Agunsoye J. O.1, Talabi S. I.2, Obidiegwu E. O.1, Awe I. O.3
1Department of Metallurgical and Materials Engineering, University of Lagos, Akoka
2Department of Materials and Metallurgical Engineering, University of Ilorin, Ilorin
3Department of Metallurgical Engineering, Yaba College of Technology, Yaba, Lagos
Correspondence to: Agunsoye J. O., Department of Metallurgical and Materials Engineering, University of Lagos, Akoka.
Email: |  |
Copyright © 2014 Scientific & Academic Publishing. All Rights Reserved.
Abstract
Epoxy resin of the type LY556 reinforced with the foundry basic slag particulates with a known composition has been investigated. 5-20% of foundry basic slag particulates were added at 5%wt interval. The characterisation tools such as scanning electron microscope, TGA 701 and X-ray diffractometer were employed for the investigation of the morphology, thermal stability and phase composition of the composites. The Pin on Disc machine was used for wear resistance characteristics in accordance with ASTM standards. The results revealed that the addition of foundry basic slag particulates at 80um enhanced the thermal stability and wear resistance of the developed composites. The wear resistance increase of the developed composites with the load and speed increase was attributable to high packing density and refractoriness of the newly formed phases. The load and speed have negative impact on the wear resistance of the developed composites. Furthermore, the natures of the worn particles at the interphase between examined wear sample and emery paper play a significant role in the investigation of the composite wear behaviour. The developed epoxy resin-foundry basic slag particulate composites are excellent materials which can be used for electrical insulation, protective case for electric iron, television and radio.
Keywords:
Keyword Epoxy resin, Foundry slag, Thermal stability, Thermogravimetric analysis
Cite this paper: Agunsoye J. O., Talabi S. I., Obidiegwu E. O., Awe I. O., The Development and Characterisation of Epoxy-Foundry Basic Slag Particulate Composite Materials, International Journal of Composite Materials, Vol. 4 No. 2, 2014, pp. 93-102. doi: 10.5923/j.cmaterials.20140402.08.
1. Introduction
Thermosets reinforced composites compared with monolithic metal alloys have found wide engineering applications due to their low density, reasonably good strength and wear resistance. Several research efforts have been geared towards optimizing its properties. Extensive research has been carried out on the use of particulate inorganic materials as filler in reinforcing epoxy resin composites. Particulate reinforced composites are very attractive due to the ease of manufacturing and mouldability. It has been observed that the additions of hard filler particles into polymer based composites, can optimize the developed composites in the form of higher modulus and improved strength (Acosta et al., 1986; Pukanszky, 1995; Gregory et al., 2003). In order to produce a low cost composite, the use of cheap and easily available fillers is a viable option. But, due to high cost of conventional ceramic fillers, it has become important to explore the potential of cheap materials like industrial wastes as fillers for the development of particle-reinforced polymer composites. Huge amount of minerals are released from the industries as a waste materials which can cause serious environmental problems. The accumulation of large amounts of waste in nature is a core problem from an environmental perspective. Government regulations and eco-consciousness has therefore forced the engineering sector to look for alternative methods to use these wastes. Appropriate usage of these industrial wastes as filler in composites development can enhance both the physical and mechanical properties of conventional polymer materials. Industrial waste such as red mud, blast furnace slag, fly ash, flue dust has been used as filler to reinforce polymer (Pukanszky, 1995: Alok and Amar, 2002; Parvaiz, et al.; Acharya et al., 2008; Mohini et al., 2008; Amar and Alok, 2009; Prasanta et al., 2012).The process of iron smelting is associated with the generation of slag which constitutes a major industrial waste in the foundries industries. The main sources of slag in a furnace are the refractory lining, and various oxides brought in during charging fluxes. Scale and sand are formed in the furnace such as (FeO, SiO2, MnO, etc.). In order to reduce the negative impact of the foundary slag on public health, there is a need for proper waste management in which one of the options is to use it in the development of new engineering materials. In this work, the effect of foundry slag particulates on the thermal stability and wear resistance of the epoxy resin was investigated. The work was also aimed at eliminating the waste from our environment.
