N. Ramesha1, S. Akhtar2
1Govt Tool Room & Training Centre Mysore, Karnataka, India
2Central Institute of Plastics Engineering & Technology, Mysore, India
Correspondence to: S. Akhtar, Central Institute of Plastics Engineering & Technology, Mysore, India.
Email: |  |
Copyright © 2014 Scientific & Academic Publishing. All Rights Reserved.
Abstract
Wood plastics composites (WPCs) have been developed not only to make plastics biodegradable but also to save valuable natural resources. With advancements in technology and by addressing the major problems associated with the WPCs such as moisture absorption and low thermal stability of wood, the WPCs are finding their way into numerous applications. For this reason a better understanding of the properties of such materials with regard to machining and surface quality is necessary. This paper reports results of LASER etching of wood plastic composites containing 30-40% wood filler in Polypropylene matrix. The LASER etching has been carried out in air, argon and under water. The LASER etching parameters were varied and the surface roughness and micro-hardness results for LASER etching in air, argon and under water were obtained and compared.
Keywords:
LASER etching, Wood plastics composite (WPC), Machining
Cite this paper: N. Ramesha, S. Akhtar, LASER Etching of Wood Plastics Composites, International Journal of Composite Materials, Vol. 4 No. 2, 2014, pp. 125-129. doi: 10.5923/j.cmaterials.20140402.11.
1. Introduction
Wood Plastics Composites (WPCs) are produced by mixing wood flour or fibre and plastics to produce a material that can be processed like conventional plastics and has the best features of wood and plastics. WPCs are light in weight owing to the low specific gravity of wood. They are attracting a lot of attention due to the fact that the addition of up to 60% of wood flour in WPCs reduces considerably the non-biodegradable content making them more environment-friendly. WPCs have better resistibility to atmospheric changes, insects and fungi attacks. Further, they do not crack and splinter. WPCs are at the centre of research for alternate decking materials. Availability of plastics in abundance, ease of processing and ability to mix with wide variety of fillers along with reasonable price make WPCs well-suited for decking materials.Due to increased usage of WPCs for a wide range of applications there will be an increased demand for secondary processing of such materials. For many applications WPCs need secondary processes like creating an opening in solid surfaces, changing profiles of an edge, or for achieving smoother surfaces for certain applications.The usage of WPCs is increasing all over the world particularly for floors, walls and entrance lobbies etc.The WPCs manufactured do not have attractive and glossy outside surfaces initially. Secondary processes like milling and turning are often used to make these surfaces more attractive. LASER etching is a very fast process and can be employed to make attractive textures and artistic images on the WPC surfaces. The present studies will definitely be helpful in increasing the application of WPCs in various areas. Furthermore, applications of LASER etching for polymer composites (which do not have any standard etching parameters as in case of metals) have not been reported so far.The paper presents a preliminary study of the effect of various LASER parameters on etching of the WPCs as there is no literature available on the subject.
2. Experiment and Methodology
2.1. Material and Machining Process
