Sérgio Augusto Mello da Silva1, André Luis Christoforo2, Sérgio Luiz Moni Ribeiro Filho2, Luciano Donizete Varanda3, Francisco Antonio Rocco Lahr3
1Department of Civil Engineering, State University “Júlio Mesquita Filho” (UNESP), Ilha Solteira, 15.385-000, Brazil
2Department of Mechanical Engineering, Federal University of São João del Rei (UFSJ), São João del-Rei, 36.307-352, Brazil
3Department of Structural Engineering, University of São Paulo (EESC/USP), São Carlos, 13.566-590, Brazil
Correspondence to: André Luis Christoforo, Department of Mechanical Engineering, Federal University of São João del Rei (UFSJ), São João del-Rei, 36.307-352, Brazil.
Email: |  |
Copyright © 2012 Scientific & Academic Publishing. All Rights Reserved.
Abstract
This study aimed to investigate, with the aid of the Brazilian NBR 14810:2002 standard, the physical properties: bulk density and moisture and mechanical properties: strength flexural modulus and internal compliance of particleboards manufacture with bicomponent polyurethane resins derived from castor oil and Cambará, Canelinha and Cedrinho fibres. The factors investigated were: nominal density (0.80 g/cm3), nominal thickness (10mm), moisture content of the particles (5%), percentage of resin (15%), time used in the pressing cycle (10min), hot pressing (100℃), pressing pressure (5MPa) and length of the particles (3 to 5mm), leading to a full factorial design of 22 type, providing four different experimental conditions. The mechanical properties of both materials prepared showed higher values than the stipulated by the standard. Physical properties, only the density has overstepped the bounds set by the NBR 14810:2002, rating the particleboards produced as high density.
Keywords:
Particleboards, Physical, Mechanical Properties, Polyurethane Resin
Cite this paper:
Sérgio Augusto Mello da Silva, André Luis Christoforo, Sérgio Luiz Moni Ribeiro Filho, Luciano Donizete Varanda, Francisco Antonio Rocco Lahr, "Particleboard Manufactured with Bicomponent Polyurethane Resin Base on Castor Oil", International Journal of Composite Materials, Vol. 2 No. 6, 2012, pp. 115-118. doi: 10.5923/j.cmaterials.20120206.01.
1. Introduction
Brazil and worldwide researches have been developed focusing the particle boards, aiming to verify the feasibility of developing panels by some experimental factors and stipulated levels[1, 2].Silva et al.[3] evaluated the equilibrium moisture content of wood panels using cluster samples and multilaminate plywood, hardboard, Oriented Strand Board (OSB), Medium Density Fiberboard (MDF), High Density Fiberboard (HDF), wood-cement and wood-plastic. Among others, the authors conclude that Nelson's equation is efficient for estimating the equilibrium moisture content in all cases studied, no significant differences in hysteresis between the products studied, revealing that all have the same dimensional stability.Akgüla and Çamlibelb[4] evaluated the strength and stiffness of particle boards made from Rhododendron timber, founded in abundance in the Black Sea (Turkey), particles having controlled humidity of 14% and held together by adhesive using urea-formaldehyde. The results indicate the use of Rhododendron timber in the manufacture of panels.Belini et al.[5] produced and evaluated MDF with three different conditions of chip shredding system, evaluated the anatomical features of wood cell components. Among the results, the authors conclude that increasing the intensity refining of wood chips reduced the average fiber length and increased the percentage of broken fibers, and cause a decrease in the number of vessels and parenchyma cells.Belini et al.[6] evaluate the production of MDF using three samples of Eucalyptus grandis wood chips. The results of anatomical and morphological analyses were discussed and compared with information from specialized literature and correlated with the production process of MDF.Abreu et al.[7] developed and evaluated waste wood panels intended to production of objects to compare their qualities, being used ten graphic designs reproduced by craftsmen in the industry. The authors concluded that the mixing of different waste panels affected the evaluation of the attributes finishing, beauty and colour, no significant difference with respect to the attributes functionality, weight, proportion and symmetry.Saffian et al.