D. C. Anike1, T. U. Onuegbu1, I. M. Ogbu2, I. O. Alaekwe1
1Department of Pure and Industrial Chemistry, Nnamdi Azikiwe University Awka, Anambra State, Nigeria
2Department of Chemistry Federal University Ndufu-Alike, Ikwo Ebonyi State, Nigeria
Correspondence to: D. C. Anike, Department of Pure and Industrial Chemistry, Nnamdi Azikiwe University Awka, Anambra State, Nigeria.
Email: |  |
Copyright © 2014 Scientific & Academic Publishing. All Rights Reserved.
Abstract
The effects of alkali treatment and fibre loads on the properties of raffia palm fibre polyester composite were studied. Some clean raffia palm fibres were treated with 10% NaOH, and ground. The ground treated and untreated fibres were incorporated into the ortho unsaturated polyester resin. The treated and the untreated fibre composites samples were subjected to tensile tests according to ASTM D638 using instron model 3369. The microhardness test was done by forcing a diamond cone indenter into the surface of the hard specimen, to create an indentation. The significant findings of the results showed that alkali treatment improved the microhardness and extension at break at all fibre loads, better than the untreated fibre composites, with the highest values at 20% (14.40 and 3.47mm for microhardness and extension at break respectively). Tensile strength, tensile strain and modulus of elasticity also improved for alkali treated fibre composites, except in 5% and 20% for tensile strength, 15% for tensile strain, and 15% and 20% for modulus of elasticity, compared to the corresponding fibre loads of untreated fibre composites.
Keywords:
Raffia palm fibre, Composite, Ortho unsaturated polyester, Alkali treatment
Cite this paper: D. C. Anike, T. U. Onuegbu, I. M. Ogbu, I. O. Alaekwe, The Effect of Alkali Treatment on the Tensile Behaviour and Hardness of Raffia Palm Fibre Reinforced Composites, American Journal of Polymer Science, Vol. 4 No. 4, 2014, pp. 117-121. doi: 10.5923/j.ajps.20140404.03.
1. Introduction
The application of natural fibres as replacement to conventional or artificial fbres in fibre-reinforced polymer composites has received increased attention in industries, and academic institutions, as well [1]. Natural fibres have many significant advantages over synthetic fibres. Currently, many types of natural fibres have been investigated for use in plastics. These include flax, hemp, jute straw, wood, rice husk, wheat, barley, oats, rye, cane (sugar and bamboo), grass, reeds, kenaf, ramie, oil palm empty fruit bunch, sisal, coir, water, hyacinth, pennywort, kapok, paper mulberry, raphia, banana fibre, pineapple leaf fibre and papyrus [2]. The growing interest in using natural vegetable fibers as a reinforcement of polymeric based composites is mainly due to their renewable origin, environmental friendliness, biodegradability, abundantly available, cheap and low density [3-5]. The reinforcement of polyester with various cellulosic fibers has been widely reported [2]. Rajulu et al. used bamboo fibers as reinforcement with epoxy/unsaturated polyester blend and studied the tensile properties and chemical resistance of the resulting composites [6]. The main drawbacks of such composites are their water sensitivity, their relatively poor dimensional stability, the changing of fiber characteristics with origin, poor adhesion to basically all matrix polymers, and poor processability at high fiber contents [7]. All plant-derived cellulose fibers are polar and hydrophilic in nature, mainly as a consequence of their chemical structure [8]. Chemical pretreatment of the natural fibre can help to overcome such drawbacks to enhance the compatibility between fibre and the matrices, resulting in improved performance of fibre-reinforced composites [9]. Natural fibres have a good potential for chemical treatment due to presence of hydroxyl groups in lignin and cellulose. Reaction of hydroxyl groups can change the surface energy and the polarity of the natural fibres [8]. In pretreatment of natural fibre, either the hydroxyl groups get activated or new moieties are added that can effectively interlock with the matrix [10]. Different surface treatment methods such as mercerization (alkali treatment), isocyanate treatment, acrylation, benzoylation, latex coating, permanganate treatment, acetylation, silane treatment and peroxide treatment have been applied on the fibre to improve its strength, size and its shape and the fibre-matrix adhesion [11].Alkali treatment of natural fibres is known to improve the stiffness, strength, and dynamic flexural moduli of the composites, indicating an increased interfacial bond strength and adhesion between the matrix and the fibres [12]. lkaline processing directly influences the cellulosic fibril, the degree of polymerization and the extraction of lignin and hemicellulosic compounds [13].The aim of this work is to investigate the effect of alkali treatment on tensile properties and microhardness of raffia palm fibre ortho-unsaturated polyester composites.
