Md. Ibrahim H. Mondal , Md. Mofakkharul Islam , Md. Khademul Islam , Md. Firoz Ahmed
Department of Applied Chemistry & Chemical Engineering, Rajshahi University, Rajshahi, Bangladesh
Correspondence to: Md. Ibrahim H. Mondal , Department of Applied Chemistry & Chemical Engineering, Rajshahi University, Rajshahi, Bangladesh.
Email: |  |
Copyright © 2016 Scientific & Academic Publishing. All Rights Reserved.
This work is licensed under the Creative Commons Attribution International License (CC BY).
http://creativecommons.org/licenses/by/4.0/

Abstract
Dyeing behaviour and colour fastness characteristics of bleached, acrylamide and acrylic acid modified jute fibres dyed with reactive dyes, namely Reactive Red 120, Reactive Blue 5, Reactive Orange 14 and Reactive Brown 10 in aqueous medium were investigated. Dye absorption were greatly affected by the parameters variables, and depended on the dye and fibre characteristics. The effective dye absorption of each dye was determined. Grafting of acrylamide and acrylic acid increased the hydrophobic nature of bleached jute fibre and hence, affected the dye absorption. Grafting improved the sunlight, wash, alkali and organic acid fastness characteristics of modified dyed jute fibre. It also reduced the strength loss of the dyed fibre on exposure to sunlight in air, in which the dye particles normally enhanced photo-oxidative degradation by absorbing UV of sunlight.
Keywords:
Jute fibre, Grafting, Dyeing, Reactive dyes, Colour fastness
Cite this paper: Md. Ibrahim H. Mondal , Md. Mofakkharul Islam , Md. Khademul Islam , Md. Firoz Ahmed , Dyeing Behaviour and Colour Fastness Characteristics of Bleached, AM- and AA-modified Jute Fibres Dyed with Reactive Dyes, American Journal of Polymer Science, Vol. 6 No. 2, 2016, pp. 39-45. doi: 10.5923/j.ajps.20160602.02.
1. Introduction
Jute is a ligno-cellulosic fibre which contains, mainly cellulose, hemi-cellulose, lignin and some other minor constituents. Due to the complex structure of jute fibre, it has some inherent drawbacks, e.g. courseness, rigidity, photo-yellowing, poor colour fastness, etc. which seriously limits it general use, especially, for textile purposes. Again, photo unstability is one of the major disadvantages of jute fibre to be used as a textile fibre. Among all the cellulosic fibres jute occupied the second place as regards extent of use and volume of production. However the invention of synthetic materials and their wide use with long durability and pleasing appearance is caused to contract the use of jute and jute goods. To utilize jute in a better way it is therefore urgently necessary to make the fibre properties acceptable as a textile material by chemical modification as well as to improve its fastness characteristics. Again, the colour of dyed jute is expected to withstand those agencies, like exposure to sunlight, weather, moisture, washing, etc, which it is likely to meet in use to a reasonable degree. Most of the jute dyer’s requirements can be met by dyestuffs of basic, acid and direct which are suitable for application, but possess low colour fastness [1, 2]. Acid and some direct dyestuffs lack sufficient affinity on jute. Mondal et al. [3] studied the effect of disperse dyes on the strength of jute fibre. They also reported improved colour fastness characteristics of direct dyed jute fibre through modification with acrylonitrile and methacrylonitrile [4]. But there are no worth mentioned works on dyeing of synthetic monomer modified jute fibre with reactive dye. Again, reactive dyed materials are more colour fastness than any other dyestuffs. In the present investigation, an attempt has therefore been made to dye jute with reactive dyes and its dyeing behaviour depending on parameter variables. The bleached fibre was modified with synthetic monomers like, acrylamide and acrylic acid through graft copolymerization. The colour fastness of dyed and modified fibres was tested under various influences. The influence of sunlight on the strength of dyed and modified fibres was also examined.
