Zakirkhodja A. Tadjihodjaev1, Minira R. Sodikova2
1Tashkent Institute of Chemical Technology, Tashkent, Uzbekistan
2Tashkent Scientific Research Institute of Chemical Technology, Tashkent Region, Uzbekistan
Correspondence to: Minira R. Sodikova, Tashkent Scientific Research Institute of Chemical Technology, Tashkent Region, Uzbekistan.
Email: |  |
Copyright © 2024 The Author(s). Published by Scientific & Academic Publishing.
This work is licensed under the Creative Commons Attribution International License (CC BY).
http://creativecommons.org/licenses/by/4.0/

Abstract
Heterogeneous amphoteric membranes based on ionites obtained by polycondensation of secondary raw materials of the fat and oil industry and secondary products of polymer products containing ionogenic groups with binders of low-pressure polyethylene and chlorinated polyethylene were obtained and studied. The influence of the ratio of ionite to binder, time and temperature of rolling and pressing on the properties of the obtained membranes has been studied and optimal conditions for the production of heterogeneous ionite membranes have been established. The limits of tensile strength and elongation of membranes reinforced with synthetic fibers have been determined. It has been established that the synthesized membranes are characterized by high thermal stability in air, in water and chemical resistance in aqueous solutions of acids and alkalis.
Keywords:
Membrane, Amphoteric ionite, Polyethylene, Chlorinated polyethylene, Furfural, Exchange capacity, Mechanical strength
Cite this paper: Zakirkhodja A. Tadjihodjaev, Minira R. Sodikova, Synthesis and Study of Physico-Chemical Parameters of Heterogeneous Ionite Membranes, American Journal of Polymer Science, Vol. 13 No. 2, 2024, pp. 13-20. doi: 10.5923/j.ajps.20241302.01.
1. Introduction
The synthesis and production of polymer membranes has been studied for many years, but recently there has been increased interest in the study of membrane ionites. Ionite membranes are widely used in electrodialysis processes, for the desalination of brackish waters, for the separation of electrolytes from nonelectrolytes and other purposes. The ionite membrane is a polymer polyelectrolyte obtained in the form of a film with electrochemical activity, which consists in the fact that, while in an electrolyte solution, this film selectively passes ions of the corresponding charges.As is known, the following types of ion-exchange membranes are distinguished by structure: homogeneous, consisting of ion-exchange polymers; heterogeneous, containing mixtures of ion-exchange polymer (55-70% by weight) and film-forming polymer (binder); interpolymeric, consisting of a mixture of ion-exchange (15-30% by weight) and film-forming polymers (these membranes by properties and method of preparation they are close to homogeneous, but do not have chemical bonds between their constituent polymers).Heterogeneous ionite membranes are obtained by mixing finely ground ionite with a film-forming binder, followed by rolling, calendering and molding the mixture into thin films or sheets and pressing into them reinforcing meshes made of silk or acid- or alkali-resistant artificial fiber [1]. Since ion-exchange materials are heterogeneous, phenomena occurring at the boundaries of the "phases" are extremely significant for them. In such materials, the transfer is carried out through a system of pores and channels surrounded by a hydrophobic matrix of polymer materials impervious to ions and water. Secondary products of fat-and-oil production, which contain fatty acids consisting of a carboxyl end group and a long aliphatic chain, were chosen as the basis for ionite. Natural fatty acids contain at least 8 carbon atoms. The composition of fatty acids contains carboxylic acids such as capric acid (С10:0), lauric (С12:0), myristic (С14:0), palmitic (С16:0), stearic (С18:0), oleic (С18:1), linoleic (С18:2), arachinic (С20:0), eicosenic acid (С20:1), begene acid (С22:0) [2].Low-pressure polyethylene (LPP) and chlorinated polyethylene (CPE) were chosen as the binding agent for ionite membranes. Because chlorinated polyethylene is increasingly being used independently as an elastomer. The chlorine content in the polymer determines the properties of the final product, for example, CPE with a chlorine content of up to 14% exhibits the properties of a thermoplastic, with 15-23% the properties of elastoplast, 24-45% elastomer, 46-58% hard leather-like polymer, 59-70% chlorine exhibit the properties of a glassy polymer [3]. In a mixture with fillers and various additives, CPE is well processed by calendering and extrusion, can be crosslinked (vulcanized) by various methods. Products made from it are characterized by good weather resistance, stainability and low flammability. These qualities determine the prospects of using the material in the production of ionite membranes.
