Priyanka Brahmbhatt, Nitish Kumar, Subrata Pradhan
Institute for Plasma Research, Bhat, Gandhinagar, 382428
Correspondence to: Nitish Kumar, Subrata Pradhan, Institute for Plasma Research, Bhat, Gandhinagar, 382428.
Email: |  |
Copyright © 2014 Scientific & Academic Publishing. All Rights Reserved.
Abstract
The report summarizes the results of the R & D on high temperature ester based insulation. This insulation system is required to possess adequate mechanical strength (inter-laminar shear strength up to > 80 MPa) and break-down strength in excess of 3 KV/mm (when impregnated) at 350℃ and is suitable for radiatively cooled magnets such as in-vessel magnets in a Tokamak. Several candidate insulation resin systems such as Abron 700, RP-46, 700 ELM imide based resins have been characterized and tested. Viscosity of polyimide based resin was found to be very high and subsequently made the vacuum pressure impregnation process difficult. Additionally, Imide resins became brittle after curing at 350 C. Adhesion of imide based resin with glass fiber and metal conductor was also found to be very poor. It was found to be difficult to achieve void free efficient impregnation with imide based resin. Therefore, this resin could not be recommended due to its high viscosity. Ester based resin were found to possess better dielectric and mechanically properties at high temperature. Void free insulation and complete fill during the vacuum pressure impregnation process have been achieved with an ester based resin at IPR. Mechanical testing of the impregnated conductor with this ester based resin has been carried out to determine the turn to turn shear strength (12.5 MPa) and inter-laminar shear strength (90 MPa). Decomposition temperature of the resin, glass transition temperature and cure range of the insulation have been identified by carrying out DSC scans, DMA scans and TGA scans. Repeated TGA scans showed negligible (<3%) weight loss. This resin insulation system will be subsequently applied in Steady State Superconducting Tokamak (SST-1) in-vessel magnets.
Keywords:
Keywords Ester, Shear strength, DSC, DMA, TGA
Cite this paper: Priyanka Brahmbhatt, Nitish Kumar, Subrata Pradhan, R & D on High Temperature Ester Based Insulation, International Journal of Composite Materials, Vol. 4 No. 2, 2014, pp. 83-92. doi: 10.5923/j.cmaterials.20140402.07.
1. Introduction
Institute for Plasma Research (IPR) is attempting at developing insulation systems appropriate for edge localized mode (ELM) coils in Tokamaks that are radiation cooled by plasma such as the proposed ones ELM coils as the Joint European Torus (JET) [1]. These insulation systems are required to be operational a nominal/working temperature of 350℃ [1]. Additionally, these insulation systems when vacuum pressure impregnated in the magnet winding packs are required to be qualified for their mechanical strength as well as breakdown strength. Several candidates’ insulations have considered for such applications. An ester based insulation system seems to be the most promising. Cyanate esters can provide attractive physical, electrical, thermal and processing properties. Cure cycle for such as ester based resin has been proposed for a high temperature that is closer to the DSC exotherm. In order to increase the glass transition temperature, the object is required to be post cured. One potential effect to take in considering during cure of CE is the relatively high exothermic heat of reaction. The CE monomers and prepolymers exhibit a very low total volatile content upon curing. Ester based resin produces a maximum volatile content of 0.5%. This feature is important in vacuum assisted processing. In this report, the thermal characterization including the curing behavior and thermal stability of such an ester based insulation system has been investigated by differential scanning calorimetry (DSC). Thermogravimetric analysis (TGA) had been carried out up to 800℃ at different heating rates towards investigating the thermal decomposition temperature of this cured resin. The cured resin was exposed to multiple thermal cycles in TGA up to 400℃ and the changes in the percentage weight loss of the sample was found to be negligible (< 3 %). The curing activation energy as per Kissinger method employing a DSC is found to be 67.1355 KJ/mol. The same is to be 72.31 KJ/mol by Flynn –WALL Ozawa method. The glass transition temperature of cured resin determined by dynamic mechanical analysis was found to be 393℃. Flexural strength, inter-laminar shear strength of the fibre glass impregnated with resin has also been studied. Prototype samples were used to investigate the mechanical properties of insulation.
