Wycliffe O. Ondiek1, Harrison T. Ngetha2, James N. Keraita3, Jean B. Byiringiro1
1Department of Mechatronics Engineering, Dedan Kimathi University of Technology, Nyeri, Kenya
2Department of Electrical and Electronic Engineering, Dedan Kimathi University of Technology, Nyeri, Kenya
3Department of Mechanical Engineering, Dedan Kimathi University of Technology, Nyeri, Kenya
Correspondence to: Wycliffe O. Ondiek, Department of Mechatronics Engineering, Dedan Kimathi University of Technology, Nyeri, Kenya.
Email: |  |
Copyright © 2018 The Author(s). Published by Scientific & Academic Publishing.
This work is licensed under the Creative Commons Attribution International License (CC BY).
http://creativecommons.org/licenses/by/4.0/

Abstract
The use of natural fibers to replace synthetic fibers as reinforcement in polymer composites has received growing attention in the 21st Century. This is occasioned by global campaigns for utilization of eco-friendly materials as substitute to the conventional non-biodegradable materials which adversely affect the environment. Academicians and researchers have focused on value addition to agro-waste fibrous materials by utilizing them as reinforcements in composites for low load structural applications such as ceiling boards, cardboards, partition boards, mirrors, and picture frames. This study focused on fabrication and mechanical characterization of composite materials made of rice husk fibers and unsaturated polyester resin matrix, with methyl ethyl ketone peroxide (MEKP) as hardener. The fibers were chemically treated with 4% NaOH then dried, milled and classified into three categories: small size (250 – 500 µm), medium size (500 – 1000 µm), and large size (1000 - 2000 µm), using standard laboratory sieves. For each size category, samples were prepared by varying fiber weight fraction (%wt) in increasing steps of 5% from 0% (lowest) to 20% (highest). Hand layup method was used to prepare the specimens, which were then sized in accordance with ASTM standards and subjected to tensile and impact testing. Statistical results for ANOVA two factor without replication at 5% level of significance showed that both fiber loading and fiber content affect mechanical behavior of the composite materials. Maximum tensile strength of 25.14 MPa was recorded by the small size rice husk fibers at 15 %wt, while large size rice husk fibers gave minimum tensile strength of 9.38 MPa at 5 %wt. Medium size rice husk fibers gave highest impact strength value of 7.75 J/mm2 at 15 %wt, while lowest impact strength value of 3.08 MPa was registered by the large size rice husks at 20 %wt. It can therefore be deduced that composite materials made of rice husk fibers can be worthwhile alternatives to synthetic fiber materials for both household and industrial applications.
Keywords:
Rice husk, Polyester resin, Hand layup, Fiber weight fraction, Fiber size
Cite this paper: Wycliffe O. Ondiek, Harrison T. Ngetha, James N. Keraita, Jean B. Byiringiro, Investigating the Effect of Fiber Concentration and Fiber Size on Mechanical Properties of Rice Husk Fiber Reinforced Polyester Composites, International Journal of Composite Materials, Vol. 8 No. 5, 2018, pp. 105-115. doi: 10.5923/j.cmaterials.20180805.01.
1. Introduction
In this present era of advanced technology, the field of composite materials has become an attractive area of research, both for academicians and engineers. There is a rising demand for more durable, light weight and cheaper materials for numerous applications. Metals and alloys had previously dominated the manufacturing industry. Plastics were later discovered, but their use was restricted to low end applications such as dustbins and food containers because they possess relatively low strength [1]. This set-back led researchers to turn their focus to composite materials. Presently, the vast fields of application of composite materials include automotive industry, sports goods, engineering, defence, marine, and aerospace [2]. Recent research in the field of composites reveal a new trend of massive shift from the use of synthetic fibers like glass, carbon and aramid, to natural fibers. Natural fibers are continuous filament hair-like materials found in plants and animals. Distinctive examples of plant fibers include sisal, hemp, coir, cotton, bamboo, jute, rice husks, ramie, and flax. The use of natural fibers as reinforcing materials has been in existence for more than 2000 years [3]. Egyptians fashioned bricks from mud and straw. The mud bricks were reinforced with sun dried straws made from papyrus reeds in 1200-1400 BC. Horse hair was also used in some instances to improve mechanical properties of mortars. Among the antiquities found in the Metropolitan Museum of Art in Egypt are the Egyptian tomb paintings showing the ancient brick-making process [4]. However, greater preference for natural fiber utilization in composite materials manufacture over synthetic fibers is evident in the 21st century. This is due to the global call for enactment of environmental conservation and sustainable development measures in manufacturing. Composites made from natural fibers are springing up in place of traditional fibers because of their combustibility, ample availability, low cost, high specific strength, low density, nontoxicity, renewability, biodegradability, light weight, non-abrasiveness, and absence of health hazards [3, 4]. The matrix material used to bind the fibers are classified as either thermoplastics or thermosetting resins. Rice husk is the tough protecting cover of rice grains. Rice is a cereal crop that is cultivated and consumed by nearly the whole world’s population. Globally, the cumulative area under rice cultivation is approximated to be 150 million hectares, with an average annual production of about 500 million metric tons [5]. This translates to 29% of the total yield of grain crops worldwide. In Kenya, rice is the third most vital cereal crop after maize and wheat. Ndiritu [6] stated that approximately 80% of rice in Kenya comes from the government's irrigation schemes where Mwea scheme produces over 60%. Processing of harvested rice involves milling to separate the husks from the rice grains. Rice husk is therefore one of the widely produced agro-waste products worldwide, which is often regarded as having no use, hence disposed by incineration, heaping or dumping in water bodies, consequently leading to environmental degradation.This research focused on development and evaluation of tensile and impact behavior of rice husk fiber reinforced polyester composites, with specific focus on the effect of fiber size and fiber loading on the resulting mechanical properties. Rice husk composites target light load bearing structures and products such as panels, back covers of mirrors, ceiling boards, plastic doors, handles, roof tiles, partition boards, window and door frames, foot rests and bumpers in automobiles.
