Ismat Z. Luna1, Krishna C. Dam1, A. M. Sarwaruddin Chowdhury1, M. A. Gafur2, Ruhul A. Khan3
1Department of Applied Chemistry and Chemical Engineering, Faculty of Engineering and Technology, University of Dhaka, Dhaka, Bangladesh
2Pilot Plant and Process Development Center, Bangladesh Council of Scientific and Industrial Research, Dhaka, Bangladesh
3Institute of Radiation and Polymer Technology, Bangladesh Atomic Energy Commission, Savar, Dhaka, Bangladesh
Correspondence to: Ismat Z. Luna, Department of Applied Chemistry and Chemical Engineering, Faculty of Engineering and Technology, University of Dhaka, Dhaka, Bangladesh.
Email: |  |
Copyright © 2015 Scientific & Academic Publishing. All Rights Reserved.
This work is licensed under the Creative Commons Attribution International License (CC BY).
http://creativecommons.org/licenses/by/4.0/

Abstract
Rice husk reinforced polypropylene-based composites were prepared by conventional compression molding. Composites contained 5-20% (by weight) of rice husk as the reinforcing agent. Then mechanical and spectroscopic properties of the composites were evaluated. Rice husk was also treated with sodium hydroxide (NaOH) solution (1% by weight) to investigate the effect of NaOH on the mechanical properties of the fabricated composites. Loading of rice husk revealed that mechanical properties of polypropylene based composites significantly improved. Fourier transform infrared (FTIR) spectroscopy confirmed the existence of hemicelluloses and lignin in the neat composite. Interfacial properties were investigated by scanning electron microscopy (SEM).
Keywords:
Composites, Polypropylene, Rice husk, Mechanical properties, SEM
Cite this paper: Ismat Z. Luna, Krishna C. Dam, A. M. Sarwaruddin Chowdhury, M. A. Gafur, Ruhul A. Khan, Mechanical and Spectroscopic Properties of Rice Husk Reinforced Polypropylene Composites: Effect of Sodium Hydroxide, International Journal of Composite Materials, Vol. 5 No. 6, 2015, pp. 162-166. doi: 10.5923/j.cmaterials.20150506.04.
1. Introduction
Composite materials are widely using in civil construction, automobiles, space and aircraft applications, naval manufacturing and many others. Composite materials are manufactured by combining two dissimilar materials into a new material which is better suited for a particular application than either of the original material alone. Nowadays, modern technologies require materials with unusual combination of properties that cannot be met by the conventional materials. A relatively new class of composite material isfiber reinforced polymers which is manufactured using fiber and polymer. Composite materials are efficient and economical for use in a variety of engineering applications. There are two types of matrix materials in fiber reinforced polymer based composites, i.e., (a) thermo-plastics and (b) thermo-sets. While different types of fibers are using as reinforcing filler in the composites. It is to be noted here that thermoplastic resins achieved much interest due to their economic and mechanical advantages such as easy fabrication, intrinsic recyclability, unlimited shelf life, high toughness and good moisture resistance. Fibers provide stiffness and tensile capacity to the composites and improve their mechanical characteristics [1-3].Every year billion of tons of agricultural crop residues are produced around the world. Among this large amount of residues, only a small quantity of them are utilized as household fuel or fertilizer and the rest is burned in the field. As a result, it causes air pollution. Utilization of the agricultural crop residues as reinforcement of polymer composites can solve this problem. Application of natural fibers as reinforcing agent to composites gained much interests due to increased environmental awareness and consciousness throughout the world. Natural fibers are now considered as an alternative to synthetic fibers for use in various fields such as building and construction, packaging, automobile and railway coach interiors and storage devices, and various load bearing applications. They are environmentally friendly, biodegradable, widely available, renewable, cheap, and have low density. The biodegradability of plant fibers contribute to a healthy ecosystem and their high performance satisfies industrial economy. Plant fibers are light in weight compared to glass, carbon, and aramid fibers. Recently, a wide variety of natural fibers have been investigated for the reinforcement of the composites. These include jute, wood, rice husk, banana fiber, sisal, bamboo, coir, hemp, flax, kenaf, and ramie [4-7].Composite materials prepared from unmodified plant fibersoften exhibit unsatisfactory mechanical properties. To overcome this drawbacks, surface treatments are required prior to composite fabrication. The mechanical properties of fiber reinforced polymer composites can be improved by both physical (corona treatment, cold plasma treatment) and chemical treatments (isocyanates, sodium hydroxide, maleic anhydride organosilanes, permanganate, and peroxides) [8-10].The aim of this research was to investigate the mechanical and spectroscopic properties of rice husk reinforced polypropylene-based composites. Then rice husk was treated with sodium hydroxide and composites were fabricated. Effect of sodium hydroxide on the composite properties were evaluated. The morphological properties and the chemical structure of the composites were also investigated.
