F. O Aguele 1, C. I. Madufor 2
1Polymer Technology Department, Auchi Polytechnic, Auchi, Edo State
2Polymer and Textile Engineering Department, Federal University of Technology, Owerri, Imo State
Correspondence to: F. O Aguele , Polymer Technology Department, Auchi Polytechnic, Auchi, Edo State.
Email: |  |
Copyright © 2012 Scientific & Academic Publishing. All Rights Reserved.
Abstract
In this study, carbonised coir (CC), was used as a filler in Natural Rubber, varying the loadings between 0 and 50phr at intervals of 10. Carbon black (CB) was also used within the same range of filler loadings. Filler for composites was characterised on the basis of moisture content, pH, loss on ignition, density, and particles size. The physical properties of the composite samples prepared were investigated. The results of the tests obtained for the composites using the carbonised coir were compared with those obtained from carbon black reinforced composites. It was observed that for hardness, the results obtained from composites of studied filler (CC) compared relatively well with the carbon black (CB) reinforced composites. The hardness for all samples maintained an increasing trend with increase in the filler loadings. For the tensile strength and modulus there were no sharp increases shown with increase in filler loading. The results from tests for elongation at break, compression set and flex fatigue showed a falling trend for the test fillers as the filler loadings were increased.
Keywords:
Keywords Composites, Reinforcing, Fillers, Carbonisation and Vulcanisate
1. Introduction
The demand for polymers in many applications has experienced a steady growth over the years. Rubbers, being a major form of polymers have not been left out. The applications of these rubbers in various areas make it mandatory that they possess some minimum basic requirements in terms of properties, so as to be able to perform effectively in the specified areas. Rubber is an organic material which can be stretched to at least 200% its original length and returns back to the initial length immediately the deforming force is removed. Because rubbers in their pure states have virtually no engineering applications, it is necessary to appropriately compound them in order to obtain good processing characteristics, and the desired cure properties in the finished products[1].Scientists and engineers involved in materials research and development have always been on the search for materials that will meet service requirements under different conditions of application. This has led to the evolution of different types of mixtures, blends, alloys, composites and reinforced materials. “No designer can afford to neglect the opportunities offered by polymers and composites”[2].Most polymers though are identified as single materials by their generic names, are actually not mono-materials. Many additives are usually incorporated to impart desired chemical/physical properties on the finished products. These additives (compounding agents) are carefully selected based on the desired performance target.Rubbers make up a class of polymers known for their ability to undergo large recoverable deformations[1]. The unique behaviour of this class of polymers include the ability to stretch to a number of times its original length, exhibit high strength and modulus while stretched and to retract rapidly to recover fully on release of the deforming stress. The molecular structures of rubbers need to meet up some requirements to enable them possess those requisite properties.For instance, they must be: High molecular weight polymers. Above their glass transition temperature (Tg) at ambient temperatures. Amorphous in their unstretched state, but preferably develop crystallinity on stretching (natural rubber). Contain a network of cross-links to restrain gross mobility of chains.[1,3] . Since network of cross links are necessary to make rubbers useful, it becomes mandatory that rubbers be vulcanised to introduce the needed crosslink networks before it can actually be available for any meaningful application.Rubbers can either be natural or synthetic, depending on their origin. The Natural Rubbers(NRs) are obtained naturally from various species of plants. It is a naturally occurring hydrocarbon polymer made up of 2-methyl-1,3- butadiene, also called isoprene. Those synthesised via chemical processes are referred as synthetic rubbers. A lot of species of trees and shrubs have been identified to produce latex on tapping[5]. The trans-isomer of polyisoprene, known as balata or gutta-percha can be obtained from Sapotaceae latex while Hevea Brasiliensis and guayule yield latex of the cis-isomer popularly known as Natural Rubber. Below, are the structures of the trans- and cis-isomers of polyisopreneRubbers, natural or synthetic have inherent properties, which are unique to them without the influence of any additive. For instance, natural rubber is known to have a very high green strength ranging between 15MNm-2 and 20MNm-2 in its unfilled state[4]. This unique strength relies on its ability to crystallise on elongation, giving high tensile strength in the direction of elongation[5]. This produces a superior form of reinforcement as it limits movement between neighbouring molecular chains and leading to increase in hysteresis and ultimate strength.[6]\. This property is usefully harnessed in the application of Natural Rubber in some areas in its unfilled or lightly filled composites. Other physical properties are shown in Table 1:Table 1. Inherent Physical Properties of Natural Rubber[5]. |
