Luciano Donizeti Varanda1, Amós Magalhães de Souza1, Diego Henrique de Almeida2, Felipe Hideyoshi Icimoto1, Fabiane Salles Ferro1, André Luis Christoforo3, Francisco Antonio Rocco Lahr4
1Department of Materials Engineering, Engineering School of São Carlos (EESC/USP), São Carlos, 13566-590, Brazil
2Pontifical Catholic University of Minas Gerais (PUC Minas), Department of Civil Engineering, Campus of Poços de Caldas, Poços de Caldas, 37701-355, Brazil
3Centre for Innovation and Technology in Composites – CITeC, Department of Civil Engineering, São Carlos Federal University, São Carlos, 13565-905, Brazil
4Department of Structural Engineering, Engineering School of São Carlos (EESC/USP), São Carlos, 13566-590, Brazil
Correspondence to: André Luis Christoforo, Centre for Innovation and Technology in Composites – CITeC, Department of Civil Engineering, São Carlos Federal University, São Carlos, 13565-905, Brazil.
Email: |  |
Copyright © 2014 Scientific & Academic Publishing. All Rights Reserved.
Abstract
This research presents the production and the evaluation of particleboards manufactured with Eucalyptus grandis and oat hulls (Avena sativa), pressure bonded with castor oil based polyurethane resin (PU). Strength and stiffness properties in static bending of the panels were determined based on the standards ABNT NBR 14810:2006 [1], ANSI A208.1: 1999 [2], BS EN 312:2003 [3] and CS 236-66:1968 [4]. Analysis of variance (ANOVA) was used to evaluate the influence of the factors: mass fractions of PU resin (10, 12 and 14%) and the composition in mass fractions of Eucalyptus grandis (100, 85, 70 and 0%) and oat hulls (0, 15, 30 and 100%) in the properties modulus of elasticity (MOE) and modulus of rupture (MOR). Statistical analysis results indicated that Eucalyptus grandis and adhesive were significant in the MOE and MOR properties. However, the interaction Eucalyptus grandis-adhesive did not significantly affect the properties evaluated.
Keywords:
Eucalyptus grandis, Static bending, Waste recovery, Lignocellulosic particles, Analysis of variance
Cite this paper: Luciano Donizeti Varanda, Amós Magalhães de Souza, Diego Henrique de Almeida, Felipe Hideyoshi Icimoto, Fabiane Salles Ferro, André Luis Christoforo, Francisco Antonio Rocco Lahr, Strength and Stiffness Properties of Particleboards, International Journal of Composite Materials, Vol. 4 No. 2, 2014, pp. 150-156. doi: 10.5923/j.cmaterials.20140402.15.
1. Introduction
Wood-based panels should be highlighted in the scenario of wood products, precisely because they are the main raw material for a range of industries, like furniture, packaging and several segments of the building construction. Among wood-based panels, particleboard (or MDP) is currently the most consumed in the world. In Brazil, according to industry data, MDP production presents a notable increase and continues providing growth prospects for the coming years [5], with applications in civil and rural constructs, objects, furniture inter alia.Waste of Brazilian agribusiness is available in large quantities and has significant potential for employment. Waste production in these segments can reach about 250 million tons per year [6]. Particleboard (or MDP) can be produced from any lignocellulosic material which provides high mechanical strength and specific weight according to standards, just because lignocellulosic structure is similar to timber [7].Several researchers have been well succeeded in the development, characterization and application of wood-based panels with addition of agro-industrial wastes such as particleboard produced with residues of Pinus sp. treated with CCB and PU resin [8], particleboard based on sugar cane bagasse and castor oil based polyurethane (PU) resin [9], particleboard made from the underutilized low-quality raw materials [10], particleboards using mixture of peanut hull and wood chips European Pinus [11], particulate composite based on coconut fiber and PU resin [12]. Alternative addition of Pinus elliottii fibres in cementitious products has also been studied [13], among others. However, product quality can be limited by material choice.Among the agro-industrial wastes, oat hulls generated in cereal processing has great potential especially in relation to their availability. Oat, food product usually consumed in the Brazil, presented in 2011 a production of approximately 400 thousand tons [14]. Oat of hulls represents about 30% of mass of oats cereal [15]. So, Brazilian production of oat hulls represented about 120 thousand tons in 2011. Oat hulls that is by product of processing oat cereal, has been discarded during grain processing, becoming a pollutant to the environment. Therefore, it is necessary, essential and appropriate to establish alternatives for its reuse.Quality of wood-based panels is evaluated by their physical-mechanical properties such as modulus of elasticity and modulus of rupture in static bending; internal adhesion; density; pullout strength of connectors; water absorption; thickness swelling, among others [16]. In this context, the aim of this paper is to produce particleboards with Eucalyptus grandis wood species and oat hulls (Avena sativa), and evaluate their performance in static bending.