1.1. Chemical Structures
The resin for high temperature application must possess high thermal decomposition temperature (Td), high glass transition temperature (Tg) and mechanical strength at high temperatures. The resin should have low viscosity so that it can be easily processed during vacuum pressure impregnation of coils. Polyimide based resins such as AFR-PE-4, ABRON 700 and RP-46 have high glass transition temperature and most thermally stable resins. Chemical structures of AFR-PE-4 and ABRON 700 have been shown in fig.1.AFR-700B polyimide resin constitutes of 2,2’-bis (3,4-dicarboxyphenyl) hexaflurorpropane dianhydride (6FDA) and 1,4-diaminobenzene (p-PDA), monoalkyl ester of 5-norbornene), 2,3-dicarboxylic acid (NE) while AFR-PE-4 constituted of 4-phenylethylphthalic anhydride (PEPA),2,2’-bis(3,4-dicarboxyphenyl)-hexafluoropropane dianhydride (6FDA) and 1,4-diaminobenzene (p-PDA). The introduction of hexafluoro dianhydride (6F) group into the structure enhance the solubility and processibility of the polyimides. Polyimide based resins have poor fibre matrix interfacial adhesion and poor wetting during pre-pregging and composite processing. Polyimide based resins make the matrix more brittle due to higher cross linking and shrinking and also matrix cracking occurs during these processes. Presence of cracks and voids had been observed in the resin rich areas upon closer examination. Delamination of the laminates had also been observed. Imide based resin has very high viscosity (8000 Cps at 260℃) which makes the resin impregnation very difficult. Therefore, polyimide alternate; that is Phenol Navolac cyanate ester based resin has to be investigated systematically. There are different types of cyanate ester resin namely Bisphenol M, Dicyclopentadienyl bis-phenol, Bis-phenol A, Tetra methyl bisphenol F, Bisphenol E, Hexafluoro bisphenol A, Bisphenol C and Phenol Navolac cyanate ester from amongst which Phenol Navolac is the most thermally stable ester based resin. Polycyanurates formation occurs when three cyanate ester monomers containing reactive functional group (-O-C≡N) undergo thermally initiated cyclomerization reaction to form triazine ring.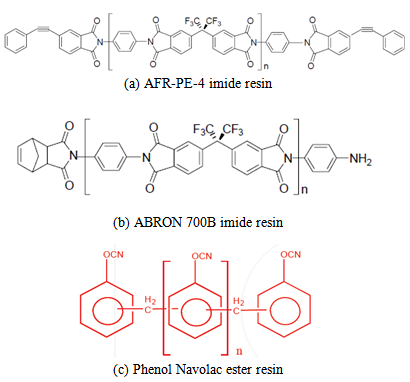 | Figure 1. Chemical structures of imide and ester based resin |
