Omprakash H. Nautiyal
Alert India Pvt. Ltd., C1, SMA Industrial Area, GT Karnal Road, New Delhi, 110033, India
Correspondence to: Omprakash H. Nautiyal , Alert India Pvt. Ltd., C1, SMA Industrial Area, GT Karnal Road, New Delhi, 110033, India.
Email: |  |
Copyright © 2012 Scientific & Academic Publishing. All Rights Reserved.
Abstract
The study was conducted with the view of improving the lustiness of the PVC air soles. The formula containing the ingredients; PVC resin, DOP, DBP, R9, Ivamol, MBR did not impart the lustiness on the soles. Hence invention was carried out employing the Methocell F50 and Methocell K100. Interestingly the use of Methocell F50 gave the expected results unlike with Methocell K100. Methocell F50 found to reduce the weight of the soles. It was revealed that the reduction in the weight increased the feasibility of the formulation. Physical evaluations found to give the uniform microcellular polymeric network with the compactness. On the other hand the use of Methocell K100 found to have increased the size of the soles and that was due to probably expanding the microcellular network of the polymeric nature. Due to this Methocell F50 was concluded for the regular manufacturing of the soles with good lustiness.
Keywords:
PVC Air Soles, Methocell F50, Lustiness, Uniform Polymeric Network
1. Introduction
Our study revealed that Methocells of cellulosic nature worked better and provided the lustiness, softness, uniform cellular polymeric network, extending durability to the polyvinyl soles. Quality control specifications were found to be much better than in the absence of these. Though Methocell K100 was not found to have the expected results instead it increases the soles size. It was observed to work much better for recycle polyvinyl batches where the lustiness was the major issue.An important characteristic of polyvinylchloride (PVC) is its ability to absorb additives, such as plasticizers, stabilizers, pigments, and impact modifiers, quickly and in sufficient quantities. However, the required level of porosity is often obtained at the expense of bulk density. Using the appropriate suspending agent during polymerization allows the producer to maintain a balance of these properties. METHOCEL cellulose ethers have been used for many years as suspending agents for vinyl chloride polymerization. These products are protective colloids made of linear polymers of condensed anhydroglucose rings that form a carbohydrate skeleton. Methyl and hydroxypropyl groups are attached to the carbohydrate skeleton via an ether linkage. METHOCEL cellulose ethers are nonionic, surface-active film formers. When used as suspending agents in vinyl chloride polymerization, they provide particle size control, uniform particle size distribution, and porosity that can be optimized for many PVC end-uses. This publication discusses the use of METHOCEL cellulose ethers as suspending agents for vinyl chloride polymerization.Cohen in the year 1982 in his patent studied the use of cellulosic fibrous flock that resulted in light weight soles with anti skid properties. The soles also exhibited the long wear life, improved flexibility.Frederick C. Leavitt in 2003 has studied the non-ionic water-soluble cellulose ethers have been cross linked by irradiation with high energy electrons in aqueous solution. This unexpected behavior of cellulosic toward radiation is reproducible. Cross linking and chain scission are competitive reactions; nevertheless, conditions are described for obtaining one or the other as the predominant reaction. It is proposed that the mechanism is free radical in nature. High beta radiation dose rates (Van de Graff generator) are necessary to crosslink substantial amounts of polymer. Low dose rates, such as usually administered with gamma radiation, fail to yield cross linked products. Degradation, oxidation, and cleavage of substituent groups occur over a wide range of radiation dose rates. The viscosity of the medium also plays a major role in determining whether cross linking will take place. Highly viscous solutions with limited freedom of chain motion are degraded until the viscosity is sufficiently low to allow free bimolecular coupling reactions; then a gelled system forms immediately. Carboxylated cellulosic have not been cross linked by this method. Samples examined were degraded at all levels of radiation. The cross linked cellulose derivatives included methyl cellulose, hydroxyethyl cellulose, methyl hydroxypropyl cellulose, and methyl hydroxybutyl cellulose.[1]This study relates to polyvinyl chloride moldable compositions used in producing flexible unitary shoe soles. More particularly, it covers a polyvinyl chloride composition in which a cellulose fibrous flock has been incorporated therein to form a thermoplastic compounded molding material which, when molded into a shoe sole product, produces a shoe sole that has improved flex life, is light in weight, and has the dull appearance of crepe rubber. This dull appearance is highly desirable from a consumer acceptance standpoint since it is associated with the skid resistance and oil resistance of synthetic rubbers. Shiny soles on the other hand are thought by consumers to have just the opposite properties.