César Martín Gómez
Department of Construction Science – Building and Energy Section, School of Architecture (Universidad de Navarra), Pamplona, 31080, Spain
Correspondence to: César Martín Gómez, Department of Construction Science – Building and Energy Section, School of Architecture (Universidad de Navarra), Pamplona, 31080, Spain.
Email: |  |
Copyright © 2012 Scientific & Academic Publishing. All Rights Reserved.
Abstract
The International Expo of Saragossa 2008 was dedicated to water and the Pavilion of Spain, as one more expository element, wanted to show how water could be used as a means of conditioning. For that reason a proposal was assessed that combined the traditional use of ceramics and evaporative cooling in an innovative solution integrated into the building itself, called 'Microclimate Generator Pillars' (MGP). The purpose of this text is to describe the constructive development of the MGP as, although the theoretical development has been described in several technical articles, it is also appropriate to describe the technical problems that emerged when building what, until then, was just a theoretical model, as well as outlining the main results of the joint after its starting up. This is therefore, a description of an implemented facility as it has not been shown in any other technical publication, despite the impact this pavillon has had on the European architecture in general, and particularly on architecture in Spain
Keywords:
Architecture, Building, Construction, Evaporative Cooling
Cite this paper: César Martín Gómez, Constructive Development of the 'Microclimate Generator Pillars' from the Pavilion of Spain in Expo Saragossa, Architecture Research, Vol. 2 No. 2, 2012, pp. 7-13. doi: 10.5923/j.arch.20120202.02.
1. Introduction
The Pavilion of Spain for the International Expo of Water at Saragossa 2008 "Water and Sustainable Development" emerged as a result of a competition held in 2005, promoted by the State Company for International Exhibitions of Spain, which was won by the Navarrese architect Francisco Mangado Beloqui and the National Renewable Energy Center of Spain, the latter body acting as a technical partner on issues related to energy performance and to the sustainability of the Pavilion.The building, after its construction, has received several architectural prizes, which fact supports its quality in the field of technological innovation and sustainability[1]. Thus, the Pavilion has low energy consumption both for materials and constructive systems used, as for the high efficiency of the proposed facilities.The floor-plan of the Pavilion is conceived as a network of pillars placed on a load-bearing water surface, designed to provide a significant reduction in thermal oscillations around the main spaces of the Pavilion The program can be divided into three basic areas developed into four floors: expository area, meeting rooms and technical offices[2].
