Dmitro Starokadomsky, Igor Telegeev
Polymer Composite&Nanomaterials Lab.No13, Institute of Surface Chemistry of prof.A.A.Chuiko, National Academy of Sciences, Ukraine
Correspondence to: Dmitro Starokadomsky, Polymer Composite&Nanomaterials Lab.No13, Institute of Surface Chemistry of prof.A.A.Chuiko, National Academy of Sciences, Ukraine.
Email: |  |
Copyright © 2012 Scientific & Academic Publishing. All Rights Reserved.
Abstract
It is established that incorporating of silica A300 (with different nature of surface) can lead to strengthening of epoxy-polymer. According experimental obtained data, the new modified silicas that increases of strength and durability of epoxy-composite were proposed. They are obtained by modifying surface of A300 by monolayers of olygoacrylates (bis-GMA, olygocarbonate-methacrylate) or sylane-acrylate A174. It is established that modification improves the distribution of the filler in the matrix and optimize the structure of composition (reducing the number of bubbles, pores, defects). It is found that such modification of A300 can significantly increase the resistance of polyepoxide to aggressive media (concentrated nitric acid and solvent diethylenglycol-diacetate). The limited swelling in solvent can reduce from 25-30% (for unfilled or neat silica filled) to 5-10% (for filled by oligoacrylate- modified silica) composite. Modification by silanacrylate A174 let increase a life-time of composite in conc.HNO3 in 2,5 and 5 times versus neat silica and unfilled polymer; also, adhesion strength after silica modification let increase to 5-17% versus unfilled polymer.
Keywords:
Polyepoxyde, Silica A300, Aggregates, Olygoacrylates, Swelling, Nitric acid, Solvent, Strength to moving, Strength to tearing
Cite this paper: Dmitro Starokadomsky, Igor Telegeev, Effect of Silica A300 Surface Modification by Acrylates on Strength and Swelling of Epoxypolymer Composite, American Journal of Polymer Science, Vol. 3 No. 5, 2013, pp. 90-98. doi: 10.5923/j.ajps.20130305.02.
Filling by nanosilica is a good method to regulate physico-mechanic properties of epoxy-polymers (EP)[1]. The nature of silica surface is a key factor of silica influence to properties of composite. As modificators, silane, aminosilane and acrylate monomers and olygomers are most popular now[2-9]. The main topics of epoxy-polymer filling are reinforcement[3,6-9], improving of thermo-mechanics [7], strength parameters[10-13], durability in acids[1], solvents[13, 14, 14A] or water[14, 15], tribology[2], and other parameters[14, 15].Today, effect of silica modification by acrylates on strength and resistance of polyepoxides is not clear investigated. In[10], effect of nano-SiO2 with acrylatesilane “coupling agent A-174” on performance of poly(MMA/BA/ MAA)/EP have been investigated - the results show that the nano-SiO2 is soft agglomerate, which diameter is about 2.08 μm. For shear strength, the most effective is 3 – 5 wt% of SiO2 with 4 – 6% of modificator A-174[10] As