2. Material and Methods
2.1. Panels Manufacturing
In panels manufacturing, particles of Eucalyptus grandis (apparent density of 640 kg/m3) and oat hulls (apparent density of 290 kg/m3) were used. These particles were generated in a knifes mill, type Willye of Marconi, brand MA 680 model, using 2.8 mm sieve opening. Eucalyptus grandis was obtained from companies in the city and region of São Carlos, SP, while oat hulls (Avena sativa) were obtained from industry sector.Particleboards with one layer (homogeneous panels) of high density were produced. Mass of particles, bonded with castor oil based polyurethane resin (PU), was established for each set of panels as function of compaction ratio and panels density. In this process PU resin, bi-component, 1:1 ratio between prepolymer and poliol, with solids content of 100% were employed. Proportions of PU resin used were 10, 12 and 14% relative to the dry mass of the particles.Panels produced in this study presented high density (above 800kg/m3), as mentioned in ABNT NBR 14810:2006 [1]. Parameters used in the press cycle were: press pressure (4 MPa), press time (10 minutes) and press temperature (100℃), as in other studies developed in Wood and Timber Structures Laboratory [8, 17]. Fig. 1 shows panels manufacturing. | Figure 1. (a) Particles of both materials, (b) glue machine, (c) pre-press, (d) panel after pre-pressing (e) hydraulic press, (f) panel after squaring |
Particles of both materials (Fig. 1a) were weighed and mixed with glue for five minutes (Fig. 1b). Glue machine used was Lieme, model BP-12 SL. Then, particles with glue were subjected to small press (about 0.013 MPa), as shown in Fig. 1c. Panel pre-pressing was performed by manual mechanical press own manufacturing. Panel after pre-pressing stayed with final thickness about 25 mm, Fig. 1d. The next step was the panel pressing, done in the semi-automatic press Marconi, model MA 098/50, as presented in Fig. 1e. Finally, before 72 hours, necessary for full resin cure and moisture equilibrium with the environment, panels produced were correctly squaring, being removed 20 mm from each edge, as shown in the Fig. 1f.Panels were divided into groups according to the different proportions of particles of Eucalyptus grandis and oat hulls. Table 1 shows factors and levels used for design of experiments, giving rise twelve experimental conditions (EC).Table 1. Experimental factors and levels 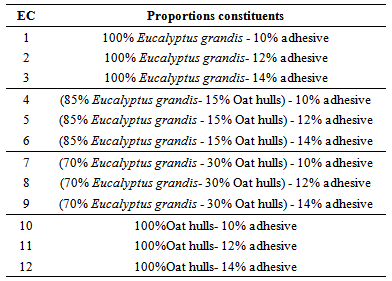 |
| |
|
For each experimental condition (EC), six panels were produced (totaling 72 panels), with nominal dimensions 10×280×280mm. From each panel, one sample with nominal dimensions 50×200mm was obtained, as recommended by ABNT NBR 14810:2006 [1], for static bending test.
2.2. Tests Performed and Results Analysis
The mechanical properties evaluated were modulus of elasticity (MOE) and modulus of rupture (MOR), both obtained by testing a three-point in static bending. Mechanical tests were performed according to ABNT NBR 14810:2006 [1]. Fig. 2 show the mechanical tests performed and specimens evaluated.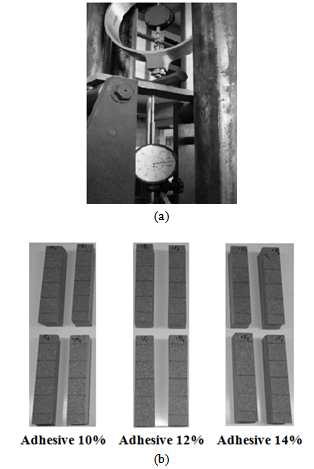 | Figure 2. Static bending test (a) and specimens (b) to obtain the MOE and MOR |
The compaction ratio of the panels was calculated by the following relation: panel density by the density of the material which originated the particles.The variance analysis (ANOVA) was used to investigate the influence of the fraction of particles of Eucalyptus grandis (compositions between particles of both materials) in the mechanical properties MOE and MOR of the panels produced. The significance level (α) was 5%, considering the null hypothesis (H0) the equivalence between the means and the non-equivalence as the alternative hypothesis (H1). P-value greater than the significance level involves accepting H0, rejecting it otherwise. In validation of the ANOVA model, Anderson-Darling and the Bartlett´s tests were used to verify the normality of the distribution and the homogeneity between variances, respectively, both at the 5% level of significance, considering the null hypotheses as the normality and of the equivalence between variances. The null hypothesis hypotheses are accepted if the P-value obtained in the tests are higher than the significance level, rejecting them otherwise. When significance of the factor was detected by ANOVA, Tukey test for grouping of the averages was employed.
