GuruRaja M. N1, A. N. HariRao2
1Research scholar R&D Centre, S.J College of Engineering, Mysore, Karnataka
2Professor, Department of Mechanical Engineering, S.J College of Engineering, Mysore, Karnataka
Correspondence to: GuruRaja M. N, Research scholar R&D Centre, S.J College of Engineering, Mysore, Karnataka.
Email: |  |
Copyright © 2012 Scientific & Academic Publishing. All Rights Reserved.
Abstract
This paper outlines the method and the results of the experimental investigation of interlaminar shear strength of carbon/glass angle ply hybrid glass composites, with the aim of determining the influence that the structure, a reinforcement type and a sort of resin exert upon the interlaminar strength. Hybrid composites are considered materials of great potential for engineering applications. One advantage of hybrid composite materials for the designer is that the properties of a composite can be controlled to a considerable extent by the choice of fibers and matrix and by adjusting the orientation of the fiber. The scope for this tailoring of the properties of the material is much greater, however, when different kinds of fiber orientations are incorporated in the same resin matrix. Two orientations viz 0/90 (cross ply), ±45(angle ply) were considered for studies. Mechanical properties such as interlaminar strength, interlaminar stiffness, & load of the hybrid composites were determined as per ASTM standards. Vacuum bagging technique was adopted for the fabrication of hybrid specimens. It was observed that orientation at 0/90 showed significant increase in ILSS properties as compared to other orientation.
Keywords:
Hybrid Composite, Interlaminar Shear Strength, Angle Ply, Vacuum Bagging, Orientation
Cite this paper: GuruRaja M. N, A. N. HariRao, Interlaminar Shear Strength of Cross Ply & Angle Ply Carbon/Glass Hybrid Composites, International Journal of Composite Materials, Vol. 3 No. 6, 2013, pp. 141-144. doi: 10.5923/j.cmaterials.20130306.01.
1. Introduction
Hybrid composites are manufactured by combining two or more fibers in a single matrix. Hybridization in order to use to tailor the material to exact needs under design[1]. Epoxy resin is used in this hybrid composite because it provides a unique balance of chemical and mechanical properties combined with extreme processing versatility. In all cases, thermoset resins may be tailored to some degree to satisfy particular requirements[2]. Epoxies are one type of thermosetting polymer that are more expensive and have better mechanical properties and resistant to moisture than the polyester and vinyl resin[3]. At present epoxy resins are widely used in various engineering applications, such as electrical industries, and commercial and military aircrafts industries. In order to improve their processing and product performances and to reduce cost, various fillers are introduced into the resins during processing[4]. Hybrid laminated composite are prepared by stacking sheets of Glass/carbon fibers to required orientation to form angle ply laminates. An individual structural glass fibre is both stiff in tensile and compression[5]. Interlaminar shear strength (ILSS) of interply woven fabric hybrid composites under the influence of a fluctuating humid environment carried out by S. Mula, B. C. Ray e tal[6]. They found that the ILSS shows a gradual degradation over a period of time and also ILSS scales inversely with crosshead velocities. Investigated the possibility of using the static ILSS data obtained by testing simple unidirectional laminates to infer the properties of ILS coupon by P. Feraboli, etal[7]. They found from the detailed shear stress contour it was possible to discover the point of maximum stress in a region within one thickness away from the supporting roller for all three laminates. Experiment carried out on interlaminar shear behavior of typical polymer matrix composites under high strain rate shear loading by N.K. Naik etal[8]. It is observed that the