Moses G. Nyang`au1, Alex M. Muumbo1, Charles M. M. Ondieki2
1Department of Mechanical and Mechatronics Engineering, Technical University of Kenya, Nairobi, Kenya
2Department of Mechanical and Mechatronics Engineering, Multimedia University of Kenya, Nairobi, Kenya
Correspondence to: Moses G. Nyang`au, Department of Mechanical and Mechatronics Engineering, Technical University of Kenya, Nairobi, Kenya.
Email: |  |
Copyright © 2019 The Author(s). Published by Scientific & Academic Publishing.
This work is licensed under the Creative Commons Attribution International License (CC BY).
http://creativecommons.org/licenses/by/4.0/

Abstract
Processing of agricultural products such as sugarcane and maize leaves a lot of agricultural waste. Sugarcane bagasse is one such product. When these wastes decompose, they produce methane, and when burnt, they emit carbon dioxide, both gases pollute the environment and contribute towards global warming. This research was to investigate an alternative use of bagasse from sugar processing industry and that from direct chewing of sugarcane. The growing demand for soft boards in the construction industry has posed a threat to forest cover since it is the largest source of raw material. The synthetic binders used are expensive and contribute towards environmental degradation through Urea Formaldehyde (UF) and Phenol Formaldehyde (PF) emissions. The research was to produce B-E boards using sugarcane bagasse and euphorbia sap and determine their mechanical and physical properties. The bending strength was found to be 0.66N/mm2, the tensile strength 0.18N/mm2, thickness swelling 9.7% and water absorption 6%. When these properties were compared with the corresponding values given by the Kenya Standard on fibre board specification (KS 2706-2:2017), the boards were found to be suitable for non-load bearing applications such as insulation and acoustics.
Keywords:
Bagasse- Euphorbia board, B-E board
Cite this paper: Moses G. Nyang`au, Alex M. Muumbo, Charles M. M. Ondieki, Production of Particle Boards from Sugarcane Bagasse and Euphorbia Sap, International Journal of Composite Materials, Vol. 9 No. 1, 2019, pp. 1-6. doi: 10.5923/j.cmaterials.20190901.01.
1. Introduction
Kenya`s economy depends largely on agriculture. The processing of agricultural products leads to wastes that are mainly disposed, of which sugarcane bagasse is the focus here. When these wastes decompose, they produce methane, and when burnt, they emit carbon dioxide, both gases pollute the environment and contribute towards global warming [1]. Sugarcane chewing is a common practice amongst the Kenyan society. The chewing process leaves the sugarcane waste littering the streets in most of the urban and rural set ups, which raises environmental and medical concerns.Euphorbia plant is a locally available tree whose branches when broken, produces white sap that has binding properties that could be used in binding the sugarcane waste. Ojuok as is traditionally known in Nyanza is natural vegetation in most parts of Kenya with no or little economic use. This research was to investigate an alternative to conventional wood fibre and synthetic binders by using sugarcane bagasse as natural fiber which has been used before [2] and euphorbia sap as natural binder for particle board production.The boards are used in interior parts of vehicles, aircrafts and buildings [3]. The main source of fibre used is wood but the decreasing global forest cover is causing a lot of concern both nationally and internationally as it causes global warming and adversely affects climatic conditions. This, therefore, calls for the need to look for alternative source of fibre for particleboard production.The commonly used binders are urea formaldehyde and phenol formaldehyde both of which are synthetic. They are both expensive [4] and give emissions as they age and contribute to global warming [5]. They bind through change of state during heating, melting and solidification hence demand high power supply [6].The main objective of this study was to use the sugarcane bagasse and euphorbia plant sap to produce Bagasse-Euphorbia (B-E) boards. Bagasse-Euphorbia (B-E) boards were produced, and the mechanical and physical properties of the resulting (B-E) board were determined and the results compared with the Kenya standard KS 2706-2:2017.
