D. Jani Christal Dhas1, S. Senthilnathan1, Gokul Manivannan1, N. Azhagesan2
1Assistant Professor, Department of Mechanical Engineering, Saveetha Engineering College, Chennai, India
2Professor & Principal, Cape Institute of Technology, Tirunelveli, India
Correspondence to: D. Jani Christal Dhas, Assistant Professor, Department of Mechanical Engineering, Saveetha Engineering College, Chennai, India.
Email: |  |
Copyright © 2017 Scientific & Academic Publishing. All Rights Reserved.
This work is licensed under the Creative Commons Attribution International License (CC BY).
http://creativecommons.org/licenses/by/4.0/

Abstract
Commercially availed implants in the bio-medical region were not comforted on its material cost. In order to overcome this risk, the material of poly-tetra-fluoro-ethylene (PTFE) has been identified because of its excellent properties like biocompatibility, corrosion resistance, prevention on the chemical reaction and comparatively lower cost. But the wear rate of PTFE is not capable of preventing the material destruction due to cyclic load developed in the human body. So, an improved wear resistance of PTFE may enrich the suitability of PTFE to replace some other bio-implants. Thus, wear resistance can be improved by adding alumina particles as a wear resistive agent. PTFE - alumina particles were blended in various compositions like 90-10%, 85-15% and 80-20% respectively and the samples were prepared by using hot press compression molding technique. At the end, the wear behavior can be evaluated by using a pin on disc wear tester against steel counter-face. After evaluation, the wear rate of various compositions was compared and plotted in the graph. The improved proportion of PTFE-alumina composite will be proposed for medical applications.
Keywords:
PTFE-alumina, Wear rate, Bio-implants, Hot Press Compression Molding, Pin on disc
Cite this paper: D. Jani Christal Dhas, S. Senthilnathan, Gokul Manivannan, N. Azhagesan, Extensive Investigation in Wear Behavior of Alumina-PTFE Composite for Medical Implant Applications, International Journal of Composite Materials, Vol. 7 No. 4, 2017, pp. 115-119. doi: 10.5923/j.cmaterials.20170704.01.
1. Introduction
Polymers are mostly found as ideal matrix material, they are fit for easy processing, lightweight and that offers some valuable mechanical properties. The different class of polymers used as matrix materials in the major applications is thermoset and thermoplastics. Thermoset will produce a well-bonded 3D-molecular structure after curing. These are forced against melting but decompose during hardening. They can be retained partly cured condition for a prolonged period of time. They are most suited for Composites that supports most of the engineering applications. The present scenario shows that an epoxy, polyesters, phenolic and polyamides are widely used thermo-set polymers.The biomaterial is a material which is found separately or composed by two or more bio-comfortable material. These materials are purposely made for enriching the strengthening properties of the matrix that was used in the organic substance but always providing biocompatibility. The present scenario derives that the polymer contained biomaterials have a signification role in many applications. In case of the reinforcement, this could be include plant fibers such as cotton, flax, hemp, fibers from recycled wood, fibers from recycled waste paper and by-products from food crops. Matrices may be polymers, which is derived from renewable resources like vegetable oils in earlier days. But nowadays synthetic and fossil-derived polymers are preponderated and may be either virgin or recycled thermoplastics such as polyethylene, polypropylene, polystyrene and polyvinyl chloride, unsaturated polyesters, phenol formaldehyde and epoxies. The commonly used biomaterials are discussed below:
1.1. Stainless Steel (alloy of Ni, Fe, Cr, Mn) (316L grade)
Due to the durability and higher corrosion resistance property of the Stainless steel material will encourage the usage it on surgical tools and medical equipment. In addition, surgical implants such as bone reinforcements and replacements (e.g. hip sockets and cranial plates) are made with special alloys formulated to reduce corrosion, mechanical wear, and biological reactions. A possible application of stainless steels is cranial plates, orthopedic fracture plates, dental implants, spinal rods, joint replacement prostheses, stents and catheters.
1.2. Cobalt-Chromium-Molybdenum
Another material Cobalt-Chromium (Co-Cr) alloy is most commonly used to make artificial joints like knee joints, hip joints on because of the higher wear resistance and biocompatibility. Co-Cr alloys tend to be corrosion resistant, which reduces complication with the surrounding tissues when implanted, and chemically inert that they minimize the possibility of irritation, allergic reaction, and immune response. Cobalt-Chromium (Co-Cr) alloy has also been widely used in the manufacture of the stent and other surgical implants as Co-Cr alloy demonstrates excellent biocompatibility with blood and soft tissues. Few cases cobalt-chromium-molybdenum (CoCrMo), cobalt-nickel-chromium-molybdenum (CoNiCrMo) is also used as implants. The alloy is a commonly used as a metal framework for dental partials.A possible application of these alloys is orbit reconstruction, dental implants, orthopedic fracture plates, heart valves, spinal rods, joint replacement prostheses.