[8] studied the feasibility of production of particle boards made with clones RRIM 2020 with four years of age, were evaluated the modulus of elasticity (MOE) and strength (MOR). The results indicate that is possible to manufacture panels with the rubber clones evaluated.One aspect to consider due to the industrialization of particleboards is to use products that pollute the environment, mainly through the emission of gases. Accordingly it is necessary to develop new products, such as the proposed study by Bradi et al.[9], having considered the influence of a mixture of vegetable oil in the polyurethane matrix strength of wood fiber panels. The analyses possible to conclude that it is possible to use mixtures of vegetable oil in the polyurethane matrix in the ratio 35:65 (by weight) for the manufacture of wood fiber panels.Silva and Lahr[10] evaluated the production of particleboard with homogeneous particles of wood in the Amazon for low and medium density (Erisma uncinatum, Nectranda lanceolata, Erisma sp). Particleboards were made with nominal thickness of 10 mm, nominal density of 0.75g/cm3, using 10% of bicomponent polyurethane resin derived from castor oil and particles with a length from 0.02 mm to 6 mm, 90℃ of hot pressing, 40MPa of pressure and time of 10 minutes. In the assessments according to NBR14810:2002 standard, panels of wood particles Nectranda lanceolata showed higher strength values, which are above the limit set by the standard.Dias et al.[11] evaluated the mechanical properties of plywood panels made of polyurethane resin based on castor oil. The results for the MOE did not reach the minimum value of 18MPa, being justified by poor distribution of the adhesive during the formation process of the panels.Fiorelli et al.[12] developed particleboards with sugar cane bagasse and polyurethane resin derived from castor oil investigating the response variables: bulk density, swelling, absorption and modulus of elasticity and strength modulus. The results indicated as those made of high density, suitable for industrial use, showing the efficiency of the polyurethane resin.Paes et al.[13] evaluated the effect of the combination of pressure (2.0, 3.0, 3.5 MPa) and temperature (50, 60, 90℃) in particleboard with Pinus elliottii wood and polyurethane resin derived from castor oil on the response variables: density, swelling and water absorption (0-2h, 2-24, 0-24h), strength modulus, screw pull-out and internal adhesion, concluding that the combinations: 3.0 MPa and 90°C and 3.5 MPa and 60℃ showed the best results, proving to be a pressing temperature the most important variable for quality (workmanship) of the panels.Sartori et al.[14] evaluated the mechanical performance of particleboards manufactured with reforestation wood, sugar cane bagasse and bicomponent polyurethane resin derived from castor oil as an alternative to the closure system side of the trunk collective management center for beef cattle. The physical and mechanical properties obtained confirmed the efficiency of the proposed structural model for use in management center.According to the Brazilian Association of Wood Panels[15], Brazil is one of the most advanced countries of the world in the manufacture of particle boards, whose annual production currently amounts to 612.000m3, accounting for worldwide production a very low percentage considering the wood potential of the country and the technology installed.Considering the positive aspects of the current MDF production in Brazil and the need for studies that will permit the use of new adhesives, this study aimed to evaluate, with the aid of the Brazilian NBR 14810[16] standard, the physical properties: bulk density and moisture and mechanical properties: strength flexural modulus (MOR) and internal adhesion (AI) of particleboards produced with bicomponent polyurethane resin derived from castor oil and Cambará, Canelinha and Cedrinho wood fibres, making it possible to evaluate the potential of the materials developed.