[4, 5]It is also known in the literatures to use a vulcanizable polyvinyl chloride molding compound containing inorganic fillers for use in producing shoe soles, but such compositions do not have the crepe-like appearance of rubber or the lightness in weight which is important in consumer acceptance of unitary shoe sole products. Also, this type of product is devoid of ease of flexing and presents a shiny plastic-like appearance which is detrimental to its use as a unitary shoe soling material where the sole per se and the heel are molded in one piece.[4, 5]Hydroxypropyl methylcellulose, acts as a general purpose suspending agent for polyvinylchloride (PVC). It is used for applications where high purity is important. It provides particle size control and uniform suspension. It is known as Methocll F50. Methocell K100 is hydroxypropyl methylcellulose and it also has the same application features that of Methocell F50. But our study has proven that both when employed for the formulation and molded then they exhibited the different results.In the compounding of the polyvinyl chloride composition, stabilizers may be used that will prevent decomposition of the polyvinyl chloride when it is exposed to elevated temperature during the molding process. Such suitable stabilizers can be a blend of barium, cadmium, zinc liquids and powders. It has been found that when from about 0.5 to about 1.5 parts of a stabilizer is used; very good results are obtained in the compounding operation. It will be appreciated that many other stabilizers and stabilizer systems which prevent decomposition of the polyvinyl chloride at elevated temperatures may be used provided only that the stabilizer(s) is compatible with the other ingredients in the composition.[2, 3]The results of research work at Dow has revealed that certain properties of cellulose ethers (hydroxypropyl methylcellulose ether structure) are useful in helping control the properties of the PVC resin. In vinyl chloride polymerizations, cellulose ethers act as both an emulsifier; and during the polymerization, as a protective colloid to prevent excessive coalescence of the monomer droplets. The average particle size of the organic droplets in the aqueous phase during the PVC polymerization reaction is a function of the interfacial tension, intensity of agitation, viscosity of the two phases, and the volume fraction of the dispersed phase. The average particle size of the PVC resin was found to be a direct function of the interfacial tension multiplied by the 0.2 power of the gel strength of the cellulose ether solution. The interfacial tension of the cellulose ether solution/organic interface is probably the most important factor in determining the resin particle size. Particle size distribution widens with an increase in interfacial tension. Resin bead porosity is also important and is directly related to the solubility of the cellulose ethers in the organic phase. This observation supports the proposed seed stabilization theory that can explain the formation of a porous resin bead. The use of a proper suspension agent like cellulose ethers with or without a secondary surfactant will help control important properties of the PVC resin product. It control the average molecular weight, degree of substitution, and grouping distribution on the cellulose chain of the cellulose ether suspension agent (all of which affect interfacial tension) is important for the PVC manufacturer.[6, 7]
2. Materials and Methods
Resin (25 Kg), DOP/DBP (8+8 Kg), CPW (3 Kg), R9 (0.750 Kg), Ivamol (0.500 Kg), Stearic acid (0.500 Kg), Foaming ADC (0.350 Kg), MBR (8kg), Methocell F50 (0.150 Kg) and CaCO3 (1 Kg) were purchased from the leading manufacturers in India. All the raw materials were pretested in the QC laboratory before employed for the production. Methocell F50 and Methocell K100 were purchased from Dow USA.
2.1. Blending and drying of the Formula
The raw materials as stated earlier were poured into reacting vessels with agitation, heating and discharge manhole. It was then agitated and heated at 100℃ for about 45 minutes. Methocell F 50, 0.150 Kg was charged and allowed to be mix properly. Later it was discharged into the carrots and allowed to cool at room temperature before it was taken for the molding. Once it was cold then it was charged into the hopper attached to 20 station molding machine along with purge of air into the mold. The molded soles were put into the baskets and were allowed to cure for 24 hour. It was then sent for the quality evaluation to quality control laboratory. 2500 Paris of air soles were produced.
