Mohammed Zubair1, Farusil Najeeb1, Mousim Mohamed1, Ayman Saeed1, Ramis M. K.1, Abdul Mujeeb M. S.1, B. K. Sarojini2
1Department of Mechanical Engineering, P A College of Engineering, Mangalore, 574153, India
2Department of Chemistry, Mangalore University, Mangalore, 574153, India
Correspondence to: Ramis M. K., Department of Mechanical Engineering, P A College of Engineering, Mangalore, 574153, India.
Email: |  |
Copyright © 2014 Scientific & Academic Publishing. All Rights Reserved.
Abstract
Chitin is a naturally abundant mucopolysaccharide which by the process of N-deacetylation gives the polymer Chitosan. High percentage of nitrogen compared to synthetically substituted cellulose gives an added commercial edge for the polymer. Chitosan is very relevant in terms of wide availability and reduced cost of the raw material. Enhanced properties of chitosan can be exploited for wider applications strengthening its existing vital role in medical and waste water treatment. Objective of the investigation carried out in this work is to study the effect of nano-copper oxide (CuO) and nano-aluminium oxide (Al2O3) particles on the mechanical properties of chitosan. Chitosan nano films have been fabricated by solution casting process using acetic acid as a solvent. Each film was tested for its Tensile Strength, Young's modulus, Stiffness and Elongation at Fracture. It is observed that, the polymer when doped with Al2O3, CuO nano particles show favourable properties only upto a certain composition limit.
Keywords:
Chitosan, Nano-CuO, Nano-Al2O3
Cite this paper: Mohammed Zubair, Farusil Najeeb, Mousim Mohamed, Ayman Saeed, Ramis M. K., Abdul Mujeeb M. S., B. K. Sarojini, Analysis of Chitosan Polymer Doped with Nano Al2O3 and Nano CuO, American Journal of Polymer Science, Vol. 4 No. 2, 2014, pp. 40-45. doi: 10.5923/j.ajps.20140402.03.
1. Introduction
Polymers are large molecules that are formed of long chains of covalently bonded repeating units (monomers) on a carbon chain backbone. The chain can have an array of branching functional groups like hydroxyl, methyl, carboxyl, amine etc. Chemical, physical properties of polymers depend, mainly, on the type of functional groups on the polymer chain. Cross linking of polymer chains, is another important parameter to alter the polymer’s properties. By processing polymers through various functionalization and cross linking techniques, much of the polymer properties can be matched for specific applications. A field of study itself emerged investigating different applications of polysaccharides such as chitin, chitosan, hyaluronic acid and alginate. Chitin, β-(1→ 4)-poly- N-acetyl D-glucosamine, a high molecular weight linear polysaccharide is next only to cellulose in its abundance in nature. Chitin is found in nature, in a variety of different species, such as crustaceans, insects, mushrooms, and in bacteria cell walls. N-deacetylated form of chitin, chitosan, is a linear block copolymer. Efforts are underway or been invested already to exploit materials’ different potentials with latest technologies and techniques. Application of nano-technology, being a valuable tool, is used widely in recent times for the material property enhancements. In our current project, nano copper oxide (CuO) and nano aluminium oxide (Al2O3) were doped on chitosan polymer matrix and property changes have been analysed. Nano CuO is characterised by its superior catalytic activity and selectivity, surface effect, superiority of the quantum size effect, volume effect and macroscopic quantum tunnelling effect in magnetic optical absorption, chemical activity and thermal resistance, catalysis, and the melting point. And, nano Aluminium oxide, in its g-phase, with large surface area and high catalytic activity, can be made into microporous spherical structure or honeycomb structure of catalytic materials, enabling them to be excellent catalyst carriers.Chitosan is of much commercial interest due to their high percentage of nitrogen (6.89%) compared to synthetically substituted cellulose (1.25%). Application as chelating agent, highlighted for its biocompatibility, biodegradability, adsorption properties, non-toxicity, availability parameters; each adds to further interest of scientific community and scientific-technological minds to explore and exploit the polymer’s different properties to the commercial scale with environmental payoffs.Present task is undertaken to widen the application of chitosan with enhanced property. Enhancement in property is demonstrated with introduction of nano-compounds to the polymer matrix. Reinforcement in nano-scale definitely scores high than with micro-scale counterpart, with a more dispersed distribution and good compactness.Importance of enhanced material properties and its substitution to different spectrum of applications understood from the various research works by great minds, some of which are discussed below, really burned inspirational for our work to begin with:Jeanette Mirian Diop [1] studied the fabrication and characterization of gelatin and chitosan films with an objective of determining the optimal method of preparing these films, to improve on their mechanical properties. Chitosan films were prepared by spin coating and drying known masses of samples in the fume hood or the oven. Each film was tensile tested for its Modulus of Elasticity, Tensile