David J. Stockton 1, Riham Khalil 2, Lawrence M. Mukhongo 3
1Director Centre for Manufacturing, De Montfort University, Leicester, LE1 7DA, United Kingdom
2Deputy Director Centre for Manufacturing, De Montfort University, Leicester, LE1 7DA, United Kingdom
3Centre for Manufacturing De Montfort University, Leicester, LE1 7DA, United Kingdom
Correspondence to: Lawrence M. Mukhongo , Centre for Manufacturing De Montfort University, Leicester, LE1 7DA, United Kingdom.
Email: |  |
Copyright © 2012 Scientific & Academic Publishing. All Rights Reserved.
Abstract
The vast majority of the research efforts in finite capacity scheduling over the past several years has focused on the generation of precise and almost exact measures for the working schedule presupposing complete information and a deterministic environment. During execution, however, production may be the subject of considerable variability, which may lead to frequent schedule interruptions. Adopting biological control principles refers to the process where a schedule is developed prior to the start of the processing after considering all the parameters requirements at a machine and updated accordingly as the process executes. This research reviews the best practices in gene transcription and translation control methods and adopts these principles in the development of an autonomous finite capacity scheduling control logic aimed at reducing excessive use of manual input in planning tasks. With autonomous decision-making functionality, finite capacity scheduling will as much as practicably possible be able to respond autonomously to process variability by deployment of proactive scheduling procedures that may be used to revise or re-optimize the schedule when variability process requirements is noted. The novelty of this work is the ability for processing machine to autonomous take decisions just as decisions are taken by autonomous entities in the process of gene transcription and translation. The idea has been implemented by the integration of simulation modelling techniques with Taguchi analysis to investigate the contributions of finite capacity scheduling factors, and determination of the ‘what if’ scenarios encountered due to the existence of variability in production processes. The control logic adopts the induction rules as used in gene expression control mechanisms, studied in biological systems. Scheduling factors are identified to that effect and are investigated to find their effects on selected performance metrics for each machine used. How they are used to deal with variability in process is one major objective for this research as it is because of the variability that autonomous decision making becomes of interest. Although different scheduling techniques have been applied and are successful in production planning and control, the results obtained from the inclusion of the autonomous finite capacity scheduling control logic has proved that significant improvement can still be achieved. This research demonstrated that the correct choice of values for finite capacity scheduling factors has a great impact on the performance measurements, such that, high throughput rate can be reached with a bigger batch size, lower percentage of rework, and shorter stoppages. Quicker movement of goods through the facility means better utilisation of assets. Better utilisation of assets creates additional capacity resulting from faster throughput thereby improving customer satisfaction through quicker delivery. It has also been shown that %waiting, %blocking and %stoppage makes it possible to examine different manufacturing constraints as well as the relationship between non-utilisation and different performance measurements.
Keywords:
Variability, Control Factors, Logic Control, Induction Rules
Cite this paper:
David J. Stockton , Riham Khalil , Lawrence M. Mukhongo , "Autonomous Planning using the Basic Principles of Gene Transcription Regulatory Control", American Journal of Operational Research, Vol. 2 No. 5, 2012, pp. 66-80. doi: 10.5923/j.ajor.20120205.04.
1. Introduction
Many manufacturing facilities generate and update schedules, which are plans that state when certain controllable activities such as processing of jobs by machine, take place. Today’s manufacturing is faced with a rising global competition, challenging customers and employees, decreasing product lifecycles and response times.Within this highly dynamic environment, variability becomes inherent characteristic of manufacturing systems. As stated by[1] “variability in operating conditions is becoming the norm, rather than the exception” and the traditional strategy of operating a manufacturing system independently of its environment is not appropriate any more.Rather, flexibility and responsiveness of manufacturing processes are important features to be considered and explored to deal with the eventual effects of variability quickly and effectively.The systematic treatment of variability is widely recognised as a real problem and one of the main challenges in the area of manufacturing ([2],[3]). George Dantzig once said, “I am working on planning under variability; that’s the big field as far as I’m concerned. That is the future”[4].There is need to develop tools capable of solving problems caused by variability quickly and efficiently. Many of these problems are characterised by a number of finite solutions as well as a value of performance measurements assigned to each solution.Many solution algorithms have increasingly been used in solving most of these problems. The successful application of emergent techniques based on natural comparisons, such as genetic algorithms and neural networks, to manufacturing problems is certainly encouraging; it most definitely points to the natural systems as a source of ideas and models for the development of various artificial systems such as manufacturing.