1.3. Nickel Titanium Alloys
Nitinol is the other name of Nickel Titanium Alloys. It is an element of shape memory alloy which is highly biocompatible and has properties suitable for the development of orthopedic implants. Due to Nitinol's unique properties, it has seen a large demand for use of less-persistent medical devices. Nitinol tubing is commonly used in catheters, stents, and super-plastic needles. This alloy is very useful in dentistry, especially in orthodontics for wires and brackets that connect the teeth. It is also used in endodontic mainly during root canals for cleaning and shaping the root canals. During colorectal surgery, it is used in various devices for the purpose of reconnecting the intestine after the pathology is removed. Nitinol stents are another significant application of this alloy in the medicinal field. Nitinol wires can be used for marking and locating breast tumors. The use of Nitinol tubing for various medical purposes is increasing in popularity.
2. Material for Experiment
In this chapter we are going to study about the characteristics of materials used for this experiment. PTFE is the major element of the composite where as Alumina powder is used as a minor element. These are identified by some extraordinary behaviors behind it.
2.1. Polytetrafluoroethylene
Polytetrafluoroethylene is called as PTFE. It is a tough, waxy, nonflammable synthetic powder produced by the polymerization of tetrafluoroethylene. It also developed by such trademarks as Teflon, Fluon, Hostaflon, and Polyflon. PTFE is distinguished by its slippery surface, high melting point and resistance to attack by almost all chemicals. PTFE is a fluorocarbon solid, with high molecular weight compound consisting wholly of carbon and fluorine. PTFE is hydrophobic: neither water nor water-containing substances wet PTFE. PTFE has one of the lowest coefficients of friction against any solid. So it is suitable for coating over nonstick cookware for consumer’s convenience. The most commercial applications of PTFE is to use as a coating element of the home appliances, production of industrial products like bearings, pipelines, and parts for valves and pumps. It is also used for the production of wiring in aerospace and computer applications, act as an insulator of cables and connector assemblies, thread seal tape in plumbing applications, circuit boards used at microwave frequencies, medical applications like hip replacement surgeries. PTFE is produced by free-radical polymerization of tetra fluoro ethylene. The net equation is: 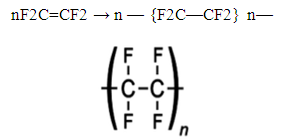 | Figure 1. Molecular Structure of PTFE |
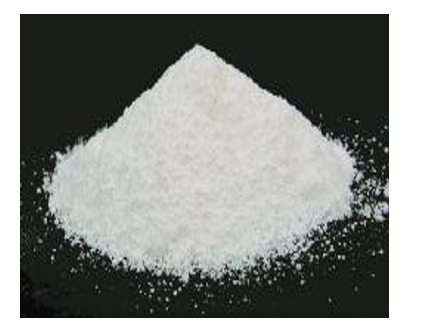 | Figure 2. PTFE Powder |
2.1.1. Properties of PTFE Powder
The various mechanical and chemical properties of PTFE powder is listed below: 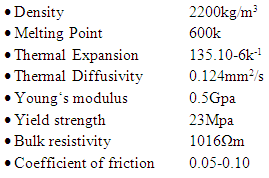
2.2. Alumina Powder
Aluminum oxide is also known as alumina, have a strong ionic inter-atomic bonding gives to enrich its desirable material characteristics. Alumina is one of the most cost effective and widely used in the family of engineering ceramics. With an excellent combination of properties and an attractive price, it is no surprise that fine grain technical grade alumina has a very wide range of applications. It exists in numerous crystalline phases which all are reverting to the most even hexagonal alpha phase at high temperatures. This is the phase of particular interest for structural applications and the availability of material is too accurate. Alpha phase alumina is one of strengthening and stiffens oxide ceramics. It’s high hardness, excellent dielectric properties, refractoriness and good thermal properties make the material of choice for a wide range of applications.
2.2.1. Properties of Alumina Powder
● It is very hard.● It is highly Wear-resistance.● It has an excellent dielectric property from DC to GHz frequencies.● It is capable of resisting a strong acid and alkali attack at high temperatures.● It has Good thermal conductivity.● Size and shape of this one are excellent to utilize.● Strength and stiffness are high.
