Rajesh C. Shah 1, Dilip B. Patel 2
1Department of Applied Mathematics, Faculty of Technology and Engineering, The M. S. University of Baroda, Vadodara, 390 001, Gujarat State, India
2Department of Mathematics, Sankalchand Patel College of Engineering, Visnagar, Gujarat State, India
Correspondence to: Rajesh C. Shah , Department of Applied Mathematics, Faculty of Technology and Engineering, The M. S. University of Baroda, Vadodara, 390 001, Gujarat State, India.
Email: |  |
Copyright © 2012 Scientific & Academic Publishing. All Rights Reserved.
Abstract
The present paper proposes the mathematical model of ferrofluid lubricated slider bearing with an inclined pad surface ( plate or pad ) including combined effects of porosity, anisotropic permeability, slip velocity at both the ends, and squeeze velocity under an oblique magnetic field. From the Reynolds’s equation of the above model, expressions for bearing characteristics like load capacity, friction on moving slider, coefficient of friction and centre of pressure are obtained which can be solved numerically to examine the exploration of its possible effects on the system. Various sizes of the porous matrix at both the ends are also discussed for the possible optimization of the bearing characteristics.
Keywords:
Mathematical Modeling, Ferrofluid, Porosity, Inclined Bearing, Anisotropic Permeability
Cite this paper:
Rajesh C. Shah , Dilip B. Patel , "Mathematical Modeling of newly Designed Ferrofluid Based Slider Bearing Including Effects of Porosity, Anisotropic Permeability, Slip Velocity at both the Ends, and Squeeze Velocity", Applied Mathematics, Vol. 2 No. 5, 2012, pp. 176-183. doi: 10.5923/j.am.20120205.05.
1. Introduction
Ferrofluid or Magnetic fluid[1] are stable colloidal suspensions containing fine ferromagnetic particles dispersing in a liquid, called carrier liquid ( in our case water ), in which a surfactant is added to generate a coating layer preventing the flocculation of the particles. When an external magnetic field is applied, ferrofluids experience magnetic body forces depends upon the magnetization of ferromagnetic particles. Owing to these features ferrofluids are useful in many applications like in sensors, sealing devices, filtering apparatus, etc.[2,3].Wu[4] in an innovative analysis , dealt with the case of squeeze film behaviour for porous annular disks in which he showed that owing to the fact that fluid can flow through the porous material as well as through the space between the bounding surfaces, the performance of a porous walled squeeze film can differ substantially from that of a solid walled squeeze film. Later[5] extended the above analysis[4] by introducing the effect of velocity slip to porous walled squeeze film with porous matrix appeared in the above plate. They found that the load capacity decreases due to the effect of porosity and slip. Prakash and Vij[6] investigated a porous inclined slider bearing without the effect of magnetic fluid and found that porosity caused decrease in the load capacity and friction, while it increased the coefficient of friction. Gupta and Bhat[7] found that the load capacity and friction could be increased by using a transverse magnetic field on the bearing and a conducting lubricant.With the advent of ferrofluid, Agrawal[8] studied its effects on a porous inclined bearing and found that the magnetizing of particles in the lubricant increased its load capacity without affecting the friction on the moving slider. Recently, many authors[9-17] have analysed effects of ferrofluid as lubricant in their study and found the increase of efficiency of the bearing performance over conventional from different viewpoints.In all above investigations, none of the authors considered both the porous plates in their study. The porous layer in the bearing is considered because of its advantageous property of self lubrication. With this motivation the study of behaviour of an inclined slider bearing with the porous matrix attached to both the plates (that is upper and lower) is proposed here with a ferrofluid lubricant under a magnetic field oblique to the lower surface. Also, effects of slip velocity and anisotropic permeability at both the porous plates, as well as squeeze velocity when the upper plate approaches to lower one are included. The ferrofluid flow model considered here is due to R. E. Rosensweig[1].A ferrofluid lubrication model is derived for the above problem and the various sizes of upper and lower porous matrix is considered for computation of various bearing characteristics like load capacity, friction, coefficient of friction and center of pressures. Also, above characteristics have been computed for two different cases of anisotropic permeabilities at upper and lower porous matrix. The ferrofluid used in the computations are water based.