2. Literature Review
The feasibleness of rice husk fibers as reinforcement in the manufacture of composite materials is no longer a novel concept. This section presents a summary of recent work done by researchers on rice husk fiber composites. Odhong et al. [7] prepared composite materials from post-consumer high density polyethylene (HDPE) reinforced with rice husks, wood flour and bagasse. They compared the mechanical properties of the composites and found out that wood flour yielded maximum tensile and compressive strengths of 83.87 MPa and 225 MPa respectively. Rice husks gave maximum flexural strength of 39 MPa. However, in their work, the effect of fiber size variation on mechanical properties of the composites was not studied. In a work published by Rassiah et al. [8], the influence of chemically treated rice husk flour weight fraction on flexural strength and water absorption characteristics of rice husks/E-glass/polypropylene hybrid composite was examined. It was observed that the accumulation of natural fibers reduced the flexural strength and modulus of the composite, while the addition of E-glass increased the flexural strength and modulus of the composite. Highest flexural strength and modulus values of 45.6 MPa and 4052:11 MPa respectively were obtained from the combination of 40 %wt polypropylene, 45 %wt E-glass, and 15 %wt rice husks. Water absorption property examination revealed that rice husks of 15 %wt weight fraction exhibited less absorption for distilled and sea water. Vasanta et al. [9] evaluated the mechanical behavior of coir fiber hybridized with rice husks in vinyl ester matrix material. In their work, coir fiber was the major reinforcement, while rice husks were added to improve the mechanical characteristics of the polymer matrix composite. Test specimens with varying weight fractions of coir fiber were prepared and a small percentage of rice husks were added. Results showed that hybridization with rice husks improved tensile strength of the composite up to 3 %wt, beyond which the flexural characteristics begun to decrease. It was therefore concluded that for applications requiring high flexural property, fiber weight fraction exceeding 3% was not recommended. This work however did not focus on rice husks as the only reinforcement, as it was merely used to boost the tensile strength. Also, the effect of rice husk particle size and weight fraction on mechanical strength of the resulting composite were not addressed. In a work published by Joshi and Chaudhary [10], physical and morphological characteristics of rice husk epoxy composites were investigated. Specimen samples having varying fiber weight percentages of 5%, 10%, 15% and 20% were fabricated and tested. Results from Scanning Electron Microscopy (SEM) test revealed that the state of fiber dispersion into the resin matrix contributed greatly to the resulting characteristics of the composite. Fiber-matrix homogeneity was observed to decrease with increase in rice husk fiber content, thus explaining the reduction in strength of the composite with increase in fiber weight fraction within the matrix. Water absorption capacity was found to increase with increase in fiber weight fraction, with the 20 %wt sample registering maximum absorption. This was attributed to the presence of pores and voids in the composite. Mishra and Padhee [11] evaluated the mechanical characteristics of rice husk-fly ash-epoxy hybrid composites. Fly ash was used as a filler, and its percentage was kept constant at 5% in epoxy matrix. Experimental design involved varying the content of rice husk fiber in the matrix i.e. 10%, 15%, and 20% weight percentages. Highest tensile strength of 33 MPa and flexural modulus of 4881 MPa results were obtained when the composite having 10% rice husk was tested, whereas impact strength was highest in the composite with 20% rice husk. Water absorption test results indicated that the composite with 10 %wt rice husk had minimum absorption, hence it was recommended for use in structural applications. Bisht and Gope [12] developed rice husk flour reinforced epoxy bio-composite and studied the influence of fiber treatment and weight fraction of rice husk on the mechanical behavior, in comparison with wood dust composite reinforced with epoxy. Fibre weight percentage was varied in steps of 10%, from 10% (lowest) to 40% (highest). They noted that addition of rice husk as filler was detrimental nearly to all mechanical characteristics of the resulting composite. It was observed of the 40 %wt untreated rice husks, that ultimate strength and Young's Modulus decreased by around 51% and 26.8% respectively. A close examination of results revealed a remarkable decrease in mechanical characteristics of composites which had more than 20 %wt filler loading. This led to the conclusion that fiber loading beyond 20% is not economical from the strength point of view. The decrease in tensile strength was attributed to the decreasing fiber-matrix interfacial bonding with addition of fibers, as well as agglomeration of rice husk fibers leading to the generation of voids between filler and matrix.As seen from the above literature review, broad research has been conducted on biodegradable natural fiber composites. However, no research has been conducted and reported on fabrication and investigation of the combined effect of varying both fiber size and weight fraction, on the tensile and impact properties of rice husk fiber composites reinforced with unsaturated polyester resin as matrix.
2.1. Aim of Research
The aim of this study was to investigate the combined effect of varying fiber size and fiber loading on the mechanical characteristics of rice husk fiber reinforced polyester composites prepared by hand layup method, with intent of determining the best fiber content and size combinations which yield optimal tensile and impact strength results.
2.2. Contribution of the Study
This research provides a suitable rationale and guideline for selecting the appropriate fiber size and fiber concentration parameters when making rice husk-polyester composite materials to suit the intended applications. Optimum tensile strength values were achieved at 15% fiber concentration in all the fiber size categories, and the 250 - 500 µm fiber size gave the best tensile strength results. Highest impact strength was attained by 500 - 1000 µm fiber size at 15% fiber content. The findings of this research affirm the fact that utilisation of readily available rice husk agro-waste material in the manufacture of polyester based composites in developing countries like Kenya, has the potential of sustaining infrastructural development and helping in the preservation of natural resources such as timber. Moreover, the procedure followed in this work can be used as reference in the investigation of mechanical characteristics of composites made from different fiber and matrix materials.