3. Method of Fabrication
The fabrication of the solid samples is necessary to evaluate its performance in wear. Powdered particles have to be found into the solid by means of various techniques. Some techniques are Blow molding, Powder metallurgy plus sintering, Extrusion molding, Compression molding, Injection molding, Laminating, Matrix molding, Resin Transfer molding, Thermoforming etc. For a thermoset polymer, it is preferred as hot press compression molding for making perfect solid samples. Hot press compression molding of thermoset materials is a manual process that transforms granular material into a molded shape by placing material inside the mold and heated up to the melting temperature of the material cause good binding strength behind particles.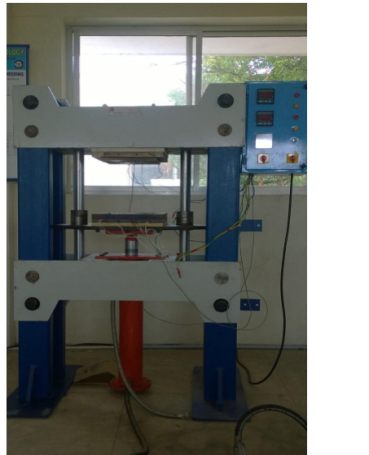 | Figure 3. Hot press compression molding machine |
In this method, the powdered polymers are heated up to the melting temperature. Then it is melted and make up as a solid component with heavy bonding strength. Powdered PTFE and Alumina particles are mixed with proper fractions before placing the material inside the mold. Then it was heated up to 600°K by means of thermocouples. The particles are bind together before liquefaction, and then this process is called sintering. 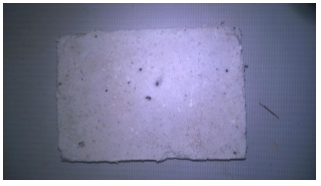 | Figure 4. Sample of Alumina – PTFE Composite |
4. Wear Analysis
Wear tests are used for quality control functions. The quality control functions are thickness, porosity, adhesion, strength, hardness, ductility, chemical composition, stress and wear resistance. In this experiment, wear behavior can be investigated for wear resistance of the material against fatigue loading. Pin on disc apparatus is used for evaluating wear against the fatigue loading.The disc made of hardened steel is placed on testing equipment. And thus the disc is connected to the motor by the chain mechanism. So when the motor rotates the disc rotates. A beam with a specimen holder is connected to balancing weight on one side and load on another side. The speed of the motor can be controlled by the regulator. The disc rotates according to the speed of the motor and thus the metal wear can be rated.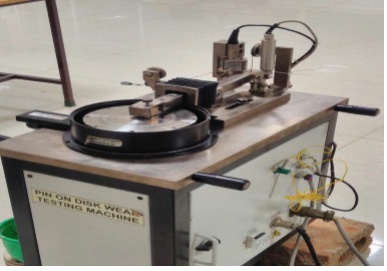 | Figure 5. Pin on Disc Apparatus |
The abrasive disc is made up of EN24 case hardened steel disc with 60 HRC which rotated by using a single phase DC motor. The disc is 200mm diameter with an inner hole of diameter 25mm. The rotation of the disc removes some amount of particles from the work piece and this process is carried out by the disk. The beam which is made of mild steel is connected to a support on one side and varying load on the other side. The beam also holds the tool holder in which the counter-face to be wearer is placed. And thus the support of the beam is further connected to the base in which motor is also placed. The specifications of a motor in this wear tester are single phase dc with an rpm of 1440 and 0.5hp. The disk in the apparatus is connected to the motor shaft. So when the motor rotates, the disk which is connected to the motor shaft also rotates. Thus the motor can rotate at high speed according to the usage of the work piece. The readings can be taken by elevating the loads and the values are plotted in the tabulation. Finally tabulated readings are calculated and analyzed by plotting the graph.
5. Experiment Results and Discussions
In this chapter, we are discussed about the result of the various processes and the testing result was analyzed and compare the performance of various weight percentages of Alumina filled PTFE composites.