| Parameter | Value | Density at 20oC | 0.906 - 0.916 g/cm3 | Specific Heat | 1.905 KJg-1K-1 | Refractive Index | 1.5191 | Heat of Combustion | 45.2KJ/Kg |
|
|
Despite the seemingly fantastic properties of Natural Rubber, it is found that its usefulness is limited. This is a reason why it has to be compounded appropriately to meet various areas of needs, followed by vulcanisation so as to improve on its properties such as hardness, modulus etc. This calls for the addition of materials, which help to enhance the properties to the designed application level. The addition of these materials modifies their properties, reduce costs and extend their service life[7, 8, 9] Among these property-enhancing additives, fillers play a very prominent role.[4,10].The quest for more materials that can be used as fillers has been on. For instance, considerable efforts have been made to produce fibre reinforced polymer composites using rice husk, groundnut shell, rubber seed shell, jute, raffia, coconut fibre, wood fibre etc[11]Fillers are solid additives, which are added to rubbers or other polymer materials to either act as cheapeners or to enhance the physical properties of the materials and to some extent, the chemical properties too[1,3, 9,12]Fillers can be classified on different bases. One basis is that, which groups fillers into two classes – inert and reinforcing fillers[3]. Another principle classifies fillers on the basis of their nature, having particulate, resinous and fibrous fillers[4,13]. This latter is more commonly used.There are some factors, which influence greatly the interaction between a given rubber and particulate filler. They include extensity, intensity and geometrical factors. The particle size has a great influence on the reinforcement ability of the fillers. It has been found that the finer the particles, the higher the reinforcement properties offered[9]. The chemical nature of the fillers’ surface also has influence on the reinforcing properties. That is why at times fillers are treated with either surface active or coupling agents before use in rubber composites[1,3,9] Extensive works have been going on in the search for possible substitutes for some grades of carbon black as filler for rubber products. For instance, by-products from agricultural sources have been used – maize cobs, rubber seed shell, ground nut husk, cassava peeling, plantain peel 14], coconut fibre[7], rubber seed shell carbon 15] and etc. In this paper, we present a study done on the effects of carbonised coir as filler from a renewable source on Natural Rubber.
2. Materials and Methods
2.1. Materials
The main material used during this work was natural rubber (NR) crumb of grade NSR – 10 (Nigeria Standard Rubber) obtained from KB Rubber Industry Sapele, Delta State, Nigeria. This rubber grade also conforms to TSR-10 (Technically Specified Rubber). The coir was obtained from Agbede in Edo State, Nigeria.The other compounding ingredients and additives used were zinc oxide, processing oil, tetramethyl thiuram disulphide (TMTD), mercaptobenzothiazole sulphanamide (MBTS), trimethyl quinoline (TMQ), stearic acid, carbon black (N330 HAF) and sulphur. These compounding agents are of commercial grade and so were obtained from various chemical out lets (Jonaz Industrial Chemicals, Stinpex Chemicals and Ally Industrial Chemicals) in Benin, Edo State.
2.2. Preparation of the Filler
The crude coir obtained from the coconut shell was sun-dried. The material was then torn and ruffled to remove the lignin. In doing this, we used mortar and pestle to pound the sun-dried material so that the fibre was separated from the mass of material (caution is needed not to grind the fibres at this stage). The coir so obtained was then dried in the oven at a temperature of 125oC, The filler was then carbonised at a temperature of 800oC. To avoid oxidation, which could subsequently cause ashing, an inert environment was created by the passage of Nitrogen gas through the carbonising pot. The carbonised material was ground and graduated mesh sieves were used to determine the particle size.
2.3. Characterisation of the Filler
The parameters which were used included moisture content, ash content, loss on ignition, filler density, pH value, diameter and surface area. These parameters were determined using the appropriate standard methods and result presented in Table 3.
2.4. Preparation of Composites
The rubber was masticated and mixed with the additives using the two roll mill and adopting the standard method specified in the American Society for Testing Materials (ASTM-D 3184-80)[16]for all the composites. The filler loadings in weight were varied from 0 to 50 phr. A separate set of composites was also prepared using carbon black as filler and likewise varied within the same range. This served as a basis for comparison in this work. The formulations are shown in Table 2.