3. Materials, Equipment and Procedure
3.1. Materials
The main raw materials used in this present work were: rice husks as reinforcement, and unsaturated polyester resin (UPR) and methyl ethyl ketone peroxide (MEKP) as matrix. Other chemicals include sodium hydroxide (NaOH) for surface modification, MR-8 mold releasing agent for easy removal of the cured composite from the mold, and acetone as a cleaning agent. Fresh rice husk fibers were procured from Mwea rice mills, located in Kirinyaga county, Kenya. The fibers were two months old from their time of harvesting. UPR, MEKP, MR-8 releasing agent, and ace-tone were all purchased from Henkel Chemicals East Africa Limited in Nairobi, Kenya.
3.2. Research Tools and Equipment
Main research tools and equipment were: universal testing machine, Charpy/Izod impact testing machine, standard laboratory sieves, fluid bed drier, universal milling machine, vertical band saw machine, surface grinding machine, distiller, and hot air oven. Miscellaneous items used include ball pen hammer, galvanized iron metal sheet, stainless steel metal sheet, polyester mixing container, stirring rod, digital electronic balance, beaker, syringe, surgical gloves, hand gloves, gas mask (respirator), and goggles.
3.3. Design of Experiments
The controllable variables in these experiments were fiber weight fraction (fiber loading) (%wt) and fiber size (µm), while the measured responses were the tensile and impact strengths of the fabricated specimens. Experimental design in this research involved varying the proportion of fiber (by mass) in the matrix for three fiber size designations (small, medium and large) during production of the composites. Fiber content for all the three grades was varied in increasing steps of 5% from 0% (lowest) to 20% (highest) [13]. Classification of fiber sizes was done using standard laboratory sieves as follows: small size (250 – 500 µm), medium size (500 – 1000 µm) and large size (1000 – 2000 µm). The aim was to examine the effect of such variations on the mechanical behavior of the resulting composites. Specimens of various fiber weight fractions and sizes were thus fabricated by hand layup method. The composites produced were then subjected to destructive testing to determine their mechanical strengths.
3.4. Fiber Preparation
Rice husk fibers were first washed with water to remove sand, dust, bran rice, and other small particles. The washing of rice husk was performed several times under vigorous stirring and squeezing. The fibers were then dried in open sun for two days, and thereafter, subjected to chemical treatment. For each batch of fibers 4% w/v NaOH solution (4g of solute per 100 cm3 of solvent) was prepared using distilled water and industrial grade caustic soda (see Figure 1). The fibers were then fully immersed in the solution, thoroughly mixed, and the setup left for three hours to allow for the chemical reaction (see Figure 2). Lignin, hemicellulose, and wax were thus removed from the fibers and their affinity for moisture absorption (hydrophilic property) was reduced.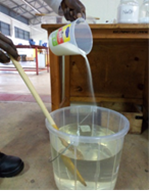 | Figure 1. NaOH preparation |
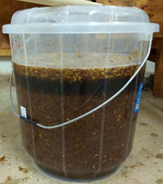 | Figure 2. Rice husks immersed in 4% NaOH |
After three hours, the fibers were rinsed with distilled water to remove all traces of NaOH, then dried for 6 hours in open sun. The sun-dried fibers were then placed in trays and put in a hot air oven for 6 hours at 105 °C to reduce their moisture content [14]. Figure 3 shows trays of rice husks taken from the oven after moisture content reduction.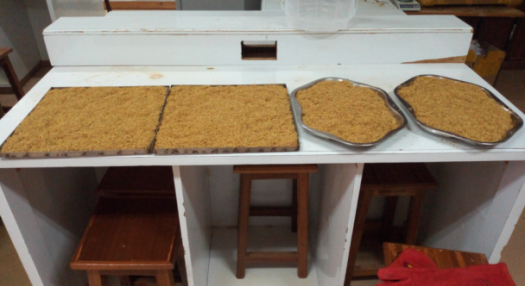 | Figure 3. Over dried rice husk fibers |
The oven dried rice husks were then stored in hermetic plastic containers to avoid contamination, entrance of impurities, or microbial attack. Size reduction of rice husk was performed by ramming the fibers on a galvanized iron metal sheet using a ball pen hammer. The three size classifications shown in Table 1 were then obtained using standard laboratory sieves.Table 1. Fiber size classification 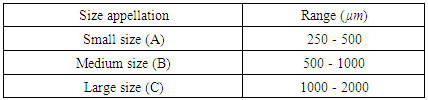 |
| |
|
3.5. Mold Fabrication
A mold of internal dimensions 200 mm × 200 mm × 6 mm was made of polished mild steel. The mold lid was made of mild steel and the inner surface polished with emery paper. The purpose of the lid was to cover and press the content during the curing period, thus preventing entrance of debris and impurities, and providing a uniform levelled surface.