Machine: The machining trials were carried out on a 75W Nd-YAG CNC LASER marking Machine (make LASER CHEVAL, France). Specimen material: The specimen material taken for our experiment was a commercially available WPC with extruded cross-section size of 20x100mm. Samples of 200mm length were cut from the extruded cross-section for the present study. Measurements and Analysis: Micro-hardness of LASER etched specimen was measured by CLEMAX Micro-hardness Machine and images were taken at magnifications of 50x and 200x. The micro-hardness of specimen was checked for the load of 10gms. Profilometer: The surface roughness was measured using a Profilometer ‘HANDY SURF E35A’ manufactured by ZEISS. The average Roughness Ra values were recorded from the instrument.The Average Standard Deviation (Avg. S.D.) shown in the micro-hardness and surface roughness graphs indicates the spread of the data.Procedure: The LASER etching of WPC specimen was carried out on Nd-YAG CNC LASER marking machine. The wave length of LASER beam was 1.064µm. The entire LASER etching was done on a single piece of WPC sample having an area of 15x15mm and the etching parameters such as LASER power, pulse width, speed, and frequency were varied and etching was done in the atmospheric air media as shown in Figure 1(a). The experiment was repeated by varying the parameters at different places on the same WPC specimen and each etched area was marked on the side for identification.The average roughness and micro-hardness of the etched surface were measured and recorded. The experiment was repeated for argon and water media. For Argon media the argon gas of 99.9% purity was supplied by a tube on to the etched area at a flow rate of 25 litres per min continuously while LASER etching was being done as shown in Figure 1(b). For water media, the specimen was immersed in water in a plastic container and the level of water above specimen was about 2mm as shown in Figure 1(c). Pure de-mineralized water was used for the experiment.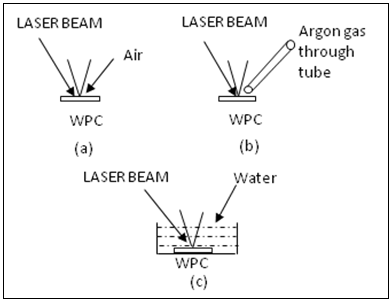 | Figure 1. Schematic experimental set-up for LASER etching in (a) air, (b) argon and (c) water |
The LASER pulse parameters during LASER etching under water was similar to the LASER shock process as shown in Figure 1(c) with the exception that ablation not shock was desired. To achieve the desired result fluence was lowered and pulse number increased. The fluence was taken to a level where the material usually vaporizes. The first experiment of LASER machining under a water film was made with the purpose of studying the processes of material removal in the interests of emission spectroscopy [1]. However, today the main reason for water assisted LASER etching is the elimination of debris deposition in the machined area. This results in cleaner and more precise surface profiles and avoids any need for after-cleaning of the work piece. The effect of the liquid on LASER etching depends on the liquid and processing parameters. When LASER etching is done in liquid, the debris is carried away due to thermal convection of liquid or by bubble-induced liquid motion [2].
3. Results and Discussion
3.1. Effect of LASER Power on Properties of the WPC Surface
Before LASER etching, the WPC sample had an average micro-hardness value of 12 HV. The comparison of variation of micro-hardness with power in different media like air, water and Argon is shown in Figure 2. It is clear that in air and argon, the micro-hardness increases with increase in LASER power. Figure 3(a) shows the micrograph of the WPC surface before LASER etching. From the micrographs for air, argon and water shown in Figure 3 and Figure 4, it is evident that the increasing power of the LASER causes the material to burn more vigorously resulting in more char formation. This results in increase in micro-hardness. However, in water media, the water dissipates the heat generated during LASER etching so the WPC does not undergo burning as it does in air and thus no char formation is observed in water like the one seen in air. Consequently the change in micro-hardness under water media is considerably less than that in air and argon as shown in Figure 2. The micrographs shown in Figure 3 and Figure 4 corroborate the same for water medium.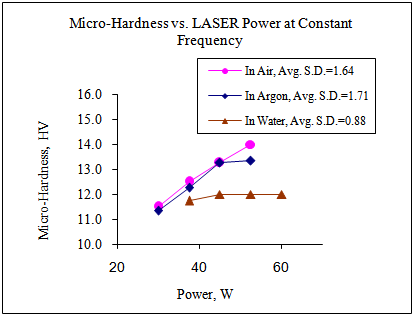 | Figure 2. Effect of LASER Power at constant frequency on the Micro-hardness of WPC LASER etched in different media |
