Lawrance C. A. 1, P. Suresh Prabhu 2
1Department of Mechanical Engineering, Karpagam Academy of Higher Education, Karpagam University, Coimbatore, India
2Karpagam University, Coimbatore, India
Correspondence to: Lawrance C. A. , Department of Mechanical Engineering, Karpagam Academy of Higher Education, Karpagam University, Coimbatore, India.
Email: |  |
Copyright © 2015 Scientific & Academic Publishing. All Rights Reserved.
Abstract
Metal matrix composites (MMCs) have been developed to meet the requirements in the field of transportation and similar engineering applications due to their superior mechanical properties. Aluminium (Al) alloys are used as common matrix phases for the production of a variety of metal matrix composites due to their low density, good corrosion resistance, high electrical and thermal conductivities, high damping capacity and their ability to be strengthened by precipitation. Al 6061 alloys are widely used in many engineering applications in the fields of construction and transportation where superior mechanical properties such as hardness and tensile strength are essential. By incorporating TiB2 reinforcement phase in the Al 6061 alloy, Al 6061-TiB2 metal matrix composite can be manufactured using the in-situ salt –metal reaction technique. The addition of TiB2 to the metal matrix increases the strength of the matrix phase. An attempt was made to synthesize Al 6061 and TiB2 using in-situ technique where halide salts namely potassium hexaflurotitanate (K2TiF6) and potassium tetrafluroborate (KBF4) were introduced in the Al 6061 melt at 850°C with different reaction holding times in order to investigate the degree of in-situ reaction in the synthesis of Al 6061 – TiB2 metal matrix composite.
Keywords:
Aluminium alloys, Al 6061-TiB2 metal matrix composite, K2TiF6, K2BF4, In-Situ, Reaction holding time
Cite this paper: Lawrance C. A. , P. Suresh Prabhu , Al 6061-TiB2 Metal Matrix Composite Synthesized with Different Reaction Holding Times by In-Situ Method, International Journal of Composite Materials, Vol. 5 No. 5, 2015, pp. 97-101. doi: 10.5923/j.cmaterials.20150505.02.
1. Introduction
Metal matrix composites (MMCs) have generated considerable scientific and technological interest, primarily because of the intrinsic advantages they offer with respect to: (a) processing (b) fabrication using existing infrastructure and (c) property development and / or enhancement [1]. MMCs attracted researchers due to the availability of reinforcements at competitive cost, suitable processing technique and the availability of standard or near-standard metal working method to fabricate them [2]. Aluminium matrix Composites (AMCs) have found extensive use in many engineering applications because of their high specific modulus, strength, hardness and stiffness, excellent wear resistance, low-heat expansion coefficient, stability of properties at elevated temperature, reduced density and competitive fabrication cost. The development of these materials has been driven by the aerospace and automotive industries for both nonstructural and structural applications [3]. Al based composite reinforced by hard ceramic particles have become more and more attractive in the research of structural composites. The addition of ceramic particles such as TiB2, SiC, Al2O3, B4C to an aluminium based matrix does not considerably change the density of the material but instead it usually leads to a significant rise in specific strength and modulus of composite. This improvement of composite plays a role as weight saving material for use in structural applications [4]. Aluminium alloy Al 6061 is widely used in numerous engineering applications including transport and construction where superior mechanical