2. Experimental
2.1. Materials
As a material for investigation, Corchorus olitorius (Tossa variety) of jute fibre was collected from Rajshahi jute mills Ltd., Bangladesh. Four chlorotriazinyl derivatives of reactive dyes, namely Reactive Red 120 (RR120), Reactive Blue 5 (RB5), Reactive Orange 14 (RO14), Reactive Brown 10 (RBr10) were purchased from Sigma, USA and used without further purification. Acrylamide (AM, CH2=CH-CONH2, RDH, Germany) and acrylic acid (AA, CH2=CH-COOH, RDH, Germany) were used as modifying agent. All other chemicals used were of A.R. grade.
2.2. Methods
2.2.1. Preparation of Jute Sample for Grafting
Discarding 70 cm from the bottom, 30 cm long fibre was taken, blended and washed with 6.5 gm detergent and 3.5 gm soda per liter at 70°C for 30 min [5]. Then this fibre was bleached with sodium chlorite (NaClO2) of strength 0.5 wt. % at pH 4 and at 85 – 90°C for 90 min [5,6]. After bleaching, the fibre was soaked in 0.2% sodium meta-bisufite solution for 15 min to neutralize chlorine action and then washed with distilled water. The bleached fibre was dried at 80°C, stored in a desiccator for next use.
2.2.2. Method of Grafting
Polymerization was done in 100 ml stoppered Erlenmeyer flask with 60 wt % monomer, 1.2 wt % potassium peroxydisulfate as initiator and 0.8 wt % ferrous sulfate as catalyst based on the weight of fibre at 80°C for 150 min in the fibre-liquor ratio of 1:50. At the end of reaction period, the modified jute fibre was thoroughly washed with boiling soap solution (1.0 wt %) to remove the loosely adhered polymer, wash with distilled water and dried [7, 8]. Percent graft yield was calculated according to the formula below and was obtained 18.5% and 15.6% for AM and AA, respectively.
Where, W1 and W0 are the weight of the ungrafted (bleached) and grafted jute fibre, respectively.
2.2.3. Method of Dyeing
Reactive dyes were dissolved, at first, by making paste with little distilled water and then, by adding cold distilled water. Dyeing was carried out with reactive dyes in a dyebath containing 0-3.5 wt.% dye and 0-12.0 wt.% aluminum sulfate (Al2(SO4)3) as electrolyte at 30-100°C for 20-90 min in the fibre-liquor ratio of 1:30. Dyeing was started by entering the fibrous material into the bath at room temperature, the temperature was raised up to 70°C within 30 min and continued for 60 min, then allowed for further 30 min as the bath cools down. After 30 min of dyeing, the bath was slightly alkalified with 2.0 wt.% sodium carbonate solution for fixation of dye on fibre and dyeing was continued. After dyeing, the amount of dye absorbed by the fibre from dyebath was determined colorimetrically [9, 10].
Where, Do and De are the original and exhausted dyebath concentration, respectively.
2.2.4. Colour Fastness
Colour fastness of dyed fibre samples was measured by Grey scale. Fastness grade 5 is the control.Sunlight fastnessThe fibre samples were exposed directly under the sun for 8 h each day on June to August and continued for 350 h [11]. After every 50 h, the change in colour of the specimen was assessed by the Grey scale comparing with the control.Wash fastness Wash fastness of reactive dyed jute fibre was determined using 5 gm / liter soap solution [12] at 50°C, 75°C and 100°C for 30 min in the fibre-liquor ratio of 1:50. Acid and alkali fastnessA sheet of dyed fibre was made and then spotted with two drops of sulfuric acid (50 gm / liter), acetic acid (300 gm / liter), tartaric acid (100 gm / liter), sodium carbonate (100 gm / liter), sodium hydroxide (50 gm / liter) and 10 % ammonium solution at room temperature [13, 14]. The samples were dried at room temperature and then the change in colour of the spotted area was assessed with the Grey scale.