2.5. Vulcanisation
The rubber composites were vulcanised in the laboratory and test pieces were prepared for analyses. Curing was done at a temperature of 140oC for five (5) minutes. Sulphur was the vulcanising agent employed in this work.
2.6. Property Analyses of Composites
Test pieces were prepared from composites, into appropriate forms and shapes for various analyses and tests. Tests performed during this work included: Hardness test, Abrasion resistance test, Compression set test, Flex fatigue test, elongation at break and Tensile Strength test the specified standard methods.(ASTM-D1415-06, D395-03[17]Table 2. Formulations for Reinforced Natural Rubber Composites. |
| |
|
3. Results and Discussion
3.1. Results
Table 3. Showing the characteristics of Carbonised Coir(CC) and Carbon Black(CB) 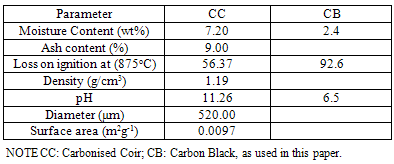 |
| |
|
3.1.1. Hardness
Table 4. Showing the result for Hardness Tests (IRHD) |
| Filler loading | CC | CB | 0 | 30 | 30 | 10 | 31 | 41 | 20 | 33 | 46.5 | 30 | 35 | 48 | 40 | 37 | 51 | 50 | 38 | 55 |
|
|
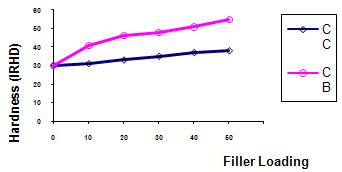 | Figure 1. Effect of Filler Loading on Rubber Hardness |
3.1.2. Compression Set (%)
Compression Set % =
Where: to = original thickness tf = final thicknessTable 5. Showing the results for Compression Set Test |
| Filler loading | CC | CB | 0 | 40 | 40 | 10 | 38 | 27 | 20 | 35.5 | 22 | 30 | 32 | 19 | 40 | 28 | 14 | 50 | 24 | 12 |
|
|
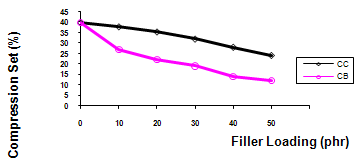 | Figure 2. Effect of Filler Loading on Compression set of Rubber Composites |
3.1.3. Elongation at Break (%)
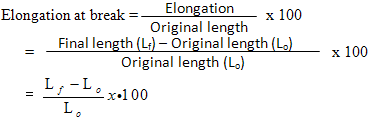
Table 6. Showing the results for Elongation at Break |
| Filler loading | CC | CB | 0 | 880 | 880 | 10 | 690 | 600 | 20 | 630 | 520 | 30 | 580 | 520 | 40 | 565 | 290 | 50 | 500 | 250 |
|
|
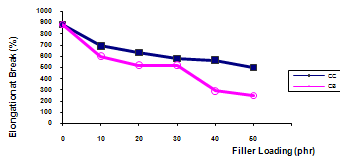 | Figure 3. Effect of Filler Loading on Elongation of Rubber Composites |
3.1.4. Flex Fatigue
Table 7. Showing the results for Flex Fatigue |
| Filler loading | CC | CB | 0 | 21000 | 21000 | 10 | 15268 | 10878 | 20 | 11750 | 10214 | 30 | 10600 | 6765 | 40 | 6540 | 3821 | 50 | 4713 | 2326 |
|
|
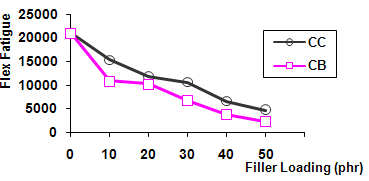 | Figure 4. Effect of Filler Loading on Flex Fatigue of Rubber |
3.1.5. Tensile Strength
Table 8. Showing the results of the Tensile Strength tests (x106Nm2) |
| Filler loading | CC | CB | 0 | 3 | 3 | 10 | 4 | 17 | 20 | 4.3 | 21 | 30 | 4.7 | 26 | 40 | 5.0 | 30 | 50 | 5.2 | 38 |
|
|
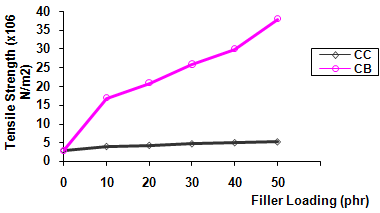 | Figure 5. Effect of Filler Loading on Tensile Strenth of Rubber |
3.1.6. Modulus
Table 9. Showing Results for the Modulus Tests |
| Filler loading | CC | CB | 0 | 1.00 | 1.00 | 10 | 1.00 | 1.80 | 20 | 1.05 | 2.40 | 30 | 0.90 | 2.50 | 40 | 1.20 | 3.80 | 50 | 1.25 | 5.70 |
|
|
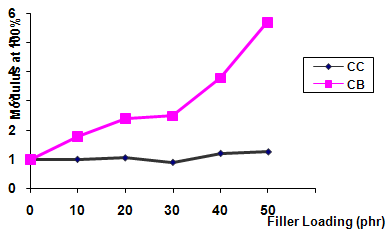 | Figure 6. Effect of Filler Loading on Modulus of Rubber Composites |
3.1.7. Abrasion Resistance
Abrasion Resistance Index (ARI) =
x 100Where:S = Standard Sample Volume Loss T = Volume Loss for Test SampleTable 10. Showing the Abrasion Resistance test results |
| Filler loading | CC | CB | 0 | 11 | 11 | 10 | 47 | 39 | 20 | 46 | 40 | 30 | 46 | 43 | 40 | 48 | 37 | 50 | 41 | 41 |
|
|
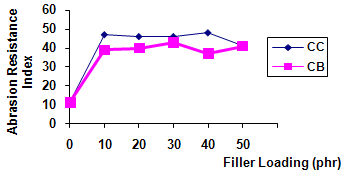 | Figure 7. Effect of Filler Loading on Abrasion Resistance Index of Rubber |
4. Discussion
Initial characterisation of the filler was done to give an insight of the expected behaviour of filler and its effect on the vulcanised rubber composites. The characterisation was done, on the basis of moisture content (%), ash content (%), loss on ignition, density, pH, particle size and surface area. These parameters are determinants of the level of distribution and dispersion of fillers in the rubber which essentially affect the properties of final products, as also accented to by other workers[7]The pH value for the carbonised coir was found to be 11.26 while that of CB was found to be 6.5. (See Table 3.). It was observed during this experiments that cure rates of vulcanisates increased with increasing alkalinity. This was in agreement with the findings documented in many literatures and researches[4,9,18,7]. It was