2. Chemical Characterization
2.1. Dynamic Mechanical Analyzer
A DMA (Q 800, TA Instrument) was used with a single cantilever probe. Samples were heated from 30 to 400℃ in air while applying uniform deformation at 1 Hz frequency. As the material is heated the storage modulus (E’) decreased step-wise by several orders of magnitude. This large change indicated that the glass transition can be measured with good sensitivity. The loss modulus (E”) is usually associated with the viscosity or toughness of the material. The ratio of the loss to the storage modulus is the Tan delta (δ) and is often called damping. It is a measure of the energy dissipation of a material. At fixed frequency, the value of Tan delta (δ) reaches maximum at glass transition temperature, thus, the value of Tg is about 393℃ as shown in Fig.2. Fig.2 shows two relaxation peaks. First relaxation peak (210℃) is considered to be associated with the relaxation of small groups. The Tg of the resin was measured from the peak of the tangent tanδ curve [2]. The glass transition temperature from these peaks was determined as a maximum value of tanδ [3]. DMA scan of ABRON and RP-46 imide based resins have been shown in fig.3 and 4. The glass transition temperature ABRON and RP-46 is found to be 391℃ and 376 ℃ respectively.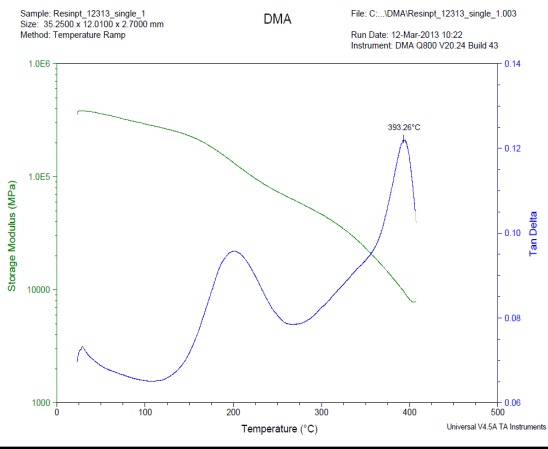 | Figure 2. DMA scan of composite impregnated with ester based resin |
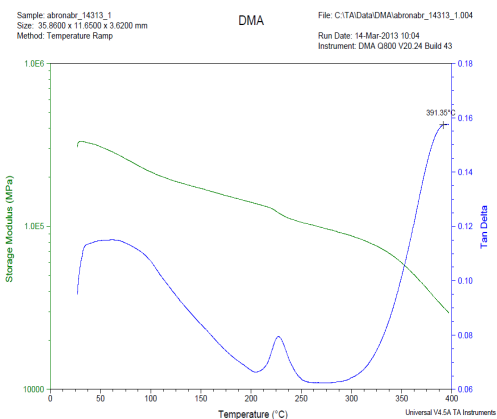 | Figure 3. DMA scan of composite impregnated with ABRON imide based resin |
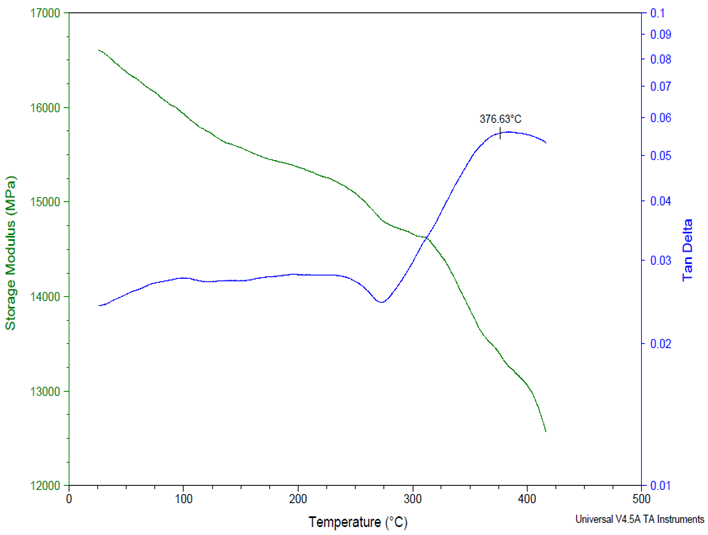 | Figure 4. DMA scan of composite impregnated with RP-46 imide based resin |
2.2. Differential Scanning Calorimeter