Strength, Yield Strength, and Elongation at Break. The results revealed that Chitosan films that were washed with sodium hydroxide solution after drying were less susceptible to humidity; further, chitosan films prepared with acetic acid tend to be easier to handle during film preparation and testing.F. Al-Sagheer and S.Muslim [2] fabricated Chitosan-silica (CSSi) hybrid films by sol-gel process with tetra ethoxysilane (TEOS) as precursor. Fracture surface was revealed through a field emission-scanning electron microscopy/energy dispersive spectrometer (FE-SEM/EDS) to probe the dispersion degree and the size of SiO2 particle. Thermal properties of these composite materials have been studied as a function of silica, which indicated thermal stability of the chitosan film being enhanced. Dynamical Mechanical Thermal Analysis (DMTA) has been carried out to measure the shift in the glass transition temperature (Tg) of the composites from the maxima of the α transition curves. The glass transition temperature (Tg) and the storage modulus showed an increase with increasing silica content. The maximum increase in the Tg value, that is, 159.37◦C, was seen with 30 wt% silica. A gradual increase of 3.0 GPa in the modulus relative to the pure polymer also observed.João P. de Mesquita [3] studied bio-based nanocomposites through covalent linkage between cellulose nanocrystals (CNCs) and the natural polymer chitosan (CH). The CNCs were first functionalized with methyl adipoyl chloride (MAC) and the reactive end groups on the surface of the CNCs were reacted with the amino groups of the CH biopolymer in an aqueous medium. Characterization of the functionalized CNCs showed that up to 8% of the hydroxyl groups in the nanocrystals were substituted by the MAC residue. The nanocomposites validated a significant improvement in the mechanical performance and a considerable decrease in the hydrophilicity comparative to the plain chitosan.Tariq R. Sobahi [4] blended PVC with Chitosan through simultaneous casting of their separate solutions in dissimilar proportions of PVC and Chitosan in suitable solvents. After dissolution, both solutions were added to each other while stirring at room temperature. The obtained mixture was left at room temperature to form the blend after evaporation of the solvent. Comparable blends have been prepared similarly in presence of carrier- mediating material such as the organic ligand, dithizone, for different metal ions. The obtained blends were found to have reasonable extent of compatibility between their components, as charecterized by thermal (TGA) and FT-IR Spectroscopic analyses and scanning electron microscopy (SEM). Obtained compatibility can be attributed mainly on the way with which the components have been blended with each other. Moreover, the polymer-supported dithizone was investigated toward its ability to be used for removal of some metal ions from their aqueous solutions. Concentration of metal ions was determined by ICP-AES analysis.B. Prakash [5] embedded the biocompatible Al2O3 nanoparticles in to Chitosan biopolymer matrix by ultrasonication route. The absorbance and transmittance of the above samples were studied and it is found that the optical transmittance of the samples increases with increase in sonication period. Measurement of the optical band gap revealed that a band gap increase with respect to the sonication time period. The glass transition temperature (Tg) of the Chitosan was measured by DSC and the value of Tg found to be increasing with increasing sonication time. The electrical conductivity of the samples was studied by the Impedence analysis method. There is a relaxation process which occurred at 160°C and it increases with increase in sonication too.Marino Quaresimin et al [6] studied the Strategies for the assessment of nanocomposite mechanical properties. And, three main stages of nanocomposite modelling with dedicated model to each stage were discussed. “Three Stage Strategy”, a concept of assembling basic model to build a multiscale modelling strategy was proposed. Moreover, classification of the available modelling strategies was also presented, to the scale from which the problem is addressed. This comprehensive analysis is thought as a necessary tool for the development of new effective approaches.Hongwei He et al [7] did a study to evaluate the effect of nano-CaCO3 particles on thermal and mechanical properties of epoxy resin cast were performed. A silane coupling agent KH550 as an interfacial modifier was introduced into nano composites through preparing KH550/nano-CaCO3 master batch. The result gave a conclusion that, the epoxy resin cast filled with nano- CaCO3 particles exhibits higher thermal stability and mechanical strength. The improvement of thermal and mechanical properties was attributed to the surface modification of nano-particles, which could enhance the interfacial properties between nano-CaCO3 fillers and epoxy resin. The mechanical properties of nano-CaCO3/ epoxy/carbon fibres composites based on the modified epoxy matrix were also enhanced.Maenghyo Cho et al [8] studied the Multi-scale modelling of cross-linked epoxy nanocomposites. The effect of different sized aluminium oxide (Al2O3) nanoparticles on the mechanical properties of thermoset epoxy-based nanocomposites investigated using Molecular Dynamic (MD) simulations combined with