Sherif M. A. S. Keshk1, 2, Mohamed S. Hamdy2, Ibrahim H. A. Badr3, 4
1Ain-Shams University, Institute of Environmental Studies and Research, Basic Science Department, Abbassia, Cairo, Egypt
2King Khalid University, Faculty of Science, Chemistry Department, Abha, Saudi Arabia
3Ain-Shams University, Faculty of Science, Chemistry Department, Abbassia, Cairo, Egypt
4Taibah University, Faculty of Science, Chemistry Department, Al-Madinah, Saudi Arabia
Correspondence to: Sherif M. A. S. Keshk, Ain-Shams University, Institute of Environmental Studies and Research, Basic Science Department, Abbassia, Cairo, Egypt.
Email: |  |
Copyright © 2015 Scientific & Academic Publishing. All Rights Reserved.
Abstract
Different strategy for successful synthesis of mercerized cellulose/TiO2 nano-composite is proposed in which amorphous TiO2 is directly embedded in the cellulose fiber without using any binder at room temperature. The crystalline structure, the particle size and the morphology of the prepared nano-composite were investigated using Fourier transformer infra-red (FTIR), X-ray diffraction (XRD), Field Emission Scanning Electron Microscopy (FESEM) and Energy-dispersive X-ray spectroscopy (EDX). The crystalline analysis had pointed out the dispersion of amorphous TiO2 particles between mercerized cellulose layers reducing its crystallite size to nano dimensions. A successful formation of mercerized cellulose/TiO2 nano-composite is confirmed from EDX analysis that illustrated a sharp peak attributed to Ti+4. Meanwhile, the as-fabricated mercerized cellulose/TiO2 by sol-gel method using NaOH as intermediate stage is considered a facile approach for synthesis of nano-composites of desired morphology and size without using chemical spacer. The photo-catalytic activity of the prepared composite was evaluated in the degradation of methyl orange (MO) dye under ultra-violet illumination. The results confirmed the self-cleaning property of the prepared nano-composite.
Keywords:
Cellulose composites, Thermal properties, Scanning electron microscopy, X-ray diffraction
Cite this paper: Sherif M. A. S. Keshk, Mohamed S. Hamdy, Ibrahim H. A. Badr, Physicochemical Characterization of Mercerized Cellulose/TiO2 Nano-Composite, American Journal of Polymer Science, Vol. 5 No. 1, 2015, pp. 24-29. doi: 10.5923/j.ajps.20150501.04.
1. Introduction
Hybrid inorganic/organic materials constitute a new class of functional nano-composites that exhibit high optical, thermal and mechanical properties due to the synergistic effects [1-4]. Natural cellulose is the most abundant polymer used in both industries and daily lives. Natural cellulose is a linear polymer of β-(1→4)-D-glucopyranose possessing abundant surface hydroxyl groups forming plentiful inter- and intra-molecular hydrogen bonds [4]. These hydroxyl groups provide a suitable substrate for metal oxide incorporation onto the cellulose surface. Moreover, the extensive hydrogen bond network builds up a defined hierarchical order of supra-molecular organization for providing a chamber with the formation of inorganic nano-materials. Incorporation of TiO2 to polymer casting solution greatly affected the morphologies and properties of the resulting composite. A wide range of applications can be obtained such as antimicrobial, anti-fungal, UV protective or self-cleaning properties. TiO2 is a promising metal oxide that is extensively involved in many industrial processes due to its stability, biocompatibility, non-toxicity and low cost [5–8]. Recently, many works have been devoted to anchored metal ions on the cellulose structure to improve its physical and mechanical properties. However, the poor thermal stability of textile requires low temperature to exhibit high activity. Anatase TiO2 sol could be prepared at a low temperature (80°C) using nitric acid to peptization of amorphous TiO2 Sol. Where, nano titania-cotton fibers with particle size smaller than 10 nm, chemical spacer have been used to attach Ti +4 to cotton [9]. TiO2 loaded cotton textile showed stable self-cleaning properties and allowed to eliminate partially the chromophore of the red wine under daylight irradiation. Gouda & Keshk (2010) have been prepared cotton fabrics coated with chitosan film containing titanium oxide and/or zirconium oxide for enhancing multifunctional properties [10]. The prepared fabric samples have a positive impact on UV-protection and the extent of protection follows the decreasing order: Ti > Zr > Ti/Zr > Zr/Ti > chitosan film > none. Abedini et al (2011) indicate that, the thermal stability of cellulose membrane was improved by adding TiO2 to cellulose acetate solution during synthesis of hybrid cellulose/TiO2 [11]. Where, TiO2 nanoparticles were located on the surface of the fibers and the resulting membrane become more porous [11]. Moreover, newly synthesized SiO2 surface treated TiO2 nanoparticles (TiO2/SiO2) that characterized and utilized in functional dyeing as combined reactive dyeing of cotton fabrics [12]. These results, indicate a pronounced improvement in the UV protection, comfort, and dyeing properties that governed by the reactant concentrations and the dyeing temperature [12]. Li et al (2013) purposed a new strategy to prepare hybrid nano-composites from cellulose and TiO2 using tetra-n-butyl titanate and cellulose solution via a hydrothermal method at 180◦C for 24 h [13]. The composite obtained exhibited high antibacterial effect. The incorporation of titanium onto cellulosic substrates has still continuously growing attention. In all previous research works, it is essential to add spacer for binding titanium with cellulose matrix [9-12]. Mechanical mixing of cellulose fibers and TiO2 powders lead to formation of poorly dense agglomerations that lead to reduce its industrial applications. The proper way to overcome such a limitation must be sol-gel synthesis of titanium hydroxide that imposed Ti4+ in the cellulose fiber cell walls. Such a hybrid entity would benefit from the synergistic effect of the physical and/or chemical interactions between the organic and inorganic components. To develop a strategy to synthesize the cellulose-based nano-composites and open a new avenue to high value added applications of biomass. Herein, the reaction of titanium ions with mercerized cellulose without any spacer will be illustrated to prepare a new nano-composite. The physicochemical features of the prepared nano-composite will be investigated using FT-IR, XRD, EDX and FESEM.
2. Experimental
2.1. Materials
Cellulose fiber were supplied from Vimal Indian fiber factory and used as received. Sodium hydroxide and TiCl4 were supplied by Sigma-Aldrich. All experiments were conducted under ambient atmosphere.
2.2. Composite Preparation
Cellulose fiber was first dispersed in water for 24 h. Then 0.5 g of wet cellulose was immersed in 10% and 20% NaOH for 24 h. About 2 ml of TiCl4 dissolved in ethanol was added to cellulose followed by addition of few drops of ammonia solution [1M] until a colloidal Ti(OH)4 sol can be observed. Then, the samples are washed well by distilled water till neutralization then dried at room temperature.
2.3. Nano-Composite Characterizations
Fine and homogeneous powders of the different samples were back-loaded into the sample holder of a P Analytical X’PERT MPD diffractometer using Cu (Kα1/Kα2) radiation. The XRD patterns were recorded in a diffraction angle range from 20° to 100° with a step of 0.03° and integration time of 4 seconds per step. The diffraction patterns have been treated with the Rietveld refinement method using the MAUD program. The instrumental imperfections were evaluated with a sample of LaB6 calibrated against a sample of NIST SRM-640b and provided by the Gem Dugout Company. Fourier-transform infrared (FTIR) spectra were measured at room temperature on an ATT Mattson series FT-IR TM spectrophotometer using the KBr disk technique. The evolution of the morphology of the samples was examined by Field emission scanning electron microscopy (FESEM) images obtained on a FESEM JEOL 6340electron microscope equipped with an EDAX energy dispersive X-ray analysis (EDX) to investigate the elemental composition of the system.
2.4. Self-Cleaning Property Evaluation
The photo-catalytic performance of the cellulose/TiO2 nano-composite was evaluated in the decolourization of Methyl Orange (MO) dye. In a typical experiment, 0.1 g of the wet nano-composite was introduced into a quartz cuvette containing 1.5 ml of MO solution (10 mg/L). The solution was kept in dark for 1 hour to study the chemisorption. Then the solution was irradiated from the top with UV light (18W, λ = 375nm). The intensity of the dye’s colour was evaluated in UV-Vis spectroscopy in the range between 200-600 nm. The first order rate constant (kα) was then determined using the following equation (1): | (1) |
Where, C0: represents the concentration of MO after chemisorption and C: is the concentration at time (t).