2. Formulation of the Mathematical Model
A schematic diagram of the system under study is presented in Fig.1 consists of a ferrofluid film of thickness h within an inclined pad surface ( stator ) and a slider of length A in the x-direction and width B in y-direction, A<< B. The value of h is h2 at the inlet and h1 at the outlet. This film thickness h is given by | (1) |
The slider and stator both have attached porous matrix of thickness l2 and l1 ( metres ) respectively. Both the porous matrix are backed by a solid wall. The slider moves with a uniform velocity U in the x-direction. Also, stator moves normally towards the slider with a uniform velocity
, where t is time in seconds.The basic flow equations governing the above phenomenon based on R. E. Rosensweig model are given by[13]  | (2) |
 | (3) |
 | (4) |
 | (5) |
 | (6) |
where
are density, film pressure, fluid viscosity, fluid velocity, free space permeability, the magnetization vector, magnetic field vector and magnetic susceptibility respectively.By combining above equations (2) to (6) under the usual assumption of lubrication, neglecting inertia terms and that the derivatives of velocities across the film predominate, one- dimensional equation governing the lubricant flow in the film region yields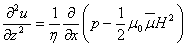 | (7) |
where u is the film fluid velocity in the x-direction and H is the magnetic field strength.Solving equation (7) under the slip boundary conditions given by Sparrow et.al.[5] and modified by Shah et.al.[14] with the addition of slider velocity U to[5]
when
,
when  | (8) |
where
being slip parameter ,
are porosities in the x- direction and
are permeabilities in the x- direction in the porous region, yields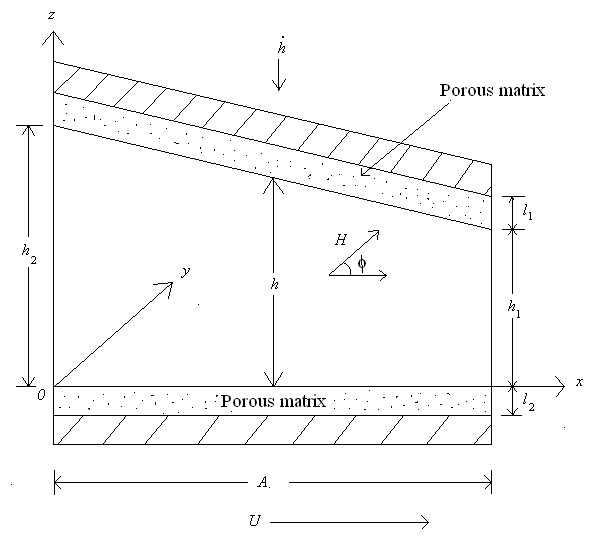 | Figure 1. Slider bearing with inclined pad surface |
 | (9) |
where
Substituting the above value of u in the integral form of continuity equation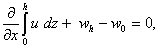 | (10) |
where w is the axial component of the fluid velocity in the film, one obtains | (11) |
Using Darcy’s law, the velocity components of the fluid in the porous matrix are given as follow:For upper porous region: | (12) |
 | (13) |
where
are fluid permeabilities in the upper porous region in x and z direction respectively, and P is the fluid pressure in the porous region.For lower porous region: | (14) |
 | (15) |
where
are fluid permeabilities in the lower porous region in x and z direction respectively, and P is the fluid pressure in the porous region.Substituting equations (12) and (13) in the continuity equation for upper porous region | (16) |
yields | (17) |
which on integration with respect to z across the upper porous matrix ( h, h+l1 ), one obtains | (18) |
using Morgan-Cameron approximation[6,11] and that the surface
is non-porous. Substituting equations (14) and (15) in the continuity equation for lower porous region | (19) |
yields | (20) |
which on integration with respect to z across the lower porous matrix (
l2, 0 ), one obtains | (21) |
using Morgan-Cameron approximation[6,11] and that the surface
is non-porous.Considering the normal component of velocity across the film porous interface are continuous, so that
, equations (18), (21) and (11) yields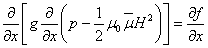 | (22) |
Where
which is the Reynolds’s type equation for the considered phenomenon.Here, magnetic field is considered to be vanish at the inlet and outlet of the bearing and inclined at an angle
with the x-axis. Thus,  | (23) |
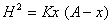 | (24) |
where K being a quantity chosen to suit the dimensions of both sides of equation (24). Such a magnetic field attains a maximum at the middle of the bearing producing magnetic pressure. On the other hand a constant field cannot produce magnetic pressure because (d / dx) H2 = 0. The direction of the magnetic field is significant since
has to satisfy the equations | (25) |
so
arises out of a potential and
satisfies the equation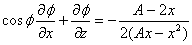 | (26) |
whose solution is determined from equations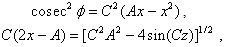 | (27) |
C being an arbitrary constant.Introducing the dimensionless quantities
equations (1) and (24) implies respectively
and
Also, equation (22) transforms to | (28) |
where
Equation (28) is known as dimensionless Reynolds’s equation.