3. Results and Discussions
Table 2 presents mean values of density with variation coefficients (VC) and compaction ratio (CR) of the panels manufactured.Table 2. Mean values of density with variation coefficients (VC) and compaction ratio (CR) 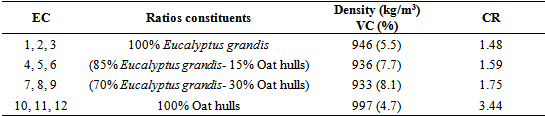 |
| |
|
Variation coefficients of compaction ratio (CR) were not presented in Table 2 because are the same that density property, once CR is calculated by the following relation: panel density by the density of the material which originated the particles.Differences in final density of particleboards are associated to characteristics of particles used in the manufacture of panels, such variables as moisture content and difference in density of the particles employed [16].Panels of experimental conditions 10 to 12 presented higher density than panels of experimental conditions 1 to 9. It can be justified by lower apparent density of oat hulls particles (290 kg/m3), a fact which provides greater accommodation in the material (higher compaction ratio), and consequently higher density to this panels. The variation coefficients (VC) obtained for the density are lower than 9%, reflecting a small variation of this property between the panels evaluated.Mean values of compaction ratio ranged from 1.48 to 1.75 for the experimental conditions 1 to 9, consistent with established by Maloney [18] and Moslemi [19]. For the experimental conditions 10 to 12, the mean value of compaction ratio obtained (3.44) is consistent with the results of Mendes et al. [20], which obtained values between 1.39 to 3.12. Table 3 presents mean values and variation coefficients (VC) of MOR and MOE.Table 3. Mean values of responses variables by experimental condition 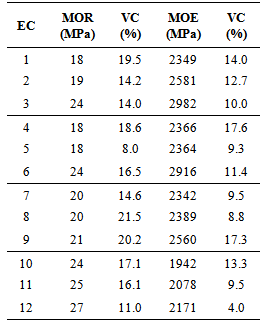 |
| |
|
Variation coefficients for MOE, ranged between 4 and 17.6%, are compatible to those determined by Bertolini et al. [8]. All MOE values exceeded BS EN 312:2003 [3] requirement (2050 MPa), except experimental condition 10. Requirement of ANSI A208.1:1999 [2] and CS 236-66:1968 [4] (2400 MPa) were exceeded in experimental conditions 2, 3, 6 and 9 (Table 3).MOE values have ranged between 1654 e 3593 MPa. P-values underlined in Table 4 (0.000 and 0.004) show significant influence of Eucalyptus grandis and adhesive percentages, respectively, on MOE.Variation coefficients for MOR have ranged between 8 and 21.5%, similar to those obtained by Weber [21].All MOR values exceed codes requirements: ABNT NBR 14810:2006 [1] (18MPa); ANSI A208.1:1999 [2] (16.5 MPa); BS EN 312:2003 [3] (15 MPa) and CS 236-66:1968 [4] (16.5 MPa). MOR values have ranged between 12.5 and 31.2 MPa. Percentages of Eucalyptus grandis and adhesive influenced this variable: p-values 0.000 and 0.003, respectively, as seen in Table 4.Table 4 presents ANOVA results for means of investigated variables. P-values ≤ 0.05 (5%) are underlined. These values are significant at a reliability level 95% [22]. Interaction Eucalyptus grandis-adhesive didn’t significant affected MOE (p-values ≥ 0.05).Table 4. P-values obtained for factors and interactions investigated 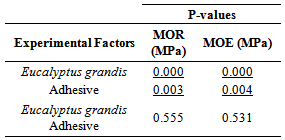 |