3. Results and Discussion
While employing Methocell K100 in the PVC formula it was observed that the soles molded were with the uniform cell structure except the front sole area where small pin holes were visualized also chemical clots were seen formed in some of the places of polymeric network. Table 1 result evaluations indicated the sole Weight (187 and 189 g) variation existed in the left and right side of the soles (283 and 283 mm) but the size was the same. Hardness Shore A measured by Dura meter was shown to be 46. Cup depth of heal measured found to varied (3.45-3.52) and (3.07-4.89). Soles thickness in both the cases was also varied 9.37 and 8.7 mm. Heal thickness measurement was also varied 26.91 and 25.3. Visual cell structures are shown in the figure 1. Table 1. Evaluations of PVC soles employing Methocell K100 (Fresh Batch) |
| Sr. No. | Inspection Description | Method | Fresh With Methocell K 100 (Rt) | Fresh With Methocell K 100 (Lt) | 1 | Weight (gm) | Weighing Balance | 187 | 189 | 2 | Sole Length (mm) | Scale | 283 | 283 | 3 | Hardness (Shore A) | Dura meter | 46 | 46 | 4 | Cup Depth (mm) | Vermeer | 3.45 ~ 3.52 | 3.07 ~ 4.89 | 5 | Sole Thickness (mm) | Vermeer | 9.37 | 8.7 | 6 | Heel Thickness | Vermeer | 26.91 | 26.3 |
|
|
Table 2. Evaluations of PVC soles employing Methocell F50 (Recycle Batch) |
| Sr. No. | Inspection Description | Method | Regular | Fresh (Film Former Added) | Fresh (Film Former Added) + Waste | 1 | Weight (gm) | Weighing Balance | 226 | 222 | 245 | 2 | Sole Length (mm) | Scale | 289 | 288 | 287 | 3 | Hardness (Shore A) | Dura meter | 42 | 35 | 37 | 4 | Cup Depth (mm) | Vermeer | 4.034.32 | 4.154.32 | 4.204.42 | 5 | Sole Thickness (mm) | Vermeer | 10.21 | 10.45 | 9.98 | 6 | Heel Thickness | Vermeer | 30.89 | 31.9 | 29.2 |
|
|
Table 3. Evaluations of PVC soles with Methocell F 50 (Fresh Batch) |
| Sr. No. | Inspection Description | Method | Without Film Former (RIGHT) | Fresh With Film Former (LEFT) | 1 | Weight (gm) | Weighing Balance | 188 | 177 | 2 | Sole Length (mm) | Scale | 276 | 275 | 3 | Hardness (Shore A) | Dura meter | 42 | 41 | 4 | Cup Depth (mm) | Vermeer | 3.29 ~ 4.05 | 3.38 ~ 4.04 | 5 | Sole Thickness (mm) | Vermeer | 9.69 | 9.67 | 6 | Heel Thickness | Vermeer | 29.69 | 28.65 |
|
|
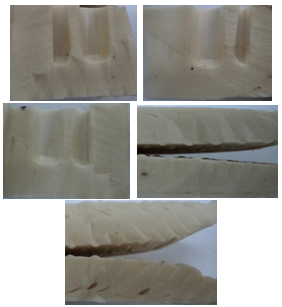 | Figure 1. Uniform cell structure is observed except the front sole area where small pin holes are visual, Chemical clots are found in some places |
When Methocell F 50 was employed in the recycle PVC formula then the result obtained in the table 2 shown, regular sole weight 226 g, regular sole weight with F50, 222 g and recycle batch PVC soles weighed 245 g. Sole length was almost unchanged but the hardness Shore A was quite fluctuating. Cup depth was slightly inconsistent. Heal thickness in case of regular formula and with F 50 was same but found to be lesser in case of recycle batch of PVC with the value of 29.2 mm.[8, 9. 10]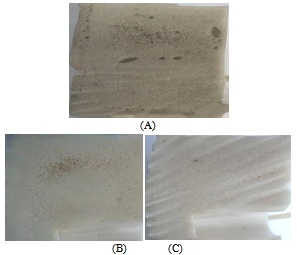 | Figure 2. Microcellular image analysis of polymeric network with Methocell F50 (Recycle PVC batch) |
In figure 2 of A shown the cell structures were Cells Structure is not uniform, big and small, both are present Not Uniform Cells Structure but less than Regular one Uniform (small) cells Structure not uniform and has the big and small network, B does shown the non uniform cell structures but were unlike the A. C image analysis of polymeric network was very uniform and even surfaces. Table 3 result evaluation was for the fresh batch of the PVC where Methocell F 50 employed. It was observed that left and right soles varied in the weight but the sole length was consistent. Hardness Shore A and cup depth measurements were consistent. Sole and heal thicknesses were also observed to be consistent. 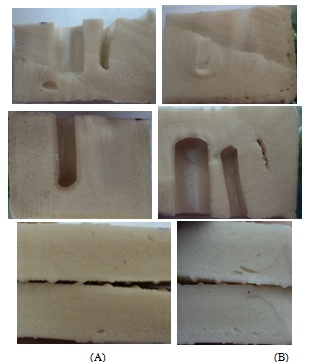 | Figure 3. (A)Mix Results are observed regarding cell structure, somewhere it seems uniform and somewhere big and cured Air Traps |