A perkin Elmer Pyris differential scanning calorimetry was used to investigate the curing behavior of ester based resin in nitrogen atmosphere. Resin sample was subjected to DSC scans at heating rates of 1, 2,3 5,10 and 30℃ min-1 respectively, the test specimen was heated from 50℃ to 350℃ as shown in Fig.5 & 6. The curing reaction kinetics parameters can be evaluated with a multiple heating rates method by determining the exothermic peak temperature at several heating rates. In practice, two convient multiple heating rate methods are generally used. One is the maximum reaction rate method proposed by Kissinger which is based on the fact that the exothermic peak temperature (Tp) varies with the heating rates [4]. The other is the iso-conversion method proposed by Flynn Wall Ozawa which is based on the fact that iso-conversion can be reached at different temperatures with various heating rates. Kissinger and Ozawa plot has been shown in fig 8 and 9 for determination of kinetic energy. The curing activation energy as per Kissinger method was investigated to be 67.1355 KJ/mol and estimated by Flynn –WALL Ozawa method to be 72.31 KJ/mol. DSC scan ester based resin was carried out at 1℃/min as shown in fig.7 and the peak temperature is observed to be 200℃. Therefore, the curing of the insulation should be carried out at 200℃. 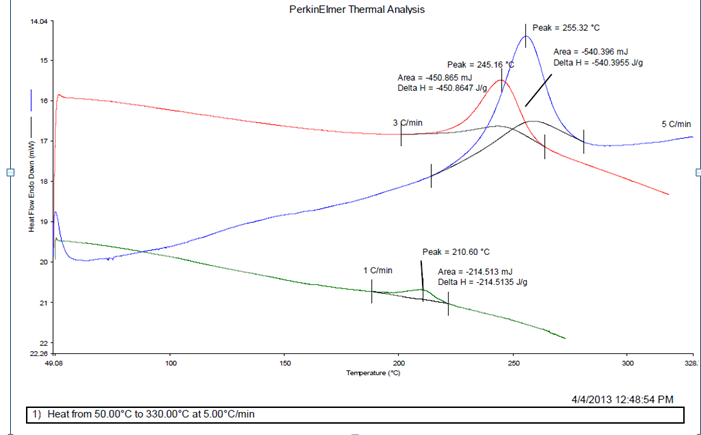 | Figure 5. DSC of ester based resin carried out at 1, 2 and 3℃/min |
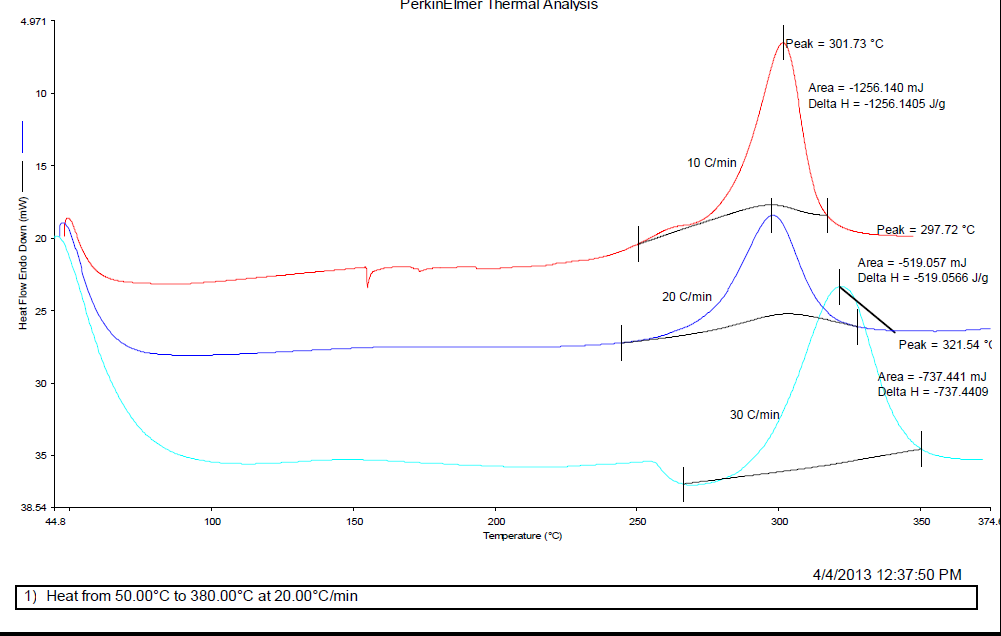 | Figure 6. DSC of ester based resin carried out at 10, 20 and 30℃/min |
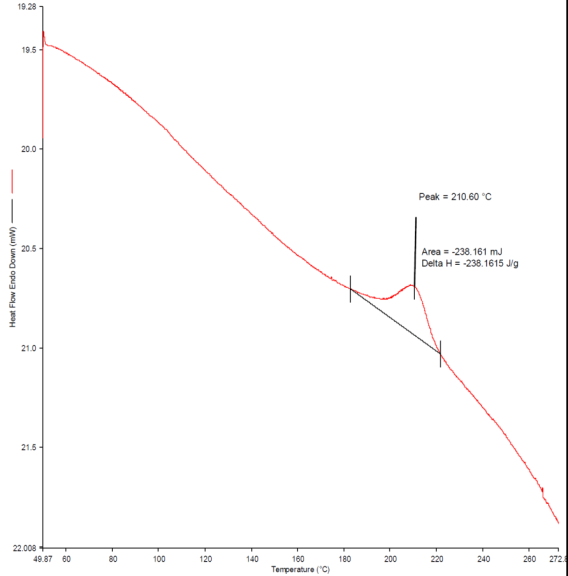 | Figure 7. DSC scan of ester based resin at 1 ℃/min |
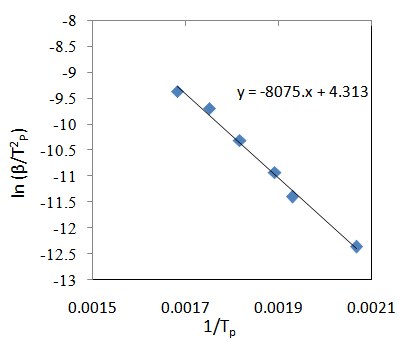 | Figure 8. Kissinger Plot for ester resin |
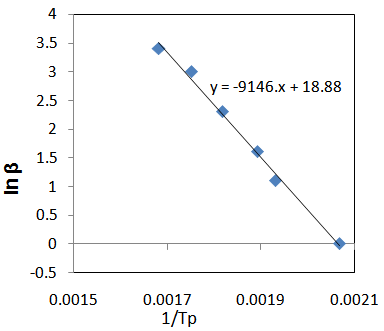 | Figure 9. Ozawa Plot for ester resin |
1. Kissinger’s Method of Analysis of Non-isothermal Transformation [5, 6]:Using the highest rate of transformation at maximum peak approximately interpreted in the equation respectively, | (1) |
Where, Tp the peak temperature, β = dT/dt heating rate,2. Ozawa’s Method of Analysis of Non-isothermal Transformation | (2) |
Activation energy for crystallized fraction can be determined by plotting lnβ against 1/Tc.