interlaminar shear strength increases with increasing shear strain rate within the range of shear strain rate considered. The classical laminate theory and the higher-order shear deformation theory, are used to predict the interlaminar shear stresses in the cross-ply laminate by C.Y. Lee e tal[9]. They found that the approach using the higher-order shear deformation theory has improved accuracy for the analysis of thick symmetric laminate over the approach using the classical laminate theory. Investigation on Interlaminar shear strength (ILSS) of traditional glass fiber reinforced epoxy composites multi-walled carbon nanotube (MWNT)–epoxy carried by ZhihangFan e tal[10]. They found results show the introduction of MWNT into the composite increased the ILSS by up to 33%. The preferential orientation of the MWNTs in the thickness direction was found to contribute to the increase in the interlaminar shear properties. Experimental and finite element analysis of carbon epoxy and carbon epoxy carbon nanotube composites to estimate interlaminar shear strength by P. Rama Lakshmi e tal[11]. They found that inferred experiment results are in good agreement with results generated by ANSYS. The superiority of the presence of carbon nanotube in the composite is proved from experimental and finite element technique from the estimated fracture parameters. An approximate method is developed to investigate the interlaminar stresses near the free edges of beam-type composite laminate structures subjected to out-of-plane shear/bending by Taehyoun Kim et al [12]. They found that interlaminar stresses under the shear/bending, particularly those for angle-ply laminates, may exhibit substantially different characteristics than under uniaxial loading or under pure bending. Analytical solution carried out to determine the interlaminar stresses of general cross-ply laminates with piezoelectric layers as actuators under transverse mechanical loads by M. Izadi etal[13]. They found numerical results show that this approach can generally predict the behavior of interlaminar stresses. Also, they clearly indicate the singular behavior of interlaminar normal and shear stresses in the boundary region near the edges of the laminate. Interlaminar shear strength as well as shear stress values corresponding to the onset of the fibre/matrix-debonding were determined by Stephan Hinz etal[14]. They found cross-ply lay-up within the laminate has been interlaminar shear loaded, damage and failure could only be found within the transverse plies. However, the present study focuses on the evaluation of interlaminar shear strength properties of Cross ply & angle ply glass/carbon hybrid laminate.
2. Experimental Methods
2.1. Materials
Woven fabric Carbon fibres (T-300 PAN based, High Strength), E-glass (FGP, RP-10) of density 360 GSM and epoxy adhesive (Bisphenol A type, Ciba-Geigy LY 556 araldite, hardener HY- 951) were used to fabricate composite laminates.
2.2. Preparation of Specimens
E-glass fibre grade 360GSM& diameter of glass fibre is 0.25 mm diameter is tailored with carbon fibre 0.25 mm diameter to prepare bi-woven clothes. The thickness of the cloth is 0.3mm which are stacked layer by layer about 10 layers to attain required thickness. During preparation of laminated required orientation of fibre is carried out for cross ply (00/900) and angle ply (±450) composites. For (00/900) glass fibre placed at 900 carbon fibre at 00, for angle ply(±450) glass is placed in + 450& carbon at-450. Epoxy resins also known as polyepoxides, grade LY556 HY951 resin used. It consists of monomers or short chain polymers with epoxide group at its end. Which contain epoxide groups co-reactants are often referred to as hardeners or curatives, and the cross-linking reaction is commonly referred to as curing. Laminates are prepared by hand-layup process using vacuum bag technique. After preparation of laminates it is cured in a reheating furnace to 1000C up to 2hrs. After curing specimens are fabricated as per the ASTM standard as shown in fig 1.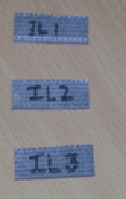 | Figure 1. Carbon/Glass ILSS specimens |
