Ayesha Kausar
Nanosciences Division, National Centre For Physics, Quaid-i-Azam University Campus, Islamabad, Pakistan
Correspondence to: Ayesha Kausar, Nanosciences Division, National Centre For Physics, Quaid-i-Azam University Campus, Islamabad, Pakistan.
Email: |  |
Copyright © 2016 Scientific & Academic Publishing. All Rights Reserved.
This work is licensed under the Creative Commons Attribution International License (CC BY).
http://creativecommons.org/licenses/by/4.0/

Abstract
Novel hybrids based on poly[(o-cresyl glycidyl ether)-co-formaldehyde] (PCGEF), poly(ethylene glycol) bis(amine) (PEGBA), and bis(4-trifluoromethylphenyl)phosphine (TFMPP) were prepared in this attempt. 4,4′-Diaminodiphenylmethane was employed as hardener. The materials were prepared using simple solution technique. According to scanning electron microscopy (SEM), PCGEF/PEGBA/TFMPP 0.1-0.5 showed dispersed TFMPP particles in wavy layered uniform pattern. In PCGEF/PEGBA/TFMPP 0.1-0.5, initial decomposition temperature (T0) and maximum degradation temperature (Tmax) were found in the range of 333-415°C and 445-511°C respectively. Similarly, the PHRR was decreased from 161 kW/m2 (110 s) to 155 kW/m2 (105 s) indicating fine flame retardancy.
Keywords:
Epoxy, Hardener, SEM, Thermal stability, Flame retardancy
Cite this paper: Ayesha Kausar, Development of Non-flammable Poly[(o-cresyl glycidyl ether)-co-formaldehyde] System with Poly(ethylene glycol) bis(amine) and Bis(4-trifluoromethylphenyl)phosphine, International Journal of Composite Materials, Vol. 6 No. 4, 2016, pp. 129-132. doi: 10.5923/j.cmaterials.20160604.05.
1. Introduction
In current polymer industry epoxy resin are extensively employed as innovative composite matrices in electrical/electronic industry due to their high strength and modulus, low shrinkage in cure, high adhesion features, excellent chemical and corrosion resistant and outstanding dimensional stability [1-3]. Additionally for compensation of the flammability of resin, the brominated compounds or antimony oxide (serves as flame retardants) are imparted to epoxy resins [4, 5]. Currently with the concern of restricting the production of toxic, corrosive and halogenated gases as well as release of toxic environmental hormone in combustion, the trend is towards the employment of halogenated flame retardants [6]. Although amongst halogenated flame retardants the organo-phosphorus compounds are the constituent of selection generating less toxic gases and smoke [7, 8]. Additionally, epoxy resin with permanently linked flame resistant groups possesses comparatively high flame resistance [9]. The above mentioned underlying attachment coming from covalently integrating flame resistant group onto epoxy chains could be obtained by employing phosphorus comprising oxiranes and/or curing agents. Studies on development of flame resistant epoxy resins from phosphorus comprising epoxides or curing agents have also been reported [10]. On the other side, in current years numerous new fabrication and packaging techniques for electronics are established, thus resulting in thin, light, short, and small electrical products. Thus advanced materials are needed for these new techniques to confirm the quality and high potential of product. Moreover, some faults in the synthesis route, thermal stability, scaling up to mass production, and cost were escorted with the established materials in literature [11-13]. Moreover, the developed surface technology and other progressive electronic packaging techniques need constituents being capable to withstand the temperature ~300°C [14-16]. Thus thermal stability plays significant role for the electronic materials. Recent investigation are trying to organize a halogen flame retardant or epoxy with high flame resistance, high thermal stability, simple synthesis methods, and low cost to fulfill the needs of the recent aerospace and future electronic applications. In this work, an epoxy resin poly[(o-cresyl glycidyl ether)- co-formaldehyde] (PCGEF) was hardened with 4,4′-diaminodiphenyl-methane. The bis(4-trifluoromethyl- phenyl)phosphine was used as flame retardant. The PCGEF was reinforced with poly(ethylene glycol) bis(amine), and various weight content of bis(4-trifluoromethyl-phenyl) phosphine. The thermal and flame-retarding properties of the resulted epoxy resins were studied. The obtained materials were suitable for aerospace and electronic applications.