3. Results & Discussions
3.1. The Morphology of the Composite
FT-IR spectra of the cellulose and cellulose/TiO2 nano-composite samples in different concentration of sodium hydroxide at room temperature were recorded in the range from 4000 to 4.00 Cm-1. The spectrum of cellulose (Figure 1) shows five characteristics peaks between 980 Cm-1 and 1160 Cm-1 corresponding to C-O bond stretching. The band at 1160 Cm-1 is assigned to the C-O-C asymmetric stretching and the peaks at 1315 Cm-1 and 1430 Cm-1 are attributed to CH2 wagging symmetric bending and CH2 asymmetric bending, respectively [14]. When the concentration of sodium hydroxide was increased from 10% to 20% during the addition of TiCl4, the FT-IR spectra of samples were shown in Figure (1). Both of the nano-composite samples at different concentrations of NaOH had similar FTIR spectra (Figure 1) and had differences comparing with cellulose. However, when the concentration of NaOH was increased , the peak intensity at 1030 Cm-1, 1430 Cm-1 and 3400 Cm-1 dramatically decreased (Figure 1), indicating decreasing cellulose concentration in the cellulose/TiO2 composite. Moreover, the band at 3400 Cm-1 became broader with addition of TiCl4 than that of cellulose due to the interaction between the cellulose and TiCl4 to produce cellulose/TiO2 nano-composite. Similar results, were reported for cellulose/ CuO or Fe2O3 nano-composites [15]. 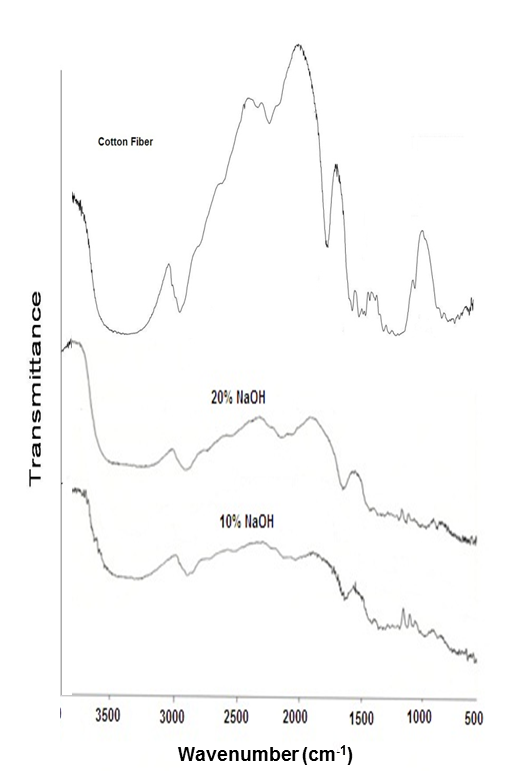 | Figure 1. FT-IR spectrum of cotton fiber is compared with the spectra of the treated fiber immersed in 10 and 20% NaOH |
