Ganiyu K. Latinwo1, Olabanji R. Ogunleye1, Samuel E. Agarry1, Ebenezer O. Dada1, Idowu A. Tijani2
1Department of Chemical Engineering, Ladoke Akintola University of Technology, Ogbomoso, Nigeria
2Department of Chemical Engineering, University of Ilorin, Ilorin, Nigeria
Correspondence to: Ganiyu K. Latinwo, Department of Chemical Engineering, Ladoke Akintola University of Technology, Ogbomoso, Nigeria.
Email: |  |
Copyright © 2018 The Author(s). Published by Scientific & Academic Publishing.
This work is licensed under the Creative Commons Attribution International License (CC BY).
http://creativecommons.org/licenses/by/4.0/

Abstract
Surface modifications of calcium carbonate as filler in flexible polyurethane foams were investigated. In order to improve the dispersion and interfacial bonding between the calcium carbonate and polyurethane matrix, the surface of calcium carbonate was modified using 0.5 wt% stearic acid and 2.72 wt% titanate coupling agent. The influence of modification on the surface of calcium carbonate was characterized with FT-IR and SEM. The mechanical properties of flexible polyurethane foam containing various amount of modified and unmodified calcium carbonate were evaluated by measuring the indentation force deflection, compression set, tensile strength and elongation at break. It was found that the modified calcium carbonate became organophilic as a result of modification. Addition of modified calcium carbonate to polyurethane foam increased the tensile strength while, the compression sets, elongation at break and foam hardness decreased.
Keywords:
Stearic acid, Titanate, Flexible polyurethane foam, Calcium carbonate, Spectroscopy
Cite this paper: Ganiyu K. Latinwo, Olabanji R. Ogunleye, Samuel E. Agarry, Ebenezer O. Dada, Idowu A. Tijani, Effect of Stearic Acid and Titanate Coupling Agent Modified Calcium Carbonate on Mechanical Properties of Flexible Polyurethane Foam, International Journal of Composite Materials, Vol. 8 No. 4, 2018, pp. 91-96. doi: 10.5923/j.cmaterials.20180804.02.
1. Introduction
Flexible polyurethane foams are open cell structure polymer material produced by reaction of diisocyanate with polyols and other low molecular weight materials as additives. The major raw materials (polyol and isocyanate) for the production of flexible polyurethane foam are petrochemical based and highly costly resulting in exorbitantly priced flexible polyurethane products. In order to reduce cost and improve some base property such as surface hardness, calcium carbonates found abundantly in rock are used as filler in foam formulation. However, calcium carbonate is inorganic and due to its hydrophilic surface which renders it incompatible with hydrophobic surface of polyurethane, it agglomerates and do not form uniform dispersion in polymer moieties [3]. Manifestation of the inadequacies results in polyurethane foam with poor mechanical properties [10]. To reduce agglomeration and improve dispersion of calcium carbonate in foam matrix, the surface of the inorganic material can be made organophilic through modification by addition of organic compounds (surface modifiers) such as titanate, fatty acids, silane, salicylates, phosphonates etc. Surface modification improves impact strength and aspect ratio of filler. It prevents phase separation and enhances interfacial bonding with chemically dissimilar polymer matrix [5]. In the present work, the surface of calcium carbonate was modified using stearic acid and titanate coupling agent and the influence of modification on the surface of the filler was investigated using FTIR and SEM. The effect of modified filler on the mechanical properties of medium density flexible polyurethane foam was studied.
2. Experimental
2.1. Materials
Mineral calcium carbonate with average particle size of 3.5μm was purchased from Success Glister Limited. The calcium carbonate was dried in an oven at 150°C for 10 h to remove moisture. Titanate coupling agent: Bis [2-[(2-minoethyl)amino]ethanolato][2-[(2-aminoethyl)amino]ethanolato-O](propan-2-olato) titanate was purchased from Feidianchem, China. Stearic acid, Isopropyl alcohol, ethanol and methanol were obtained from Labtrade. Polypropylene glycol (PPG), Toluene Diisocyanate (80/20), Amine catalyst (TEGOAMIN* BDE), Silicone oil (TEGOSTAB) and Tin catalyst (KOSMO* 29) were obtained from Unifoam, Ilorin, Nigeria.