2.2.5. Tenacity of Jute Sample
Breaking strength of jute fibre was measured by Torsee’s Schopper Type – OS-100 Tensile Tester. The length of each specimen (total length 25 cm and its weight 0.5 gm) between the jaws of the machine was maintained by 10 cm and a twist per 2 cm was given along the length of the fibre. The average breaking load (the mean of 25 readings) of the fibre was measured in kg/yarn [5, 15]. Tenacity was calculated by the following formula [16]:
3. Results and Discussion
3.1. Dye Concentration
The absorption of RR120 dye by bleached, AM- and AA- modified jute fibres is shown in Figure 1. It can be observed from Figure 1 that dye absorption by bleached AM- and AA- modified jute fibres decreased with the increase of dye concentration in the dye bath. In this case, the presence of more dye ions in solution at higher concentration hindered absorption by increasing dye ions or molecules size through aggregation. Again, the dye absorption by bleached jute fibres was higher than that of AM- and AA-modified fibres. AM and AA monomers increased the hydrophobic nature of jute fibre by their incorporation through grafting. Hence, the lower absorption occured by the modified fibres. Although absorption of a reactive dye by the fibre is different to that of other, similar behaviour is observed in all other cases of used dyes. From the experiment it was evident that brilliant and uniform hue were produced on jute fibre when it was dyed with 1.5 wt.% RR120, 2.5 wt.% RB5, 2.5 wt.% RO14 and 2.5 wt.% RB10 on the basis of jute fibre in presence of 7.0 wt.% (Al2(SO4)3) solution at 80°C for 60 min. Above or below of these concentration of dye, dull and uneven shades were determined. At 1.5 wt.% RR120, 2.5 wt.% RB5, 2.5 wt.% RO14 and 2.5 wt% RBr10 in the dye bath, the dye absorption was 75.6%, 63.0%, 43.2% and 33.0% for bleached jute fibre; 77.0%, 58.0%, 45.0% and 37.8% for AM-modified jute fibre and 75.0%, 60.0%, 41.9% and 34.4% for AA- modified jute fibre respectively. The dye absorption depends on the nature of dye and characteristics of jute fibre. 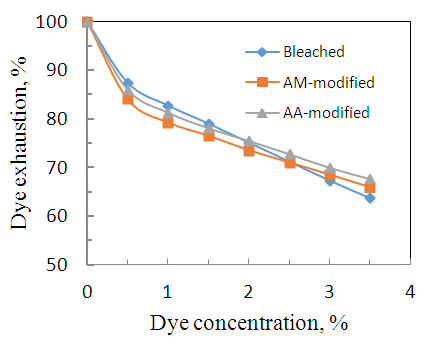 | Figure 1. Effect of dye concentration on dye exhaustion of RR120 by bleached, AM- and AA- modified jute fibres |
3.2. Electrolyte Concentration
Effect of aluminum sulfate concentration as electrolyte on absorption of RR120 by bleached, AM-and AA-modified jute fibres is shown in Figure 2. From Figure 2, it can be seen that some dye absorption occurred without electrolyte in the dye bath. The absorption of dye increased with the increase of Al2(SO4)3 concentration in the dyebath up to a maximum and then absorption is nearly plateau on further addition of Al2(SO4)3. RR120 dye contained impurities which might be inorganic salt, dextrin and possibly wetting or dispersing agent, etc. Again, electrolyte may also be present in the water used in dyeing. These electrolytes were added to bring the dye to a standard tinctorial strength to produce an increase in