2. Experimental Methods
2.1. Materials
Rice husk (Local name: Aman rice husk; Scientific name: Oryza sativa) was collected from local rice mill of Dhaka, Bangladesh. Polypropylene (PP) in the form of pellets was purchased from Polyolefin Company Private Limited, Singapore. Sodium hydroxide and hydrochloric acid were collected from Sigma-Aldrich, Germany.
2.2. Methods
Rice husk was washed thoroughly to remove dust, soil, sand and rice particles. Then it was dried and sieved. Fine rice husk powders were treated by NaOH solution (1% by weight) for 72 hours. The solution was then neutralized using HCl solution (1% by weight), and then rice husk was taken out from the solution and washed. Finally, the treated rice husk was dried in a vacuum oven at about 85°C for 24 hours to remove moistures. Both raw (untreated) and treated rice husk were used for making composites. Before the preparation of composites, rice husk was grinded using planetary ball mill (Model PM 100) and then screened to get 45-70 mesh size of rice husk flour. Polypropylene pellets and rice husk (untreated and treated separately) were blended at different percentages (Table 1). Then the pellets of PP and rice husk were compounded using an extruder (Axon ab Plastic Machinery, S-26550, Machine Type BX 25, Sweden). The processing was carried out at a screw speed of 15 rpm and at a heating program of 175-180-185-180-175°C along the line of extrusion. Repeated (three times) extrusion was carried out for homogeneous mixing of the rice husk and PP. Then the melt mixture was compression molded for making composites using heat press (Paul-Otto Weber-Presser Hydraulic Press, USA) at 180°C and 3 kPa for 5 min. Composite samples were cooled down to room temperature and then taken out from the compression molding machine for characterization.Table 1. Percentages of polypropylene and rice husk in composites of different compositions 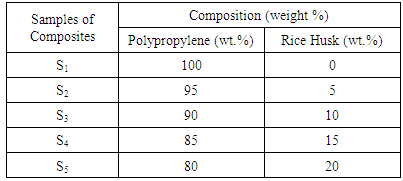 |
| |
|
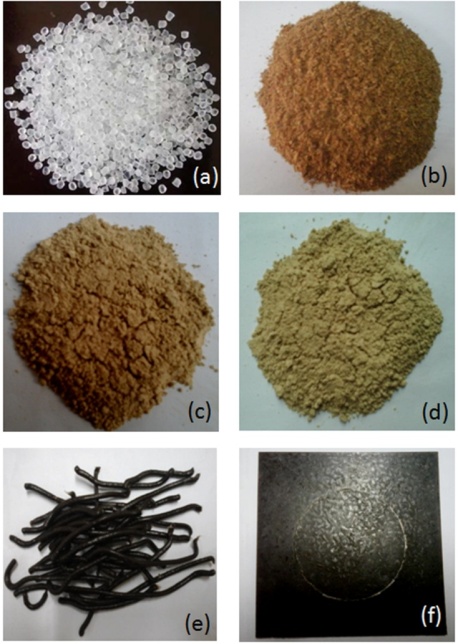 | Figure 1. (a) Commercial PP pellets, (b) Rice husk, (c) Untreated rice husk, (d) Treated rice husk, (e) Extruded rice husk/PP samples, and (f) Fabricated composite sample |
2.3. Characterization
Scanning electron microscopy (JEOL JSM-7600F, Japan) was used to observe the morphology of surfaces of untreated and treated husk reinforced PP composites. The fourier transform infra-red (FTIR) spectroscopic analysis of the untreated and treated rice husk reinforced composites were taken in the region between 500-4000 cm-1 (with Perkin Elmer 1650, USA) in order to understand the chemical structure of the composites. Different mechanical properties such as tensile strength, percentage elongation and flexural strength of prepared composites were investigated using Universal Testing Machine (Model 1011UK, INSTRON, England). Rebound hardness was also measured using Leeb Rebound Hardness Tester (Model H1000, Sweden).