also necessary to measure the loss on ignition for the selected filler. The value of loss on ignition gives an indication of the carbon content lost during combustion and it is a pointer to the effectiveness of the filler. Higher values of loss on ignition indicate the ability of the filler to give higher levels of reinforcement[15]. This is because higher loss on ignition points to higher level of carbon content in the filler. The observation in this work did not quite go in line with that. The reinforcement properties of those rubber composites filled with CC did not show significant rise compared to the CB filled ones. This observation is noticeable in the results displayed for the various physical tests (see Tables 4 – 10 and Figures 1 – 7). The observation could be attributed to the fact that apart from carbon level, other factors, such as particle size, structure and nature of filler play very significant roles in determining the reinforcement potential of given fillers. It was observed that filler loading generally affected all the physical properties tested for both the CC and CB studied in this work, showing an indication for reinforcement potential. However, the extent to which the CC influenced or affected the measured physical properties was significantly low compared to the effect of CB. The general trend of increasing hardness with increase in filler loadings was observed for the fillers (see Table 4 and Figure 1). This is an expected trend attributed to the fact that as more filler loadings are incorporated into the rubber matrix, the composites become more rigid, owing to the progressive reduction of rubber chain elasticity. However, test results obtained from samples with carbon black (CB) have clearly higher values for the various filler loadings (Table 4 and Figure 1). But it is sufficient to say that as shown from results obtained for hardness, the CC filler compared reasonably well with the commercial filler (CB) used. This assertion was informed by the fact that the hardness values obtained for samples reinforced with the test filler (carbonised coir (CC)) rated above 50% of the results obtained for carbon black reinforced products. For instance, comparing the values for hardness for both fillers at a loading of 50phr, we obtained 38IRHD (69.1%) for CC, using that of CB filled vulcanisate as reference point. (55IRHD = 100%).We considered the values as reasonably good since it is above 50% of the hardness value for carbon black filled composite. The results for the compression set test as presented in Figure 2, were observed to take a falling trend as the filler loading was increased. This trend was similar for the carbon black filled vulcanisates. This observation may be connected with the amount of filler incorporated into the Rubber matrix, the particle size of fillers and their extents of dispersion. As more filler are put in the rubber matrix it becomes more rigid and less susceptible to compression loading. High value of compression is an indication for less reinforcement (Figure 2). For elongation at break, (Table 6 and Figure 3), the result revealed a falling trend as filler loading was increased. This fell in line with the observations previously made by some other persons in their independent works. For instance, with rubber seed shell carbon (RSSC)[19] partially ashed rice husk (BRHA) and completely ashed rice husk (WRHA)[20] . The unfilled sample had the highest value of elongation at break and the CB filled samples had the least values for each case of filler loading. This behaviour is linked with the adherence of the fillers to the polymer phase, which results in the stiffening of the rubber chain and thus exhibited as resistance to stretching under applied strain. Figure 4 shows a graph of flex fatigue as against filler loading. The result showed decreasing values with increasing filler loading. Carbon black filled vulcanisates maintained the lowest values again. This once again explained that CB filler give higher rigidity and hardness thereby bringing down the rubber chain flexibility. From Table 8 and Figure 5, which presents the results for the tensile strength