2. Challenges in Manufacturing
With the evolving mass customisation, the competitiveness in manufacturing is increasingly dependent on the ability to adapt to the novel requirements for on-demand manufacturing. Such adaptation requires increased flexibility in manufacturing capacity and quick response to variability induced by unpredictable operating conditions. Scheduling problem has usually been seen as a function of known and reliable information, providing solutions based on actual or estimated values for all the parameters, and totally assuming that a predictive schedule will be carried out exactly as planned.A wide range of manufacturing and service work environments are characterised by uncertainty. The environment in which a human expert (controller) makes decisions is often complex, making it difficult to formulate modelling of some kind; hence the development of autonomous finite capacity scheduling control logic seems justified in such situations. Developing models for solving difficult finite capacity scheduling problems characterised by variability is a very important and challenging research task.Finite capacity scheduling techniques need to be combined with control principles adopted from biological systems to improve the level of autonomous decision-making functionality of machines under unpredictable conditions of system variability. As can be learnt in biological systems, survival is not for the fittest but for the most adaptive; hence firms better prepared to survive are those that better respond to variability by adapting dynamically their operations.Responding to this variability in the system is related with the having capability of autonomous decision-making functionality as encountered in biological processes. The decision-making requires the ability to maintain performance in face of internal and external variability. Inability to respond quickly to different types of variability leads to deviations from initial plans and causes delays and generally unwarranted stoppages.Most of the organisations operating in the traditional way suffer from the centralised and hierarchical control that has weak response to variability. In this regard, the challenge is to develop an autonomous finite capacity scheduling control logic adopting biological control principles founded in gene transcription and translation – a control method displaying immense capabilities of dealing with system variability.A response to customer needs, input and process variability, recovery capability and autonomous decision-making could facilitate the smooth operation of manufacturing firms. A practical solution is possible through the application of the control principles in gene transcription and translation – the concept of biological manufacturing systems – by considering a number of control factors. Such manufacturing operations could be seen as individual genes that are responding to their environmental stimulus by either assembling the processing mechanisms or processing parts through production of required proteins for gene expression. Potential genetic information such as customer requirements could describe the manufacturing system variability required to adapt or process more efficiently the given tasks.The potential of variability continuously appearing in manufacturing processes and equipment (machine, tools, and operators) and raw materials or parts resulting, require an autonomous system that aims at reducing excessive highly skilled manual input in finite capacity scheduling activities. The work presented here makes use of biologically inspired approach based on gene transcription and translation control principles which localise their decision-making at respective production machines using reduction rules.By adopting this idea taken from natural gene transcription and translation control processes and by taking into account changes in systems parameters occurring in time at each machine levels, modelling the way the system should respond is still an open question. Many other methods have been explored but in this paper, the final decision on how the machine responds to variability among available options will be made based on some reduction rules to guide the system autonomy. Specific comparative cases between manufacturing and biological systems are presented. A modelled validation is developed and explained. This work attempts to contribute towards increased adaptability of a production line affected by variability.
2.1. Manufacturing and Biological Systems
Many recent studies in manufacturing systems have reported continuous changes in the production processes caused by variability of many kinds[5]. Taking into consideration these variability during planning and scheduling is a vital undertaking to ensure quick response to customer demands and also remaining competitive to the ever changing business environment. The inclusion of variability in scheduling in manufacturing and service work environments may be improved further by adopting some principles of biological control providing highly autonomous decision making functionalities especially in gene transcription and translation processes.Scheduling has become a core manufacturing tool both on strategic and operational levels. In fact, any activity that is perceived as significant and necessary from the customer perspective could be variability which should be taken into consideration during the scheduling process or after a schedule has already been constructed. Consequently, such developments change the way manufacturing systems are controlled, such that future scheduling of activities will have to adopt strategies and methods founded in biological systems.This section provides the useful similarities between biological systems and manufacturing systems. Some basic principles of biological control are underscored in line with the fundamental principles of autonomous decision-making functionalities of these systems with a possible application to manufacturing is presented.
2.2. Overview of Modern Manufacturing Operations
