Joan J. Kiptarus
Department of Mechanical & Production Engineering, Moi University, Eldoret, Kenya
Correspondence to: Joan J. Kiptarus, Department of Mechanical & Production Engineering, Moi University, Eldoret, Kenya.
Email: |  |
Copyright © 2017 Scientific & Academic Publishing. All Rights Reserved.
This work is licensed under the Creative Commons Attribution International License (CC BY).
http://creativecommons.org/licenses/by/4.0/

Abstract
This study aimed at developing cardboard composite made from bagasse and PP material that will be suitable for use as decorative ceiling boards, walls and floors of a home, office or commercial building in order to reduce the amount of plastics from our environment and conserve our natural resources such as forests from depletion. This composite was compared to the already existing ceiling materials in the market. A composite cardboard of melted waste PP as the matrix was reinforced with bagasse fibers after being treated by alkali solution (NaoH) were prepared and the mechanical properties such as Compressive strength, Impact strength, Flexural strength, Material toughness and Machining were investigated. Water absorption was also studied. From the results obtained, it was observed that the compressive strength, flexural strength, Impact strength and toughness of the treated bagasse reinforced PP cardboard increased with fibre loading increment. It was also observed that the rate of absorption in the composite increases as the percentages of fibres increases, however the rate of water absorption was less compared to that of soft ceiling board and hard ceiling board. Machining operations such as drilling, grinding, milling and cutting can also be performed on the composite. It is clear that the composite with 30% fibre loading showed the best performance in all the tests. It is evident that the composite of PP reinforced bagasse can produce an excellent alternative cardboard material for industrial application.
Keywords:
Bagasse, Polypropylene, Cardboards, Composites, Fibre
Cite this paper: Joan J. Kiptarus, Development of Cardboards from Waste Plastics (PP) and Bagasse, International Journal of Composite Materials, Vol. 7 No. 5, 2017, pp. 131-135. doi: 10.5923/j.cmaterials.20170705.01.
1. Introduction
In Kenya, construction industry has over the years been heavily dependent on wood as construction of materials such as ceiling boards, particle board, block board and floor tiles among others (Kimutai et al, 2014) and less has been done to develop more alternative materials to replace wood in order to save our forests from depletion.More recently natural fibers have been employed in combination with plastics. Availability of natural fibres in Kenya such as Bagasse, Sisal, Pineapple, Bamboo, Banana etc. are abundant and this gives attention on the development of natural fibre composites primarily to explore value-added application avenues.Polythene bags and plastics, including PVC items, make up approximately 225 tonnes out of the 2000 tonnes of solid waste generated daily in Nairobi, Kenya (KAM, 2003). This represents about 11% of total waste generated daily. This results in lot of plastics as wastes in our environment that are never recycled but rather end up in landfills or in dumpsites. This plastic bags poses the biggest challenge to solid waste management in Kenya (Odhiambo et al, 2014) and so this calls for proper disposal.Natural fibres reinforced with polymer composites have gained more interest because of their biodegradable, less expensive, light weight, easy processing, high specific modulus and also environmentally appeal (Mustafa et al, 2013). Plant fibres from agricultural crops are renewable materials which have potential for creating green products and replacing synthetic materials which have potential for creating composites panel (Khalil et al, 2001). According to all the natural fibers listed, bagasse is biomass remaining after sugarcane stalks are crushed to extract their juice and today, bagasse is used as a major raw material for fuel, as well as for pulp and paper production, in addition to being a reinforcement material in value-added composite panel production. Transforming bagasse into high-quality panel products provides a prospective solution because it has a potential as the core material replacing high density and expensive wood-based fiberboard (Mustafa et al, 2013).This study aimed at developing a composite made of polypropylene matrix and sugarcane bagasse fibres of wt% (20, 25 and 30) materials that can be used as cardboards for construction purposes suitable for floors, walls, ceilings of homes. The samples of the composites were designed and fabricated by hot press. The tests that were carried out include; Compression test, Bending/flexural test, Impact test, Toughness test and Water absorption test. Furthermore, the samples of the composite were compared to already existing ceiling materials in the market to determine their stiffness, strength and mode of failure.