3. Results and Discussion
3.1 Mechanical Properties of the Composites
One of the most important and widely measured properties of composites is the ability to resist fracture under tensile stress. Figure 2 illustrates the effect of addition of untreated and treated rice husk on tensile strength the composites. Tensile strength for untreated and treated rice husk reinforced PP composites is lower than that of neat PP. This is due to the poor dispersion of the rice husk filler on the polymer matrix so that the stress transfer between the filler and the matrix does not work properly [11]. Physical properties of rice husk filler and interfacial adhesion of filler with the polymer matrix also affects tensile strength. The tensile strength of composites increased with the increase in the percentage addition of rice husk filler to polymer matrix [12]. This is because both rice husk filler and PP matrix bear the load and the filler content made the composite resistant to slip. However, the composite strength cannot be improved by addition of filler if the volume fraction of the filler is lower than the critical quantity [13]. The highest value of tensile strength is obtained for both 20% untreated and treated rice husk reinforced PP composites. It was also observed that treated husk reinforced composites had higher tensile strength than untreated husk composites. In case of 20% treated rice husk composite, the tensile strength increased by 10.82% for 20% untreated rice husk.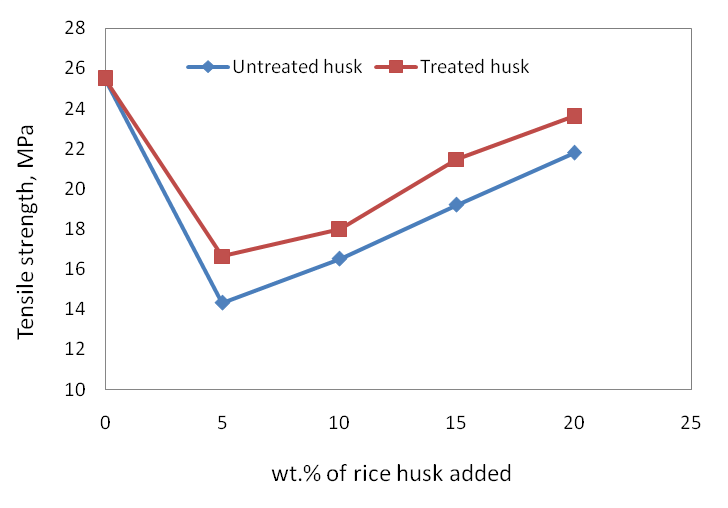 | Figure 2. Tensile strength of untreated and treated husk reinforced PP composites |
Figure 3 shows the percentage elongation at break of untreated and treated husk reinforced PP composites with varying weight fractions of rice husk. The elongation at break for both composites significantly decreased with the loading of rice husk. In addition, as the filler content increases the amount of polymer matrix becomes insufficient to wet the filler entirely and leads to poor interfacial bonding between the filler and the matrix. As a result, the composite fails to elongate when force is applied. Moreover, filler content restricts the slip and hardens the composite which results in lesser ductility and consequently the percent elongation decreases with increase in filler content [14]. It was also observed that treated husk composites had lower elongation than untreated husk reinforced composite. 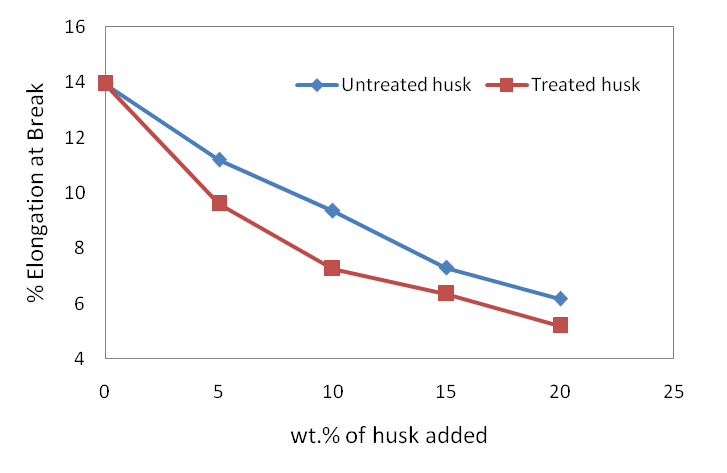 | Figure 3. Percentage elongation of untreated and treated husk reinforced PP composites |