Figure (2) illustrates the XRD patterns of as-prepared nano-composites; cotton and pure TiO2 to investigate the influence of TiO2 on the nature and size of the crystalline phase. Relatively broad peak characteristics indicate the existence of cellulose particles in nano dimensions with a crystallite size about of 22-41 nm. The disappearance of titania crystalline phases suggesting that the TiO2 particles are present in amorphous phase that may be coating cellulose particles and preventing their growth. The X-ray pattern of cotton linter (Fig.2) clearly exhibits the typical diffraction peaks at 14.8°, 16.3° and 22.5°, that belong to the (101), (101-) and (020) planes of crystalline structure of cellulose I [16]. In contrast, mercerized cellulose (10% and 20% NaOH) (Fig.2) exhibits the typical diffraction peaks at 2θ=12.03°, 20.1° and 21.5° that belong to (101), (101-) and (020) planes of the crystalline structure of mercerized cellulose [17].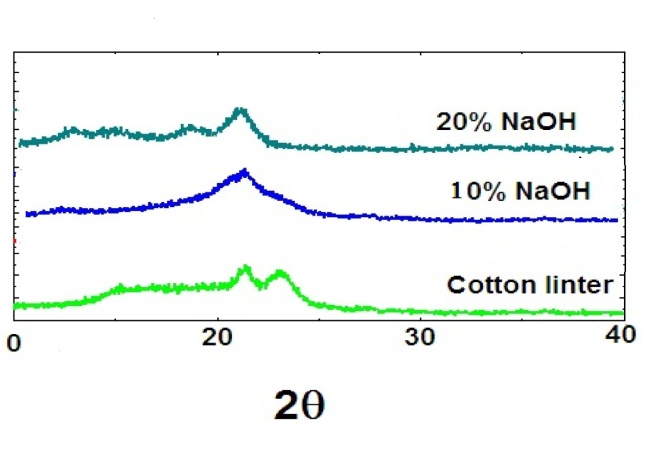 | Figure 2. XRD of cotton fiber compared with the treated cotton fiber immersed in 10 and 20% NaOH |
DSC analysis was performed to determine thermal behavior of the prepared samples. Figure (3) demonstrates DSC data for cotton fiber and treated with 10% and 20% NaOH respectively. For all samples, the curve displays a stage at T < 150°C which is attributed to removal of physically adsorbed water and results in an endothermic peak centered at 90°C in the DSC data. The second stage involves de-hydroxylation of titanium hydroxide and formation of titania which is accompanied by formation of an endothermic peak at 340-341°C due to de-hydroxylation of titanium hydroxide and exothermic peak at 435 -450°C due to crystallization of titania. The results of DSC studies indicate that heating the dried gels at temperature below 500°C is sufficient to complete all reactions. That is, further heating (above 500°C) of the dried gels did not show any thermal and/or weight changes. 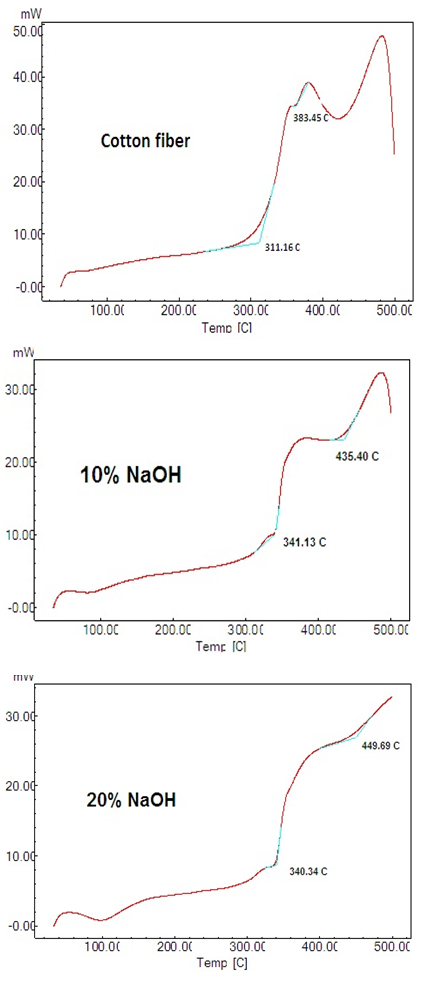 | Figure 3. DSC patterns of untreated cotton (top panel), treated cotton with 10% NaOH (middle panel) and 20% NaOH (bottom panel) |