2. Methodology
2.1. Materials and Methods
The raw materials used to make particle boards in this research were obtained from the Nairobi City County. The sugarcane was sourced from Kisii County, and the Euphorbia plant was obtained from Ruiru-Kenya where it is used for fencing.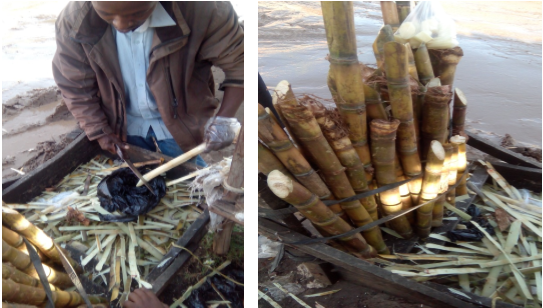 | Figure 1. Sugarcane vending to customers, and the remaining stock |
Figure 1 shows a sugarcane vendor in Sunton estate in Nairobi City which is the scenario with all estates in the Nairobi City. It is very easy to obtain the sugar cane waste since it is not being put into any economic use within the City. Sugarcane is the source of fibre used in this research and has been used in the past with proven results [7].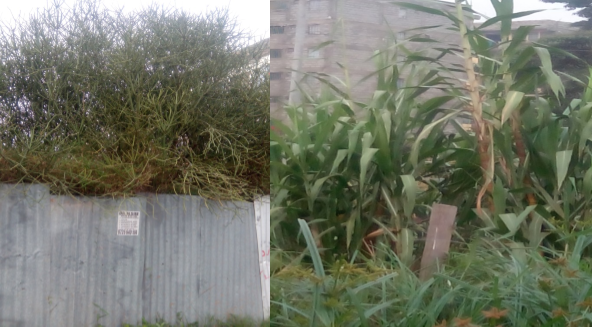 | Figure 2. Euphorbia and sugarcane plants in Nairobi city, Sunton estate |
It is common to find individual homes fenced by euphorbia plant while sugarcane is a popular crop cultivated both in large and small scale in various parts of the country. Figure 2 shows a sample of what one can find in Nairobi and many parts of the country.Sugarcane was bought, cut into pieces and given to the university workers to chew; this produced four kilograms of bagasse. This was left to dry naturally for three weeks reducing to three and half kilograms then crushed in an improvised and fabricated maize milling machine but without a screen.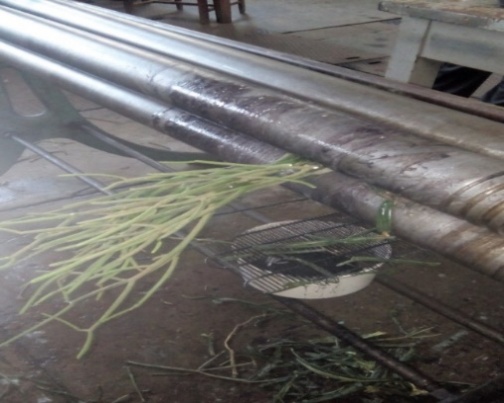 | Figure 3. Extraction of euphorbia sap using a sheet rolling machine |
The leafy parts of the euphorbia plant stalks were cut and squeezed through a rolling machine at the Technical University of Kenya welding workshop. The sap was tapped by a container under the machine until it was adequate for the soft board formation. In total, three litres were collected. During extraction, 2.24kg of euphorbia produced 280ml of the sap.Bagasse was weighed to various amounts using a weighing machine and put into the blender. Then the binder was measured to various amounts using a measuring jar and added into the blender. The hand operated blender was then used to mix them homogeneously. This mixture was then divided into equal parts and inserted by hand into the rectangular forming box on the support member of the hydraulic press. After ensuring uniform level in the forming box and central positioning of the forming box with the hydraulic cylinder actuator, the hydraulic system was put on and the pressing continued until the materials were compressed to 15mm thick. The density of euphorbia sap extracted was determined from the mass and volume extracted, and was found to be 982.14 Kgm-3; the density was calculated using the formula, (density = mass/volume).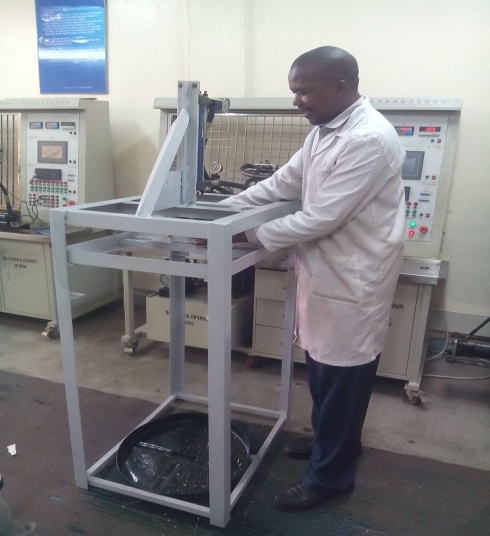 | Figure 4. Positioning of the forming box on the hydraulic press ready for operation |