properties such as tensile strength, hardness etc. are essentially required. Its superior corrosion resistance makes it a suitable candidate material for marine structural applications. The demand for lighter weight, cost effective and high performance materials for use in a spectrum of structural and non-structural applications have resulted in the need for fabrication of metal matrix composites (MMCs) of various types [5]. The composite prepared by ex - situ method suffers thermodynamic instability between matrix and reinforcements thus limiting their ambient and high temperature mechanical properties. The major challenges in processing of ex-situ MMC is the thermodynamic instability of ceramic reinforcing phases with the matrix. This is due to poor wetting between matrix and reinforcement. Ex-situ process possesses drawbacks like agglomeration, poor wetting and heterogeneity in microstructure [6]. Fabrication of in-situ composite involves synthesis of reinforcing phases directly within the matrix. This approach is in contrast to ex-situ composite where the reinforcements are synthesized separately and then introduced into the matrix during a secondary process such as melting, infiltration (or) powder processing [7]. The main problem lies in ex-situ composite is thermodynamic instability of reinforcing ceramic phases with the matrix [8]. This problem can be solved by using in-situ technique. And also there are several potential advantages associated with in-situ composite such as thermodynamic stability, kinetic control of the reaction, reduced size and uniform distribution of the reinforcing particles, good interfacial bond and economy in processing [9]. Using the in-situ approach MMCs with wide range of matrix materials (Al, Fe, Cu, Pb, Ni and Ti) and the second phase particles (borides, carbides, nitrides and oxides) can be produced [10].Al based composite reinforced by hard ceramic particles have become more and more attractive in the research of structural composites. The addition of ceramic particles such attractive in the research of structural composites. The addition of ceramic particles such as TiB2, SiC, Al2O3, B4C to an Aluminium based matrix does not considerably change the density of the material but instead it usually leads to a significant rise in specific strength and modulus of composite. This improvement of composite plays a role as weight saving material for use in structural applications [4]. Among the various reinforcing particles TiB2 is particularly attractive because it exhibits high elastic modulus and hardness as well as good thermal conductivity. Compared to Al-SiC, the Al-TiB2 MMC has better high temperature properties [11]. The incorporation TiB2 particles in the matrix by in-situ processing offer special advantages such as clean matrix-particle interface resulting in effective load transfer and minimizing wear rates [9]. The present study is to develop a metal matrix composite with Al 6061 as the matrix phase and TiB2 as the reinforcement phase using in-situ technique where two halide salts potassium hexafluorotitanate (K2TiF6) and potassium tetrafluoroborate (KBF4) are introduced in the molten Al 6061 alloy at the temperature of 850°C and holding at this temperature with different reaction holding times.
2. Materials and Methods
The matrix phase used was Al 6061 and the reinforcement phase was TiB2. The chemical composition of the matrix phase, Al 6061 alloy is shown in the following TABLE-1.Table 1. Chemical Composition of Al 6061 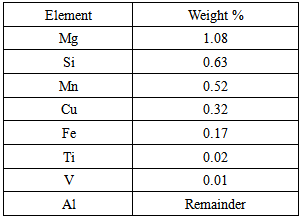 |
| |
|