Figure 3 Image analyses of A shown mix results with regard to cell structures, it does seem uniform but at some places big and cured air traps were observed. B image analysis had shown uniform cell structures at all the places besides heal area where pin holes were observed near the skin. With the use of Methocell F 50 the Sole skin was soft and bright but the K 100 gave the soles with the hard skin and with the yellowish shade. Since the chemical structures of the Methocell F 50 and K 100 have the different structures so the synergies with polyvinyl chloride may have been different due to this the results were consisted in case of F 50 but inconsistent in case of K 100. Porosity is a key parameter of PVC resins. Porosity determines the ease of removal of un reacted vinyl chloride monomer as well as the speed of plasticizer uptake. Porosity is largely influenced by the choice of an organ soluble secondary suspending agent. The balance of porosity and bulk density is a constant issue for the suspension PVC producer. Aqueous solutions of METHOCEL cellulose ethers reduce the interfacial tension (IFT) of the vinyl chloride monomer, facilitating dispersion and yielding smaller droplets. METHOCEL cellulose ether forms a skin at the interface, preventing droplets from coalescing. Upon heating, cellulose ethers dehydrate, forming a gel that further strengthens the protective film. The gelling temperature determines the application temperature of the cellulose ether. Cellulose ethers show a limited solubility in organic solvents. Higher grain porosities are observed with increased solubility.[8, 9. 10]Interfacial tension is determined by substitution pattern, concentration of the cellulose ether, temperature, and nature of the organic phase. Some typical interfacial tension (IFT) values of 0.05% cellulose ether solutions and 1, 2- dichloroethane at 30°C for different cellulose ether products. Within the chemistry of METHOCEL cellulose ethers, IFT increases in the following order: J < E < F < A < K. The lower the IFT value, the smaller the initial droplet size. The highly substituted chemistry products show the lowest IFT values, indicating a more hydrophobic nature. METHOCEL K products have the lowest level of substitution and show the lowest reduction of interfacial tension.[8, 9. 10] It can be shown that gel strength has a small impact on the average grain size of PVC. Particle diameters have been found to be a direct function of interfacial tension multiplied by the 0.2 power of the gel strength of a 5% aqueous solution at 65°C. The gel strength of METHOCEL products decreases in the following order: A > F > E > K > J. Gel temperature is also strongly determined by the substitution pattern. Different reaction temperature ranges are recommended to make full use of the gelation effect. Grain size differences can be explained by variations in interfacial tension. METHOCEL K100 has the highest IFT value, resulting in larger initial monomer droplets and eventually causing larger resin grains. Gel strength affects properties only by the power of 0.2, and its effect is probably hidden by other effects within this series of experiments.
