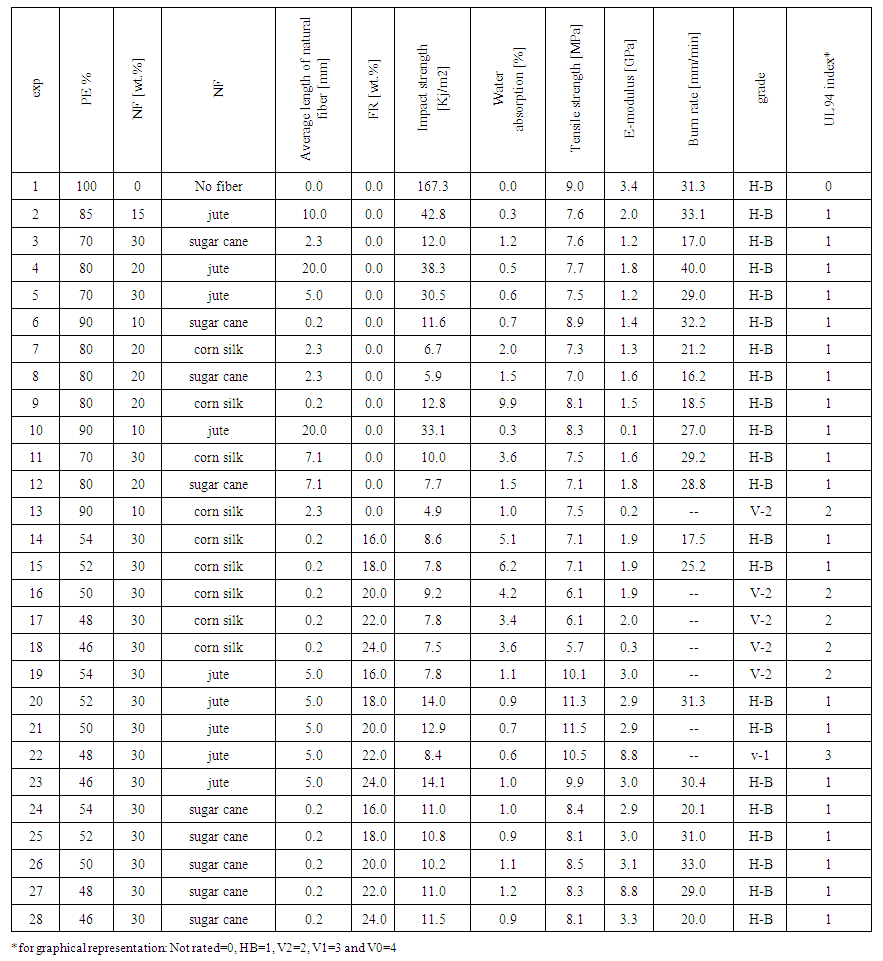 | Table 2. Shows the tensile test and the elsticity results for all samples. [8] |
Figure 1 shows the effect of flame retardant on both the mechanical behavior and flame retardance of PE. Other estimated effects of fiber content and fiber length are meaningless for the non-reinforced PE case. FR content affects the E-modulus positively by 60% improvement to 5 GPa. Tensile strength and impact strength does not change significantly by the addition of FR. Figures 2-4 show the effect of fiber content, FR content and fiber length on the tensile strength, E-modulus, impact strength and flame retardance for corn silk, jute and sugar cane (Bagasse) respectively.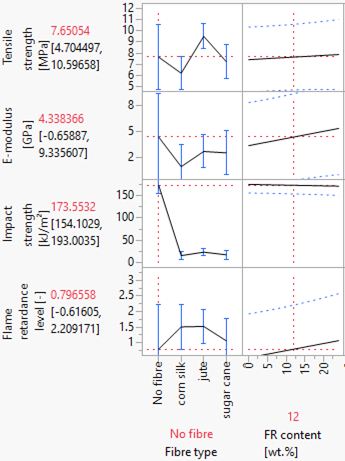 | Figure 1. Profile of the effect of FR content and fiber length on tensile strength, E-modulus, impact strength and flame retardance level of PE without fiber reinforcement |
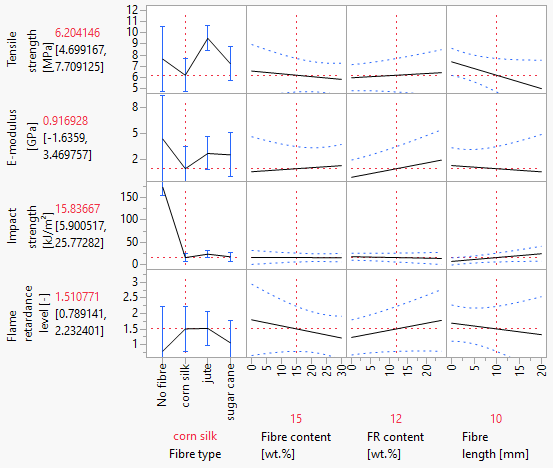 | Figure 2. Profile of the effect of fiber content, FR content and fiber length on tensile strength, E-modulus, impact strength and flame retardance level of PE reinforced with corn silk |
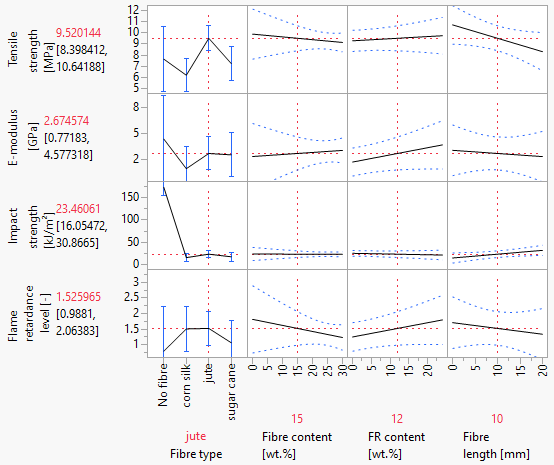 | Figure 3. Profile of the effect of fiber content, FR content and fiber length on tensile strength, E-modulus, impact strength and flame retardance level of PE reinforced with jute |