2. Material and Methods
The factors and levels investigated in the preparation of the panels are nominal density (0.80 g/cm3), nominal thickness (10mm), moisture content of the particles (5%), resin (15%), cycle time used in pressing (10min), hot pressing (100℃), the pressing pressure (5MPa) and length of the particles (3 to 5 mm).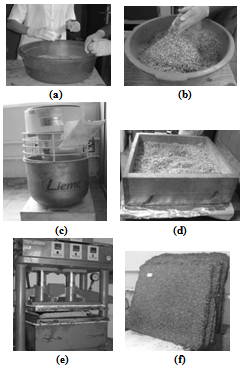 | Figure 1. Sequence used in the preparation of the particleboards |
With respect to procedures for producing the panels, it should be noted:- Addition of 15% of bicomponent polyurethane resin: for each component was considered the addition of a part corresponding to 50% of the total content of the resin and according to the manufacturer's instructions, was initially added to and mixed with the substrate content corresponding to 1 part polyol, and then the content corresponding to a part of prepolymer. This procedure provided good homogenization of resin to the substrate and prevented expansion reactions;- Pressing cycle: was to apply a constant pressure of 5MPa over 3 minutes, followed by the pressure relief of the press for a time of 30 seconds and subsequent use of the pressure of 5MPa for 7 minutes. This procedure was used for making up all the panels, there were no formation of bubbles and cracks in the particleboards produced;- Temperature of pressing: used 90oC, avoiding bubble formation, leading to panels with good qualities;- Press pressing: the particleboards were prepared employing 5MPa, pressure used in the industrial production of medium density panels.The particleboards were made following the procedures as shown in Figure 1.Were produced two panels for the investigated conditions, with dimensions 400×400×1mm.Seven specimens were extracted from each panel produced to determine the strength flexural modulus (MOR), with nominal dimensions of 50×250×10mm.For internal adhesion (AI) were extracted two samples of each specimen used to determine the strength flexural modulus, with nominal dimensions of 50×50×10mm.With respect to density and moisture, each specimen used in the bending test were extracted two another specimens, with nominal dimensions of 50×250×10mm.
3. Results and Discussions
Table 1. Mechanical properties of the particleboards |
| Canelinha | Cambará | Cedrinho | MOR (MPa) | AI (MPa) | MOR (MPa) | AI (MPa) | MOR (MPa) | AI (MPa) | 21.18 | 0.85 | 30.59 | 1.2 | 24.41 | 1.0 | Sd:1.69 | Sd: 0.13 | Sd:1.86 | Sd:0.16 | Sd:1.24 | Sd:0.12 |
|
|
According to NBR 14810[16] standard, the minimum suggested for strength flexural modulus (MOR) and internal adhesion (AI) should be 18MPa and 0.4 MPa respectively. The values of MOR and AI for both wood species were above the limits established by the standard. The lower values of MOR and AI were obtained for the panels made with Canelinha wood, still being 1.17 and 2.12 times higher than the standard.The average values of bulk density (dap) and moisture (um) of the panels for both species are shown in Table 2.Table 2. Bulk density and moisture of the particleboards |
| Madeira | Wood dap (g/cm3) | Panels dap (g/cm3) | um (%) | Canelinha | 0,65 | 0,88 | 9,1 | Cambará | 0,70 | 0,90 | 8,2 | Cedrinho | 0,55 | 0,82 | 9,5 |
|
|
4. Conclusions
The analysis of the strength flexural modulus, the bulk density and moisture allowed inferences about the manufacturing process of the panels and consequently on the experimental parameters used:- The moisture of the particles (5%) did not result in expansion reaction of the bicomponent polyurethane resin which impair the homogeneity of the mixture;- The time pressing (10 minutes) was sufficient to cure the resin, however, the use of 100oC caused bubbles to form in the surfaces of the particleboards;- The pressing pressure (5MPa) was suitable for compression of the panels that acquired density exceeding 0.8 g/cm3 and a thickness of 10mm, as planned;- The use of the resin in the proportion 15% (dry weight basis) gave strong adhesion between the particles, because the values of sheet properties are better than the values suggested by NBR 14810[16].Even considering the significant results, mainly for the mechanical properties, it is necessary to adjust the variables of the process of manufacture the panels aiming the use of smaller amounts of resin, allowing reduction of cost of the materials produced.