3.6. Composite Fabrication Process
Hand layup method [15] was used to prepare the specimen, because it is the most elementary method with minimum infrastructural and capital requirement. First, the mold base, frame, and lid were cleaned with acetone, then MR-8 mold releasing agent was applied on the inner surfaces to prevent the composite from sticking to the mold surface. Rice husks were then weighed on a digital electronic balance. Based on the measured mass of reinforcement and desired fiber weight fraction, the corresponding resin mass was calculated. The pre-calculated mass of unsaturated polyester resin (UPR) was then measured and gently poured into the plastic jar containing the rice husk fibers. The mixture was gently stirred for 15 minutes to minimize air entrapment, and to improve homogeneity and isotropy of the composite [13]. Methyl ethyl ketone peroxide (MEKP) catalyst (2% by weight of unsaturated polyester resin) was then added to the mixture and stirred carefully to initiate the curing process. The content was gently poured into the mold and covered with the lid. As the composite begun to cure, the lid was pressed mildly to exert pressure on the composite, thus compacting it and further removing trapped air bubbles. The set up was then left for 24 hours to cure at room temperature (23±2 °C). The composite material was thereafter released from the mold and cut to desired dimensions using vertical band saw machine, in readiness for tensile and impact testing. A universal milling machine was used for further machining of the tensile test specimens, thus producing the desired dumbell shapes according to ASTM standards. Figure 4 and Figure 5 show samples of specimens ready for tensile and impact tests.Tensile strength of the specimen was computed by the Universal Tensile Machine according to equation 1. | (1) |
Where, st is the tensile strength, Pmax is the maximum tensile load applied, A is the original cross-sectional area.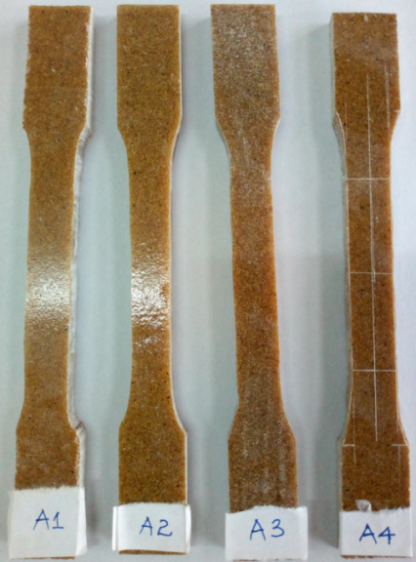 | Figure 4. Tensile test specimen samples |
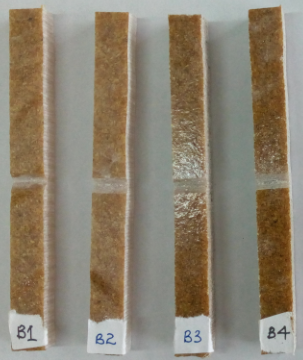 | Figure 5. Impact test specimen samples |
3.7. Mechanical Testing
Tensile and impact tests were conducted on the fabricated specimens in the Materials Engineering Laboratory of Multimedia University of Kenya (MMU), at relative humidity of 65% and ambient temperature of 23±2 °C. Tensile tests were conducted in accordance with ASTM D638-14 standard method of plastic testing, using a universal testing machine (UTM). Tensile specimen samples were machined to conform with the requirements of Type I specimen dimensions, and the preliminary settings on the machine before the test were made as per the standard. For each experimental run, eight pieces were tested, out of which mean values of five best specimens with slightest variances were tabulated.Charpy impact tests were conducted as per ASTM D6110-04 standards using Charpy/Izod impact testing machine with a pendulum having impact energy of 142 J. By fracturing the test pieces, the machine measured the kinetic energy required to initiate and propagate fracture till breakage of specimen occurred. The machines used for carrying out tensile and impact tests on the specimens are shown in Figure 6 and Figure 7 below. Figure 8 shows a sample of tensile test specimen after failure.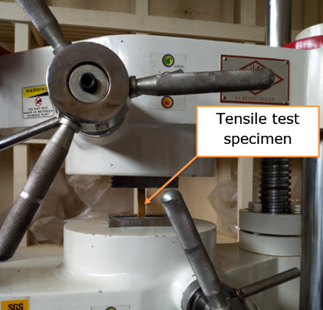 | Figure 6. Tensile specimen between grips of the UTM |
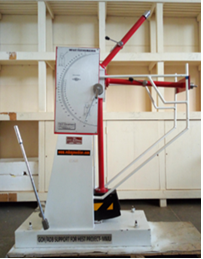 | Figure 7. Charpy/Izod impact testing machine |
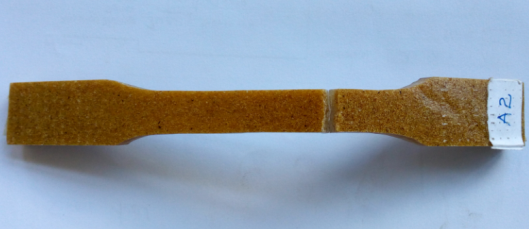 | Figure 8. Broken tensile test piece |
3.8. Hypothesis Formulation
Hypothesis was formulated based on the possible influence of fiber weight fraction (%wt) and fiber size (µm) on tensile and impact strengths of the fabricated composite test pieces. The following approach was adopted:Null hypothesis (H0): Fiber weight fraction has no significant influence on tensile and impact strengths of rice husk fiber reinforced polyester resin composite test pieces, and the observed differences are due to chance, i.e. γ1=γ2=γ3=0. γi is the fiber weight fraction effect in each case.Alternative hypothesis (H1): Fiber weight fraction has a significant influence on tensile and impact strengths of rice husk fiber reinforced polyester composites i.e., γ1 ≠ γ2 ≠ γ3 ≠ 0.Null hypothesis (H0): Fiber size has no significant influence on tensile and impact strengths of rice husk fiber reinforced polyester resin composite test pieces, and the observed differences are due to chance, i.e. α1=α2=α3=0. αj is the fiber size effect in each case.Alternative hypothesis (H1): Fiber size has a significant influence on tensile and impact strengths of rice husk fiber reinforced polyester composites i.e., α1 ≠ α2 ≠ α3 ≠ 0.The following models were used: | (2) |
 | (3) |
Where,
is the tensile strength,
is the impact strength, μ is the mean tensile strength, η is the mean impact strength,
is the error term for tensile strength, and
is the error term for impact strength [16].