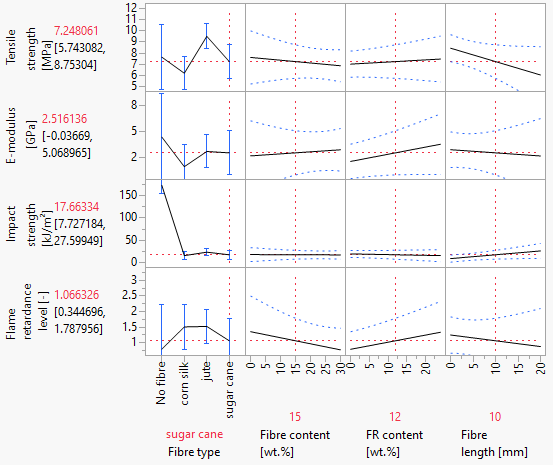 | Figure 4. Profile of the effect of fiber content, FR content and fiber length on tensile strength, E-modulus, impact strength and flame retardance level of PE reinforced with sugar cane (Bagasse) |
In case of corn silk, the mechanical properties are lower than their correspondents in jute and bagasse, but it is distinguished with V1 and V2 flame retardance levels at 20-24% FR. On the other side, jute was distinguished in strength but not in flame retardance. Bagasse show intermediate behavior between jute and corn silk for mechanical and flame retardance properties.Fiber length shows relatively good behavior on the behavior of the impact strength but unexpectedly negative effect on tensile strength. However, this can be justified with the theory of flexible fiber does not support strengthening [9].Water absorption behavior is presented in figure 5. a), b) and c) Tensile strength and flame retardance levels are also presnted in the same figure for the sake of comparison. Corn silk has the highest water absorption of an average of 5% which decrease with more natural fiber. On the other hand, corn silk has the best flame retradance level.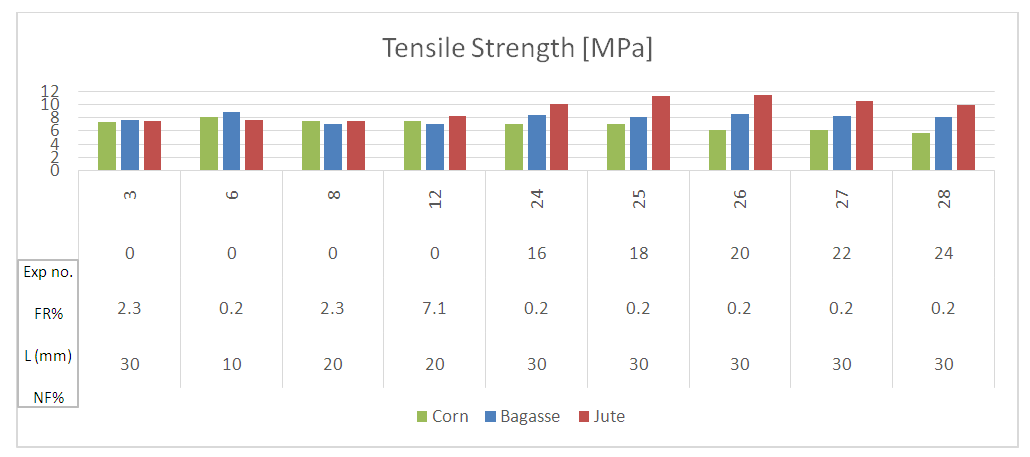 | Figure 5a). Tensile strength values for of different fibers (jute, bagasse, corn silk) at certain (FR%, L in mm, NF%) |
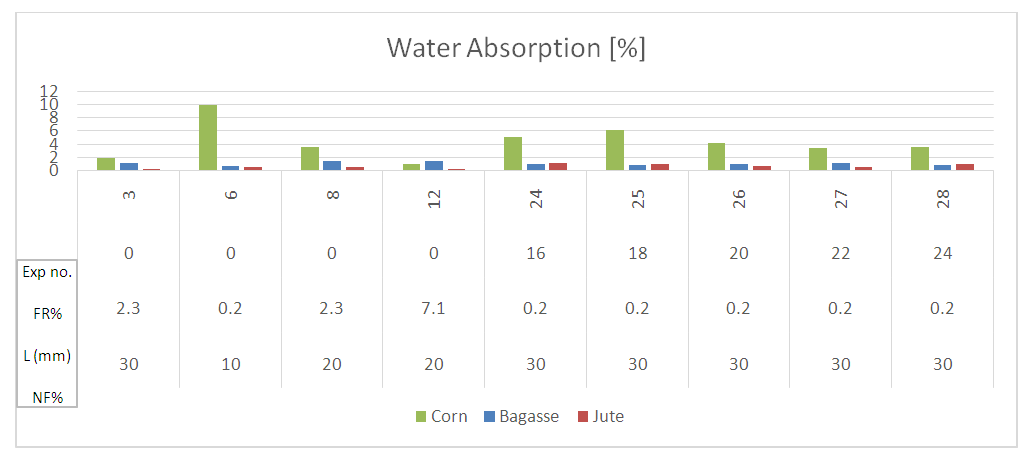 | Figure 5b). Illustrts the water absorbtion results of different fibers (jute, bagasse, corn silk) at certain (FR%, L in mm, NF%) |