tests, showed slight increases with increments in filler loading. The graphs ended up as lines almost parallel to the x-axis, signifying low increase in strength as filler loading is increased. However, the values were quite very low when compared to the tensile strength of the CB filled composites. This is as previously observed by Cohan and Spielman and Oguniyi in their independent reports[21,22]These poor strength reinforcements are attributed to the large particle size, nature, structure and low surface activity of the carbonised coir (CC), as used in this work, compared to the particle size and other properties of CB[5,9,23,24]. It was found that reducing the particles size enhanced the mechanical properties like tensile strength, when working with CB[25,26]. The low values of tensile strength of the composites reinforced with CC are also attributable to the nature of both the CC and the rubber[27].The results for the modulus as presented in Figure 6 showed a rising trend as the filler loadings was increased. However, this was very clear with the CB filled vulcanisates while those the CC filled composites as used in this study maintained lower values. This behaviour can be explained by the fact that adhesion occurred between the filler and the rubber matrix, which led to the increase in stiffness, rigidity, strength and hence the modulus. The behaviour could also be explained on the basis of filler properties. For instance, it was found that by improving the surface properties of fillers such as surface area, surface reactivity, filler dispersion and filler-rubber interaction, the modulus of filled rubber vulcanisates was significantly enhanced as reported independently by[26,28]. The fact that the test filler used in this study has larger particle sizes, leading to smaller surface areas than carbon black explain for the low levels of modulus imparted. Another reason is that the CC has more tendencies for filler agglomeration, making dispersion and distribution more difficult. This observation was accented to by other workers[7,9].The abrasion resistance displayed by the test samples took irregular trends of increase in resistance as the filler loadings were increased. The result in Figure 7 actually looked like a single step up, after which, an almost horizontal trend was maintained. This means that filler loading may not continuously increase the abrasion resistance index of the composites. As the filler loading is increased, the adhesion strength between polymer and fillers falls, this could partly account for the irregular behaviour of abrasion property. Also from observation, there may be a maximum level of loading for optimum performance.
5. Conclusions
This work was an investigation of effects of carbonised coir on the reinforced properties of natural rubber composites. It was motivated by the drive to search for possible alternatives to carbon black as compounding filler for polymer products, which could find valuable applications in various areas. It is expected that the success of this work, if well harnessed or given the appropriate priority, would reduce the pressure on CB, which is obtained from petroleum by-products, an exhaustible source and reduce the cost of rubber products thereby raising the availability to the common man. The carbonised coir showed some potential enhancement on the reinforcing or other mechanical properties of rubber composites as evidenced from the results obtained during this study. However, the performance of the commercially available reinforcing filler (carbon black) was observed to be better in comparison. The enhancement of the mechanical properties of the rubber composites with increase in the filler loading was found to be dependent on the nature of the filler. Further improvements as to harnessing the viability of CC as used in this work as reinforcing filler for rubber composites are expected if some further modifications are done on the filler. It is also expected that varying the carbonisation temperatures could have reasonable effects on the final possible reinforcement imparted on rubber composites. These are possible areas for future studies.