the 3% nano-SiO2 is added, the nano-SiO2 distributes uniformly in the matrix, and particles do not accumulate, therefore, a higher strength of nano-SiO2/Poly(MAA/BA/MAA) /EP is obtained[10]. As the amount of nano-SiO2 increases, the accumulating tendency of nano-SiO2 increases, which causes the mechanical properties to decrease[10].Polonska and Vasilchenko[11] has established that maximal quantity of reacted with acrylatesilanes (MMA-methyl-etoxy-silane) free silanol groups in SiO2 do not exceed 40%. Influence of solvents (CCl4, ethanol, acetone, methylethylketone) on 1-3 wt% silica-filled epoxypolymer (system of Araldite CY-230 and hardener HY-951) were investigated by Kaushik[14]. The SEM micrographs indicated the uniform distribution at lower concentrations, that is, up to 2% of colloidal silica, and TGA results show improved thermal stability and increase in ash content with increase in silica content[14].The aim of this work is to investigate possibilities of olygo- or silan-acrylate modificators of SiO2 on improvement of macro-characteristics of EP. There are homoheneity, viscosity, various forms of adhesive strength and durability to aggressive environments. The possible success in this field is important for industrial applications. For example, high swelling of EP in ink solvent is important for polygraph applications[2; 13, page 63], problems of strength– for build and automotive industries etc.Theoretical base of this work consist in next. The surface of SiO2 have a weak-acide centers (SiOH-groups). Polyepoxides (EP) have also OH-groups and other centers of cooperation with SiO2-surface. This fact explain the comparative facile interaction “EP – pureSiO2”. But existence of OH-groups and other structures (doublated OH-groups, strained Si-O-structures, metal impurities) leads to concentration of water clusters and physical adsorption of organic and gas impurities on SiO2-surface. It is a factor of weakening of EP – SiO2 interaction. It explains necessity of surface modification of SiO2, for liquidation of their factors. In process of work we We see that such substances for three-dimensional polymers (polyacrylates, polyesters and polyepoxides) can be acrylatesilanes and olygoacrylates. Acrylatesilanes can chemically immobilisate to SiO2-surface and his acrylate brain is oriented in polymer bulk (fig.1). Olygoacrylates "lie down" to the surface, with different orientation acrylate groups (fig.2). The scheme of interaction can include mechanical inter-penetration with polymer chains or appearance of inter-penetrating polymer chains (polyacrylate – polyepoxide). Figures 2 - 4 shows the possible schemes of such interaction with the surface modifier SiO2. An important effect of such modifiers can be considered "cleaning up" their surfaces from dirt and water adsorbed on the original SiO2.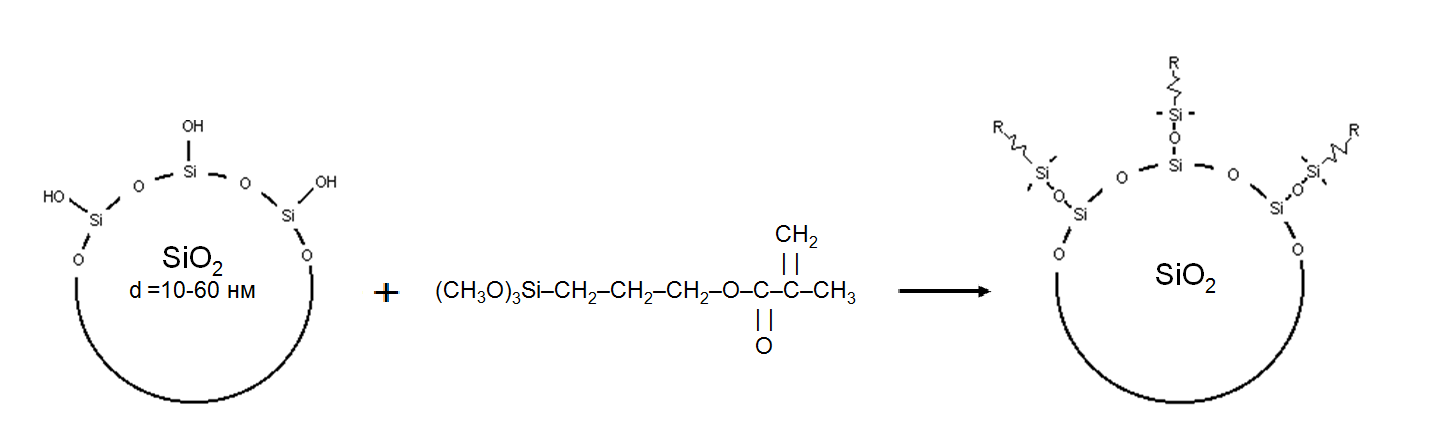 | Figure 1. Interaction SiO2 – acrylatsilane monomer A-174. “R” – methacrylate group |