3.9. Statistical Analysis
Data collected from tensile and impact strengths of the composites was analyzed using two factor analysis of variance (ANOVA), for completely randomized block design (CRBD), at 5% level of significance. ANOVA tables for both tensile and impact test data were generated by the software, from which the Fratio values were used as rationale for accepting or rejecting the null hypotheses.
4. Results and Discussion
Table 2 gives a summary of tensile strength, modulus, and impact strength results for pure unsaturated polyester resin (UPR), unmixed with rice husk fibers (RHF).Table 2. Tensile and impact results for unsaturated polyester resin  |
| |
|
Table 3 shows a summary of tensile strength, modulus, and impact strength reports for UPR/RHF composites of various fiber sizes, at various fiber weight fractions (%wt). Table 3. Tensile and impact test results for RHF/UPR composites 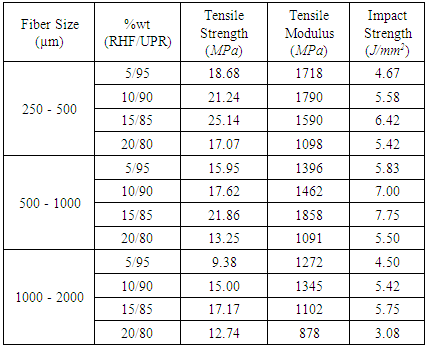 |
| |
|
4.1. Tensile Test Report
4.1.1. Stress-strain Curves
Figures 9, 10 and 11 show the stress-strain behavior of small size (250 – 500 µm), medium size (500 – 1000 µm), and large size (1000 – 2000 µm) RHF composites at various weight fractions (%wt). It can be seen from all the figures that there was a steady increase in load up to a peak point, followed by a sudden drop, which depicts a brittle fracture. Also, UPR recorded the largest strain of 0.0185 before fracture. This suggests that UPR has better elongation properties than the reinforced composites. 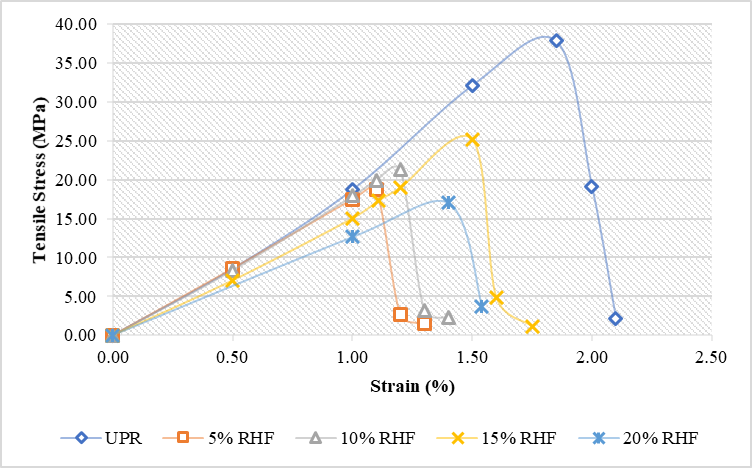 | Figure 9. Tensile stress-stain curve for small size RHF composite |
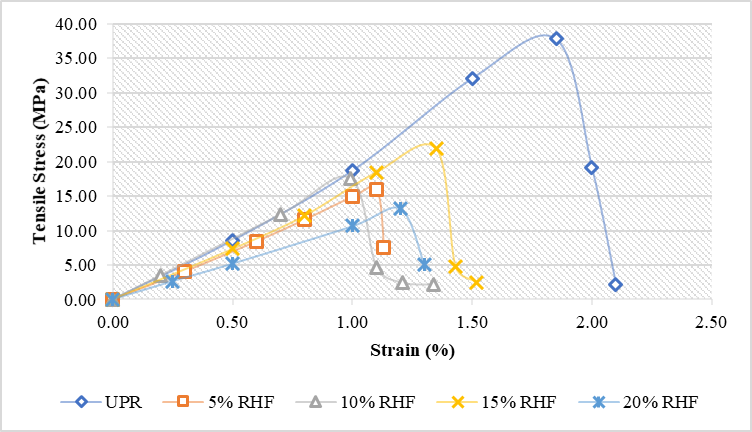 | Figure 10. Tensile stress-strain curve for medium size RHF composite |
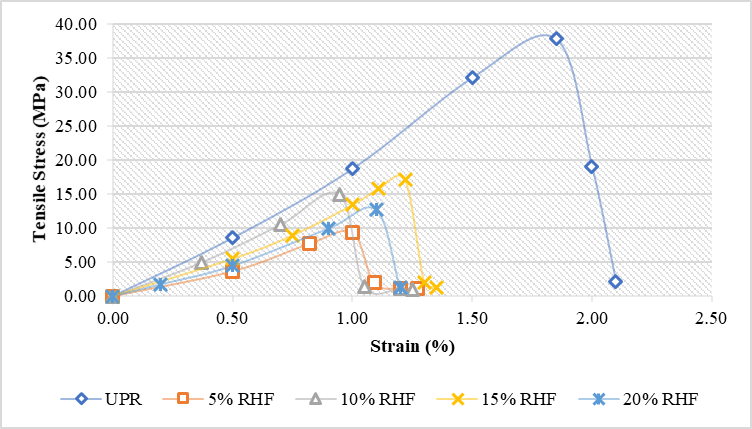 | Figure 11. Tensile stress-strain curve for large size RHF composite |
Stress-strain report for small size RHF composites (See Figure 9) reveal that 15 %wt composite had a maximum strain of 0.015 before failure, while 5 %wt composite recorded minimum strain of 0.011 before failure. A similar trend was observed in medium size RHF composites, as evident in Figure 10. Maximum elongation at break depicted by strain value of 0.0135 occurred in 15 %wt composite, while 10 %wt composite fractured after undergoing minimum elongation depicted by strain value of 0.0099. Results for large size RHF samples shown in Figure 11 also clearly show that the trend was generally similar, with maximum strain of 0.0122 being observed in 15 %wt composite sample. However, minimum strain value of 0.0095 was recorded by 10 %wt composite.From the stress-strain curve reports, it can also be clearly seen that elongation at break decreases with increase in fiber size. This is because chances of air entrapment during mixing process are increased when fiber size increases. The entrapped air leads to void formation in the cured composite, which increases the material’s brittleness.
