Hisham A. Maddah 1, 2
1Department of Chemical Engineering, King Abdulaziz University, Rabigh, Saudi Arabia
2Department of Chemical Engineering, University of Southern California, Los Angeles, United States
Correspondence to: Hisham A. Maddah , Department of Chemical Engineering, King Abdulaziz University, Rabigh, Saudi Arabia.
Email: |  |
Copyright © 2016 Scientific & Academic Publishing. All Rights Reserved.
This work is licensed under the Creative Commons Attribution International License (CC BY).
http://creativecommons.org/licenses/by/4.0/

Abstract
This paper critically reviews polypropylene (PP) material in several aspects. The aim of this study is to prove that polypropylene is a promising plastic by showing its great chemical, physical and mechanical properties, understanding and comparing between PP types as well as thermoplastics to identify their pros and cons, providing a comprehensive explanation regarding to Dow/UNIPOL PP technology process, and including extensive reviews on infinite number of PP applications. It is found that PP is the main output of propylene among other derivatives with two-thirds consumption rate. PP is the lightest type of plastics with a density of 0.90 g/cm3. Homo-polymer PP (HPP) has a market share of 65-75%. Branching, reinforcing and filling PP are some techniques to produce plastics with superior mechanical properties. Semi-crystalline isotactic polypropylene (iPP) showed appropriate optical characteristics upon recycling. BOPP and PP-OH films are ideal plastics for electrical applications. There are 26 operating PP plants and 4 PP plants in construction around the globe. PP applications include, but not limited to, fabrics, films, bottles, sheets and automotive products.
Keywords:
Polypropylene, UNIPOL Technology, Dow, Applications, Properties, Plastic, Polymer, Thermoplastic
Cite this paper: Hisham A. Maddah , Polypropylene as a Promising Plastic: A Review, American Journal of Polymer Science, Vol. 6 No. 1, 2016, pp. 1-11. doi: 10.5923/j.ajps.20160601.01.
1. Introduction
Plastics are categorized into four main groups: thermoplastics, elastomers, thermosets and polymer compounds. Macromolecular structures distinguish the class of any plastic material as well as its physical properties. Elastomers and thermosets have soft and hard elasticity, respectively; and their resins cannot be melted for recycling purposes. However, thermoplastics are either amorphous or semi-crystalline. Amorphous resins are disordered statistical oriented macromolecules whereas semi-crystalline resins macromolecules are nearly ordered since they are embedded with crystalline phases. Typical amorphous resins are polycarbonate (PC), polystyrene (PS) and polyvinylchloride (PVC) where typical semi-crystalline resins includes polyamide (PA) and polypropylene (PP). Since PP is under the semi-crystalline class, our focus will be on this group [22].Polypropylene was discovered in 1954 and gained a strong popularity very quickly due to the fact that PP has the lowest density among commodity plastics. PP has an excellent chemical resistance and can be processed through many converting methods such as injection molding and extrusion. Polypropylene is a polymer prepared catalytically from propylene. It is major advantage is related to the high temperature resistance which makes PP particularly suitable for items such as trays, funnels, pails, bottles, carboys and instrument jars that have to be sterilized (cleaned) frequently for use in a clinical environment. Polypropylene is a free-color material with excellent mechanical properties and it is better than polyethylene for the previous reasons [1]. Polypropylene is a downstream petrochemical product that is derived from the olefin monomer propylene. The polymer is produced through a process of monomer connection called addition polymerization. In this process, heat, high-energy radiation and an initiator or a catalyst are added to combine monomers together. Thus, propylene molecules are polymerized into very long polymer molecules or chains. There are four different routes to enhance the polymerization of any polymer: solution polymerization, suspension polymerization, bulk polymerization and gas-phase polymerization. However, polypropylene properties vary according to process conditions, copolymer components, molecular weight and molecular weight distribution. Polypropylene is a vinyl polymer in which every carbon atom is attached to a methyl group and can be expressed as shown in Figure 1 [2].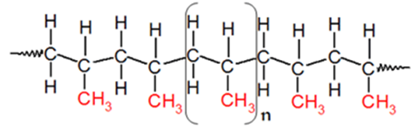 | Figure 1. Polypropylene structure |
The annual global demand for plastics reached 245 million tons and it is project to grow dramatically because of the increase in public demand. Figure 2 shows the total plastics demand by 2006. Around 90% of the total demand is accounted for five main commodity plastics: polypropylene (PP), polyethylene (PE), polyvinyl chloride (PVC), polystyrene (PS) and polyethylene terephthalate (PET). In 1954, Giulio Natta discovered PP, but commercial production began in 1957. PP is the most widely used thermoplastic since it is very cheap and flexible for molding. The second common plastic type is PE. There are different grades of PE linear low density (LLDPE), low density (LDPE), medium density (MDPE) and high density (HDPE). The density of PE grades ranges between 0.925-0.965 and obviously is higher than PP. However, the uniqueness of PVC is associated with chlorine content (57 wt. %) in its structure. Annual worldwide PVC demand is approximately 35 million tons. According to previous studies, plastics are the most recyclable materials and there were 4.4 million tons of plastics recycled in 2006 [17]. 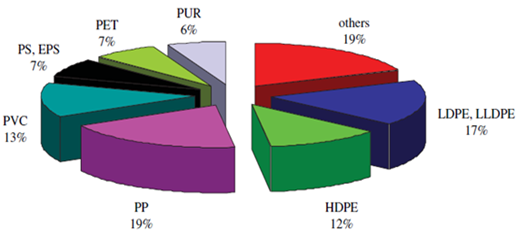 | Figure 2. World plastics demand by resin types 2006 (49.5 million tons) |