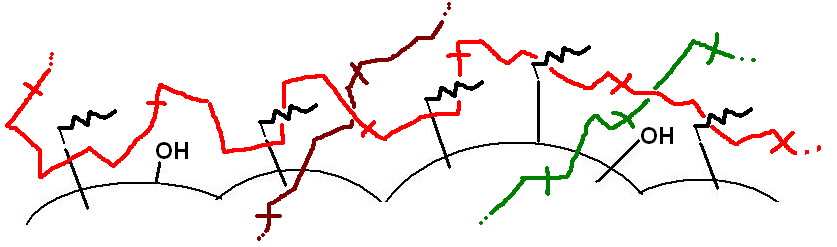 | Figure 2. The possible scheme of interaction “SiO2 + acrylate modificator” (spherical structures and black lines) with polymer chains (colour lines) |
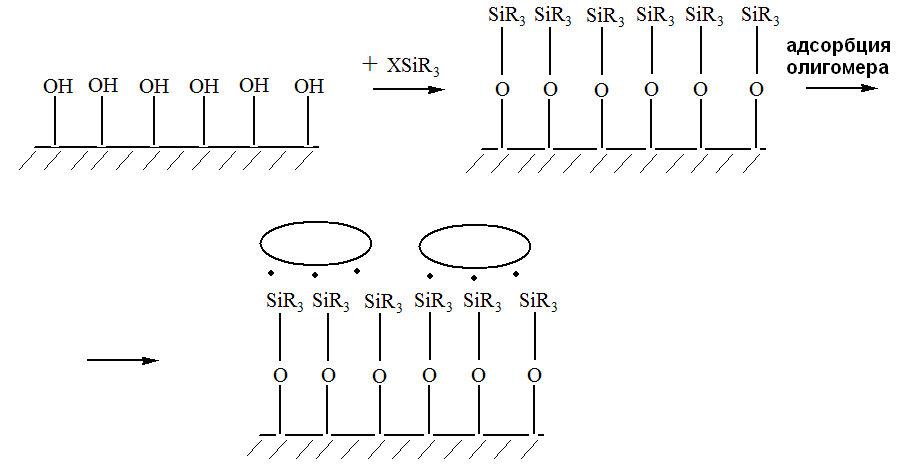 | Figure 3. Scheme of combinated interaction of methacrylate-silane and olygoacrylate (ellipsoids) with surface of SiO2 |
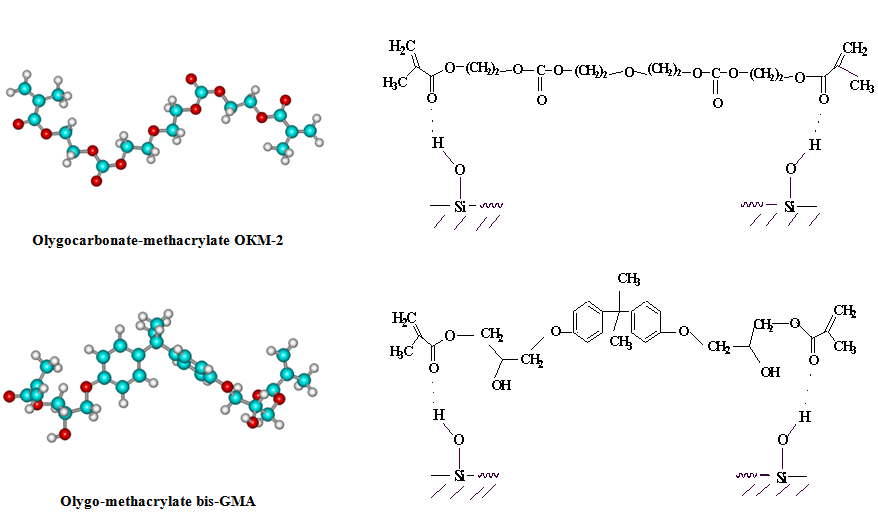 | Figure 4. Scheme of interaction of olygoacrylates with SiO2 (red – O, blue – C, white – H) |
1. Methodics
1. Silica and modificationIn this work, the silica Aerosil A300 (Degussa-s licensed TM of Kalush Factory of our Institute) with surface area 340 m2/g and their modificated forms (tab.1) were taken. Surface modification carried out from gaz-phase. The fact of modification were fixed by IR-spectra of silica (by disappearance of band 3750 cm-1 of free OH-groups) and by gravimetric analysis.Table 1. Types of silica for our investigation 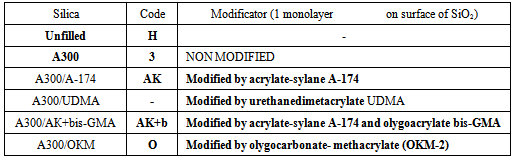 |
| |
|
2. Polymerisation.Epoxydian resin ED-20 (UfaChemProm, Russia) was filled through addition of silica in could resin and periodical intensive mixing (by spatula) at 50-60℃. After 1-2 week, this operation is repeated, and hardener Polyethylene- Polyamine (12.5 wt% or resin: polyamine ratio is 7:1) is added. After enduring in thermostate at 75℃ (1-2 min) composition was mixed by spatula during 5-10 min and returns in thermostate at 75℃ (1 min). Ather that composition was used for preparation of templates. 3. Mechanic techniquesThe next strength characteristics of composites were measured: – Strength T of adhesion fiberglass-composite layer- fiberglass (for fiberglass plates with glue area 1.5 * 2 cm, fig.5A-B).– Strength O of adhesion steel (fig.5A-A)–composite layer–steel (for steel cylinders with glue area 5 cm2). 4. Swelling techniques For investigations of chemical stability of composites (4 wt% of silica, at 17-20℃), the swelling and stability of lens-formed (fig.5A) templates in conc.HNO3 were investigated. Also, the swelling in polygraph ink solvent (dyethyleneglicol-dyacetate DEGDAc, production INKWIN, China) were measured. As a life-time, the time of finally destruction (when cannot to take a destructed template for measure from solution) were adopted. Templates (weight 0.05+-0.01 g) was endured in polyethylene forms with conc.HNO3 (closed non-hermetically by glass plate). For periodical weighting template sample was removed, wiped with filter paper and dried under normal conditions for 30-50 minutes. Swelling (dynamics of change in mass) Q was measured by classical gravimetric method Q= 100(m-mo/mo).5. Optical and TEM-microscopy.TEM-images of silica were obtained using transmission electron microscope SELMI 125K, with tensile 100 kV. Template of silica were dispersed in ethanol and suspension applied on a carbon film-coated copper mesh, and dried. Optical photoimages of compositions are obtained via photography of image in lens of optical microscope.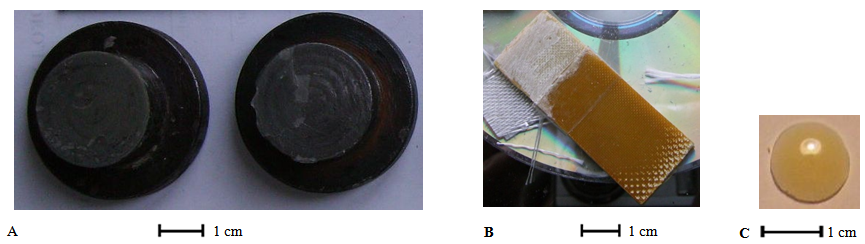 | Figure 5A. Steel cylinders for tearing tests (A), fiber-glass plate for moving tests (B) and typical sample for swelling tests (C) |