4.1.2. Ultimate Tensile Strengths
The effect of fiber weight fraction on tensile strength has been illustrated in Figure 12, developed from the data in tables 2 and 3. It can be seen clearly that unreinforced UPR gave the highest tensile strength of 37.84 MPa, and the RHF composite samples had comparatively lower strength properties. This is due to homogeneity of the cured UPR material, high density, and absence of micro and macroscale voids, compared to the reinforced composites. It can therefore be deduced as was concluded by Cholachagudda et al [9], that composites with randomly oriented fibers are generally low strength materials, and can be useful only in low load structural applications and non-structural building elements.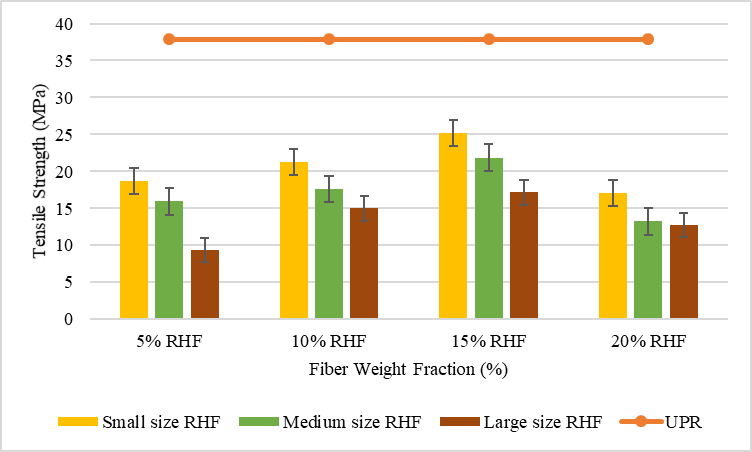 | Figure 12. Effect of %wt fiber on tensile strength |
For the small, medium and large fiber size categories, a uniform pattern can be seen, of increase in ultimate tensile strength as fiber weight fraction increased up to 15 %wt, followed by a drop at 20 %wt. This increase in tensile strength can be attributed to the increase in interfacial adhesion bond between the hydrophilic fiber and the hydrophobic thermosetting resin matrix, which resulted from morphological changes, as reported by Atuanya et al [17]. From 5 %wt to 15 %wt, there was an increase in tensile strength by 34.58%, 37.05%, and 83.08% in the small, medium and large size RHF categories respectively. Tensile strength peak values of 25.14 MPa, 21.86 MPa, and 17.17 MPa were observed in the small, medium and large size RHF composites respectively at 15 %wt. The drop in tensile strength at 20% fiber loading can be attributed to the entrance of air bubbles during the casting process of the composite material with 20% fiber weight fractions, leading to formation of voids. It can also be explained by Joshi and Chaudhary’s approach [10], that fiber-matrix homogeneity decreases at high fiber contents, which explains the reduction in tensile strength of the composite upon increase in fiber %wt beyond 15%. Increasing reinforcement concentration beyond optimum value also increases the discontinuity between fiber and matrix surface, thus leading to a decrease in mechanical performance.As particle size increased from small to large, it can be seen that tensile strength correspondingly decreased. This is due to the higher surface area of contact with matrix (a characteristic of small size RHF), which resulted in increased interaction between the C=O groups of the polyester matrix and the OH groups of RHF [18], leading to formation of strong bonds. Conversely, as fiber size increases, the surface area of RHF decreases resulting to weak bonding hence low strength.
4.1.3. Tensile Modulus
From Figure 13, it can similarly be observed that tensile modulus followed a uniform pattern; the small and large size RHF yielding peak values of 1790 MPa and 1345 MPa respectively at 10 %wt, whereas medium size RHF recorded highest tensile modulus value of 1858 MPa at 15 %wt.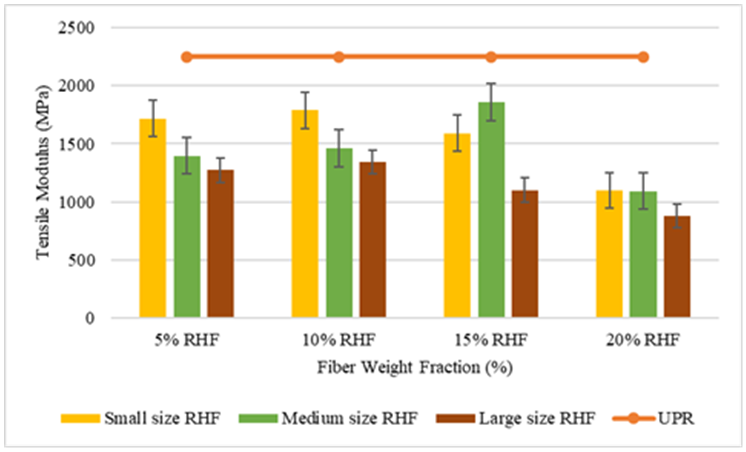 | Figure 13. Effect of %wt fiber on tensile modulus |
As in the case of tensile strengths, UPR yielded the highest tensile modulus value of 2249.65 MPa. Tensile moduli of fiber reinforced composites appear to decrease with increase in fiber weight fraction, except for medium size RHF composite. These tensile moduli results appear contrary to those obtained by Ofem et al. [19], whose results showed an increase in modulus with increase in fiber weight fraction. Thus, it may be concluded from these results, that UPR matrix has a greater stiffness than RHF.