2.2. Surface Modification of Calcium Carbonate
2.2.1. Modification Using Titanate Coupling Agent
Calcium carbonate was modified with titanate coupling agent using wet solution method [1]. 35g of calcium carbonate and 100 ml of isopropyl alcohol were stirred in a beaker for 10 min. A dispersed solution of 0.952g titanate coupling agent (2.72 wt%) in isopropyl alcohol was added dropwise into calcium carbonate mixture under continuous stirring for 30 minutes. The mixture was dried in an oven for 24 h at 100°C. The resultant product was denoted as T-GCC.
2.2.2. Modification Using Stearic Acid
Calcium carbonate was modified with stearic acid using wet solution method [8]. 0.175 g (0.5 wt%) of stearic acid and 100 ml of ethanol were mixed and stirred in a 250 ml beaker for 10 min at 68°C. 35 g of dried GCC was subsequently added under continuous stirring for 30 min. The mixture was dried in an oven at 60°C for 24 h. The resultant product was denoted as S-GCC. FT-IR spectroscopy was carried out to determine the presence of organic layer on the surface of the modified calcium carbonate. Samples were prepared by mixing small quantity of modified and unmodified calcium carbonates with potassium bromide (KBr) which were then compressed into thin pellets. The IR spectra were recorded between the ranges of 4000 - 400 cm-1.Scanning electron micrographs were examined to study the cell morphology of modified and unmodified calcium carbonates. The samples were treated with liquid nitrogen and then coated with gold. Images were taken on the scanning electron microscope (SEM) operated in the secondary electron mode at a 15 kV accelerating voltage.
2.3. Preparation and Production of Flexible Polyurethane Foam
Modified (S-GCC and T-GCC) and unmodified (GCC) filler reinforced flexible polyurethane foams were synthesized with the amounts of each chemical component chosen to obtain a target density of 24 kg/m3. The amount of filler in the foam formulations were varied from 15 to 25 php as shown in Table 1. The foam was produced using one shot technique. The mixture of polypropylene glycol and filler were stirred in a plastic bucket until there is complete homogenization. Silicone oil, water, Tin and amine catalyst were added simultaneously to the mixture and stirred continuously for 10 min. Toluene diisocyanate was then added to the mixture and the stirring continued for 10 s. The resulting mixture was poured immediately into a mould (22 × 20 × 17 in). After 10 min, the foams were removed from the mould and left to cure for 7 days.Table 1. Foam Formulations for production of flexible polyurethane foam 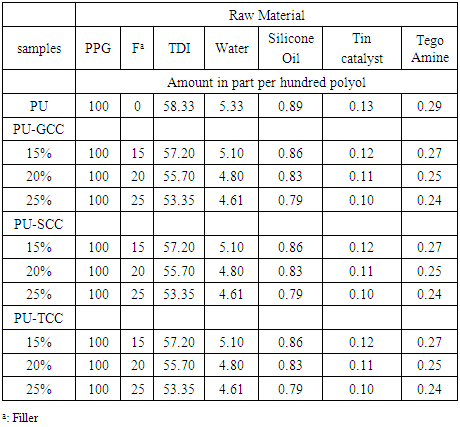 |
| |
|
Indentation force deflection of the foams were measured by depressing a foam sample of dimension 380 x 380 x 50 mm in an indentometer (ATI, testing machine) following the procedure described in ASTM D3574 with objective of determining the characteristic hardness of the filled and unfilled foams at various filler loadings. The indentation force at 65% deflection was recorded for the samples. The compression set, tensile strength and elongation at break were recorded at ambient temperature and 70°C for all the foam samples following the procedure of ASTM D3574. Three samples were measured for each of the test conducted and all the samples were cut from the same source along foam rise direction.