2.3. Differential Scanning Calorimeter
The thermal decomposition of the cured system was carried out at heating rate of 10℃/min under N2 atm (20 cm3 / min). The cured sample was prepared by pouring the uniform viscous mixture into an aluminium pan and heating in an oven using programme schedule at 100℃ 1 hr, 200℃/4 hr, and 260℃/1 hr. The sample was cut into small pieces with 30 mg for tests and put into a ceramic cell, placed on detector places and the furnace then heated upto 800℃ at a heating rate of 10℃/min. TGA scan of the cured sample provides its thermal stability and thermal degradation behavior under nitrogen atm. Thermal stability can be determined in terms of initial decomposition temperature and temperature at maximum weight loss takes place [7]. The thermal decomposition temperature of the cured sample was found to be 420℃ as shown in Fig. 10. TGA scans were carried out repeatedly on the same cured sample, however the weight loss was found to be less than 2 % as shown in Fig.11. This ester based resin can be recommended for high temperature applications since the weight loss is negligible after multiple thermal cycles.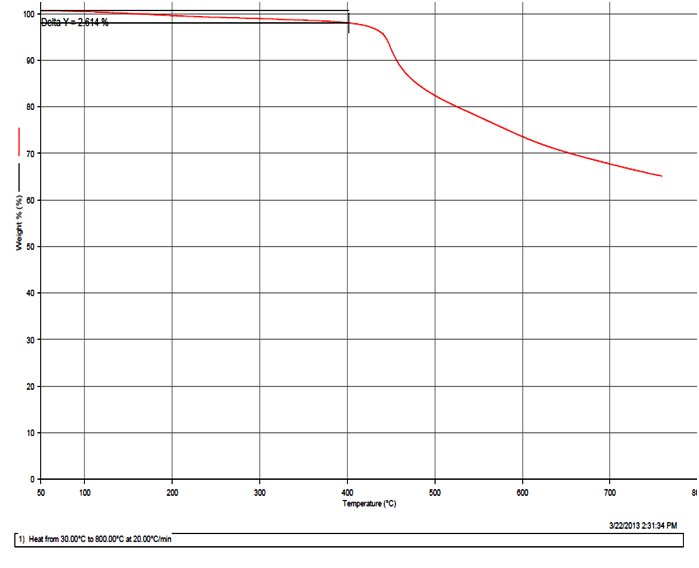 | Figure 10. TGA scan of cured resin up to 800℃ |
 | Figure 11. TGA scans up to 400 C on the same cured sample |
3. Mechanical Characterization
1. Shear testing: Specimens were tested using an in house punch shear assembly. The test set up is similar to ASTM D732-85 but with smaller dimension to achieve failure within a desired load frame specification and predicted strength. Shear strength of the insulation of