2. Materials and Methodology
LY 556 Epoxy resin has been used as the matrix with foundry basic slag particulate as reinforcing filler (see Plate 1). A mixture containing 95%wt epoxy resin (LY 556) and 5%wt foundry slag particulates were blended together. The blend was manually stirred vigorously for 3minutes with a glass rod inside one litre capacity stainless basic pot. The blend was poured into a two halves carbon basic die mould with two locating pins for proper alignment (see Plate 2). The epoxy resin-foundry basic slag particulate blend was left for 24 hours in the mould for curing after which the epoxy resin-foundry-slag particulate composite was carefully removed from the mould (Plate 3). The same processes were repeated in the development of the remaining epoxy resin-foundry slag particulate composite blends with increasing percentage compositions of foundry basic slag particulate additions at 10, 15 and 20%wt respectively. Samples of the as-cast epoxy resin –foundry slag particulate composites are presented in Plate 4.Each sample of the epoxy resin-foundry basic slag particulate composites was shaped into different coupons for x-ray diffraction (XRD), microstructural analysis; thermo gravimetric analysis (TGA), and wear tests.Phase distribution and segregation present in the matrix of the developed epoxy resin-foundry basic slag particulate composites was analysed with the aids of X-ray diffractometer.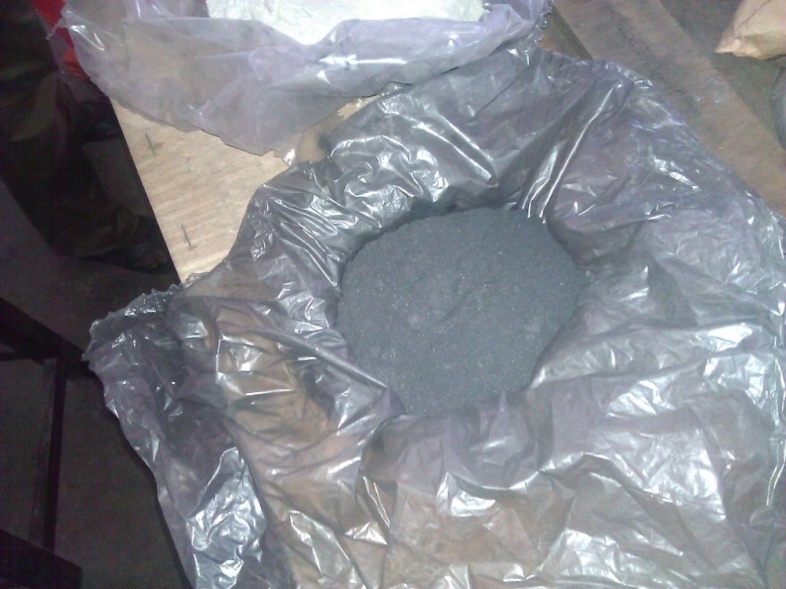 | Plate 1. Foundry basic slag |
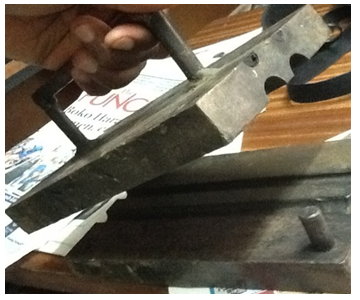 | Plate 2. A medium carbon basic die mould with improvised cavity |
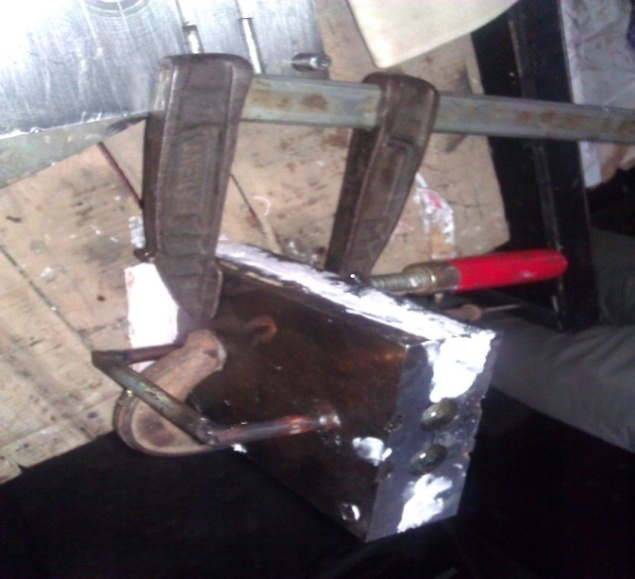 | Plate 3. Curing of the epoxy resin-foundry slag particulate blend |
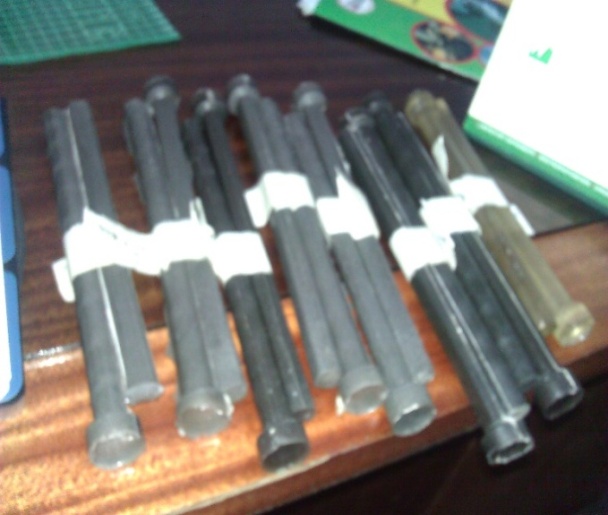 | Plate 4. Cast ingots of the epoxy resin-basic slag particulate composite |