2. Theoretical Design of MGP
One of the technological innovations used for the first time in the buildings is the cooling system integrated by the so-called Microclimate Generator Pillars (MGP).During the Pavilion’s implementation project phase, it was treated as a ‘minor element’, which would show the possibilities of cooling with water at the Expo of Water but, nevertheless, it had enormous media coverage impact, despite its limited impact on the total building energy consumption.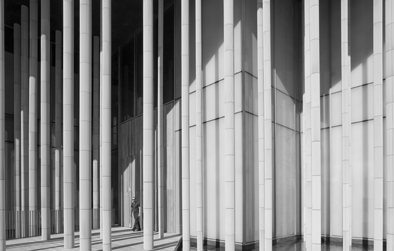 | Figure 1. Image of the Pavilion |
Spanish law prohibits outdoor conditioning, except when using residual energy sources[3]. In this case, the fans received their energy from the photovoltaic panels integrated into the roof, while the water came from rainwater tanks located in the basement.Furthermore, it must be noted that the purpose of the MGPs was not to air-condition a large space outside, but only to cool Saragossa’s hot summer temperatures at the visitor waiting area, before they reached the first exhibition. This point must be underlined in order to understand the results obtained in the final assembly.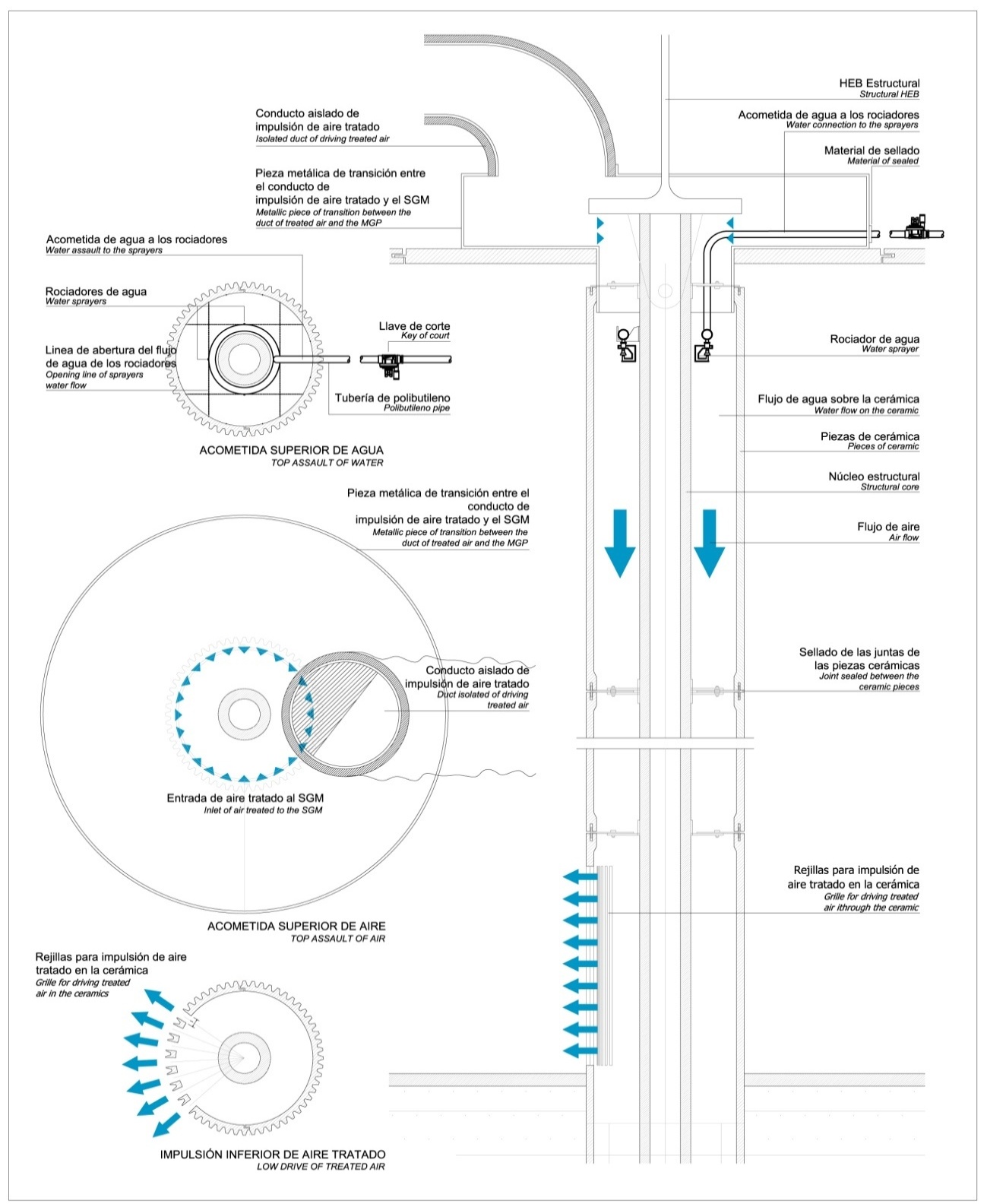 | Figure 2. MGP execution operation plan |
The origin of the solution used in these supports is evaporative cooling: an effect to reduce room temperatures, used for centuries in climates such as the Mediterranean, with hot dry summers.Briefly, the operation of the MGPs is as follows [Figure. 2]:- The MGPs are comprised of a structural core around which pieces of pottery are placed. Pottery was chosen due to its porosity, strength and low environmental footprint, and long lifespan. This is traditionally a key material in Spanish architecture; its environmental advantages lie in its durability and the low energy costs when manufacturing, setting up and maintaining.- At the top of the pillar, some sprinklers wet the inside of the pieces of pottery.- The draught, entering at the top of the pillars, cools while running down the 14.6 meter pillar.- At the bottom, one of the pieces of pottery has slits which drives the treated air to the external environment.Since the main objective of this article is the constructive development of the MGPs, and not the theoretical understanding of its operation, please refer to the final bibliography for more information about both external conditions of design and the theoretical calculations and initial trials of fluid-dynamics[4].