the winding pack is required to be measured at room temperature as well as at 350 C operating temperature. Samples cut from arrays measured 2 cm were tested for shear strength. A plunger that is slightly smaller than a CuCrZr conductor was used to push against a single turn of copper while the other conductors were supported against the stand as shown in Fig.12. Load was applied to plunger until the copper turn would fail in shear [8]. Shear measurement method is used to determine the strength of CuCrZr ester based insulation. Shear failure in the ester based array was measured to be 11.756 MPa. Shear tests were also performed at 350 c as shown in Fig.14. Shear strength of the aged sample at 350 C was found to be 10 MPa. Central CuCrZr conductor with inter turn insulation slid out of its array has been shown in Fig.13.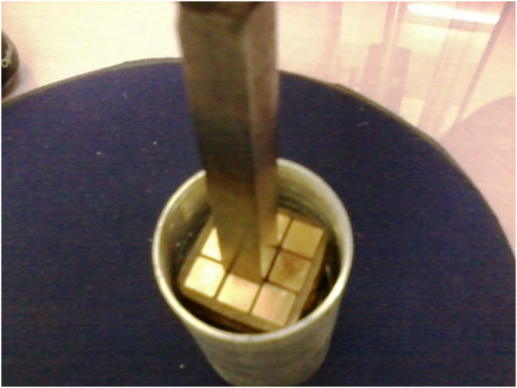 | Figure 12. Test set up for shear strength measurement |
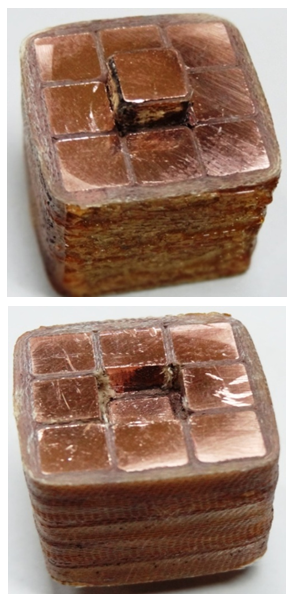 | Figure 13. Shear test sample as copper sliding out of array |
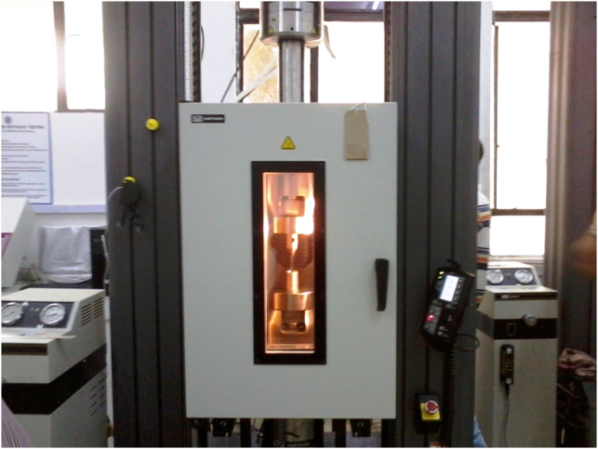 | Figure 14. Shear strength measurement of array at 350 C |
2. Inter-laminar shear test: Inter-laminar shear strength testing was conducted on an Insron using three point bending according to ASTM D-2344 as shown in Fig.11 [9, 10]. The test was performed as a testing speed of 1 mm/min. The dimensions of the samples were kept 20 X 6 X 2 mm3. The inter-laminar shear strength of the composite impregnated with ester resin at room temperature was evaluated to be 89 MPa. Both interface fracture energy and inter-laminar shear strength of composite decrease under the effect of temperature. Inter-laminar shear strength of the laminate after aging for 24 hrs at 350 C was found to be 39.07 MPa.