Microstructural analysis was carried on the representative sample of the developed epoxy resin-foundry basic slag particulate composites with the aids of the Scanning Electron Microscope model EVOMA 10 LaB6 Analytical VP-SEM at 20KV.Thermo gravimetric analyser model TGA 701 was used to investigate the oxidation characteristics and thermal stability of the developed epoxy resin-foundry basic slag particulate composites under linear temperature ramp conditions at a heating rate of 10℃/min starting from room temperature to the maximum temperature of 900℃ at which the weight of the sample remained constant.The tribological behaviour of the developed epoxy resin- foundry basic slag particulate composite was studied with the aids of pin on disc machine. The wear test was carried out on a 200mm circular rotating disc with attached emery paper of 180 grit size. The initial weight of the coupon before the test was measured with the aids of the digital electronic scale. The surface of the test sample was placed against the rotating disc for a period of 60s under different applied loads and speed. The weight difference before and after the wear test were measured in grammes with the aids of digital electronic scale. The experiment was rerun for four times and the weight loss at each instance was calculated using equation 1 | (1) |
The volume loss for each sample of experiments was calculated using equation 2  | (2) |
Sliding distance and moment were calculated using equations 3 and 4 respectively | (3) |
 | (4) |
The wear coefficient of each sample was calculated using equation 5 | (5) |
3. Results and Discussion
3.1. XRD Compositional Analysis
Figures 1-3 show the diffraction pattern of spots or reflection reported on a screen of a laser pointer of the foundry slag and epoxy resin-foundry basic slag particulate composite, examined with the aids of X-ray diffractometer.Figure 1 reveals the presence of following compounds: haematite, pyrolusite, high quartz, burnt lime, phosphorus oxide and alumina in the basic foundry slag. The count scores of the compounds with their corresponding compound formulae are also presented in Table 1.Table 1. Count Scores and Chemical Formulae of Identified Compounds present in the basic slag 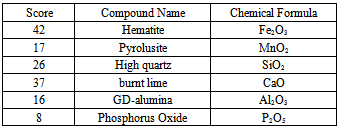 |