2. Main Body
2.1. Materials
For the synthesis of amphoteric ionite, a secondary product of fat–and-oil production was used – olein-palmitic fraction of cotton soapstock (OPF CS), which contains carboxylic acids. Synthesis tests and studies of amphoteric ionites based on polycondensation products of fat-and-oil waste from cotton production, polyethylene polyamine (PEPA) and furfural have been carried out [4]. Low-pressure polyethylene (LPP) and chlorinated polyethylene (CPE) were chosen as the binding agent for ionite membranes.
2.2. Methods
The fatty acid composition of the studied oils was determined by chromatography-mass spectrometric analysis of methyl esters of fatty acids (Figure 1). The analysis was carried out on a chromato-mass spectrometer «Agilent Technology» GС 7890В/МS 7000D, using a capillary column with a size of 30m×0.25mm× phase thickness of 0.25 mkm (stationary phase consists of 5% phenylmethylsiloxane and 95% dimethylpolysiloxane). The carrier gas is hydrogen (Figure 1).The IR spectra of the initial compounds and amphoteric ionite were studied using a Fourier spectrometer Bruker Invenio S-2021, in the interval 4000‒400 sm–1 ATR (Figure 2).The study of the thermal properties of synthesized ionites was carried out on a DTG-60 device manufactured by Shimadzu (Japan). The 5 mg sample was heated from 20 to 600°C at a heating rate of 10°C/min. The analysis was carried out in an atmosphere of inert gas – argon, at a feed rate of 80 ml/min. (Figure 3)Chlorination of polyethylene was carried out with chlorine gas in solution. The process was carried out at a temperature of 70-80°C, with exposure to UV rays for 5-6 hours. The chlorine content in the product is 15-20% [3]. For the synthesis of ionite, the process of polycondensation of secondary products of fat-and-oil production (SPFP) with amines, a secondary product of polymer products (SPPP) and furfural was carried out as follows: 5 mass parts was placed in a reactor equipped with a reverse refrigerator, devices for mixing, temperature measurement, heating and cooling. OPF CS and 5 mass parts SPPP, heat up to 60°C, turn on the stirrer, and gradually add 10 mass parts of polyethylene polyamine for 10 minutes. After achieving a homogeneous consistency of the reaction mass, 10 mass parts of furfural is added drop by drop and the temperature in the reactor is increased to 90-100°C. After stirring the reaction mass for 15 minutes at the same temperature, a gel-like, but still mobile mass is formed, which is poured into a baking tray and cured for 1.5 hours at 100°C and for 6 hours at 120°C. [4].Ionite membranes with a thickness of 0.8-1 mm were obtained by mixing powdered ionite with a particle size of no more than 50 microns with LPP or CPE in percentages of 75:25 on rollers. The rolling temperature was carried out at – 130-135°C, the pressing temperature was 130–135°C at 50MPa pressure. The preparation of membranes for testing was carried out according to a generally accepted method [5]. The membranes, washed and transformed into the desired shape, were stored in distilled water. The determination of physico-chemical properties was carried out in accordance with the interstate standards (GOST) № 20301, №. 20298 [6-7] for ion exchange resins. To determine the true strength of the membranes, the breaking force, conditional strength and elongation at break were measured according to state standard (GOST) №.270 on type «IV» samples on an AGS-X Shumadzu (Japan) breaking machine with a scale of 0-1000 kg at a moving clamp speed of 25 mm/min.