3. Implementation of MGP
Research in architecture has a feature that differentiates it from other branches of knowledge: if the research is too innovative or based on approaches that are overly theoretical, it may not ever be applied in a building. If certain innovation in a building is applied, although it means a step forward in construction science, if it has taken into account the durability of the solution in the building, it might occur that in certain scientific societies, it is not deemed relevant research.For these reasons, it is then described what were the highlights in the real construction in a building on a theoretical model.
3.1. Construction
One of the most unique aspects of the construction of the MGPs, was the peculiar geometry of the Pavilion, which implied that the entire assembly held up by small based scaffolding for easing movement between the 'forest' of columns. Therefore, several assembly and operation tests were first performed at the base of the building, and then they were moved progressively further away from the pillars for easier access to the rest, as any mistake, would have involved many hours of assembly and disassembly, something unacceptable in a project with a very tight timeframes.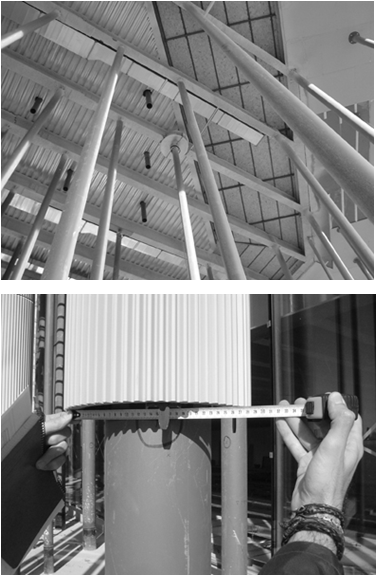 | Figure 3 - 4. MGP construction details |
The pottery from all the pillars was anchored to the structural metal core, with no type of hallmark between them, which was unacceptable in the case of MGPs, which should ensure that all the airflow reaches the bottom grilles It should be noted that in the designing stage the joint among the pieces of pottery was not exactly defined. After various tests, we decided to seal the joints with a black outdoor silicone (for aesthetic reasons), which turned out difficult to place both due to the curved geometry of the pieces and the small space between them, large enough to allow air to exit, and small enough to hinder the introduction of the usual tools for such work. During the operation tests, tracer gas testing was fundamental, and permitted the location of some flaws in the seal [Figure. 5].One of the changes regarding the original design was that although the plan was that a piece of metal at the bottom of the MGP would force air movement towards the exit grilles, at the work itself, the person in charge of assembling that piece explained the difficulties of assembling (welding to a steel column, distance to ceramics...) and asked why the lower air outflow could not be the sheet of water itself, and not an additional element. This suggestion seemed reasonable to all the people responsible, and the corresponding tests were carried out, in which there were neither significant losses of flow nor speed of the air outflow at the grilles of the MGPs.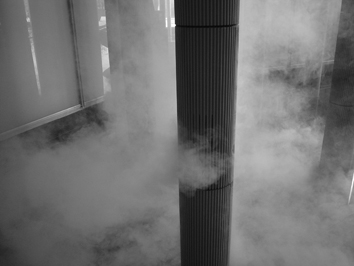 | Figure 5. Tracer gas test in one of the MGPs during the implementation of the system, and how the air is distributed homogeneously at the outflow |
3.2. Facilities
Regarding facilities that serve to the MGPs, the following points can be highlighted:- The system consists of the following elements:• In order to force the flow of the untreated outdoor air through the tube network down to the MGPs, two centrifugal fans mounted on boxes of galvanized sheets were used, with the frequency controller installed at the covered floor. The characteristics of these devices are described in Table 1.• 1 Motorized valve for water supply to the MGPs.• 5 Temperature probes located in sample pillar, at different heights.- The outside air transport to the different MGPs was by means of tubes manufactured of galvanized steel sheet[5].- They were two pipeline networks proposed: one at the main entrance to the Pavilion before accessing the cinema and another between leaving the cinema and accessing the exhibition area.- The assembly adjustment of the steel structure involved two significant changes in the service facilities of the MGPs:• First, the sprinklers that should wet the ceramics at the top of the MGPs had to be changed as the final assembly implied distance and height changes from the theoretical model. Finally, mini-sprinklers of proven efficacy in the field of gardening were put in place. Various tests were performed in works for operation with this solution, and it was found that the ceramic pieces were properly dampened [Figure. 6].• The most sensitive part of the assembly was the transition between the metal plate ducts from the fan to the top of the MGPs. In the project a specially manufactured metal part was designed and evaluated, which fitted the double-T outline of the metal structure and received two flexible connecting pipes with the main tube of plate. Finally, adjustments in the structure gave some centimeters of way for the tubes, and connection was made with a single flexible pipe to the top of the MGPs, a solution that considerably reduced the loss of load over the original piece [Figure. 7].Table 1. Characteristics of the fans of pressure to the MGPs. The technical data presented in this table are taken from the Definitive Project Report, and not from the Implementation Project |
