Cristiane Inácio de Campos1, Francisco Antonio Rocco Lahr2, André Luis Christoforo3, Maria Fátma do Nascimento4
1Paulista State University, UNESP/FEIM, Experimental campus of Itapeva, Geraldo Alckmin Avenue, 519, 18409-010, Itapeva/SP – Brazil
2São Paulo University, USP. School of Engineering of São Carlos, EESC. Department of Structural Engineering, Trabalhador Sãocarlense Avenue, 400, 13566-590, São Carlos/SP – Brazil
3Centre for Innovation and Technology in Composites (CITeC), Department of Civil Engineering (DECiv), Federal University of São Carlos (UFSCar), São Carlos, 13565-905, Brazil
4Department of Materials Engineering (SMM), Engineering School of São Carlos (EESC/USP), São Carlos, 13566-590, Brazil
Correspondence to: André Luis Christoforo, Centre for Innovation and Technology in Composites (CITeC), Department of Civil Engineering (DECiv), Federal University of São Carlos (UFSCar), São Carlos, 13565-905, Brazil.
Email: |  |
Copyright © 2014 Scientific & Academic Publishing. All Rights Reserved.
Abstract
The medium density fiberboard (MDF) is a wood derived product. The wood-based panel is normally produced with urea-formaldehyde, melamine-formaldehyde and/or phenol-formaldehyde adhesives. However, the former is considerably toxic and environmentally damaging, while the lather is expensive, thus motivating the search for alternative raw materials in fiberboard production. This research discusses a study of MDF produced from alternative castor oil based polyurethane adhesive and Pinus caribaea var. hondurensis fibers. The castor oil based polyurethane resin developed at the São Carlos Institute of Chemistry, University of São Paulo, is an environmentally friendly vegetal oil-based polymer that is harmless to humans. The Pinus caribaea var. hondurensis offers favorable properties for fiberboard manufacture. The MDF’s performance was evaluated based on the results of physical and mechanical tests recommended by the European standard (EC). Tests results showed higher values than those recommended by the European standard, indicating that the castor oil-based polyurethane resin is promising adhesive for the manufacture of MDF.
Keywords:
MDF, Polyurethane resin castor oil based, Wood-based product
Cite this paper: Cristiane Inácio de Campos, Francisco Antonio Rocco Lahr, André Luis Christoforo, Maria Fátma do Nascimento, Castor Oil Based Polyurethane Resin Used in the Production of Medium Density Fiberboard, International Journal of Composite Materials, Vol. 4 No. 4, 2014, pp. 185-189. doi: 10.5923/j.cmaterials.20140404.02.
1. Introduction
The growing popularity of wooden panels renders this market segment increasingly competitive. Wood-based products offer an interesting alternative to expand the range of materials for use in civil construction, cabinetmaking and other industries. Brazil is a potentially important worldwide producer/supplier of general purpose boards and possesses state-of-the-art technology to produce reconstituted wood products. The advantage of wood-based products is that the wood’s properties can be improved through the application of science and technology [1-3]. Wood-based panels are classified as wood-based layers, fiber and particleboard.Although Brazil’s share in the production and consumption of wooden panel was not significant in the past, this situation has been changing in recent years owing to new investments in board production units, especially, particleboards and MDF [4]. This increase production is also attributed to the increasing use of boards in some industrial sectors, e.g., cabinetmaking, civil construction, packaging, etc.Among wood-based panels are detached the medium density fiberboard (MDF), a product that it offers good work condition. MDF is manufactured to dry, made of fibers lignocellulosics, combined with resin, and compacted by hot pressure. MDF is a nonstructural wood-based panel that is composed of wood fibers bonded together with resin under heat and pressure [4, 5]. In recent years, great changes have taken place in the MDF industry. Production of this product has increased dramatically and new plants are planned worldwide. In 1996, MDF shipments from U.S. plants set another in an unbroken series of annual records, totaling 2.1 million cubic meters, an 8.5% increase from 1995. Production for 1997 production was forecast to be 3 million cubic meters. Canadian plant capacity was predicted to increase 19%, to 1.2 million cubic meters. In 1996, European production of MDF jumped 18% to 4.5 million cubic meters, continuing an unbroken upward trend there.The popularity of this relatively new panel product is due to its capability to be produced in molded form as well