Flexural strength is the ability of the composite to withstand bending forces applied perpendicular to its longitudinal axis. Flexural test is important to investigate the strength of a beam. From Figure 4, it is observed that for untreated and treated husk reinforced composites, the flexural strength increased with the increase of rice husk in the composites. Alkali (NaOH) treated rice husk significantly increased the flexural strength of the composites as filler/matrix adhesion is affected by the alkali treatment [15]. In case of 20% treated rice husk reinforced composite, the flexural strength increased by 11.10% times over that of the untreated husk based composites. 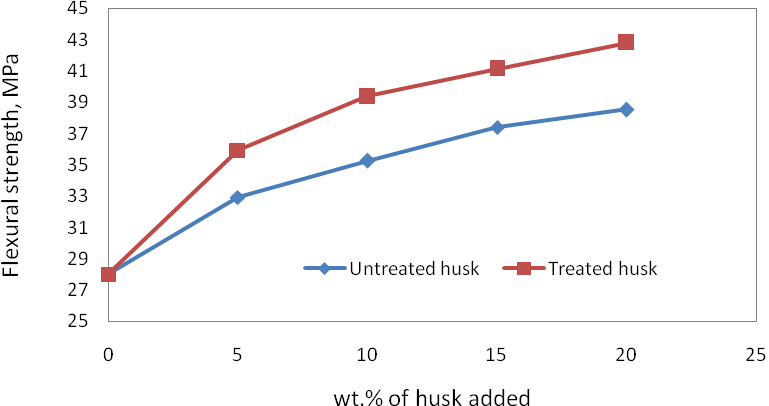 | Figure 4. Flexural strength of untreated and treated husk reinforced PP composites |
The effect of rice husk content on rebound hardness of untreated and treated rice husk reinforced PP composites is presented in Figure 5. Results indicated that the rebound hardness of untreated and treated rice husk reinforced composites was decreased with the increase of rice husk content due to elastic deformation. As the stiffness of composite is lower than neat PP, so composites became soft than neat PP. It was also found that treated husk reinforced composites had less Leeb rebound hardness than their control counterpart composites.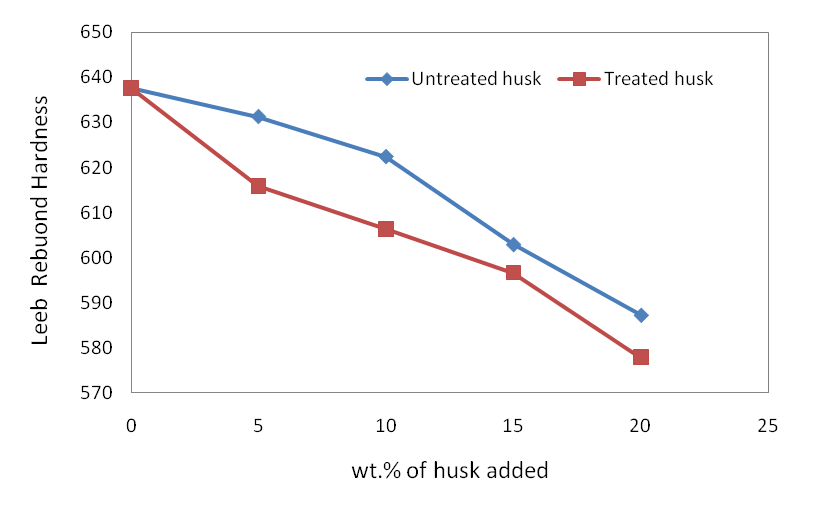 | Figure 5. Leeb rebound hardness of untreated and treated husk reinforced RH-PP composites |
3.2. Scanning Electron Microscopic (SEM) Analysis
Surfaces of untreated and treated rice husk reinforced PP composites are shown by SEM micrograph in Figure6 (a-b). In case of untreated husk reinforced PP composites (a), the existence of clustered impurities such as hemicelluloses and lignin are found which make the surface of the composite uneven. Moreover, some voids are also observed in case of untreated husk composites which resulted a poor adhesion between rice husk and PP. However, for treated husk reinforced composite samples (b), the surface of the composite was less porous and homogeneous which is due to the reduction of impurity contents caused by alkali treatments.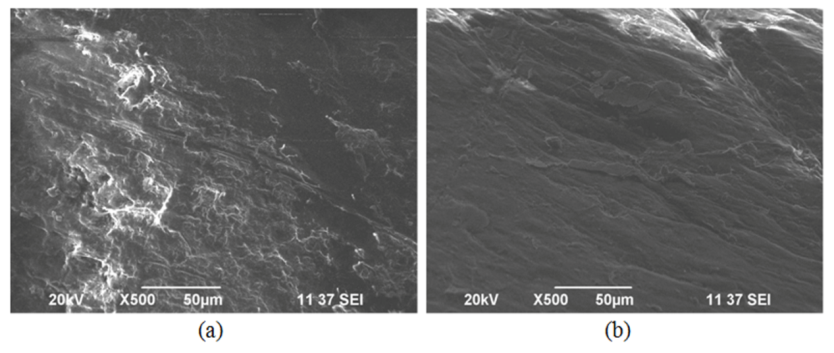 | Figure 6. SEM images of (a) untreated and (b) treated RH-PP composites |