2. Experimental
2.1. Materials
Poly[(o-cresyl glycidyl ether)-co-formaldehyde] (average Mn ~1,080), Bis(4-trifluoromethylphenyl)phosphine (97%), 4,4′-diaminodiphenylmethane (≥97%), poly(ethylene glycol) bis(amine) (Mw 3,000), and tetrahydrofuran (THF, 99%) were purchased from Aldrich.
2.2. Instrumentation
IR spectra were taken at room temperature with a resolution of 4 cm-1 using Excalibur Series FTIR Spectrometer, Model No. FTSW 300 MX. The SEM images were obtained by Scanning Electron Microscope S-4700 (Japan Hitachi Co. Ltd.). The thermal stability was determined by METTLER TOLEDO TGA/SDTA 851 thermogravimetric analyzer using 5 mg of sample at a heating rate of 10C/min under nitrogen atmosphere. The combustion properties were calculated using cone calorimetry. Samples having dimensions 100×100×5 mm3 were exposed to a FTT 0007 cone calorimeter (FTT Company, England) under a heat flux of 50 kW/m2 according to ISO-5660 standard procedure.
2.3. Formation of poly[(o-cresyl glycidyl ether)- co-formaldehyde]/4,4′-diaminodiphenylmethane film (PCGEF)
1g epoxy was stirred in 5 mL THF for 15 min. Then 4,4′-diaminodiphenylmethane (2g) was dispersed in THF with 0.5 h stirring. The both solutions were mixed and again stirred for 0.5 h (Fig. 1). The final mixture was poured in Teflon Petri-dish and dried at 60 °C for 2h [16, 17].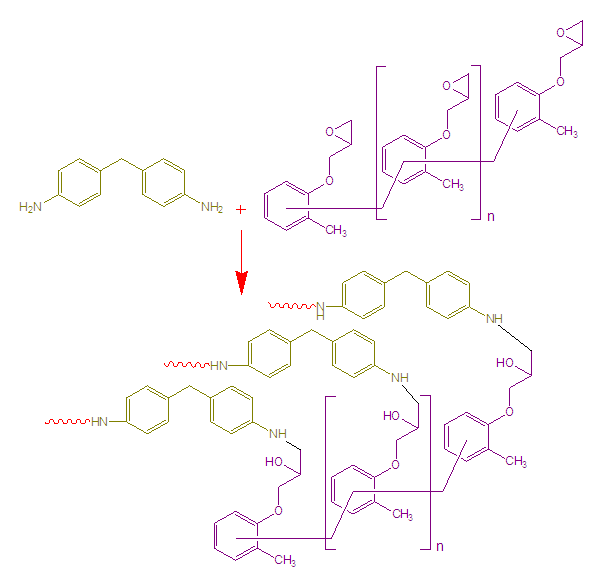 | Figure 1. Hardening of epoxy resin |
2.4. Formation of poly[(o-cresyl glycidyl ether)- co-formaldehyde]/poly(ethyleneglycol) bis(amine)/ Bis(4-trifluoromethylphenyl)phosphine film (PCGEF/ PEGBA/TFMPP)
The epoxy films with various weight ratio of 4,4′-diaminodiphenylmethane were prepared. First 1g PCGEF was stirred in 5 mL THF for 15 min. Before the addition of hardener, 0.1 g of PEGBA and bis(4-trifluoromethyl-phenyl)phosphine (0.1 to 0.5 g) was dispersed in the epoxy solution and stirred for 0.5 h. Then a solution of 4,4′-diaminodiphenylmethane (2g) in THF was added to the mixture and stirred for 0.5 h. Both the solutions were mixed and again stirred for 0.5 h. The final mixture was poured in Teflon Petri-dish and dried at 60°C for 2h.