as in straight-edged, flat panels for a host of industrial markets [6]. MDF is used extensively in factory-assembled and ready-to assemble furniture, as well as cabinets, underlayment, drawer fronts, molding, and counter tops. Finishes and overlays can be used to provide a grain pattern typical of lumber, and many wood finishing components such as door edgings, decorative trim, frames, and cornices are being replaced by MDF. Moreover, MDF is replacing thin plywood and wet-process hardboard in the production of molded and flush door-skins. New MDF products include generic and proprietary panels. One example is a super-refined board in which fine fibers are distributed throughout the board to facilitate deep routing and machining. In some countries, panels are being made from many different hardwood and softwood species as well as from nonwood-based lignocellulosics from raw materials such as bagasse and cotton stalks.The Adhesives are one of the main components in the production of wood-based panels [7-9]. MDF is produced according to two main specifications: a - for indoor use, glued with urea-formaldehyde resin, which is employed chiefly in the furniture industry, and b - for outdoor use, glued with melamine-formaldehyde resin, employed in civil construction.Urea and melamine-formaldehyde adhesives have a serious drawback, which is the emanation of formaldehyde fumes and use it is limited in countries with strict environmental control. Though MDF is normally produced using formaldehyde based adhesives, however, in our search for new adhesives and resins for the manufacture of boards, we have employed an alternative, castor oil based polyurethane resin to produce MDF in the laboratory.An alternative adhesive deriving from a natural and renewable source, castor oil based polyurethane adhesive is classified as impermeable and non-aggressive to the environment and to humans, besides representing a Brazilian technology [10]. This adhesive is cured at ambient temperature, but curing can be accelerated using temperatures of 60 to 90ºC, and it is believed that its large scale availability on the market will bring its price down to a very reasonable level. Polyols and prepolymers with different characteristics can be synthesized from this natural and renewable source, which, when mixed, result in a polyurethane. Its competitiveness in relation to other polymers is superior to those of material, its mechanical properties are superior to those of petroleum-derived polymers, and the cost of the diisocyanates in Brazil is reasonable [11].Claro Neto [11] characterized the physical and mechanical properties of a castor oil based polyurethane polymer. The study of the chemical properties aimed to characterize the functional organic groups present in the polyol/prepolymer components that react during preparation of the polyurethane. The castor oil based polyurethane was developed for use in medical applications as a bone implant material.To expand the application of this product, Jesus [12] and Azambuja [13] studied of the behavior of castor oil based polyurethane adhesive for use in glued laminated timber (GLT) with reforested species of the genera Pinus and Eucalyptus. The adhesive’s efficiency was evaluated based on mechanical tests of shearing strength parallel to the grain, tensile strength perpendicular and tensile strength parallel to the grain. The results reported by these authors demonstrated that castor oil based polyurethane adhesive is a good alternative for the technological use for GLT.The wood panel industry represents an important segment of the country’s economy, not only because it generates revenue and jobs but also due to its increasing dynamism to continue, technological investments are required to expand and improve the production of panels.Brazil’s prospects for becoming a major manufacturer of particleboard are excellent, with reconstituted wood panels, today represented by MDF and more recently by OSB, promising to change the profile of internal consumption. Some of the practical factors the justify the preferential use of wood-based panels are the reliability of the material, stability of the pieces, possibility of producing pieces with dimensions not found in solid wood, use in modern and complex applications with low cost-efficiency ratio, and utilization of most of the log [14].The purpose of this research, therefore, was to evaluate the performance of medium density fiberboard produced with the wood species Pinus caribaea var. hondurensis and the performance of the castor oil based polyurethane adhesive, comparing the results with the properties of MDF reported in the European standard requirements.