Polypropylene chemical resistance can be described as follows: excellent resistance to dilute and concentrated acids, alcohols and bases, good resistance to aldehydes, esters, aliphatic hydrocarbons, ketones and limited resistance to aromatic and halogenated hydrocarbons and oxidizing agents [1]. Polypropylene has a crystalline structure with a high level of stiffness and a high melting point compared to other commercial thermoplastics. The Hardness resulted from the methyl groups in its molecular chain structure. Polypropylene is a lightweight polymer with a density of 0.90 g/cm3 that makes it suitable in many industrial applications. Still, polypropylene is not suitable to be used at temperatures below 0°C [2]. Experiments proved that polypropylene has excellent and desirable physical, mechanical, and thermal properties when used in room temperature applications. It is relatively stiff and has a high melting point, low density and relatively good resistance to impacts [3]. Typical crystallinity of PP is between 40-60%. PP is a low-cost thermoplastic polymer with excellent properties like flame resistance, transparency, high heat distortion temperature, dimensional stability and recyclability making it ideal for a wide range of applications [16]. Propylene is one of the most important industrial petrochemical building blocks used to produce various chemical derivatives. The dominant outlet for propylene is PP which accounts for nearly two-thirds of global propylene consumption as shown in Figure 3 [3]. There are three major sources of propylene: from steam cracking of naphtha, gasoline refining process and propane dehydrogenation technology [16]. Polypropylene is the most important material among polyolefins due to three main reasons. First, great properties of PP such as low density, high melting temperature and chemical inertness with low cost making PP optimum for long-life applications. Second, polypropylene is a highly versatile material meaning that diversity in structural designs and mechanical properties are achievable. Third, different morphological structures of PP are possible by using fillers or reinforcing agents and blending PP with other polymers which yield to have superior characteristics. Special and reinforced polypropylene grades include elastomer-modified PP, elastomer modified filled PP, glass fiber-reinforced PP, filled PP, esthetic filled PP, flame-retardant PP and thermoplastic elastomers [23].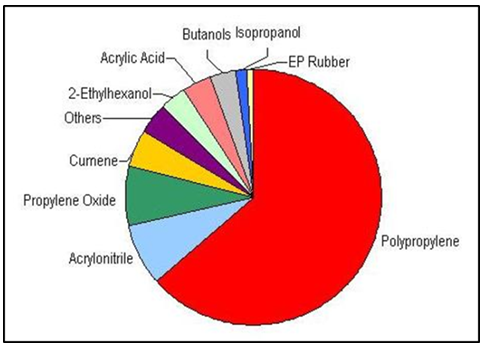 | Figure 3. Global propylene consumption (two-thirds for polypropylene) |
A study shows that branching process of linear Ziegler–Natta polypropylenes is possible by creating chains based on the molecular weight distribution. Introducing branching into a linear polypropylene will result in having a product with high molecular weight, high melt strength and better properties like high modulus and tensile strength, rigidity and excellent heat resistance. Branching parameters β, the average number of branch points per molecule, and λ, the number of branch points per 103 carbons, are calculated to identify the polymer structure and properties. A post-reactor is used for the branching process. The branching efficiency is associated with chemical composition and temperature of the reaction. The relationship between branching parameters and molecular weight is important to design polymers with unique properties for different applications [15].PP is very suitable for reinforcing and filling. Thus, another study focuses on studying the effect of fibers reinforcement on the mechanical properties of fiber-reinforced polypropylene composites (FRPCs). A composite material is a polymer matrix that is embedded with reinforcement fibers such as glass or carbon. FRPCs have better durability, moisture resistance and high strength properties; making them ideal in applications related to constructions, sports equipment and cars. Synthetic fibers yield to have better mechanical properties compared to natural ones. Glass fibers are widely used as a synthetic reinforcement with PP to produce very good mechanical properties composites. However, mechanical characteristics of composites are controlled by numerous fiber treatments and coupling agents. Fiber diameter is another significant factor in designing composites material. A certain value of fiber diameter thickness should not be exceeded; if so fibers will decrease composites strength [16]. Electrically conductive PP and PE composites are cost-effective, commercially proven and with outstanding electrical and mechanical properties. It is mandatory to understand the distribution, orientation, interaction and aspect ratio of conductive fillers with the polymer matrix to obtain the required conductivity. Better filler-matrix interactions are achievable at low viscosity, low surface tension and high crystallinity. Grafting technique initiates the interactions and the distribution of the fillers with PP and PE matrices [20].
2. Polypropylene Properties and Types
In order to understand the different types of polypropylene, one needs to dig in and understand thermoplastics categories with a different point of view. Thermoplastics are categorized into two groups: commodity thermoplastics, this group covers the major plastics such as polyethylene, polypropylene, polystyrene and polyvinyl chloride. They have further sub-divisions such as PP-homo-polymers and Co-polymers, PVC-Rigid and Plasticized, PE-High density, low density and linear low density. Engineering thermoplastics is the second thermoplastics group and products in this class are related to electrical and mechanical engineering applications. Using these plastics may replace other materials like metals and load-bearing components. These include polysulfone, nylons, polycarbonates, acetal and ABS terpolymers [4].However, thermoplastics are characterized by softening upon heating and hardening by cooling which is an advantage in processing procedures such as extrusion or injection molding where discarded materials can be recycled. Polypropylene is found in three stereo specific configurations: isotactic, methyl groups on one side of polymer backbone, syndiotactic, methyl groups alternate on both sides and atactic, irregular arrangement of methyl group [4]. Melting point of perfectly isotactic PP is 171°C, but syndiotactic PP (30% crystallinity) has a melting point of 130°C [16]. Polypropylene is attractive to petrochemical companies because of its great properties. For instance, polypropylene is semi-rigid, translucent, a good chemical resistance, tough, a good fatigue resistance and a good heat resistance. Moreover, PP has high softening or glass-transition point, high resistance to flexing stress, low water absorption, good electrical resistance, a lightweight, dimensional stability, high impact strength and a non-toxicity property. PP is stiffer than HDPE and biaxial orientation of PP results in films and containers with superior optical and barrier properties. Table 1 shows properties of isotactic homo-polypropylene as an example [5, 6].Table 1. Properties of Isotactic Homo-polypropylene [5, 16] 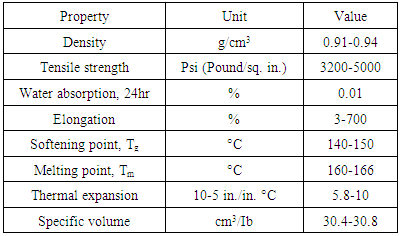 |
| |
|