Figure (4) displays the FESEM micrographs to investigate the influence of TiO2 nanoparticles on the samples morphology. It is clear from this figure the existence of large number of rods dispersed homogeneously through the whole matrix. In the photograph of the cellulose fiber, the cellulose fiber is fluffy, similar to raw cotton, with lustrous, curly fibers running throughout the solid matrix. These millimeter-long fibers also exhibited a very straight and smooth surface; no defects were observed at the cellulose surface. The sample morphology is not affected by existence of NaOH. However, a pronounced reduction in the size of cotton fibers is observed upon addition of NaOH. Moreover, in the sample that treated with 10% NaOH, (middle panel, Figure 4), TiO2 particles are observed very clearly.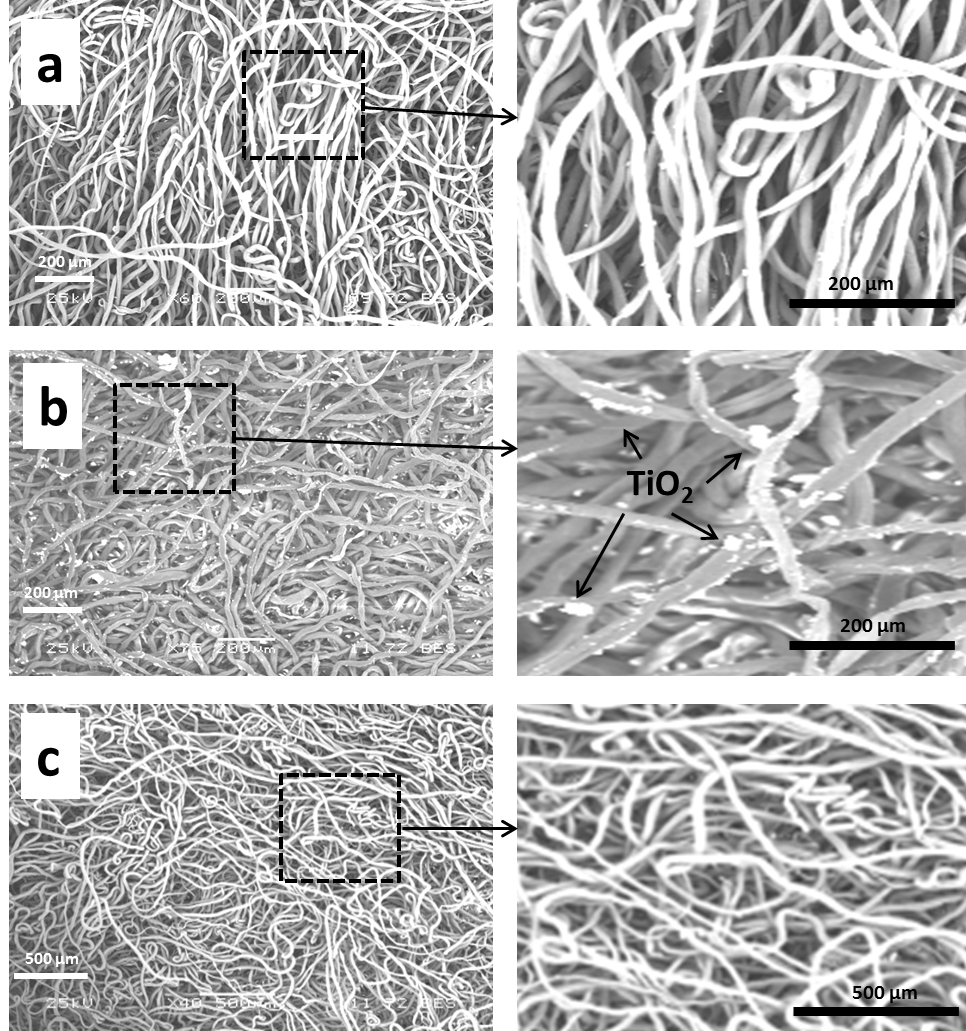 | Figure 4. FE-SEM of cotton fiber (a), cotton fiber treated by 10% NaOH (b) and 20% NaOH (c) |
The EDX analysis is performed and represented in Figure (5) to investigate the elemental composition of the nano-composites and to ensure the presence of Ti ions as an indication for the presence of TiO2 particles embedded in the cotton fiber. The EDX spectrum exhibited various intense peaks that are associated with Ti, O and C atoms for the samples. It is obvious to notice the presence of Ti ion peaks.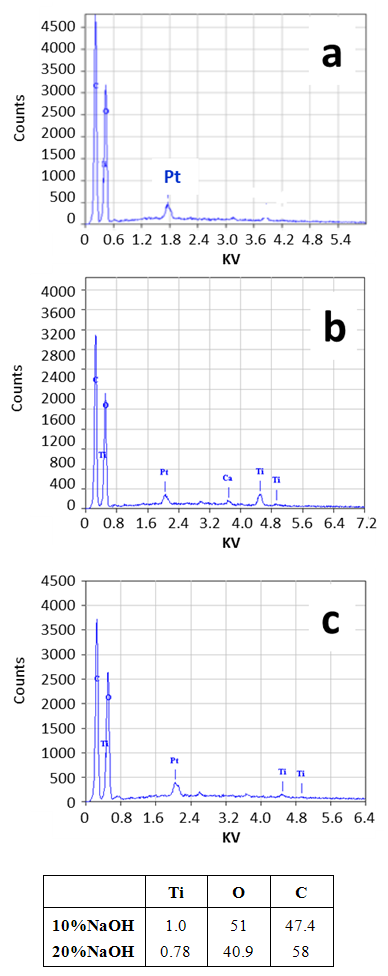 | Figure 5. EDX of cotton fiber without any treatment (a), cotton fiber treated by 10% NaOH (b) and 20% NaOH (c) |