2. Experimental Analysis
Raw MaterialsSugarcane bagasse was collected from Mumias Sugar Company Ltd after juice had been extracted. They were neutralized by soaking in 70% ethanol for an hour with a volume ratio of ethanol (litre) to the weight of fibers (kg) as 2:1. The aim of neutralization was to prevent bagasse from fermentation. Neutralized sugarcane bagasse was then dried in an open air for 6 hours. After drying, the bagasse were soaked in alkaline solution (NaOH). Treated bagasse was rinsed with distilled water few times and they were ensured clean when the pH level of rinsed water reached 7 as indicated by pH meter. They were dried in an open air for 6 hours followed by oven dried at 50°C for 1 hour to remove all moisture content from the fibres. The dried bagasse was crushed using the universal power blender. The fibres were sieved using sieve test equipment. The sieve size of 3.25mm was used to obtain small size fibers to design a composite with consistent properties. A magnet was passed over the material to remove any ferromagnetic metals present and finally weighed.Thermoplastic resins (Plastics-polypropylene PP) used were waste plastics collected from the Moi University (Soweto dumpsite). The collected plastics were first cleaned using warm water and soap to remove dirt, paper labels, oils, fats etc. They were sorted according to the type of plastic in order to remain with the PP plastics. The PP plastics were further sorted according to color to act as dye and size. To achieve homogeneous mixture between bagasse and PP, the Polypropylene plastics were cut into small square pieces of approximately 20mm x 20mm and left to dry in the open air and finally weighed.
2.1. Samples Preparation and Material Testing
Preparation of composite and the mixed proportionsSugarcane Bagasse and PP were weighed to prepare composite samples with various wt. % ratio of bagasse to PP of 20/80, 25/75, and 30/70. Each composition was prepared in 1000 grams total weight per mixture. The mixture was then dried for 20 minutes using an oven with the temperature of 70°C before the samples were prepared with a hot press.Hot pressA steel mold was designed to produce the composite panel with length of 150mm, width of 150mm and thickness of 10mm. The steel mold was preheated for 3 minutes. Each mixture was placed on the steel mold ready to be formed into composite sheet by hot pressing using a pressure of 150MPa at heating temperature of 175°C for 3 minutes. After pressing, each sample is cooled for 3 minutes. Cooling process make the compound hardened, so that it can be removed without distortion when the mould is opened.Material testingMechanical property of the final composites was evaluated using compression test, bending/flexural test, impact and hardness test, material toughness and machine tests such as drilling, grinding, sawing/cutting, and hammering/nailing. Furthermore the composite samples were compared with that of wooden cardboards available in the market. The samples were identified as: Cardboard (soft ceiling board) - SPECIMEN C, Cardboard (hard ceiling board) - SPECIMEN D and Composite- SPECIMEN F. The composite samples had various wt. % ratio of Bagasse to PP of 20/80, 25/75, and 30/70, this was done based on previous works done. This were identified as: SPECIMEN F20% - Bagasse to PP ratio is 1:4, SPECIMEN F25% - Bagasse to PP ratio is 1:3 and SPECIMEN F30% - Bagasse to PP ratio is 3:7.Compression TestThe compressive strength of the materials was determined by use of the 100 KN manually controlled universal testing machine as shown in the Fig.1. Compression test determine the behaviour of materials under crushing loads. The specimen is compressed and deformed at various loads and the recorded. 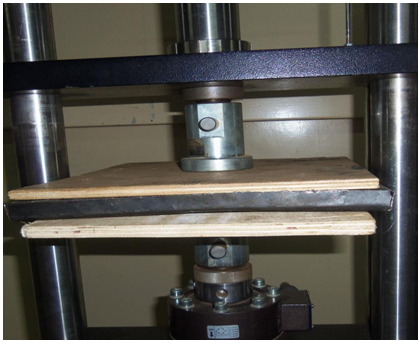 | Figure 1. Specimen under compression test |
Bending /Flexural TestFor flexure testing, the metal grips on the universal hydraulic testing machine were replaced by a three point test jig. The flexure test method measures the behavior of material subjected to simple beam loading. Maximum stress and maximum strain is calculated for increments of load. Results were plotted in stress- strain diagram. The force required to bend the specimen was then recorded. 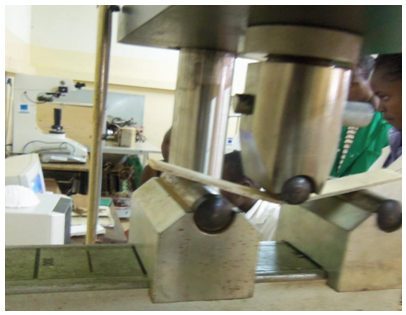 | Figure 2. Specimen under bending test |
Impact TestImpact testing is the ability of an object to resist high rate loading. It is determined by the energy absorbed in fracturing a test speed at high rate velocity. The machine used was the Pendulum Impact testing machine, shown below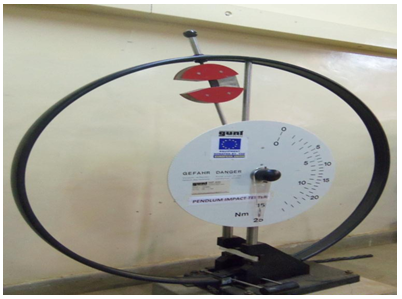 | Figure 3. Specimen under Impact test |
Hardness TestHardness test was carried out using the Rockwell Hardness testing machine. The test was done using steel indenter.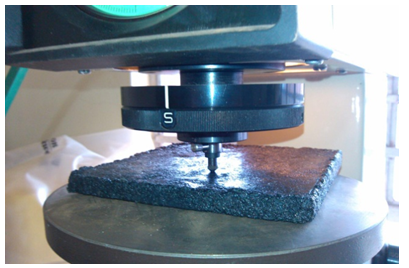 | Figure 4. Specimen under hardness test |
Water AbsorptionThis test was done to determine the amount of water absorbed by the composite material when immersed in water for a stipulated period of time. The sample test specimen samples of 150mm x 150mm were prepared and dried in the oven, and then allowed to cool. The specimens were then weighed on the electronic weighing machine to the nearest 0.001g before soaking in water. After 5 days, the specimens were removed from water and weighed again. With 5 days intervals the specimens were weighed again and returned to the water. The results were recorded and a graph of water absorption against number of days of different specimens was plotted.