4.2. Impact Test Report
Impact strength results of the fabricated coupons are illustrated graphically in Figure 14. It can be seen from the graph that UPR yielded lower impact strength results (4.08 J/mm2) compared to the reinforced composites. As the fiber size was increased, there was a corresponding increase in impact strength from small to medium fiber size, but the large size RHF composites registered a fall in impact strength at all weight fraction levels, thus yielding inferior toughness properties - a phenomenon that featured also in tensile test. Highest impact strength value of 7.75 J/mm2 was recorded by medium size RHF at 15 %wt. The increase in toughness of the composites with increased fiber size is attributed to the presence of longitudinal fibers at the impacted area which increases resistance to crack propagation, consequently leading to better toughness properties [19]. Large fiber size therefore implies more longitudinal fibers, hence greater resistance to crack propagation, as opposed to small fiber size. The decrease in impact strength as witnessed in large size fiber composites can be attributed to the possibility of poor internal structure of the coupons such as inhomogeneity, anisotropy, and microscale voids, which may have resulted from the fabrication process.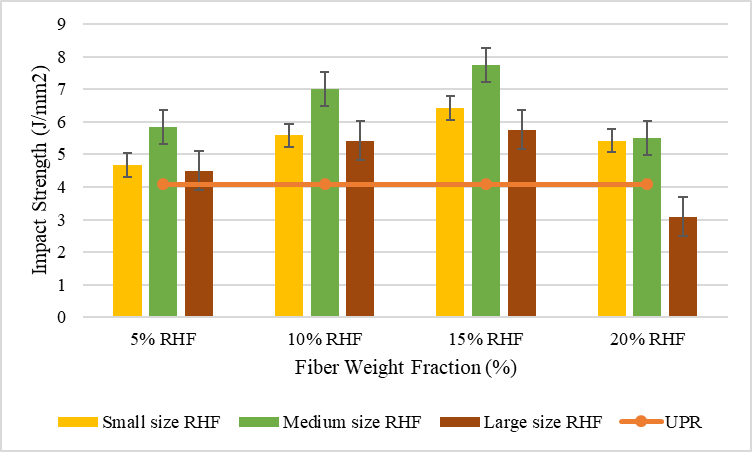 | Figure 14. Effect of fiber weight fraction (%wt) on impact strength |
It can also be clearly seen that as fiber weight fraction increased, impact strength increased for all the three categories of RHF/UPR composites. From 5 %wt to 15 %wt, impact strength increased by 37.5%, 32.9%, and 27.7% for the small, medium and large size RHF categories respectively. Atuanya et al. [17] however reported contrary results with polyethylene thermoplastic matrix.
4.3. ANOVA
4.3.1. Experimental Areas and Results
Analysis of variance was conducted for CRBD at 5% level of significance. The experimental areas shown in tables 4 and 5 for tensile and impact test results were chosen for analysis. The results are shown in Tables 6, 7, 8, and 9, where fiber weight fractions (%) are represented in rows while fiber sizes are represented in columnsTable 4. Experimental area for tensile test 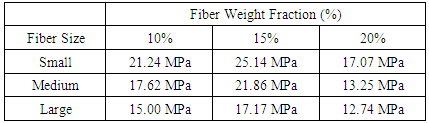 |
| |
|
Table 5. Experimental area for impact test 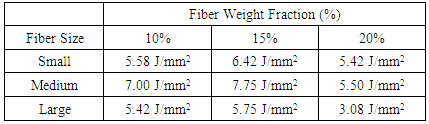 |
| |
|
Table 6. Tensile test ANOVA: Two-Factor without Replication 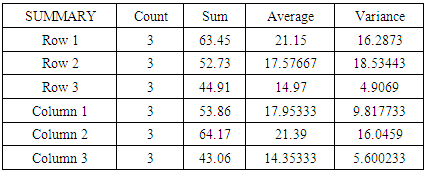 |
| |
|
Table 7. Impact test ANOVA: Two-Factor without Replication 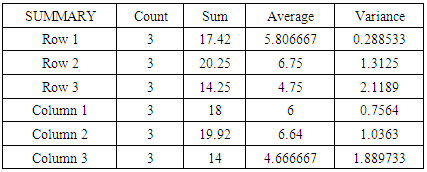 |
| |
|
Table 8. Tensile test ANOVA table for CRBD  |
| |
|
Table 9. Impact test ANOVA table for CRBD  |
| |
|
4.3.2. Statistical Inferences from Tensile Test ANOVA
Based on the formulated hypothesis in section 3.8, and looking at table 8, we see that F>Fcrit for rows which represent fiber weight fraction (%wt). The null hypothesis was therefore rejected, and it was deduced that tensile strengths of RHF composite materials were affected by the variation of fiber weight fraction. Considering the columns which represent fiber size; F>Fcrit, hence the null hypothesis was rejected and it was decided that variation of fiber size influenced the tensile strengths of the fractured RHF composite coupons.
4.3.3. Statistical Inferences from Impact Test ANOVA
Considering table 9, it is similarly evident that F>Fcrit for rows, implying that the variation of fiber weight fraction affected the impact strengths of the composites. Thus, the null hypothesis was rejected. Looking at the columns, it can also be seen that F>Fcrit. This connotes that impact strengths of the composite materials were affected by varying fiber size; hence the null hypothesis was rejected.