There are three different types of polypropylene. First, polypropylene containing only propylene monomer in a semi-crystalline solid form; which is called a homo-polymer PP (HPP). Second, polypropylene containing ethylene as a co-monomer in the PP chains at levels in the range of 1-8% and this is referred to as a random copolymer (RCP). Third, HPP containing a co-mixed RCP phase that has an ethylene content of 45-65% is referred to as an impact copolymer (ICP). In general, polymers consisting of identical monomers are called homo-polymers where polymeric compounds with more than one type of monomer in their chains are known as co-polymers [1].Homo-polymer PP (HPP) is the most widely used polypropylene material in industry. HPP is a two-phase system contains both crystalline and non-crystalline regions. The non-crystalline (amorphous) regions have both isotactic PP and atactic PP. The isotactic PP in the amorphous regions is crystallizable and crystallizes slowly over time. In other words, HPP consists of only one propylene unit along the chain with mostly isotactic propylene units and that give us a crystalline structure to the polymer. Therefore, HPP exhibits a high level of stiffness at room temperature and a high melting point but lower transparency as well as diminished impact strength. Random copolymers (RCP) are ethylene/propylene copolymers that are produced in a single reactor by copolymerizing propylene and small amounts of ethylene (usually 7% or lower). Ethylene disrupts the regular structure of polypropylene and results in a reduction of crystalline uniformity in the polymer. The relation between ethylene and crystalline thickness is inversely proportional which means that as the ethylene content increases the crystalline thickness gradually decreases and resulting in reaching lower melting point. Co-polymers usually have slightly better impact properties, decreased melting point and enhanced flexibility. Impact copolymers (ICP) are physical mixtures of HPP and RCP with an overall ethylene contents approximately 6-15% weight. Impact polymers are optimal at low temperatures with higher impact resistance. The RCP part of the mixture is designed to have ethylene contents in the order of 40-65% ethylene and it is called the rubber phase. The rubber-like reinforcement greatly improves impact strength particularly at low temperatures (below − 20°C). However, stiffness is retained resulting in excellent stiffness/impact balance. ICP product as well as the impact resistance varies with respect to size, shape and distribution of the rubber particles. A comparison between homo-polymers and copolymers in their advantages and disadvantages of PP, in general, is illustrated in Table 2 [2].Table 2. Advantages and Disadvantages of Polypropylene 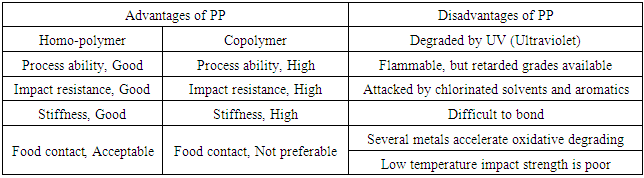 |
| |
|
The following is the approximate market share for PP types: homo-polymer (HPP) 65-75%, impact copolymer (ICP) 20-30% and random copolymer (RCP) 5-10%. Generally, different PP grades are available depend on the required application. Commercial grades are available in a variety of molecular weight distributions, and co-monomer types as well as contents and additives. Enhanced physical properties allow polypropylene to be the core material in most demanding applications such as films, fibers, tapes, sheets, thermoforming, injections, and blow molding [2]. Some mechanical and thermal properties of commercial polypropylene plus a comparison of thermal conductivity and recoverable energy content of different plastics are shown in Table 3 and Table 4, respectively [25, 17]. Table 3. Mechanical & Thermal Properties of Polypropylene [25] 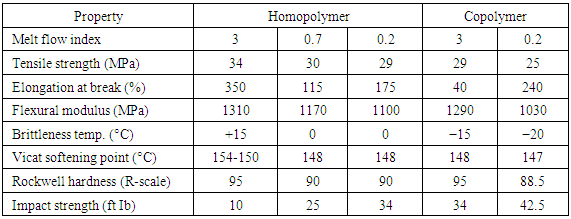 |
| |
|
Table 4. Thermal Conductivity & Recoverable Energy of Plastics [17] 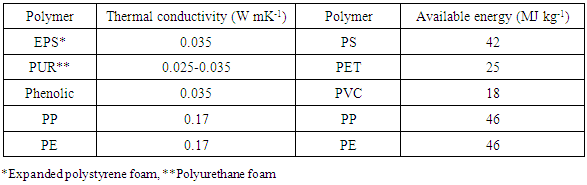 |
| |
|
Recycling of polymers causes depletion in their mechanical and optical properties. Optical characteristics are extremely important for food packaging applications. A commercial polypropylene grade called semi-crystalline isotactic polypropylene (iPP) was studied in a previous work to ensure a suitable opacity upon recycling [18]. Semi-crystalline iPP structures characterize with several crystal modifications including monoclinic (
), trigonal (β) and orthorhombic (γ) forms [19]. Optical transparency in semi-crystalline polymers depends on crystallinity, morphology and surface properties. The lower the transparency is the more haze we get. Hence, reduced crystallinity increases the clarity of the product. iPP polymers are extruded, recycled, several times and cooled upon extrusion to see the effect of recycling on opacity. It is found that opacity decreases on increasing recycling steps and cooling rate. However, increasing the amount of
phase and increasing their average size of the spherulites increases opacity [18]. β-modification of isotactic polypropylene (β-iPP) is another commercial grade with unique features. For example, toughness and impact strength of β-iPP significantly exceed those of
-iPP. The development of β-phase is completed by crystallization in a temperature gradient or in a strained melt. Yet, β-modification cannot substitute or cancel the use of
-modification since each grade has its own superior properties. Results proved that iPP grades have excellent mechanical properties and appropriate optical characteristics [18, 19]. Typical properties for various semi-crystalline resins and thermoplastic composites with glass fibers and phase-transition temperatures for common semi-crystalline thermoplastic resins are illustrated in Tables 5 and 6, respectively [22].Table 5. Typical Properties for Various Semi-crystalline Resins and Thermoplastic Composites with Glass Fibers [22]  |
| |
|
Table 6. Phase-transition Temperatures for Semi-crystalline Resins [22] 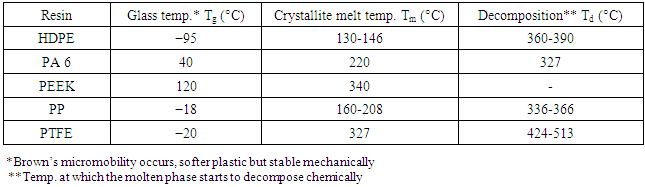 |
| |
|
Low temperature brittleness is a negative criterion for PP polymers in certain applications. A promising technique showed that superior balance of impact strength and modulus is possible by blending PP with various elastomers such as ethylene-propylene random copolymer (EPR), styrene-butadiene-styrene block copolymer (SBS), ethylene-propylene-diene terpolymer (EPDM) and isoprene-styrene di-block copolymer (ISR-A). For example, a blend of 80/20 and 70/30 of PP/ISR-A have a very high impact strength of 83 and 100 J/m, with flexural modulus of 1280 and 1070 MPa, respectively, compared to those results of PP (32 J/m, 1530 MPa) [24].