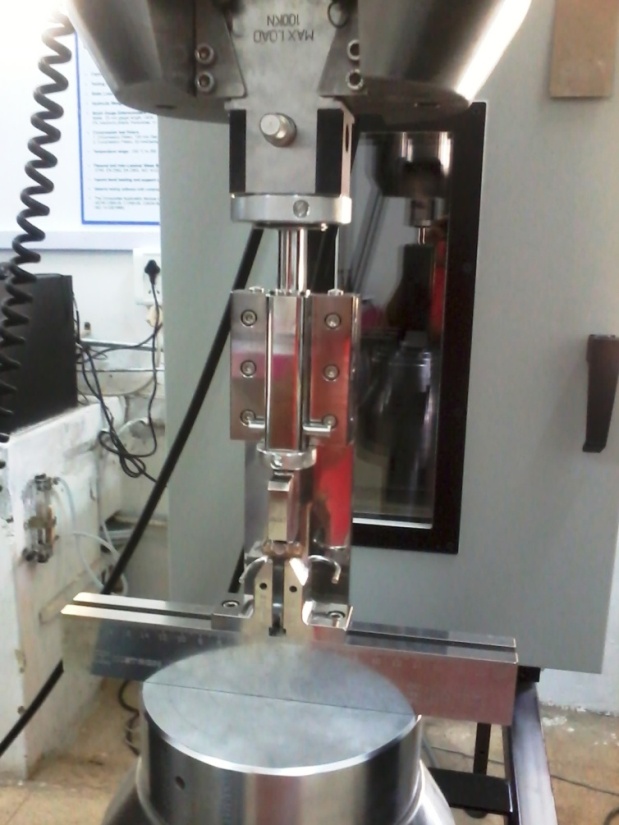 | Figure 15. Inter-laminar shear strength measurement as per ASTM D-2344 |
3. Flexural strength Test: A long length of array ( 4 X 2) was prepared to carry out a three point bend flexure test to failure in accordance with ASTM standard D-2344 as shown in Fig.16 [8]. As per standard, the flexural strength of the array was measured to be 8 MPa and 8.35 MPa after carrying out aging at 350℃. 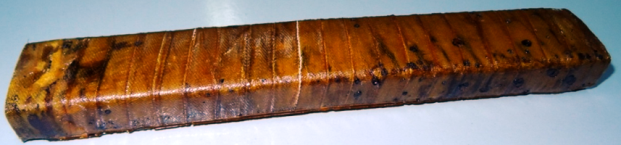 | Figure 16. Array tested for Flexural strength measurement |
4. Compression testing: Thick sample measured 20 X 20 x 20 mm were used for compression testing. A compression test determines behavior of materials under crushing loads as per ASTM D695 [8]. Compression modulus is measured to be 3.13 GPa and compressive strength measured to be 312.98 MPa. Compression strength set up has been shown in Fig.17.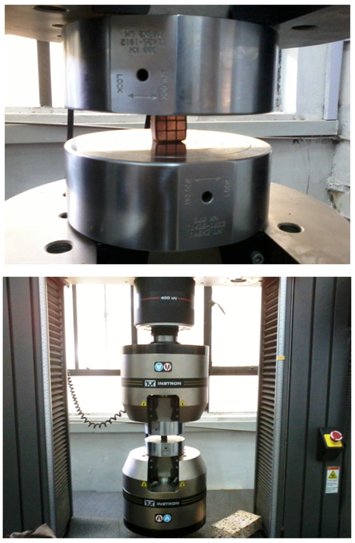 | Figure 17. Compression test set up |
5. Ultimate tensile strengthTensile test confirmed to ASTM D638 is used to measure the force required to break a specimen using Universal Tester Extensometer (Instron). Tensile tests measure the force required to break a specimen and the extent to which the specimen stretches or elongates to that breaking point. Tensile tests produce a stress-strain diagram, which is used to determine tensile modulus. Tensile strength of the composite was found to 300 MPa at room temperature.