[6] define manufacturing system as an objective-oriented network of process activities through which flow of material and information occur. In this definition several aspects are highlighted:a. objectives help to know the direction the organisation takes to meet customer demands and to sustain itself, which are viewed as performance metrics in this research;b. process activities which may include the usual physical processes or steps taken during production or other steps that support the direct manufacturing processes, such as kitting, shipping, maintenance etc.;c. flow of materials for the parts being manufactured from machine to machine that is used to make the product;d. flow of information describing how information about orders, activities being executed, products in-production, products made, operators, work process etc. is gathered, stored, transferred, processed, used for manufacturing or decision making processes[7], and;e. network of interacting parts as well as information which when managed will establish good synchronisation in production activities, to the betterment of the customer. Modern manufacturing operations are accomplished by mechanised, automated equipment supervised by operators and they include assembly and almost always the activities are carried out as a sequence of operations[8]. Manufacturing is therefore concerned with the transformation of materials into items of greater value by means of one or more processing and/or assembly operations. It adds value to the material by changing its shape or properties, or by combining it with other materials, hence having variety of inputs and outputs. Figure 1 shows the general structure of a manufacturing system, where inputs are scheduling factors acting as sources of variability, causing process variability at machines and finally outputs being products or services and performance metrics.Increased challenges from global competitors have prompted many manufacturing firms to adopt a number of manufacturing approaches[9]. Of particular significant among these approaches is the concept of lean production[10]. 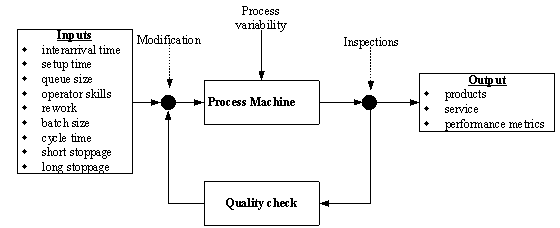 | Figure 1. Manufacturing system inputs and outputs |
3. Similarities between Manufacturing and Biological Processes
Biological processes have been found to display a number of similarities with manufacturing systems. Because of these similarities, attempts have been reached to learn the structures and behaviours of biological systems with the aim of establishing the possibility of adopting biological control principles into manufacturing. It is because of this background that this research develops autonomous finite capacity scheduling control logic adopting biological control principles founded in gene transcription and translation processes.Table 1. Structural similarities between Biological cell and Manufacturing |
| Manufacturing | Cell Organelle | Function | Plant/Factory facility | Cytoskeleton | Factory premises | Planning and scheduling logic | Nucleus | Manages activities, initiates production and controls different activities | Receive Inspection/Entry Point | Cell membrane | Receiving goods and ready to be processed at different machines | Shop floor | Cytoplasm | Factory floor where products are assembled, finished and shipped | Machine/ working area | Ribosomes | Machines which can include conveyor belts and robots that make parts | Assembly Line | Endoplasmic reticulum | Machines, tools and operators that assemble different parts | Storage area/ buffer | Vacuole | Store different levels of inventories for later use, or if the succeeding is not ready to accept work | Energy Producer/ Generator, boiler room or furnace | Mitochondrion | Produces energy for the factory | Transportation | Centrioles | Move the material among different machines/area via forklift, AVGs etc. | Packaging and Dispatch | Golgi bodies | Packs products for distribution | Scrap Area | Lysosome | Scrap parts that need decision where |
|
|
3.1. Overview of Modern Manufacturing Operations
Some structural similarities between manufacturing and biological cell have been identified ([11],[12],[13], and[14] and are tabulated in Table 1.
3.2. Functional Similarities
Functional similarities show the operational similarities between biological and manufacturing systems which make use of the structures identified in Table 1. They comprise the control features that run the structures identified to achieve the set goals. Table 2 list some of the functional similarities identified in this research. Table 2. Functionally commonalities |
| i. flow of information and material among different machines in production flow lines[15]; ii. generate highly ordered and complex structures from simple options, stores information for making choices between different options, and transmit adequate instructions to the correct places; iii. comprise of a large number of different machines (as enzymes for biological systems) where different activities may take place such as assembling, breakdowns, planned and unplanned maintenance. This was introduced in this research here to as process variability, mean time to repair (MTTR), mean time to failure (MTTF), and % rework and change over[11]; iv. ability to measure completed job represented as throughput, equivalent to metabolic flux through a certain pathway in biological systems[14]; v. degree of flexibility to manufacture mixed products which is the need of nowadays successful manufacturing system[16]; vi. managing different types of variability that can occur in flow production lines[17]; vii. need to be adaptive i.e. quick response to variability (as in (vi)) or in the whole supply chain of process. However, this research will investigate the levels of variability that occur only in the manufacturing process[18] and; viii. multiple control points that enhance the efficiency of operation and also improve process synchronisation[11]. |
|
|
4. Proposed Steps for Research Experi-ment
This section presents the steps of the experiment and results obtained demonstrating the usefulness and possibilities of adopting biological control principles in autonomous finite capacity scheduling. The results from the experiments showed that there are significant improvements in all the performance measurements identified and because of this, variability in identified factors affects the overall system performance. This effect enables the development of the control logic for the autonomous finite capacity scheduling adopting biological control principles. The experiments showed that operator skills has no direct significant effect on the attainment of the required machine performance, but affects overall queue time and lead time; additionally, variability in factors has different effects on machine variability.