3. Results and Discussion.
3.1. Evaluation of Surface Modification Using FT-IR and SEM
Figure 1 shows the FT-IR spectra of unmodified calcium carbonate (GCC), stearic acid modified calcium carbonate (S-GCC) and titanate coupling agent modified calcium carbonate (T-GCC). The spectra of S-GCC show absorption band at 3293.93 cm-1 which is attributed to stretching vibrations of O-H group. The peak at 1090.24 cm-1 is that of an ester C-O bond [7]. The bond was created as a result of reaction between the stearic acid with free hydroxyl group present on the surface of the calcium carbonate. The absorption peak appearing at 2917.15 cm-1 and 2817.49 cm-1 are attributed to C-H asymmetric and symmetric of methylene group [13]. The characteristic asymmetric stretching appearing at 2359.89 cm-1 is ascribed to CO2 [17]. The spectra of T-GCC show a broad band at 3439.56 cm-1 which is due to stretching vibration of N-H groups [4]. The N-H is from the amino substrate which is part of organo-functional fragment of the titanate coupling agent used for modifying the calcium carbonate. The weak peak around 1302.37cm-1 is attributed to C-O-Ti vibration [6]. Figure 2 shows the cell morphology of the modified and unmodified calcium carbonate. The S-GCC and T-GCC cells are densely packed with less porosity compared to the GCC with particles that are loosely packed and of high porosity. With these characteristics, it is clear the surfaces of S-GCC and T-GCC have been modified.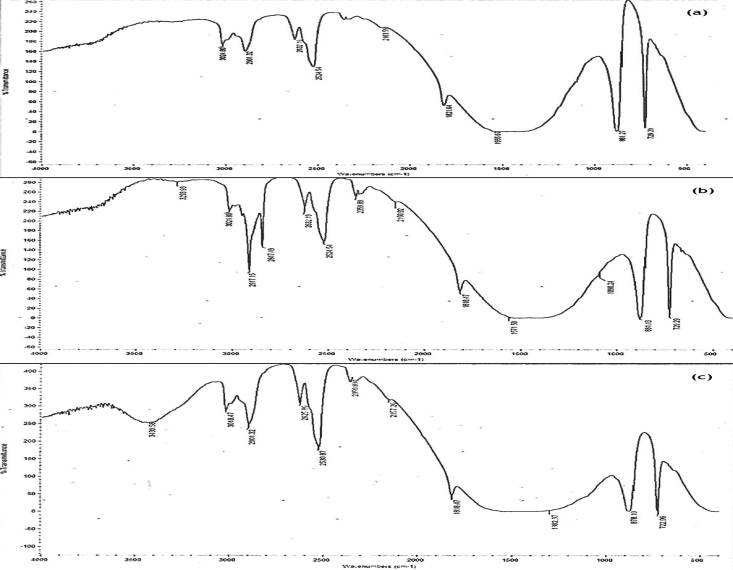 | Figure 1. FT-IR spectra of (a) GCC (b) S-GCC (c) T-GCC |
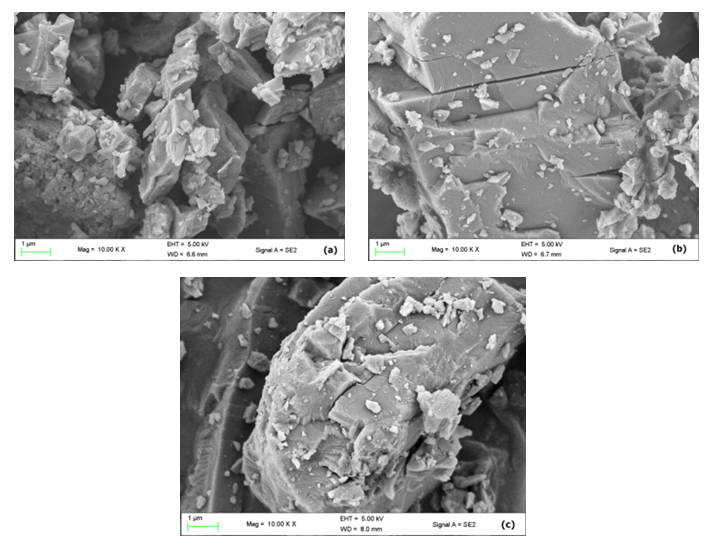 | Figure 2. SEM Image (a) GCC (b) S-GCC (c) T-GCC |
Figure 3 shows the indentation force deflection (IFD) of unfilled (PU) and filled flexible polyurethane foams containing unmodified filler (PU-GCC), stearic acid modified fillers (PU-SCC) and Titanate coupling agent modified fillers (PU-TCC). IFD measures foam hardness. Generally, the higher the Indentation force deflection values, the higher the foam hardness. The result revealed that IFD increases as the filler loading increases for PU-GCC, PU-TCC