| |
|
Results of Anderson-Darling test for MOE and MOR led equal to 0.259 and 0.174, respectively, and Bartlett test for MOE and MOR led equal to 0.381 and 0.165, respectively, evidencing be normal distributions and equivalent variances between treatments, validating the model ANOVA [22]. Normality, independence and homogeneity of residuals obtained from ANOVA for MOE and MOR were evaluated with Anderson-Darling normality test, graphic of residuals × fits and residuals × observation order, respectively, obtained with the aid of software Minitab® version 14.P-values from ANOVA were significant for the individual factors: fractions of particles of Eucalyptus grandis and percentages of adhesive, and the Tukey test was used (Tables 5 to 8), possible to elect the best level (percentages of adhesive) for the fixed factor (fraction of Eucalyptus grandis) and his successors for the mechanical properties. Tables 5 and 6 show the results of the Tukey test for MOR and MOE, respectively. Grouping by Tukey test considered amount of particles of Eucalyptus grandis as factor fixed and ranged the amount of adhesive.Table 5. Results of Tukey test for MOR of the adhesive levels 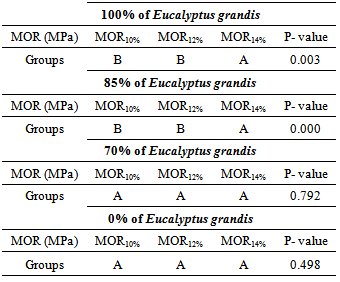 |
| |
|
According to Tables 5 and 6, for fractions 85 and 100% of Eucalyptus grandis, variation in the percentages of adhesive was significant in the MOR and MOE, to 95% level of significance [22]. The proportions of 10 and 12% of adhesive did not differ in both properties (MOR and MOE).For fractions 70 and 0% of Eucalyptus grandis the variation in percentages of adhesive were not significant in the MOR and MOE, and three of adhesive ratios evaluated did not differ in both properties (MOR and MOE).Table 6. Results of Tukey test for MOE of the adhesive levels 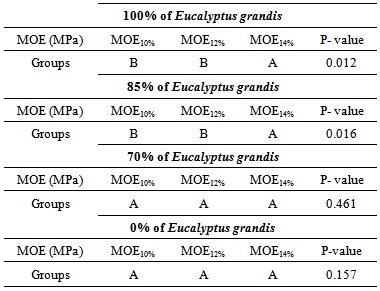 |
| |
|
Tables 7 and 8 show the results of the Tukey test for MOR and MOE, respectively. Grouping by Tukey test considered adhesive amount as factor fixed and ranged the amount of particles of Eucalyptus grandis.Table 7. Results of Tukey test for MOR of the Eucalyptus grandis wood particle levels 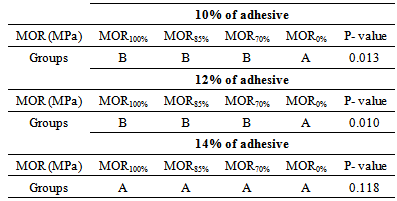 |
| |
|
Table 8. Results of Tukey test for MOE of the Eucalyptus grandis wood particle levels 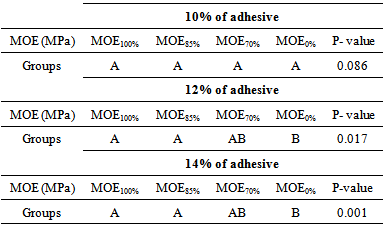 |
| |
|
According to Table 7, for fractions 10 and 12% of adhesive, variation in percentages of particles of Eucalyptus grandis were significant in the MOR. The fractions 100, 85 and 70% of particles of Eucalyptus grandis showed no statistical difference in MOR property. For the fraction 14% of adhesive, the variance in percentages of particles of Eucalyptus grandis was not significant in MOR, and did not differ.According to Table 8, for fraction of 10% of adhesive, variance in percentages of particles of Eucalyptus grandis were not significant in the MOE, and did not differ.For fractions 12 and 14% of adhesive, variation in percentages of Eucalyptus grandis particles were significant in MOE. Ratios 100 and 85% of Eucalyptus grandis particles did not differ in MOE property, for both percentages of adhesive (12 and 14%).Fig. 3 exhibits the main effect plots of the experimental factors on MOE. It can be observed that MOE increases when Eucalyptus grandis and adhesive percentages increase (Fig. 3a and 3b). Gains reached 20.5 and 13.5%, respectively.