absorption [17]. The Al2(SO4)3 dissociated into Al3+ and SO42- ions in the aqueous solution of dyes. The positively charged Al3+ ions migrated towards the negatively charged fibre surface and thus, by reducing the negatively charged potential between the similar charged fibre surface and the coloured dye anions, and thus improved dyeability. [18a] On the other hand, the presence of an electrolyte in the dyebath decreased the membrane potential of cellulose, reduced the repellency of cellulose and dye particles with the same charges and also improved dyeability. The absorption reached saturation absorption when bleached, AM- and AA- modified jute was dyed in presence of 10.0%, 10.0% and 9.0% wt% Al2(SO4)3 respectively and the corresponding dye absorption is 76.1%, 79.2%, 80.1%. Above or below these concentrations of Al2(SO4)3 shades were uneven and dull. 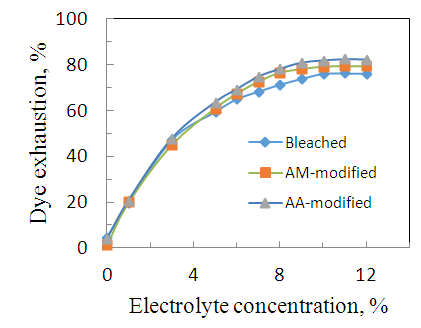 | Figure 2. Effect of Al2(SO4)3 (electrolyte) concentration on dye exhaustion of RR120 by bleached, AM- and AA-modified jute fibres |
3.3. Dyeing Time
The effect of reaction time of bleached, AM- and AA- modified jute fibres on RR120 dye exhaustion is shown in Figure 3. It can be observed from Figure 3 that the absorption of dye by bleached, AM- and AA- modified jute fibres increased with the progress of dyeing time and the absorption reach maximum within 50, 60 and 60 min, respectively. The absorption remained nearly the same at a further increase of dyeing time. Jute fibre immersed in a solution of a dye would absorb dye until equilibrium was reached. The speed of dye diffusion inside the fibre depends on the size or mass of the dye particles and also depends on the solubility of the dyes, and on the state of the fibre. More clearly, the smaller the dye particles and the greater the fibre swelling, the higher was mobility of the particles and quicker they penetrated inside the fibre, and conversely the larger dye particles and the less the swelling capacity of the fibre, the slower was the diffusion. The dyeing time of bleached, AM- and AA- modified jute fibres at maximum dye exhaustion was 50 min, 60 min and 60 min respectively and the corresponding dye absorption are 77.2%, 80.3% and 81.3%.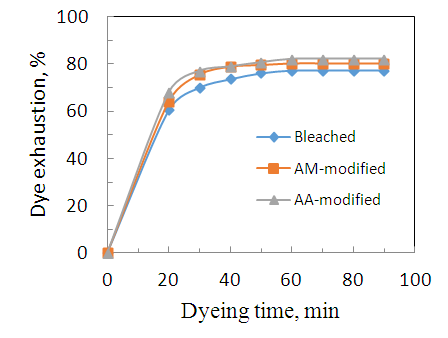 | Figure 3. Effect of dyeing time on dye exhaustion of RR120 by bleached, AM- and AA- modified jute fibres |
3.4. Dyeing Temperature
The effect of reaction temperature of bleached, AM- and AA- modified jute fibres on RR120 dye exhaustion is shown in Figure 4. It can be observed from Figure 4 that the absorption of dye by the fibre increased with the increase of dyeing temperature and became maximum at 90°C, and after that the dye absorption decreased with the further increase of temperature. It seems that dyes were existed in solution as aggregates of various sizes. When the solution temperature increased the thermal energy coming from outsides impeded aggregation to maintain the overall dynamic equilibrium of the system and