4.1. Results of the Research Experiments
Step 1: Data collection The triangulation research method was used in data collection where both qualitative and quantitative research methods were applied. Methodological triangulation was adopted here by obtaining information from published data used in the simulation model in Step 2. This research has identified nine factors for modelling purposes that are used as controllers for finite capacity scheduling as shown in Table 3. The matrix in Table 4 shows how the factors affect each other and where each feeds into or utilises the same output information. For example from the matrix, Batch size[1] feeds or affects Inter arrival time[3], Queue time[5], Rework[6] and Setup time[7], while Short stoppage is fed by Cycle time[2], Inter arrival time[3], Operator skills[4], % Rework[6] and Setup time[7].These relationships flow through the machines as manufacturing proceeds and hence relationships between machines also exist such that one machine may have a direct or indirect effect on another machine.Table 3. Factors identified for modelling |
| Scheduling Factors | Modelling Parameter | Description | Inter-arrival time | Numbers | Time between work items entering the system i.e. arrival time | distribution | Cycle time | Time | This is time allocated for each machine to complete a specified task, such the time for a punch press to cycle. | distribution | Batch size | Time | Number of work items of the same type to be processed at a machine before the machine is set up to process a different part. | distribution | Operator skills | Resource availability | Operators can move between machines when and where they are needed based on the skills they posse, enhancing operator flexibility. | distribution | Queue time | Time | This the amount of time work spends before being attended to, or before value adding work is performed to or on it. | Rework | % Rework | All pieces of work that do not pass inspection the first time are sent back to a special rework bin and only drawn from this bin if the operation is starved of work | distribution | Setup time | Time | The period of time required to prepare a device, machine, process, or system for it to be ready to function or accept a job. | distribution | Short stoppage | Time | Variety of events such as equipment changeovers that cause minor stoppages within flow processing operations | distribution | Long stoppage | Time | Variety of events such as major equipment breakdowns that cause major disruptions and stoppages in processing operations | distribution |
|
|
Table 4. Relationship between factors 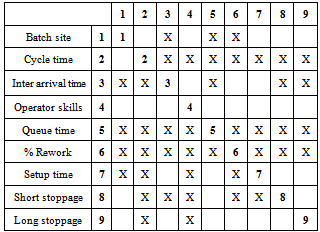 |
| |
|
Step 2: Customer order and Process mapping, Development of simulation model, and Modelling elements and AttributesTable 5. Modelling Element and Attributes 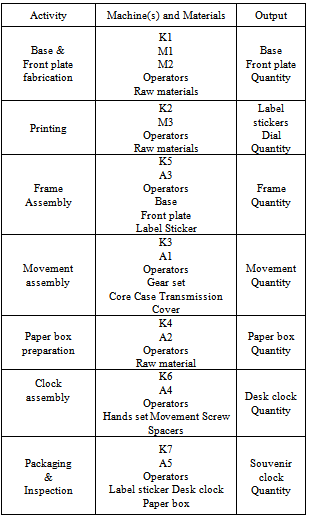 |
| |
|
The idea represented by Figure 2 is implemented as a simulation model. The figure also provided necessary information to determine the manufacturing steps, inputs in terms of raw materials or parts and number of machine in the routine for each part produced to make the final product. Each activity from the customer order may be accomplished using one or more machines, in conjunction with the production constraints and input factors (identified for each machine) to control the activities of each machine. Table 5 shows the input machines, input activities, modelling elements, input factors together with their attributes, and expected outputs.Customer order fulfilment flow chart provides means for the identification of various activities in a customer order used to identify the modelling elements. Each activity was accomplished using one or more machines, together with the production constraints and input factors (identified for each machine) to control the workstation activities. Table 5 shows the input machines, input activities, modelling elements, input factors, and expected outputs.Table 6. Finite Capacity Scheduling Factors with their values at three levels 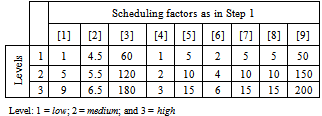 |
| |
|
Taguchi techniques were used as a structured method of experiments for investigating the types of variability among the finite capacity scheduling factors used. Minitab was used to determine which factor had significant effect and the contribution of each factor towards the identified process variability and selected production line performance measurements. L-27 was chosen for this experiment because of the nine (9) factors at three levels each.Figure 2 shows an example of the flow chart for customer order indicating the required input and output machines, input activities and material/parts, and expected output. The process layout was determined from the flow chart and the machines involved in the processes were identified. The cycle time for each processes activity was estimated to determine appropriate scheduling strategies. Machines that required setup were identified because setups cause unnecessary part waiting time; and having many setups results in unnecessary expenses as in wasted storage space and long lead times.Step 3: Performance MetricsTo measure the effectiveness of the proposed method, the following eight performance metrics in Table 6 were used in testing the logic control for autonomous finite capacity scheduling. The output variability (occurring at machine level) being affected by the variability of finite capacity scheduling factors has been considered as performance metrics in this research. The output variability is used to determine the overall system performance metrics identified as throughput, throughput rate, lead time and queue time. Figure 3 shows the objective as relates to each performance metric.Table 6. Manufacturing performance measures used in this research |