4. Conclusions
In our entire study of employing Methocell F 50 and K 100 it was concluded that Methocell F 50 gave the better results from the soles quality point of view as the complete factors of quality were most acceptable for the market. Methocell F 50 provided the softness and lustiness to the soles besides the uniform microcellular structures. The soles were also found to pass the SATRA test of 1lacs cycles and no cracks existed at 90℃ movements. Methocell K 100 gave the toughness and yellow shade on the skin of the soles that might have interfered with lacquers coating.Bulk density and grain porosity are directly related to interfacial tension. High IFT values, such as in the case of METHOCEL K100, result in high bulk densities and extremely low porosities. The opposite is observed for METHOCEL E50.A common way to control PVC grain size is to change the amount of cellulose ether added to the reactor. Increasing the concentration of the METHOCEL suspending agent results in better surface coverage of the initial monomer droplets and reduces the aggregation tendency during the “sticky” state o polymerization. Although the difference is not very large, the standard variation data of Table 8 indicate that METHOCEL F50 produces a smaller particle size distribution than METHOCEL K100.The bulk density increases with an increase in METHOCEL F50 concentration while the corresponding porosity decreases. The trend with METHOCEL K100 is less clear concerning bulk density, which remains rather constant with variation of the concentration of the suspending agent. Hydroxypropyl methylcellulose dehydrates in aqueous solution when the temperature rises, forming a gel that contributes to droplet protection against coalescence. This gelling effect is reversible when the temperature is reduced below the gel point. When using METHOCEL cellulose ethers as suspending agents, one must consider that the surface activity of these products decreases when the products are heated above the gel point.
ACKNOWLEDGEMENTS
I am heartily indebted to the Marketing Director of the Dow Chemical Inc. USA for providing the courteous samples of Methocell F 50 and K 100 for carrying out the R&D at the pilot and commercial level. Further the team is also thanked for explaining the every technicality of their products.
References
[1] | Cohen Arnold, Polyvinyl chloride shoe sole molding composition containing cellulosic fibrous flock, US Patent 1982, 4343727. |
[2] | Nitis Sarkar, Wesley L. Archer, Utilizing cellulose ethers as suspension agents in the polymerization of vinyl chloride, Journal of Vinyl Technology, vol. 13, no. 1, 26-36, 1991. |
[3] | L Ford, Alir RS, Effect of Media on the Dissolution Profiles of Propranolol Hydrochloride from Matrices Containing Different Substitution Types of Methocel, Pharmacy and Pharmacology Communications, vol. 4, no. 8, 377-383, 2011. |
[4] | Drew S. Poché, Al J. Ribes and Debbie L. Tipton Characterization of Methocel Correlation of static light-scattering data to GPC molar mass data based on pullulan standards, Journal of Applied Polymer Science, vol. 70, no. 11, 2197–2210, 1998. |
[5] | N. Sarkar, Thermal gelation properties of methyl and hydroxy propyl methyl cellulose, Journal of applied polymer science, vol. 24, no. 4, 1073-1087, 1979. |
[6] | Holger Nilsson, Christer Silvegren, Bertil Törnell, Jörgen Lundqvist and Sven Pettersson Suspension stabilzers for PVC production control for resin porosity, Journal of vinyl technology, vol. 7, no. 3, 123-127, 1985. |
[7] | Holger Nilsson, Toomas Norviit, Christer Silvegren and Bertil Törnell Suspension stabilizers for PVC production II: Drop size distribution, Journal of vinyl technology, vol. 7, no. 3, 119-122, 1985. |
[8] | Holger Nilsson, Christer Silvegren and Bertil Törnell Suspension stabilizers for PVC production I: Interfacial tension measurements, Journal of vinyl technology, vol. 7, no. 3, 112-118, 1985. |
[9] | Frederick C. Leavitt, Cross linking of cellulosic by high energy radiation. II, Journal of polymer science, vol. 51, no. 155, 349-357, 2003. |