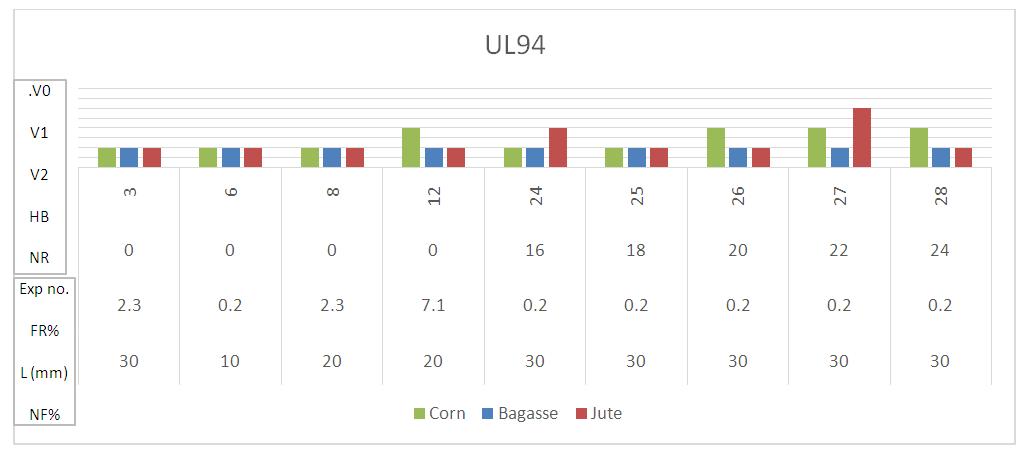 | Figure 5c). Flame retardance levels of different fibers (jute, bagasse, corn silk) at certain (FR%, L in mm, NF%) |
Two opposite processes are affecting the flammability behaviour of the natural fibres and hence the composite. The aromatic rings, available in the lignin, hinders the fibre oxidation. Therefore, lignin produces less volatiles. Oppositely, cellulose supports the flammability process because it produces volatile flammables. Briefly, increasing cellulose content supports the flammability whereas lignin supports the formation of insulating char [12]. Out of [9, 12], (cellulose/lignin) in jute and corn silk are (65/10) and (59/16) respectively. Therefore, flame retardance of corn is better. However, this justification is not totally matching with bagasse where lignin is 25% [7] where the average flame retardance of bagasse is worse than that of corn. This can be attributed to the fiber size which is bigger than the other investigated fibers.
4. Conclusions and Future Recommendations
Mechanical properties (Strength, E-modulus and Impact strength) are proved to be better enhanced with Jute fibers. Fiber content affects positively on E-modulus but negatively on strength and impact strength. Flame retardancy level has the best performance at corn silk due to the fiber constituents (less cellulose and higher lignin). Fiber size shows a negative on the mechanical properties but also on the flammable behavior.
5. Future Work