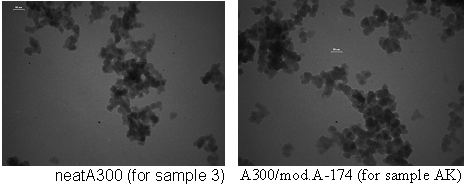 | Figure 5B. TEM-images of neat silica A300 and A300/mod.A-174 (in ethanol) |
2. Results and Discussion
1. Homogeneity of SiO2-filled compositionsThe comparison of TEM-images tell about similarity of self-aggregation in organic substances. Can see also that particles of modified A300 are more large.As a rule, unfilled composition concern a bubbles of air. After SiO2-filling, this size and number of bubbles decreases, and agglomerates of silica appears. After filling by unmod.A300 agglomerates of SiO2 appears (fig.6). The little part of A300 form greats (great agglomerates 0.1-1 mm), the most part of silica disperses in epoxy-resin. Modification of A300 let obtain the more homogeny composite and less viscous, therefore a quantity and diameter of bubbles decreases compared with unmod. A300 (fig. 6 E – L), however the individual units of aggregates remain (fig.6 E - L). For example, the dendrytes of silica aggregates are well clearly visible in fig.6 E, I (small points near bubbles).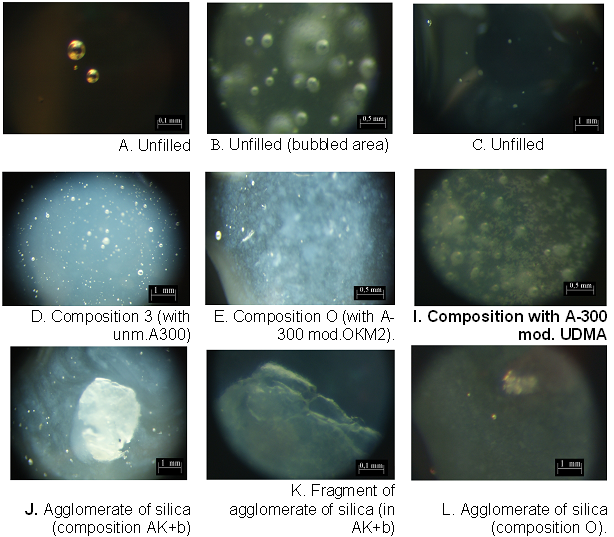 | Figure 6. Photoimages (growt in 10-50 and 100 times) of compositions before hardening, 2 wt% of silica |
2. Swelling in solvent DEGDAcThe experiment shows a classic type of swelling of the epoxypolymer (Fig. 7) - with faster access to the saturation (4-5 days). The degree of swelling in a state of saturation is usually a considerable amount - 20-30%.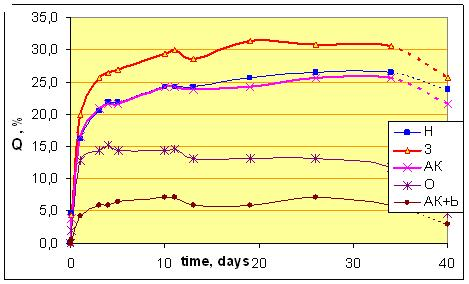 | Figure 7. Swelling Q of composites in ink solvent DEGDAc (at 25oC). The final point show percent of not-removed solvent after drying |
Table 2. Swelling (%) in solvent DEGDAc. H-double – additional control unfilled sample 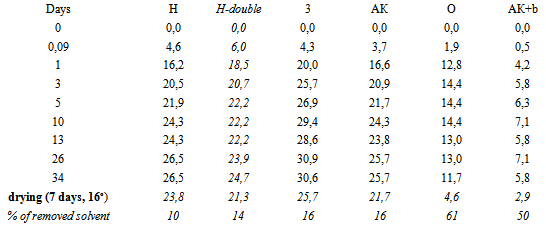 |
| |
|
Unfilled polymer is already on the 4th day swells to 22% - up to quazy-saturation. Subsequently, after 2 weeks of exposure, swelling resumes, and can reach 26-27% (sample H, Figure 7). Thus, the supramolecular structure of unfilled polymer is quite permeable for aggressive solvent. It is important that after drying of fully swollen sample the most of solvent (almost 90%, Figure 7) remains in polymer. This clearly shows the limitations of the use of unfilled polyepoxide in the real industry (where contact with solvents is regular).Filling by 4 wt% of unmod.A300 due to the opposite effect - the swelling is greatly accelerated, and maximal Q increases by more than 1.3 times (fig.7). The curve of sample "3" (SiO2 + A300) go to the saturation only after Q=31-32% (fig.7).The behavior of the curve for template “3” (with neatA300) suggests that pure SiO2 provokes a significant loosening of the supramolecular structure in EP. Probably, silica create a permeable boundary between phases, or causes weakening of interaction between macromolecules. The important point is the behavior of aggregates and agglomerates