sequential scale bridging methods. In order to investigate the particle size effects, various unit cells having different particle radii but the same volume fraction were considered and simulated. The mechanical properties of the nanocomposites were calculated using the Parrinello–Rahman fluctuation method to give an enhanced reinforcing effect in smaller particle reinforced cases. Based on the MD simulation results, the sequential bridging method was adopted for efficient estimation of the particle size and epoxy networking effects. The values calculated from the micromechanics model were in good agreement with those of the molecular dynamics simulations.The literature review reveals some of the many attempts happened around the globe to enhance composite polymer property with adept introduction of compounds to the matrix. Works to understand material property alteration of chitosan matrix with introduction of nano-compounds, however, is few. We acknowledge and understand the importance of exploiting this naturally abundant mucopolysaccharide’s potential to human life. Deriving motivation from this fact, the objective of present investigation is to study the effect of nano-copper oxide (CuO) and nano-aluminium oxide (Al2O3) particles on the mechanical properties of chitosan.
2. Materials and Methodology
The study involves the preparation of polymer films and nano powder doped polymer films. Chitosan – nano compound films is prepared by solution casting process with acetic acid as solvent. Thin film thickness measured using hand held micrometer, Mitutoyo make. Their mechanical properties were studied with the help of Thin Films Universal Testing Machine. Lloyd universal testing machine with 5KN grips and cross head speed 25 mm/min, bench top universal testing machine used for the purpose. The chitosan films were defined by their Modulus of Elasticity (ME), Tensile Strength (TS), Yield Strength (YS) and Extension till Break (EB). Tensile properties of films may be affected by various innate properties, as – moisture content of the films, physio-chemical properties of the films, humidity of the atmosphere during testing. Extra measures have to be taken, so that, these parameters will not affect result much.
2.1. Materials
Materials used were - Medium molecular weight chitosan with the degree of deacetylation between 75-85%, nano - Copper oxide, nano - Aluminium oxide and acetic acid was of reagent grade. Chitosan purchased from BlueLine Foods (India) Pvt. Ltd., Mangalore. Nano copper oxide and nano aluminium oxide purchased from Durga labs, Mangalore.
2.2 Preparation of Chitosan and Nano Doped Chitosan Films
Generally thin films are prepared in the following ways.• Solution casting• Vapour deposition• Spin coatingSolution Casting is the simplest method used to create thin films from solution using centrifugal force. Thin films of chitosan and nano compounds (aluminium oxide and copper oxide nano powder) doped Chitosan were prepared with different concentration of chitosan and nano powders using Solution casting method. In the first set, 1g of chitosan was added to 50ml of deionized water and stirred, using a magnetic stirrer, for about 0.5-1 hour while 1% acetic acid was added to bring the solution to the desired pH level. The solution was then filtered to remove the insoluble clumps that were still in the solution. Solvent removed by decanting method, and the prepared clear solution was cast onto Petri-dish for film formation. Films dried by keeping in hot air oven at 60℃. In equal 3 hour time intervals, Petri-dish checked for cured sample film, for 3-4 days. After drying, the obtained films were peeled off gently from the glass plates. In second set of thin films, 1g of Chitosan was added to 50mlof deionized water and stirred for about 0.5-1 hour while 0.1g of nano copper oxide and acetic acid was added. The solution kept in Ultra sonicator for 2 hours which is to impart better dispersion. The prepared clear solution was cast onto Petri-dish for film formation after solvent being removed by decanting method. Hot air oven used to dry the sample film. Temperature set to 60℃ for 3-4 days. In equal intervals of 3 hours, sample checked for proper curing. After drying, the obtained films were peeled off gently from the glass plates. Same procedure was repeated for 0.2g of nano-copper oxide.In third set of thin films; 1g of Chitosan, 50ml of deionized water stirred for about 0.5-1 hour while 0.1g of aluminium oxide nano powder and acetic acid was added. Ultra sonicator used to well disperse the solution. By the decanting method solvent is removed. The prepared clear solution was cast onto Petri-dishes and dried with the aid of hot air oven set at 60°c. Sample films confirmed for proper curing in each 3 hour time interval, for 3-4 days. Dried films were peeled off gently from the Petri-dishes. For 0.2g of nano aluminium oxide, same procedure was followed.After drying the films, each sample formed to shapes of rectangular film of dimension 50mm x 25mm x 0.165mm. Respective samples were presented for mechanical property testing with the aid of Thin Films Universal Testing Machine. The chitosan films with identified doping composition and dope-concentrations were tested for their Modulus of Elasticity (ME), Tensile Strength (TS), Yield Strength (YS) and Extension till Break (EB). And, results have been recorded.