2.3. Results
The determination of the fatty acid composition of the studied oil was carried out by chromatography-mass spectrometric analysis, the analysis results are shown in table 1 and figure 1.Table 1. Olein-palmitic fraction of cotton soapstock of the test sample 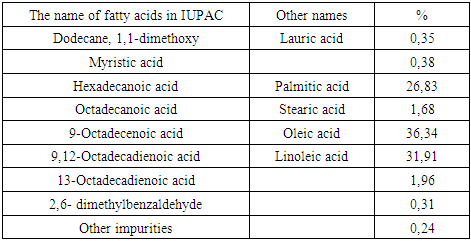 |
| |
|
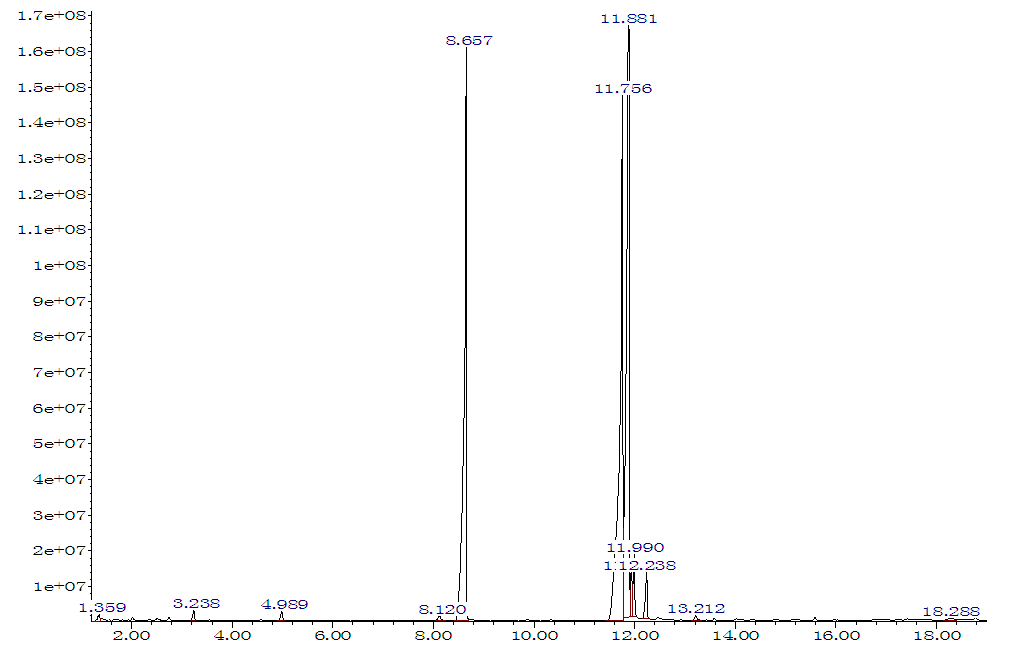 | Figure 1. Chromatography-mass spectrometric analysis of olein-palmitic fraction of cotton soapstock |
In order to obtain heat-resistant and chemically stable, mechanically strong heterogeneous membranes, we used ion-exchange resins containing furan and aromatic rings as an active component [4], which contributed to obtaining membranes with a number of valuable properties, such as a sufficiently high exchange capacity, mechanical strength, chemical and heat resistance (Table 2).Table 2. Physico-chemical and mechanical properties of synthesized ionites 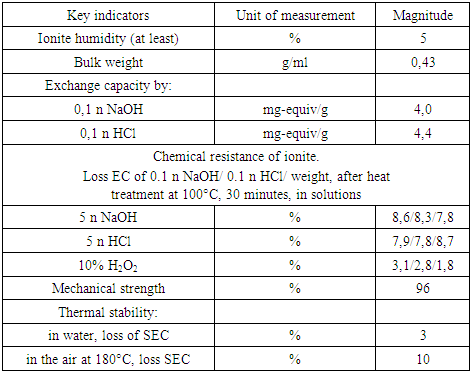 |
| |
|
The IR spectrum of amphoteric ionite (Figure 2) showed that an intense band is observed in the region of 1294 and 1254 cm-1 (which corresponds to OH deformation fluctuations), 1149 cm-1 – OH deformation fluctuations in the COOH groups. Absorption bands are also observed in the region of 924 and 970 cm-1, which corresponds to deformation fluctuations of OH in dimerized carboxyls. Thus, from the analysis of the spectra, it can be concluded that the synthesized ionite contains dimerized carboxyl groups, which makes it possible to exhibit cationic abilities in amphoteric ionite. Absorption bands were also identified in the region of 1634 and 1556 cm-1, which, according to the literature data [7], can be attributed to deformation vibrations of secondary amino and amide groups. Thus, it can be concluded that the synthesized ionite contains secondary and tertiary amino groups, which makes it possible to exhibit anionic abilities in amphoteric ionite.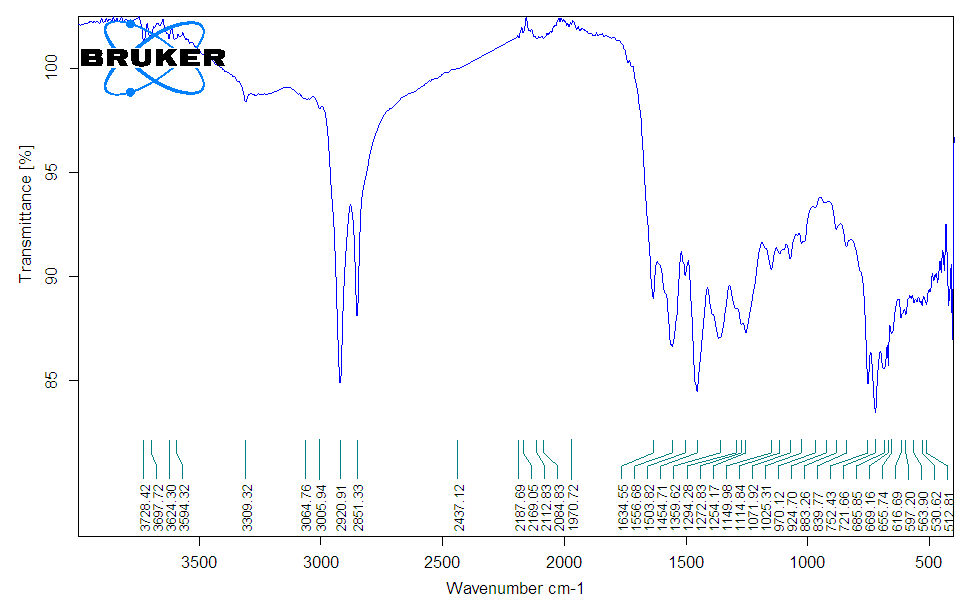 | Figure 2. IR spectrum of amphoteric ionite |
Thermograms were taken to determine the melting point of the binder polymers (Figure 3). The melting temperatures for LPP are 130°C, and for CPE – 122°C. These data are necessary for the rolling process, since rolling of heterogeneous membranes with a binder based on LPP and CPE was carried out at 10-15°C above the melting point of polymers.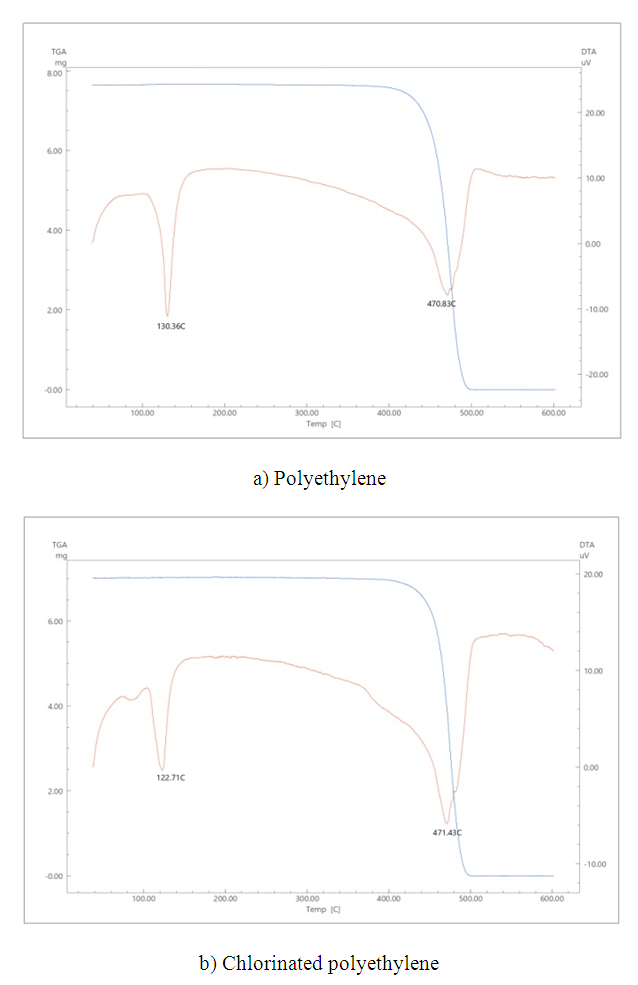 | Figure 3. TGA analysis of binding polymers |