| Denomination | Fan 1 | Fan 2 | Model | S&PCVTT-22/22-650-5’5 | S&PCVTT-12/12-1050-1’1 | Flow (m3/h) | 18.000 | 5.000 | Eng. Power (W) | 5.5 | 1.1 | Supply | 400/III/50 | 400/III/50 |
|
|
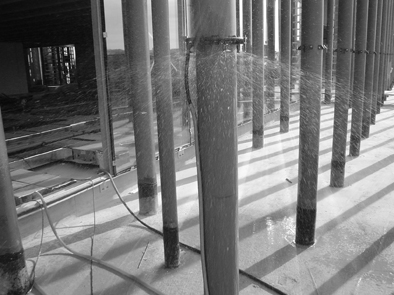 | Figure 6. Sprays of water from the MGPs: wetting test |
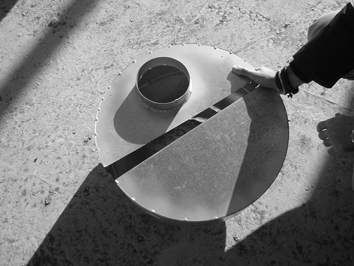 | Figure 7. Image of the transition piece between the tube of plate and the top of the MGP |
3.3. Control
All Pavilion facilities design was conceived and integrated in a Building Management System (BMS), which should ensure a reduction in operating costs and the maintenance of the comfort conditions and safety requirements.The elements that constitute the BMS in general, including those required for MGPs operation are:- Control center.- Distributed controllers.- Elements of field (instrumentation), actuators and motorized valves.- Electrical and communicating lines, with their connections.- Panels for housing and mechanical-electrical protection of the control center and the regulators of terminal air conditioning units.The functions provided by the system of control over the MGPs are:- Supervision of the status of all facilities, by displaying a Synoptic diagram with color changes of the symbols which represent each team according to its state.- Reception of any alarm occurred.- Automation of: starting and stopping of the equipment; graphical and digital recorders to follow the historical evolution of the signs of the system; chronological registration of alarm events of the different installations and the user commands (in this case, noting the user-name who requested the command).- Generating reports of alarms and events.The control system should allow the central computer to act on the water supply solenoid valve and on the fans in different ways:- User’s guide for both elements, in order to carry out tests and tasks maintenance.- Individual timing for both items.- Performance of both elements linked to the temperatures marked by the inner probes of the sample BMS.- Automatic joint action between the two elements.The description of the sequence in automatic way would be [Table 2]:1. When the system detects high temperature outside (defined at start up to 20℃) during the operation hours from 10 to 20 h, the sprinkler system inside the ceramic turns on, opening the solenoid valve of the water network. After various tests, it was found that 5 minutes was needed to wet the ceramics enough..2. The solenoid valve is closed.3. The fans start until it is detected that the water inside the pillars has evaporated and the inside of the MGPs are soaked again, re-starting the process.As noted, the job reference values are not shown because they were altered over the three-month period of the Expo (June-August) based on the system performance. That is, although the system worked out, the months of operation, actually coincided with the months of testing a system that was set in motion by first time. During this time the architectural needs were combined (by the architecture studio), with the initial design theoretical values (provided by CENER), along with the system of adjustments and calibrations to be performed by the company responsible for the installation.Table 2. Checklist of points for control of the installation of the MGPs by the Building Management System of the Pavilion 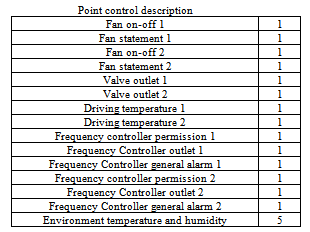 |
| |
|
3.4. Maintenance
The Pavilion of Spain was visited by hundreds of thousands of people during the Expo, which meant that at all times there were people in charge of maintenance on the building, so the installation – according to data provided by the Property– was running permanemtly, and no severe abnormality led the system to stop[6].But given the particularities of the facility, a separate consideration was the prevention of the risk of the growth of the bacterium 'Legionella pneumophila’.Although the starting position was very favourable for several reasons, firstly, as the evaporative coolers do not provide the right conditions for the growth of the bacterium[7], and the water temperature would tend to be below the temperature range for the growth of 'Legionella', plus the fact that warer was not recirculated in the MGPs, the architecture team and the officials responsible for managing Saragossa’s water, were very sensitive to this problem.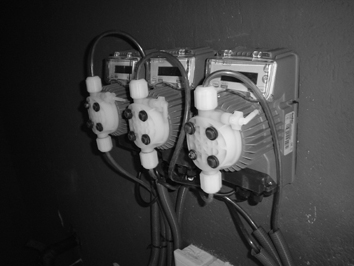 | Figure 8. Dispenser of chlorine and polyphosphates |