2. Material and Methods
The industrial dry process was used to produce the MDF in the laboratory. The Pinus fiber for the MDF was supplied by DURATEX Madeira Industrializada S.A. and, in collaboration with this research; KHEL Indústria Química donated the castor oil based polyurethane resin.1500 g lots of fiber with 3% moisture content were used for the laboratory scale production of MDF. After being weighed, the fiber was placed in the upper part of a motor-driven gluer machine with a rotation rate of up to 120 rpm. The machine was closed, the motor activated and, with the blades rotating, the glue was added under high pressure to pulverize the adhesive for optimal distribution. After the fiber and glue were properly mixed, the mixture was transferred to another container to smooth out the lumps.The material was then placed in a molding box. After deposition of the fibers, the material (air mattress) was compacted in a pre-press under a load of approximately 800 N, which corresponds to the pre-pressing is to reduce the volume of the mattress to be placed in the press.The pre-pressing procedure was following by pressing in a hydraulic press heated electrically to a temperature of until 160ºC. The pressure applied was adapted to the pressing cycle proposed by Neves [15]. The pressure varies from 0 to 3 MPa. In this work, the pressure on the sheet was determined by 1 cm thick limiters.Starting from the fiber the sheets were produced in the following sequence: drying of the fibers; preparation of the adhesive; mixing of the adhesive with the fibers in the mixer; dissolution of the lumps; preparation and formation of the mattress; cold pre-pressing; hot pressing; cutting and acclimatization of the sheets.Figure 1 illustrates the MDF manufacturing sequence in the laboratory: a) fibers ready to be placed in the mixer; b) material from the mixer, composed of wood fibers, adhesive, catalyzer and water; c) dissolution of lumps in the mixture of the panel’s constituents; d) placement of the mattress in the thermo-mechanical press; e) sheet removed from the press immediately following pressing; and f) sheet ready for use.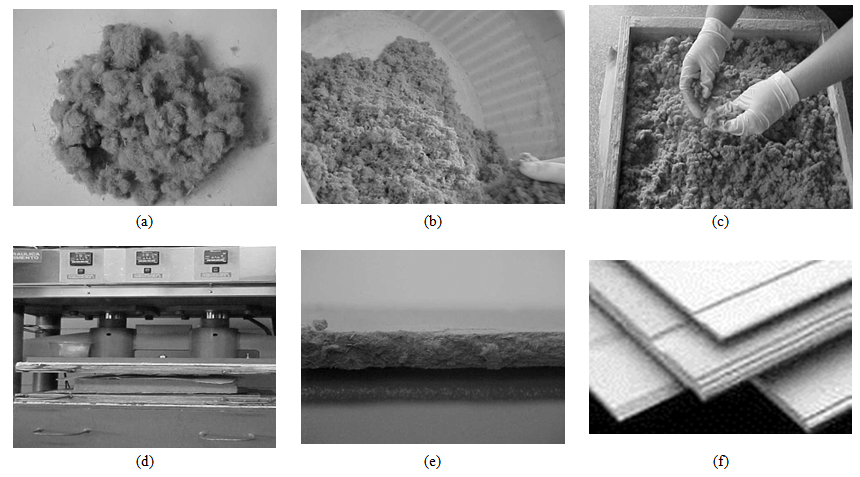 | Figure 1. Sequence of the MDF production process in the laboratory |
Following the manufacturing process, the sheets were acclimatized at a temperature of about 25ºC for 48 hours, after which test specimens were prepared for physical and mechanical tests performed according to the EUROCODE (EC), whose results are listed below:- Density (EC 323) [16];- Moisture content (EC 322) [17];- Swelling in thickness (EC 317) [18];- Water Absorption (EC 317) [18];- Bending tests [MOE - modulus of elasticity; MOR - modulus of rupture] (EC 310) [19];- Internal bond (EC 319) [20].Table 1 presents the minimum requirements stipulated by the European standards.Table 1. Values specified by the Euro MDF Board 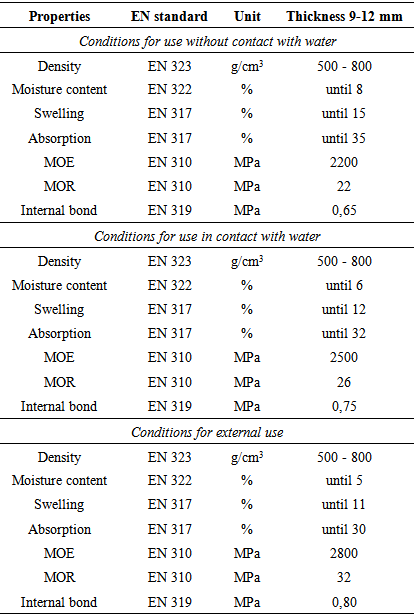 |
| |
|
3. Results and Discussions