| |
|
Figure 2 and 3 represent the result of the analysis for the epoxy resin-foundry basic slag particulate composites, indicating the distribution of phases present within the matrix of the developed composites. The chemical formulae and the count score of the compounds are presented in Tables 2 and 3 respectively.It was observed that some new phases which include MnAl6, SiO2, Al0.64Ti0.36, TiO2, Fe3C, Al2O3, Ti3O5 etc were formed due to interaction of slag particulates and the epoxy resin. This might be due to the exothermic reaction taking place during curing, mixing and solidification processes.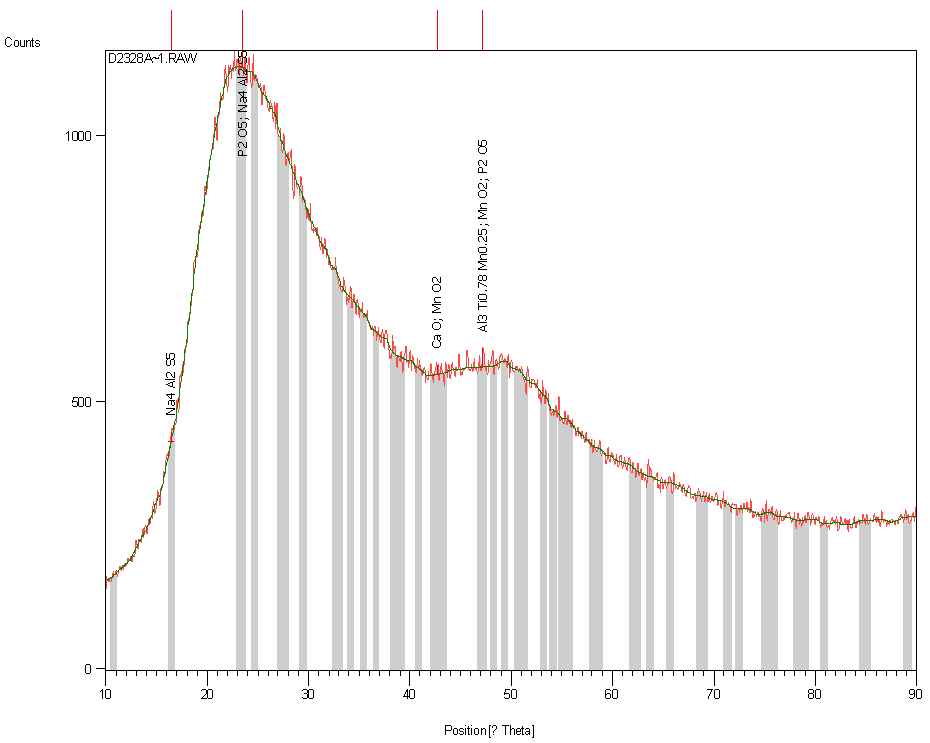 | Figure 1. XRD Compositional Analysis of the slag |
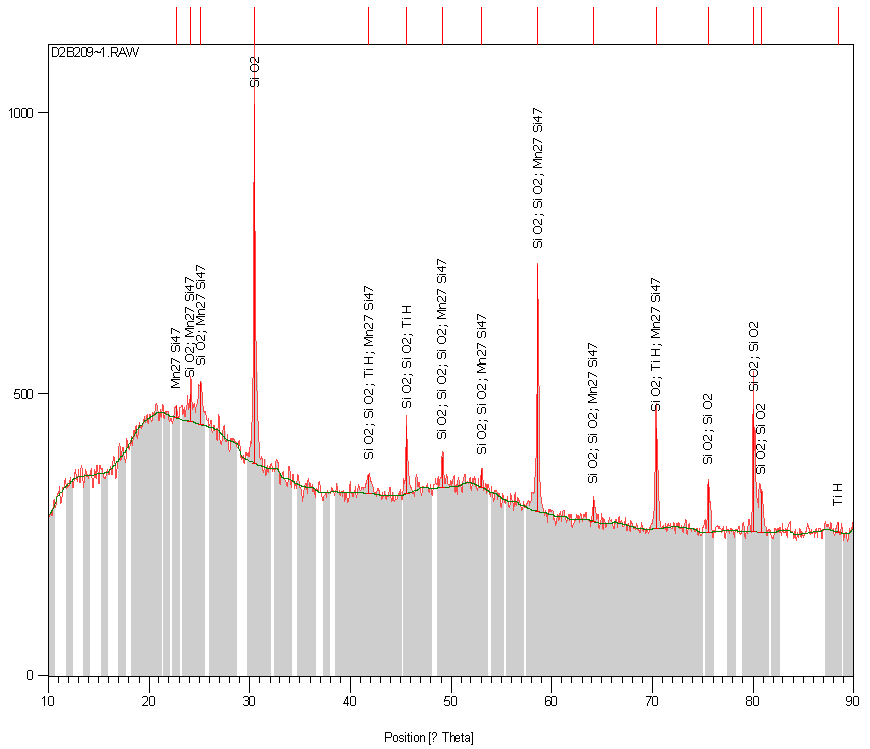 | Figure 2. XRD compositional analysis of ER-5% foundry slag particulate composite |
Table 2. Count Score and Chemical Formulae of the Identified Compounds in the Matrix of ER-5% foundry slag particulate composite 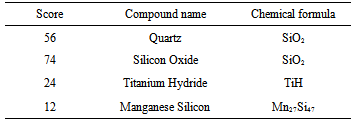 |
| |
|
Table 3. Count scores and formulae of identified phases in the matrix of ER-20%foundry slag particulate composite 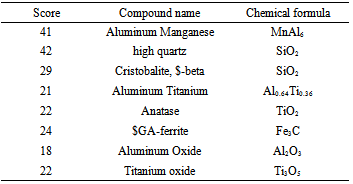 |
| |
|
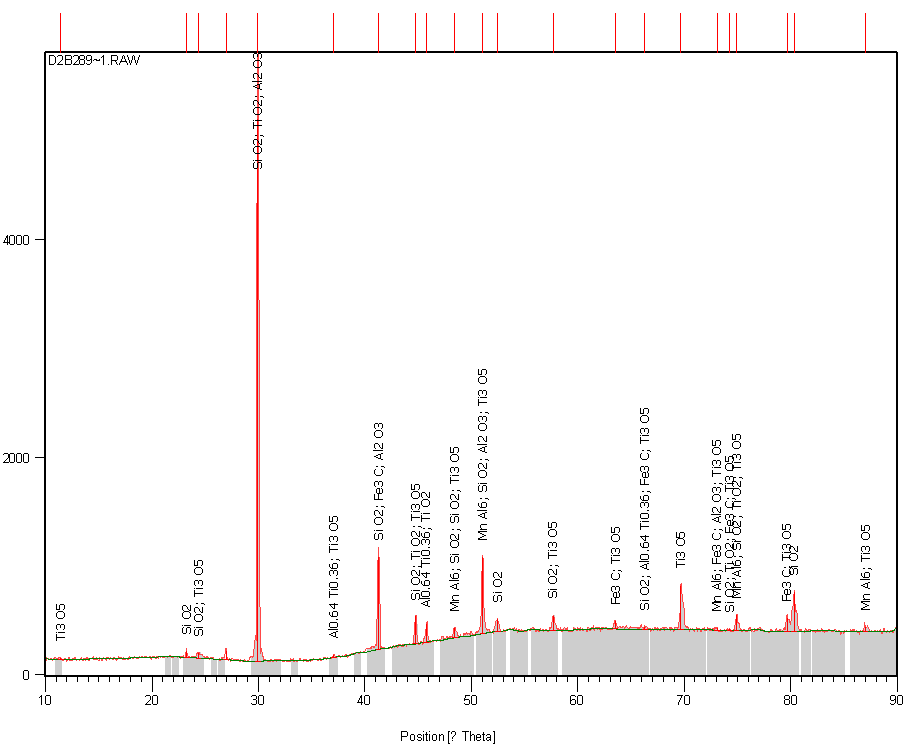 | Figure 3. XRD phase compositional analysis of ER-20% foundry slag particulate composite |
3.2. Microstructural Analysis
Plate 5 represents the SEM micrograph of the epoxy resin (control sample). It can be seen that the microstructure of epoxy resin without the presence of the second phase particles when compared with the microstructure of the developed composites is fairly homogenous. 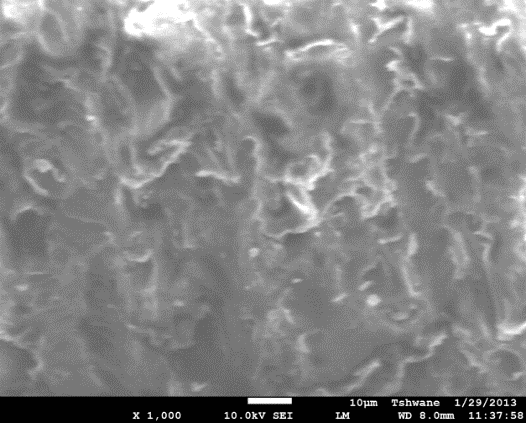 | Plate 5. SEM micrograph of ER (x1000) |