The operation of compacting was carried out in the hydraulic lab at the Technical University of Kenya. The materials was filled in a rectangular forming box, which was carefully positioned at the center of the hydraulic cylinder actuator with a rectangular pressing plate on its end as shown in figure 4. The hydraulic system was switched on and the cylinder activated on the extraction stroke at a reduced speed using a variable speed regulator.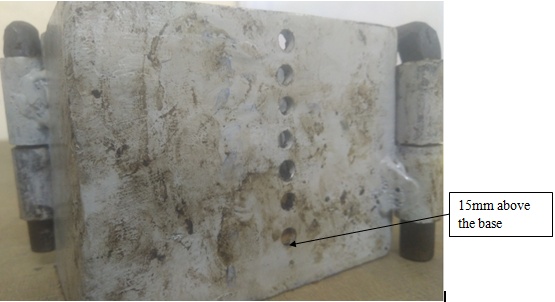 | Figure 5. Forming box with inspection holes on the side |
The materials were compressed until it was 15 mm thick as shown in figure 5 and being an essential step of molding and pressing in particle board production [8]. While producing the particleboards, it was observed that after releasing the pressure of the hydraulic cylinder, the formed particle boards from bagasse and euphorbia sprung back. This necessitated the use of a restricting dead load on the wet particleboards to restrict the boards from springing back. The forming box was made to have two pins at diagonal corners for ease of disengagements to avoid interference on the wet sample made.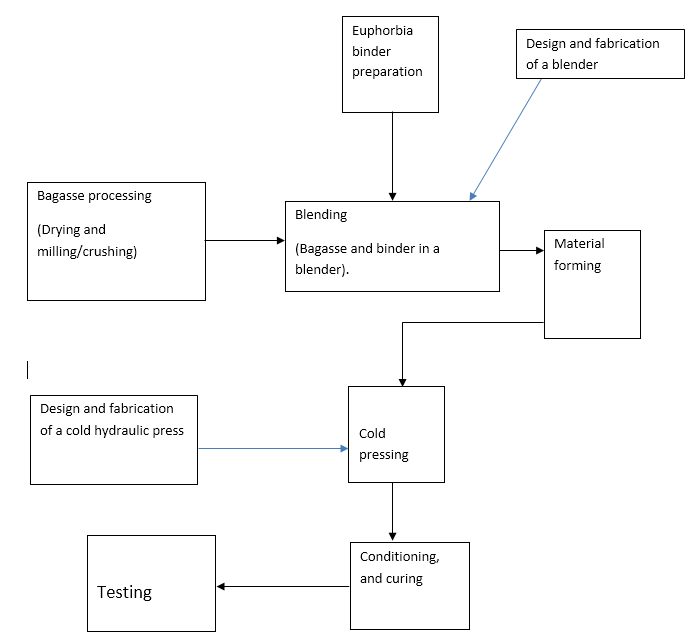 | Figure 6. Process flow diagram of particle board production |
Figure 6 shows the process flow of activities in this research which is different from the one by Ronald, 1972 which had depithing, hot pressing, and use of synthetic binders [9]. Bagasse and euphorbia were obtained and processed separately then stored. A blender and cold press were also designed and fabricated in the research. Bagasse was then mixed with euphorbia sap in the blender and the mixture filled into the forming box to a determined depth and placed on the cold press supports ready for compaction. The material was pressed to a suitable pressure, left at the pressure for a short duration then released. Conditioning and curing of the compacted material was done under the natural environment with some post forming load placed on it. After curing, the post forming load was removed, density of board calculated and testing of physical and mechanical properties done.