and PU-SCC foam samples. This shows that the presence of filler in foam increase the hardness compared to PU foam. The increase in foam hardness by filler is as a result of deposition of the filler on the cell window during foam growth which decreases the mobility of the soft segment in polyurethane matrix and thereby increases the foam hardness [9]. Also, PU-SCC and PU-TCC foam samples have lower IFD at all filler loading compared with PU-GCC due to more random distribution of filler in polymer matrix (higher dispersion) [14]. At 15 wt% of filler, the 65% IFD of PU-GCC, PU-SCC and PU-TCC are 351.8kN, 310.9kN and 254.2kN respectively. Furthermore, PU-TCC foam has lower IFD compared to PU-SCC foam at all filler loading, also, due to more random distribution of filler in polymer matrix (higher dispersion) [14].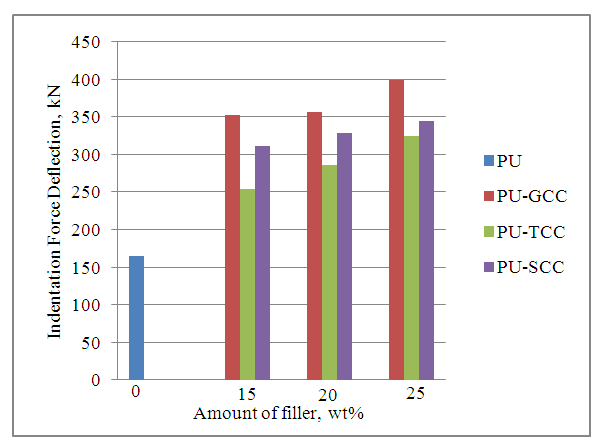 | Figure 3. Effect of filler on the 65% Indentation force deflection |
At 15 wt% of filler, the 65% IFD of PU-GCC, PU-SCC and PU-TCC are 351.8kN, 310.9kN and 254.2kN respectively. Figure 4 shows the compression set (CS) variation with the amount of filler. Compression set measures the deformation of foam when compressed at controlled time and temperature. The variation in compression set was obtained at room temperature and heat aging (70°C) after 22 h of compression. For the foam samples, the property increased with increase in filler loading at room temperature and heat aging condition. This indicates that fillers increase the percentage reduction in the final height of the foam after compression, due to buckling of the foam cell wall by the filler and chain slippery during compression [11]. Further, PU-TCC and PU-SCC have lower compression set compared to PU-GCC as a result of chemical reaction between the modifier and the polyurethane which overcomes the chain slippery that occurred with the unmodified filler [16]. The compression set of all foam samples at heat aging is higher than compression set at room temperature. This is due to deformation of the surface and internal layers of the foam as a result of aging.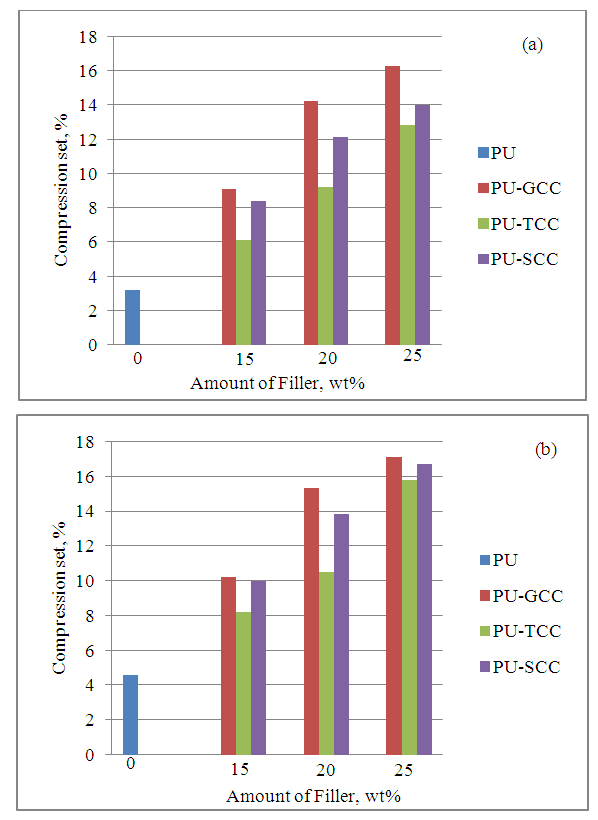 | Figure 4. Effect of filler on compression set (a) at room temperature (b) at heat aging |