3. Results and Discussion
Compression TestThe maximum value in the stress – strain graph of each specimen was used to plot the above graph for comparison purpose. From the graph above, it shows that compressive strength increased with increase in fibre content. Specimen C and D showed a very small compressive strength compared to the specimens of F20%, F25% and F30% because specimen (F) made of varying fibre content could withhold more compressive force than wooden ceiling (Specimens C and D). It was observed that the composite with 30% fibres showed the best compressive strength than the other specimens.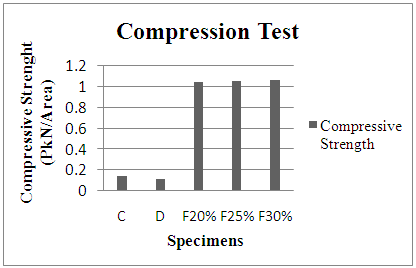 | Figure 5. Graph showing the compressive strength of the different specimens |
Bending/ Flexural TestFrom the above graph, specimen C recorded the lowest flexural strength of 1125MPa, followed by specimen D (1856MPa). For the composite specimens; Specimen (F20%) showed a low flexural strength of (1688MPa) due to higher percentage of polymer matrix compared to the other ratios. Specimen (F25%) showed an average flexural strength of (2810MPa). Specimen (F30%) showed a higher consistent flexural strength of (3150MPa). It was observed that the addition of fibre increased linearly with the flexural strength because it could withstand more bending loads, hence it could not fracture easily. 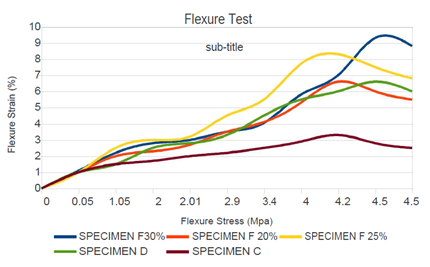 | Figure 6. Graph showing variation in flexure stress of different specimens |
Impact and High Rate TestThe material impact strength is a factor of its ability to absorb energy during plastic deformation. From the graph above it is clear that, the composite is tougher than the wooden cardboards. Also, the addition of bagasse fibres in the composite increases its impact strength. It can be concluded that bagasse fibres improves the impact strength of a composite.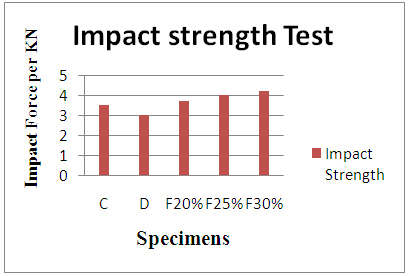 | Figure 7. Graph showing the Impact strength of the different specimens |
Toughness testFrom the graph above it is evident that the composite material (Specimen F) is tougher than the wooden cardboards (Specimen C (1.83 J/M3) and D (2.03 J/M3)). Also the toughness increases with increase in the bagasse composition in the material. Specimen F30% showed the highest toughness of 8.3 J/M3, while Specimen F25% recorded a toughness of 6 J/M3 and specimen F20% was 4 J/M3. Therefore material toughness increased with increase in fiber components.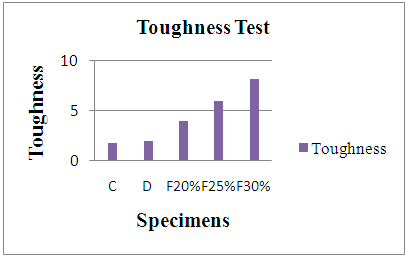 | Figure 8. Graph showing the Toughness test of the different specimens |
Water AbsorptionThe increase in mass is calculated as follows;
Where W= wet weightD= dry weightDensity of the samples can also be evaluated from the masses and the volumes.