2.2. Sample Testing
2.2.1. Thickness Swelling and Water Absorption Tests
Table 1. Density, water absorption, experimental and standard swelling values 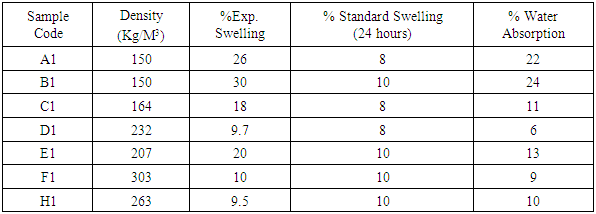 |
| |
|
Table 1 has been derived from the recorded data of samples A1-H1. The increase in thickness after the experiment was divided over the original thickness value and converted into percentage. This is recorded as a percentage of the experimental swelling. The standard has given a percentage of thickness swelling depending on the original sample thickness. The corresponding thickness values are tabulated in table 1. On water absorption, the increase in mass of the samples after the 24 hours was divided by the original mass and converted into percentage. This was recorded in the last column of table 1. However, the Kenyan standard on fibre board, does not give recommended values for water absorption. The column on density has been included in the table as additional information about the samples under research. The standard used in this research is the Kenyan standard on fibre board, KS 2706-2:2017.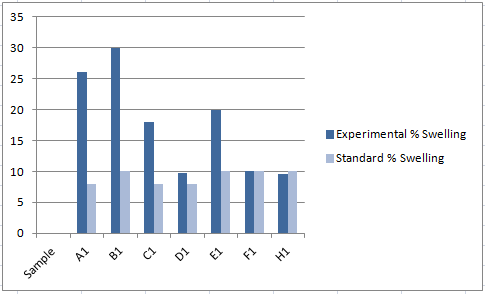 | Figure 7. Comparison between the % experimental thickness swelling values with % standard thickness swelling given |
The bar graph in figure 7 show a comparison between the swelling values obtained during the experiment and the recommended values by the standard. It is observed that some samples have a wide variation from the standard recommended values. However, there are those which are very close to the recommended values such as F1 and H1. More investigations should be done to show the impact of density, mix ratio and fibre properties to percentage thickness swelling.
2.2.2. Tensile Strength Results
Table 2. Density, mix ratio, experimental and standard tensile strength values 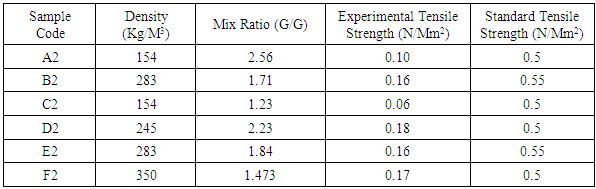 |
| |
|
Table 2 gives the experimental tensile strength obtained in N/mm2 from the universal testing machine. These are compared to the standard tensile strength recommended in the Kenyan standard of particular sample thickness. There could have been errors in the measured values especially due to gripping challenge of the samples. It was not easy to know adequate gripping force without fracturing the sample. The density and mix ratios have been given in table 2 to provide additional background information about the samples under test.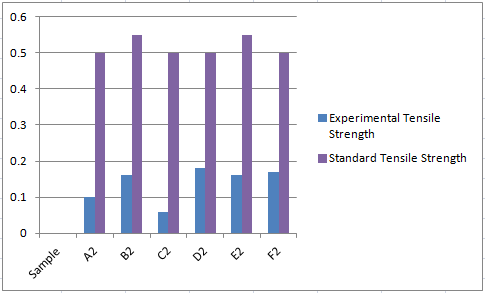 | Figure 8. Comparison between experimental and standard tensile strength |
The comparison between the experimental and standard values as given in the Kenya standard KS 2706-2:2017, shows a fairly huge difference between the experimental tensile strength and the values recommended in the standard as shown in figure 8. This is largely attributed to the fact that conventional method of production use synthetic binders namely; UF and PF. During the production, heating at about 150oC is done making the UF and PF in the binding process become thermosets [10]. The euphorbia sap used in this research does not undergo such transformation but has a surface geometry for adhesion which is the reason it has been used in this research [11]. The strength obtained here is therefore out of the binding and curing under the ambient temperatures between the bagasse fibre and the euphorbia binder.