Tensile strength (TS) measures the amount of stress required to break foam when pulled. Figure 5 shows the tensile strength for the foams at different filler loadings. The result revealed that tensile strength of PU-GCC reduces as the filler loading increases at both room temperature and heat aging conditions due to uneven dispersion of the filler, which create stress concentrations in the foam matrix [9]. However, tensile strength of PU-SCC and PU-TCC foams increased compared to PU-GCC and PU foam samples at both room temperature and heat aging. This trend is as a result of the hydrophobic characteristics of the modifiers which promote strong interaction and adhesion between the modified fillers and the polyurethane foam matrix [12] and also due to cross-linking that occur between the modified filler and polyurethane [2]. Moreover, at all filler loading, the tensile strength of PU-TCC and PU-SCC foam at heat aging is higher than the tensile strength at room temperature. This was caused by the complete cross-linking between the modifiers and the polyurethane polymer and loss of volatile matters that occurs during aging [15]. The PU-TCC has a high tensile strength at all filler loading than PU-SCC at aging and room temperature.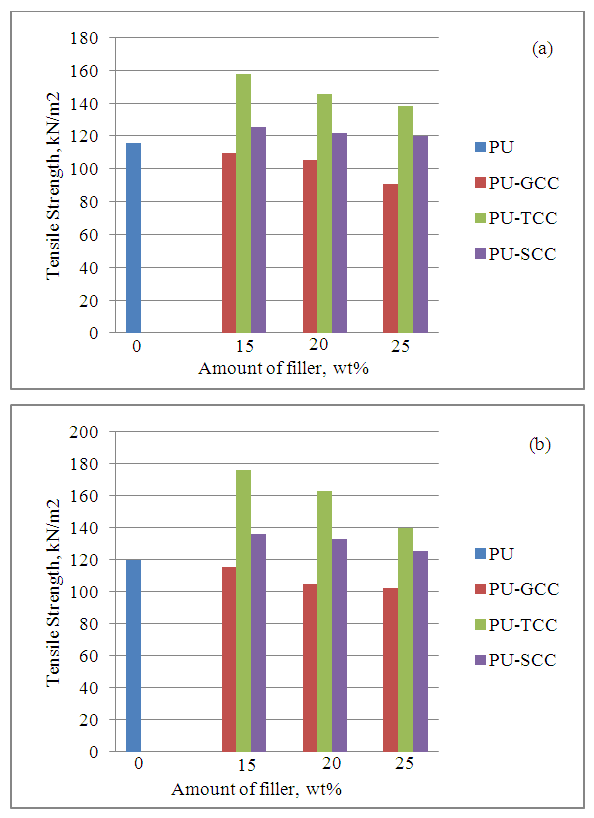 | Figure 5. Effect of filler on tensile strength (a) at room temperature (b) at heat aging |
From Figure 6, the elongation at break at room temperature and heat aging (70°C) for all foam samples decreases as the filler loading increases.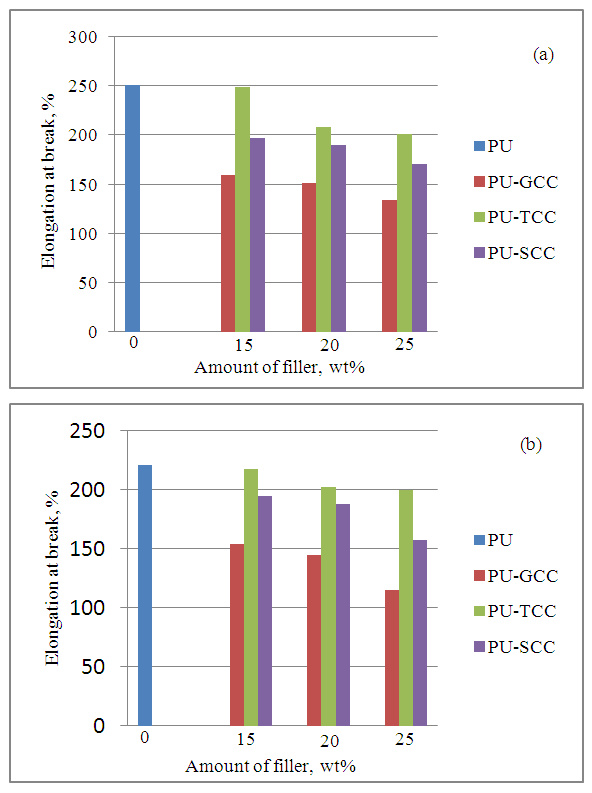 | Figure 6. Effect of filler on elongation at break (a) at room temperature (b) at heat aging |
The trend was attributed to the stress created in the foam matrix due to presence of filler [9]. Also, at all filler loading, the elongation at break at heat aging is lower than the elongation at break at room temperature for all foam samples. This was attributed to the complete cross-linking that occured during aging between the