Ilyos Majidovich Maxmudov1, Ravshan Irkinovich Adilov2, Muzafar Ganiyevich Alimuhamedov2
1Applicant, Tashkent Institute of Chemical Technology, Tashkent, Uzbekistan
2Doctor of Technical Sciences, Professor, Tashkent Institute of Chemical Technology, Tashkent, Uzbekistan
Copyright © 2024 The Author(s). Published by Scientific & Academic Publishing.
This work is licensed under the Creative Commons Attribution International License (CC BY).
http://creativecommons.org/licenses/by/4.0/

Abstract
Composite panels are integral components in various industrial applications, necessitating continuous improvements in their physical and mechanical properties. This study investigates methods to enhance these properties specifically at the Shurtan Gas-Chemical Complex, focusing on the incorporation of both primary and secondary polyethylene granules from diverse brands. The research employs a comprehensive approach involving experimental analyses encompassing mechanical testing and material characterization to optimize the composition of composite panels. The primary objective is to achieve superior performance characteristics while concurrently ensuring the production of high-quality liquid products. By systematically varying the types and proportions of polyethylene granules, the study evaluates their impact on critical parameters such as tensile strength, impact resistance, and thermal stability. The findings underscore the effectiveness of this approach in significantly improving the overall quality and functionality of composite panels. The research contributes valuable insights into advancing manufacturing processes within the gas-chemical industry. It underscores the feasibility of integrating various polyethylene sources to enhance product durability, sustainability, and economic viability. Ultimately, this work seeks to inform and guide future developments in composite panel production, aiming to meet evolving industrial demands for robust and versatile materials.
Keywords:
Polyethylene, Density, Yield index, Tensile strength, Shore hardness, Fraction composition
Cite this paper: Ilyos Majidovich Maxmudov, Ravshan Irkinovich Adilov, Muzafar Ganiyevich Alimuhamedov, Development of the Technology of Obtaining the Inner Layer of Composite Panels on the Basis of Polyethylene in the “Shurtan Gas Chemical Complex”, American Journal of Polymer Science, Vol. 13 No. 1, 2024, pp. 6-11. doi: 10.5923/j.ajps.20241301.02.
1. Introduction
Currently, the production of polymer composite materials occupies an important place in global industry. As you know, today it is very difficult to imagine the construction industry without three-layer composite panels. There are several examples of this, one of the main reasons for this is the wide range of physical and mechanical properties and advantages of this product. Today we are witnessing the use of three-layer composite panels in various fields, for example, exterior decoration of ventilation systems, facades of new and reconstructed buildings, cladding of balconies, cornices and canopies, cladding of gas stations, tunnels and pillars, various special and non-standard objects, etc. These can offer a long service life (50 years), insulation and protection, ease of processing, availability of various colors, etc.In the Republic of Uzbekistan over the past few years, a number of enterprises have been formed for the production of aluminum plastic profiles - various finishing materials used for interior and exterior decoration of buildings. For example, “ALCO”, “ALSTAR”, “AND-POLIC”, “ALUCOBOND” and others. Three-layer composite panels are in great demand for finishing the exterior facades of new and reconstructed buildings.The purpose of this article is to improve the physical and mechanical properties of three-layer composite panels produced at Shurtan gas chemical complex using primary and secondary polyethylene granules and to obtain highly marketable products.
2. Objective
The aim of the study is to create a technology for the production of three-layer composite panels and the production of an inner polymer layer based on secondary raw materials produced in Shurtan GCC, determine the optimal formulation, polymer grades, select the technological mode and improve the physical and mechanical characteristics of a three-layer composite panel.Today, all manufacturers in the Republic of Uzbekistan use different grades of polyethylene from Shurtan GCC for the production of three-layer composite panels. Shurtan Gas Chemical Complex produces 16 grades of polyethylene with a density of 0.918 to 0.965 g/sm³, and a flow rate of 0.19 to 30 g/10 min. About 130 thousand tons of polyethylene granules are produced annually, of which more than 30-35% is used for the production of three-layer composite panels.