2. Materials and Methods
2.1. Material
The raffia palm fibres were collected from raffia palm trees around a stream at Emene, Enugu state. The ortho-unsaturated polyester resin, methyl ketone peroxide, MEKP (catalyst) and cobalt octoate (accelerator) were bought from Polyconsult venture (25 ogunleti street), Ojota Lagos.
2.2. Methods
a) Preparation of materialsThe pinnate leaves of the raffia palm (Raphia) were pulled out from the leaf stalks. Thereafter, the raffia fibres were taken off from the pinnate leaves. The fibres were washed thoroughly and allowed to dry under the sun.b) Chemical Pretreatment of the FibresThe raffia palm fibres were divided into two (2) portions. One portion was treated using alkali treatment method; also know as mercerization, while the other portion was left untreated.Alkali Treatment (Mercerization)The clean raffia palm fibres were soaked in 10% NaOH solution for I hour at 30℃. Later, the alkaline treated fibres were washed thoroughly in plentiful of distilled water to remove the excess NaOH (or non reacted alkali). The fibres were drained and sun dried.Thereafter, the fibres (alkali treated and untreated) were taken to electric oven, where they were oven-dried at 70℃ for 2 hours. The oven-dried fibres were ground into small particle sizes. c) Preparation of the CompositePolyvinyl Alcohol (PVA), was first applied on all the surfaces of the mould, and allowed to dry. A thin film was formed on the mould when the PVA dried. The film formed acts as the mould releasing agent. Thereafter the unsaturated polyester resin was mixed with different loads of the raffia palm fibres, following the procedure below.First, the unsaturated polyester resin was weighed in a glass beaker, using a digital weighing balance. 2% (by weight of the polyester) of the catalyst, methyl ethyl ketone peroxide (MEKP) was added and the mixture was stirred for 2 mins. After which, 1% (by weight of the polyester) of the accelerator cobalt octoate, was added and stirred for additional 2 mins. The fibre was then added gradually and stirred properly until a homogenous mixture was observed. Then, the prepared formulation was poured into the mould, and allowed to cure for one hour. When fully hardened, the composites were carefully removed from the mould and the overflow flakes were trimmed off. The procedure above was repeated for all the fibre loads of 5%, 10%, 15% and 20%, both for the alkali treated and untreated fibres. The formulation used is shown in table 1. Table 1. Formulation of Fibre-Polyester Composites 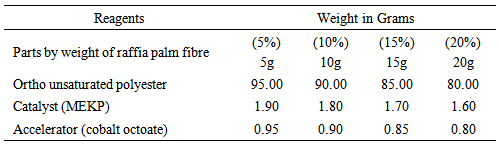 |
| |
|
2.3. Characterization of the Samples
Tensile Tests: Test for tensile test was done using Instron Universal testing machine (3369 model), as described in ASTM method D638.Each tensile specimen was positioned in the Instron Universal tester and then subjected to tensile load. As the specimen stretches, the computer generates the graph as well as all the desired parameters properties of the specimen fractures. The various properties determined include; ultimate tensile strength, modulus of elasticity, tensile strain, extension at breaks. Microhardness test: The hardness test was carried out using microhardness tester, LECO/M700AT. The test was done by forcing a diamond cone indenter into the surface of the hard specimen, to create an impression.