5. Conclusions
This present work aimed at developing composite materials from rice husk fiber reinforcement and polyester resin matrix. The effect of varying fiber size and fiber weight fraction on the tensile and impact properties of the resulting composites was also examined. The objectives have been successfully achieved. In general, small size rice husk fiber reinforced polyester composites displayed better tensile and impact properties as compared to medium and large fiber size categories. Experimental analysis revealed that both fiber size and fiber weight fraction have a significant effect on the tensile and impact characteristics of rice husk fiber reinforced polyester composites.In all the three fiber size categories, tensile and impact strength increased steadily with increase in fiber loading up to 15 %wt, then decreased at 20 %wt. Unsaturated polyester resin yielded better tensile strength properties than rice husk fiber reinforced composites, whereas the impact properties of the composites were superior to those of unsaturated polyester resin. The methods used in this research provide a roadmap for further study in optimizing fiber size and weight fraction parameters during the production of composite materials made from other plant fibers. Ample time and effort should also be invested in modalities for industrial scale manufacture of composites using rice husk fibers.
ACKNOWLEDGEMENTS
The authors of this work are pleased to acknowledge and appreciate the entire administration of Dedan Kimathi University of Technology (DeKUT), for fully funding this research, and for granting access to the lab facilities, tools and equipment which were used.
References
[1] | P. Totiger, M. Gothe, S. Nagavi, and R. Mulimani, “Comparative study of mechanical and thermal characterization of glass/carbon hybrid composite,” Int. J. Res. Eng. Technol., vol. 04, no. 07, pp. 300–307, 2015. |
[2] | M. Sanjay and B. Yogesha, “Studies on Mechanical Properties of jute/E-glass fiber reinforced epoxy hybrid composites,” J. Miner. Mater. Charact. Eng., vol. 4.0, no. January, pp. 15–25, 2016. |
[3] | K. P. Kumar and A. S. J. Sekaran, “Some natural fibers used in polymer composites and their extraction processes: a review,” J. Reinf. Plast. Compos., vol. 33, no. 20, pp. 1879–1892, 2014. |
[4] | A. Chauhan and P. Chauhan, “natural fiber reinforced composite: a concise review article,” J. Chem. Eng. Process Technol., vol. 03, no. 02, pp. 2–4, 2012. |
[5] | A. Onyango, “Exploring options for improving rice production to reduce hunger and poverty in Kenya,” World Environ., vol. 4, no. 4, pp. 172–179, 2014. |
[6] | G. Ndiritu, “Estimating rice production efficiency in Kenya: a case study of Mwea irrigation scheme.” |
[7] | E. Odhong, P. Wambua, and A. Mayaka, “Recycling and value addition to thermoplastic wastes to produce plant fiber composites,” Trade Sci. J., vol. 8, no. 1, pp. 1–6, 2012. |
[8] | K. Rassiah, T. Sin, and M. Ismail, “A study on flexural and water absorption of surface modified rice husk flour/E-glass/polypropylene hybrid composite,” IOP Conf. Ser. Mater. Sci. Eng., vol. 152, no. 1, 2016. |
[9] | C. Vasanta, P. Udayakumar, and Ramalingaiah, “Mechanical characterization of coir and rice husk reinforced hybrid polymer composite,” Int. J. Innov. Res. Sci. Eng. Technol., vol. 2, no. 8, pp. 3779–3786, 2013. |
[10] | V. Joshi and A. Chaudhary, “Physical & morphological properties of rice husk epoxy composites,” Int. J. Res. Emerg. Sci. Technol., vol. 8, no. 228, pp. 2015–2015, 2015. |
[11] | A. Mishra and D. Padhee, “Evaluation of mechanical properties of rice husk-fly ash-epoxy hybrid composites,” IOSR J. Mech. Civ. Eng., vol. 14, no. 03, pp. 91–99, 2017. |
[12] | N. Bisht and P. Gope, “Mechanical properties of rice husk flour reinforced epoxy bio-composite,” Int. J. Eng. Res. Appl., vol. 5, no. 6, pp. 123–128, 2015. |
[13] | M. Islam, H. Kabir, F. Ahmed, and A. Gafur, “Study and characterization of rice husk ash with polyester resin composite,” Daffodil Int. Univ. J. Sci. Technol., vol. 11, no. 1, 2016. |
[14] | E. Odhong, A. Muumbo, and A. Mayaka, “Improving impact strength recovery of fractured and healed rice husks fibre reinforced polypropylene composites,” Int. J. Eng. Res. Appl., vol. 6, no. 10, pp. 76–83, 2016. |
[15] | A. Borah, D. Suchiang, K. Debnath, M. Alam, and M. Muralidhar, “Studies on design and fabrication of polymer based composite materials with fish scale reinforcement,” J. Mech. Civ. Eng. (IOSR-JMCE, no. Special Issue, pp. 6–11, 2017. |
[16] | D. Montgomery, Design and analysis of experiments, 8th Edition. 2013. |
[17] | C. Atuanya, S. Olaitan, T. Azeez, C. Akagu, O. Onukwuli, and M. Menkiti, “Effect of rice husk filler on mechanical properties of polyethylene matrix composite,” Int. J. Curr. Res. Rev., vol. 5, no. 15, 2013. |
[18] | H. Rozman, L. Musa, and A. Abubakar, “The mechanical and dimensional properties of rice husk-unsaturated polyester composites,” Polym. Technol. Eng., vol. 44, pp. 489–500, 2005. |
[19] | M. Ofem, M. Umar, and F. Ovat, “Mechanical properties of rice husk filled cashew nut shell liquid resin composites,” J. Mater. Sci. Res., vol. 1, no. 4, pp. 89–97, 2012. |