3. Polypropylene UNIPOL Technology
UNIPOL polypropylene process technology is a gas-phase technology that is occurred in a fluidized bed reactor system. The process is stable and predictable. The core facility has the smallest footprint in the industry which allows us to establish the whole polypropylene plant in an area of 60m x 65m [7]. Dow makes Shell High Activity Catalyst (SHAC) for UNIPOL process at Norco plant owned by Shell. The last improved using catalyst was in 1996, which is SHAC-320 with less tails for reduced smoke and improved clarity film. Dow produces commercial homo-polymer polypropylene by using UNIPOL technology. Dow Company is a major worldwide licensor for polypropyelen technologies. The company has 30 licensees in 18 countries with 26 operating plants and 4 plants in construction. The largest single reactor line with a capacity of 200,000 tons per year is operated by SABIC in Saudi Arabia and can produce more than 290,000 tons per year homo-polymer. The main processing blocks of UNIPOL plant are catalyst handling, propylene treatment for removal of trace catalyst poisons, polymerization, resin purging, integrated palletization, storage, packaging and loading [8].In Figure 4, fresh propylene feedstock (99.5% propylene) passes through a degassing column for removal of oxygen and goes through molecular sieves (separator) to remove trace quantities of water and other materials such as acetylene and sulfur compounds. Then, the feedstock passes through a heat exchanger (cooler) and it is sent to a dryer before entering the gas-phase polymerization reactor. The reactant gas stream is circulated through the bed; goes to a blower and then cooled in an external heat exchanger to remove the exothermic reaction heat. Also, heat removal is primarily done by condensation of propylene where 10-12% of propylene fed into the reactor is liquid. The reactor system holds an expandable vertical pressure vessel in the upper section that handle polymer particles and it is constructed of carbon steel and operates at 34.5 bar, 65°C. The operating conditions satisfy the dew point of the monomer. One advantage of the blower in the recycle loop is that it balances the pressure differences in the whole loop route, where the pressure is about 1.7 bar. The fluidized-bed reactor has a residence time of less than 1.5 hours and an extensive back mixing. The fresh liquid polymer-grade propylene is combined with recycled gases and enters the reactor bottom. Gas stream provides fluidization of the polymer inside the reactor. Titanium-supported catalyst, co-catalyst, hydrogen and an electron donor are added into the reactor to control molecular weight and selectivity. In homo-polymer production, polymer is taken out, periodically, from the polymerization reactor into a series of high-pressure gas/solid separators. The separated gas is recycled back to the top of the reactor where the liquid polymer goes through further processing and is converted to powder polymer [9].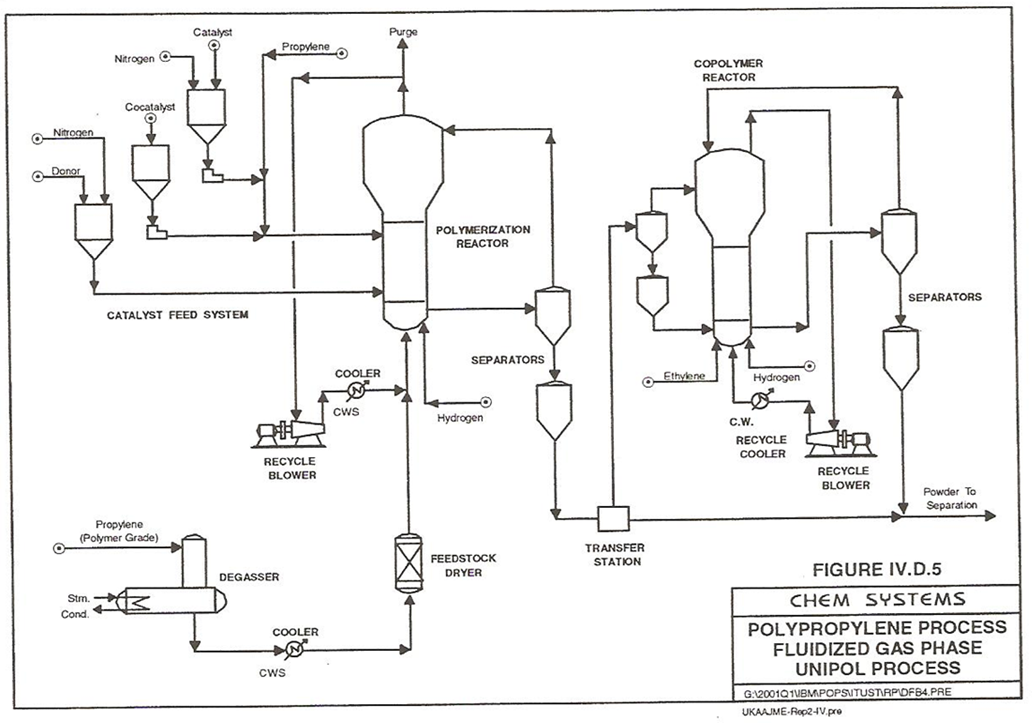 | Figure 4. Polypropylene fluidized gas-phase UNIPOL process (stage 1) |