The strength and service life of ionite membranes are enhanced by reinforcement with various materials. Synthetic fabrics and nets are usually used as reinforcing material. Reinforcement with synthetic fabrics ensures the creation of large-sized high-strength ionite membranes capable of working for a long time without mechanical transformations, improves transportability and simplifies their storage methods. The effect of the type of reinforcing material on the properties of membranes was studied on samples obtained from membranes. Polyamide fiber - nylon and polyester fiber – polyester was used as reinforcing material. The density of these synthetic fibers is almost the same, the melting point of polyamide fibers is slightly lower [8]. Comparative data on the properties of non-reinforced and reinforced membranes are shown in Table 3.Table 3. The effect of reinforcing material on the mechanical properties of synthesized membranes 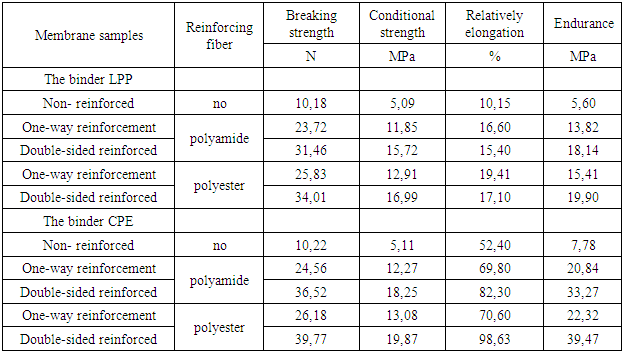 |
| |
|
To determine the chemical resistance, membrane samples were treated at a temperature of 100°C with 5n solutions of H2SO4 and NaOH for 30 minutes, and in a 10% solution of hydrogen peroxide they were kept for 24 hours. The results of these tests indicate the thermal and chemical stability of the obtained membranes. A decrease in the exchange capacity of all membranes (up to 8%) is observed after exposure to a 10% solution of hydrogen peroxide (Table 4).Table 4. Chemical and thermal stability of ionite membranes 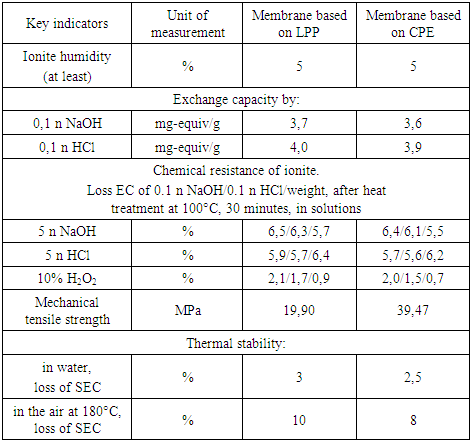 |
| |
|
2.4. Discussions
The study of the effect of the ratio of the initial components on the properties of the obtained membranes showed that the properties of heterogeneous membranes depend mainly on the ratio of the ionite component and the binder. The content of the ionite component in the membrane ranges from 60-75%. With an increase in its content above 75%, along with an increase in the exchange capacity, a significant decrease in the conditional strength of the membranes is observed. In order to study the effect of the amount of binder on the properties of membranes, the ion exchange component-binder ratios were used in percentages from 60/40 to 85/15 (Table 5). With an increase in the amount of binder to 40%, the conditional strength of the membranes increases, but the exchange capacity decreases (Figure 4).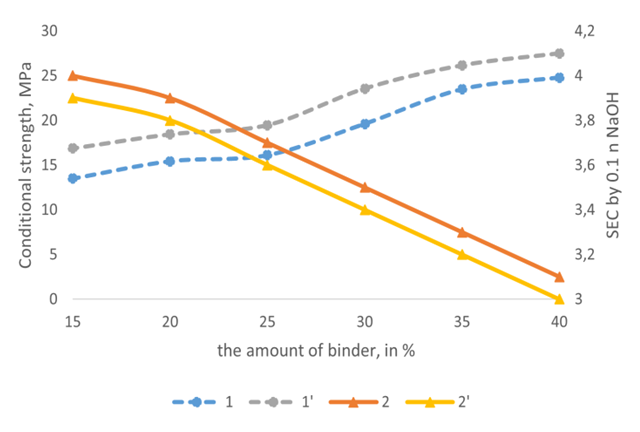 | Figure 4. Dependence of conditional strength (1-1') and exchange capacity (2-2') of heterogeneous membranes. 1-2 LPP binding component, 1'-2' CPE binding component |