modifiers and the polyurethane polymer and loss of volatile matters [15]. At 15 wt%, the elongation at break of PU-GCC, PU-SCC and PU-TCC are 153.9%, 194.8% and 217.2% at aging and 159.8%, 196.4% and 249.1% at room temperature respectively. The PU-TCC has a high elongation at break at all filler loading than PU-SCC at heat aging and room temperature.
4. Conclusions
In this study, ground calcium carbonate (GCC) particles were modified with 0.5 wt% stearic acid and 2.72 wt% titanate to render the GCC surface hydrophobic via wet solution methods. Flexible polyurethane /GCC composite foams containing various amount of modified and pristine GCC were prepared using a one-shot foaming technique. FT-IR patterns showed presence of ester C-O on the S-GCC which was formed from the reaction of stearic acid with the free OH group on the surface of the GCC, and the presence of C-O-Ti which precipitated on the surface of T-GCC particles forming a discontinuous coating layer. It was also shown through SEM that the S-GCC and T-GCC contained densely packed cells compared to pristine GCC. Mechanical properties of the polyurethane foam samples were affected by the incorporation of GCC in such a way that the IFD increased with increase in GCC loadings for the PU-GCC, PU-SCC and PU-TCC. Compared to pristine PU, all the reinforced PU show improved IFD. Modification of the GCC to some extent have appreciable influence on the IFD of PU foam, although IFD of PU-GCC was superior to that of PU-SCC and PU-TCC. Compression sets were affected in a similar manner for the room temperature and heat ageing conditions. Tensile strength of the pristine PU foam was good and those of the reinforced PU foam with GCC, modified or not, decreased with increase in GCC loadings. Among the reinforced PU foam, T-GCC has the best tensile strength property. Similar trend as of tensile strength was observed for the elongation at break for the foam samples. In this regard, one can conclude that the modified calcium carbonate, having better dispersion in PU foam matrix improve the mechanical properties of PU/GCC composite foam.