In Figure 5, the separated polymer powder (bottom) from gas/solid separator is delivered to a purge tower where residual monomers (2000-3000 ppm) are stripped with injected nitrogen and steam to neutralize the catalyst residues. Then, polymer powder comes out of the purge tower bottom by gravitational force and is fed into a downstream extrusion unit, Figure 6. On the other hand, vented material from the purge tower (distillate) is sent to a small recovery operation at which it is compressed, passed through two heat exchangers to remove light gases and sent to a degassing pot where ethylene at distillate is recycled and the remaining product at bottom is sent to another separator tower. Ethylene, propylene and propane are separated from each other in a separator tower. However, ethylene and propylene streams are recycled for impact copolymer production [9].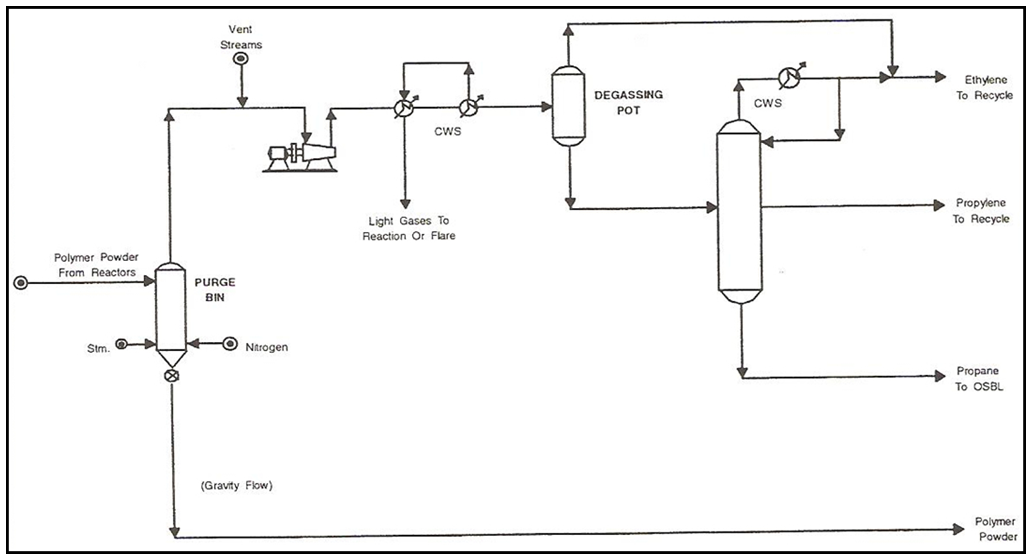 | Figure 5. Polypropylene fluidized gas-phase UNIPOL process (stage 2) |
Impact copolymer production takes place in the second reactor in Figure 4, where the reactor-discharged resins with active catalysts are sent to a transfer unit. Then, it is fed to the fluid-bed copolymer reactor before entering the purge tower (stage 2). Ethylene, recycled propylene and hydrogen are fed to the copolymer reactor. However, the recycle cooler system of the copolymer reactor is similar to the homo-polymer reactor system except that the gas recycle loop for copolymer operates 100% in gas-phase. Reactor polymer product (bottom) is sent to a set of gas/solid separators where the separated gas (distillate) is recycled back to the top of the copolymer reactor. The final polymer powder product goes from the separators bottom to the purge tower (stage 2) [9].The extrusion section, Figure 6, processes the polymer powder either homo-polymer or copolymer that is coming from the purge bin by gravity means. The powder stream is blended with certain additives in a blender. Then, it goes to a feed hopper and is fed into an extruder via a gravimetric feeder controller. There is a liquid feeder that compresses a liquid with the powder stream into the extruder. Extruder systems offered by Dow comprise melt mixers (e.g. twin screw extruder) with gear-pumps arrangement and underwater die-faced pelletisers [9].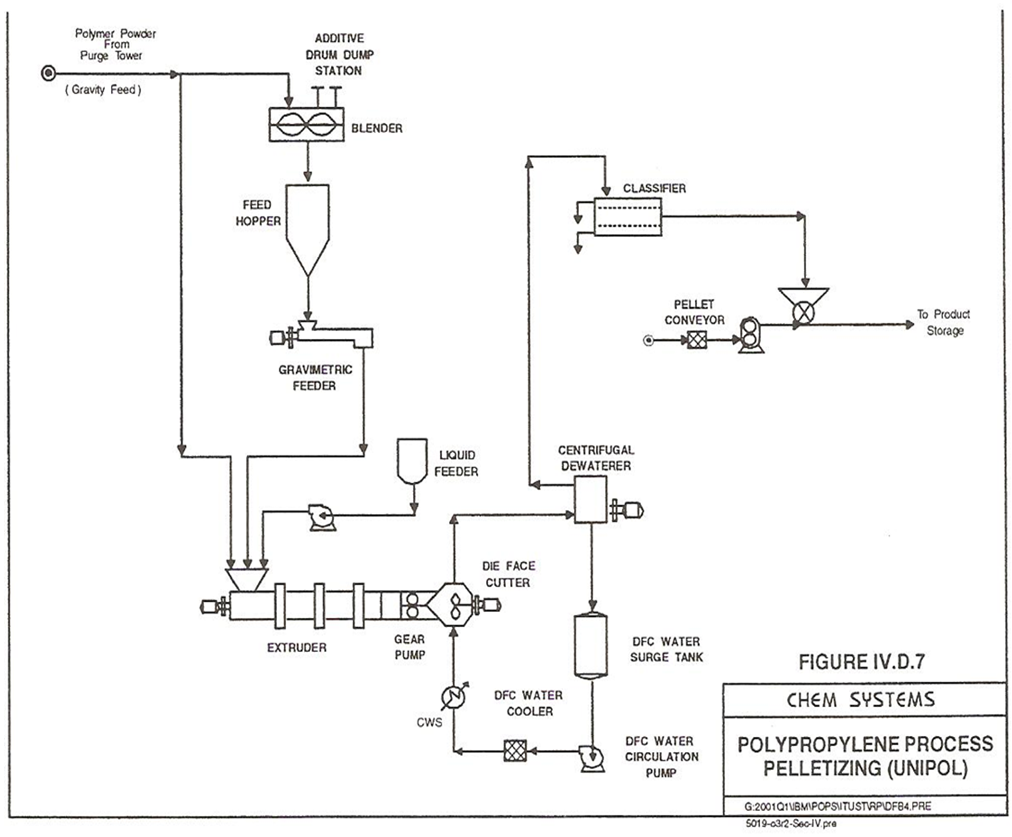 | Figure 6. Polypropylene fluidized gas-phase UNIPOL process (stage 3) |
During extrusion process, the liquefied polymer solidifies and is cut into tiny pellets underwater and carried out of the pelletisation unit in a sweeping water stream. The die face is kept at 280°C by exposing the die to a high-pressure steam to heat it. Then, the polymer/water stream is sent to a centrifugal de-waterer unit. At the bottom of the centrifugal de-waterer, the decanted water is collected and is stored in a water surge tank to be circulated in the system. The recycled water is pumped, filtered and cooled before it is returned to the underwater pelletiser unit. The distillate of the centrifugal de-waterer will have only dry polymer pellets that are sent to a classifier for size segregation processing. Next, pellets are transported to a conventional resin handling system [9].It is recommended to have a combination of two storage/continuous blending bins plus one loading bin per reactor line in order to make it easier for bagging, pelletising and wrapping the final product [9].