| |
|
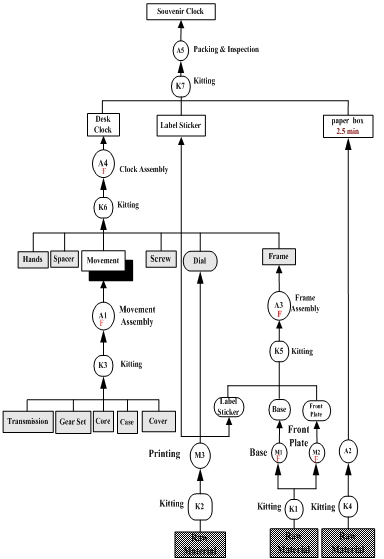 | Figure 2. Flow Chart for Customer Order[19] |
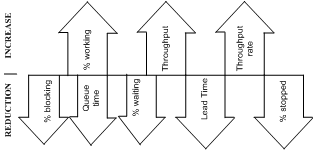 | Figure 3. Overall objective of the selected performance metrics |
Step 6: Applying Taguchi Orthogonal ArrayAccording to the number of factors identified and the levels of depth needed Taguchi L27 OA was chosen and the values for the set of process parameters for each work centre were identified. The experiments were run for 21000 minutes each and a total of twenty seven (27) experiments were obtained. Triangular distribution was used to represent the variability in work centre operation. Figure 4 show the analysis by running DOE to determine the effect each of the nine factors has on the eight performance metrics identified in Table 6.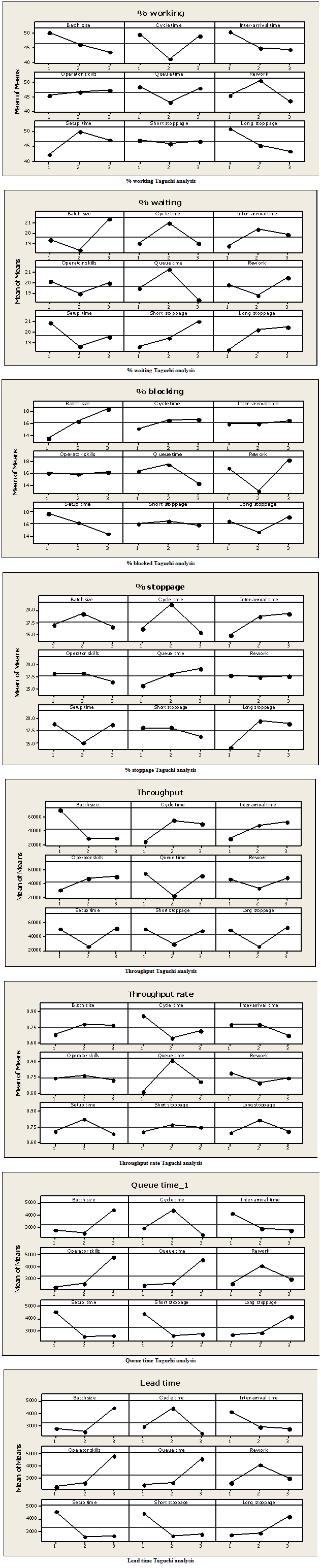 | Figure 4. Analysis of running DOE (Taguchi Orthogonal Arrays) on the schedule control factors |
From the analysis of the results, effect of every factor was observed as related to the production performance. Taguchi method helps to identify the gravity of each factor on production, and it becomes easy to know their relationship with the desired performance. After determination of the variability levels and their related effect on the machines, the experiments were re-running (using the logic developed as explained in Step 8) to note any improvements in the performance. The simulation was again run for the same period of 21,000 minutes, similar to when it was run without the logic to compare the results with previous results. Mean-time-to-Repair and Mean-time-to-Failure were used to determine the machine requirement fulfilment and their availability for finite capacity scheduling. The objective of developing autonomous finite capacity scheduling is to detect the variability in production and remedy the situation early enough without unnecessarily involving manual planning tasks. Step 8: Development of Logic ControlHaving recognised the effects of each finite capacity scheduling factor through Taguchi techniques, it became important to introduce biological control principles as learnt from the literature. The pattern of regulation of gene expression is consistent with protein making process as an important selective process in response to the changing environmental conditions of the gene, which in manufacturing terms we call variability. This information is quite vital to the development of the control logic for autonomous finite capacity scheduling. Manufacturing systems can be made to adopt biological control principles by recognising that:a) there exists causal relationship of machines in the manufacturing system identified to process a certain product;b) there exist partial knowledge of machines (input and output) of direct correlation between observed variability and factors that course them; andc) with knowledge reached in (ii), application of inductive rule technique can help quickly spot the potential variability in processing when unambiguous diagnosis of the conditions is either complex or impossible.Biological control induces rules in the form:if <condition>then <prediction>where <condition> is a conjunct of existence of factors and <prediction> is the prediction of the variability at machines or it could be a group of variability experienced (if ambiguity is not resolvable) of factors which satisfy the rule’s tests.Each factor test is of one of the forms:
for normal, single and multivalued variability a disjunct of values of factors can be used to determining them. <comparator> is either ‘>’ or ‘≤’. These rules show that presence or absence of factors during manufacturing nearly always lead to totally different kind of variability, just as is the case for types of proteins produced with different combinations of amino acids.Machines are related by the part routing, the machine variability and factors that cause them. The variability on one machine may cause some other variability on another machine upstream and downstream. To create a relationship between machines, inductive rules are applied such that feedback mechanisms are introduced at all hierarchical levels forming inputs to other machines and as control signals to others.From the literature, it was possible to determine similarities between manufacturing and biological systems as shown in Section 3, such that the control mechanisms envisioned in biological systems could be adopted in manufacturing systems to improve on efficiency and autonomous decision-making functionality.The development of autonomous finite capacity scheduling control logic calls for in-depth understanding of causal relationships of the involved machines from input to output in form of cause and effect, and the factors or conditions that govern them. The logic developed followed the following steps in line with Figure 2:8a. Determining the relationship between preceding and succeeding machine in a production system.Table 8. Links between preceding and succeeding machines 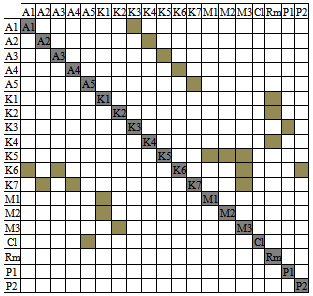 |
| |
|