2.3. ILSS Testing of Hybrid Laminates
Interlaminar shear strength analysis was carried out at room temperature through three-point bend testing as specified in ASTM D 2344, using BIS Model Bi-10-101of capacity 15 KN universal testing machine as shown in Fig 3. The speed of the crosshead was 2 mm/min. Fig 1 shows the test specimens & Fig 3 shows the failure of specimen under shear loading. Three composites specimens were tested & for each sample interlaminar shear strength was calculated using equation (1) 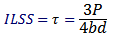 | (1) |
where,
= interlaminar shear strength, MPa, P = Max load at a given point on the Load deflection curve, N; b = width of specimen in mm, d =depth of specimen in mm, d = thickness of the samples (mm) z 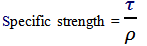 | (2) |
where,
= stiffness strength in GPa,
= mass density of specimen (gm/mm3)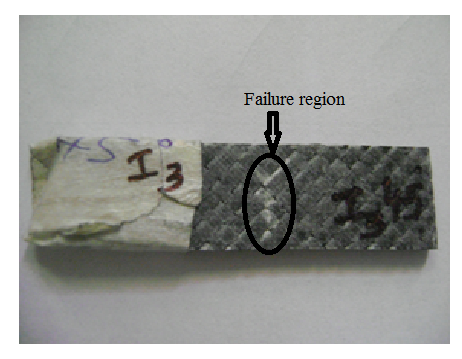 | Figure 2. Carbon/Glass failure specimen |
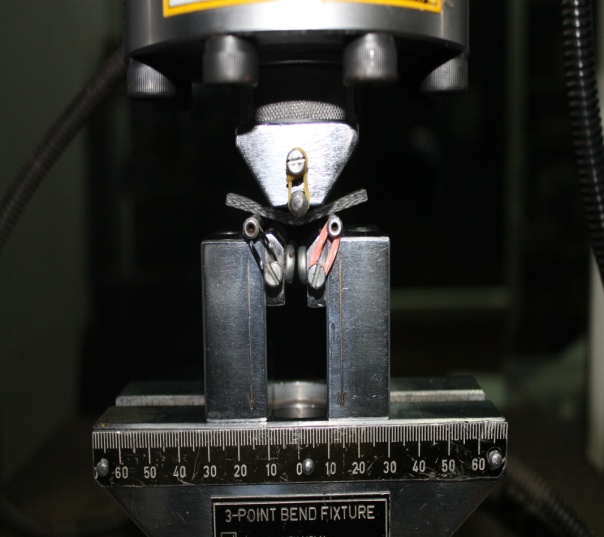 | Figure 3. ILSS testing of hybrid laminates |
3. Results & Discussions
In this paper, inter laminar shear strength estimated using experimental technique and is presented. From table 1 and table 2 it is evident that the shear strength for Carbon/Glass hybrid laminate with [0/90] orientation is 11.6 MPa as a while for [0/45] fiber orientation it is 8.55 MPa. Figures 4 and 5 shows the variation of displacement under different loading rate. Due to variation in load there is variation in deflection. The maximum load is used to determine the shear stress at the critical interface. This requires the use of the measured thickness and width of the specimens in combination with the formula for transverse shear stresses (Eq. 1), because the stress distribution depends on the lay-up. For both orientations [0/90] & [0/45] the measured displacements are similar with only small differences. The interlaminar stress distributions are used in a simplified quadratic stress criterion[15] to estimate the delaminating initiation load. The results suggest that for angle-ply hybrid laminates the interlaminar shear stresses are mainly responsible for the delamination initiation. Finally, it has been reported that for carbon/glass hybrid laminate with 0/90 orientation possess higher shear delamination strength as compared to ±450 orientation hybrid laminate.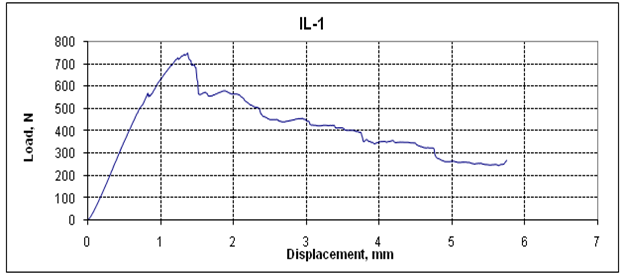 | Figure 4. Carbon/Glass Hybrid laminate (0/90) |
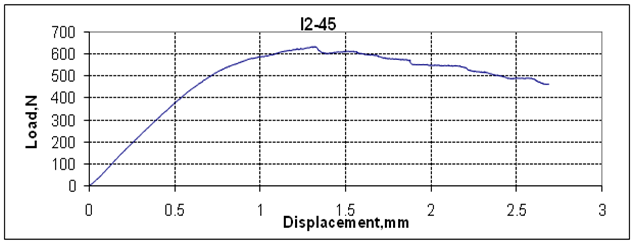 | Figure 5. Carbon/Glass Hybrid laminate (±450) |
Table 1. CARBON/GLASSS HYBRID –0/90 ILSS Test results  |
| |
|
Table 2. CARBON/GLASSS HYBRID – ± 45 ILSS Test result 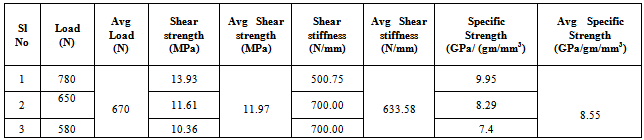 |
| |
|
4. Conclusions
Experiments were conducted on Carbon fiber/ Glass fiber/Epoxy resin hybrid angle ply laminates with different fiber orientation to characterize the ILSS properties. The following conclusions were drawn and recorded:a) The composite laminates with two different orientations were fabricated using hand layup process. Because of the different orientations, the distributions of fiber along the loading direction are different from each other. b) Experimental evaluation of ILSS properties of carbon/glass epoxy hybrid specimens have been attempted and it is observed that the ILSS strength, increases predominantly in 0/90 hybrid as compared to ±45 for the same volume fraction of glass.c) Short beam Test method adopted here appears to be the simple and effective way of evaluating the ILSS properties of hybrid laminated specimens.d) On visual inspection failure was observed in the hybrid specimen from shear mode across the width of the specimen away from the end supports.Finally, it can be concluded that the ILSS experiments conducted on hybrid specimen yielded good results through a simple short beam test set up.