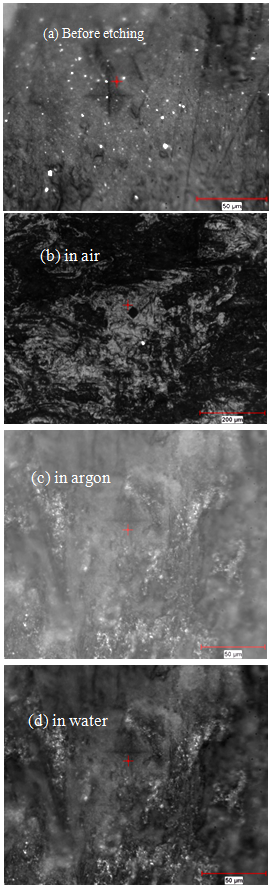 | Figure 3. LASER etching of WPC (a) before etching,and etching in (b) air, (c) argon and (d) water. LASER beam 1.064µm (Nd:YAG LASER) Power 37.5 W, Speed 350mm/sec, Frequency 12 kHz, Pulse 5µsec |
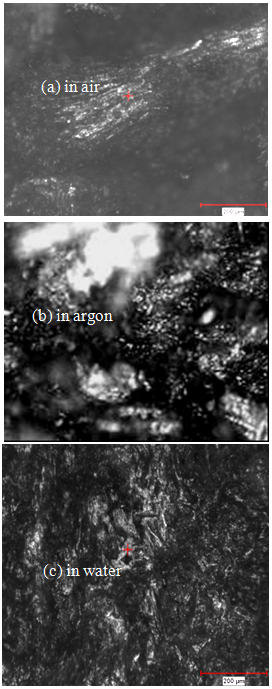 | Figure 4. Micrographs of LASER etched surface of WPC in (a) air, (b) argon and (c) water. LASER beam 1.064µm (Nd:YAG LASER) Power 52.5 W, Speed 350mm/sec, Frequency 12 kHz, Pulse 5µsec |
Machining in water reduces formation of carbon by burning of wood and plastic and reduces debris re-deposition in machined area at short LASER pulses (in microsecond / nano second). The WPC sample showed an average surface roughness value of 0.97 microns prior to LASER etching. The variation in surface roughness of the samples on being exposed to the LASER beam in different media viz. air, argon and under water is shown in Figure 5. The changes observed in air and argon is quite similar. There is hardly any change up to 40 Watts but as the power increases from 40 to 50 Watts the roughness increases suddenly. After that further increase in the LASER power has no effect on the surface roughness. 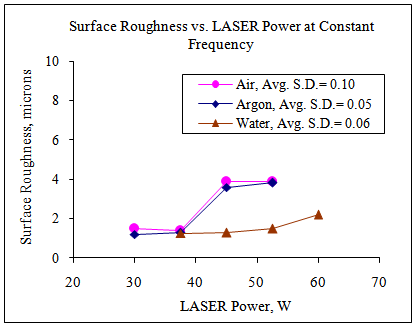 | Figure 5. Effect of LASER power at constant frequency on the Surface Roughness of WPC LASER etched in different media |
Apparently at the lower power values burning starts and the debris resulting from etching causes roughness values to increase. But at higher LASER power values charring starts to occur and therefore roughness values do not change any further. On the other hand, under water LASER power has little effect on the roughness at low power values. Under water the surface roughness of WPC increases gradually at with increasing LASER power. Also charring does not occur under water. The low values of roughness observed under water in contrast to that in air and argon is apparently due to elimination of re-deposition of debris (burnt material) and non-formation of carbon char unlike in the cases of air and argon which results in cleaner and more precise surface.When LASER etching is done under water the debris resulting from etching is carried away due to the thermal convection of liquid or by bubble induced liquid motion.It is observed that when LASER etching is done in air there is a layer of carbon which is darkening the LASER etched WPC surface as shown in Figure 6(a). This darkening is due to burning of wood particles in the presence of oxygen resulting in a charred surface. This effect is reduced slightly in argon media as seen in Figure 6(b). However when the LASER etching is carried out under water, the surface is almost free from char and appears to be neat as can be seen in Figure 6(c).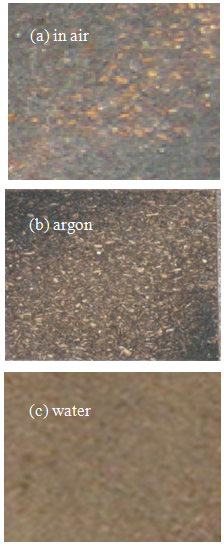 | Figure 6. Photo images of LASER etched area of WPC in (a) air, (b) argon and (c) water |
3.2. Effect of LASER Beam Frequency on Surface Properties of WPC