4. Polypropylene Applications
4.1. Fibers and Fabrics
Fibers are produced by various kinds of extrusion processes. Fibers include slit film or slit tape. The advantages offered by PP include low specific gravity which means greater bulk per given weight, strength, chemical resistance and stain resistance. There are different applications for fibers like slit film, staple fibers, nonwoven fabrics and monofilaments. Slit film is a wide web extruded film. The major application of slit film is in carpet backings. Nowadays, carpet backings are produced from PP more than from natural jute fibers. The reason is that jute fibers damage faster than PP fibers in high moisture weather. High humidity weather will allow higher absorption of water that yields to mold attack. Slit film applications are twine, woven fabrics for feed and fertilizer sacks, sand bags and bulk container bags, tarpaulins, mats, screens for erosion prevention and geotextiles to stabilize soil beds. More conventional fibers than slit-film fibers are known as continuous filament fibers and they result from extrusion. Staple fibers are short fibers ranging from less than an inch to a little less than a foot in length depending on the application [10].Nonwoven fabrics are the most common single fiber application for PP usage. There are three types of nonwoven fabrics: thermo-bonded, spun-bonded and melt-blown. The fabrics of each differ from another in properties and appearance. For example, spun-bonded fabrics are strong whereas melt-blown fabrics are soft. However, this type of fabrics often used by combinations of two types together. The fibers formed in the melt-blowing process are very fine and allow for the production of lightweight uniform fabrics that are soft and not strong. Fabrics from fine melt-blown fibers are utilized in medical applications because they allow the passage of water vapor but prevent the penetration of liquid water and aqueous solutions. Monofilaments are produced by extruding PP through a plate containing many small holes and then monofilaments are quenched into a water bath which cools the fabrics. Twisting bundles of monofilament together gives us applications like rope, twine and fishing nets that are strong and moisture resistant; making them ideal in marine applications, Figure 7 [10]. 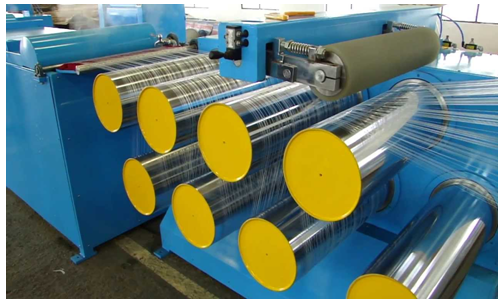 | Figure 7. Monofilaments extrusion process |
4.2. Strapping
Strapping is similar to slit film but fabrics here are thicker approximately in the order of 20 mils. Fibers are produced either from a direct extrusion or from slit sheets. Applications include securing large packages, boxes or to hold stacks together. The most important property of strapping fibers is strength where, sometimes, fabrics can replace steel [10].
4.3. Film
An extrusion process of PP produces films. Film is less than 10 mils thick. The film uses embrace food products, tobacco and clothing. There are two broad classes of films: cast films and oriented films [10]. Cast films are manufactured by depositing a layer of liquid plastic onto a surface and stabilizing this form by allowing melt to cool or by evaporation of solvent [4]. Film thickness is usually in the range of 1-4 mils. An important feature of cast films is softness. Both homo-polymers and random copolymers are used in cast films. Cast films are converted to products like bags, pages, sheet protectors, tapes and pressure-sensitive labels [10].Bi-axially oriented polypropylene film (BOPP) is another film type that is produced by extruding the plastic through a circular die followed by expansion cooling [4]. Two methods are widely used for producing BOPP films: tenter process (film thickness 0.5-2.5 mils) and tubular process (film thickness 0.25-2 mils). BOPP films have excellent clarity and gloss properties. They are printable when using some additional surface treatment technology. The main applications for BOPP films are in flexible packaging where the major use is in snack food packaging. BOPP film provides resistance to moisture vapor to keep snacks crisp and fresh tasting and provides a heat-sealable layer. Also, BOPP films are used in packaging of bakery products and many adhesive tapes. An opaque film is a special kind of BOPP which is used in packaging products such as candy, chocolate bars, soaps and labels on soft drink bottles [10]. Moreover, BOPP films are used in electrical applications to store energy. Still, hydroxylated polypropylene (PP-OH) is an optimum material to increase electric energy density. Dielectric constant (ε) of 4.6 is recorded for PP-OH that contains 4.2 mol% OH. A cross-linked polypropylene (x-PP) has a dielectric value (ε) around 3. Polypropylene network structure decreases loss of electricity and narrow breakdown distribution. Therefore, dielectric constant maintains constant over a wide range of temperatures (–20-100°C) and frequencies (0.1-1MHz). PP-OH is applied in various electrical applications as a reliable thin film energy storage capacitor with high releasing energy density > 7 J/cm3 upon an electric field of E = 600 MV/m. PP-OH dielectric constant and energy density values are better than those of BOPP by two to three times [21].
4.4. Sheet / Thermoforming
Thermoforming process involves heating of a thermoplastic sheet to its softening point followed by forming of the softened sheet into a desired shape by mechanical means and finally solidification into the desired shape [4]. Extrusion process produces a sheet that is greater than 10 mils in thickness and typical thickness is about 40 mils. Sheet width is usually between 2-7 ft. Sheets are used in the production of thermoformed containers for rigid packaging applications. Differences between PP and polystyrene in producing rigid packages perceived by noticing that PP resins resist the stress cracking in the presence of fatty products whereas polystyrene resins do not. PP is tougher and more rigid than polystyrene. Also, PP has lower specific gravity than polystyrene which allows us to manufacture lighter weight containers at the same thickness and shape [10].