3.3. Fourier Transform Infrared Spectroscopic (FTIR) Analysis
Figures7 (a-b) show the results of FTIR spectra of the untreated and treated husk reinforced PP composites, respectively. For both the composites, the stretching vibration band of the hydroxyl groups of cellulose appeared between 3400-3450 cm−1. In case of untreated husk reinforced composite (a), the absorption peak found at about 2957.89 cm-1 which reflected C-H stretching of methyl, methylene or methane group. This band is more intense than that of treated husk reinforced composite. However, for untreated husk reinforced composite, there is a considerable decrease in intensity of peak at around 1350-1650 cm−1 which corresponded the aromatic skeleton vibrations of hemicelluloses and lignin. From Figure 7(b) it is noticed that the amount of hemicelluloses and lignin components is reduced for alkali treated husk reinforced composite.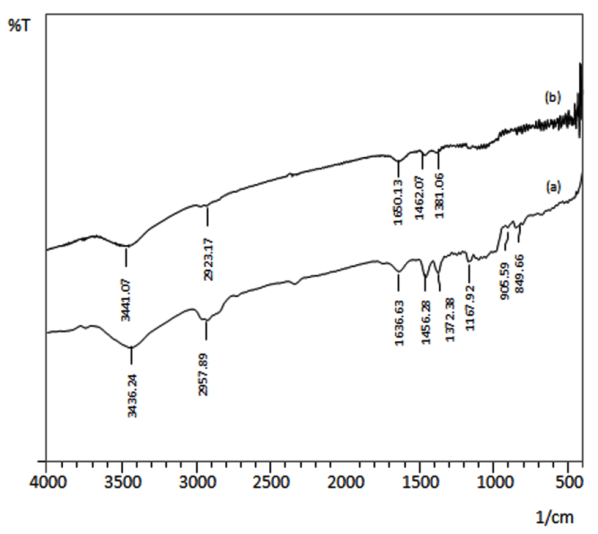 | Figure 7. FTIR spectra of (a) untreated and (b) treated husk reinforced RH-PP composites |
4. Conclusions
In conclusion, addition of untreated and alkali treated rice husk to the PP matrix significantly affects the mechanical properties of the prepared composites. Tensile and flexural strength of composites increased with the loading of rice husk in the composites. Alkali treated rice husk based composites performed better properties that of their untreated counterpart composites. Results revealed that the highest tensile strength and flexural strength for composites were found for 20weight percent of rice husk loading. However, percentage elongation at break and rebound hardness of composites found to decrease with the loading of rice husk in PP matrix. Finally, rice husk performed a potential filler for PP matrix and alkali treatment showed better mechanical strength. The prepared semi-biodegradable composites have the potential to be used in many construction applications.