Biodegradation investigation and scanning electron microscopy study will be carried out to explain the findings of this paper.
ACKNOWLEDGMENTS
The author would like to thank Professor Ahmed Elsabbagh and Dr. Medhat Lotfy Abdallah Elmagd, Abdel Rahman Mokhtar, Ibraheem Ibraheem, Nourhan Taha, Sameha Sadek and Elsalam Plast factory for their help during this research.
References
[1] | R. Porta, J. Appl. Biotechnol. Bioeng. 2017, 2, 2. |
[2] | J. Song, M. Kay, R. Coles, Food Beverage Packag. Technol. 2011, 295. |
[3] | A. K. Bledzki and J. Gassan, Prog. Polym. Sci. 1999, 24, 221. |
[4] | M. Garcia, I. Garmendia, and J. Garcia, J. Appl. Polym. Sci. 2008, 107, 2994. |
[5] | A. Coutoure, G. Lebrun, L. Laperriere, Composite Structures 2016, 16, 263. |
[6] | A. El-Sabbagh, L. Steuernagel, D. Meiners, G. Ziegmann, O. Toepfer, Compos. Part B Eng. 2016, 62, 12. |
[7] | N. S. Balaji, S. Jayabal, S. Kalayana Sundaram, Macromol. Symp. 2016, 361, 42. |
[8] | A. Elmagd, A. Mokhtar, I. Ibraheem, N. Taha and S. Sadek. Evaluation of Biodegradable Thermoplastic Composites with Fire Retardant Properties, Bocheler degree, Faculty of Engineeering Ainshams University 2018. |
[9] | A. El-Sabbagh, Compos. Part B Eng. 2014, 57, 126. |
[10] | A. Elsabbagh, A. Ramzy, L. Steuernagel, G. Ziegmann, Compos. Part B Eng. 2019, 162, 198. |
[11] | A. Elsabbagh, T. Attia, A. Ramzy, L. Steuernagel, G. Ziegmann, Compos. Part B Eng. 2018, 141, 1. |
[12] | J. Muessig, Industrial Applications of Natural Fibres, Wiley, ISBN 978-0-470-69508-1. |