3. Expressions of Bearing Characteristics
Since the pressure is negligible on the boundaries of the slider bearing compared to inside pressure, solving equation (28) under boundary conditions
when
.The dimensionless film pressure
is obtained as:
,where
The load carrying capacity W , friction on the moving slider F, coefficient of friction f and the x- coordinate of the centre of pressure
are expressed respectively in dimensionless forms as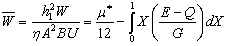


where 
4. Calculation of Results
The various bearing characteristics like load capacity, frictional force on the moving slider, the coefficient of friction and x- coordinate of centre of pressure are computed for various sizes of upper and lower porous matrix for
= 0.00001(m2),
= 0.001(m2) and for
= 0.001(m2),
= 0.00001(m2), using Simpson’s one third rule with step size 0.1, for the following values of the parameters :
,
,
(kgms-2A-2),
,
(A2m-4),
(m),
(m),
( kgm-1s-1),
(ms-1),
(ms-1),
(m).
5. Discussion of Results
The mathematical model of water based ferrofluid lubricated slider bearing with an inclined pad surface including combined effects of porosity, anisotropic permeability, slip velocity at both the ends, and squeeze velocity is proposed under an oblique magnetic field. The results of various bearing characteristics ( refer Section 3 ) are obtained for the various values of the parameters ( refer Section 4 ) are presented graphically as follows:From the Figs. 2-9 the following observations are made: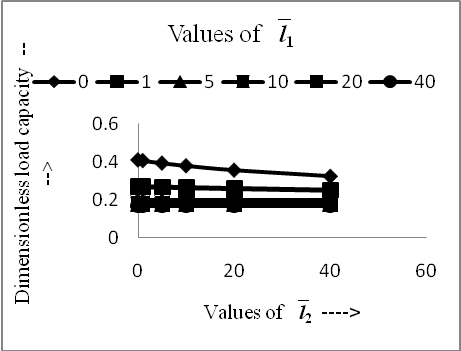 | Figure 2. Dimensionless load capacity for various values of and for = 0.00001, = 0.001 |
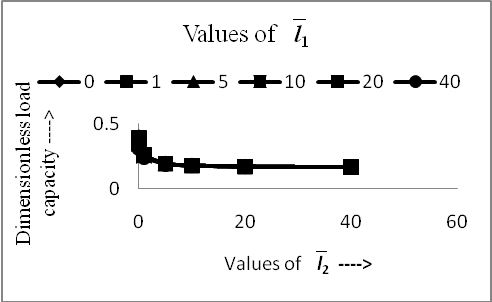 | Figure 3. Dimensionless load capacity for various values of and for = 0.001, = 0.00001 |
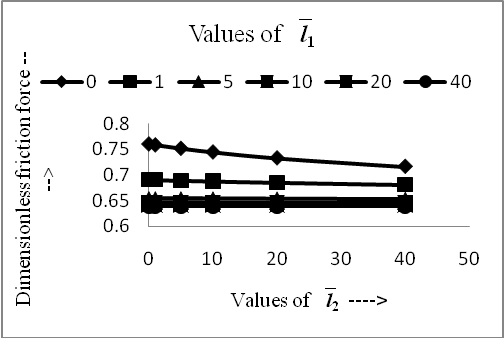 | Figure 4. Dimensionless friction force on the moving slider for various values of and for = 0.00001, = 0.001 |
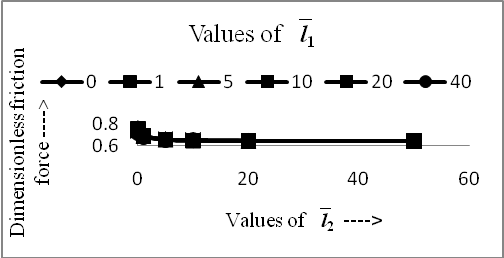 | Figure 5. Dimensionless friction force on the moving slider for various values of and for = 0.001, = 0.00001 |
(1) In Figs. 2 and 3, the dimensionless load capacity
for various values of lower porous matrix
and values of upper porous matrix
are displayed for the constant values of
= 0.00001,
= 0.001 and
= 0.001,
= 0.00001, respectively.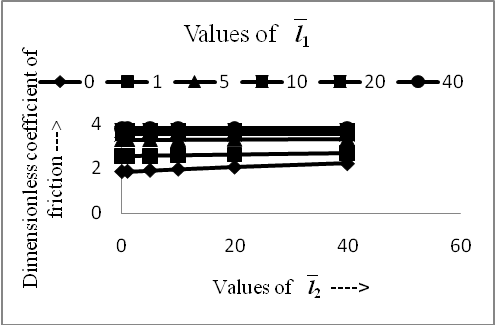 | Figure 6. Dimensionless coefficient of friction for various values of and for = 0.00001, = 0.001 |
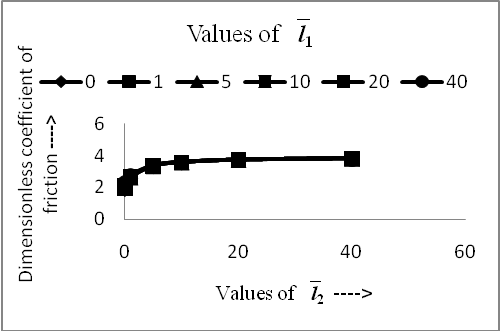 | Figure 7. Dimensionless coefficient of friction for various values of and for = 0.001, = 0.00001 |
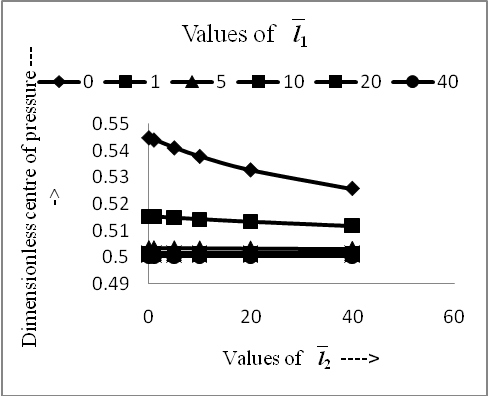 | Figure 8. Dimensionless the x –ordinate of the centre of pressure for various values of and for = 0.00001, = 0.001 |
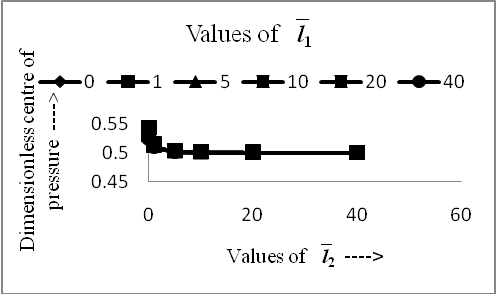 | Figure 9. Dimensionless the x –ordinate of the centre of pressure for various values of and for = 0.001, = 0.00001 |
It is observed from the Fig.2 that the dimensionless load capacity decreases with the increase of porous matrix thickness
as well as
.The decrease rate of load capacity is slow with respect to
. It is observed from Fig.3 that, the dimensionless load capacity decreases with respect to
but its behaviour is almost remains same with respect to
. The maximum dimensionless load capacity is obtained when
=