With a decrease in the amount of binder to 30%, the exchange capacity of the membranes increases, but the mechanical strength decreases slightly due to a decrease in the amount of binder polymer that gives the membrane strength (Table 5). The use of products in percentages of 75:25 leads to the production of heterogeneous membranes with sufficiently high exchange capacity and mechanical strength.Table 5. Dependence of the properties of amphoteric heterogeneous membranes on the amount of LPP or CPE injected (membrane thickness 1 mm) 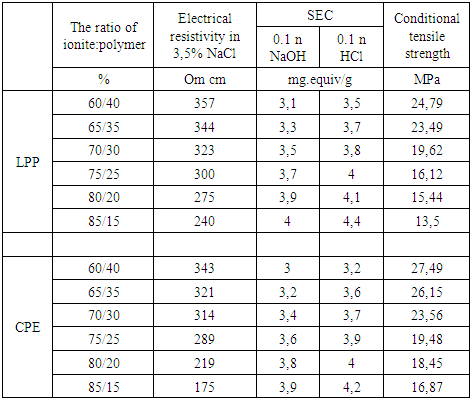 |
| |
|
The study of the influence of temperature and duration of rolling has shown that the properties of membranes are greatly influenced by the rolling process. Which is carried out in order to homogenize the mass by softening the binder and then obtaining a membrane in the form of sheets. Rolling of compositions containing ionite and binder was carried out in the temperature range 125-140°C.An increase in the rolling temperature to 140°C slightly increases the mechanical strength, however, it reduces the SEC index. At temperatures below 120-130°C, the masses are not rolled due to an insufficient degree of softening of the binder polymer. Rolling the mass at a temperature of 135°C (for LPP) and 130°C (for CPE) leads to the production of membranes with sufficiently high exchange capacities (Table 6).Table 6. Effect of rolling temperature on membrane properties (time 20 minutes, ionite ratio:binder – 75:25%) 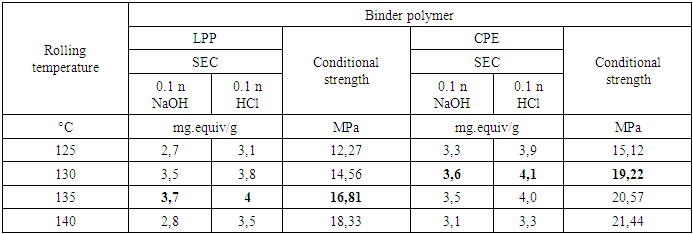 |
| |
|
The study of the effect of rolling duration on the conditional strength showed that rolling from 5 to 10 minutes at a temperature of 135°C/130°C has a slight effect on the properties of membranes. Rolling for 15-20 minutes at a temperature of 135°C/130°C slightly increases the conditional strength, lowers the electrical resistivity, which is associated with an increase in mass density, an increase in the degree of homogenization and mechanochemical processes occurring during rolling (Figure 5). Increasing the rolling time to 25 minutes at a temperature of 135°C/130°C or more worsens the elasticity of the membrane.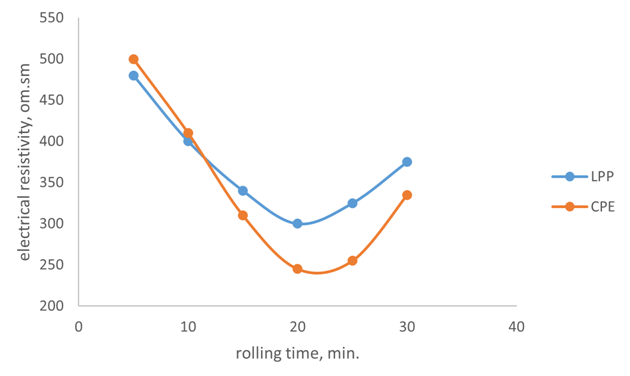 | Figure 5. The effect of rolling duration on specific volumetric electrical resistance |