A300 that are visible in resin (as turbidity and mini-greats) - a signification of lack interaction with polymer phase. Drying of the sample saturated with solvent can not remove the majority of penetrating solvent, but quantity of non-removed solvent (up to 84%) is smaller than for the unfilled template H (almost 90%).Modification of the A300 is a natural way to improve its performance as a filler. Can see that the samples with modified A300 are almost transparent. Already it says about the hidden opportunities for enhancing chemical resistance by modifying of silica.Indeed, modification by olygo-carbonate-methacrylate (sample O) and two-layer modification "silanacrylate A174 + oligoacrylate bis-GMA" (sample АК+b) due to significant increase of resistance to solvents. For sample O the maximal degree of swelling of Q(O) is lower than Q(H) for unfilled in 1.5-2 times (Fig. 7, Q(O)=15%, and Q(H)=27%), and for АК+b (Fig. 7, Q(АК+b) = 7%) - almost 4 times! For unfilled polymer (sample H in fig.7) and EP+neatA300 (sample 3) drying remove only 10-15% of penetrated solvent (tab.2). Drying of the samples saturated with solvent removes almost 2\3 of penetrated solvent for the sample O, and for АК+b – >50% of penetrated solvent. It says about increasing of density of composite structure after modifying of A300. In this case, penetrated solvent cannot find a cells for fasten the molecules in polymer structure. Note that the sample АК+b was the most resistant also in concentrated HNO3 (see below, tab.3). Thus, from the analysis of the curves says that unfilled polymer is well-permeable for solvent, and drying cannot remove the most part of incorporated solvent. Filling by nemod. A300 loosens the structure of the polymer, making it more permeable to the solvent, not adding the capacity of his discharge from the composite structure (Fig. 7). However, if modify A300 by optimal substances, can reach the optimal high-dense structure, weak-permeable for solvent. In plus, penetrating solvent into modified composite molecules is easier deletes itself after drying the sample. It means a significant reduction of defects, the decompression and "dead-end pores", suitable for long-term preservation of solvent molecules.3. Swelling in concentrated HNO3The behavior of epoxide samples in conc.HNO3 is highly dependent on the ambient temperature, the freshness of the polymer, the other factors. In our case, in the first hours (table 4), a rapid swelling - by 5-6%, and for the first day - by 25-35%, takes place. In the future, the rate of swelling decreases, but remains highly - 10-15 %/day. After 6 days of exposure swelling slows down due to dissolution and degazation (CO2, NO2) of sample. After 10 days for all composites processes of mass loss (dissolution, degazation etc.) begin to dominate (tab.3).Table 3. The lifetime L of the samples in conc.HNO3  |
| |
|