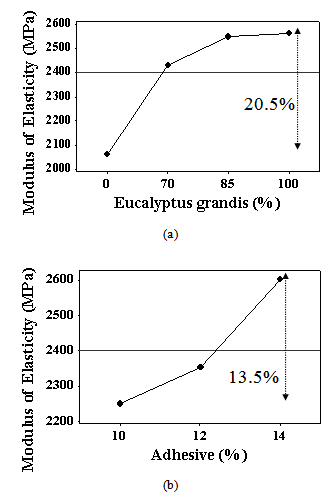 | Figure 3. Main effect plots of the modulus of elasticity (MOE): Fractions of Eucalyptus grandis (a) and fractions of adhesive (b) |
It must be pointed out that fraction 0% of oat hulls (or 100% of Eucalyptus grandis) in Fig. 4a, refers to experimental conditions 1, 2 and 3 (Table 1).Authors as Lee and Kang [23] and Melo et al. [24] have obtained analog results, i.e., reduction of MOE values when another material is added. Reduction of MOE values between the experimental conditions is due to the many variables involved in the manufacturing process of panels (density of materials, pressing variable, adhesive used) that directly influence the final quality of the panel and it’s physico-mechanical properties [16].It can be observed that MOR increases with adhesive percentage (Fig. 4b), proportioning gains of 15.9%. Adding Eucalyptus grandis, in experimental conditions 0 to 100%, reduced MOR values in 22.5% (Fig. 4a). Interaction Eucalyptus grandis-adhesive didn’t significant affected MOR (p-values ≥ 0.05, as seen in Table 4). MOR values in this study were similar to those obtained by Iwakiri et al. [25]: high values statistically to MOR when adhesive percentage increased. Khorami and Ganjian [26] tested the fiber-cement reinforced with agricultural wheat fibers and Eucalyptus and concluded that such material had MOR and MOE acceptable based on standards consulted.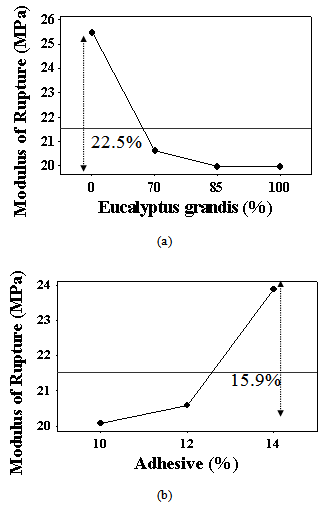 | Figure 4. Main effect plots of the modulus of rupture (MOR): Fractions of Eucalyptus grandis (a) and fractions of adhesive (b) |
4. Conclusions
Results obtained allow the following conclusions:- MOE values have been exceeded BS EN 312:2003 [3] requirement in eleven of twelve experimental conditions and, also, ANSI A208.1:1999 [2] and CS 236-66:1968 [4] requirements in four experimental conditions;- All MOR values have been exceeded requirement of ABNT NBR 14810:2006 [1], ANSI A208.1:1999 [2], BS EN 312:2003 [3] and CS 236-66:1968[4];- Percentages of Eucalyptus grandis and adhesive were influent in MOE and MOR values;- Interaction Eucalyptus grandis-adhesive didn’t affected MOE and MOR values;- Adding oat hulls particles imposes reduction in MOE and increase in MOR values;- Best values of MOE and MOR were obtained with 14% of adhesive;- Better properties to particleboards evaluated in this study were obtained to compositions: 90 to 100% of Eucalyptus grandis; 0 to 10% of oat hulls and e 14% of adhesive.
ACKNOWLEDGEMENTS
The authors would like to thank the São Paulo Research Foundation (FAPESP – process number 2010/14407-7) and the Coordination for Improvement of Higher Education Personnel (CAPES) - by the scholarships granted and by support the researches.