The properties of membranes are also greatly influenced by the pressing process, which is carried out in order to strengthen and reinforce the membrane sheets. The resulting membrane sheets were pressed with a reinforcing material made of synthetic (polyamide or polyester) fabric. Pressing between polished metal plates using foil substrates gives the membranes a smooth surface, seals the material, eliminates microcracks that can form during rolling (calendering).Table 7. Influence of pressing temperature on membrane properties (time - 10 minutes) 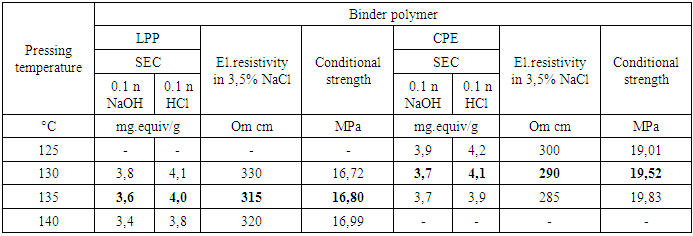 |
| |
|
The study of the dependence of membrane properties on the pressing temperature showed that at 120°C the mass does not soften or press, and an increase in the pressing temperature to 140°C and above leads to an increase in the fragility of the membranes due to an increase in the degree of crosslinking and the possibility of destructive processes under these conditions. Membranes with good mechanical strength were obtained by pressing at temperatures of 135°C for HDPE and 50 MPa for CPE 130°C. (Table 4). When pressing for less than 10 minutes, the mass does not have time to fill the mold cavity, and an increase in the pressing time of more than 10 minutes is associated with the possibility of destructive polymer processes.The effect of the reinforcing material on the mechanical properties of synthesized membranes was studied (Tables 3). From the data of the comparative table, it can be seen that the mechanical tensile strength of membranes reinforced with synthetic fibers increases by 3-5 times. In addition, polyester fiber reinforced membranes are more resistant to aggressive environments. As tests have shown, reinforcement with synthetic fibers increases mechanical strength, but slightly reduces the exchange capacity. This is due to the fact that the reinforcing fabric shields part of the membrane cross-section, and also reduces the swelling and moisture capacity of the membranes. Therefore, one-sided reinforcement or reinforcement in the middle of the sheet was used. However, the one-sided reinforcement of the membrane became uneven, curved and collapsed when swelling in water. Reinforcement of membranes in the middle of the sheet is associated with technological difficulties, since the symmetrical arrangement of membrane layers is not