In the case of a long endurance in conc. HNO3 without decomposition, the sample is covered with cracks and fissures, and agglomerates of A300 become visible as white dots and spots. This suggests for active penetration of aggressive media on the phase boundary (which leads to the degradation of many samples).As seen from fig.8 and table 2, at the first steps up to 6 days (as occurs mainly physical swelling) unfilled polymer shows higher degree of swelling than unfilled polymer (sample H) or filled with modified A-300. But then (after the vertical "and" Figure 2) is dominated by dissolution of the sample, and soon (after 10 days, a vertical "b" in Figure 2) unfilled polymer begins to lose weight faster than others. After 15-16 days of unfilled polymer is fully expanded, moving into foam-viscous state.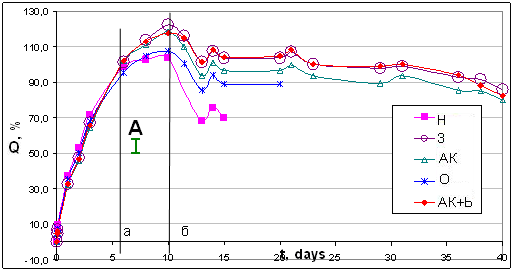 | Figure 8. Change in mass Q, % (swelling) in conc.HNO3 of samples with 4 wt% of silica. * - mo for sample "AK + b" - 0.051 g, for the rest samples - 0.041 g; segment "A" represents the maximum confidence interval |
Table 4. The change in mass 100m/mo, % (mo for sample "АК+b" - 0.051 g, for the rest - 0.041 g) of samples in conc.HNO3 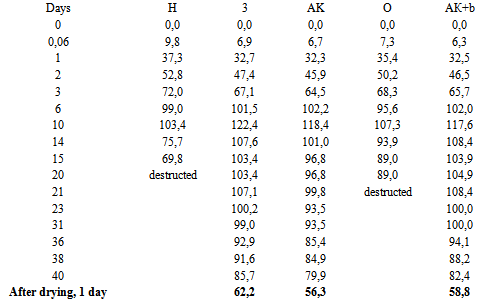 |
| |
|
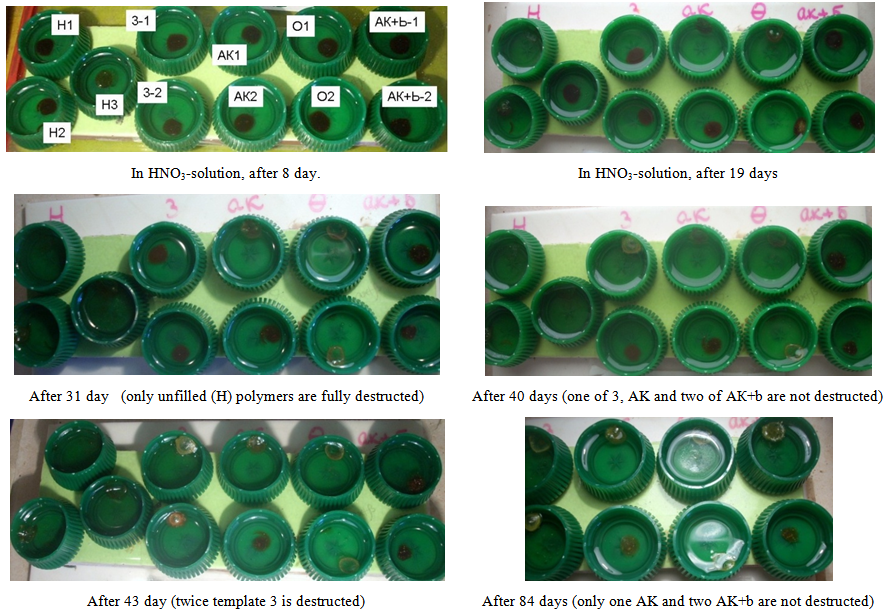 | Figure 9. Templates of EP-composites in conc.HNO3. Samples from left to right (as top row as bottom row of samples): H - 3 - AК - О - AК+b. Sample H3 between rows – additional unfilled template that was placed in solution in a week later |
From that moment, the stabilizing (strengthening) effect of the of silica is most notably. Samples with as unmod.A-300 as mod.A300 (except sample O, Figure 8) continue to maintain own integrity for more than 40 days. Thus, filling can extend life-time of epoxy-polymer in conc.HNO3 in 2.5 times without modification of SiO2, and in 6 times or more - after SiO2-modification (samples AK and AK+b).The most interesting is the behavior of the sample with SiO2+propylmethyl-acrylate-trimethoxy-silane A-174 (sample AK). This modifier is chemically reacts with the surface, while "the tail" of his molecule remains active methacrylate group. Theoretically, it is able not only to physical interaction with the polymer grid (through hydrogen bonding, interlocking), but also to self-polymerization. Effect of compatibility with polymerized resin may increase by consequent applying to the surface by acrylatesilane A174 and then the olygomer bis-GMA (Fig. 3). Indeed, a such modification of SiO2 can increase the lifetime of the sample in 10 times (table 1).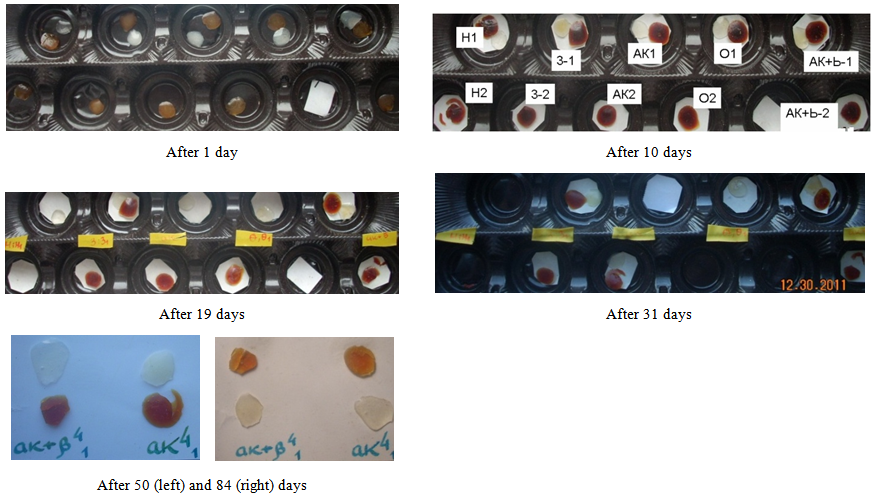 | Figure 10. Samples from left to right (as top row and bottom row): H-3-AК-О-АК+b. As comparative, the native samples (white tablets) are represented |