3. Results and Discussion
The test results of the tensile properties and the microhardness of the composite samples are shown in table 2, and fig 1-5.Table 2. Results of the Tensile Properties and Microhardness of the Composites 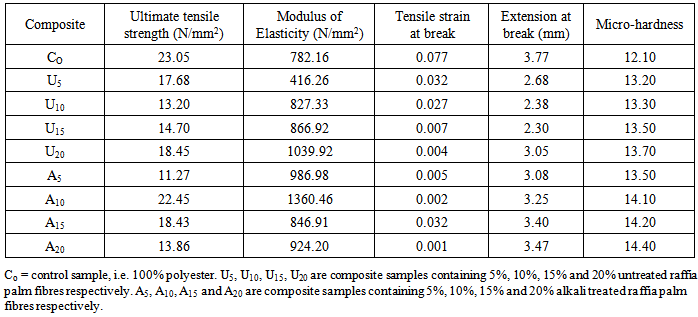 |
| |
|
Fig.1 shows the ultimate tensile strength of the composites. From the graph, the ultimate tensile strength for 5% (17.68N/mm2) and 20% (18.45N/mm2) untreated fibre composites increased more than the 5% (11.27N/mm2) and 20% (13.86 N/mm2) alkali treated, whereas the 10% (22.45 N/mm2) and 15% (18.43 N/mm2) of the alkali treated fibre composites increased more than the 10% (13.20 N/mm2) and 15% (14.70 N/mm2) untreated fibre composites.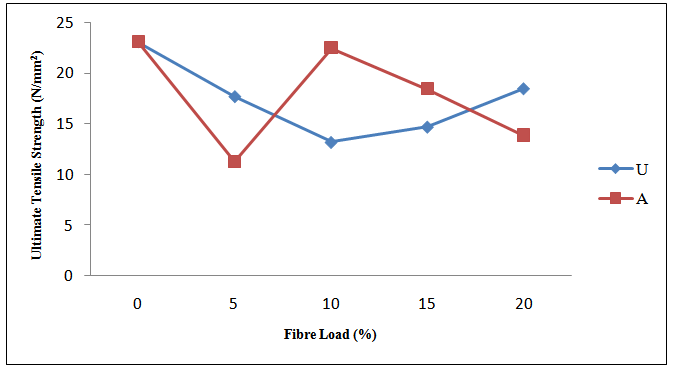 | Figure 1. Effect of Fibre Loads on tensile strength |
However, the control sample (0%) gave a higher value of ultimate tensile strength more than the untreated and treated composites for the fibre loads considered. This implies that treatment, as well as fibre loads studied, did not improve the ultimate tensile strength.From Fig .2, the modulus of elasticity of the composite samples increases as the fibre load increases, for all the untreated fibre composites. There is a significant decrease at 15% fibre loads (846.91N/mm2) of alkali treated fibre composites.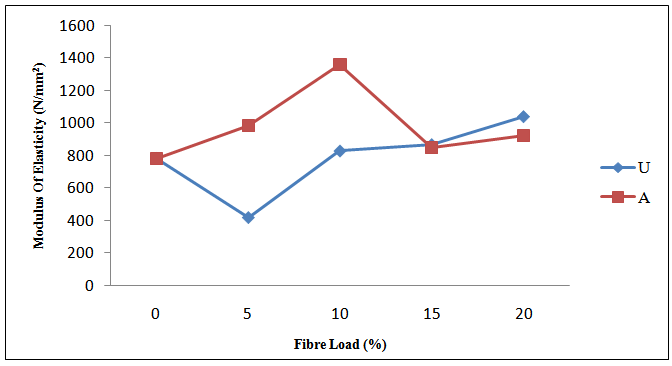 | Figure 2. Effect of Fibre Loads on modulus of elasticity |
The modulus of elasticity of the alkali treated fibre composites of only 5% (986.98N/mm2) and 10% (1360.46N/mm2) are better than the corresponding 5% (416.26N/mm2) and 10% (827.33N/mm2) untreated fibre composites.Fig .3 shows that the tensile strain decreases as the fibre load increases for both the untreated and treated fibre composites, except a rise at 15% (0.032) of the treated fibre composite. This implies that except for the 15% fibre load of treated fibre composites, the untreated fibre composites are more prone to deformation.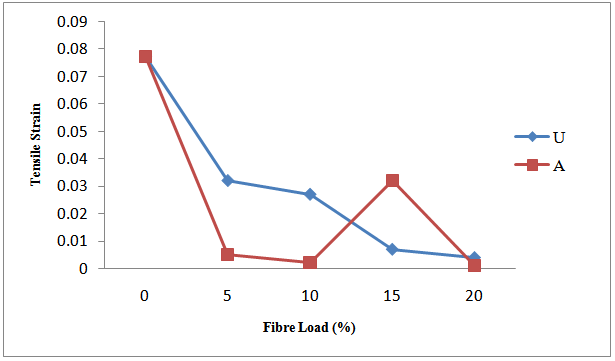 | Figure 3. Effect of Fibre Loads on tensile strain |
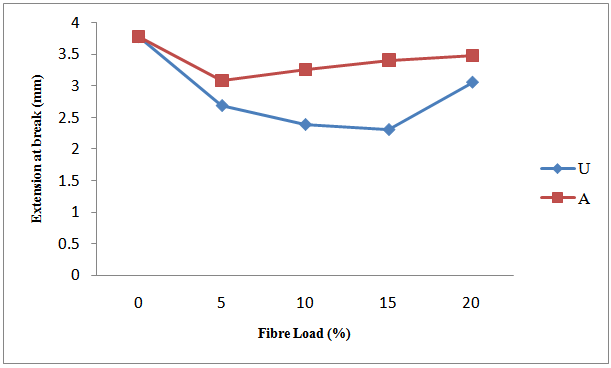 | Figure 4. Effect of Fibre Loads on Extension at Break |
The extension at break for untreated fibre composites decreases as fibre load increases from 5% to 15%. The graph shows that the extension at break for treated samples generally increases with increase in fibre load, and that even the 5% (lowest fibre load) of the treated has higher value than all fibre loads of the untreated samples.Here again, the control sample (0%) has a higher value than all the fibre loads (5%, 10%, 15% and 20%) for the untreated and treated fibre samples.Fig. 5 shows the effect of the treated and untreated fibres, at different fibre loads, on the microhardness of the composites.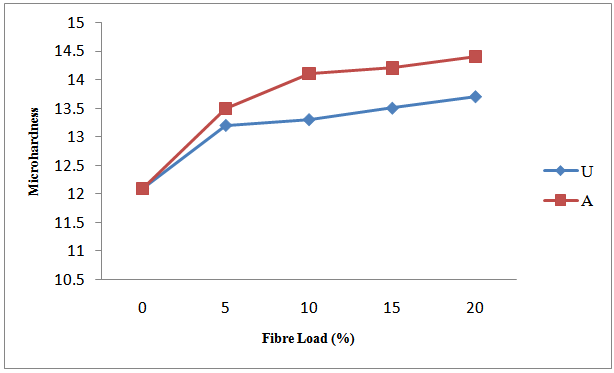 | Figure 5. Effect of Fibre loads on the Microhardness |
From the graph, it can be seen that treatment as well as increase in fibre load increases the microhardness of the composites. The microhardness for each fibre load of the treated fibre composite improved, more than the corresponding untreated ones.