= 0 but with the disadvantage that the bearing has no self lubricating property. This behaviour of decrease in load capacity with the insertion of porous matrix also agrees with the conclusions of[5,6]. According to[5] the above trends for squeeze film bearing can be obtained because of the physical process as under :The presence of the porous medium provides a path for the fluid to come out easily form the slider bearing to the environment. The higher the permeability, the more readily does fluid flow through the porous material. Thus, the presence of the porous material decreases the resistance to flow in x – direction and as a consequence the load carrying capacity is reduced. The effect of velocity slip is to decrease the resistance encountered by the fluid flowing in the gap itself and, by this means, to diminish the load carrying capacity.(2) In Figs. 4 and 5, the dimensionless friction force on the moving slider F for various values of lower porous matrix l2 and values of upper porous matrix
are displayed for the constant values of
= 0.00001,
= 0.001 and
= 0.001,
= 0.00001, respectively. It is observed that the same behaviour is obtained for
as we have discussed in (1) for
with respect to
and
.(3) In Figs. 6 and 7, the dimensionless coefficient of friction
for various values of lower porous matrix
and the values of upper matrix
are displayed for the constant values of
= 0.00001,
= 0.001 and
= 0.001,
= 0.00001, respectively. It is observed that
increase with the increase of
and
.(4) In Figs. 8 and 9, the dimensionless x – coordinate of the centre of pressure Y for various values of lower porous matrix
and the values of upper porous matrix
are displayed for the constant values of
= 0.00001,
= 0.001 and
= 0.001,
= 0.00001, respectively.It is observed that the position of the centre of pressure does not affect much with respect to
and
.Also, one can obtain the following cases for the specific values of the parameters:(a) When l1= 0,
= 0, the case of[12] is obtained from equation (28) as
where
(b) When
=0, the non- ferrofluid case[6] is obtained from equation (28) as
where

6. Conclusions
The present paper proposes the mathematical model of water based ferrofluid lubricated slider bearing with an inclined pad surface including combined effects of porosity, anisotropic permeability, slip velocity at both the ends, and squeeze velocity under an oblique magnetic field. The results of various bearing characteristics are presented graphically. The porous layer in the bearing is considered because of its advantageous property of self lubrication. With this motivation the present study is proposed. Based upon the formulation in Section 2, and Results & discussion ( Section 4 and 5 ) the following conclusions can be made for designing slider bearing:(1) Because of having the self lubrication property of the porous plate bearings, it is suggested to have both the porous plate for better self lubrication.(2) Better load capacity is obtained when the thickness of l1 and l2 are small.(3) Small thickness of l2 has more influence on better load capacity when l1= 0 and
= 0.00001,
= 0.001 .(4) Small thickness of l1 has more influence on better load capacity when l2= 0 and
= 0.001,
= 0.00001 .(5) It should be noted that a constant magnetic field does not enhance the bearing characteristics in this model due to Rosensweig since
= 0 in equation (7).