The reinforcement phase, TiB2 is formed during the in-situ process where two halide salts namely potassium hexaflurotitanate (K2TiF6) and potassium tetrafluroborate (KBF4) are introduced into the molten aluminium alloy at 850°C in the atomic ratio in accordance with Ti/2B using the stirring method. A mild steel stirrer coated with zirconium is used to avoid possible contamination of the melt. The formation of TiB2 takes place as a result of chemical reaction between the halide salts and the molten aluminium alloy in two steps. In the first step, the two halide salts reacts with molten aluminium forming intermediate compounds Al3Ti and AlB2. In the second step, these intermediate compounds react together forming TiB2 and cryolite slag. The composite is formed as a result of uniform distribution of TiB2, the reinforcement phase in the Al 6061 alloy, the matrix phase. The cryolite slag that is formed during the chemical the Al 6061 alloy, the matrix phase. The cryolite slag that is formed during the chemical reaction between the halide salts and the molten aluminium alloy is skimmed thoroughly before pouring the melt into the die. The following are the chemical reactions in the formation of TiB2 which serves as the reinforcement in the Al 6061 matrix for the synthesis of Al 6061-TiB2 composite:  | (1) |
 | (2) |
The experimental setup for the stir casting method is shown in Figure-1. Using an electrical resistance furnace Al 6061 alloy was melted to a temperature of 850°C in a graphite crucible of 1 kg capacity. The alloy was kept at this temperature for about 5 minutes for homogenization of the temperature while being stirred at 600 rpm using a zirconium coated mild steel stirrer. Stirring was continued while the two halide salts in appropriate quantities were introduced to the melt. With different reaction holding times in steps of 15 minutes to 45 minutes the temperature was maintained at 850°C to investigate the relationship between the degrees of chemical reaction and the growth behavior of the reinforcement phase. At the end of each holding time, the cryolite slag was skimmed thoroughly and the composite was cast into rods of 16 mm diameter using a mild steel hollow cylindrical die coated with zirconium as shown in Figure-2.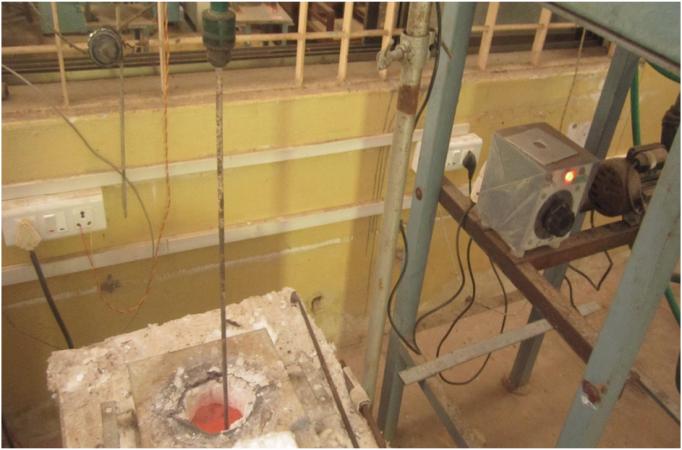 | Figure 1. Experimental setup for stir casting Al 6061-TiB2 composite |
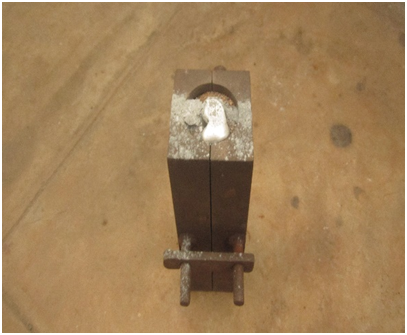 | Figure 2. Composite casting |
The casted composite bars are shown in Figure-3.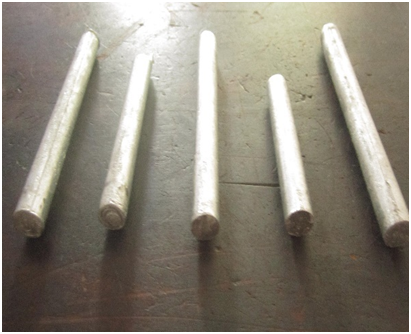 | Figure 3. Casted composite bars |
Metallographic examination, measurement of tensile properties and hardness were carried out for the characterization of the composite samples prepared.
2.1. Characterization of Alloy and Composites
A microscopic examination of the composites prepared with different reaction holding times and the base alloy was conducted by optical microscope after preparing suitably ground, polished and etched specimens in order to evaluate the microstructure. The tensile test specimens for measuring tensile properties were prepared as per ASTM E8 standard and the tensile tests were carried out at room temperature under constant strain rate using a Hounsfield Tensometer. Table-2 shows the results of the tensile tests for various samples with different reaction holding times. The tensile properties of the composites of Aluminium alloy reinforced with TiB2 are compared with the results of Aluminium 6061 alloy.Table 2. Tensile properties of composites with Different Reaction Holding Times 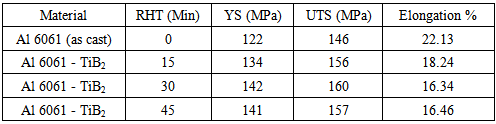 |
| |
|
Test specimens for measuring hardness were prepared from both the base alloy and the composites. Using a Brinell hardness tester, hardness measurements were carried out on the composites and the base metal in order to assess the influence of the various reaction holding times in which the salt-metal reaction took place.