4.5. Injection Molding
In this process, granules of polymer are heated until melting. Then, the molten material is injected into a closed mould. The mould normally consists of two halves which are held together under pressure to overcome the force of the melt. After that, the injected material is allowed to cool and solidify in the mould. The two halves of the mould are then opened and the molding is become out, Figure 8. Usually, mould shapes have very complex geometries that provide designers with infinite number of design possibilities [4]. Thin-wall injection molding is used for rigid packaging container applications. The thickness does not usually exceed 25 mils and often less than that. Rigid packaging containers are used in consumers’ items such as food storage containers and water bottles. Water bottles have many shapes and can be round, square, flat or tall. Injection molding is the best choice for producing containers with verities of shapes easily [10]. Housewares applications include storage systems, toys, sports equipment, paintbrushes and garden furniture [11]. Screw caps for bottles and jars are some examples of closures applications produced from PP. Further, injection molding includes some appliances and hand tools applications like coffee makers, can openers, blenders and mixers as well as different medical applications such as disposable syringes [10].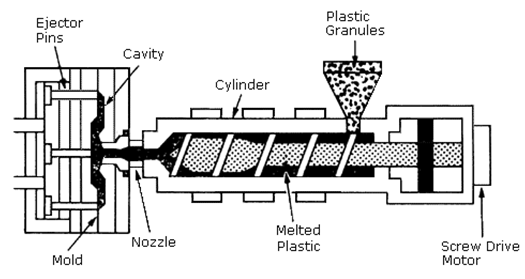 | Figure 8. Injection molding process [12] |
4.6. Blow Molding
The basic principle of blow molding process is to produce a hollow object by blowing a thermoplastic with hot air. A heated thermoplastic hollow tube is known as parison is placed inside a closed mould before blowing. The parison takes the shape of the mould, after blowing, and retains the shape upon leaving it. Bottles and jars are the main products of blow molding process [4]. There are three types of blow molding: extrusion blow molding in which produced PP bottles have hot-filling capability and good contact clarity, injection blow molding to produce relatively small bottles and wide-mouth jars and injection stretch blow molding to produce bi-axially oriented jars and bottles with greater clarity, strength and barrier properties [10]. Typical applications are water bottles, shampoo bottles and lubricant/pesticides containers [4].
4.7. Automotive
Polypropylene has a large presence in vehicles. For example, one of the original uses is in battery cases and AC ducts. Since PP is considered as the lightest thermoplastic due to its low density, 0.9 g/mL, much of the plastics in new cars are PP because car companies tend to reduce the overall weight of their cars to save some gas expenses for customers. Also, interior trim and several exterior components are made completely of PP or PP compounds. Interior trim like doors, pillars, quarter panels, and consoles are all molded of PP. Weight reduction has been an important factor so PP became a major material for automotive exterior parts. A special known material that is produced from PP called thermoplastic olefin (TPO) is used in car bumpers. TPO is also used in air dams, body side claddings, rocker panels and even grills in some vehicles [10]. A study in 2005 showed that the global consumption of polypropylene by end use application is primarily for injection molding and fibers, Figure 9 [8].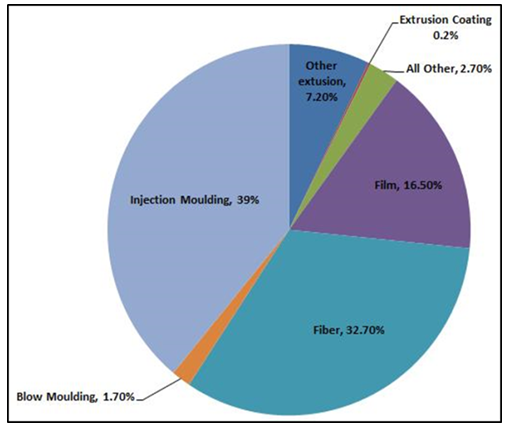 | Figure 9. Global consumption of polypropylene by end use application |
Polypropylene has many other applications associated with plastics in medical or laboratory tools, plastic tubs, plastic containers, wastebaskets, pharmacy prescription bottles, cooler containers, dishes, pitchers, rugs, insulation for electrical cables, stationery folders, storage boxes, light shades, loudspeaker drive units and water filters or air-conditioning-type filters. Furthermore, PP is used to produce clothes or even products related to clothing like diapers or sanitary products where PP is treated to absorb water (hydrophilic) rather than naturally repelling water (hydrophobic). PP is perfect for fabrication of cold-weather base layers and under-armor clothing. Another interesting PP application is called polypropylene sheet foam, Table 7 [13].Table 7. Applications of Polypropylene Sheet Foam 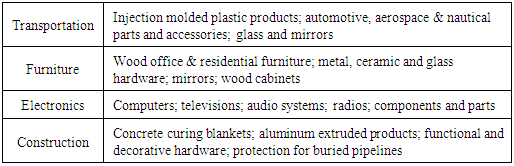 |
| |
|
5. Results and Discussion
High demands on polypropylene will lead petrochemical companies to invest in this business to produce essential goods to humanity around the world. The vast number of applications from PP showed that it is the ideal choice among all other polymers to produce flexible, long-lasing, cheap and light plastics for numerous industrial, commercial, medical and personal uses. Dow chemical company is a leading polypropylene technology licensor. Despite that there are other PP technologies provided by other parties, it is been proven that Dow’s technology (UNIPOL) is the optimal selection regarding to production costs, products qualities and grades. It is worth mentioning that Grace Corporation purchased Dow’s UNIPOL™ Polypropylene technology licensing business on Dec. 2, 2013 [14].Branching into a linear polypropylene produces plastics with high modulus and tensile strength, rigidity and excellent heat resistance. Polypropylene is very suitable for reinforcing and filling and this has been discussed by showing that fiber-reinforced polypropylene composites (FRPCs) have better durability, moisture resistance and high strength properties; and glass fibers produce very good mechanical properties composites. Further, electrically conductive PP and PE have outstanding electrical and mechanical properties. Despite the fact that recycling of polymers causes depletion in their optical properties, semi-crystalline isotactic polypropylene (iPP) showed excellent mechanical properties and appropriate optical characteristics upon recycling. We may overcome the issue of low temperature brittleness of PP by blending PP with various elastomers. A blend of 80/20 and 70/30 of PP/ISR-A have a very high impact strength of 83 and 100 J/m. Applications of PP are unlimited and they include fibers, strapping, films, sheets, injection and blow molding. Slit film, non-woven fabrics and monofilaments are all different types of fibers or fabrics. Polypropylene is a core material in many advanced plastics (modified for better properties) like BOPP and TPO. BOPP and PP-OH are ideal to be used as thin-film capacitors in electrical applications to store energy. Rigid packaging and houseware items are some applications of sheet and injections molding. Bottles and jars are the main products of blow molding technique.