2.2.3. Bending Strength Results
Table 3. Experimental and standard bending strength |
| |
|
Table 3 shows the experimental bending strength obtained from various samples as labeled A3-F3. The range between the experimental values and the standard recommended values is huge and equally attributed to the type of binders used and their heating process. However, errors could have also risen from the fact that there was some compression at the point of load applications before the actual bending strength was determined. The density and mix ratio values given are for background information about the samples under consideration.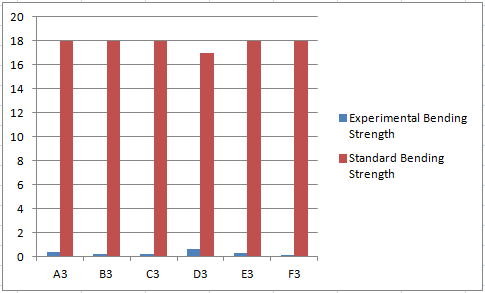 | Figure 9. Comparison between experimental and standard bending strengths |
The bar graph shown in figure 9 shows the comparison between the experimental bending strength of selected samples A3-F3 to the values recommended in the Kenyan standard of samples corresponding in thickness. The synthetic binders used to produce samples relied on the standard data, have strong resistance to molecular movement hence high strengths [12]. This is the expected contributing factor to the disparity seen between the experimental values from natural materials under ambient temperature conditions and standard values using conventional method. The euphorbia sap used in this research has been used as an adhesive for other purposes in the past [13].
2.2.4. Findings
The table below shows important results obtained during the tests.Table 4. Summary of major findings from the experimental data on B-E boards produced 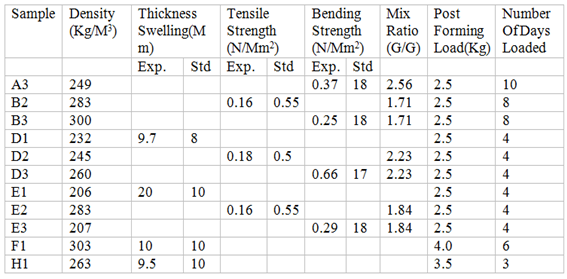 |
| |
|
Table 4 show a summary of selected samples whose density was found to be close to the recommended value of 230 Kg/m3 for soft boards [14]. Different tests whose values are shown were conducted on these B-E board samples because all the tests conducted for water absorption, thickness swelling, and tensile strength and bending strength are destructive in nature [15]. Bending strength test was conducted on samples A3, B3, D3, and E3. The results of these tests show a wide disparity from the standard values given by the Kenyan standard KS 2706-2:2017. Samples B2, D2, and E2 underwent tensile strength test which when its results are compared with the values given in the Kenyan standard KS 2706-2:2017, they relate fairly well though still less than the standard values given. Samples E1, F1, and H1 underwent a thickness swelling test whose results compare well with the one given in the standard KS 2706-2:2017. The mix ratios, post forming loads and the number of days loaded have also been given to provide background information on their production process.Although the strength values from this research are low, the boards can be used for non-load bearing applications like insulation and acoustics given that the range of densities obtained in the research have a high noise reduction coefficient [16]. Previously some boards used for acoustic and insulation purposes have been made of bagasse [17]. This research, therefore, was important because if B-E board production is commercialized, there will be a huge economic benefit as the euphorbia plant is naturally available in abundance with little or no economic use while bagasse is available as waste product from sugar processing industries in Kenya. Since properties of natural fibres have been known to vary considerably depending on factors such as fibre diameter and structure, [18], then more research can be recommended on their impact in bagasse euphorbia board characteristics as obtained in this research.
3. Conclusions
Bagasse fibre from sugarcane and euphorbia sap binder was used successfully to produce bagasse euphorbia boards in their natural conditions and at ambient conditions of temperature. The process of B-E board production was established successfully which is different from the conventional heating and use of synthetic binders. The physical and mechanical properties of the B-E board samples were determined. These are; water absorption test, thickness swelling test, tensile strength test and the bending strength test. Values obtained in these tests were compared to the values recommended in the Kenya Standard for fibre boards of which the disparities in strength values suggest that the B-E board samples produced may only be suitable for non-load bearing applications. When density values obtained as shown in this research are compared to tabulated noise reduction coefficient values, they give an indication of suitability for use in sound reduction applications. While bagasse has been used to produce particle boards in the past, and euphorbia sap used for other bonding tasks, it has now been demonstrated that the two can be used to produce boards for day to day applications.