ACKNOWLEDGEMENTS
The authors are thankful to Centre for Advanced Research in Sciences (CARS), University of Dhaka for providing additional research facilities.
References
[1] | Khan RA, Beck S, Dussault D, Salmieri S, Bouchard J, Lacroix M. Mechanical and barrier properties of nanocrystalline cellulose reinforced poly (caprolactone) composites: Effect of gamma radiation. J Appl Polym Sci 2013; 129(5): 3038-3046. |
[2] | Yu L, Dean K, Li L. Polymer blends and composites from renewable resources. Progress Polym Sci 2006; 31: 576-602. |
[3] | Saheb DN, Jog JP. Natural fiber polymer composites: A review. Adv Polym Technol 1999; 18: 351–363. |
[4] | Avella M, Buzarovska A, Errico ME, Gentile G, Grozdanov A. Eco-challenges of bio-based polymer composites. Materials 2009; 2: 911-925. |
[5] | Abdul Khalil, H.P.S., Siti Alwani, M., Kamarudin, H., Khairul, A. Chemical Composition, Morphological Characteristics, and Cell Wall Structure of Malaysian Oil Palm Fibers. Polym Plast Technol Engg 2008; 47: 1-8. |
[6] | Khan RA, Khan MA, Zaman HU, Khan MN, Pervin S, Saha M, Sultana S. Comparative studies of mechanical and interfacial properties between jute and E-glass fibers reinforced polypropylene composites. J Reinf Plast Compos 2010; 29: 1078–1092. |
[7] | Devi LU, Bhagawan S, Thomas S. Mechanical properties of pineapple leaf fiber‐reinforced polyester composites. J Appl Polym Sci 1997; 64: 1739-48. |
[8] | Facca AG, Kortschot MT, Yan N. Predicting the tensile strength of natural fibre reinforced thermoplastics. Composites Science and Technology 2007; 67: 2454-66. |
[9] | Khan MA, Hassan MM, Drazal LT. Effect of 2-hydroxyethyl methacryate (HEMA) on the mechanical and thermal properties of jute/polycarbonate composites. Composites Part A. 2005; 36: 71–82. |
[10] | Mohanti AK, Khan MA, Hinrichsen G. Surface modification of jute and its influence on performance of biodegradable jute-fabric/biopol composites. Compos Sci Technol 2000; 60: 1115–1127. |
[11] | Moczo J, Pukanszky B. Polymer micro and nanocomposites: structure, interactions, properties. Journal of Industrial and Engineering Chemistry 2008; 14: 535-63. |
[12] | Ku H, Wang H, Pattarachaiyakoop N, Trada M. A review on the tensile properties of natural fiber reinforced polymer composites. Composites Part B: Engineering 2011; 42: 856-73. |
[13] | Herrera-Franco P, Valadez-Gonzalez A. A study of the mechanical properties of short natural-fiber reinforced composites. Composites Part B: Engineering 2005; 36: 597-608. |
[14] | Kord B. Investigation of reinforcing filler loading on the mechanical properties of wood plastic composites. World Applied Sciences Journal 2011; 13: 171-4. |
[15] | Kumara KK, Babub PR, Reddyc KRN. Evaluation of Flexural and Tensile Properties of Short Kenaf Fiber Reinforced Green Composites. International Journal of Advanced Mechanical Engineering 2014; 4: 371-80. |