4. The results of strength tests: shear and peelAs seen in Tab.5, filling by pure A300 let increase (to 10%) the strength Ö on adhesion tearing. But scatter of data allows conclude a loosening of composite structure by filler with gradient of mechanical properties. This is obviously due to as aggregation of pure A-300 filler as not perfect interaction of pure A300 with the polymer surface. Draws attention to the high quality of the sample AK: In both strength tests the performance is significantly higher than the others - and data error Δ is small. For tearing test Ö, growth for AK versus H-polymer reach 17% (tab.5), and for moving test T, there is unique sample with growth of average T (tab.6). It proves most optimum (homogeneous) structure of this sample. Also two-layer modification is promising: for shear strength the ratio of the maximum values Tmax for filled samples with average TH for unfilled sample is maximal (tab.6).Table 5. The values of the breaking load for tearing (adhesion on area of 5 cm2, filler - 4 wt%) in the lead. In ascending order and with confidence intervals Δ (. Modificator - 1 monolayer of each substance. AK - Acrylsylane A174; OKM2 - Oligoester acrylates  |
| |
|
Table 6. The strength to moving (bonded fiberglass, an area of 1.5 cm2) of samples with 4 wt% filler. TH corresponds to T for unfilled polymer 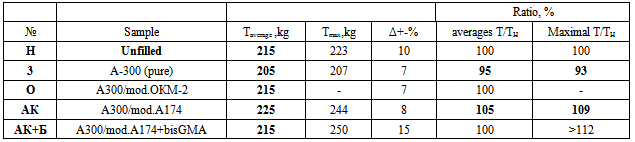 |
| |
|
3. Conclusions
1. Influence of filling by 4 wt% of A300 (with initial and the modified surface) on strength and chemical resistance of polyepoxide is investigated. It is shown that the introduction of silica A300 enhances chemical resistance of epoxy-composite. This results in increased life time (time to complete degradation) of specimens in concentrated nitric acid in 2.5 times (from 16 to 41 days), without modifying the A300 and 6 times or more - after modification (samples AK and AK+b). This is a consequence of the composite seal, remove or localization of defects in the polymer structure by filler surface, increase the resistance to acid exposure as a result of the introduction of weak acid filler (SiO2). Optical microscopy shows that filling not only leads to a new phase (the filler aggregates), but changes (decreases) the size and number of air bubbles. At the same time, activisation of swelling in organic solvent proves that initial A-300 loosens composite polymer network.2. Surface modification of A300 by olygo- and silanacrylates (bis-GMA, A174, olygocarbonate- methacryate) improves the chemical resistance in concentrated acid, resulting in multiple increase of the lifetime of the sample (up to 100 days for the initial A300 – 41 days, for unfilled - 16-20 days). Surface modification can also reduce swelling in a solvent - compared with the unfilled polymer and especially - with the unmodified A300. This shows the structure of the composite reach high density after surface modification of the filler. Increase the resistance of the composite allows a double-layer modification (in our case, it is system AK+b).3. Surface modification of silica generally allows for a more substantial (compared with the original A300) improve the strength of the investigated indicators. We conclude that the modified surface of the composite structure let optimize and expand interaction of polymer and solid phases.