3. Results and Discussion
3.1. Morphology Study
Morphology of neat epoxy and PCGEF/PEGBA/ TFMPP nanocomposite is shown in Fig. 2. 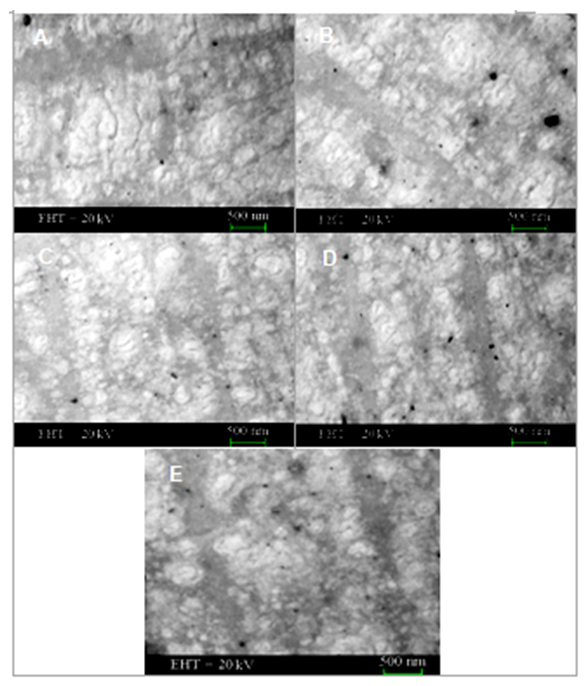 | Figure 2. FESEM images of (A) neat epoxy film; (B) PCGEF/PEGBA/TFMPP 0.1; (C) PCGEF/PEGBA/TFMPP 0.2; (D) PCGEF/PEGBA/TFMPP 0.3; and (E) PCGEF/PEGBA/TFMPP 0.5 |
The SEM micrographs of neat epoxy film showed somewhat smooth morphology (Fig. 2A). In the case of PCGEF/PEGBA/TFMPP 0.1, there was uniform dispersion of poly(ethylene glycol) bis(amine) and bis(4-trifluoromethyl-phenyl)phosphine particles (Fig. 2B). However the particles formed by the second phase were dispersed and embedded in the epoxy matrix. With the 0.2 wt.% TFMPP loading, the particles were seemed to be dispersed in the form of fine aligned wavy layered pattern (Fig. 2C). This type of morphology is unique in the case of epoxy hybrids [18]. The pattern suggested non-covalent interaction between the matrix and reinforced phases. The micrographs also revealed unvarying morphology of small dispersed particles in wavy form. Further TFMPP loading up to 0.5 wt.% depicted wavy layered pattern similar to PCGEF/PEGBA/TFMPP 0.2 (Fig. 2E). Nevertheless some larger particles were also visible in the micrographs with higher TFMPP content. Obviously, the resulting morphology may influence the thermal behavior of novel materials.
3.2. Thermal Properties
Fig. 3 shows thermogravimetric analysis of neat polymer and PCGEF/PEGBA/TFMPP materials. The incorporation of bis(4-trifluoromethylphenyl)phosphine and 4,4′-diaminodiphenyl-methane enhanced the thermal stability of the resulting materials considerably. Normally, the incorporation of rigid structures may increase the thermal properties of polymeric systems [19]. For neat polymer, the initial degradation temperature (T0) of 300°C, 10% weight loss (T10) of 350°C, and (Tmax) of 424°C was observed. Results showed that the bis(4-trifluoromethyl-phenyl) phosphine reinforced materials had reasonably high heat constancy. For PCGEF/PEGBA/TFMPP 0.1, the T0 was 333°C, T10 was 366°C, and Tmax was 445°C. The PCGEF/PEGBA/TFMPP 0.3 showed the T0 as 402°C, T10 of 421°C, and Tmax of 499°C. For PCGEF/PEGBA/TFMPP 0.5, the T0 was observed as 415°C, T10 as 433°C, and Tmax of 511°C. On the whole, the TFMPP addition enhanced the thermal properties of final material.  | Figure 3. TGA thermograms of PCGEF and PCGEF/PEGBA/TFMPP materials |