therefore increased in the amount of the non-aggregated dye particles in the solution. [18b] Penetration of smaller dye particles into the fibre were easily occurred. At higher temperature, size of fibre pores might be increased and dye particles easily penetrated into the fibre. When the dye bath cools down the fibre pores contracted and hence the dye particles remained in the fibre. However, at very high temperature the decrease in absorption might be due to the change in texture or morphology of the fibre material, and the dye molecule in solution might be broken down into other products. The dyeing temperature of bleached, AM- and AA-modified jute fibres at maximum dye absorption was 90°C in each case and the corresponding dye absorption was 87.3%, 84.5% and 86.2% respectively.It was observed from the experimental results, absorption of the used four reactive dyes, e.g. RR120, RB5, RO14 and RBr10 was different to each other and depended on the structure of dye and conditions of parameter variables, but their absorption nature is more or less similar. The reactive dyes are RR120, RB5, RO14 and RBr10 which contained 6, 3, 2 and 1 sulfonic groups in their structure respectively. The sulfonic acid group is responsible for the solubility behaviour of dyes. Depending on the solubility characteristics, the order of dye absorption is RR120 > RB5 > RO14 > RBr10. The effective optimum condition of the used reactive dyes are listed in Table 1.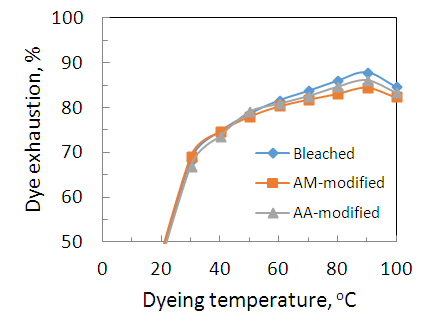 | Figure 4. Effect of dyeing temperature on dye exhaustion of RR120 by bleached, AM- and AA-modified jute fibres |
Table 1. Effective optimized conditions for dyeing of bleached, AM- and AA modified jute fibres dyed with reactive dyes 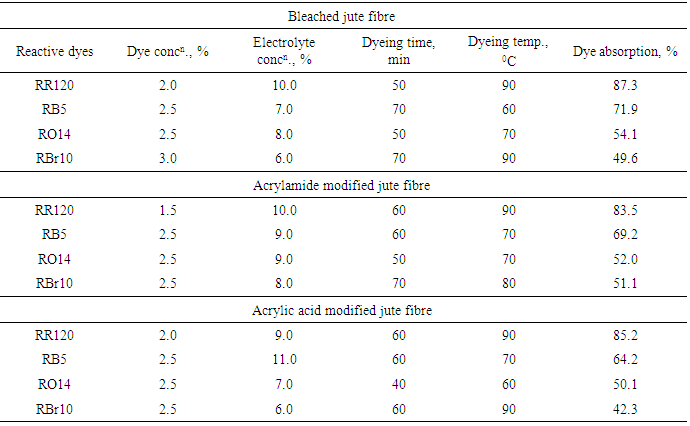 |
| |
|
3.5. Colour Fastness
The fastness of a dye refers to the ability of the colour produced by it to withstand the destructive effect of certain agencies acting upon it. No dyestuff or organic nature can be considered as absolutely fast, that is to say, the colour produced by it can be changed or destroyed. Again, colour of fibrous materials are very sensitive to various factors, such as light, washing etc. Experimental results of bleached, AM- and AA- modified jute fibres became yellow on exposure to sunlight in air. This yellowing effect is due the photo chemical degradation of lignin component in jute in presence of oxygen or moisture which results in the formation of quinonoid type compounds [19]. The modified jute showed lower yellowing rate because of low rate of oxygen or moisture diffusion to the site of fading.It is observed from the Table 2 that colour of bleached, AM- and AA- modified jute fibres dyed with RR120, RB5, RO14 and RBr10 was faded on 300 h exposure to sunlight in air in the month of June to August and colour fastness of dyed modified jute fibre was somewhat better than that of dyed bleached jute fibre. Some of the absorbed dye was embedded in the matrix of the fibre that it