References
[1] | Alkadasi N. A. N., Bhimrao D. S., Hundiwale D.G., and Kapadi D. R. 2004. Studies on Effect of Titanate Coupling Agents on the Mechanical Properties of Clay Filled Chloroprene Rubber. Journal of Scientific and Industrial Research 63(10): 830 – 834. |
[2] | Balköse D. 2015. Influence of Filler Surface Modification on the Properties of PP Composites. 1st ed. edited by Weinheim V. M.: Wiley-VCH Verlag GmbH & Co. |
[3] | Buasri A., Chaiyut N., Borvornchettanuwat K., Chantanachai N., and Thonglor K. 2012. Thermal and Mechanical Properties of Modified CaCO3 / PP Nanocomposites. 6(8): 689 – 692. |
[4] | Vasconcelos D. C. L., Costa V. C., Nunes E. H. M., Sabioni A. C. S., Gasparon M., Vasconcelos W. L.. 2011. Infrared Spectroscopy of Titania Sol-Gel Coatings on 316L Stainless Steel. Materials Sciences and Applications. 2(1): 1375 – 1382. |
[5] | Elshereksi N. W., Ghazali M., Muchtar A., and Azhari C. H. 2017. Review of Titanate Coupling Agents and Their Application for Dental Composite Fabrication. Dental Materials Journal. 36(5): 539 – 552. |
[6] | Garcia-hernandez M. 2012. Luminescent System of Ln Doped BaTiO3 nanostructured Powders and Films Prepared by Soft Chemical Routes. National Polytechnic Institute, Mexico. |
[7] | Han S. J., Hyung-il L., Han M. J., Byung K. K., Anjanapura V. R. and Kakarla R. R. 2014. Graphene Modified Lipophilically by Stearic Acid and Its Composite with Low Density Polyethylene. Journal of Macromolecular Science. 53(14): 1193 – 1204. |
[8] | He Y., Yi F., Pingya L., and Qiangbin Y. 2015. Synthesis of Stearic Acid Modified Ground Calcium Carbonate (SA-GCC) Hybrid Material and Properties of SA-GCC/Epoxy Composites Coating. Russian Journal of Applied Chemistry. 88(6): 962 – 969. |
[9] | Latinwo G., Aribike D., Oyekunle L., Susu A, and Kareem S. 2010. Effects of Calcium Carbonate of Different Composition and Particle Size Distributions on the Mechanical Properties of Flexible Polyurethane Foam. Nature and Science. 8(9): 92 – 101. |
[10] | Palimi M. J., Rostami M., Mahdavian M., and Ramezanzadeh B. 2014. Surface Modification of Fe2O3 Nanoparticles with 3-Aminopropyltrimethoxysilane (APTMS): An Attempt to Investigate Surface Treatment on Surface Chemistry and Mechanical Properties of Polyurethane/Fe2O3 Nanocomposites. Applied Surface Science. 32: 60 – 72. |
[11] | Park K., Gue-Hyun K., and Chowdhury S. R. 2008. Improvement of Compression Set Property of Ethylene Vinyl Acetate Copolymer/Ethylene-1-Butene Copolymer/ Organoclay Nanocomposite Foams. Polymer Engineering and Science. 48(6): 1183 – 1190. |
[12] | Pradittham A., Charitngam N., Puttajan S., and Atong D. 2014. Surface Modified CaCO3 by Palmitic Acid as Nucleating Agents for Polypropylene Film: Mechanical, Thermal and Physical Properties. Energy Procedia 56: 264 – 273. |
[13] | Salem I. A. S., Rozyanty A. R., Betar B. O., Adam T., Mohammed M., and Mohammed A M. 2017. Study of the Effect of Surface Treatment of Kenaf Fiber on Chemical Structure and Water Absorption of Kenaf Filled Unsaturated Polyester Composite. Journal of Physics. 908: 1 – 8. |
[14] | Mihajlovi S., Vučinić D., Sekuli Ž., Milićević S., and Kolonja B. 2013. Mechanism of Stearic Acid Adsorption to Calcite. Powder Technology. 245:208 – 216. |
[15] | Abbas T., Farzaneh S., Abdallah-Elhirtsi S., Esmaeillou B., Nony F., and Baron A. 2014. Thermal Aging Effect on Mechanical Properties of Polyurethane. International Journal of Polymer Analysis and Characterization 19(7): 571 – 584. |
[16] | Ping W. Y., Ma Y., Wang Y. Q., and Zhang L. Q. 2004. Effects of Characteristics of Rubber, Mixing and Vulcanization on the Structure and Properties of Rubber/Clay Nanocomposites by Melt Blending. Macromolecular Materials and Engineering. 289(10): 890 – 894. |
[17] | Zhuang G. V., Hui Y., Jr Philip N., Ross K. X., and Richard J. 2005. Lithium Methyl Carbonate as a Reaction Product of Metallic Lithium and Dimethyl Carbonate. California Digital Library. 1 – 24. |