The fabrication of titanium dioxide nanoparticles attach directly between cellulose matrixes especially to the primary OH groups that dispersed in cellulose structure is not simple. The traditional methods involve using a chemical spacer that require high temperature that may lead to destroy a cellulose structure during the progress of calcination. In our route, the greet inclusion of titanium dioxide between mercerized cellulose sheets happened. This result can be explained by presence of Na ion increases the distances between mercerized cellulose sheets more than that in non-treated cellulose, so, it eases inclusion of titanium dioxide between cellulose sheets. 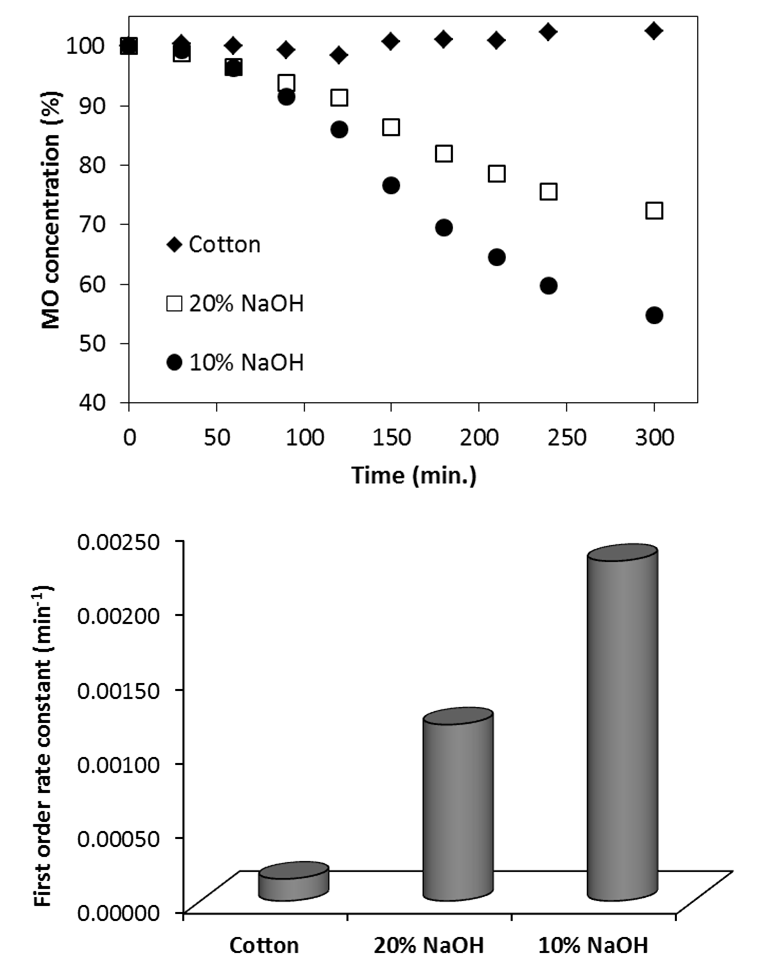 | Figure 6. Top: the decolorization profile of MO over cotton (un-treated and treated) fiber. Bottom: The first order rate constant of the MO decolorization catalyzed by the un-/treated cotton fiber |
3.2. Self-Cleaning Property of Cellulose/TiO2 Composite
The degradation of MO dye in contact with the untreated cotton and the treated ones is presented in Figure (6), top panel. The untreated sample did not exhibit any photo-catalytic activity. That was expected and it is in agreement with the previous reports [18]. However, the treated samples exhibited a photo-catalytic activity and the color of the dye was discharged under the effect of UV. The photo-catalytic performance of the sample treated with 10% NaOH was higher than the sample treated with 20% NaOH, this is most likely due to the strong interaction between NaOH and TiCl4 that results the less contacting with cellulose owing to formation of Ti(OH)4. The loading of TiO2 in samples was the same after washing several times that prove the stability of TiO2 on cellulose as observed by EDX analysis.