Therefore, even if the growth of Legionella given the above conditions would be unusual, due to the Saragossa’s water hardness and to the formation of biocapes (inherent to those processes that use water), it was decided to perform a detailed protocol of maintenance and water treatment (which included the dosage from time to time of chlorine and polyphosphates into the water network that fed the MGPs) in order to minimize the risks of growth and transmission of 'Legionella'
4. Results
In an International Expo, the safety of the public is a working principle, and even more in the Pavilion of the organizing country. This situation meant that, although having daily access to the Pavilion to check the operation of the fitting-out system and thus the control of the installation of MGPs, data from the BMS’s PC could not be taken out from the pavilion for safety reasons.This, obviously, diminishes the research in scientific terms, since one cannot prove everything that is asserted, but the authors believe this communication of information is better than silence.In this publication we have been permitted to show a screen image of the control computer during the testing phases. In the test shown, held at 11 am, outdoor air temperature in the street was 24.7℃ with 42.5% humidity[8], and the air that arrived at fans was 20.7℃. However, in people’s perception, this measure was lower due to the spreading of the air flow coming out from the grids.The resulting values for a second publishable test are summarized in Table 3.Table 3. Data from one of the publishable test of the system |
| Outside air temperature | 34'9℃ | Outside air humidity | 33'6℃ | Engine power | 100% | Water main - Electrovalves opening | 0% | Probe 1 - Upper | 32'5℃ | Probe 2 | 31'1℃ | Probe 3 | 28'4℃ | Probe 4 | 27'9℃ | Probe 5 - Lower | 25'2℃ |
|
|
5. Conclusions
We can divide the conclusions in two groups: numerical and architectonical.In numerical terms, after three months of intensive use of the building, although the author can not demonstrate completely all the data (temperatures, ventilation flows, humidity) because of the security problems commented before, it is possible to say that the system reached their objectives for this building during the Expo. And what is more important: the architects and engineers team have showed how this solution could be replicated in similar climatic situations.But this article has been developed from and architectonical point of view, and it is necessary to focus the conclusions in this direction, explaining the main results as a form to integrate (not just paste) this kind of efficient technology in other buildings. In this way, we have the following three architectonical conclusions.The main problem faced by this research project is that it was part of complex works in which there were other complicated issues to resolve, such as structure, closures, the innovative ceramic system, the placement of the photovoltaic panels... with a very tight implementation deadlines, and strict economic controls. For which reason the investigation of the MGPs was not for the Property, far from being the main objective.Furthermore, the work team of the Pavilion could not count on any technician who was dedicated exclusively to solving the many technical and theoretical variables that occurred during the assembly of the MGPs.So the first architectonical conclusion would be the need to raise awareness to the Property of the importance of research into these matters, and even more in cases of special buildings like this, where the results (whether good or not) may be of major relevance in its communication.Together with this issue, there is the obvious problem that it was the first time this kind of system was used, and there were no references to be compared with, for which, given the changes brought about by other architectural problems and –fundamentally- the short periods of implementation, the luck factor should be considered too. Clearly, the union and the work of so many good professionals formed the basis necessary to achieve a good result but, seen with hindsight, many things could have prevented reaching fruition.This reflection allows us to reach a second architectonical conclusion: good research work in architecture has to be coordinated with the project’s deadlines for implementing where it is included.Third and final architectonical conclusion: the results, although promising, we must take into account that the system is only applicable in geographical areas with similar climatic conditions to those of Saragossa. In any case, in such areas, this is is a solution of easy replication that has validated its behaviour after the visit of the hundreds of thousands of people who accessed the Pavilion.