References
[1] | Katchy, E.M. (2000); Introduction to Polymer Technology. 1st edition. El Demark Enugu. |
[2] | Ashby, F. Michael and Jones R.H. David (1998); Engineering Materials 2. An Introduction to Microstructures, Processing and Design. 2nd edition. Butterworth-Heinemann, Oxford. |
[3] | Billmeyer, F.W. (1970); A Textbook of Polymer Science John Wiley and Sons, New York. |
[4] | Asore, E.J. (2000); An Introduction to Rubber Technology. Joseg Books Benin City. |
[5] | Bhatnagar, M.S. (2004); A Textbook of Polymers: Chemistry and Technology of polymers; (Processing and Applications). Vol. II 1st edition S Chand New Delhi. |
[6] | Cain, M. E. (1974); Engineering Design with Natural Rubber. Malaysian Rubber Producers’ Research Association, Hertford, England. |
[7] | Egwakhide, P.A; Akporhonor, E.E and Okieimen F.E. (2007); Effect of Coconut Fibre Filler on the Cure Characteristics, Physico-Mechanical and Swelling Properties of Natural Rubber Vulcanisates, Int. J. Phys. Sci. 2(2):39. |
[8] | Ski, K.B. (1970); Engineering Materials. Properties and Selection. Reston Publishing, New York. |
[9] | Kumar, A. Anil and Gupta K.R. Rakesh (1998); Fundamentals of Polymers. International edition. McGraw Hill, Singapore. |
[10] | Brennan J.J and Jermyn, T.E. (1965); Properties of Black Reinforced Blends of Natural Rubber and Butadiene Rubber. J. Appl. Sci.9:27. |
[11] | Brydson J.A. (1985); Plastic Materials. 4th edition, Butterworth London. |
[12] | Drivers, W.E. (1979); Plastic Chemist and Technology. Van Nostrand, London |
[13] | Boonstra B.B. and Blow C.M. (1971); Rubber Technology and Manufacture. Butterworth, London 227. |
[14] | Wafwoyo, W., Seo, C. W. and Marshall, W. E. (2001); J. Chem.. Technol. Biotechnol. 74; 1117. |
[15] | Okieimen, F.F. and Imanah, J.E. (2003); Characterization of Agricultural Waste Products as Fillers in Natural Rubber Formulations. Nig. J. Polym. Technol. 3(1):201 |
[16] | ASTM D 395 – 03(2008); Standard Test Methods for Rubber Property. – Compression Set. |
[17] | ASTM D1415 -06 Standard Test Methods for Rubber Property. – International Hardness. |
[18] | Horn, J. B. (1971); Rubber Technology and Manufacture. Blow, C. M. (Ed). Butterworth, London. |
[19] | Okieimen, F.E. and Imanah, J.E. (2005); Physico-Mechanical and Equilibrium Swelling Properties of Natural Rubber Filled with Rubber Seed Shell Carbon J. Polym. Materi 22 (4): 409. |
[20] | Ishak, Z.A.M. and Baker, A.A. (1995); An Investigation on the Potential of Rice Husk Ash as Fillers for Epoxidised Natural Rubber. Eur polym. J. 31(3):259. |
[21] | Cohan, L.H. Spielman, R. (1948); Ind. Eng Chem.. 40:2204. |
[22] | Oguniyi, D.S. (1989); Nig. J. Appl. Sci. 7(1):87. |
[23] | Paterman, M.Q. (1986); Chemorheology of Model Filled Rubber Compound During Curing. Rubber World. 194:38. |
[24] | Morton M. (1987); Rubber Technology. 3rd Edition. Van Nostrand New York. |
[25] | Lawrence, E.N. (1974); Mechanical Properties of Polymers and Composites Vol.2. Marcel Dekker, New York. |
[26] | Parkinson, D. (1957); Reinforcement of Rubbers. Lakeman and Co London pp12. |
[27] | Meyrick, T. J. (1971); Rubber Technology and Manufacture. Blow, C. M. (Ed). Butterworth, London. |
[28] | Wagner, M.P (1976); Silicone Rubber Compositions Incorporating Silicone Treated Carbon Black. Rubb. Chem. Technol. 50:342 |