4. Conclusions
In this paper, TiO2/cellulose inorganic–organic hybrid nano-composites were successfully prepared by sol-gel method using different compositions of NaOH. The structural and crystalline features of the nano-composites were investigated using FESEM, FTIR, EDX and XRD techniques. Adding TiO2 to cellulose are greatly affected the morphologies and the crystalline properties of the resulting nano-composite. The XRD and EDX results revealed that the TiO2 dispersed on the surface and in the interior of the cellulose due to the TiO2 conglomeration. The crystalline analysis confirms the distribution of titanium ions between cellulose layers. FTIR analysis confirms that Ti4+ ions replace the Na ions of mercerized cellulose structure. The sample treated with 10% NaOH was found to be more photo-catalytically active than the sample treated with 20% NaOH.
ACKNOWLEDGMENTS
Authors would like to thank King Abdul Aziz City for Science and Technology for their miscellaneous help during this study. This project (AT-34-95) was supported by King Abdul Aziz City for Science and Technology (KACST). 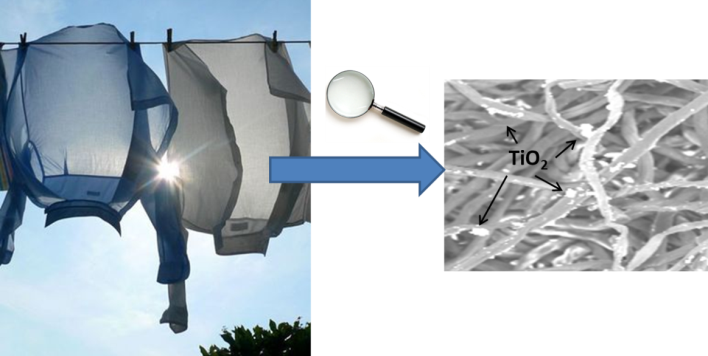 | Graphical Abstract |
References
[1] | P.A.A.P. Marques, T. Trindade, C.P. Neto, Compos. Sci. Technol., 66 (2006) 1038–1044. |
[2] | J.H. Clark, Green Chem., 8 (2006) 17–21. |
[3] | J.S. Zhou, J. Qi, L. Zhang, J. Appl. Polym. Sci., 101 (2006) 3600–3608. |
[4] | A.A. Hebeish, M.M. Abdel Hady, A.M. Youssef, Carbohydrate Polymers 91 (2013) 549–559. |
[5] | X. Chen, S.S. Mao, Chem. Rev., 107 (2007) 2891–2959. |
[6] | J. Ryu, W. Choi, Environ. Sci. Technol., 1072(2008) 294–300. |
[7] | P. Salvador. J. Phys. Chem. C 111 (2007) 17038–17043. |
[8] | T. Nanba, S. Masukawa, J. Uchisawa, A. Obuchi, Appl. Catal. A. 419 (2012) 49–52. |
[9] | K.T. Meilert, D. Laubb, J. Kiwi. J. Mol. Catal. Chem. 237 (2005) 101–108. |
[10] | M. Gouda, S.M.A.S. Keshk, Carbohydrate Polymers 80 (2010) 504–512 |
[11] | R. Abedini, M. Mousavi, R. Aminzadeh, Desalination 277 (2011) 40–45. |
[12] | D. Fakin, N. Veronovski, A. Ojstrseka, M. Bozic, Carbohydrate Polymers 88 (2012) 992–1001. |
[13] | S.M. Li, Y.Y. Dong, M.G. Ma, L.H. Fu, R.C. Sun, F. Xu, Carbohydrate Polymers 91 (2013) 15–20. |
[14] | S.M.A.S. Keshk. Carbohydrate Polymers 74 (2008) 942-945 |
[15] | M. Guo Ma, S. Qing, S. Mingli, J. Zhu, L. Hua, R. Sun, Carbohydrate polymer, 91 (2013) 162-168. |
[16] | Y. Nishiyama, P. Langan, H. Chanzy. Journal of the American Chemical Society. (2002)124, 9074-9082. |
[17] | H. Nishimura, T. Okano, A. Sarko, Mercerization of cellulose: Macromolecules (1991)24, 759–770. |
[18] | K.T. Meilert, D. Laub, J. Kiwi, Journal of Molecular Catalysis A: Chemical (2005) 237, 101–108. |