For clear show of the links between preceding and succeeding machines, Table 8 was used. For example, F5 is the input of A3 only, but K5 is the output of M1, M2, and M3. Another example is M3 which the input to K2, and yet it is an output of K5, K6 and K7. In this table, going along columns indicate the input machines and along the rows indicate output machines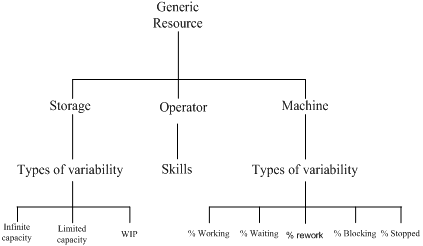 | Figure 5. Simple production line |
8b. Determining machine information: e.g. unique machine name (buffer1); generic machine type (storage); what controls the machine (shelf life, processing time, etc.); and the preceding and succeeding machines (upstream machines and downstream machines). Figure 5 shows three classes of machines and their related types of variability.8c. Determining different machine variability and their defining factors or conditions8d. Identifying performance measurements associated with each machine8e. Developing of the activity rules (as discussed here- under)For example, in Figure 6, if Machine 2 fails, it can be seen that a simple conflict occurs where the Buffer 2 contents (with state = finite) is linked upstream to Work centre 1, blocking it from sending out its finished parts. This conflict can be resolved using a general rule such as shown in Table 9: | Figure 6. Simple production line |
| Rule: IF machine M2 of_type_ Machine is stopped is linked with machine B2 of_type_storage is finite (capacity of buffer reached) THEN machine WC1 of_type_Machine is blocked note_fault in machine M2 type_ Machine OR check machine downstream of M2 |
|
|
As studied from biological systems, the rules governing gene transcription and translation are of the form:if <condition> then <prediction>where <condition> is combination of tests on the factors and <prediction> are expectations that satisfy the rules, <condition> tests. These sets of rules indicate correlations between factors (conditions) and the predictions (different variability) for the system. The rules will inspect a number of different factors before arriving at a conclusion to whether allocate the machine to the activity or otherwise. All this information is valuable for the autonomous finite capacity scheduling control logic. As it stands, a complex manufacturing system such that sketched in Figure 2 (flow chart) may be described and modelled successfully, and a rule set produced.Since the control logic has only a limited knowledge of the system in the form of activity rules, it can quickly recognise the changing conditions of the machine without having to perform a complex in depth, cause-effect analysis of the system.The logic aggregates available information occurring at machine local levels and by doing so, provide control to the manufacturing system as a whole. The decision related to a manufacturing control function is made according to the available information in form of factors having different distribution levels and are appropriate for decision-making.The developed rules mirror the autonomous decision making displaying the three parameters as exemplified in the literature for autonomous decision making – system uncertainty, self-organising, and system recovery.Figures 7 – 14 present plots that compare the results for each of the identified effects input variability as well as the performance measures before and after the application of the autonomous finite capacity scheduling control logic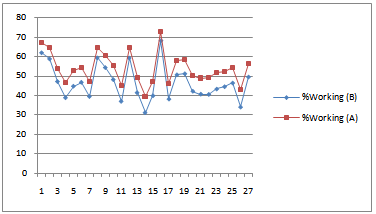 | Figure 7. % working before and after application of the control logic |
% working has been improved after the application of the logic such that more time is spent doing meaningful processing work, for example in experiment number 14, there is a significant increase of 9% working.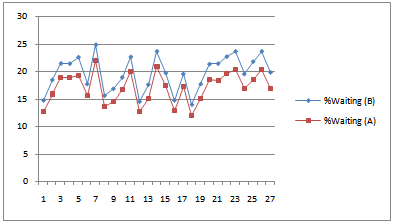 | Figure 8. % waiting before and after application of the control logic |
% waiting has been reduced in every experiment due to an improvement in system synchronisation and consistent and coordinated parts flow in the system.There is a slight improvement in the % blocking in virtually all the 27 experiments carried. This could due the fact there is information feedback which at multiple control points of the manufacturing system. Use of constraints as information signals may have brought about this improvement.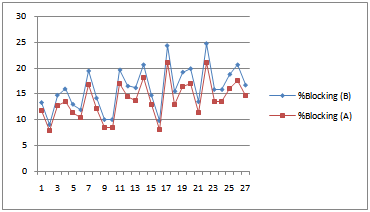 | Figure 9. % blocking before and after application of the control logic |
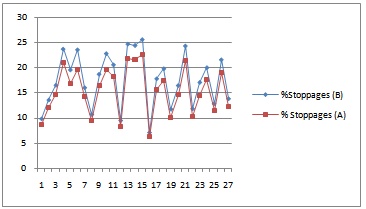 | Figure 10. % stoppage before and after application of the control logic |
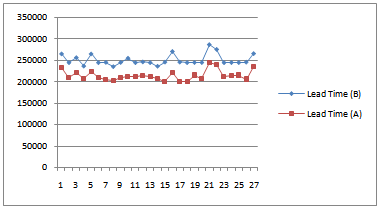 | Figure 11. Lead Time before and after application of the control logic |
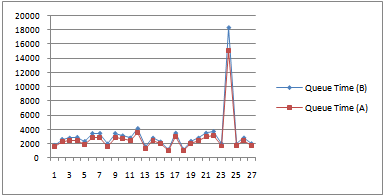 | Figure 12. Queue Time before and after application of the control logic |
There is a marginal reduction in the % stoppage throughout the 27 experiments run. There were less machine stoppages due to the fact that every resource was able to take appropriate action autonomously and so overall system stoppage to perform maintenance was avoided.Because of the improvements in system performance as witnessed in Figure 7 to 14, overall manufacturing lead time was reduced, for example in number 16, the lead time was reduced by about 50,000 minutes. 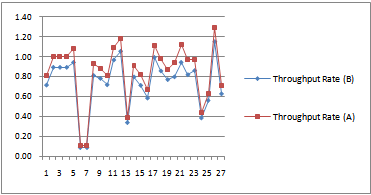 | Figure 13. Throughput Rate before and after application of the control logic |
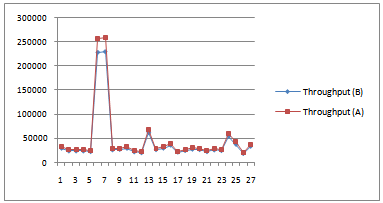 | Figure 14. Throughput before and after application of the control logic |
Table 10. Overall percentage improvement after the application of the logic for four performance metrics |