4. Conclusions
From the results obtained, it can be established that the alkali treated fibre showed better reinforcing properties than the untreated fibre, for almost all the properties studied. At all corresponding fibre loads, the extension at break, as well as the microhardness results of alkali treated composites, improved better than the untreated ones. Only the alkali treated fibre composites of 10% and 15% gave improved tensile strength than the corresponding untreated fibre composites. For modulus of elasticity, 10% fibre load gave the highest value (1360.46N/mm2) for treated fibre composite.
5. Recommendations
We recommend that raffia palm fibre should be implored as natural fibre for reinforcement, but that large set of samples (many different fibre loads), and that short particle length of the fibre, instead of ground ones be considered.
ACKNOWLEDGEMENTS
The authors wish to thank the staff of Engineering Material Development Institute, Akure where the samples were prepared and characterized.
References
[1] | Onuegbu T. U., Umoh E.T. & Okoroh N. C., 2013, Tensile Behaviour and Hardness of Coconut Fibre-Ortho Unsaturated Polyester Composites. Global Journal of Frontier Research, 13(1): 1-10. |
[2] | Depeepya M., Raju T.D., & Jayananda T., 2012, Effect of alkali treatment on Mechanical and Thermal Properties of typha Angustifolia Fibre Reinforced Composites. Int. J. Mech. Ind. Eng (IJMIE), 1(4):12-14. |
[3] | Joseph P.V., Rabello M.S., Mattoso L.H.C., Joseph K. and Thomas S., 2002, Compos. Sci. Technol. 68, 1357. |
[4] | Van V. B., Smit H.G., Sinke R.J., D Klerk B., 2001, Compos A: Appl Sci Manuf 32:1271. |
[5] | Devi L., Bhagawan S. and Thomas S., 1997, Mechanical Properties of Pineapple leaf Fibre-reinforced Polyester Composites. J. Appl. Polym. Sci. 64; 1739-1748. |
[6] | Rajulu A.V., Devi L.G., Rao G.B., Reddy R.L., 2003, Journal of Reinforcement Plastics and Composites 22, 1029. |
[7] | Nekkaa S., Guessoum M., Chebira F. and Haddaoui N., 2008, “Effect of fiber content and chemical treatment on the thermal properties of spartium junceum fiber-reinforced polypropylene composites,” International Journal of Polymeric Materials. 57(8).771–784. |
[8] | Hetal S., Srinivasulu B. and Subhas S., 2012, The Effect of Surface treatment on the Properties of Woven Banana Fabric based Unsaturated Polyester Resin Composites. International Journal of Scientific Engineering and Technology.1 (3). 86-90. |
[9] | Beg M.D and Pickering K.L., 2004, Effect of Fibre Pretreatment on the mechanical properties of wood / polypropylene composites. Proceedings of SPPM. Dhaka. 240 - 247. |
[10] | Ganan P. and Mondragon L., 2004. Fibre-Reinforced Polyester Composites. Effects of Fibre Surface-Treatment on Mechanical Behaviour. Journal of Material Science 39(9). 1573-4803. |
[11] | Luo S. and Netravali A. N., 1999., Mechanical and Thermal Properties of Environmentally Friendly Green Composites made from Pineapple leaf fibres and Ply(hydroxybutyrate- co-valerate) Resin: Polymer Composites 20(3). 367-378. |
[12] | Aziz, S. H., and Ansell, M. P., 2004, The effect of alkalization and fibre alingnment on the Mechanical and Thermal Properties of Kenaf and Hemp bast fibre Composites: Part I- Polyester resin matrix,” composites:science and technology 64(9), 1219-1230. |
[13] | Jahn A, Schroder MW, Fu¨ ting M, Schenzel K, Diepenbrock W., 2002, Spectrochim Acta A: Mol Biomol Spectrosc 58:2271. |