The results of physical and mechanical properties of the panels manufactured are showing in Table 2 and Table 3.The results obtained by using castor oil-based polyurethane adhesive and Pinus caribaea var. hondurensis in the production of MDF panels were quite satisfactory when compared with the minimum requirements stipulated by European standards, indicating the possibility of varying the adhesive used in its fabrication and especially used in conditions for use in contact with water (Table 1), demonstrating the capability of the MDF produced.Table 2. Values of physical tests for Pinus sheets produced with polyurethane adhesive 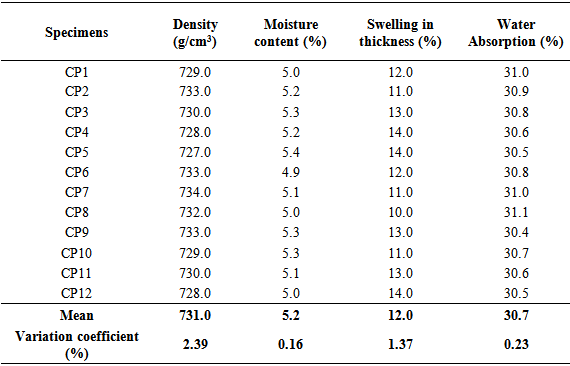 |
| |
|
Table 3. Values of mechanical tests for Pinus sheets produced with polyurethane adhesive 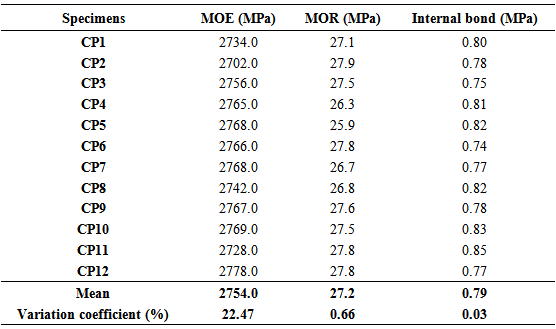 |
| |
|
4. Conclusions
The results of physical and mechanical properties of MDF panels produced were both superior to the requirements established by normative documents used, indicating that the castor oil based polyurethane resin is promising adhesive for the manufacture of MDF as well as all wooden based panels.This would allow for nee materials to be proposed for future use by the wood panel manufacturing sector, and especially of MDF such as that proposed herein, aiming particularly at making use of wood processing residues and adhesive from natural renewable sources, and incentive to realized research news relationship to subject.
ACKNOWLEDGMENTS
The authors gratefully acknowledge FAPESP (Fundação de Amparo à Pesquisa de São Paulo) for financially supporting this research, also gratefully acknowledge to DURATEX Madeira Industrializada S.A. and KHEL Indústria Química by donated materials.
References
[1] | Alves, L. S.; Silva, S. A. M.; Azambuja, M. A.; Varanda, L. D.; Christoforo, A. L.; Goncalves, D.; Rocco, F. A. L. Study of the Feasibility of mix of Species from Sawmill Waste and Limiting for Particleboard. International Journal of Composite Materials (Online), v. 4, p. 30-37, 2014. |
[2] | Ferro, F. S.; Almeida, D. H.; Souza, A. M.; Icimoto, F. H.; Christoforo, A. L.; Rocco, F. A. L. Influence of Proportion Polyol/Pre-Polymer Castor Oil Resin Components in Static Bending Properties of Particleboards Produced with Pinus sp.. Advanced Materials Research (Online), v. 884-885, p. 667-670, 2014. |
[3] | Alves, L. S.; Silva, S. A. M.; Azambuja, M. A.; Varanda, L. D.; Christoforo, A. L.; Rocco, F. A. L. Particleboard Produced with Sawmill Waste of Different Wood Species. Advanced Materials Research (Online), v. 884-885, p. 689-693, 2014. |
[4] | Bertolini, M. S.; Ferro, F. S.; Silva, M. R.; Calil Neto, C.; Christoforo, A. L.; Rocco, F. A. L. Homogeneity Analysis of MDF in Parallel and Perpendicular Directions Related to Panel Production. International Journal of Composite Materials (Online), v. 4, p. 103-107, 2014. |
[5] | Silva, S. A. M.; Christoforo, A. L.; Goncalves, R.; Rocco, F. A. L. Strength Properties of Medium Density Fiberboards (MDF) Manufactured with Pinus Elliottii Wood and Polyurethane Resin Derived from Castor Oil. International Journal of Composite Materials (Online), v. 3, p. 7-14, 2013. |
[6] | Campos, C. I.; Rocco, F. A. L. Estudo comparativo dos resultados de ensaio de tração perpendicular para MDF produzido em laboratório com fibras de Pinus e Eucalipto utilizando uréia-formaldeído. Matéria (UFRJ), Rio de Janeiro, v. 9, n.1, p. 32-42, 2004. |