3. The Experimental Part
The technological process of the three-layer composite panel uses secondary grades of polyethylene. For the application of secondary grades of polyethylene and the production of highly liquid products, different grades of secondary raw materials are used. Linear polyethylenes of the LLDPE, MDPE and HDPE grades which are produced by "Shurtan GCC" LLC were selected as a matrix for filling (Table 1).Table 1 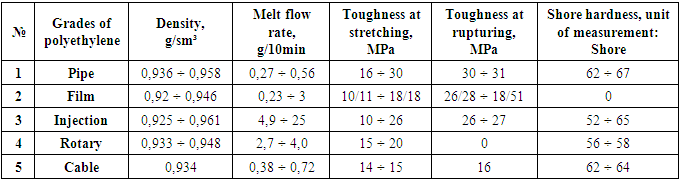 |
| |
|
In the article, I would like to focus on the preparation of samples, the formulation of raw materials and the results obtained.
4. Experimental Results and Their Discussion
In order to fulfill the tasks set, samples of composite panels were obtained to determine the optimal formulation based on different grades of polyethylene, the choice of technological mode and physico-mechanical characteristics. At the same time, to regulate the physical and mechanical properties and suffocation, local raw materials were introduced into the formulation of the middle layer of the panels - natural calcium carbonate from Kitab and Yangiyul mines. The fractional composition, volumetric weight and specific volume of fillers are presented in Tables 2 and 3.Table 2. Fractional composition of calcium carbonate 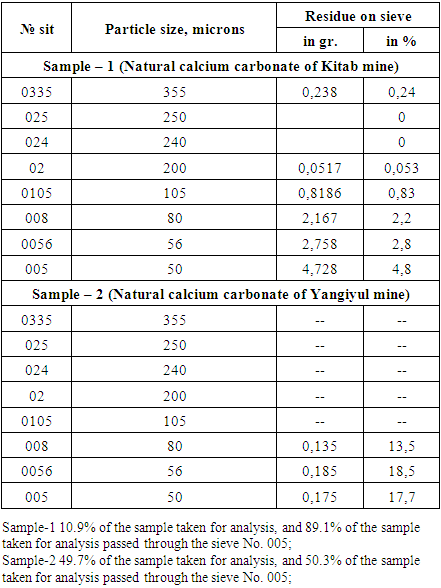 |
| |
|
Table 3. Volumetric weight and specific volume of fillers  |
| |
|