6. Dielectric Evaluation : Insulation was electrically tested to a 1 KV, 2 KV, 2.5 KV, 3.5 KV, 4 KV, 4.5 KV and 5 KV voltage standoff with a leakage current 0.08 nA. Break down strength of the insulation was found to be 15 KV/mm. Test set up has been shown in Fig.18.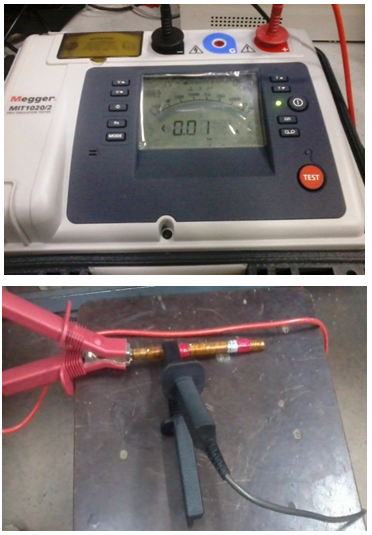 | Figure 18. Dielectric characterization of insulation using Megger |
4. Conclusions
Cyanate ester resins present outstanding thermal properties with glass transition temperature 400℃ that has been identified using DMA. Cyanate ester is better material choice than polyimide when high temperature application is the key importance. Thermal decomposition mechanism for polycyanurates begins at a temperature between 400-450℃ with negligible mass loss. Mechanical properties of the resin have been determined by carrying out impregnation of glass fiber with ester based insulation system. These samples were aged at 350℃ for longer hours. The mechanical properties do not get deteriorated even after carrying out aging at higher temperature (Table 1).• Good mechanical properties• Excellent solvent and radiation resistance• Outstanding dielectric properties• Easy processing and stable viscosity• Good adhesion properties.Table 1. Technical Comparative sheet of Polyimide based resin and Ester based Resin [IPR] 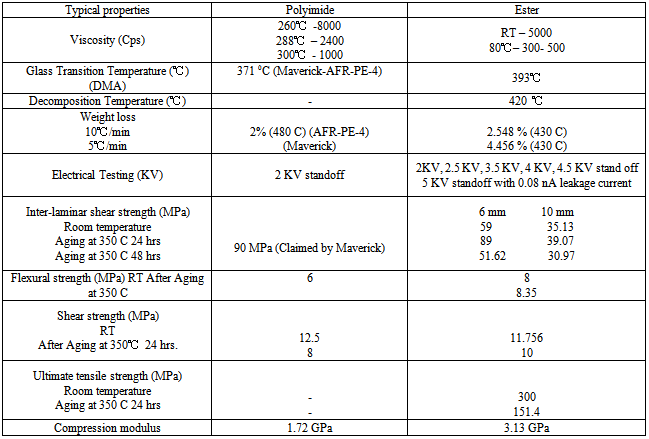 |
| |
|
ACKNOWLEDGEMENTS
The authors would like to thank Mr.Azadsinh Makwana for his support in carrying out breakdown strength measurement of the insulation.
References
[1] | FZJ. Jullich, JET ELM Control Coil Feasibility study, 2010 |
[2] | Sie Chin Tjong, Shi-Ai Xu, Robert Kwok-Yiu Li, Yiu-Wing Mai, “Mechanical behavior and fracture toughness evaluation of maleic anhydride compatibilized short short glass fiber/SEBS/polypropylene hybrid composites”, Composite Science and Technology, vol62, issue 62, May 2002, 831-840. |
[3] | Fan-Long Jin, Soo-Jin Park, “Thermal stability of Trifunctional Epoxy resins Modified with Nanosized Calcium Caurbonate”, Bull Korean Chem. Soc. 2009, vol.30 No.2. |
[4] | S.Pradhan, P.Brahmbhatt et al., Influence of manganese acetylacetonate on the cure kinetics parameters of Cyanate ester-Epoxy blend systems in Fusion Relevant Magnets Winding Packs. |
[5] | M.Satheesh Chandran, M.Krishna, Sheshappa Rai et al. “Cure Kinetics and Activation energy studies of modified Bismalemide resins”, ISRN Polymer Science vol.2012, article ID 309861. |
[6] | Chin-Lung Chiang, Ri-Chang Chang, Yie-Chan Chinu, “Thermal stability and degradation kinetics of novel organic/inorganic epoxy hybrid containing nitrogen/silicon/ phosphorous by sol-gel method”, Thermochimica Acta, 453, 2007, 97-104. |
[7] | Nishar Hameed, P.A. Sreekumar, Bejoy Francis et al. “Morphology dynamic mechanical and thermal studies on poly(styrene-co-acrylontrile) modified epoxy resin/glass fibre composites, composites part A: Applied Science and Manufacturing, vol. 38, issue 12, 2007, 2422-2432. |
[8] | I.J Zatz, G. H. Neilson, S.Juczynski et al., R & D of Polyimide Insulated JET ELM Control Coils for Operation at 350 C. |
[9] | Masaya Miura, “Characterization of Cryogenic inter-laminar shear strength of composite insulation systems for superconducting magnets in fusion reactors”, Asia Pacific Conference for Materials and Mechanics, 2009, Japan, Nov. 13-16. |
[10] | R.Prokopec, K.Humer, H. Fillunger, R.K. Maix and H.W. Weber, “Property change of Cyanate Ester/Epoxy insulation systems caused by an ITER like Double Impregnation and by Reactor Irradiation, Advances in Cryogenic Engineering Transactions of the Cryogenic Engineering Materials conference-ICMC, vol.56. |