Plate 6 and 7 show the SEM micrographs of ER-5% slag and ER-20%foundry basic slag particulate composites respectively. The matrix of composite contains the new phases such as quarts, silicon oxide and titanium hydride respectively. The silicon oxide is the most dominant phase (see Table 2). The white patches area represented by Q is the titanium hydride. The presence of titanium hydride and silicon oxide in the composite is beneficial in improving the thermal stability of the developed composite due to their high refractory properties.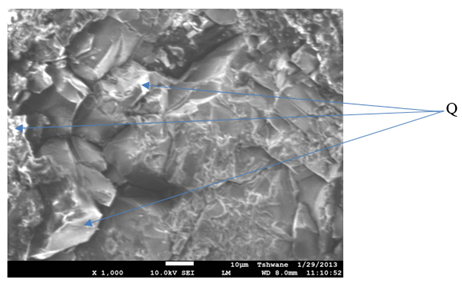 | Plate 6. SEM micrograph of ER-5% foundry basic slag particulate composite (x1000) |
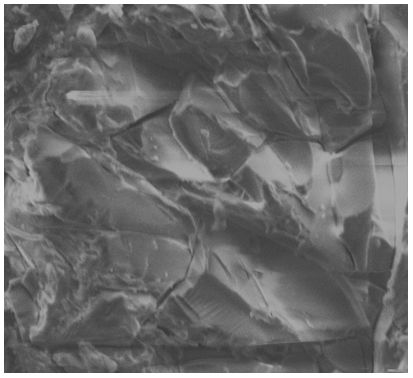 | Plate 7. SEM micrograph of ER-foundry slag particulate composite (x1000) |
3.3. Thermo Gravimetric Analysis
The thermo gravimetric analysis (TGA) of the epoxy resin sample and epoxy resin-foundry slag particulate composites were examined. The graphs of weight loss as a function of temperature and time was automatically plotted (See Figures 4-6).The analysis was carried out in an oxidising environment with a linear temperature ramp. The samples were heated from room temperature (about 30°C) to a maximum temperature of 900°C until the weight of the samples remained constant. The maximum temperature is the temperature attained when the oxidation reaction has been completed (all the polymeric molecules have been burnt off leaving behind non-volatile oxides). The three important numerical pieces of information employed in the examination are weight loss, heating time and oxidation temperature. Oxidation temperature includes onset oxidation temperature (Ton) and maximum oxidation temperature (To). The latter is the temperature at which the oxidation rate is maximum i.e. where the weight loss is maximum and the former corresponds to the temperature when the oxidation of the polymeric