achieved. Therefore, double-sided reinforcement of membranes with synthetic fabrics was used.As can be seen from the data in Table 3, the tensile strength of samples in which the CPE binder is slightly higher than that of LPP. This is due to the fact that CPE is much more elastic and the rates of rupture deformation are much higher than LPP (Figure 6):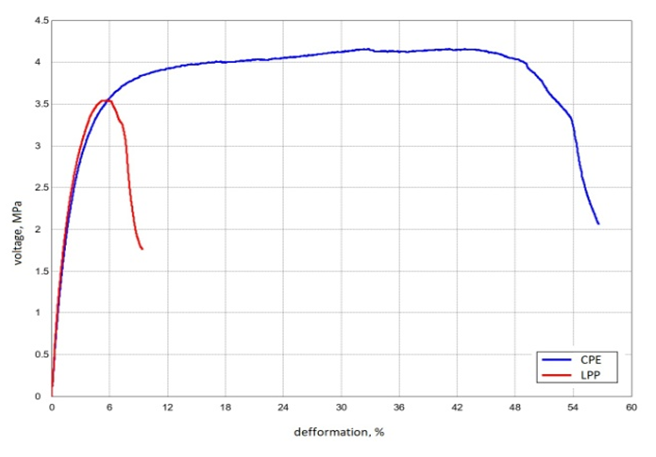 | Figure 6. Graph of the dependence of the breaking stress on the breaking strain during the tensile test |
The tensile stress values of the samples with CPE are 3.98 MPa, the tensile strain reaches 49.15%, under the same conditions, the tensile stress values of the sample with LPP are 3.4 MPa, and the deformation is much lower – 6.74%. It follows from this that CPE-based membranes have better mechanical strength indicators, and due to deformation they are more elastic and wear-resistant.The chemical stability of ion-exchange materials is one of the important indicators in assessing their properties. It is known that the action of alkali and acid solutions on some ion-exchange materials, especially at high temperatures, causes their destruction, leads to side processes, additional crosslinking, branching and other undesirable processes. When ion-exchange materials, especially polycondensation materials, come into contact with oxidants, there is a significant change in the physico-chemical properties of ion-exchange materials. Therefore, the study of the chemical stability of ion-exchange materials is of interest for solving the problem of the synthesis of ion-exchange materials with the necessary properties, the possibility of determining in advance the fields of application, the conditions of their operation and storage. The chemical stability of the obtained membranes was assessed by changes in the exchange capacity of the membranes. As can be seen from comparative tables 2 and 4, the exchange capacity of ionite and membrane ionite after contact with oxidants are slightly different, that is, the loss of exchange capacity in membrane ionites is slightly lower, this is due to the presence of a polymer framework in membrane ionite. It can also be observed that the membrane with a CPE binder has SEC indicators slightly lower, but the chemical resistance indicators have improved by almost 2%, the mechanical tensile strength is 2 times greater, and with thermal stability, the loss of SEC has decreased.