3. Results and Discussions
3.1. Tensile Strength Analysis
Figure 1 shows the variation in tensile strength of undoped chitosan and chitosan with different concentrations of nano metal oxides. 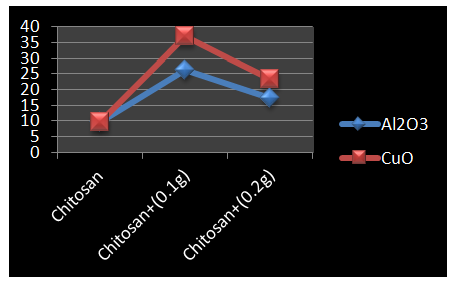 | Figure 1. Variation in Tensile Strength (MPa) for Chitosan |
The graphical trend recording shows Tensile Strength (in MPa) varying for different concentrations as 0.1g and 0.2 g of nano aluminium oxide and nano copper oxide.From the figure, it is observed that the tensile strength of 0.1g nano-aluminium oxide doped chitosan (26.08MPa) has increased almost three times than that for undoped chitosan (9.692MPa). And when it’s doped with 0.1g of nano copper oxide, the value of tensile strength (37.061MPa) has been increased more than four times that of the normal chitosan.But when the same amount of chitosan is doped with 0.2g of nano aluminium oxide and nano copper oxide, we have observed that the value of tensile strength has been dropped to a lesser value. Still it has enhanced the tensile strength, double the value of the undoped chitosan film prepared.
3.2. Stiffness
Figure 2 show the Stiffness of undoped chitosan and, 0.1g and 0.2g of nano-aluminium oxide and nano-copper oxide doped chitosan.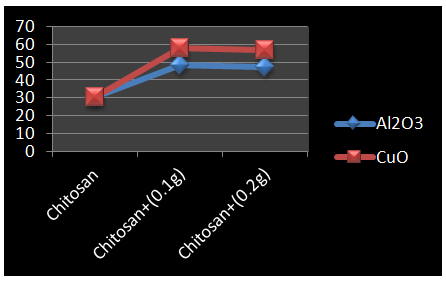 | Figure 2. Variation in Stiffness for Chitosan (KN/m) |
From the above graph we have observed that the stiffness of 0.1g aluminium oxide doped chitosan (48.192kN/m) has increased to a greater value than that of the value of undoped chitosan (30.261KN/m). And when it’s doped with 0.1g of nano-copper oxide, the value of Stiffness (58KN/m) has been increased almost two times than that of the normal chitosan. But when the same amount of chitosan is doped with 0.2g of nano-aluminium oxide and nano-copper oxide, we have observed that the value of stiffness has been dropped slightly to a lesser value, as listed in the table, than expected. Still it has enhanced the stiffness, almost double the value of the plain chitosan film prepared. The value of stiffness in the case of nano-copper oxide doped chitosan is more. So we could conclude that the stiffness is more for nano-copper oxide doped chitosan films.
3.3. Young’s Modulus
Figure 3 show the young’s modulus of chitosan, 0.1g and 0.2g of nano-aluminium oxide and nano-copper oxide doped chitosan.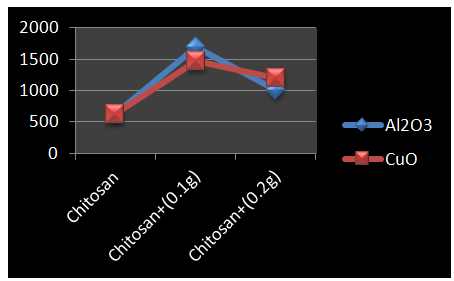 | Figure 3. Variation in Young’s Modulus for Chitosan |
From the above graph we have observed that the Young’s modulus of 0.1g nano-aluminium oxide doped chitosan (1690.9MPa) has increased to almost three times than that of the value of plain chitosan film (630.44MPa). And when it’s doped with 0.1g of nano-copper oxide, the value of Young’s modulus (1468.3MPa) has been increased more than two times than that of the normal chitosan. But when the same amount of chitosan is doped with 0.2g of nano-aluminium oxide and nano-copper oxide, we have observed that the value of young’s modulus has been dropped to a lesser value, as listed in the table, than expected. Still it has enhanced the young’s modulus, almost double the value of the plain chitosan film prepared.