Calcium carbonate as a filler of polymer materials has such advantages as wide variation of particle sizes and particle size distribution, ease of applying various coatings to the surface of particles to improve the rheological properties of filled polymer materials and resistance to temperatures up to 550°C. To determine the most rational method of processing the source material and the resulting compositions, a melt flow index test was performed using method A according to GOST 11645-2021 with a load of 2.16 kg and a temperature of 190°C (Table 4).Table 4. Melt flow rate of the resulting compositions and starting polymer material 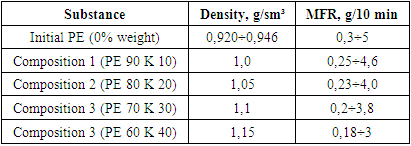 |
| |
|
With a filler content of 40 wt. % there is a decrease in the MFR value by 0.6 times compared to the MFR of the original polymer. With a subsequent increase in filler content by 10 wt. % and 20 wt. The % melt flow rate expectedly continued to decrease from 4.6 and 4.0 g/10 min, respectively, compared to the MFR of the original polymer material.But to assess the technical properties of materials, only the MFR value is not enough, because to a greater extent the conclusion is based on the physical and mechanical properties of the compositions. In the process of manufacturing and testing samples of three-layer composite panels on technological equipment, the influence of different grades of polyethylene on their properties was studied (Tables 5-7).Table 5. Melt flow rate of the resulting compositions 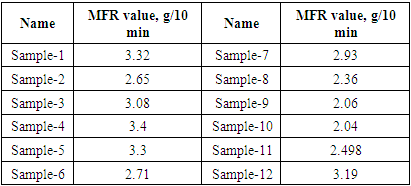 |
| |
|
Table 6. Density of the resulting compositions 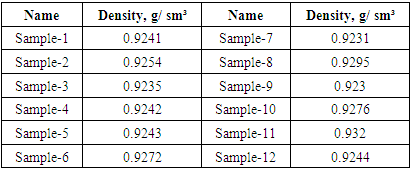 |
| |
|
Table 7. The composition of the inner layer of polyethylene for the production of three-layer composite panels 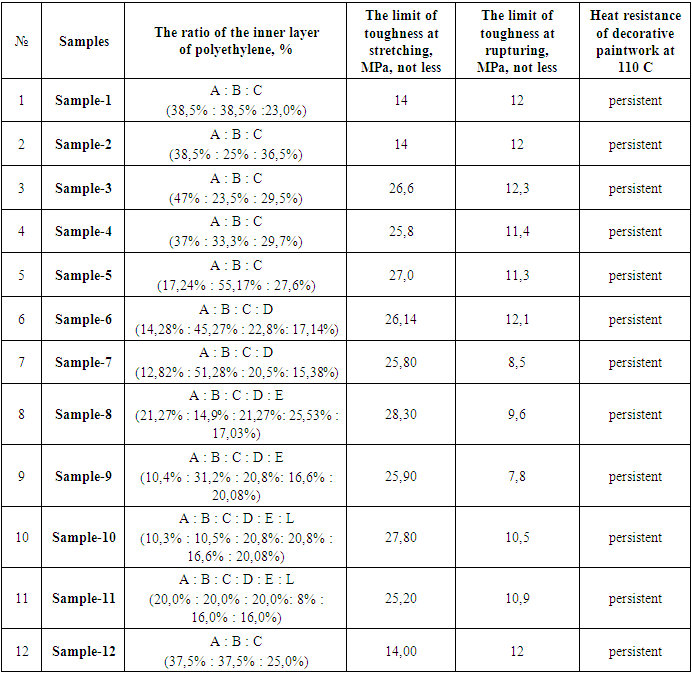 |
| |
|