material just begins. It is very difficult to determine the Ton accurately due to resistance of material to thermal application. The resistance to thermal application at initial stage is attributed to the presence of particulate foundry slag particulates in the reinforced epoxy resin composites because of the refractoriness of the fillers. For the epoxy resin, degradation of the resin began in the temperature range of 100-150℃ corresponding to time interval between 40 and 45min which is accompanied with breakage of C-C, CO, C-H and OH bonds of the resin while the initial and final decomposition temperatures (IDT and FDT) are 250 and 320°C respectively (see Figure 4).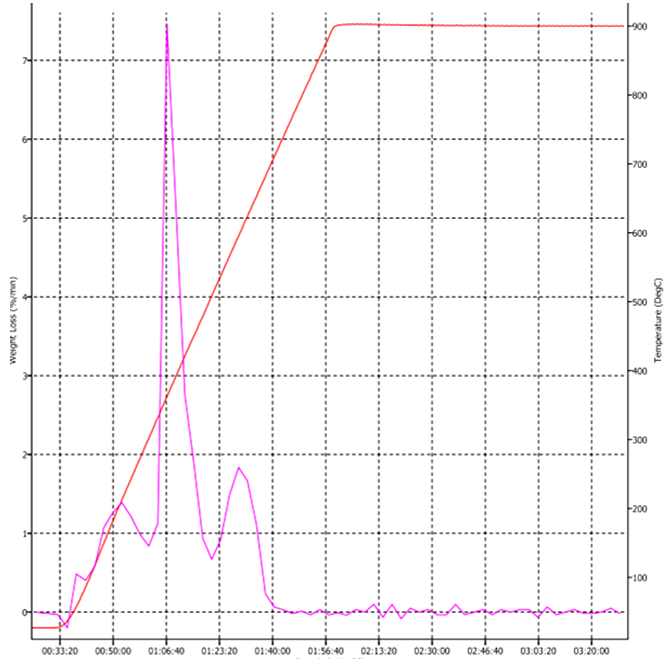 | Figure 4. TGA of the epoxy resin sample (the control) |
Considering Figures 5-6, it was discovered that the developed composite decomposed within the initial temperature ranges from 250-450℃ and final temperature range from 520 to 600℃ respectively.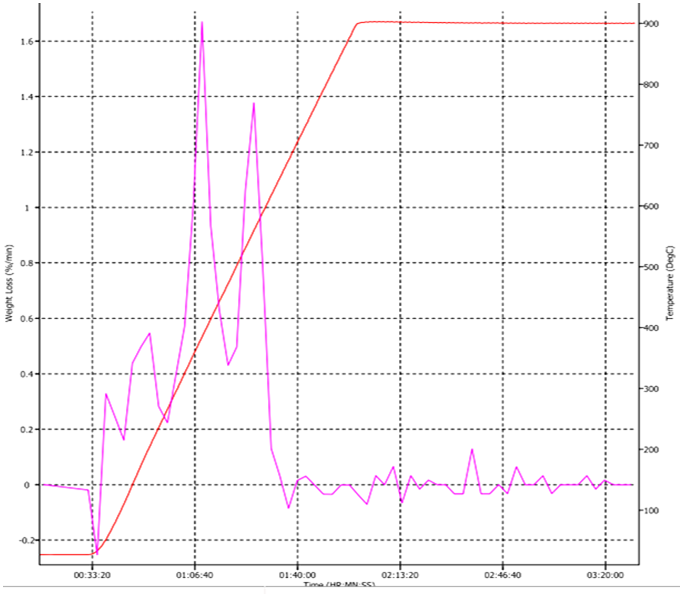 | Figure 5. TGA of the ER-5% foundry slag particulate composite |
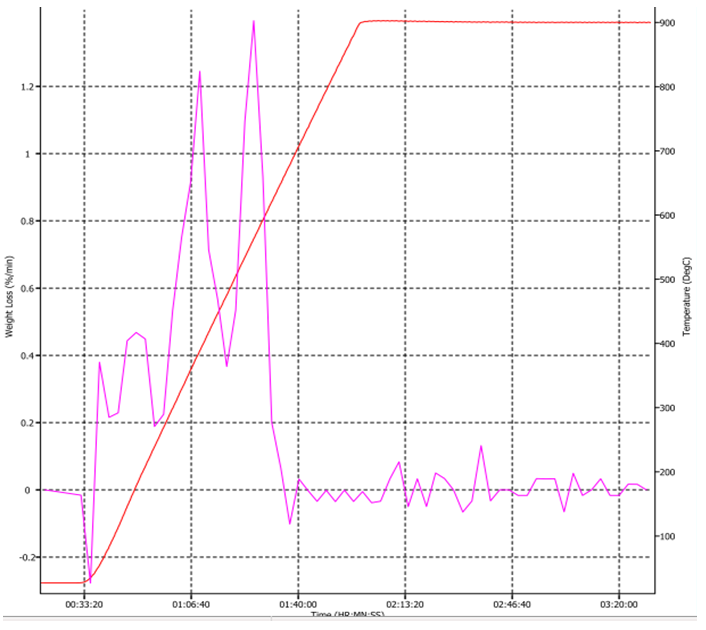 | Figure 6. TGA of the ER-15% foundry slag particulate composite |
The increase in the values of the initial and final decomposition temperatures of the epoxy resin-slag composites is attributed to the presence of the foundry basic slag particulate which is a refractory material in the matrix of the developed composites. The developed composites are able to withstand higher temperature than the epoxy resin control without the foundry slag addition.Also, the variation in the degradation temperature can be attributed to the presence of the second phase (Figures 5-6) particles. Hence, it is not easy to give a maximum service temperature for the developed composites. The more the number of peaks in the curve, the more the presence of second phase particles with higher refractory properties in the matrix.