3.4. Percentage Total Elongation at Fracture
Figure 4 shows the percentage total elongation at fracture of undoped chitosan and chitosan with 0.1g and 0.2g of nano aluminium oxide and nano copper oxide doped.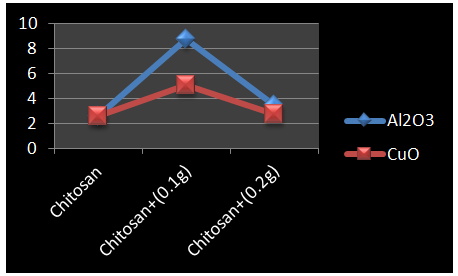 | Figure 4. Variation in %ge Elongation for Chitosan |
From the figure, we have observed that the percentage total elongation at fracture for 0.1g nano-aluminium oxide doped chitosan (8.744) has increased to almost three times than that of the value of undoped chitosan (2.604). And when it’s doped with 0.1g of nano-copper oxide, the value of percentage total elongation at fracture (5.1075) has been increased more than two times than that of the undoped chitosan. But when the same amount of chitosan is doped with 0.2g of nano-aluminium oxide and nano-copper oxide, we have observed that the value of percentage total elongation at fracture has been dropped to a much lesser value than expected. Still it has enhanced the percentage total elongation at fracture, to a value much better than that of the chitosan film prepared.From the above mentioned graphs; for properties such as tensile strength, stiffness, young’s modulus, percentage of elongation at fracture for undoped chitosan; chitosan with 0.1g, 0.2g concentration of nano-aluminium oxide, nano-copper oxide; we came to a conclusion that 0.1g nano-compound doped chitosan films has much better results and enhanced properties than that of 0.2g nano-compound doped chitosan films. Even though the 0.2g nano-compound doped chitosan has enhanced the properties not to the extent of 0.1g doping case, but still much more than for the plain chitosan films.
3.5. Comparison of Polymer Property Behavior for Plain Chitosan and Chitosan with Different Concentrations of Nano-Aluminum Oxide and Nano-Copper Oxide
From the above two graphs it’s clear that the properties of chitosan films have enhanced when it is doped with 0.1g of both nano-aluminium oxide and nano-copper oxide. Bar chart shows that the tensile strength of nano-copper oxide doped chitosan is more than that of the nano-aluminium oxide doped. Moreover, as we can observe from the graph 6, the percentage total elongation at fracture is more in the case of nano-aluminium oxide doped Chitosan films.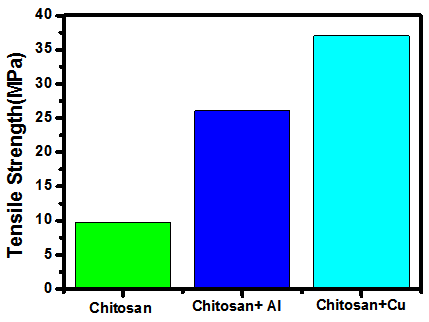 | Figure 5. Tensile Strength comparisons |
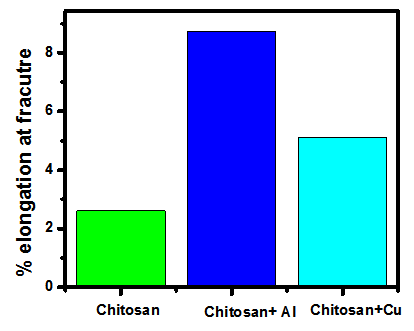 | Figure 6. Percentage elongations at Fracture comparisons |
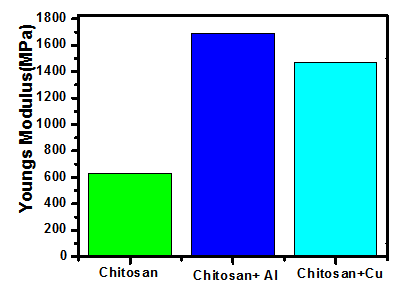 | Figure 7. Young’s Modulus comparison |
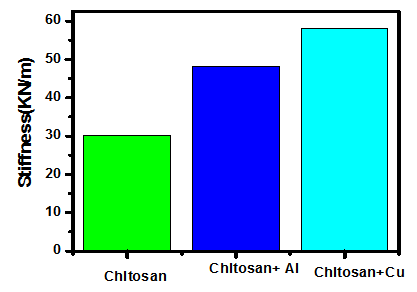 | Figure 8. Stiffness comparison |
From the above two graphs it is clear that the properties of chitosan films have enhanced when it is doped with 0.1g of both nano-aluminium oxide and nano-copper oxide. The young’s modulus of nano-aluminium oxide doped chitosan is more than that of the nano-copper oxide doped. Also, as we observe, the stiffness is more in the case of nano-copper oxide doped chitosan films than of the nano-aluminium oxide doped counterpart.Figure 9, a plot with percentage stress to percentage strain values, gives a better understanding on the stress-strain relationship exhibited by the chitosan in its plain form to that of nano-compound doped films. Material failure seems to be prolonged in terms of strain for nano-aluminum oxide, but better loading extent to chitosan doped with nano-copper oxide.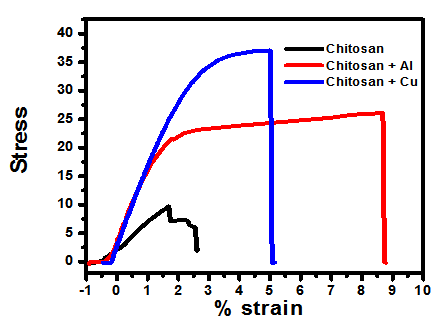 | Figure 9. Stress-Strain relations, a comparison |