References
[1] | D. L. Starokadomsky, Igor G. Telegeev. Resistance of Epoxypolymer with 2 - 5 wt% Nanosilica in Aggressive Acid Medium. Open Journal of Polymer Chemistry. 2012; 2: 117-123. - Published Online August 2012(http://www.SciRP.org/journal/ojpchem |
[2] | Starokadomsky D. and Telegeeff I. Influence of TiO2 and SiO2 Fillers on Swelling of Polyepoxide in Solvent Diethyleneglycol-Diacetate. Journal of Material Science and Engineering. August 2010: V.4. No 8: 51-55. |
[3] | Mahrholz T., Stangle J., Sinapius M. Quantitation of the reinforcement effect of silica nanoparticles in epoxy resins used in liquid composite moulding processes . Composites, A. – 2009. - V. 40. – P. 235–243. |
[4] | Antoine Guillet. Treatment of fillers with organofunctional silanes, technology & application. Macromol. Symposia. 2003; 194: 63-74 |
[5] | I. Freris∗, D. Cristofori, P. Riello, A. Benedetti Encapsulation of submicrometer-sized silica particles by a thin shell of poly(methyl methacrylate). Journal of Colloid and Interface Science. 2009; 331: 351–355. |
[6] | J. G. Iglesias, J. Gonzalez-Benito, A. J. Aznar, J. Bravo, and J. Baselga1. Effect of Glass Fiber Surface Treatments on Mechanical Strength of Epoxy Based Composite Materials. Journal of Colloid and Interface Science 2002; 250: 251–260. |
[7] | Michele Preghenella, Alessandro Pegoretti and Claudio Migliaresi. Thermo-mechanical characterization of fumed silica-epoxy nanocomposites Polymer. 12.2005; V46, Iss.26: 12065-12072 |
[8] | Caihua Ni, Guifeng Ni, Shengwen Zhang, Xiaoya Liu, Mingqing Chen and Lihua Liu. The preparation of inorganic/ organic hybrid nanomaterials containing silsesquioxane and its reinforcement for an epoxy resin network. Colloid & Polymer Science. 2009; V 288, N 4: 469-477.[8A] J.Jiao, X.Sun, Th.J.Pannavia. Mesostructured silica for the reinforcement and toughening of rubbery and glassy epoxy polymers. Polymer. 2009; 50: 983-989. 8B. |
[9] | Kang S, Hong SI, Choe CR, Park M, Kim J. Preparation and Characterisation of epoxy composites filled with functionalised nanosilica particles obtained via Sol-Gel process. Polymer. 2001: V 42, N3 : 879-887. |
[10] | Wenjun Zou, Jin Peng, Yun Yang, Linqi Zhang, Bo Liao, Furen Xiao. Effect of nano-SiO2 on the performance of poly(MMA/BA/MAA)/EP. Materials Letters 2007; 61: 725–729. |
[11] | D.Vasilchenko, I.Polonska. Gaz-phase modification of fillers for polymers. Ukrainian Chemical Journal (in Russian) 1993; V.59, N 12 : 1321-1324. |
[12] | Wunpen Chonkaew, B.S. Modifications of Epoxy Resins for Improved Mechanical and Tribological Performances and their Effects on Curing Kinetics . Diss.Ph.D. – Univ.of North Texas. – 5.2008 : 190 p. |
[13] | Sandra Lynn Case. Fundamental Importance of Fillers, Cure Condition, and Crosslink Density on Model Epoxy Properties. Diss…Ph.d.in Chem. -2003. Blacksburg, Virginia, US. : 170 p. |
[14] | A.Kaushik, J. Kaushik. Solvent Absorption Characteristics of Epoxy-Colloidal Silica Nanocomposites. Journal of Reinforced Plastics and Composites. September 2010. V. 29, N 18. : 2821-2833.(http://jrp.sagepub.com/content/early/2010/04/21/0731684409360995.abstract) |
[15] | V. A. Kochetkov and R. D. Maksimov. Water absorption and swelling of glass/epoxy syntactic foams. Mechanics of Composite Materials. 1.1996; V.32, N 1. : 61-70 |
[16] | Y.Zheng, Y.Zheng, R.Rong. Effects of nanoparticles SiO2 on the performance of nanocomposites. Materials Letters. 2003; 57 : 2940-2944. |
[17] | Stephan Sprenger. Epoxy resins modified with elastomers and surface-modified silica Nanoparticles. Polymer. 2013; V.54. : 4790-4797. |