3.4. Wear Analysis
Figures 7-12 show the relationship between wear coefficient and time of the wear investigation performed on the control sample (epoxy resin) and the developed epoxy resin-foundry basic slag particulate composites under different loads and speed. Generally, it was observed that the wear resistance increased as the time and speed increased at different applied loads from 6 to 16N. The wear coefficient is the tool for measuring wear resistance. The higher it is, the lower is the wear resistance. As the percentage of slag particles incorporated in the epoxy resin increased, there was an increase in the wear resistance of the composite. This may be attributable to the higher packing density of the foundry slag particulate additions. Furthermore, at low applied load of 6N, it was observed that the wear coefficient was very high for the first 120s. Within this time interval, the wear mechanism is predominantly a three body wear. However, the shape of the particles of the third body is irregular which aids the wear. Beyond 120s, the particle shape of the interphase between sample and the emery paper becomes fairly round. This phenomenon tends to reduce friction between the sample and the emery paper. Hence, it significantly lowers the wear coefficient.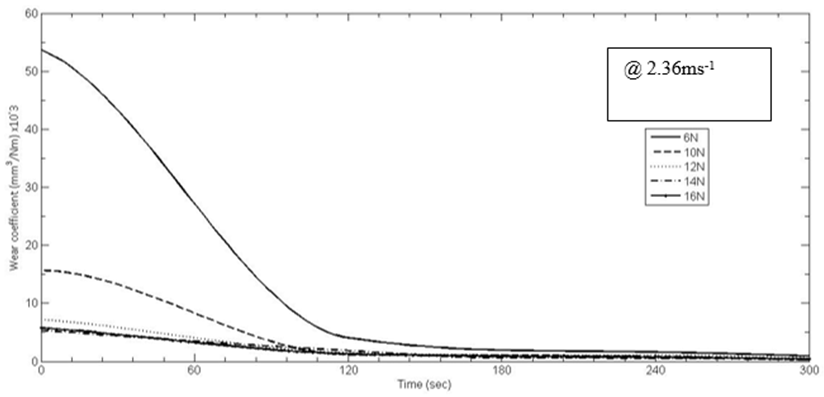 | Figure 7. Wear coefficient of epoxy resin (control sample) with time at 2.36 |
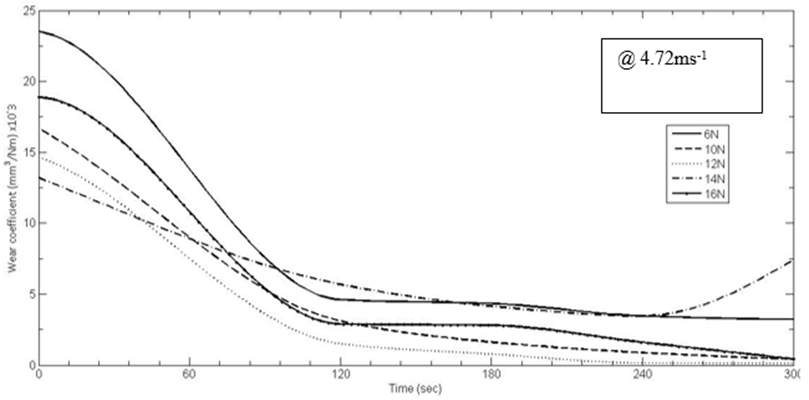 | Figure 8. Wear Coefficient of epoxy resin (control sample) with time at 4.72 |
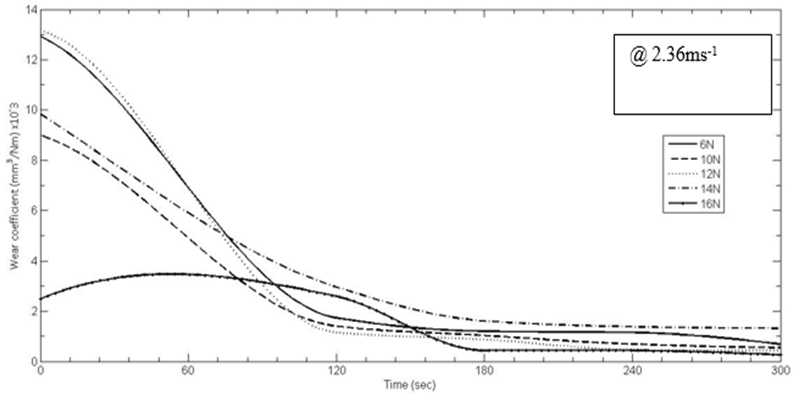 | Figure 9. Wear Coefficient of the ER-5% foundry slag particulate composite with time at 2.36 |
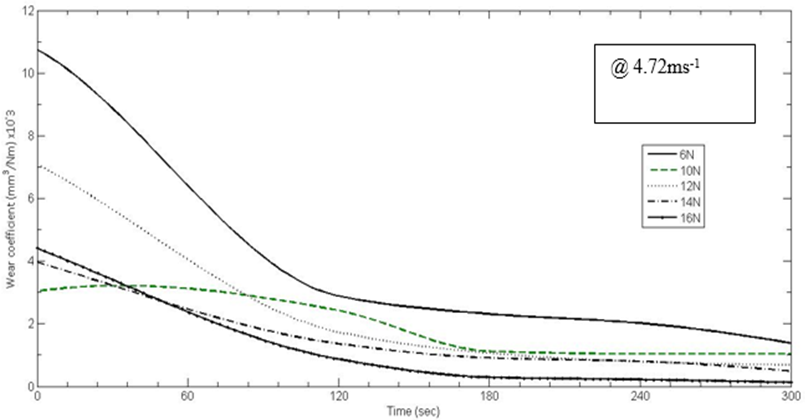 | Figure 10. Wear Coefficient of the ER-5% foundry slag particulate composite with time at 4.72  |
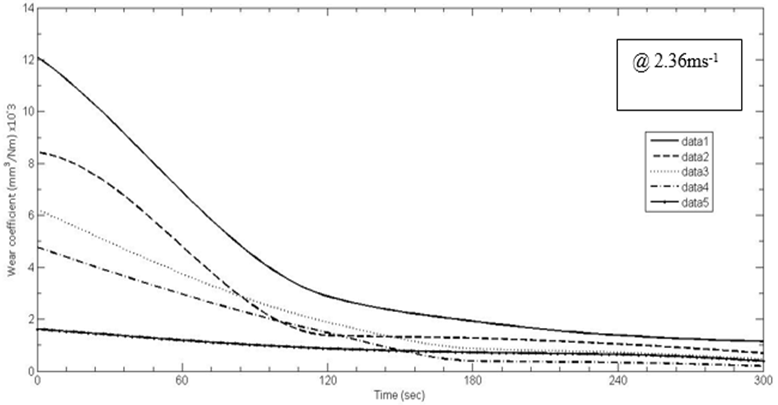 | Figure 11. Wear coefficient of the ER-20% foundry slag particulate composite with time at 2.36 |
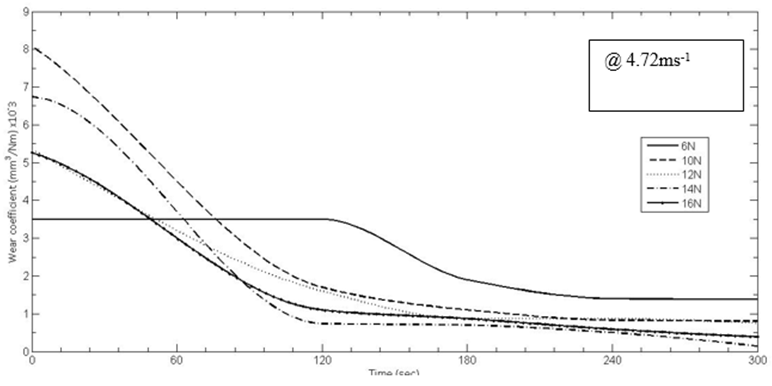 | Figure 12. Wear Coefficient of the ER-20% foundry slag particulate composite with time at 4.72 |
4. Conclusions
From the results and discussion of this work, the following conclusions are drawn:1. Addition of foundry slag particulates to epoxy resin improves the wear resistance of the epoxy resin composites. 2. The developed composites are able to withstand higher temperature than the epoxy resin control without the foundry slag addition. The observed improvement on the thermal stability of the developed composite is due to formation of new phases that are characterised with high refractoriness.3. New phases are formed in the matrix of the developed composite may be attributable to the exothermic reaction of the epoxy resin and constituent elements in the foundry basic slag particulates.4. Speed and load increase led to increase in the volume loss during wear.