can not be reached at all by the moisture and oxygen that caused lower fading. Another explanation is that the lignin of modified fibre did not accelerate by sunlight to fade or discolouration like unmodified dyed fibre. The colour of RR120 and RO14 dyed fibre was good for 300 h exposure and that of RB5 and RB10 dyed fibre was good for 150 h exposure.Table 2. Colour fastness and change in colour of bleached, AM- and AA- modified jute fibres dyed with reactive dyes on exposure in sunlight in air 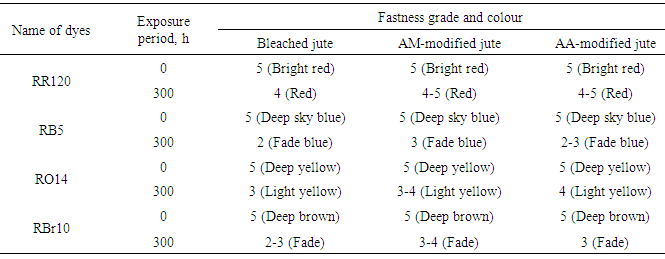 |
| |
|
Colour fastness of RR120, RB5, RO14 and RBr10 dyed bleached, AM- and AA- modified jute fibres on washing with 5% soap solution at 75°C for 30 min was listed in Table 3. The colour of both dyed fibres became fade on washing with soap solution. The wash fastness of the used dyes are in the order of RR120 > RO14 > RBr10 > RB5. This indicates the better dye-fibre covalent bond formation ability of the dyes used.Table 3. Colour fastness and change in colour of bleached, AM- and AA- modified jute fibres dyed with reactive dyes on washing with soap solution 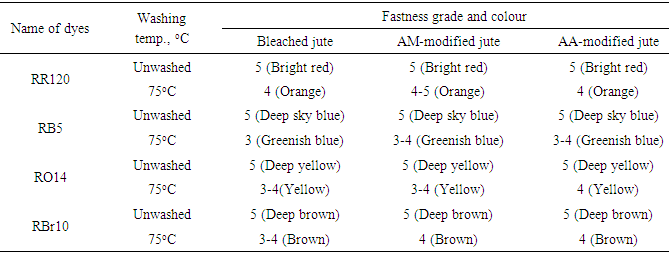 |
| |
|
The colour fastness of bleached, AM- and AA- modified jute fibres dyed with RR120, RB5, RO14 and RBr10 to spotting with inorganic acids e.g. sulfuric acid was good. It was also good with organic acids e.g. acetic acid, tartaric acid. Similarly the colour fastness of these fibres dyed with RR120, RB5, RO14 and RBr10 to spotting with alkalis, like sodium carbonate, sodium hydroxide and ammonia solution were highly satisfactory but in few cases it gave unsatisfactory results by changing colour.
3.6. Tenacity
From Table 4, it can be seen that the loss in tenacity of bleached, AM- and AA-modified jute fibres on exposure to sunlight in air for 250 h were 17.2%, 9.1% and 8.0% respectively. The loss in tenacity of these fibres was enhanced by the dyeing with reactive dyes. The lower loss in tenacity of grafted jute fibres than the bleached fibres was due to the lower affinity of grafted jute fibre towards moisture. This ultimately reduced the photo-oxidative degradation of jute fibre. But the dye particles in the dyed samples enhanced the photo-oxidative degradation by absorbing UV of sunlight in presence of moisture. The lower loss in tenacity was obtained in the case of grafted dyed fibres. The oxidative reaction varies from dye to dye and their interaction with the fibre molecules.Table 4. Loss in tenacity of bleached, AM- and AA-modified jute fibres dyed with reactive dyes on exposure to sunlight in air 250 h 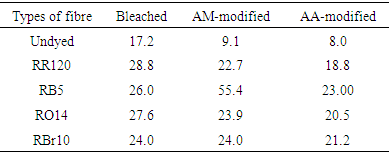 |
| |
|
4. Conclusions
The dyeability of acrylamide and acrylic acid modified jute fibres was greatly influenced by the characteristics of monomer which increased the hydrophobic nature of the fibre grafted. Graft co-polymerization of acrylamide and acrylic acid improved the colour fastness and strength characteristics of bleached jute fibre dyed with reactive dyes.