4. Conclusions
From the obtained results we can arrive to the following conclusions:• When a Polymer is doped with nano-compound, its properties are enhanced.• As the concentration of the nano-compounds increased, after a limit, resulted material property starts declining (as per our current study – tensile strength, stiffness, young’s modulus, percentage elongation at fracture).• For the case of nano copper oxide doping, as the concentration increases resulting material turns more brittle. And, nano-aluminium oxide causes the material towards ductility.• When nano-aluminium oxide doping increased young’s modulus and percentage elongation at fracture of chitosan film than with nano-copper oxide doping; nano-copper oxide doping resulted in increased value of tensile strength and stiffness than for nano-aluminium oxide counterpart.From the above observations, as per the experiment demonstrated, we conclude that the optimum concentration for enhanced property is 0.1g of nano-compound. Moreover, use of acetic acid instead of Sodium hydroxide and hydro chloric acid made it easier for the preparation of thin films.
References
[1] | Jeanette Mirian Diop, "Preparation and Characterization of Gelatin and Chitosan Films", An Honors Thesis for the Department of Chemical and Biological Engineering, 10-13, Tufts University, 2009. |
[2] | F. Al-Sagheer and S. Muslim, "Thermal and Mechanical Properties of Chitosan/SiO2 Hybrid Composites", Journal of Nanomaterials, Volume 2010, Article ID 490679, 7 pages. |
[3] | João P. de Mesquita, Claudio L. Donnici, Ivo F. Teixeira, Fabiano V. Pereira, “Bio-based nanocomposites obtained through covalent linkage between chitosan and cellulose nanocrystals”, Carbohydrate Polymers 90 (2012) 210– 217. |
[4] | Tariq R. Sobahi, Mohammad Saleh I. Makki, Magdy Y. Abdelaal, “Carrier-mediated blends of Chitosan with polyvinyl chloride for different applications”, Journal of Saudi Chemical Society (2013) 17, 245–250. |
[5] | B. Prakash, M. A. Jothirajan, S. Umapathy, Viji Amala, “Synthesis and characterization of biodegradable ultrasonicated films made from chitosan/Al2O3 polymer nano-composites”, Physics Procedia 49 ( 2013 ) 84 – 91 |
[6] | Marino Quaresimin, Marco Salviato, Michele Zappalorto, "Strategies for the assessment of nanocomposite mechanical properties", Composites Part B: Engineering, Volume 43 (2012) 2290-2297. |
[7] | Hongwei He, Kaixi Li, Jian Wang, Guohua Sun, Yanqiu Li, Jianlong Wang, "Study on thermal and mechanical properties of nano-calcium carbonate/epoxy composites", Materials and Design 32 (2011) 4521-4527. |
[8] | Maenghyo Cho, Suyoung Yu, Seunghwa Yang, "Multi-scale modeling of cross-linked epoxy nanocomposites", Polymer, Volume 50, Issue 3, 28 January 2009, Pages 945–952. |