3.3. Non-flammability Measurement
In order to examine the flame retardancy of PCGEF/PEGBA/TFMPP, the cone calorimetry technique was employed (Fig. 4). For neat epoxy, the maximum peak heat release rate (PHRR) was found as 250 kW/m2, while time to achieve PHHR was 100 s. In PCGEF/PEGBA/TFMPP 0.1, the PHRR was slightly decreased to 161 kW/m2 in 110 s. With 0.3 wt.% TFMPP loading in epoxy, the PHRR was notably decreased to 155 kW/m2 in 105s. In the case of PCGEF/PEGBA/TFMPP 0.5, there was significant decrease in heat release rate. The PCGEF/PEGBA/TFMPP 0.5 revealed PHRR of 150 kW/m2 in 100 s. The decrease in heat release rate of materials during combustion indicated increase in flame retardancy of epoxy. The time to PHRR was also condensed considerably by flame retardant TFMPP addition. The non-flammability of the material was found better than the reported materials [20, 21].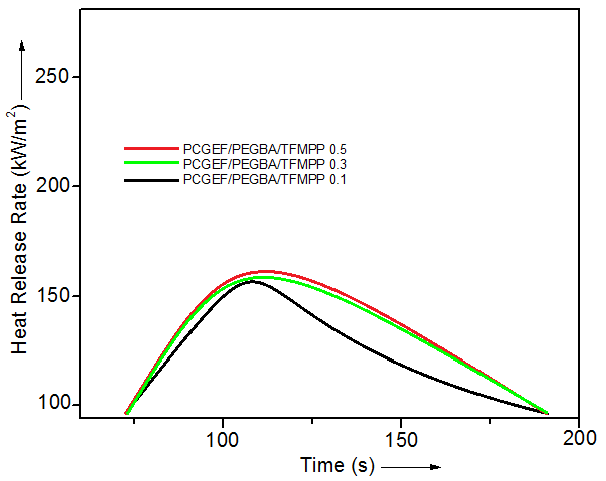 | Figure 4. Peak heat release rate vs. time curves for PCGEF/PEGBA/TFMPP materials |
4. Conclusions
Fabrication of novel epoxy from poly[(o-cresyl glycidyl ether)-co-formaldehyde] and 4,4′-diaminodiphenylmethane hardener was an effective approach to form thermally stable as well as non-flammable materials. Later the hybrids of poly[(o-cresyl glycidyl ether)-co-formaldehyde] and bis(4-trifluoromethylphenyl) -phosphine were prepared via incorporation of poly(ethylene glycol) bis(amine). Solution technique was employed as a proficient and cost effective procedure to form the desired materials. There was some sort of non-covalent interaction between the matrix and bis(4-trifluoromethylphenyl)phosphine. Consequently the hybrids depict unique morphology due to fine compatibility between PCGEF, PEGBA, and TFMPP. The thermal properties of epoxy were found to increase with TFMPP loading. A remarkable effect of TFMPP loading was observed in the case of flammability tests. The halogenated flame retardant acted as shield for epoxy material towards the flame. Novel poly[(o-cresyl glycidyl ether)-co-formaldehyde] and bis(4-trifluoromethylphenyl)- phosphine-based materials may find applications in flame retardant automobile parts, electronic appliances, adhesives, and several other technical applications.