ACKNOWLEDGEMENTS
The authors wish to acknowledge the valuable contribution of Raheem I. A. of Physics Department, University of Lagos, Akoka Lagos for his assistance in carrying out some tests.
References
[1] | Acosta J.L., Morales E., Ojeda M.C., Linares A., 1986, Effect of addition of sepiolite on the mechanical properties of glass fiber reinforced polypropylene, Angewandte Makromolekulare Chemie, 138, 103–110. |
[2] | Alok S., Amar P., 2008, Analysis of dry sliding wear behaviour of red mud filled polyethylene composites using taguchi method” Journal of reinforced plastics and composites, 29(24), doi:10.1177/0731684408092453. |
[3] | Alok S. and Amar P., 2010, Analysis of dry sliding wear behavior of red mud filled polyester composites using the taguchi method, Journal of Reinforced Plastics And Composites.:29(19), 2883-2897. |
[4] | Alok S., Mishra S.C., Ananthapadmanabhan P.V., Sreekumar K.P., 2006, Development of ceramic coatings using red mud, a solid waste of alumina plants, Proceedings of the 21st International Conference on Solid Waste Technology and Management. Widener University, Chester, USA, 232-240. |
[5] | Amar P. and Alok S., 2009), “Erosion wear response of flyash-glass fiber-polyster composites a study using taguchi experimental design, Malaysian Polymer Journal. 4(2), 13-28. |
[6] | Acharya S.K., Dikshit V., Mishra P., 2008, Erosive wear behaviour of red mud filled metal matrix composite, Journal of reinforced plastics and composites, 27, 145-152. |
[7] | Gregory S.W., Freudenberg K.D., Bhimaraj P., Schadler L.S., 2003, A study on the friction and wear behavior of PTFE filled with alumina nanoparticles”. Wear, 254, 573–580. |
[8] | Mohini Saxena, Asokan P. Prasad B. K., 2008, Plant fiber-industrial waste reinforced polymer composites as a potential wood substitute material, Journal of Composite Materials, 42(4), 367-384. |
[9] | Prasanta K. P. and Alok S., 2012, “Parametric evaluation of erosion response of epoxy resin filled with blast furnace slag using taguchi technique, International Conference on "Advancements in Polymeric Materials, APM 2012, February 10 -12, 2012, CIPET Ahmedabad. |
[10] | Parvaiz M.R., Mohanthy S., Nayak S.K.,.Mahanwar P.A. Polyetherketone (2010), “Composites reinforced with Fly Ash and Mica”, Journal of Minerals & Materials Characterization & Engineering, 9, 25-41. |
[11] | Pukanszky B., 1995, Particulate filled polypropylene: Structure and properties. In: Karger-Kocsis J (ed) Polypropylene: structure, blends and composites. Chapman & Hall, London. |
[12] | Vijaya Kumar N., Sarcar M. M. M., Inayatulla M.D., 2012, Evaluation of Wear Properties of Flue Dust Reinforced Particulate Polymer Composite, International Journal of Earth Sciences and Engineering, vol. 5, pp. 931-935. |