References
[1] | G. Kretsis, a review of the Tensile, Compressive, Flexural and shear properties of hybrid fibre reinforced plastics, Composites, Vol 18:1987. |
[2] | J. Harding and L.M Welsh, A tensile testing technique for fibre-reinforced composites at impact rates of strain, J Master Sci 18:1983. |
[3] | Chawla, K. Kumar, 1999 “Mechanical Behavior of Materials”, Prentice Hall, Inc. |
[4] | Callister, W. D. and Rethwlsch, D. G., 2007 “Materials Science and Engineering an introduction”, 7th Edition, John Wiley and Sons, Inc. |
[5] | J.Cho, Mechanical enhancement of carbon fibre/epoxy composites by graphite nano platelet reinforcement, S. Direct 2007:685-688. |
[6] | S. Mula, B. C. Ray and P. K. Ray, Assessment of interlaminar shear strength of hybrid composites subjected to a fluctuating humid environment International symposium research students on materials science and engineering. Dec 20-22.2004 |
[7] | P. Feraboli*, K.T. Kedward Four-point bend interlaminar shear testing of uni- and multi-directional carbon/epoxy composite systems Composites: Part A 34 (2003) 1265–1271 |
[8] | N.K. Naik*, Addis Asmelash, Venkateswara Rao Kavala, Veerraju “Interlaminar shear properties of polymer matrix composites: Strain rate effect Structures Panel, Aeronautics Research and Development Board, Ministry of Defense, Government of India, Grant No. DARO/08/1051204/M/I. |
[9] | C.Y.Lee & C.C.Huang Evaluation of interlaminar shear stress by strain measurements on laminate surfaces, Department of Mechanical Engineering, Da-Yeh University, Da-Tsuen, Chang-Hwa, Taiwan 515, and R.O.C. |
[10] | Zhihang Fan, Michael H. Santare, Suresh G. Advani* Interlaminar shear strength of glass fiber reinforced epoxy composites enhanced with multi-walled carbon nanotubes Composites: Part A 39 (2008) 540–554 |
[11] | P. RamaLakshmi, Dr P.Ravinder Reddy Investigation of interlaminar shear strength in carbon epoxy and carbon epoxy carbon nanotubes using experimental and finite element technique, International Journal of Engineering Research and Applications (IJERA) ISSN: 2248-9622 |
[12] | Taehyoun Kim* and Satya N. Atlurif , Interlaminar Stresses in Composite Laminates Under Out-of-Plane Shear/Bending AIAA JOURNAL Vol. 32, No. 8, August 1994. |
[13] | M. Izadi, M. Tahani , Analysis of interlaminar stresses in general cross-ply laminates with distributed piezoelectric actuators Composite Structures 92 (2010) 757–768 |
[14] | Stephan Hinz a, Toshihiro Omoori b, Masaki Hojo b, Karl Schulte a, Damage characterisation of fibre metal laminates under interlaminar shear load Composites: Part A 40 (2009) 925–931. |
[15] | Tsai S W and Hahn H T. Introduction to Composite Materials, Technomic Publishing Co., 1980. |