ACKNOWLEDGEMENTS
Architect Francisco Mangado Beloqui.Architect Almudena Fiestas Marín.Engineer Pedro López Clément.
Footnotes
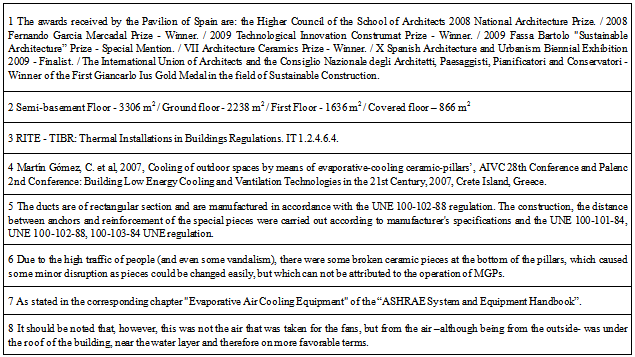
References
[1] | ASHRAE Guideline 12-2000. "Minimizing the Risk of Legionellosis Associated with Building Water Systems". ISSN 1041-2336 (2000). |
[2] | Bowman, N., Lomas, K., Cook, M., Eppel, H., Ford, B., Hewitt, M., Cucinella, M., Francis, E., Rodriguez, E., Gonzalez, R., Álvarez, S., Galata, A., Lanarde, P. and Belarbi, R. (1997), Application of PDEC to non-domestic buildings, Renewable Energy 10 (2-3), 191-196. |
[3] | Erell, E., Pearlmutter, D. and Etzion, Y. (2007). A multi-stage down-draft evaporative cool tower for semi-enclosed spaces: Aerodynamic performance, Solar Energy, 82, 420-429. |
[4] | Gillet, A. C., de Laminne, J. M. and Lefebvre, S. (1991). An Illustration of Semi-Passive Bioclimatic Architecture: The Belgian Pavilion Project for the Seville World Fair 1992, Plea ́91 Architecture and Urban Space, Seville, Spain, 589-594. |
[5] | Hicks, N. G., Thomson, T. L., Yoklic, M. R., Chalfoun, N. V. and Kent, K. J. (1991). Evaporative Cooling for Large Exhibition Spaces: A Methodology for System Design/Engineering based on Human Comfort, PLEA ́91 Architecture and Urban Space, Se- ville, Spain, pp.159-164. |
[6] | Incropera, F. P. and De Witt, D. P. (4th ed) (1996). Fundamentals of Heat and Mass Transfer, New York, Wiley & Sons. Kundu, P. K. and Cohen, I. M. (3rd edition) (2004). Fluid Mechanics, San Diego, Elsevier. |
[7] | Launder, B. E. and Spalding, D. B. (1974). The Numerical Computation of Turbulent Flows. Computer Methods in Applied Mechanics and Engineering, 3:269-289. Ponter et al. (1967). Int. J. Heat Mass Transfer, 10, 349–359; Trans. Inst. Chem.Eng., London, 45, 345–352. |
[8] | Pearlmutter, D., Erell, E. and Etzion, Y. (2008). A multi-stage down-draft evaporative cool tower for semi- enclosed spaces: Experiments with a water spraying system, Solar Energy, 82, 430-440. |
[9] | Stainthorp and Allen (1967). Trans. Inst. Chem. Eng. London, 43, 85–91. Watanabe et al. (1975). J.Chem. Eng., Japan, 8, 75. |