References
[1] | Kausar A, Rafique I, Muhamma B. A Review on Applications of Polymer/Carbon nanotube and Epoxy/CNT Composites. Polym Plast Technol Engineer 2015, 55: 312-333. |
[2] | Fu Y X, He Z X, Mo D C, Lu S S. Thermal conductivity enhancement of epoxy adhesive using graphene sheets as additives. Int J Therm Sci 2014, 86: 276-283. |
[3] | Kausar A Estimation of Thermo-Mechanical and Fire Resistance Profile of Epoxy Coated Polyurethane/Fullerene Composite Films. Fuller Nanotub Carbon Nanostruct 2016, DOI:10.1080/1536383X.2016.1172067. |
[4] | Gul S, Kausar A, Muhammad B, Jabeen S. Technical Relevance of Epoxy/Clay Nanocomposite with Organically Modified Montmorillonite: A Review. Polym Plast Technol Engineer 2016. DOI:10.1080/03602559.2016.1163593. |
[5] | Kausar A, Siddiq M. Epoxy composites reinforced with multi-walled carbon nanotube/poly (ethylene glycol) methylether-coated aramid fiber. J Polym Engineer DOI:10.1515/polyeng-2015-0191. |
[6] | Kausar A, Rafique I, Anwar Z, Muhammad B. Perspectives of Epoxy/Graphene Oxide Composite: Significant Features and Technical Applications. Polym Plast Technol Engineer 2015, DOI:10.1080/03602559.2015.1098700. |
[7] | Kausar A. Composite of Poly [(phenyl glycidyl ether)-co-formaldehyde] with Cement and Graphite-Cement. Int J Mater Chem 2016, 6: 1-5. |
[8] | Kausar A, Siddiq M, 2015. Nanofiltration membranes of poly (styrene-co-chloro-methylstyrene)-grafted-DGEBA reinforced with gold and polystyrene nanoparticles for water purification. Appl Water Sci 2015, 1-13. |
[9] | Kausar A. Novel Nanofiltration Membranes of Poly (4-Chlorostyrene)-grafted-1-(4-thiocarbamoylaminophenyl-sulfonylphenyl) thiourea and Gold/Polystyrene Composite Nanoparticle. Am J Polym Sci Engineer 2015, 3: 33-49. |
[10] | Kausar A, Anwar Z, Muhammad B. Recent Developments in Epoxy/Graphite, Epoxy/Graphene and Epoxy/Graphene Nanoplatelet Composites: A Comparative Review. Polym Plast Technol Engineer 2016, DOI:10.1080/03602559.2016.1163589. |
[11] | Mehwish N, Kausar A, Siddiq M. Advances in polymer-based nanostructured membranes for water treatment. Polym-Plast Technol Engineer 2014, 53: 1290-1316. |
[12] | Budan D A, Vijarangan S, Arunachalam S, Page T. An Analysis of Machining Forces on Graphite/Epoxy, Glass/Epoxy & Kevlar/Epoxy Composites Using a Neural Network Approach. i-Manag J Futur Engineer Technol 2008, 4: 28. |
[13] | Du L, Jana S C. Highly conductive epoxy/graphite composites for bipolar plates in proton exchange membrane fuel cells. J Power Source 2007, 172: 734-741. |
[14] | Levchik S, Piotrowski A, Weil E, Yao Q. New developments in flame retardancy of epoxy resins. Polym Degrad Stab 2005, 88:.57-62. |
[15] | Kausar A. Mechanical, Thermal, and Electrical Properties of Epoxy Matrix Composites Reinforced With Polyamide-Grafted-MWCNT/poly (azo-pyridine-benzophenone-imide)/ Polyaniline Nanofibers. Int J Polym Mater Polym Biomater 2014, 63: 831-839. |
[16] | Rafique I, Kausar A, Anwar Z, Muhammad B. Exploration of Epoxy Resins, Hardening Systems, and Epoxy/Carbon Nanotube Composite Designed for High Performance Materials: A Review. Polym-Plast Technol Engineer 2016, 55: 312-333. |
[17] | Liu Y L, Wu C S, Chiu Y S, Ho W H. Preparation, thermal properties, and flame retardance of epoxy–silica hybrid resins. J Polym Sci Part A: Polym Chem 2003, 41:.2354-2367. |
[18] | Zhu J, Wei S, Ryu J, Budhathoki M, Liang G, Guo Z. In situ stabilized carbon nanofiber (CNF) reinforced epoxy nanocomposites. J of Mater Chem 2010, 20: 4937-4948. |
[19] | Becker O, Varley RJ, Simon GP. Thermal stability and water uptake of high performance epoxy layered silicate nanocomposites. Eur Polymer J 2004, 40: 187-195. |
[20] | Kausar A, Ullah W, Muhammad B, Siddiq M. Novel mechanically stable, heat resistant and nonflammable functionalized polystyrene/expanded graphite nanocomposites. Adv Mater Sci 2014, 14: 61-74. |
[21] | Kausar, A., 2016. Bucky Papers of Poly (methyl methacrylate-co-methacrylic acid)/Polyamide 6 and Graphene Oxide-Montmorillonite. Journal of Dispersion Science and Technology, 37(1), pp.66-72. |