6. Conclusions
By considering the global consumption of propylene, it is irrational to go for other products except polypropylene. The high consumption of propylene is due to the high production of polypropylene that is in need in many industries. There is no other plastic like PP which has a diversity in its applications. The unlimited number of PP applications makes it unique. The advancements in the production of PP since its discovery, 1954, are astonishing and should be continued to cover the expected increasing demands on PP. Branching, reinforcing and filling PP are some techniques to produce plastics with superior mechanical properties. Maintaining optical properties of a recycled PP is crucial. However, semi-crystalline isotactic polypropylene (iPP) showed appropriate optical characteristics upon recycling. Nevertheless, researchers should continue researching on the area of BOPP and PP-OH films are ideal plastics for electrical applications. PP compounds to produce better plastics for the future. In addition, studies are recommended to overcome small problems in processing polypropylene by developing new catalysts, enhancing yield and conversion percentages and reduce side products. Dow Company offers tens of grades of PP to the market, where each grade has a certain application. Thus, coming up with new polypropylene grades is vital for special kinds of applications and studies have to keep on track on those grades to have a perfect choice for future civilization necessities.
ACKNOWLEDGEMENTS
I am grateful to Saudi Aramco Company for providing me the opportunity to access polypropylene process manuals during my summer training. To all my family and friends, thank you for all the support.
References
[1] | “Home - Dynalon." N.p., n.d. Web. 12 Aug. 2011. < https://www.dynalon.com/PublicStore/>. |
[2] | “HMC Polymers.” Polypropylene. “N.p., n.d. Web. 15 Aug. 2011. . |
[3] | "Chemicals Prices, News and Analysis | Chemicals Market Intelligence | ICIS.com." N.p., n.d. Web. 16 Aug. 2011. http://www.icis.com/v2/chemicals/9076455/propylene/uses.html>. |
[4] | Introduction to Polypropylene, Saudi Aramco, PowerPoint Slides, 2010. |
[5] | Feasibility study report for production of 180,000 tons/year polypropylene by gas-phase polymerization in Jubail, Saudi Arabia, prepared by Al-Zamil Group, January 2001. |
[6] | "British Plastics Federation." Polypropylene (PP). N.p., n.d. Web. 13 Sep. 2011. . |
[7] | "The Human Element At Work." The DOW Chemical Company. N.p., n.d. Web. 15 Sep. 2011. . |
[8] | Pre-feasibility study for PDH/ACN/PP complex, volume I, Al-Zamil & Brothers Company, October 2004. |
[9] | Dow UNIPOL Technology Handbook, Polypropylene process, Chem systems, 2001. |
[10] | Karian, Harutun G. Handbook of Polypropylene and Polypropylene Composites. New York: Marcel Dekker, 1999. Print. |
[11] | "Polyolefins | Base Chemicals | Fertilizers | Borealis." N.p., n.d. Web. 23 Dec. 2015. . |
[12] | "Four Parts of a Used Injection Molding Machine." N.p., n.d. Web. 23 Aug. 2011. . |
[13] | "Pregis North America, Packaging Material, Protective Packaging Systems, Paper Packaging, Foam-in-place Solutions from Pregis Corporation." N.p., n.d. Web. 20 Sep. 2011. . |
[14] | "News Release." W.R. Grace -. N.p., n.d. Web. 23 Dec. 2015. . |
[15] | He, Chunxia, et al. "Molecular structure of high melt strength polypropylene and its application to polymer design." Polymer 44.23 (2003): 7181-7188. |
[16] | Shubhra, Quazi TH, A. K. M. M. Alam, and M. A. Quaiyyum. "Mechanical properties of polypropylene composites: A review." Journal of thermoplastic composite materials (2011): 0892705711428659. |
[17] | Andrady, Anthony L., and Mike A. Neal. "Applications and societal benefits of plastics." Philosophical Transactions of the Royal Society B: Biological Sciences 364.1526 (2009): 1977-1984. |
[18] | De Santis, Felice, and Roberto Pantani. "Optical Properties of Polypropylene upon Recycling." The Scientific World Journal 2013 (2013). |
[19] | Varga, József. "β-Modification of isotactic polypropylene: preparation, structure, processing, properties, and application." Journal of Macromolecular Science, Part B 41.4-6 (2002): 1121-1171. |
[20] | Gulrez, Syed KH, et al. "A review on electrically conductive polypropylene and polyethylene." Polymer Composites 35.5 (2014): 900-914. |
[21] | Chung, TC Mike. "Functionalization of Polypropylene with High Dielectric Properties: Applications in Electric Energy Storage." Green and Sustainable Chemistry 2.02 (2012): 29. |
[22] | Klein, Rolf. "Material Properties of Plastics." Laser Welding of Plastics: Materials, Processes and Industrial Applications (2011): 3-69. |
[23] | Galli, P., S. Danesi, and T. Simonazzi. "Polypropylene based polymer blends: fields of application and new trends." Polymer Engineering & Science 24.8 (1984): 544-554. |
[24] | Shibata, Mitsuhiro, Zhu Xiaochuan, and Ryutoku Yosomiya. "Impact properties of the polymer blend of polypropylene and thermoplastic elastomer." Journal of Macromolecular Science—Pure and Applied Chemistry 35.7 (1998): 1207-1215. |
[25] | Brydson, John Andrew. Plastics materials. Butterworth-Heinemann, 1999. |