ACKNOWLEDGEMENTS
The authors would like to acknowledge the Ministry of Education in Bangladesh for funding the project as Higher Education Research Grant in 2014 (Memo nos.: 37.01.0000.078.02.018.13-206(38)/6-35, 2014).
References
[1] | Patro, P. S. (1971). Dyeing of jute with basic, acid, direct and sulphur dyestuffs, Text. Dyer. Printer, 4(8), 57-62. |
[2] | Pandey, S. N. and Day, A., Chattopadhyay, S. N. and Pan, N. C. (1993). Computerised study on colour strength and fastness properties of direct dyed jute fabric, Text. Dyer. Printer, 26, 23-27. |
[3] | Mondal, Md. I. H., Farouqui, F. I. and Maniruzzaman, Md. (2002). Light and thermal effects on the strength of jute fibre dyed with disperse dyes, Colourage, 49(8), 33-38. |
[4] | Mondal, Md. I. H and Alam, R. (2007). Dyeing behaviour and colour fastness characteristics of bleached, AN- and MAN-modified jute fibres dyed with direct dyes, Colourage, 54(10), 68-73. |
[5] | Farouqui, F. I. and Mondal, Md. I. H. (1989). Scouring and bleaching of jute fibre in relation to its strength, The Rajshahi University Studies, Part-B, 17, 1-8. |
[6] | Sarkar, P. B. and Chatterjee, H. (1948). The bleaching of jute with chlorite, J. Text. Inst., 39, T274-81. |
[7] | Mondal, Md. I. H., Farouqui, F. I. and Enamul Kabir, F. M. (2002). Graft copolymerization of acrylamide and acrylic acid onto jute fibre using potassium persulphate as initiator, Cellul. Chem. Technol., 36(5-6), 471-482. |
[8] | Sikdar, B., Basak, R. K. and Mitra, B. C. (1995). Studies on graft copolymerization of acrylonitrile onto jute fiber with permanganate ion initiated system in presence of air, J. Appl. Polym. Sci., 55(12), 1673-1682. |
[9] | Farouqui, F. I. and Mondal, Md. I. H. (1990). Dyeing of jute fibre with direct dyes and their fastness characteristics, Indian J. Fibre Text. Res., 15, 65-72. |
[10] | Trotman, E. R. (1990). Dyeing and chemical technology of textile fibres (6th Ed), Edward Arnold, London, pp. 353-372. |
[11] | International Standard ISO 105-BO3-1978 (E) (1978). Colour fastness to weathering: Outdoor exposure. International organisation for standardization, Switzerland. |
[12] | International standard ISO 105-COI-1982 (E) (1982). Colour fastness to washing: Test 1, International organisation for standardization, Switzerland. |
[13] | International standard ISO 105-EO5-1978 (E) (1978). Colour fastness to spotting: Acid, International organisation for standardization, Switzerland. |
[14] | International standard ISO 105-EO6-1978 (E) (1978). Colour fastness to spotting: Alkali, International organisation for standardization, Switzerland. |
[15] | International Standard ISO 5081-1977(E) (1977). Textile-woven fabrics: Determination of breaking strength and elongation (Strip method), International Organization for Standardization, Switzerland. |
[16] | Haque, M. M. and Habibuddowla, Md. (1980). Studies on tenacity of ceric ion initiated methyl methacrylate grafted jute fibre, Bangladesh J. Sci. Ind. Res., 15, 64-70. |
[17] | Vickersstaff, T. (1954). The Physical Chemistry of Dyeing, Imperial chemical Industries Ltd., London, p. 234. |
[18] | Sadov, F., Korchagin, M. and Matetsky, A. (1973). A Chemical Technology of Fibrous Materials, Mir publishers, Moscow, pp. (a) 329-331, (b) 374-78. |
[19] | Macmillan, W. G. (March 1957). Indian Textile Journal, p. 342. |