3. Conclusions
• By combining amphoteric ionites obtained by polycondensation of secondary raw materials of the fat and oil industry and secondary products of polymer products containing ionogenic groups with LPP and CPE binders, heterogeneous membranes characterized by high mechanical strength, chemical and thermal resistance were obtained and studied;• The scope of application of a chlorinated polymer as a binder for the production of ion-exchange membranes is considered, which made it possible to approach the development of ion-exchange membranes of a new type;• The influence of the ratio of ionite to binder, time and temperature of rolling and pressing on the properties of the obtained membranes has been studied and optimal conditions for the production of heterogeneous ionite membranes have been established;• It has been established that the synthesized membranes are characterized by high thermal stability in air, in water and chemical resistance in aqueous solutions of acids and alkalis.
References
[1] | Sodikova M.R. Ionoobmennyye materialy: obzor, syr’yo, sintez, primenenie, texnologii, utilizatsiya, identifikatsiya i kodirovaniye [Ion exchange materials: overview, raw materials, synthesis, application, technologies, disposal, identification and coding]. LAP LAMBERT Academic Publishing. Language, Russian. 2023, 124. ISBN-10, 6206755371. |
[2] | Fatxullaev E., Djalilov A.T. eds. Kompleksnoe ispol’zovaniye vtorichnykh produktov pererabotki khlopchatnika pri poluchenii polimernykh materialov [Complex use of secondary cotton processing products in the production of polymer materials]. Tashkent, Fan Publ., 1988, 144. |
[3] | Abdumavlyanova M.K., Sodikova M.R. Vtorichnyye polimernyye materialy: Utilizatsiya, modifikatsiya, vtorichnaya pererabotka, primeneniye v poluchenii kompozitsionnykh materialov [Secondary polymer materials: Recycling, modification, recycling, application in the production of composite materials]. LAP LAMBERT Academic Publishing. Language, Russian. 2023, 104. ISBN-10, 6206164039. |
[4] | Sodikova M.R. Cintez, issledovanie i spektrometricheskaya identifikatsiya amfoternyx ionitov na osnove vtorichnogo syrya [Synthesis, research and spectrometric identification of amphoteric ionites based on secondary raw materials]. Kompozitsionnyye materialy. Uzbekskiy Nauchno-texnicheskiy i proizvodstvennyy jurnal. 2024, (2), 58-63. |
[5] | Nesterov Yu.V. Ionites and ion-exchange. Sorption technology during the mining of uranium and other metals by in-situ leaching. — Moscow, 2007, 392. |
[6] | GOST №20301-1974. Ion-exchange resins. Anionites. Specifications, Moscow, Gosstandart Publ., 1974, 24. |
[7] | GOST №20298-1974. Ion-exchange resins. Cation exchangers. Specifications, Moscow, Gosstandart Publ., 1974, 15. |
[8] | GOST 51626-2000 Chemical (synthetic) fibres. Safety requirements. Moscow, Gosstandart Publ., 2000, 38. |
[9] | Tarasevich B.N. IK spektrы osnovnykh klassov organicheskix soedineniy. Spravochnyye materialy [The IR spectrum of the main classes of organic compounds. Reference materials], Moscow, 2012, 55. |