5.1. Calculation
PTFE – 90% and Alumina – 10% Diameter of the disc, d = 0.60 m Load Applied=5N Rotating Velocity of Wheel, V=2 m/sec Travel distance of the grinding wheel, D = V x t = 1200 minutest=time taken to weight loss. Time of Each Experiment, T = Distance/velocityT = 1200/2×60 = 10 minutesSpeed, N = 60V/πDN = 60×2/π×0.06=636.6 rpmRepresentation of Samples in the Table is mentioned below:S1 - PTFE-100% & AL-0%,S2 - PTFE-90% & AL-10%,S3 - PTFE-85% & AL-15%,S4 - PTFE-80% & AL-20%Table 1. Wear Behavior Tabulation 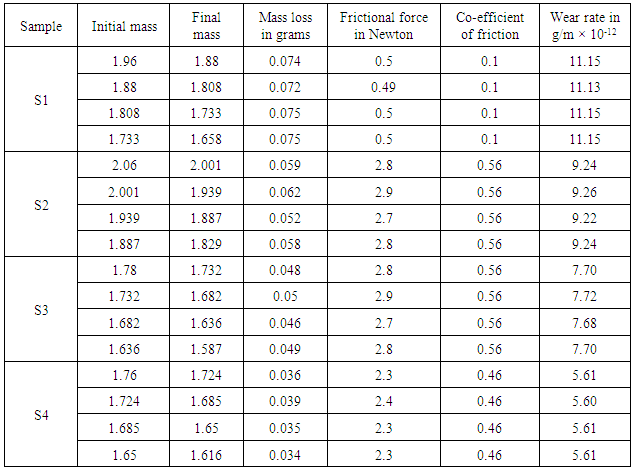 |
| |
|
Table 2. Cumulative Tabulation 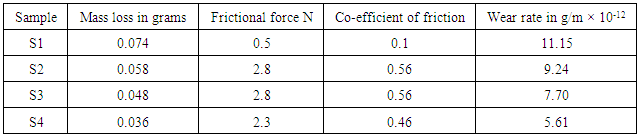 |
| |
|
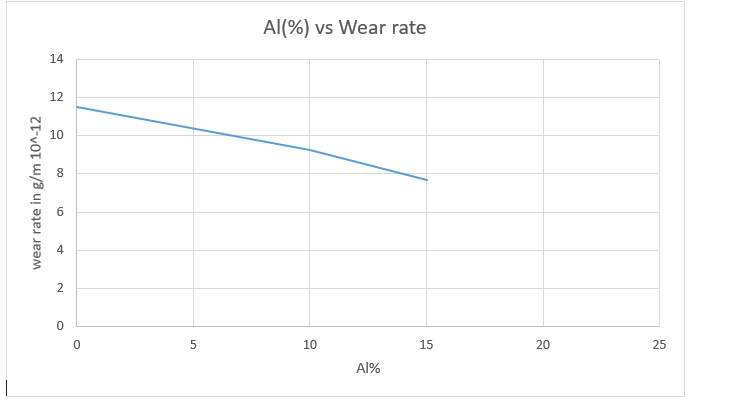 | Figure 6. Wear Rate Depletion Chart |
 | Figure 7. Coefficient of Friction Enhancement Chart |
From the above results, the wear rate of alumina filled PTFE composites the wear resistance gradually increases with increases in the percentage of alumina.
6. Conclusions
The present work clearly shows that alumina is one of the best filler material is to be added with PTFE to fabricate as bio comfortable materials. The following conclusions are made based on the extensive experimental study: ● The wear resistance of alumina filled PTFE composites increases with increase in filler concentration of alumina.● The alumina filled PTFE composite is reducing the wear of the materials.Finally, from the results addition of alumina in PTFE decreases wear rate of PTFE and the composite is best suitable for medical applications where the implants suffers with fatigue loading.
References
[1] | David L. Burris, W. Gregory Sawyer, (2006), ―Improved wear resistance in alumina-PTFE nanocomposites with irregularly shaped nanoparticles‖, Science direct, Wear vol:260 (2006) pp:915–918. |
[2] | Park, J. B., Lakes, R. S., (1992), ―Biomaterials—An Introduction‖, 2nd ed., Plenum Press, New York. |
[3] | S. K. Senavati and S. Pal, (2002), ―UHMWPE-alumina ceramic composite. |
[4] | V. Banchet, V. Fridrici, J.C. Abry, Ph. Kapsa (2007), ― Wear and friction characterization of materials for hip prosthesis‖ Science Direct, Wear vol.263 (2007) pp 1066–1071. |
[5] | W. Gregory Sawyer, Kevin D. Freudenberg, Praveen Bhimaraj, Linda S. Schadler, (2003), ―A study on the friction and wear behavior of PTFE filled with alumina nanoparticles‖ Science direct, Wear vol. 254 (2003) pp.573– 580. |
[6] | Wang, O., Xue, Q., and Shen, W. (1997), "The Friction and Wear Properties of Nanometre SiO2 Filled Polyetheretherketone," Tribology International, vol. 30, 3, pp 193-197. |
[7] | Williams, J. L., Lewis, J. L., (1982), ―Properties and an Anisotropic Model of wear behavior of alumina filled PTFE particles‖, Journal of Biomechanical Engineering, Vol. 104, pp. 50-56. |
[8] | Xiujing ZHAI, Yan FU, Gang GHU, (2006), ―Combustion synthesis of a Nano-structured Alumina powder‖ Nano-science, Vol.11, No.4, pp 286 – 292. |
[9] | Matthews, R.D. Rawlings, Composite Materials: Engineering and Science, Chapman and Hall, London, 1994, pp. 371–377. |