The effect of LASER frequency on LASER etching of WPC in air was studied at a constant LASER power of 30 W. It was observed that the LASER frequency has negligible effect on the surface roughness of WPC in air as seen in Figure 7. This could be attributed to less burning of wood particles at low frequencies. Even when the frequency of LASER power was increased there was hardly any effect on the surface roughness values. At constant power of 30W, the effect of LASER frequency on micro-hardness is also shown in Figure 7. The micro-hardness reduces slightly with the increase of LASER frequency up to 10 kHz and then appears to increase somewhat at 12 kHz frequency. At lower frequencies, the thin layer of plastics on the top melts causing the micro-hardness to reduce. But at higher frequencies the plastics and the wood fibres start to burn leaving a carbonaceous layer behind which is reflected in the increased value of micro-hardness at 12 kHz. The same is visually seen in the micrographs of the samples as shown in Figure 8 (a) & (b).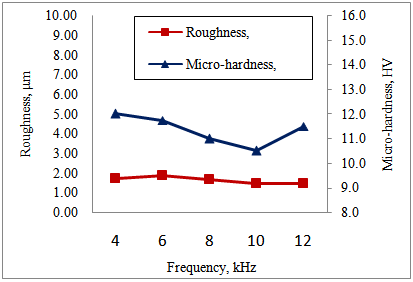 | Figure 7. Effect of LASER beam Frequency on the Surface Roughness and Micro-hardness of the WPC |
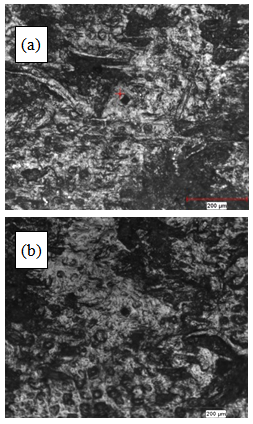 | Figure 8. Micrographs of LASER beam etched surface of WPC after etching in air at LASER Frequency of (a) 4 kHz and (b) 12 kHz at constant LASER Power of 30W, Speed 350mm/sec, Frequency 12 kHz and Pulse 5µsec |
3.3. Effect of LASER Beam Speed on Surface Properties of WPC
At constant LASER power of 30 W, the effect of LASER etching speed on micro-hardness of WPC can be seen in Figure 9. The micro-hardness reduces slightly with increasing LASER etching speed; this may be due to reduction in LASER exposure time which consequently reduces the burning of both plastic and wood which can be observed in the images shown as Figure 10 (a) & (b) at LASER etching speeds of 300mm/sec and 600mm/sec at constant LASER power of 30W. Increase in LASER etching speed has little effect on the roughness for similar reasons as stated above in the case of micro-hardness.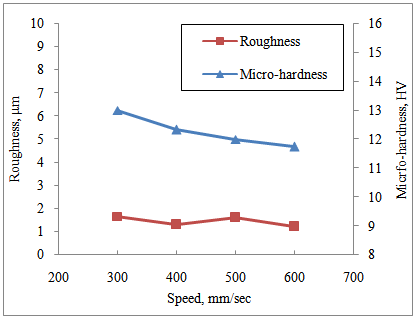 | Figure 9. Effect of speed of LASER beam on the Roughness and Micro-hardness of WPC in air at constant LASER Power of 30 W |
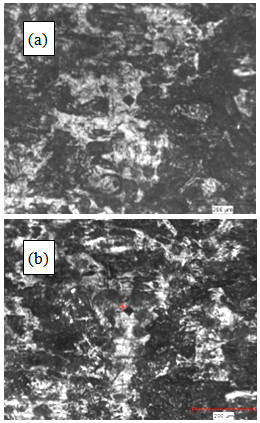 | Figure 10. Micrographs of WPC surface after LASER etching at LASER Speed of (a) 300 mm/sec and (b) 600 mm/sec at constant LASER Power of 30W and constant Frequency |
4. Conclusions
Preliminary studies were conducted to ascertain the effect of LASER etching on Wood Plastics Composites (WPCs). The quality of LASER etching on WPC was studied by measuring the surface roughness and micro-hardness of the etched WPC surface and also by visual examination of the etched surface. The effect of variation of LASER parameters such as Power, Speed and Frequency while keeping the hatching angle and pulse duration constant were studied. The effect of the media in which LASER etching was done was also studied by conducting the experiment in air, argon (inert environment) and under water. It was observed that LASER power had considerable effect on the etching quality while LASER frequency and LASER speed had much less effect. Particularly when the LASER etching was carried out under water there was much less charring and a cleaner WPC etched surface was found as compared to that carried out in air or argon.It was observed that etching under water provides better tolerances due to the absence of re-deposition of debris unlike that in air and argon. Among the parameters under which LASER etching was carried out, it was observed that the LASER power and medium had more effect on the micro-hardness and roughness of the WPCs than the LASER speed and frequency.
ACKNOWLEGDEMENTS
The authors would like to acknowledge the valuable inputs provided by Prof. Siddaramaiah, SJCE, Mysore, India.
References
[1] | Ageev VA. Study of the erosion of metals in liquids. Zh Prikl Spektrosk., 3(1), 42-46, 1975. |
[2] | Kruusing A. Underwater and water-assisted laser processing: Part 2–Etching, cutting and rarely used methods., Optics and Lasers in Engineering, 329–352, 2004. |