[7] | Ferro, F. S.; Icimoto, F. H.; Almeida, D. H.; Souza, A. M.; Varanda, L. D.; Christoforo, A. L.; Rocco, F. A. L. Mechanical properties of particleboards manufactured with Schizolobium amazonicum and castor oil based polyurethane resin: influence of proportion polyol/pre-polymer. International Journal of Composite Materials (Online), v. 4, p. 52-55, 2014. |
[8] | Poleto, S. F. S.; Varanda, L. D.; Nascimento, M. F.; Christoforo, A. L.; Rocco, F. A. L. Evaluation of the Mechanical Properties of Particleboards Manufactured with Waste of Pinus elliottii Tree Pruning. International Journal of Composite Materials (Online), v. 3, p. 7-14, 2013. |
[9] | Varanda, L. D.; Nascimento, M. F.; Christoforo, A. L.; Silva, D. A. L.; Rocco, F. A. L. Oat hulls as addition to high density panels production. Materials Research (São Carlos. Impresso), p. 1355-1361, 2013. |
[10] | Araújo, L. C. R. Caracterização química e mecânica de poliuretanas elastoméricas baseadas em materiais oleoquímicos. Dissertação (Mestrado), Instituto de Física e Química de São Carlos. Universidade de São Paulo, São Carlos, 1992. |
[11] | Claro Neto, S. Caracterizações físico-químicas de um poliuretano derivado de óleo de mamona utilizado para implantes ósseos, Tese (Doutorado), Instituto de Química de São Carlos, Universidade de São Paulo, p. 123, São Carlos, 1997. |
[12] | Jesus, J. M. H. Estudo do adesivo poliuretano à base de mamona em madeira laminada colada. Tese (Doutorado), Escola de Engenharia de São Carlos, Universidade de São Paulo, p. 106, São Carlos, 2000. |
[13] | Azambuja, M.A. Avaliação do adesivo poliuretano à base de mamona na fabricação de MLC, Dissertação (Mestrado), Escola de Engenharia de São Carlos, Universidade de São Paulo, São Carlos, 2003. |
[14] | Pranda, J. Painéis de fibra de média densidade feitos de Pinus pinaster e Eucalipto globulus. Área de composição química específica da madeira desfibrada. Drevarsky Vyskum. V. 2. p. 19-28, 1995. |
[15] | Neves, J.M., Celulose e papel – Tecnologia de fabricação de pasta celulósica. Cap. VII p Polpação de alto rendimento e semiquímica. SENAI/IPT – São Paulo, v.1, 1988. |
[16] | European Committee for Standardization. European Standard EN 323 – Parcicleboards and Fiberboards – Determination of density. Bruxelas: 1993. |
[17] | European Committee for Standardization. European Standard EN 322 – Parcicleboards and Fiberboards – Determination of moisture content. Bruxelas: 1993. |
[18] | European Committee for Standardization. European Standard EN 317 – Parcicleboards and Fiberboards – Determination of absorption and swelling in thickness after immersion in water. Bruxelas: 1993. |
[19] | European Committee for Standardization. European Standard EN 310 – Parcicleboards and Fiberboards – Determination of modulus of elasticity in bending and bending strength. Bruxelas: 1993. |
[20] | European Committee for Standardization. European Standard EN 319 – Parcicleboards and Fiberboards – Determination of tensile strength perpendicular to the plane of the board. Bruxelas: 1993. |