According to the data recorded, it showed that water absorption in the composite ranged from 21% to 32% which is much less compared to wooden cardboards which was more than 65%. From the graph above, it can be observed that the water absorption in the composite is much less compared to wooden cardboards. This is because composite material has more tied bonding and fewer pores compared to wooden cardboards. On the other hand, the fiber content also affect the water absorption values which shows that composite with 20% fibres has less absorption compared with composite with 25% and 30% fibres. This shows that the presence of thermoplastic as a filler in the formulation seems to reduce the water absorption of the fiber board.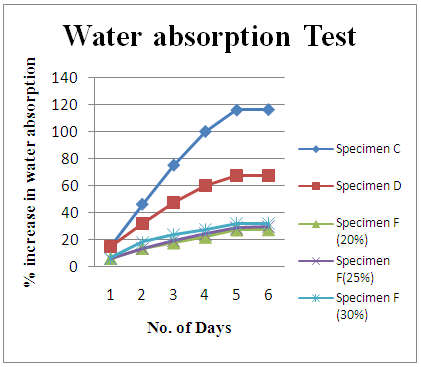 | Figure 9. Graph showing the Water absorption of the different specimens |
Machining TestsDrillingIt was possible to drill the composite and the resultant surface was not as distorted as it was with drilling cardboard ceilings. GrindingGrinding was done as a surface finish process. It is possible to grind the composite material. Cutting with a sawThe composite material could be easily cut. This is important because it allows the user to cut the ceiling to any desired shape. NailingA nail was hammered through the composite for joining purposes just as it is possible for wooden and cardboard ceilings. This allows for joining of the ceiling as desired.
4. Conclusions
Bagasse (sugarcane residue) is currently underutilized in Kenya and is therefore available to be used, bonded with a resin to make a composite material. Also the use of waste plastics to make the composite material is a very effective way of recycling plastics and hence removing them from our environment. Since bagasse fibre and waste plastics (PP) are easily available, this will cut down the cost of materials for manufacturing the composite hence becomes less expensive compared to other cardboards in the market.Experiments carried out evidently showed that the type and proportion of plastic resin and quantity of natural fiber used lends the finished composite its physical and mechanical properties which include: Resistance to impact, Resistance to absorption of watertight, Resistance to rot, ability to withstand bending, High impact strength and Toughness. Machining operations such as drilling, cutting, grinding and nailing can be performed on the composite without any problem. Polypropylene and bagasse fibres can be effectively used to develop a cardboard composite that can be used in construction industry and it that way it will be the effective way of disposing waste plastics and making use of the naturally available fibre (bagasse).
References
[1] | Bhagwan, D.A and J.B. Lawrence, (1990). Analysis and Performance of Fiber Composite, 2nd Edition. John Wiley and Sons, Inc. |
[2] | International Journal of Application or Innovation in Engineering & Management (IJAIEM) January 2013. |
[3] | Kenya Natural Cleaner Production Centre, (July 2006). Concept of Composites-Composite Material, Web based course. |
[4] | Matthews, F.L and R.D. Rawlings, (1994). Composite Material: Engineering and Science. Chapman and Hall. |
[5] | Odhiambo, O.R.; Musalagani, A.C Lyanda, N.J.; Ruth, S.J. (2014). The plastic waste menace in Kenya. |
[6] | A Nairobi City Situation, International Journal of Current Research vol. 6 Issue, 04, Pp.6175-6179. |
[7] | Ovidui Chiparus, (1993). Bagasse Fiber Composite for Production of Non-woven Materials. |
[8] | Punyapriya Mushra, (2004). Effect of environment on Mechanical Properties of Bagasse fiber Reinforced Polymer Composite. |
[9] | Sharma, P.C. (2008). Production Technology, 7th Edition. S. Chand Publication. |
[10] | Stephen K. Kimutai, Zachary O.Siagi, Joan J. Kiptarus, Anthony D. Kibet, Comparative Study of Composite Made from Ensete False Banana Fibre and Polyethylene with Block Board, Journal of Energy Technologies and Policy, Vol. 4, No. 12, (2014), pp.48-53. |
[11] | Verma, D.; Gope, P.C; Maheshwari, M.K.; Sharma R.K (2012). Bagasse Fiber Composite, A Review, Journal of mater. Environ. Sci. 3(6) 1079-1092 ISSN: 2028-2508. |