The polyethylene grades used are encrypted A, B, C and others. The dimensions of the manufactured products are equal to – 1220 x 2440 x 4mm.According to the Table, the following graphical dependencies were obtained, shown in Fig. 1, 2.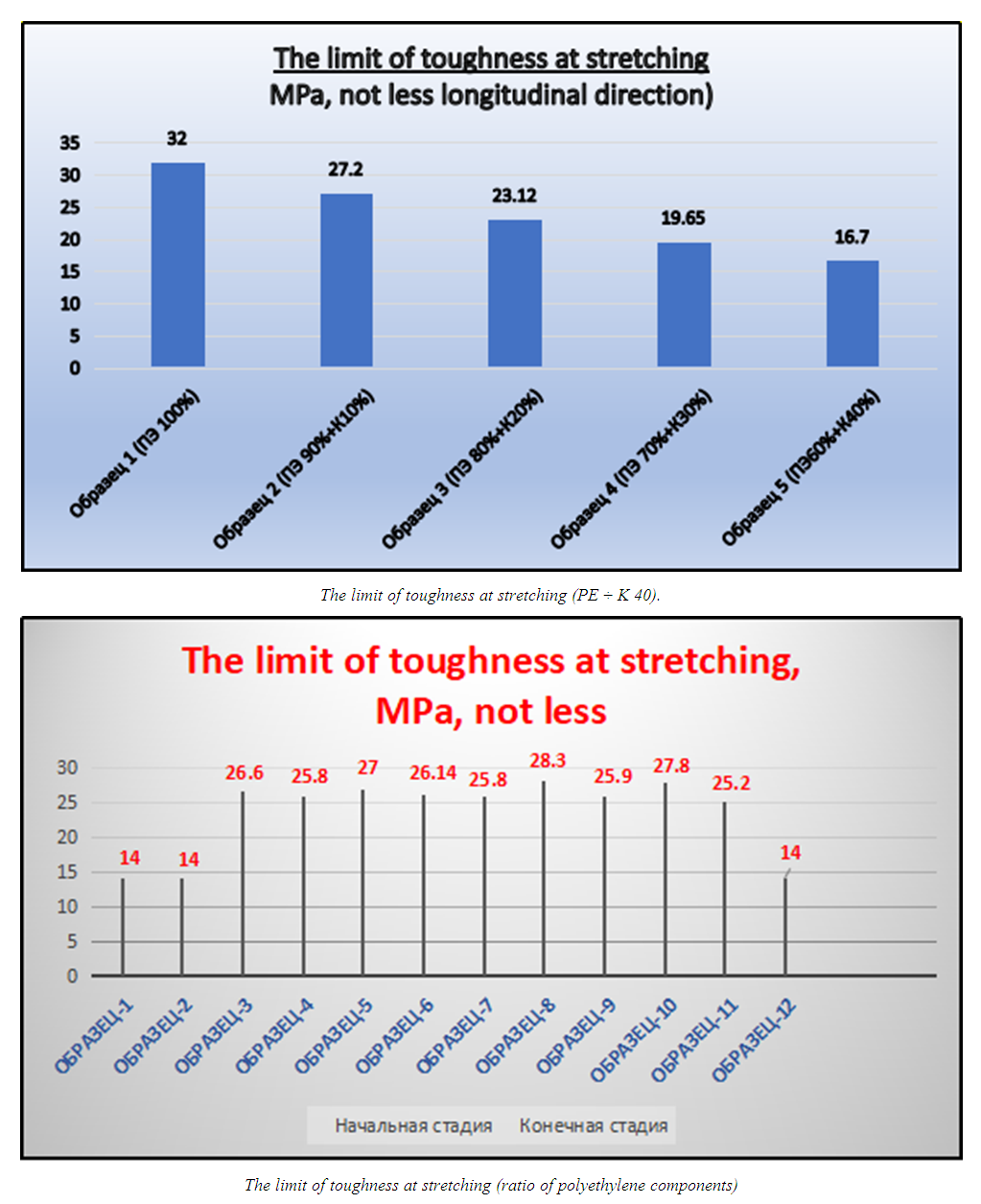 | Figure 1 |
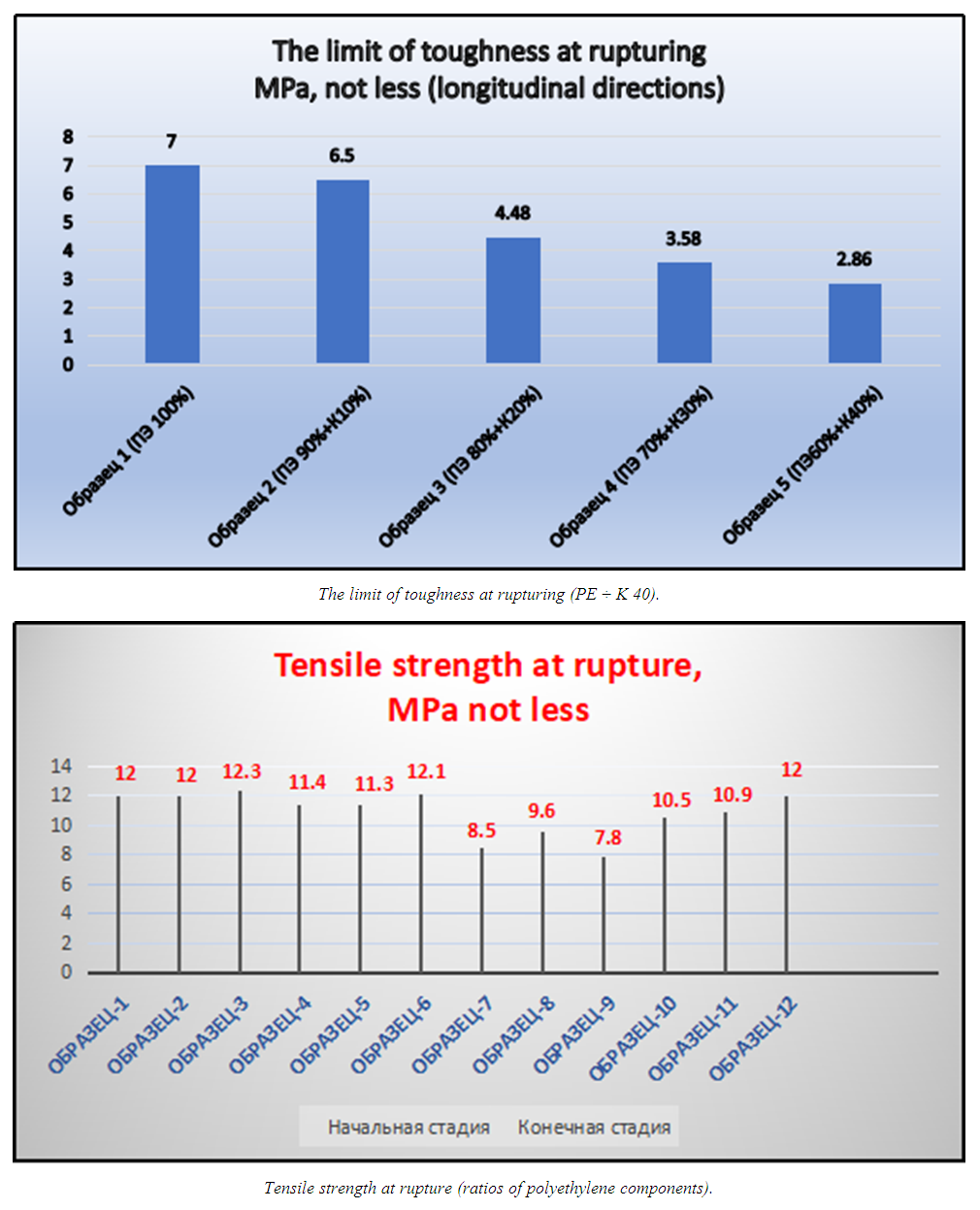 | Figure 2 |
5. Conclusions
The main purpose of the work is to determine the optimal formulation of polyethylene grades of Shurtan GCC for the production of three-layer composite panels and analyze the selection of the technological regime, as well as to improve the physical and mechanical properties of the produced three-layer composite panels. Based on production factors (technological mode of equipment) and laboratory tests, we have determined:To produce three-layer composite panels, it is necessary to use injection grades of primary and secondary grade polyethylene;1) The composition of injection grades should not exceed 14% to 16%.2) In the production cycle of secondary grades of polyethylene granules, it is not required to use mineral additives such as calcium carbonate.The use of recycled polyethylene allows not only the use of local raw materials, in addition to obtaining highly liquid products, but also will attract new jobs and profits due to new products.
References
[1] | GOST 11262-80-“Plastics. Tensile test method”. |
[2] | O'zDST 936:2004 – “Household products from plastic masses”. |