ACKNOWLEDGEMENTS
My special thanks go to The Almighty God for His unfailing Love, Care and Grace to me this far. Secondly, to my research supervisors: Professor Alex Muumbo and Professor Charles Manasseh M. Ondieki for their guidance throughout the research period. Several individuals, technicians and technologists supported me to make sure I got better results throughout the research period. These include Mrs. Alice Mutai, Mr. Machanja of the welding workshop and Mr. Buliva of hydraulics lab where the experiments were conducted in the Technical University of Kenya. The support I received from Multi-Media University in materials lab under Mr. Musyoki, the technician is much appreciated. The moral support and encouragement I have always received from my dear wife Zipporah Kerubo to soldier on is highly appreciated. This research could not have gone as smooth were it not for DAAD sponsors who paid for me all fees and other operational expenses. I will not forget the role played by my research mentor, the late Professor Wilson O. Ogola, May His Soul Rest in Eternal Peace.
References
[1] | Mumias Sugar CO. Ltd. (2006). Project Design Document. Nairobi: UNFCCC Clean Development Mechanism. |
[2] | Sugar Processing Research Institute. (2005). Sugar and Other Sweeteners. Sugar Processing Research, 2-12. |
[3] | Olusegun, D. S. (2015). Natural Fibres. Journal of Minerals and Materials Characterization and Engineering, 1-3. |
[4] | Wuhan LVYIN Chemical Co. Ltd. (2017, October 21). Alibaba.com. Retrieved from Alibaba.com Site International: http://www.wuhan-ivyin.com. |
[5] | Ursula, et al (2007). Natural Binders. In Ursula et al, Molecular Wood Biotechnology (pp. 347-359). Gottingen: Research Gate. |
[6] | Soren, H. (2010). Manufacture of straw mdf and fibre boards. Fibre Science and Communication Network, 32. |
[7] | Asokan, P., Firdoosus, M., & Sonai, W. (2012). Properties and potential of bio-composites. Advanced Materials and Processes Research Institute, India, 254-255. |
[8] | Matoke, G., Owido, S., & Nyaanga, D. (2012). Effect of production methods and material ratios on physical properties of the composites. American International Journal of Contemporary Research, 1-3. |
[9] | Ronald, A. S. (1972). Bagasse Particle Board: A Production Study and Investment Analysis. Massachusetts Institute of Technology, 37-57. |
[10] | Paul, A. M., Emmanuel, C. E., E.C, G., & David, E. A. (2014). Comparative study of Phenol Formaldehyde and Urea Formaldehyde particle boards from wood waste for sustainable environment. International Journal of Scientific and Technology Research volume 3 issue 9, 54. |
[11] | Omare, J., & Friday, E. (2010). Phytochemical composition, bioactivity and wound healing potential of Euphorbia Heterophylla (Euphorbiaceae) leaf extract. International Journal on Pharmaceutical and Biomedical Research, 54-58. |
[12] | Rolf, K. (2011). Laser welding of plastics. In K. Rolf, Material properties of plastics (p. 13). Verlag GmbH: Wiley-VCH Verlag GmbH & CO. KGA. |
[13] | Julius, M., & Patrick, V. D. (2011). The Miracle tree: Current status of available knowledge. Scientific Research and Essays, 4909-4910. |
[14] | Acara Concepts LTD. (2017, September 21). Soft Board Standard. Retrieved from Acara Concepts LTD web site: www.acaraconcepts.com. |
[15] | I.Y, S., V.S, A., SHUAIBU, L., & SHANGALO, M. (2013). Development of eco-friendly particle boards composites using rice husk particles and gum arabic. Journal of material science and engineering with advanced technology, 79-82. |
[16] | Anand, N., M.C.Kiran, & Varadarajulu, K. (2017). Influence of Density on Sound Absorption Coefficient of Fibre Board. Open Journal of Acoustics, 6-8. |
[17] | Indiamart. (2017, May 25). mid-lan boards. retrieved from mid-lanBoards: https://2.imimg.com/data2/KA/BH/MY-/plane-softboard.pdf |
[18] | Thomas, S., Paul, S., Pothan, L., & Deepa, B. (2011). Natural Fibres. Cellulose Fibres, 4-6. |