| % reduction in Lead Time after application of logic | 14.3% | % increase in Throughput after application of logic | 13.1% | % increase in Throughput Rate with application of logic | 13.2% | % reduction in Queue Time after application of logic | 15.3% |
|
|
This research has demonstrated that the correct choice of values of finite capacity scheduling factors has a great impact on the performance metrics. Figures 7 – to – 14 shows: That high throughput rate can be reached with a bigger batch size, lower percentage of rework, and shorter stoppages. Faster movement of goods through the facility means better use of assets. Better use of assets creates additional capacity resulting from faster throughput improving customer satisfaction through faster delivery. The % waiting, % blocking and % stoppage make it possible to examine different manufacturing constraints as well as the relationship between non-utilisation and different performance metrics. By identifying different scenarios in the running of the experiments and by the help of Taguchi Orthogonal Array gave a good standing of each operational factor that can affect the completion of activities in every step in the transformation process. From these results, it can be observed that there was a greater improvement in queue time indicating that with proper coordination there is possibility of avoiding or reducing system inefficiencies between successive steps in the production process. In line with this, to ensure that resources are not starved of raw materials and parts, the methodology implemented ensures that raw materials/parts inter-arrival times are tuned to real time resource availability.The simulation was run with 27 experiments according to the L27 Taguchi Orthogonal Array chosen for the nine factors investigated at three (3) levels updated at the end of each run. Results were collected based on the different scenarios in order to determine the effects and influences of the selected performance measures.
5. Discussion
The main aim of this research was to elucidate the best practices from biological and manufacturing systems, and comparing the developed solution with existing ones with an objective of developing an autonomous finite capacity scheduling control logic. The following provides a discussion of the major issues undertaken: The paper undertook to study the similarities between manufacturing and biological systems to gain an understanding of how principles of control from biological systems could be applied in finite capacity scheduling; By identifying % Working, % Waiting, % Blocking, % Stoppages allows scheduling personnel to determine the source of these process variability and hence design ways of improving machine utilisation as well examining the relationship between non-utilisation and different performance measures. The use of modelling enables examination and simulation of the designed schedule at the shop floor level, providing a tool for checking the schedule; As it is planned, the AFCS acquires its data from the shop floor and hence it should be available as an easy-to-use tool not requiring a large overhead of data entry before it can be run; The coupling of the model with induction rules as developed from biological control principles provides some exciting possibilities of application. At present AFCS performs the synthesis of shallow information for machine interpretation from the model, information is essential for scheduling personnel;
6. Conclusions
The contribution of this thesis emerges from the systematic and thorough examination of the inherent scheduling problems in manufacturing systems. It provides a novel platform for adoption of biological control principles in developing an autonomous finite capacity scheduling control logic. Literature review was conducted about manufacturing systems and biological systems and the comparative analysis focussed on both the structural and functional similarities of the two systems. The two systems have been considered as a good illustration of systems operating with high uncertainty due to variability of orders that are not easy to predict. The theoretical development and practical applications of finite capacity scheduling was defined on the basis of published research primarily. Simulation modelling was developed in order to give a clear and comprehensive description of a manufacturing system. The initial results from the simulation model which covers the scheduling of customer orders were used as the frame for identifying prior empirical and theoretical studies on scheduling rules. Control logic was then developed adopting biological control principles to bring the aspect of autonomous decision-making functionality. There were notable successes of this research shown by the improvements observed in the identified performance metrics. This research has: enabled modelling of manufacturing systems with causally connected machines, each with its own control factors analysed separately providing information on processes variability; made it possible to synthesise the machine specific information to determining the process variability; demonstrated the usefulness and possibilities opened up by the coupling of modelling with decision rule adopted from biological control principles for autonomous finite capacity scheduling; and shown existence of network of dependencies based on particular problem at hand
ACKNOWLEDGEMENTS
The authors gratefully thank De Montfort University, UK, for funding the research paper.