[3] | Makhmudov, I. M., Adilov, R. I., & Alimukhamedov, M. G. (2024). Physico-mechanical properties of three-layer composite panels based on polyethylene produced by Shurtan gas-chemical complex. In Prospects for the creation of thermosetting oligomers, utilization of polymer waste, polyfunctional compounds and polymer materials based on them (pp. 345-347). Paper presented at the conference held on January 18-19, 2024, in Tashkent. |
[4] | Makhmudov, I. M., Adilov, R. I., & Alimukhamedov, M. G. (2023). Development of technology for obtaining the inner layer of three-layer composite panels based on polyethylene produced by Shurtan gas-chemical complex. Oriental Renaissance: Innovative, educational, natural and social sciences, 3(10), 149-159. |
[5] | Makhmudov, I. M., Begamov, Sh. T., Adilov, R. I., & Alimukhamedov, M. G. (2022). The development of technology for obtaining the inner layer of three-layer compositional panels on the basis of polyethylene produced at Shurtan GCC. *Actual Problems of Innovation Technologies in the Development of Chemical, Oil and Gas Processing and Food Industries, Tashkent, November 25, 2022, 61-62. |
[6] | Alucom. (n.d.). Ob aliuminievykh kompozitnykh panelyah [About aluminum composite panels]. Retrieved June 23, 2024, from https://alucom.ru/articles/zarubej_opit/ob-alyuminievyh-kompozitnyh-panelyah1. |
[7] | Makhmudov, I. M., Sultanov, N. J., Rakhmonov, G. K., & Abdurashidov, T. R. (2012). Features of technological and modification of aluminum composite panels. *Innovative Technologies*, 1(5), 24-27. |
[8] | Lipatov, Yu. S. (1991). *Physico-chemical bases of polymer filling*. Moscow: Publisher. |
[9] | Kryzhanovsky, V. K., Bulatov, V. V., Panimatchenko, A. D., & Kryzhanovsky, Yu. V. (2003). *Technical properties of polymer materials*. St. Petersburg, Russia: Professiya. |