3. Results and Discussion
3.1. Microstructure
Figures 4a, 4b, 4c and 4d show the optical micrographs of the composites of Al 6061-TiB2 resulting from various reaction holding times up to 45 minutes in steps of 15 minutes. These micrographs show a uniform distribution of reinforcement particles in the matrix phase. There was no gap between the matrix and the reinforcement phases due to good bonding between the phases. It was also found that the volume of cryolite slag that was formed during the reaction between aluminium alloy and the halide salts at the temperature of the melt increases with reaction holding time. 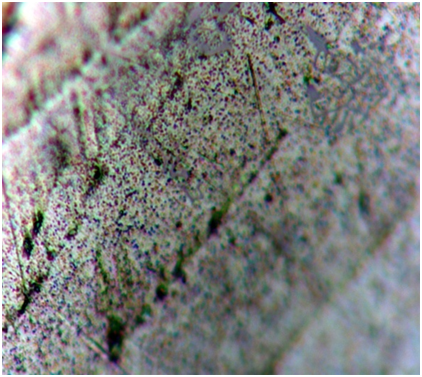 | Figure 4a). Micrograph of Al 6061alloy, as cast (100X) |
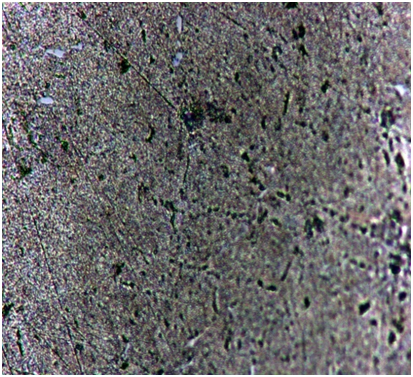 | Figure 4b). Micrograph of composite with 15 minutes reaction holding time (100X) |
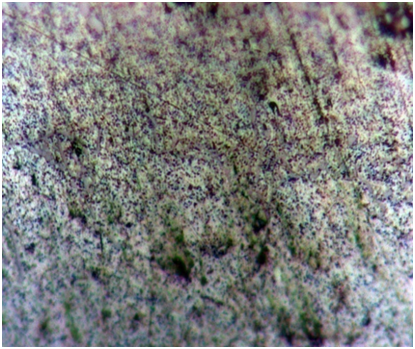 | Figure 4c). Micrograph of composite with 30 minutes reaction holding time (100X) |
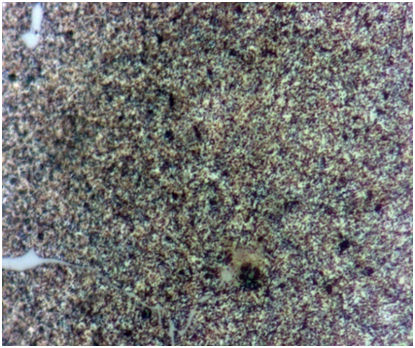 | Figure 4d). Micrograph of composite with 45 minutes reaction holding time (100X) |
3.2. Tensile Strength
The composite has a higher tensile strength than the Al 6061 alloy but with lower ductility. The improvement in the tensile strength of the composite compared to the alloy, Al 6061 is due to the uniform distribution of the reinforcement phase, TiB2 in the matrix. The stress value increases with reaction holding time up to 30 minutes and then it decreases. Hence the optimum reaction holding time of halide salts in Al 6061 alloy is 30 minutes. The percentage elongation of the matrix alloy and the composites with different reaction holding times are also shown in TABLE-2. It decreases with the reaction holding time up to 30 minutes and then it slightly increases. Compared to the Al 6061 alloys, the decrease of percentage elongation of the composite may be due to the presence of reinforcement particles in the composite giving rise to increase in hardness.