References
[1] | David Bogle, State of the art of research in flexibility, operability and dynamics, CAPE.NET Technology Working Group 3 - Discussion paper, 2000. |
[2] | Ignacio E. Grossmann, Challenges in the new millennium: Product discovery and design, enterprise and supply chain optimization, global life cycle assessment. Computers and Chemical Engineering, Vol. 29, pp. 29–39, 2004. |
[3] | Christodoulos A. Floudas, Research challenges, opportunities and synergism in systems engineering and computational biology, American Institute of Chemical Engineers, Vol. 51, No. 7, pp. 1872–1884, 2005. |
[4] | Peter R. Horner, Planning under uncertainty. Institute of Operations Research and the Management Sciences (OR/MS) Today, Vol.26, 1999. |
[5] | Olga Perminova, Magnus Gustafsson, and Kim Wikstrom, Defining Uncertainty in Projects – a New Perspective, International Journal of Project Management Vol. 26 pp. 73-79, 2008. |
[6] | Wallace J. Hopp, and Mark L. Spearman, Factory Physics: Foundation of Manufacturing Management. 2nd ed., Irwin/McGraw-Hill, Boston, 2000. |
[7] | Vaidotas Petrauskas, The Use Of Information Flow Analysis For Building An Effective Organization, Information Technology And Control, Vol. 35, No. 4, 2006. |
[8] | Shamsuddin Ahmed, Masjuki Hj Hassan, and Yap Hui Fen, Performance Measurement and Evaluation in an Innovative Modern Manufacturing System, Journal of Applied Sciences, Vol. 5, No. 2, pp. 385-401, 2005. |
[9] | Rachna Shah, and Peter T. Ward, Lean manufacturing: context, practice bundles, and performance. Journal of Operations Management, Vol. 21, No. 2, pp. 129–149, 2003. |
[10] | Peter Hines, Matthias Holweg, Nick Rich, Learning to evolve- A review of contemporary lean thinking. International Journal of Operations & Production Management, Vol. 24 Iss: 10 pp. 994 – 1011, 2004. |
[11] | David J. Stockton, Maria J. Schilstra, Riham A. Khalil and Mark McAuley, Biological Control Processes and their Applications to Manufacturing Planning, ICMR07 Conference Proceedings, De Montfort University, UK, 2007. |
[12] | Lieven L. Demeester, Knut Eichler, and Christopher Loch., What the Biological Cell Can Teach Us About The Future of Manufacturing, INSEAD Working Paper, 2002. |
[13] | Olaf Wolkenhauer, and Mihajlo Mesarovic, Feedback Dynamics and Cell Function: Why Systems Biology is Called Systems Biology, Molecular Biosystem Vol. 1. pp. 14-16, 2005. |
[14] | Zoltan Szallasi, Jorg Stelling, and Vipul Periwal, eds., System Modelling in Cellular Biology: From Concepts to Nuts and Bolts (Boston: The MIT Press), 2006. |
[15] | Fernando L.F. Almeida, Designing and implementation of an intelligent. Journal of Industrial Engineering and Management, Vol 4, No. 4, pp. 718-745, 2011. |
[16] | Nigel Slack, The flexibility of manufacturing systems, International Journal of Operations & Production Management, Vol. 25, No. 12, pp.1190 – 1200, 2005. |
[17] | Frank Mill, and Andrew Sherlock, Biological analogies in manufacturing, computers in Industry, Vol. 43, pp. 153-160, 2000. |
[18] | Carl Anderson, and John J. Bartholdi III, Centralized versus decentralized control in manufacturing: lessons from social insects, Complexity and Complex Systems in Industry, Proceedings, University of Warwick, 19th–20th Sept. pp 92-105, 2000. |
[19] | Jianxin Jiao, Mitchell M. Tseng, Qinhai Ma, and Yi Zou, Generic Bill-of-Materials-and-Operations for High-Variety Production Management, Concurrent Engineering: Research and Application, Vol. 8, No. 4, pp. 297-322, 2000. |