References
[1] | R. E. Rosensweig, Ferrohydrodynamics, Cambridge University Press, New York, 1985. |
[2] | N. C. Popa, I. Potencz, L. Brostean, L. Vekas, Some applications of inductive transducers with magnetic fluids, Sensors and Actuators A , 59 (1997) 197-200. |
[3] | M. Goldowsky, New methods for sealing, filtering, and lubricating with magnetic fluids, IEEE transactions on Magnetics, Mag.- 16 (1980) 382-386. |
[4] | H. Wu, Squeeze-film behavior for porous annular disks, Journal of Lubrication Technology, Trans. ASME, Series F, 92(4) (1970) 593-596. |
[5] | E. M. Sparrow, G. S. Beavers, I. T. Hwang, Effect of velocity slip on porous walled squeeze films, Journal of Lubrication Technology 94 (1972) 260-265. |
[6] | J. Prakash, S. K. Vij, Hydrodynamic lubrication of a porous slider, Journal of Mechanical Engineering Science 15 (1973) 232-234. |
[7] | J. L. Gupta, M. V. Bhat, An inclined porous slider bearing with a transverse magnetic field, Wear 55 (1979) 359-367. |
[8] | V. K. Agrawal, Magnetic fluid based porous inclined slider bearing, Wear 107 (1986) 133-139. |
[9] | P. Sinha, P. Chandra, D. Kumar, Ferrofluid lubrication of cylindrical rollers with cavitation, Acta Mechanica 98 (1993) 27-38. |
[10] | P.Ram, P.D.S.Verma, Ferrofluid lubricated in porous inclined slider bearing, Indian journal of Pure and Applied Mathematics 30 (12) (1999) 1273-81. |
[11] | R. C. Shah, M. V. Bhat, Ferrofluid lubrication in porous slider bearing with velocity slip, International Journal of Mechanical Sciences 44 (2002) 2495-2502. |
[12] | R. C. Shah, M. V. Bhat, Magnetic fluid based porous inclined slider bearing with velocity slip, International journal of Applied Mechanics and Engineering 8 (2003) 331-336. |
[13] | R. C. Shah, M. V. Bhat, Analysis of a porous exponential slider bearing lubricated with a ferrofluid considering slip velocity, Journal of the Brazilian Society of Mechanical Sciences and Engineering 25 (2003) 264-267. |
[14] | R. C. Shah, M. V. Bhat, Ferrofluid lubrication equation for porous bearing considering anisotropic permeability and slip velocity, Indian Journal of Engineering & Material Sciences 10 (2003) 277-281. |
[15] | R. C. Shah, M. V. Bhat, Ferrofluid squeeze film between curved annular plates including rotation of magnetic particles, Journal of Engineering Mathematics 51 ( 2005) 317-324. |
[16] | H. Urreta, Z. Leicht, A. Sanchez, A. Agirre, P. Kuzhir, G. Magnac, Hydrodynamic bearing lubricated with magnetic fluids, Journal of Physics : Conference Series 149 ( 2009 ) 012113. |
[17] | R. C. Shah, D. B. Patel, Squeeze film based on ferrofluid in curved porous circular plates with various porous structure, Applied Mathematics 2 (4) (2012) 121-123. |