3.3. Hardness
The results of the Brinell hardness tests obtained for both the base alloy and the composites with different reaction holding times at different locations over the surface are tabulated as shown in TABLE-3.Table 3. Hardness of alloy and composites 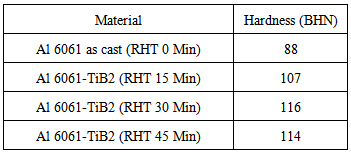 |
| |
|
It is obvious that the presence of TiB2 particles in the aluminium matrix increases the hardness of the composites up to 30 minutes’ reaction holding time with a decrease in hardness for the next 15 minutes’ time. The primary cause of reduction in hardness is the increase of micro porosities due to higher reaction holding time at the temperature of the melt. It can be concluded that absorption of gases by the aluminium melt at 850 C resulted in the increase of micro porosities and hence the reduction in hardness. At the same time, the percentage of elongation reduced significantly up to the same level of reaction holding time. The TiB2 particles in the Al 6061 alloy matrix phase increased the hardness as these particles are very much harder than the alloy Al 6061.
4. Conclusions
Based on the present study, it can be concluded that: AL 6061-TiB2 metal matrix composites were synthesized successfully by incorporating halide salts, K2TiF6 and KBF4 in the Al 6061 alloy at 850°C.TiB2 reinforcement phase was made to be distributed uniformly in the Al 6061 matrix phase by the in-situ method.With increase in reaction holding time, there was an increase in the amount of cryolite slag formed during the reaction between the liquid alloy and the halide salts.A uniform distribution of reinforcement particles has been obtained in the matrix phase. With increase in reaction holding time, there was an increase in tensile strength and hardness of the composite up to 30 minutes of reaction holding time followed by a decrease in both tensile strength and hardness for the next higher level of 15 minutes reaction holding time.A similar opposite trend was seen in the case of percentage of elongation and ductility of the composite with increase in reaction holding time up to 30 minutes.Tensile strength and hardness of the composite synthesized is higher when compared to the cast aluminium alloy.
References
[1] | Clyne, T.W. and Withers, P.J., “An Introduction to Metal Matrix Composites”, Cambridge University Press, Cambridge, pp 1-525, 1995. |
[2] | .S.S. Daniel, V.S.R. Murthy and G.S. Murty, “Metal Ceramic Composites via In-situ Methods”, Journal of Materials Processing Technology, Vol.68, pp.132-155, 1997. |
[3] | M.R. Ghomashchi, A.Vikhrov, “Squeeze Casting: an overview”, Materials Processing Technology, Vol.101, pp.1-9, 2000. |
[4] | Yue N.L., Lu L., Lai M.O., “Application of thermodynamic calculation in the in-situ process of Al/TiB2”, Composite Structures Vol.47, pp. 691-694 1999. |
[5] | T.V. Christy, N. Murugan and S. Kumar, “A Comparative Study on the Microstructures and Mechanical Properties of Al 6061 Alloy and the MMC Al 6061/TiB2/12P”, Journal of Minerals& Materials Characterization& Engineering, Vol.9, No.1,pp.57-65, 2010. |
[6] | C. Cui, Y. Shen and F. Meng, “Review on Fabrication Methods of In-situ Metal Matrix Composites”, Journal of Material Science Technology, Vol.16, pp. 619-626. |
[7] | Ramesh C.S. Abrar Ahamed, Chanabasappa B.H., Keshavamurthy R. “Development of Al 6063-TiB2 in-situ composites”, Material and design Vol.31, pp.2230-2236, 2010. |
[8] | Emamy M., Mahta M, Rasizadeh J., “Formation of TiB2 particles during dissolution of TiAl3 in Al-TiB2 metal matrix composite using an in-situ technique”, Composites Science and Technology, Vol. 66, pp. 1063-1066, 2000. |
[9] | Mandal A., Chakraborty, Murty B.S., “Effect of TiB2 particles on sliding wear behaviour of Al-4Cu alloy”, Wear, Vol., 262, pp.160-166, 2007. |
[10] | S.C. Tjong and Z.Y. Ma, “Micro-structural and Mechanical Characteristics of In-situ Metal Matrix Composites”, Material Science and Engineering: R. Reports, Vol. 29, pp. 49-113, 2000. |
[11] | C.F. Feng and L. Froyen, “Microstructures of In-situ Al/TiB2 MMCs Prepared by a Casting Route”, Journal of Material Science, Vol. 35, pp.837-850, 2000. |