References
[1] | Brazilian Association of Technical Standards, ABNT NBR 14810. Plywood Sheets. Rio de Janeiro, 2006. |
[2] | American National Standards Institute, ANSI A208.1. Particleboard. In: Composite Panel Association. Gaithersburg, 1999. |
[3] | British Standard, BS EN 312. Particleboards – specifications. London, 2003. |
[4] | Commercial Standard, CS 236-66. Mat formed Wood particleboard, 1968. |
[5] | Brazilian Association of Wood Panels Industry - ABIPA. Números do setor em 2012. Available  Accessed: 06/12/2013. |
[6] | Tamanini C, Hauly MCO. Resíduos agroindustriais para produção biotecnológica de xilitol. Ciências Agrárias, 25 (4), p. 315-330, 2004. |
[7] | Rowell RM, Han JS, Rowell JS. Characterization and factors affecting fiber properties. In: Frollini E, Leão AL, Mattoso LHC, editors. Natural polymers and agrofibers composites, São Carlos: Embrapa Instrumentação Agropecuária; 2000, p. 115-134. |
[8] | Bertolini MS, Rocco Lahr FA, Nascimento MF, Agnelli JAM. Accelerated Artificial Aging of Particleboards from Residues of CCB Treated Pinus sp. and Castor Oil Resin. Materials Research, 16 (2), p. 293-303, 2013. |
[9] | Fiorelli J, Rocco Lahr FA, Nascimento MF, Savastano Junior H, Rossignolo JA. Particleboards based on cane bagasse and castor resin: production and properties. Acta Scientiarum. Technology, 33, p. 401-406, 2011. |
[10] | Ashori A, Nourbakhsh A. Effect of press cycle time and resin content on physical and mechanical properties of particleboard panels made from the underutilized low-quality raw materials. Industrial Crops and Products, 28 (2), p. 225-230, 2008. |
[11] | Guler C, Copur Y, Tascioglu C. The manufacture of particleboards using mixture of peanut hull (ArachishypoqaeaL.) and European Black pine (Pinus nigra Arnold) wood chips. Bioresource Technology, 99 (8), p. 2893-2897, 2008. |
[12] | Fiorelli J, Curtolo DD, Barrero NG, Savastano Junior H, Pallone EMJA, Johnson R. Particulate composite based on coconut fiber and castor oil polyurethane adhesive: An eco-efficient product. Industrial Crops and Products, 40, p. 69-75, 2012. |
[13] | Morton JH, Cooke T, Akers SAS. Performance of slash pine fibers in fiber cement products. Construction and Building Materials, 24 (2), p. 165-170, 2010. |
[14] | Brazilian Institute of Geography and Statistic - IBGE. Levantamento Sistemático da Produção Agrícola. Available from: < http://www.sidra.ibge.gov.br>. Accessed: 26/11/2013. |
[15] | Webster FH. Oats. In: Henry RJ, Kettlewell PS, editors. Cereal grain quality, Atlanta, p.179-203, 1996. |
[16] | Iwakiri S. Painéis de madeira reconstituída. Curitiba: FUPEF, 2005. |
[17] | Rocco Lahr FA (Org.). Produtos Derivados da Madeira: síntese dos trabalhos desenvolvidos no Laboratório de Madeiras e de Estruturas de Madeira, SET/EESC/USP. São Carlos: EESC/USP, 2008. |
[18] | Maloney TM. Modern particleboard and dry-process fiberboard. San Francisco: Miller Freeman, 1993. |
[19] | Moslemi AA. Particleboard. London: Southern Illinois University Press, 1974. |
[20] | Mendes RF, Mendes LM, Carvalho AG, Guimarães Júnior JB, Mesquita RGA. Determinação do módulo de elasticidade de painéis aglomerados por Stress Wave Timer. Floresta e Ambiente, 19 (2), p. 117-122, 2012. |
[21] | Weber C. Estudo sobre viabilidade de uso de resíduos de compensados, MDF e MDP para produção de painéis aglomerados. Dissertação - Setor de Ciências Agrárias. Curitiba: Universidade Federal do Paraná, 2011. |
[22] | Montgomery DC. Design and analysis of experiments. 6thed. Arizona: John Wiley & Sons Inc., 2005. |
[23] | Lee HH, Kang CW. Development of rice hull insulation board using urea formaldehyde resin. Mokchae Konghak, 26 (4), p. 50-55, 1998. |
[24] | Melo RR, Santini EJ, Haselein CR, Stangerlin DM. Propriedades físico-mecânicas de painéis aglomerados produzidos com diferentes proporções de madeira e casca de arroz. Ciência Florestal, 19 (4), p. 449-460, 2009. |
[25] | Iwakiri S, Cunha AB, Albuquerque CEC, Gorniak E, Mendes LM. Resíduos de serraria na produção de painéis de madeira aglomerada de Eucalipto. Scientia Agraria, 1 (1-2), p. 23-28, 2000. |
[26] | Khorami M, Ganjian E. Comparing flexural behaviour of fibre–cement composites reinforced bagasse: Wheat and eucalyptus. Construction and Building Materials, 25 (9), p. 3661-3667, 2011. |