References
[1] | T. Akbulut, T.; E. Koç, "The effect of the wood species on the roughness of the surface and profiled areas of medium density fiberboard", Wood Research, v 51, n 2, p 77-86, 2006. |
[2] | M. C. N. Yemele; P. Blanchet; A. Cloutier; A. Kouba, "Effects of bark content and particle geometry on the physical and mechanical properties of particleboard made from black spruce and trembling aspen bark". Forest Products Journal, vol. 58, issue 11, pp. 48-56, 2008. |
[3] | A. S. Silva; L. M. Mendes; P. F. Trugilho; F. A. Mori; I. F. Santos, "Umidade de equilíbrio de painéis de madeira". Revista Árvore, Viçosa-MG, v.29, n.4, p.639-646, 2005. |
[4] | M. Akgüla; O. Çamlibelb, "Manufacture of medium density fiberboard (MDF) panels from rhododendron (R. ponticum L.) biomass". Building and Environment. Part Special: Building Performance Simulation, Volume 43, Issue 4, pp. 438–443, 2008. |
[5] | U. L. Belini; Filho M. Tomazelo; M. P. Chagas; J. T. S. Oliveira, "Alterações na estrutura anatômica da madeira de cavacos de Eucalyptus grandis em três condições de desfibramento para a confecção de painéis MDF". Revista Árvore, Viçosa-MG, v.32, n.3, p.523-532, 2008. |
[6] | U. L. Belini; Filho, M. Tomazello; M. P. Chagas; T. S. Dias, "Caracterização da estrutura anatômica, densidade básica e morfologia de cavacos da madeira de Eucalyptus grandis para a produção de painéis MDF". Revista Árvore, Viçosa-MG, v.32, n.4, p.707-713, 2008. |
[7] | L. B. Abreu; L. M. Mendes; J. R. M. Silva, "Aproveitamento de resíduos de painéis de madeira gerados pela indústria moveleira na produção de pequenos objetos". Revista Árvore, Viçosa-MG, v.33, n.1, p.171-177, 2009. |
[8] | H. A. Saffian; J. Harun; P. M. Thair; K. Abdar, "Feasibility of Manufacturing a Medium Density Fibreboard Made of 4-Year Old Rubber Tree RRIM 2020 Clone". Key Engineering Materials - Composite Science and Technology, Vol. 471, pp. 839-844, 2011. |
[9] | K. H. Bradi; K. A. M. Amim; Z. Othman; H.A. Manaf; N. K. Khalid, "Effect of filler-to-matrix blending ratio on the mechanical strength of palm-based". Source: Polymer International, 55 (2): p. 190-195. Publisher: John Wiley & Sons LDT. The Atrium, Southern Gate, Chichester PO19 8SQ. England, 2006. |
[10] | S. Silva; F. A Rocco Lahr, "Chapas de partículas confeccionadas com resíduos de madeiras tropicais de baixa densidade". Livro: Reciclagem de resíduos para a construção civil. Editora da Universidade FUMEC. Capítulo 14, p. 343-365. Belo Horizonte (MG), 2007. |
[11] | F. M. Dias, "Aplicação de resina poliuretana à base de mamona na fabricação de painéis de madeira aglomerada". Capítulo de Livro: LAHR, F. A. R. Produtos derivados da madeira. São Carlos: EESC/USP, p. 37-160, 2008. |
[12] | J. Fiorelli; F. A. Rocco Lahr; M. F. Nascimento; Jr., H. Savastano; J. A. Rossignolo, "Painéis de partículas à base de bagaço de cana e resina de mamona – produção e propriedades". Acta Scientiarum Technology, Maringá, v. 33, n. 4, p. 401-406, 2011. |
[13] | J. B. Paes; S. T. Nunes; F. A. Rocco Lahr; M. F. Nascimento; R. M. A. Lacerda, "Qualidade de chapas de partículas de pinus elliottii coladas com resina poliuretana sob diferentes combinações de pressão e temperatura". Ciência Florestal, Santa Maria, v. 21, n. 3, p. 551-558, 2011. |
[14] | D. L. Sartori; J. C. M. Cravo; N. G. Barrero; J. Fiorelli; Jr., H. Savastano, "Painel em madeira de reflorestamento e chapas de partículas para instalações rurais". Floresta e Ambiente, 19(2), p. 171-178, 2012. |
[15] | Associação Brasileira das Indústrias de Painéis de Madeira (ABIPA) - Produtos e Tecnologias. "Sobre consumo mundial de aglomerado em 2004/2005", www.abipa.org.br, São Paulo (SP). 2006. |
[16] | Associação Brasileira de Normas Técnicas (ABNT) NBR 14810. "Chapas de madeira aglomerada. Parte I – Terminologia, Parte II – Requisitos e Parte III – Métodos de ensaio", Rio de Janeiro, 2002. |